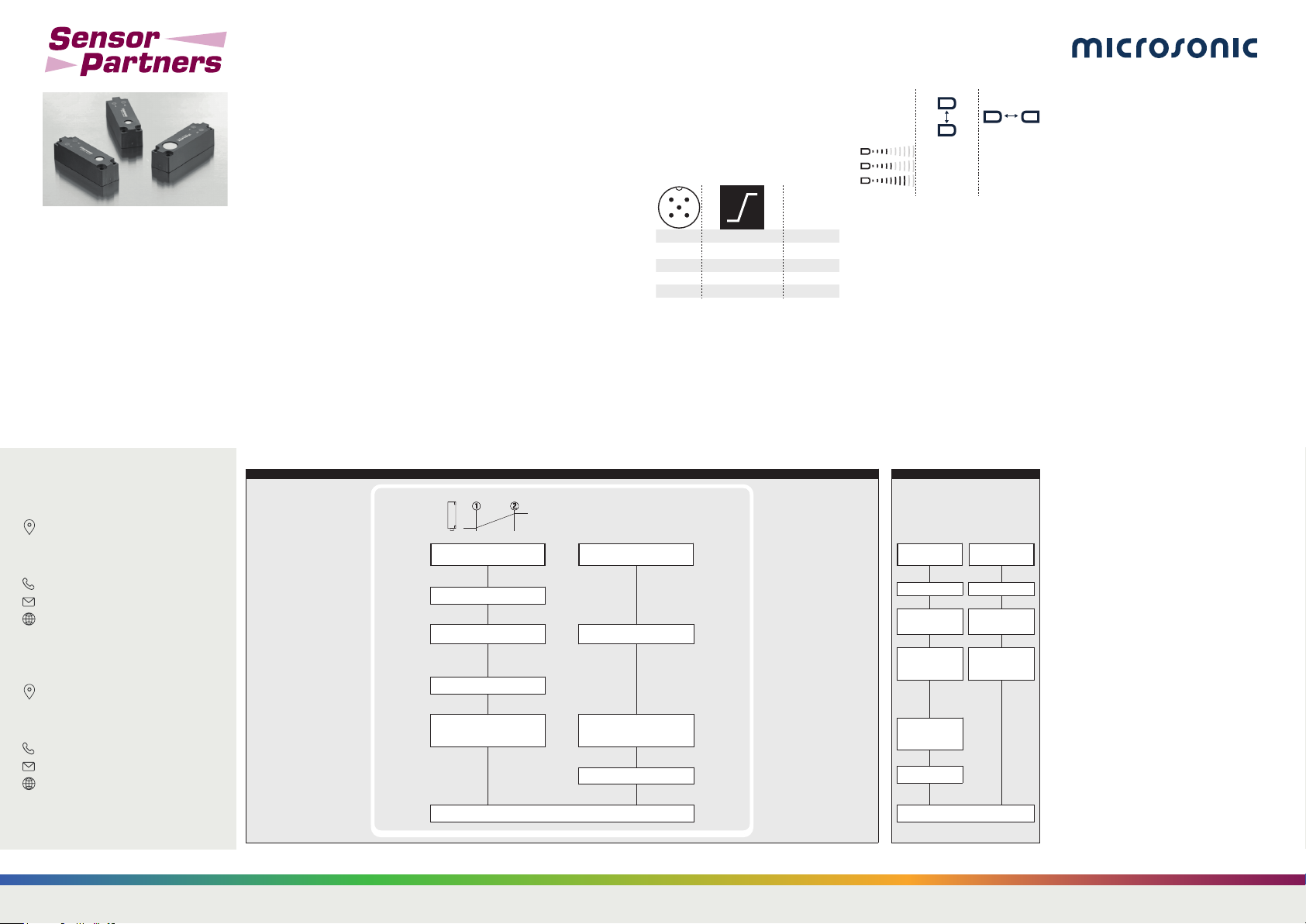
Product description
The lcs-sensor with one analogue out-
put measures the distance to an object
within the detection zone contactless. A
signal proportional to distance is cre-
ated according to the adjusted window
margings of the analogue characteristic
curve.
The sensor automatically detects the
load put to the analogue output and
switches to current output or voltage
output respectively.
Choosing between rising and falling
output characteristic is possible.
