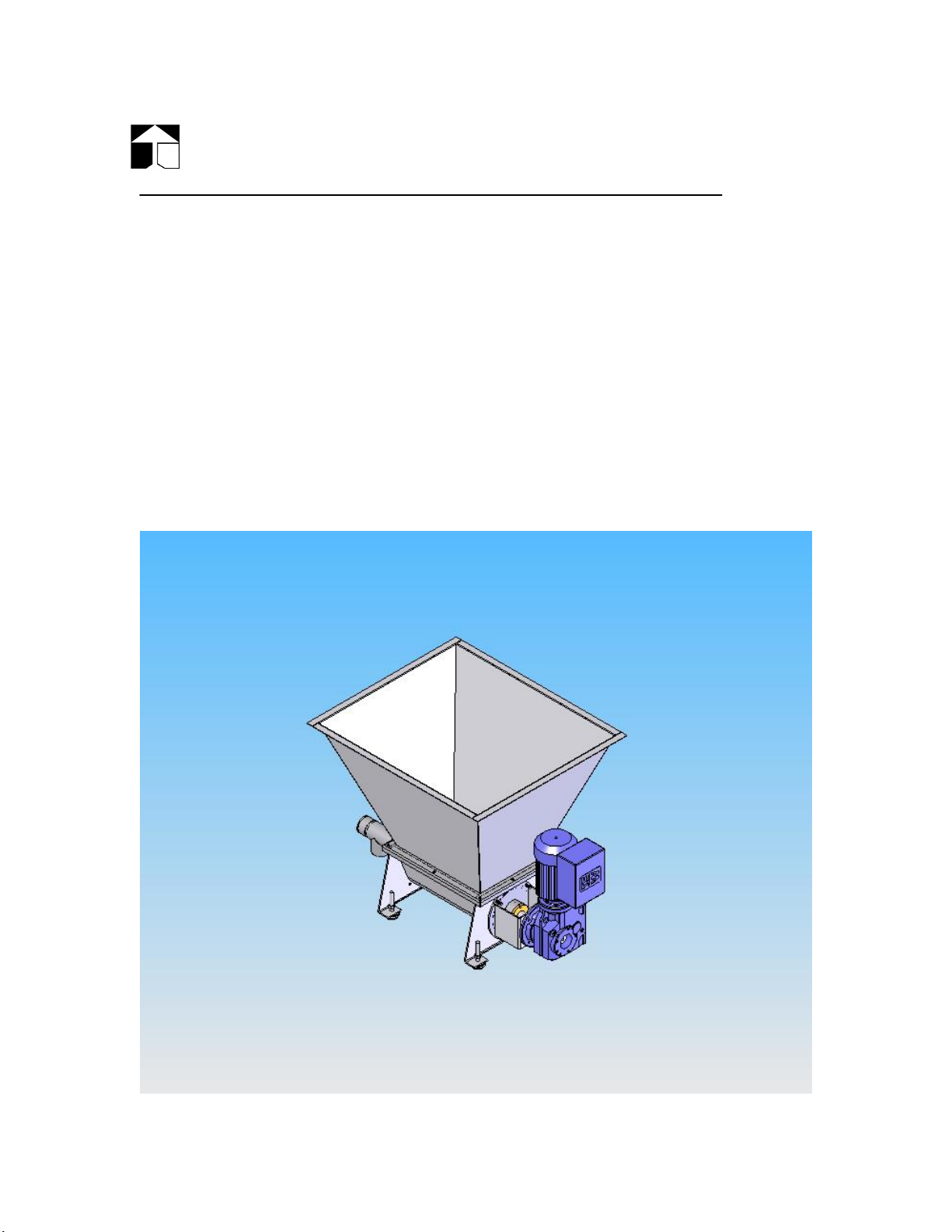
MMetalfab, Inc.
