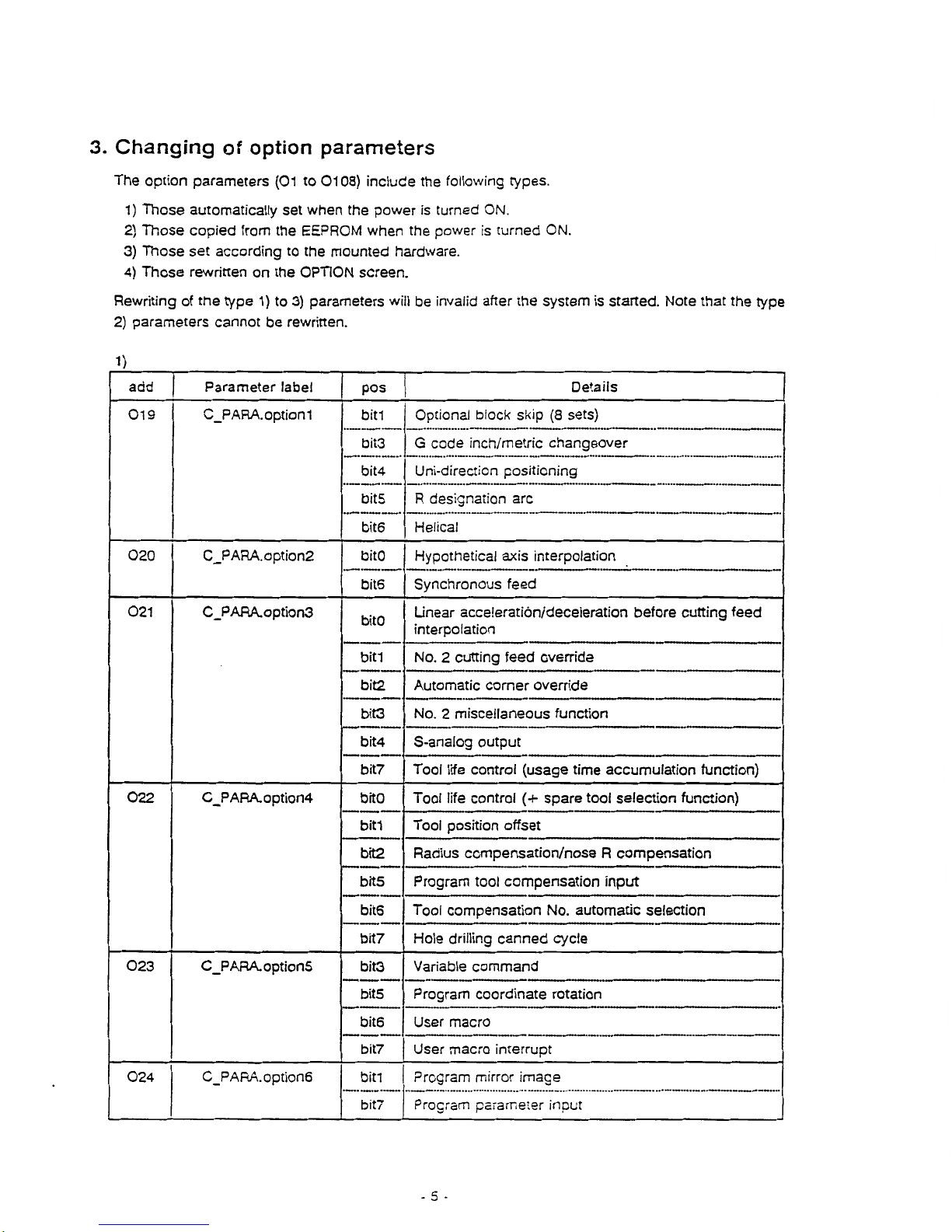
3.
Changing
of
option
parameters
The
option
parameters
(01
to
0108)
include
the
following
types.
1)
Those
automatically
set
when
the
power
is
turned
ON.
2)
Those
copied
from
the
EEPROM
when
the
power
is
turned
ON.
3)
Those
set
according
to
the
mounted
hardware.
4)
Those
rewritten
on
the
OPTION
screen.
Rewriting
of
the
type
1)to3)
parameters
will
be
invalid
after
the
system
is
started.
Note
that
the
type
2)
parameters
cannot
be
rewritten.
1)
Parameter
label
Details
add
pos
019
C_PARA.option1
Optional
block
skip
(8
sets)
bill
bit3
G
code
inch/metric
changeover
bit4
Uni-direction
positioning
bits
R
designation
arc
bit6
Helical
020
C_PARA.option2
bitO
Hypothetical
axis
interpolation
Synchronous
feed
bite
021
C_PARA.option3
Linear
acceleration/deceleration
before
cutting
feed
interpolation
bitO
bit1
No.
2
cutting
feed
override
bit2
Automatic
corner
override
bit3
No.2miscellaneous
function
bit4
S-analog
output
Tool
life
control
(usage
time
accumulation
function)
bit7
022
C_PARA.option4
Tool
life
control
(+
spare
tool
selection
function)
bitO
Tool
position
offset
bill
bit2
Radius
compensation/nose
R
compensation
Program
tool
compensation
input
bits
bite
Tool
compensation
No.
automatic
selection
Hole
drilling
canned
cycle
bit7
023
C_PARA.option5
Variable
command
bit3
bits
Program
coordinate
rotation
bit6
User
macro
User
macro
interrupt
bit7
024
C_PARA.option6
Program
mirror
image
bitl
Program
parameter
input
bit7
-5-