Light emitting diodes (three-colour
LEDs) indicate the operation conditions.
The sensors can be trained using Teach-
in processes.
Using the LinkControl adapter (optional
accessory) all sensor parameter settings
may be made by a Windows-Software.
Important instructions for assembly and
application
All employee and plant safety-relevant
measures must be taken prior to assembly,
start-up, or maintenance work (see operation
manual for the entire plant and the operator
instruction of the plant).
The sensors are not considered as safety
equipment and may not be used to ensure
human or machine safety!
The lcs-sensors indicate a blind zone, in
which the distance cannot be measured. The
operating range indicates the distance of the
sensor that can be applied with normal re-
flectors with sufficient function reserve.
When using good reflectors, such as a calm
water surface, the sensor can also be used up
to its maximum range. Objects that strongly
absorb (e.g. plastic foam) or diffusely reflect
sound (e.g. pebble stones) can also reduce
the defined operating range.
Assembly instructions
Assemble the sensor at the installation
location.
Plug in the connector cable to the M12
connector.
Fig. 1: Pin assignment with view onto sensor
plug and colour coding of the
microsonic connection cable
Assembly distances
The assembly distances shown in Fig.2 for
two or more sensors should not be fallen
brown
blue
4
2
5
-
I/U
black
white
Com. grey
Fig. 2: Assembly distances
Start-up
lcs-sensors are delivered factory made with
the following settings:
Rising analogue characteristic
Window margins for the analogue out-
put set to blind zone and operating
range
Measurement range set to maximum
range
Set the parameters of the sensor using the
Teach-in procedure.
≥0.25 m
≥0.35 m
≥1.30 m
≥2.50 m
≥1.10 m ≥8.00 m
Operation
lcs-sensors work maintenance free. Small
amounts of dirt on the surface do not influ-
ence function. Thick layers of dirt and caked-
on dirt affect sensor function and therefore
must be removed.
Note
lcs-sensors have internal temperature
compensation. Because the sensors heat
up on their own, the temperature com-
pensation reaches its optimum working
point after approx. 30 minutes of opera-
tion.
If an object is within the set window
margins of the analogue output, then
LED D1 lights up green, if the object is
outside the window margins, then LED
D1 lights up red.
The load put to the analogue output is
detected automatically when turning
supply voltage on.
If the signal at the Com line does not
Product description
The lcs-sensor with one analogue out-
put measures the distance to an object
within the detection zone contactless. A
signal proportional to distance is cre-
ated according to the adjusted window
margings of the analogue characteristic
curve.
The sensor automatically detects the
load put to the analogue output and
switches to current output or voltage
output respectively.
Choosing between rising and falling
output characteristic is possible.
Light emitting diodes (three-colour
LEDs) indicate the operation conditions.
The sensors can be trained using Teach-
in processes.
Using the LinkControl adapter (optional
accessory) all sensor parameter settings
may be made by a Windows-Software.
Important instructions for assembly and
application
All employee and plant safety-relevant
measures must be taken prior to assembly,
start-up, or maintenance work (see operation
manual for the entire plant and the operator
instruction of the plant).
The sensors are not considered as safety
equipment and may not be used to ensure
human or machine safety!
The lcs-sensors indicate a blind zone, in
which the distance cannot be measured. The
operating range indicates the distance of the
sensor that can be applied with normal re-
flectors with sufficient function reserve.
When using good reflectors, such as a calm
water surface, the sensor can also be used up
to its maximum range. Objects that strongly
absorb (e.g. plastic foam) or diffusely reflect
sound (e.g. pebble stones) can also reduce
the defined operating range.
Assembly instructions
Assemble the sensor at the installation
location.
Plug in the connector cable to the M12
connector.
Fig. 1: Pin assignment with view onto sensor
plug and colour coding of the
microsonic connection cable
Assembly distances
The assembly distances shown in Fig.2 for
two or more sensors should not be fallen
below in order to avoid mutual interference.
Fig. 2: Assembly distances
Start-up
lcs-sensors are delivered factory made with
the following settings:
Rising analogue characteristic
Window margins for the analogue out-
put set to blind zone and operating
range
Measurement range set to maximum
range
Set the parameters of the sensor using the
Teach-in procedure.
Operation
lcs-sensors work maintenance free. Small
amounts of dirt on the surface do not influ-
ence function. Thick layers of dirt and caked-
on dirt affect sensor function and therefore
must be removed.
