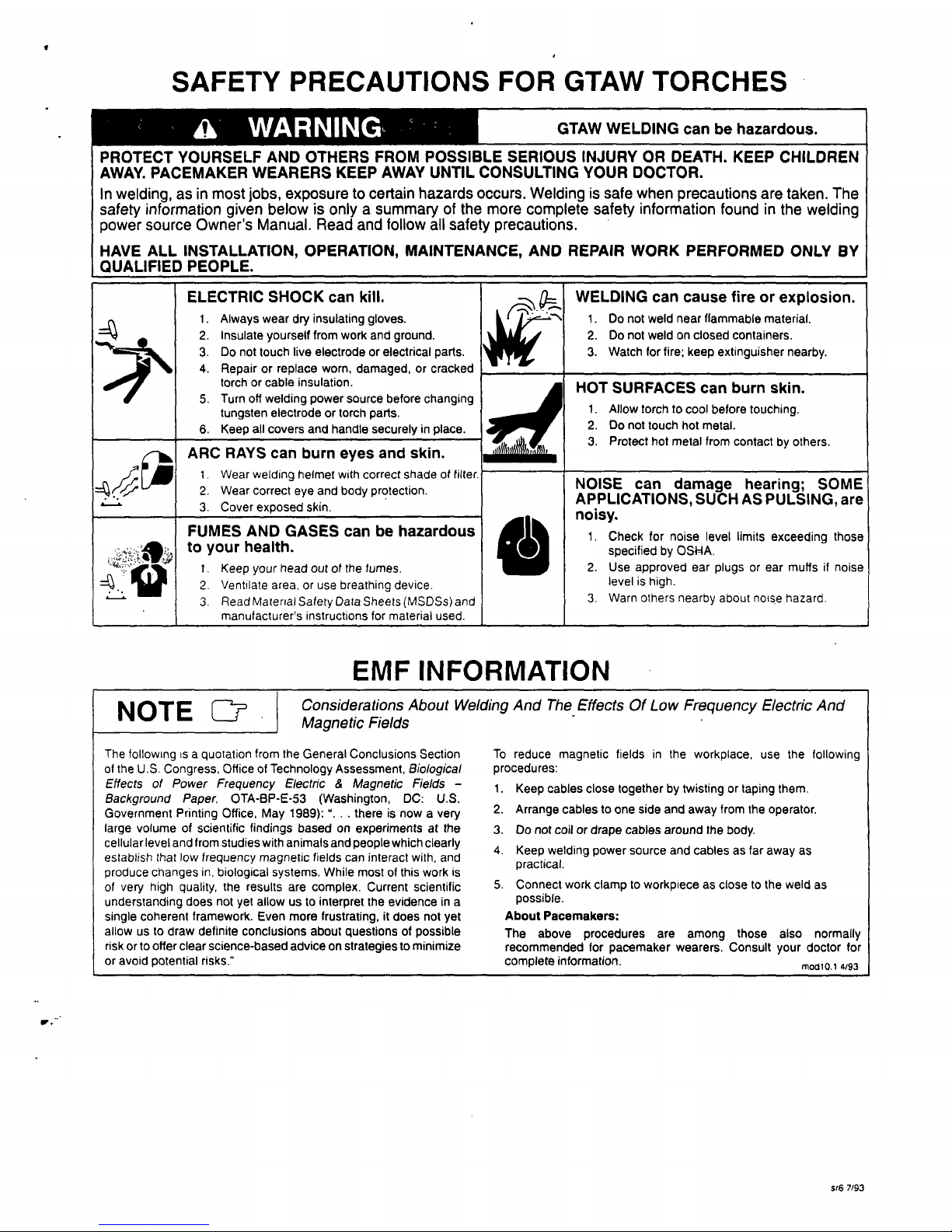
SAFETY
PRECAUTIONS
FOR
GTAW
TORCHES
ELECTRIC
SHOCK
can
kill.
1.
Always
wear
dry
insulating
gloves.
2.
Insulate
yourself
from
work
and
ground.
3.
Do
not
touch
live
electrodeorelectrical
parts.
4.
Repair
or
replace
worn,
damaged,
or
cracked
torch
or
cable
insulation.
5.
Turn
oft
welding
power
source
before
changing
tungsten
electrode
or
torch
parts.