Dry Solids Processing Equipment
P.O. BOX 9, PRICES SWITCH ROAD, VERNON, NEW JERSEY 07462 ♦ 973-764-2000 ♦ FAX # 973-764-0272
INSTRUCTIONS FOR OPERATION & MAINTENANCE
MetaTech MT-X-XXX Series
VOLUMETRIC SCREW FEEDER
Fig A.
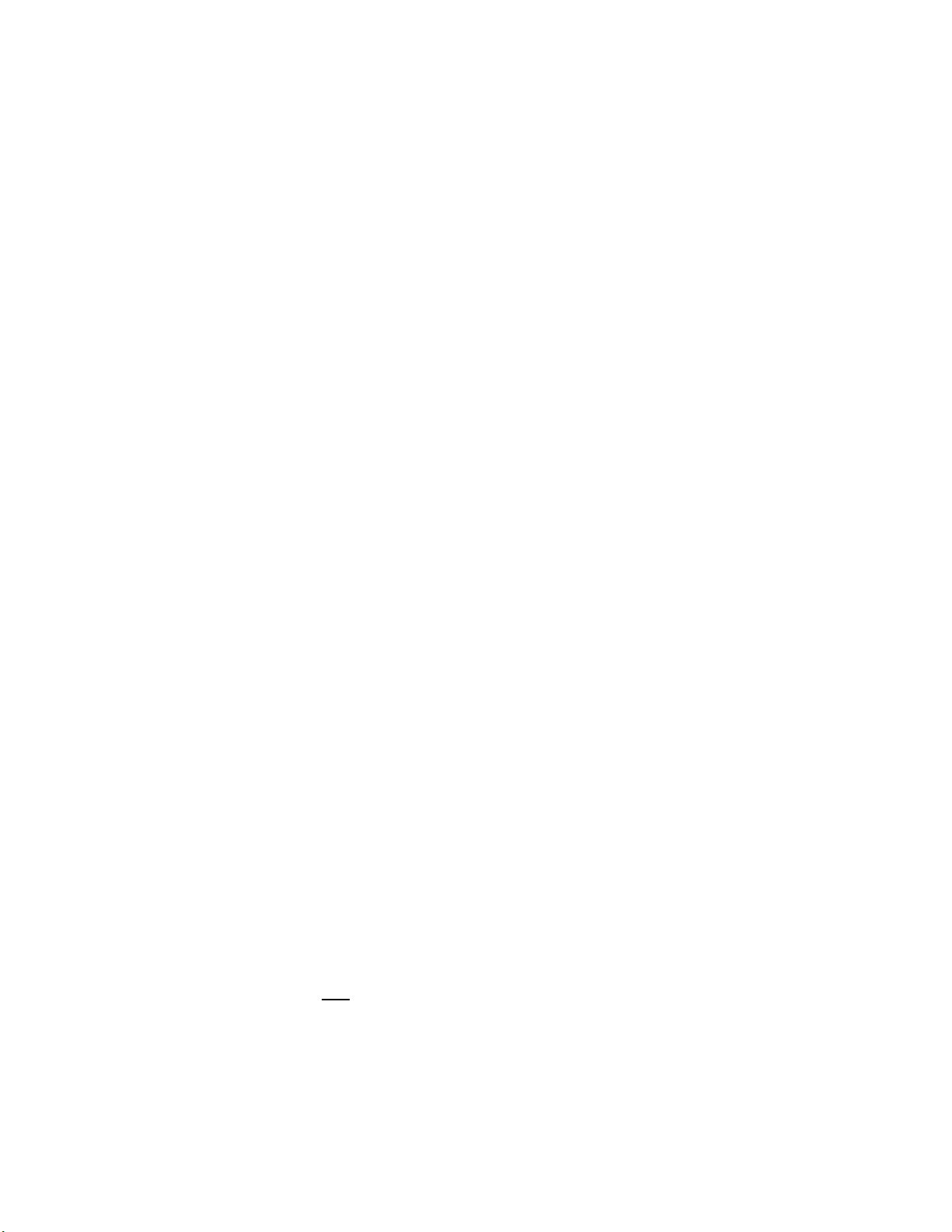
The MetaTech Feeder is a simple, rugged and accurate Volumetric Feeder used
for the dependable metering of dry solid materials into a variety of
manufacturing processes. It consists of a trough assembly. a hopper in various
capacities, a GearMotor Drive (which is available in many input power
configurations and ratios), a Metering Screw and Tube in sizes and styles to fit
the application. The metering screw is coupled to the variable speed drive,
either AC with a VFD or DC with an SCR; all mounted on the trough assembly
with isolation feet mounts or mounted to a custom frame.
