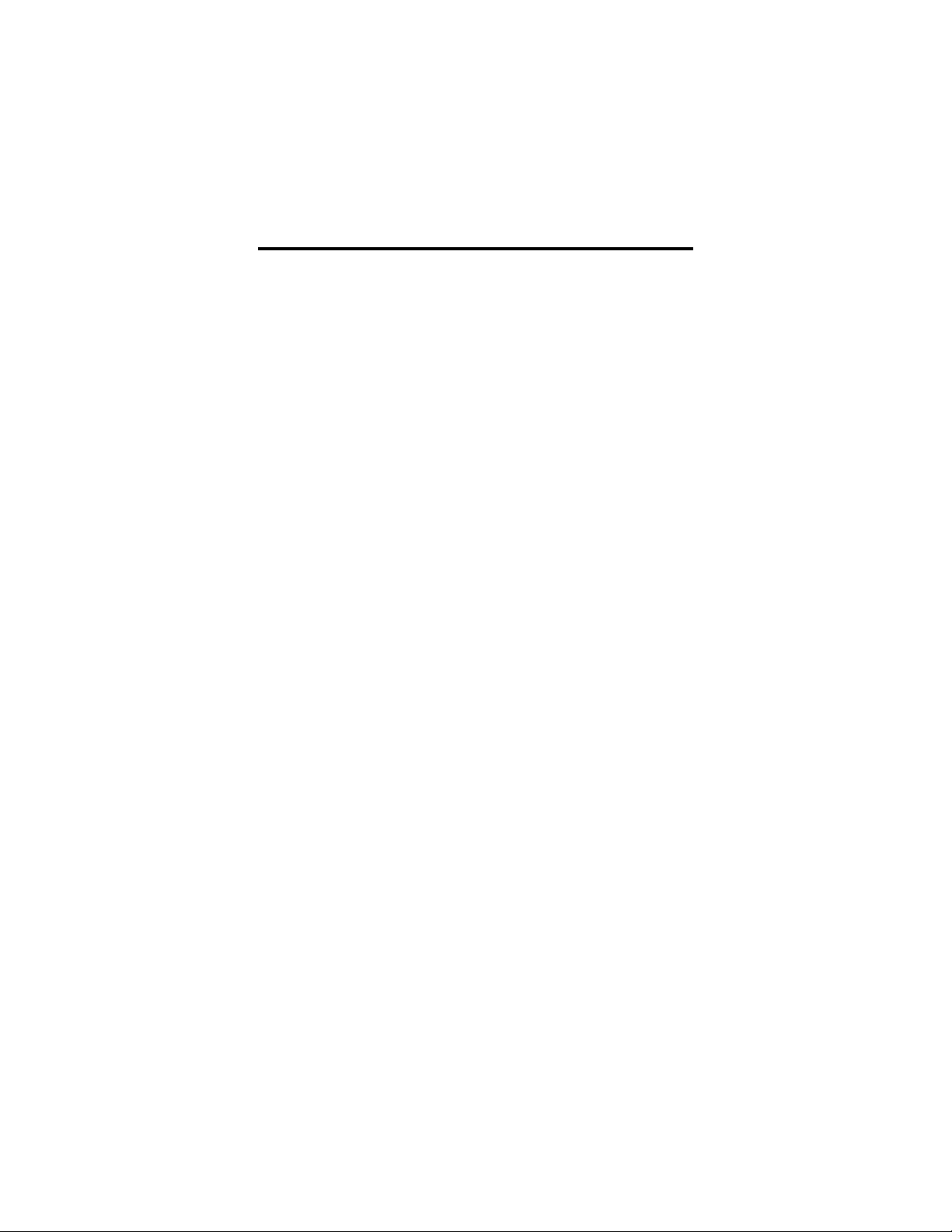
MILODON
2250 Agate Court
Simi Valley, Ca 93065
(805) 577-5950
ANGLED SIDE BOLT MAIN CAP
INSTALLATION INSTRUCTIONS
Congratulations, you have purchased the highest quality 4-bolt performance main caps
available. The tensile strength of the ductile iron that Milodon uses in these main caps is 85,000
PSI. This is considerably stronger than other mild steel “Billet Caps". Also the expansion rate
of ductile iron is equal to that of the cylinder block, eliminating engine bearing failure due to
irregular bearing bore expansion when the engine reaches operating temperature.
