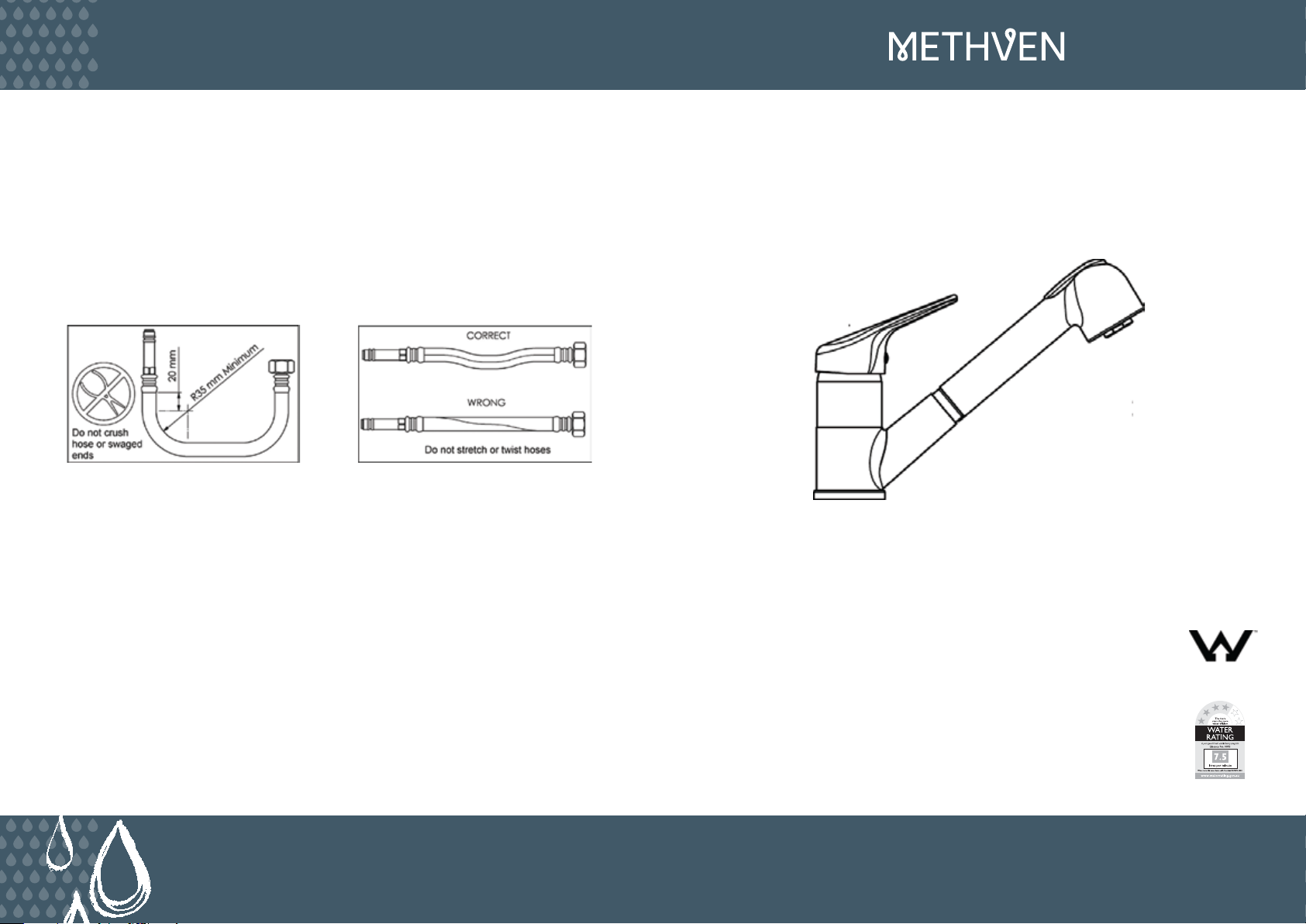
Futura Sink Mixer
Hose Requirements for mixers
The maximum working pressure of the ceramic cartridge is 1000kPa.
Do not hydrostatic test the installation with this mixer installed. Damage to
the ceramic cartridge may occur.
with Pullout Spray
02-4353
Illustration may not reflect actual product shape.
Installation Guide
“In situ” testing
The maximum working pressure of the ceramic cartridge is 1000kPa. Do not
hydrostatic test the installation with this mixer installed. Damage to the ceramic
cartridge may occur, voiding our warranty.
FEB 2009 MA433082
Methven Australia Pty Ltd
ABN 15 104 813 390
Melbourne, Australia
www.methven.com
IMPORTANT
Please read all of the instructions before installation
Use of this product in non-domestic applications voids warranty.
All pipe work must be thoroughly flushed prior to the installation of the mixer.
NEFA inline filters must be installed on both hot and cold supplies.
Do not remove the ceramic cartridge from the mixer when installing.
Damage caused by hydrostatic testing is not covered by our warranty.
www.methven.com
Spec 001
LN: WMKA21005

Technical Specifications
Installation
Inlet Connections: All 1/2’ BSP
Operating Pressure: 150kPa - 500kPa
Operating Temperatures: Recommended hot water supply 50°C,
maximum 70°C. AS 3500 requires all hot
water supplies to any sanitary fitting to be
tempered to 50°C.
1. Cut a 40mm diameter hole through the bench top. Ensure the thickness of the
bench top does not exceed 30mm.
2. Remove the rubber seal washer and brass lock nut.
3. Fit the ‘o’ ring sealing washers (provided in a separate bag) over the tail pipes and
push it up to fit against the underside of the sink faucet.
4. Secure the ‘hot’ hose into the left hand of the two shorter pipes when viewed from
the front. Secure the ‘cold’ hose into the right hand of the two shorter pipes when
viewed from the front.
5. Place the mixer body and hoses through the hole cut in the bench top. (NB: The
hoses will need to be placed through the holes one at a time).
6. Place the rubber seal washer over the hoses to form a seal on the underside of the
bench.
7. Secure the faucet in place using the brass backnut, against the underside of the
bench.
8. Screw the pull out spray handpiece into the conical end of the spray hose, ensuring
firm seal is made with the sealing washer within the hose’s conical end fitting.
9. Place the smaller threaded end of the pull out spray hose through the faucet spout
opening. Push the hose down the spout and through the faucet body until it exits
out the bottom of the faucet next to the hot and cold hoses. Continue pushing the
hose through the faucet body until the pull out spray handpiece engages in the
spout opening.
10. Screw the spray hose connection into the remaining pipe connection, ensuring the
small rubber sealing washer provided in the bag is fitted in the remaining pipe
connection to form a water tight seal.
11. Attach the lead weight to the spray hose using the screws provided. The screws are
used to assemlbe the two halves of the lead weight around the hose. The optimum
position for the lead weight is at the bottom of the front loop of the spray hose
12. Flush pipework thoroughly.
13. Connect the hoses to their respective water supplies (see over page). Two rubber
washers are provided for the flexible hose supply connections. Machined nipple
ends are required to ensure a seal to the flexible hose nuts and the rubber washers.
We recommend that this product is installed by a licensed plumber.
THE METHVEN GUARANTEE
The warranty statement shall apply to all tapware & showers supplied by Methven
For more information visit www.methven.com
THIS WARRANTY ISSUED BY: Methven Australia Pty Ltd, Melbourne Australia