The steep, sloped hopper, with its large rectangular outlet, allows for material
flow to the metering screw. The metering screw consists of three spiral wraps,
the largest being the agitator which assists the motion of produce within the
trough, the mid sized The function of this screw is to keep the material in motion
and also "condition" the material to a constant density while insuring complete
filling of the metering screw flights. Hence, accuracy is maintained while rates
are varied by screw speed changes.
Installation
The MetaTech Feeder is shipped complete and ready for operation. For
enhanced safety, the unit should be bolted in place, absent this there are four
(4) levelers positioned under the base which are equipped with rubber pads.
Room should be provided at the discharge end to allow for screw removal.
Normally, 20" clearance is sufficient.
Electrical Requirements
Standard units are provided with AC Inverter Duty Drives which can have their
own VFD controllers mounted integral to the motor housing or stand alone
VFDÅfs of the Customer specification. Typical VFDÅfs capable of varying output
frequency from 0 to 100 Hz, minimum operation at 5 hz is recommended for
adequate cooling. The controller may be mounted at the Feeder location or
remotely. SEW Eurodrive Inverter Manual and DC SCR Control Manuals are
attached at the end of this manual. All standard motors are TEFC (totally
enclosed, fan cooled), severe heat applications may require TEBC (blower
cooled) models which will require a separate power input for the blower.
Inverter Duty Motors are dual voltage 230/460 three phase. Inverter Drives
(VFDÅfs) are 230 vac OR 460 vac models special applications for single phase
input power can be accommodated as can 380vac, 575vac and 50Hz models;
contact Metalfab Inc. for these special applications and consult Inverter Drive
Manuals and for specifications. For amperage considerations 460/3 motors will
draw 1 amp per Hp and should be equipped with supply capacity 2X this nominal
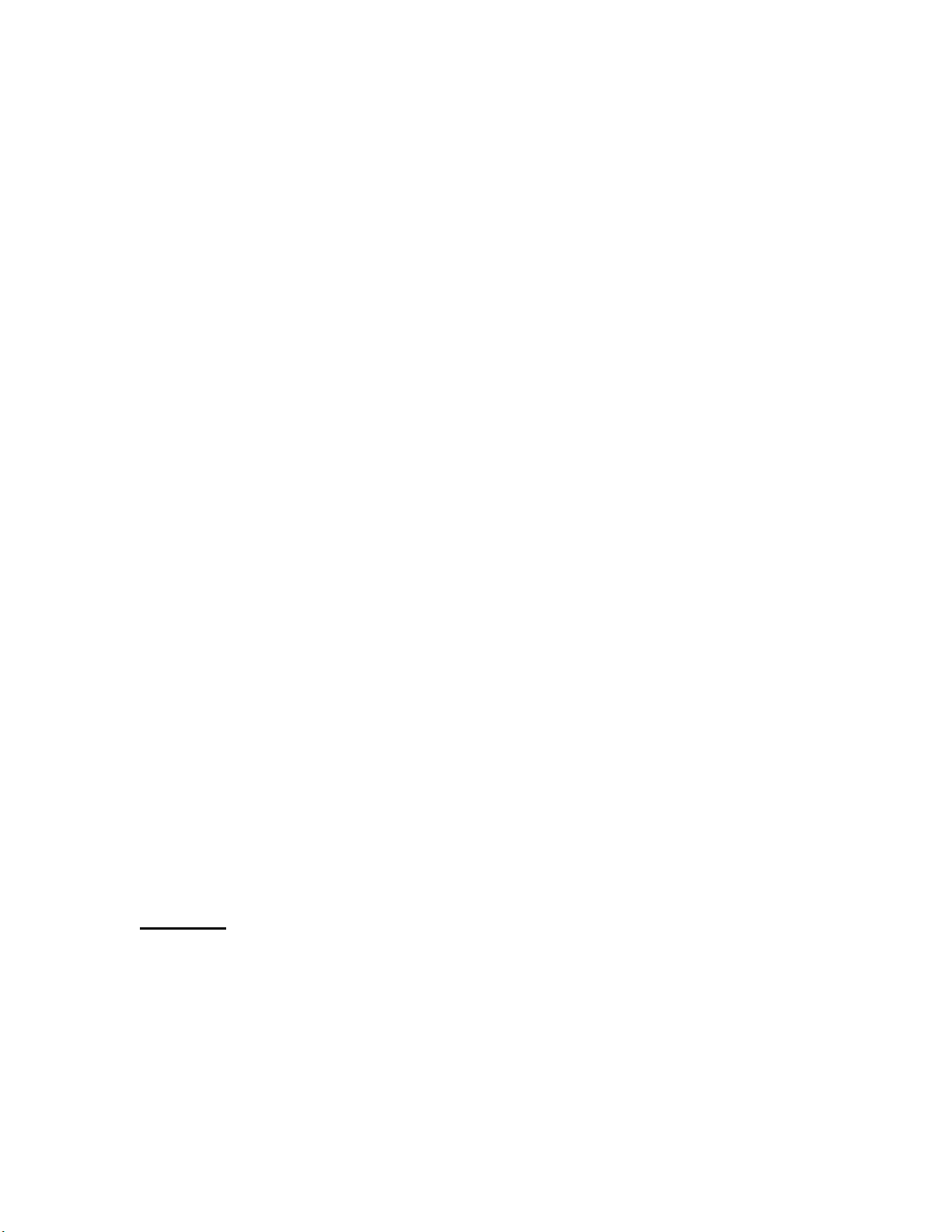