In addition to being precision machined, this design uses the superior angled side bolt
configuration. It is this feature that makes them vastly more desirable than the stock 4-bolt cap or
even other aftermarket, stock designed 4-bolt pattern main caps. The side bolts pull from the
side wall of the block and not the flimsy main web area. The entire saddle area is supported
more firmly and the register, that locates the cap, is preloaded to stop any cap movement. In
blown, nitrous and other high power applications this becomes extremely important. In a test we
ran on a Big Block Chevy Pro Stock engine, there was an increase of 1 MPH through the lights
by just installing a set of Milodon main caps!
Before beginning your installation check the parts list. Milodon supplies complete bolt
kits with all main cap sets. However, if maximum strength and durability are required, studs
should be used. Studs are available for all applications, refer to the Milodon catalog for specific
part numbers.
Your Main Cap Kit includes: 3 - Center main caps (#2, #3, #4)
6 - Center main bolts & washers
6 - Outer main bolts & washers
1 - Drill Bushing
STEP 1 Measure #2, #3 and #4 cap registers in the block to determine if registers are equal. If
not, the registers must be squared by milling. Take the largest reading of the six
registers (both sides of three mains) and mill the other registers, at the portion in the
block where the bolts holes are located, down to this measurement. Now that the
block registers are equal, to get your necessary register depth for the main cap, take
the register depth measurement in the block and add the .001 to .003 required side
bolt pad clearance. Mill the cap to yield this dimension. If the clearance dimension is
too large then mill the cap register on the bolt hole pad. If the dimension is too small
then mill the outer most pad taking great care not to kiss the vertical register step.
STEP 2 Main caps should be milled so register depth is .001-.003 more than block register
