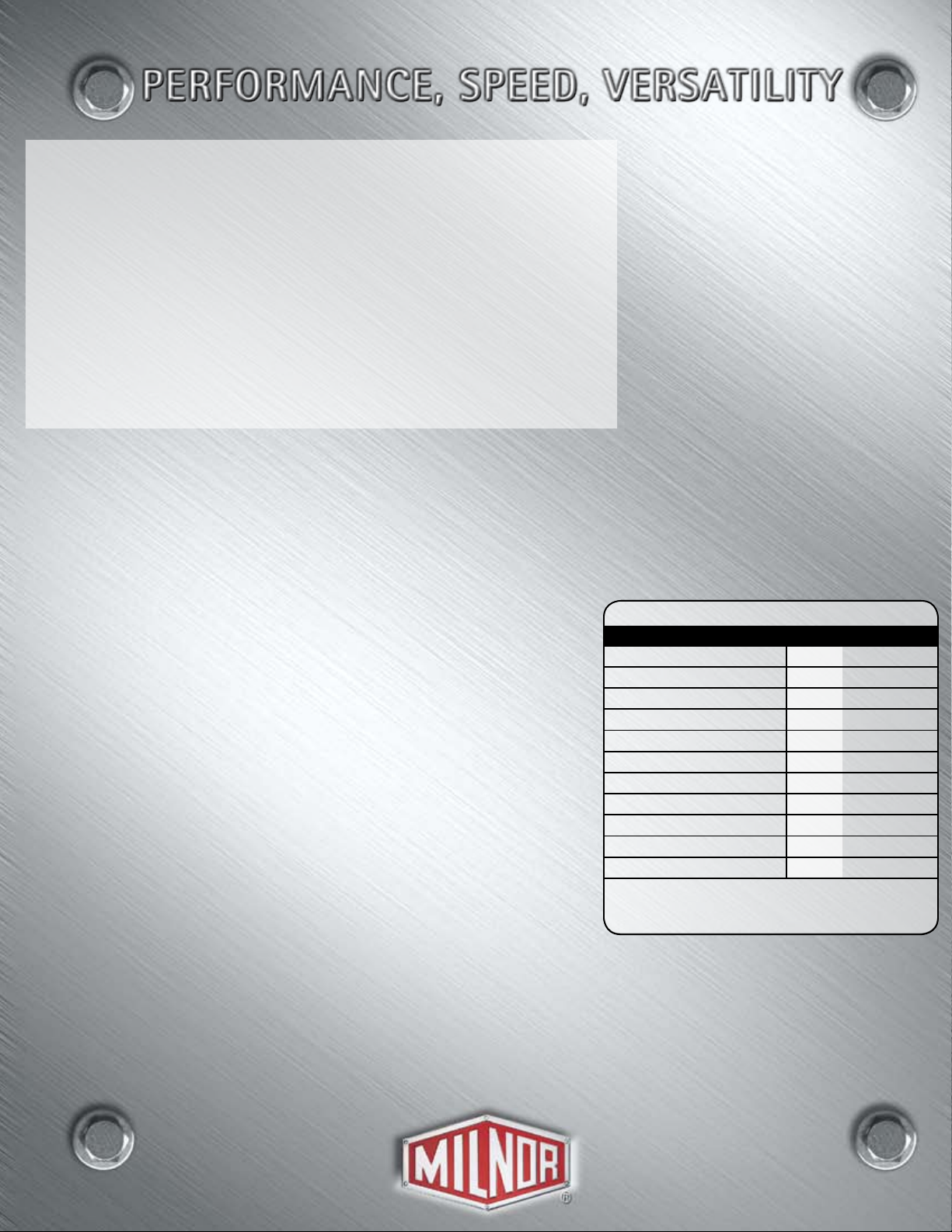
Two-stage extraction saves time, removes more water.
The two most important features in a batch washer’s extraction press are speed (to avoid delaying the washer) and effective
moisture removal (to save time and fuel in the next finishing step). Here’s how Milnor’s press accomplishes both:
Membrane assures uniform extraction.
A soft, pliable membrane adapts to the shape of the batch, allowing
even pressure throughout.
Extraction is divided into two brief stages – pre-press and main press. In the first, a tamper removes most water quickly but
gently. Water exits freely beneath the load, at the sides, and through the top of the tamper. The pre-press basket has large
holes for fast initial water removal and lower final moisture retention.