Note
lcs-sensors have internal temperature
compensation. Because the sensors heat
up on their own, the temperature com-
pensation reaches its optimum working
point after approx. 30 minutes of opera-
tion.
If an object is within the set window
margins of the analogue output, then
LED D1 lights up green, if the object is
outside the window margins, then LED
D1 lights up red.
The load put to the analogue output is
detected automatically when turning
supply voltage on.
If the signal at the Com line does not
change for 20 seconds during parameter
setting mode the made changes are sto-
red and the sensor returns to normal
mode operation.
You can reset the factory settings at any
time, see »Lock Teach-in & factory set-
ting«
.
lcs-sensors optional can be programmed
using the LinkControl adapter LCA-2,
see «Optional setting of parameters
using the LinkControl Adapter LCA-2».
Lock Teach-in & factory setting
Activate/deactivate
Teach-in
While Com is connected
to -UB turn on
power suply
While Com is connected
to -UB turn on
power suply
Keep Com connected to
-UB until both LEDs flash
simultaneously
(ca. 3 s)
on: Teach-in
activated
off: Teach-in
deactivated
To activate or
deactivate Teach-in
connect Com to -UB for
about 1 s
Keep Com connected to
-UB until both LEDs
stop flashing
(ca. 13 s)
Place object at position
Set rising/falling output
characteristic curve
Connect Com to +UB until both LEDs flash
simultaneously (ca. 3 s)
Place object at position
Connect Com to +UB
for about 1 s
Connect Com to +UB until both LEDs flash
mutually (ca. 13 s)
flashes
an: rising /
aus: falling output
characteristic curve
To change output characteristic connect
Com to +UB
for about 1 s
Instrucion manual
lcs-Ultrasonic Sensors with
one analogue output
lcs-25/IU/QP
lcs-35/IU/QP
lcs-130/IU/QP
Product description
The lcs-sensor with one analogue out-
put measures the distance to an object
within the detection zone contactless. A
signal proportional to distance is cre-
ated according to the adjusted window
margings of the analogue characteristic
curve.
The sensor automatically detects the
load put to the analogue output and
switches to current output or voltage
output respectively.
Choosing between rising and falling
output characteristic is possible.
Light emitting diodes (three-colour
LEDs) indicate the operation conditions.
The sensors can be trained using Teach-
in processes.
Using the LinkControl adapter (optional
accessory) all sensor parameter settings
may be made by a Windows-Software.
Important instructions for assembly and
application
All employee and plant safety-relevant
measures must be taken prior to assembly,
start-up, or maintenance work (see operation
manual for the entire plant and the operator
instruction of the plant).
The sensors are not considered as safety
equipment and may not be used to ensure
human or machine safety!
The lcs-sensors indicate a blind zone, in
which the distance cannot be measured. The
operating range indicates the distance of the
sensor that can be applied with normal re-
flectors with sufficient function reserve.
When using good reflectors, such as a calm
water surface, the sensor can also be used up
to its maximum range. Objects that strongly
absorb (e.g. plastic foam) or diffusely reflect
sound (e.g. pebble stones) can also reduce
the defined operating range.
Assembly instructions
Assemble the sensor at the installation
location.
Plug in the connector cable to the M12
connector.
Fig. 1: Pin assignment with view onto sensor
plug and colour coding of the
microsonic connection cable
Assembly distances
The assembly distances shown in Fig.2 for
two or more sensors should not be fallen
below in order to avoid mutual interference.
brown
blue
4
2
5
-
I/U
black
white
Com. grey
Fig. 2: Assembly distances
Start-up
lcs-sensors are delivered factory made with
the following settings:
Rising analogue characteristic
Window margins for the analogue out-
put set to blind zone and operating
range
Measurement range set to maximum
range
Set the parameters of the sensor using the
Teach-in procedure.
≥0.25 m
≥0.35 m
≥1.30 m
≥2.50 m
≥1.10 m ≥8.00 m
Operation
lcs-sensors work maintenance free. Small
amounts of dirt on the surface do not influ-
ence function. Thick layers of dirt and caked-
on dirt affect sensor function and therefore
must be removed.
Note
lcs-sensors have internal temperature
compensation. Because the sensors heat
up on their own, the temperature com-
pensation reaches its optimum working
point after approx. 30 minutes of opera-
tion.
