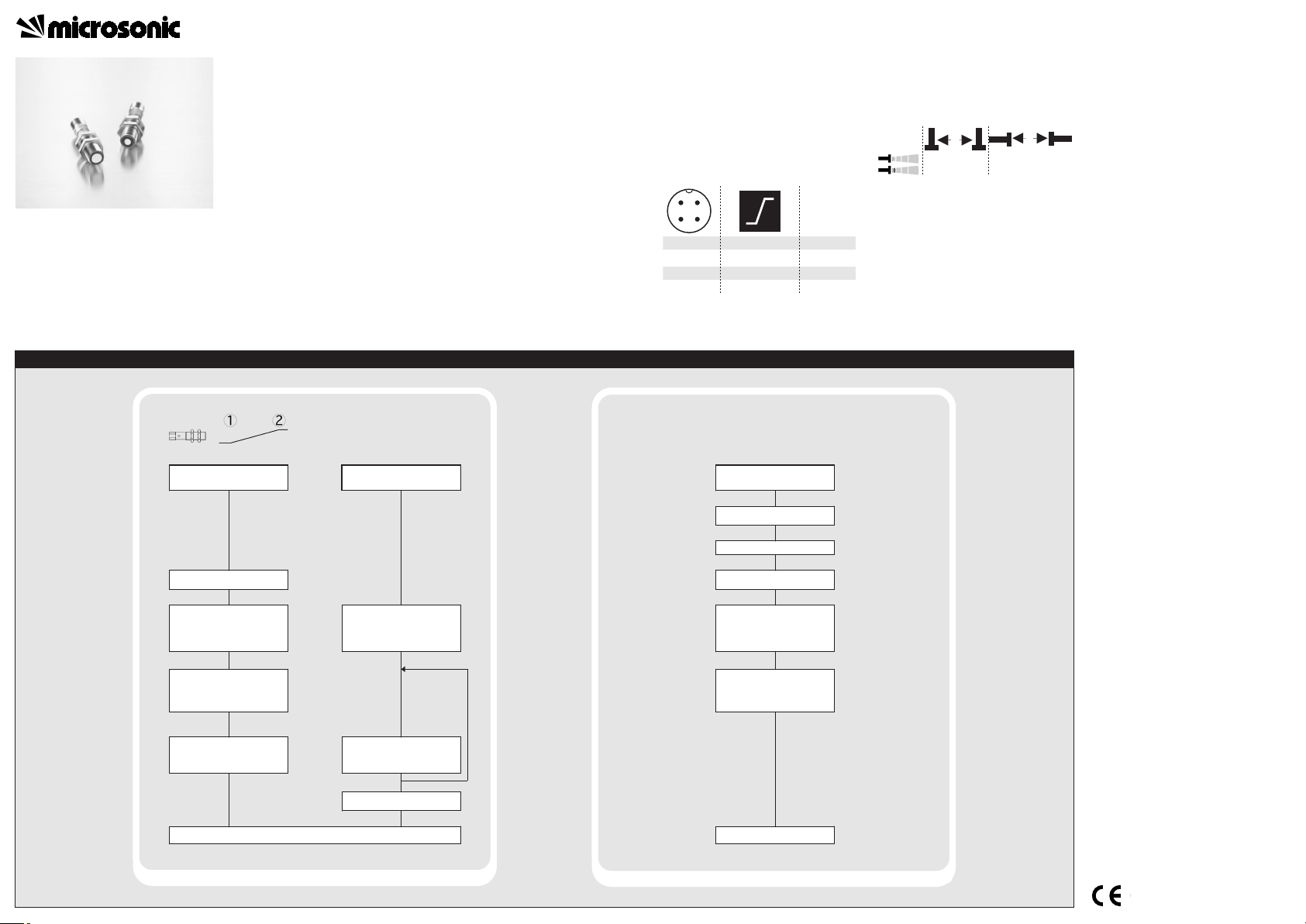
Sensor adjustment with Teach-in procedure
Place object at position .
Connect Teach-in for about
3 s to +U
B
, until LED
flashes yellow.
Place object at position .
Set rising/falling output
characteristic curve
Connect Teach-in for about
13 s to +U
B
, until LED
flashes green/yellow
alternately.
green, green/
yellow:
rising,
green:
falling characteristic curve
Connect Teach-in to +U
B.
Keep Teach-in connected to
+U
B
for about 13 s,
until LED flashes
green/yellow alternately.
Disconnect Teach-in from
+U
B
within 5 s before
switching off power supply.
Connect Teach-in for about
1 s to +U
B.