amperage for inrush consideration. 230/3 models will draw exactly double the
460/3 ratings.
DC Motors are available with field windings (shunt wound) or permanent
magnet, both are available in 90vdc (std _ Hp) and 180vdc (std 1Hp) armatures.
DC motor speed is modulated by varying the armature voltage from 0 to max,
15% speed should be considered the min speed for motor cooling considerations
Operation
After the Feeder is in place and wired, it is ready for operation. Units equipped
with electrically variable speed drives can have their speed adjusted at anytime,
i.e., with the unit stopped or in motion. The dial provides for setting screw
speeds to 1 part in 100. Speed is increased by turning the potentiometer in
clockwise rotation. Optional digital keypads for Local/Remote operation are
available, again consult the feeder specification and pricing sheets for options.
The hopper should be filled with the feed material and the potentiometer should
be set to 50%. The unit should be allowed to run for 5 minutes before a 1
minute sample is collected and weighed. It is suggested that 5 or more samples
be taken to assure the Feeder is operating properly. Once the feed rate is
known at 50%, the required rate may then be obtained by proper speed change.
The drive and, therefore, the feed rates are linear, hence, at setting of 50% the
Feeder will be operating at approximately half capacity. As an example, if at a
50% setting a 20#/minute rate is achieved and a 10#/minute rate is desired,
change the setting to 25% and a 10#/minute rate will be delivered. Take
samples at 3 or 4 settings and plot a graph, setting versus rate. From this
graph, any feed rate may be selected. This calibration should be done at the
end user application as material bulk density and condition due to prior steps in
the process will have an impact on the ÅgActual Discharge RatesÅh, approximate
rates are listed on the drawing on the final pages in the spare parts section of
this manual.
Warning: Keep hands clear of all moving parts. Serious injury can occur.