If an object is within the set window
margins of the analogue output, then
LED D1 lights up green, if the object is
outside the window margins, then LED
D1 lights up red.
The load put to the analogue output is
detected automatically when turning
supply voltage on.
If the signal at the Com line does not
change for 20 seconds during parameter
setting mode the made changes are sto-
red and the sensor returns to normal
mode operation.
You can reset the factory settings at any
time, see »Lock Teach-in & factory set-
ting«
.
lcs-sensors optional can be programmed
using the LinkControl adapter LCA-2,
see «Optional setting of parameters
using the LinkControl Adapter LCA-2».
MV-DO-074366-595316
2014/30/EU
Lock Teach-in & factory setting
Keep Com connected to
-UB until both LEDs flash
on: Teach-in
activated
off: Teach-in
deactivated
Sensor adjustment with Teach-in procedure
Connect Com to +UB until both LEDs flash
Connect Com to +UB until both LEDs flash
flashes
an: rising /
aus: falling output
characteristic curve
Instrucion manual
lcs-Ultrasonic Sensors with
one analogue output
lcs-25/IU/QP
lcs-35/IU/QP
lcs-130/IU/QP
Contact
Sensor Partners BV
James Wattlaan 15
5151 DP Drunen
The Netherlands
+31 (0)416 - 37 82 39
info@sensorpartners.com
sensorpartners.com
Sensor Partners BVBA
Z.1 Researchpark 310
B-1731, Zellik
Belgium
+32 (0)2 - 464 96 90
info@sensorpartners.com
sensorpartners.com
Set window margins
Place object at position
Place object at position
Connect Com to +UB
for about 1 s
To change output characteristic connect
Normal mode operation
Set analogue output
SENSORPARTNERS.COM
1
2
5
1
3
4
2
5
-U
-
I/U
Com. grey
Set rising/falling output
characteristic curve
Com to +UB
for about 1 s
Wait for 10 s
≥0.25 m
≥0.35 m
≥1.10 m ≥8.00 m
brown
blue
black
white
Activate/deactivate
deactivate Teach-in
Teach-in
to -UB turn on
simultaneously
Wait for 10 s
Reset to factory
to -UB turn on
-UB until both LEDs
for
B
Normal mode operation
≥1.30 m
≥2.50 m
setting
stop flashing

Resolution, sampling rate
Temperature drift internal compensated, ≤ 2%, may
be deactivated 1) (0,17%/K without compensation
9 V to 30 V DC, reverse polarity protection
No-load current consumption
ultrasonic transducer: polyurethane foam,
Class of protection to EN 60 529
Yes, with LCA-2 & LinkControl
Time delay before availability
RL ≤ 100 Ω at 9 V ≤ UB ≤ 20 V;
Temperature drift internal compensated, ≤ 2%, may
be deactivated 1) (0,17%/K without compensation
9 V to 30 V DC, reverse polarity protection
ultrasonic transducer: polyurethane foam,
Yes, with LCA-2 & LinkControl
RL ≤ 100 Ω at 9 V ≤ UB ≤ 20 V;
lcs-25...
lcs-35...
lcs-130...
Detection zones
The dark grey areas are determined
with a thin round bar (10 mm dia.)
and indicate the typical operating range
of a sensor. In order to obtain the light grey
areas, a plate (100 x 100 mm) is introduced
into the beam spread from the side.
In doing so, the optimum angle between
plate and sensor is always employed.
This therefore indicates the maximum
It is not possible to evaluate ultrasonic
for different objects:
detection zone of the sensor.
reflections outside this area.
10 cm
5 cm
threaded bush
5 cm
0 cm
ausgerichtete Platte
Plate
Rohr ø 10 mm
Round bar
10 cm
0 cm
5 cm
10 cm
15 cm
20 cm
25 cm
30 cm
35 cm
0 to 65 mm
350 mm
600 mm
See detection zone
400 kHz
0,18 mm
± 0,15 %
20 cm
10 cm
threaded bush
0 cm
10 cm
ausgerichtete Platte
Plate
Rohr ø 27 mm
Round bar
20 cm
0 cm
10 cm
20 cm
30 cm
35 cm
40 cm
50 cm
60 cm
0,8 m
0,4 m
threaded bush
0,4 m
0 m
ausgerichtete Platte
Plate
Rohr ø 27 mm
Round bar
0,8 m
0 m
0,4 m
0,8 m
1,2 m
1,3 m
1,6 m
2 m
Type of connection
Voltage output 0 – 10 V
1) Can be programmed with LinkControl
Accuracy
Order No.