To change output charac-
teristic connect Teach-in for
about 1 s to +U
B.
brown
blue
4
2
I|U
Teach-in
black
white
Ultrasonic Sensors
Operating instructions
Ultrasonic sensor with one
analogue output
nano-15/CI nano-15/CU
nano-24/CI nano-24/CU
Product Description
The nano sensor offers a non-contact
measurement of the distance to an
object that has to be present within
the sensor’s detection zone. Depending on the set window limits, a distance-proportional analogue signal is
output.
The window limits of the analogue
output and its characteristic can be
adjusted with the Teach-in procedure.
One 2-colour LED indicates operation
and the state of the analogue
output.
Safety Notes
Read the operating instructions
prior to start-up.
Connection, installation and
adjustment works should be carried out by expert personnel only.
No safety component in
accordance with the EU Machine
Directive
Use for intended purpose only
nano ultrasonic sensors are used for
non-contact detection of objects.
Installation
Mount the sensor at the installa-
tion site.
Connect a connection cable to the
M12 device plug.
The assembly distances shown in fig.
2 for two or more sensors should not
be fallen below in order to avoid mutual interference.
Fig. 1: Pin assignment with view onto sensor
plug and colour coding of the
microsonic connection cable
Start-Up
Connect the power supply.
Carry out the sensor adjustment in
accordance with the diagram.
Fig.2: Assembly distances, indicating syn-
chronization
Factory Setting
Rising analogue characteristic
curve between the blind zone and
the operating range
Maintenance
microsonic sensors are maintenancefree. In case of excess caked-on dirt
we recommend to clean the white
sensor surface.
Notes
Every time the power supply is
switched on, the sensor detects its
actual operating temperature and
transmits it to the internal temperature compensation. This results
in a slight correction of the analogue output value after 45 seconds.
If the sensor was switched off for
at least 30 minutes and after power on an object is placed in the
middle of the adjusted analogue
window for 30 minutes (the analogue output value is in the range
of 11 to 13 mA or 4.4 to 5.6 V) a
new adjustment of the internal
temperature compensation to the
actual mounting conditions takes
place.
The sensors of the nano family
have a blind zone. Within this
zone a distance measurement is
not possible.
In the normal operating mode, an il-