A two-stage press accommodates two batches at once; each undergoes part of the job concurrently to save time.
Unlike other two-stage presses, Milnor‘s has a traveling basket. It holds the load together while transporting it from pre-press
to the main press. This helps prevent faults that impede production. The machine’s two-speed drive gives fast turnaround and
precise positioning. Its ability to avoid abrupt stops also helps prevent cake collapse.
Microprocessor is flexible, easy-to-use.
Proven microprocessor control provides 16 programmable extraction sequences. Forty-character,
alphanumeric display tells operating status – including time remaining in extraction cycle, loading status,
and status for receiving another load. It also shows production and accounting data, plus fault recognition
with error statements. Control components are interchangeable with those of other Milnor machines, to
®
simplify inventory. Control can be linked to the Mildata
computer system for central programming, data
collection, and system monitoring.
Milnor engineering creates high value.
The high quality design, construction and materials employed are just what you’d expect from MILNOR.
• All steel parts that contact the goods are stainless.
• The press is able to operate at high pressure because the bell is a true spherical-end pressure vessel. This
eliminates the need for intersecting reinforcement members, which creates stress concentration and
thus, failure points.
• Free-oating, roller-guided bell needs no guide rods (which can cause the bell to jam or travel slowly).
• The bell is clamped by a ring of steel that distributes stress uniformly and permits high pressure.
• The membrane press frame is rigidly constructed of thick steel, continuously welded for strength.
• Pressure and volume pumps are belt-driven, not direct-driven with a coupling (so perfect pump/motor
alignment is not needed to prevent strain on the pump shaft).
• There are no mechanical pumps for lifting water (these tend to wear out faster because they cavitate
or lose suction and overheat). Instead, MILNOR removes water from the bell by a trouble-free venturi
pump (which has no moving parts).
• The press can be ordered for various installation arrangements – straight-line or right angle in either
direction, fitting to your laundry’s size and shape.
• The press can be added to existing batch washer installations. The feed end is at an ideal height for
many batch washers, eliminating the need for digging a pit for the press.
• Higher pressure insures better extraction in a given period. This reduces drying time and saves fuel.
• MILNOR also employs relatively small motors, which consume less power.
Compare this to systems using unyielding steel plates. With those
machines, if the batch is lumpy or pyramid-shaped, full pressure
is applied only to the high spots. Other areas are left with more
moisture. Also, if too much pressure is exerted on one spot, there is a
risk of breaking buttons or bending zippers. A steel plate under full
pressure can pinch goods, too.
Because the membrane pressure in the MILNOR press is so effective,
there is no need to supplement it with air pressure. So, you avoid the
expense of a huge air compressor. You also avert uneven extraction
due to air channeling (in “lumpy” batches, air takes the path of
least resistance) and different degrees of permeability throughout
the load (the less permeable goods prevent air from passing through
the goods underneath).
Milnor’s membrane also affords more variability in terms of load
sizes. A variable volume of water enables the press to accommodate
loads that are up to 50% smaller than the rated capacity.
MP2501 SPECIFICATIONS
Rated capacity – lbs. (kg)
Maximum pressure – psi (bar)
Nominal cake diameter – ins. (mm)
Bell diameter – ins. (mm)
Pressure pump motor – HP (kW)
– standard ow
– high ow
Volume pump motor – HP (kW)
Sled drive motors – HP (kW)
Bed (discharge) height – ins. (mm)
Approx. net weight* – lbs. (kg.)
Specifications and appearance subject to change without notice.
Contact factory for acoustics data.
110 (50)
450 (31)
40 (1016)
46 (1168)
7.5 (5.59)
10 (7.46)
10 (7.46)
2/.75 ( 1.49/.56)
13.19 (335)
19,980 (9062)
Ask about Milnor’s other automated
laundry machinery.
Contact us for information about Milnor’s CBW® batch washers, passthrough dryers, centrifugal extractors, conveyors, and washer-extractors.
Our Laundry Engineering Department can design an integrated laundry
system that will give you maximum productivity and energy efficiency.
Printed in U.S.A.
© Pellerin Milnor Corporation
Class 5-9 Brochure B22SL01001/08204
Pellerin Milnor Corporation
P.O. Box 400, Kenner, LA 70063-0400 USA
504-712-7656 • 800-469-8780
Fax: 504-468-3094
E-mail: mktg@milnor.com
www.milnor.com