Temperature drift internal compensated, ≤ 2%, may
be deactivated
9 V to 30 V DC, reverse polarity protection
±10 %
< 60 mA
PBT
epoxy resin �with glass content
5-pin M12 initiator plug
Rising/falling output characteristic
100 kΩ at UB ≥ 15 V, short-circuit-proof
R
Rising/falling output characteristic Rising/falling output characteristic
ultrasonic transducer: polyurethane foam,
epoxy resin �with glass content
IP 65
EN 60947-5-2
5-pin M12 initiator plug
2 three-colour LEDs
Yes, with LCA-2 & LinkControl
-25°C to +70°C
-40°C to +85°C
120 g
70 ms
< 300 ms
lcs-35/IU/QP
RL ≤ 100 Ω at 9 V ≤ UB ≤ 20 V;
R
≤ 500 Ω at UB ≥ 20 V
L
Rising/falling output characteristic
RL ≥ 100 kΩ at UB ≥ 15 V, short-circuit-proof
1)
(0,17%/K without compensation
SENSORPARTNERS.COM
epoxy resin �with glass content
5-pin M12 initiator plug
Rising/falling output characteristic
100 kΩ at UB ≥ 15 V, short-circuit-proof
R
Rising/falling output characteristic

Setting of additional functions in the LCA-2
Start here
Optional setting of parameters using the LinkControl Adapter LCA-2 (Offline programming)
T1 T2
+
Press on the LCA-2 simultaneously for about 3 s until welcome message has passed
Offline programming
Load Sensor parame-
ters in the LinkControl
Adapter LCA-2
Change parameters
and additional functions as described here
Write changed para-
meters back into the
lcs- sensor
Please refer to the quick reference guide on the LCA-2.
Set analogue output
Start here
T1 + T2
T1 T2
Press on the LCA-2 simultaneously for about 13 s until «Add» is shown in the LED-display.
+
T1
T1
T2
Set sensor close window
T2
margin in mm or cm
Set sensor-distant window
T1
T1
T2
margin in mm or cm
Choose rising « » / falling « »
T2
output characteristic curve
T2
T1 + T2
Ready
T1
Note
Changes in the Add-on
menu may impair the sensor
function.
A6, A7, A8 , A10 , A11, A12
have influence on the response time of the sensor.
T2
T1 + T2
Ready
T1
T1 + T2
T1
T1
No function! No function!»F00«: no filter
Low power mode Display mode Measurement filter Filter strength Foreground
T1
T2
T1 + T2
T2
T1
No function! No function! Minimum value: sen-
T2
T2
T1
T1 + T2
T1
»Aut«: automatic detection of the load
»U«: voltage output
»I«: current output
Choose current/
voltage output
T2
T2
T1
T1
T1 + T2
T2
»F01«: standard filter
»F02«: averaging filter
»F03«: foreground filter
»F04«: background
filter
T1
T1
T2
Defines the strength
of the chosen filter.
»P00«: weak filter up
to
»P09«: strong filter
T1 + T2
T1
T2
T1
T2
T1 + T2
T2
Delay in seconds between the detection of
an object and the output of the measured
distance in case of object approach (behaves as on-delay).
"00": 0 s (no delay)
up to
"20": 20 s response
time
Response time
SENSORPARTNERS.COM
T1
T1
T2
Minimum value: blind
zone
Maximum value: nearwindow limit - 1
T1 + T2
suppression
T2
T2
T1
T1 + T2
T1
Multiplex mode
device addressing
T2
T2
T1
T1 + T2
T1
Multiplex highest
device address
T2
T2
T1
T1 + T2
T1
sor-distant window
margin
Maximum value: 999
mm for mic+
25/...,mic+35/...,
999 cm for mic+
130/...,mic+340/...,
mic+600/...
Measurement range
T2
T1
T2
Affects the size of the
detection zone.
»E01«: high
»E02«: standard
»E03«: slight
T1
T1 + T2
Detection zone
sensitivity
T2
T2