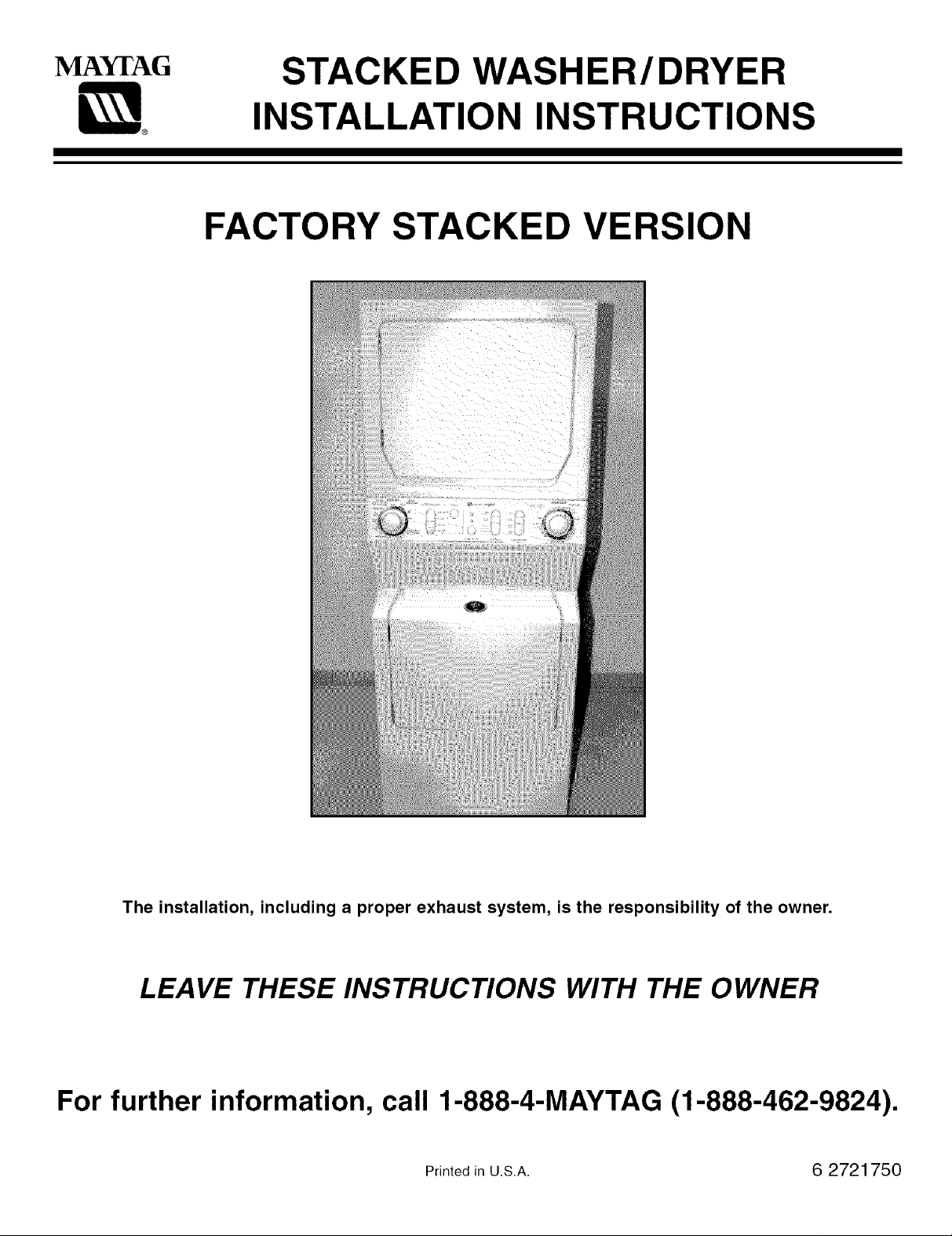
STACKED WASHER/DRYER
INSTALLATION INSTRUCTIONS
FACTORY STACKED VERSION
The installation, including a proper exhaust system, is the responsibility of the owner.
LEAVE THESE INSTRUCTIONS WITH THE OWNER
For further information, call 1-888-4-MAYTAG (1-888-462-9824).