depth. This allows .001-.003 clearance between cap and block when the center bolts
are torqued down. This clearance is critical, as it is this small air gap that gives the
cap its bite on the register and thus stops the cap walk. Clearance in excess of .003"
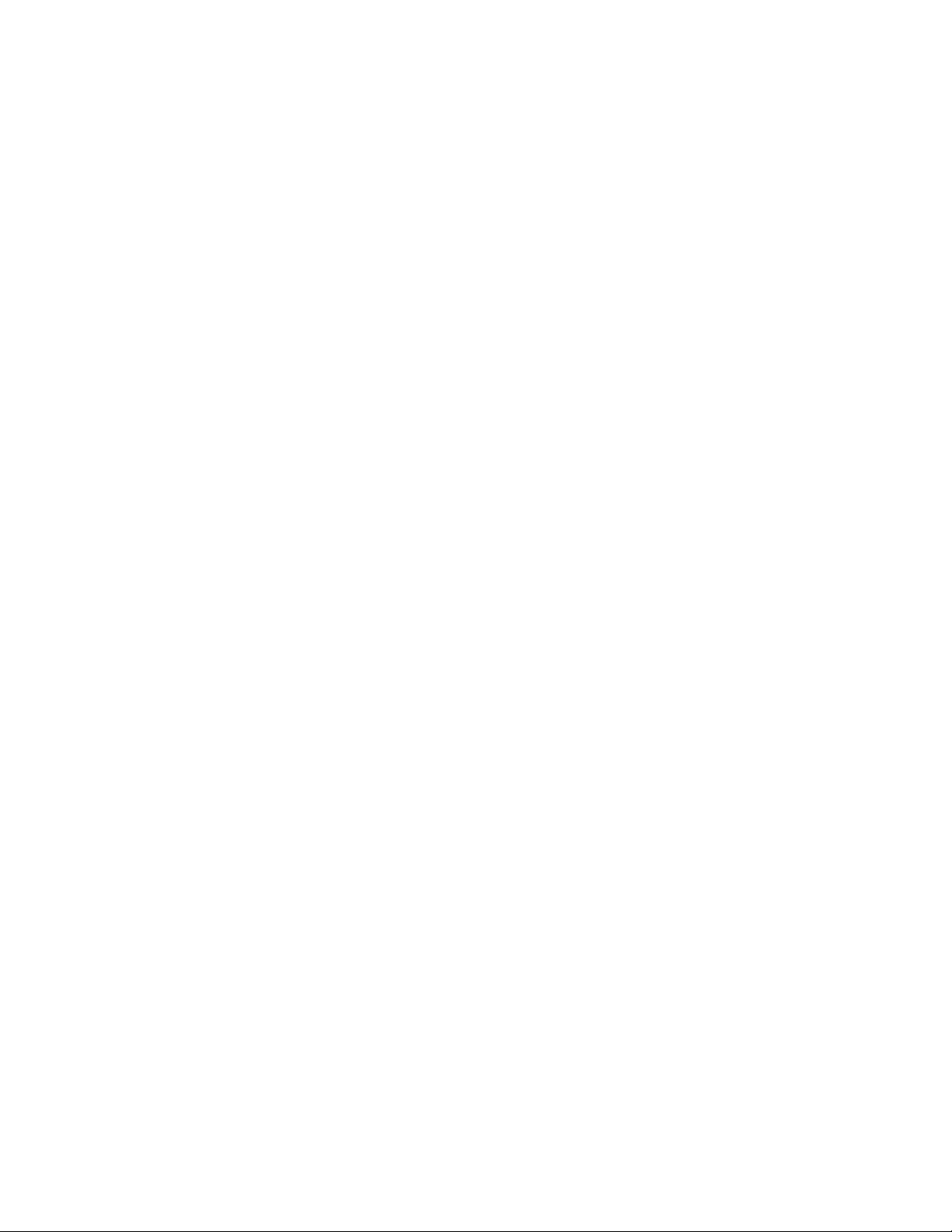
will excessively distort the main bearing bores. These tolerances are important and
must be held closely.
STEP 3 Clean all main bolt holes with a tap. A bottoming tap is recommended on all blocks.
Bolts should be checked on each hole to be sure the bolts do not bottom out in the
holes or an incorrect torque reading will result. For maximum strength main studs
should be used.
STEP 4 Once register depths are correct, install the main caps on the block and tighten center
bolts. Insert bushing supplied with your kit into angled side bolt hole in cap. For
3/8" bolts drill block with 5/16" drill bit ONLY deep enough for bolt length plus
approximately 1/8" clearance. DO NOT drill any deeper than necessary or you will
drill into the water jacket. Check to be sure bolt will not bottom out in hole. Remove
drill bushing and use the cap itself as a tap fixture then tap 3/8"-16 threads. Finish up
with a bottom tap. Note: for 7/16" side bolts follow same procedures above except
drill block with 3/8" drill bit and tap with 7/16" - 14. Extra care must be taken not to
drill too deep as the main oil passage will be intersected.
STEP 5 Clean block thoroughly removing all chips and burrs. Tighten all bolts with a
conventional inside to outside pattern, using oil.
7/16" center bolts torque to 65 ft lbs.
1 / 2" center bolts torque to 110 ft lbs
3 / 8" side bolts torque to 35 ft lbs.
7/16" side bolts torque to 45 ft lbs.
STEP 6 The block is now ready to be align bored. Align bore block initially with a rough cut to
.010 under finished size. On the second pass, align bore exactly to finish size. Align
honing should not necessary if bore can be done close enough. If not, rough align
bore then hone for the final finish. Debur and clean as necessary.
2/99