6.
Keep
all
covers
and
handle
securely
in
ARC
RAYS
can
burn
eyes
and
skin.
1.
Wear
welding
helmet
with
correct
shade
of
filter.
2.
Wear
correct
eye
and
body
protection.
3.
Cover
exposed
skin.
FUMES
AND
GASES
can
be
hazardous
to
your
health.
1.
Keep
your
head
out
of
the
fumes.
2.
Ventilate
area,
or
use
breathing
device.
3.
Read
Material
Safety
Data
Sheets
(MSDSs)
and
manufacturers
instructions
for
material
used.
WELDING
can
cause
fire
or
explosion.
1.Donot
weld
near
flammable
material.
2.
Do
not
weldonclosed
containers.
3.
Watch
for
fire;
keep
extinguisher
nearby.
HOT
SURFACES
can
burn
skin.
1.
Allow
torch
to
cool
before
touching.
2.
Do
not
touch
hot
metal.
3.
Protect
hot
metal
from
contact
by
others.
NOISE
can
damage
hearing;
SOME
APPLICATIONS,
SUCH
AS
PULSING,
are
noisy.
1.
Check
for
noise
level
limits
exceeding
those
specified
by
OSHA.
2.
Use
approved
ear
plugs
or
ear
muffs
if
noise
level
is
high.
3.
Warn
others
nearby
about
nos~e
hazard.
EMF
INFORMATiON
a
WARNING
GTAW
WELDING
can
be
hazardous.
PROTECT
YOURSELF
AND
OTHERS
FROM
POSSIBLE
SERIOUS
INJURY
OR
DEATH.
KEEP
CHILDREN
AWAY.
PACEMAKER
WEARERS
KEEP
AWAY
UNTIL
CONSULTING
YOUR
DOCTOR.
In
welding,
as
in
most
jobs,
exposure
to
certain
hazards
occurs.
Welding
is
safe
when
precautions
are
taken.
The
safety
information
given
below
is
only
a
summary
of
the
more
complete
safety
information
found
in
the
welding
power
source
Owners
Manual.
Read
and
follow
all
safety
precautions.
HAVE
ALL
INSTALLATION,
OPERATION,
MAINTENANCE,
AND
REPAIR
WORK
PERFORMED
ONLY
BY
QUALIFIED
PEOPLE
______________________________
A
NOTE
~H
Considerations
About
We/ding
And
The
Effects
Of
Low
Frequency
Electric
And
Magnetic
Fields
The
following
is
a
quotation
from
the
General
Conclusions
Section
of
the
U.S.
Congress,
Office
of
Technology
Assessment,
Biological
Effects
of
Power
Frequency
Electric
&
Magnetic
Fields
Background
Paper,
OTA-BP-E-53
(Washington,
DC:
U.S.
Government
Printing
Office,
May
1989):.
.
.
there
is
now
a
very
large
volume
of
scientific
findings
based
on
experiments
at
the
cellular
level
and
from
studies
with
animals
and
people
which
clearly
establish
that
low
frequency
magnetic
fields
can
interact
with,
and
produce
changes
in,
biological
systems.
While
most
of this
work
is
of
very
high
quality,
the
results
are
complex.
Current
scientific
understanding
does
not
yet
allow
us
to
interpret
the
evidence
in
a
single
coherent
framework.
Even
more
frustrating,
it
does
not
yet
allow
us
to
draw
definite
conclusions
about
questions
of
possible
risk
or
to
offer
clear
science-based
advice
on
strategies
to
minimize
or
avoid
potential
risks.
To
reduce
magnetic
fields
in
the
workplace,
use
the
following
procedures:
1.
Keep
cables
close
together
by
twisting
or
taping
them.
2.
Arrange
cables
to
one
side
and
away
from
the
operator.
3.
Do
not
coil
or
drape
cables
around
the
body.
4.
Keep
welding
power
source
and
cablesasfar
away
as
practical.
5.
Connect
work
clamp
to
workpiece
as
close
to
the
weld
as
possible.
About
Pacemakers;
The
above
procedures
are
among
those
also
normally
recommended
for
pacemaker
wearers.
Consult
your
doctor
for
complete
information.
modlo,1
4/93
5t6
7/93