luminated yellow LED signals the object is within the adjusted window
limits.
The sensor can be reset to its fac-
tory setting (see »Further settings«).
2004/108/EC
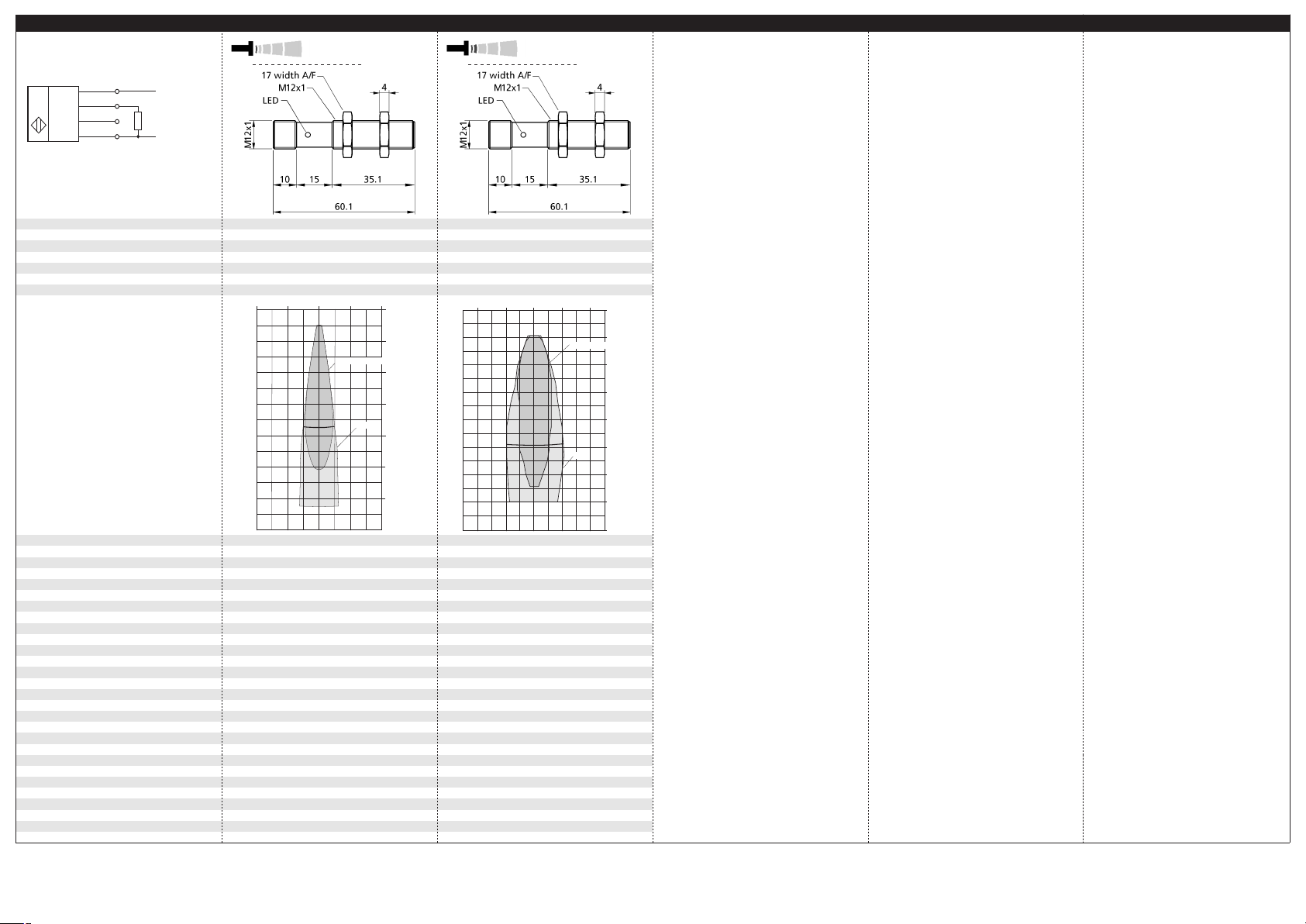
Technical data
detection zones
for different objects:
The dark grey areas are determined with a
round bar and indicate the typical operating
range of a sensor. In order to obtain the light
grey areas, a plate (100 x 100 mm) is
introduced into the beam spread from the side.
In doing so, the optimum angle between
plate and sensor is always employed.
This therefore indicates the maximum
detection zone of the sensor.
It is not possible to evaluate ultrasonic
reflections outside this area.
no-load current consumption
± 1 % (temperature drift internally compensated)
brass sleeve, nickel-plated, plastic parts: PBT;
max. tightening torque of nuts
class of protection to EN 60 529
ultrasonic transducer: polyurethane foam,
time delay before availability
RL ≤ 500 Ω, rising/falling characteristic
10 - 30 V DC for RL ≤ 100 Ω,
15 - 30 V DC for RL > 100 Ω,
RL ≥ 100 kΩ, short circuit proof,
rising/falling characteristic
15 - 30 V DC, reverse polarity protection
1 analogue output
1
2
4
3
+U
B
-U
B
Teach-in
U
R
L
U | I
8 cm 4 cm 0 cm 4 cm 8 cm
0 cm
4 cm
8 cm
12 cm
16 cm
20 cm
24 cm
Round bar ø 10 mm
Plate
microsonic GmbH | Hauert 16 | 44227 Dortmund | Germany | Tel: +49 2 31 / 97 51 51-0 | Fax: +49 2 31 / 97 51 51-51 | E-Mail: info@microsonic.de | www.microsonic.de |
The content of this document is subject to technical changes. Specifications in this document are presented in a descriptive way only. They do not warrant any product features.
69 µm
40 mm
240 mm
350 mm
See detection zone
500 kHz
69 µm
± 0,15 %
10 cm 5 cm 0 cm 5 cm 10 cm
nano-24...
Round bar ø 10 mm
Plate
0 cm
5 cm
10 cm
15 cm
20 cm
25 cm
30 cm
± 1 % (temperature drift internally compensated)
± 10 %
< 40 mA
brass sleeve, nickel-plated, plastic parts: PBT;
epoxy resin with glass content
1 Nm
4-pin M12 initiator plug
analogue output 4-20 mA
analogue output 0-10 V
ultrasonic transducer: polyurethane foam,
epoxy resin with glass content
1 Nm
IP 67
EN 60947-5-2
4-pin M12 initiator plug
Teach-in via pin 2
LED green/yellow
Teach-in
-25°C to +70°C
-40°C to +85°C
15 g
30 ms
< 300 ms
nano-24/CI
RL ≤ 500 Ω, rising/falling characteristic
10 - 30 V DC for RL ≤ 100 Ω,
15 - 30 V DC for RL > 100 Ω,
nano-24/CU
R
≥ 100 kΩ, short circuit proof,
L
rising/falling characteristic
15 - 30 V DC, reverse polarity protection
35 cm