Printed in U.S.A. 6 2721750
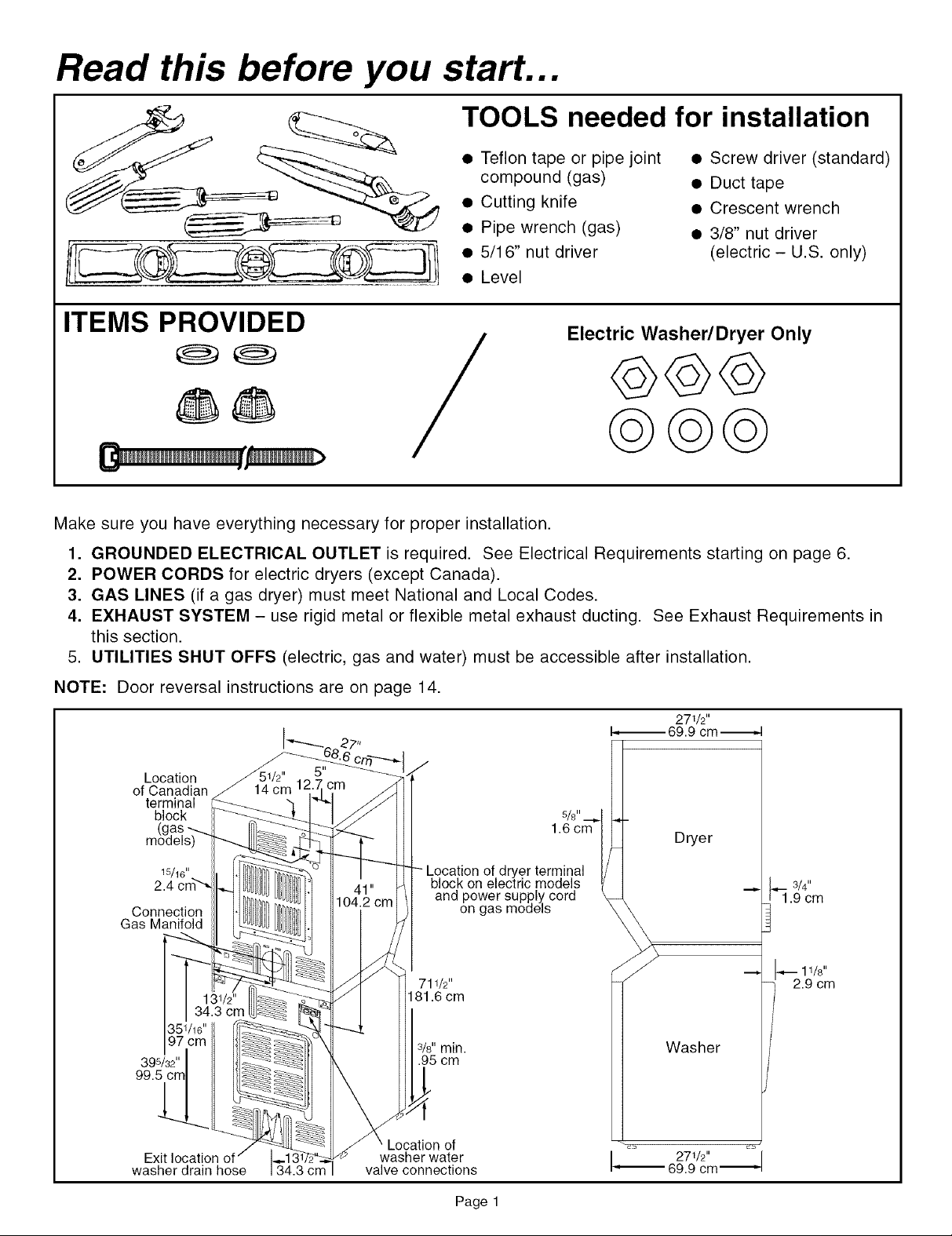
Read this before you start...
TOOLS needed for installation
• Teflon tape or pipe joint
compound (gas)
• Cutting knife
• Pipe wrench (gas)
• 5/16" nut driver
• Level
• Screw driver (standard)
• Duct tape
• Crescent wrench
• 3/8" nut driver
(electric - U.S. only)
ITEMS PROVIDED
Electric Washer/Dryer Only
@@
©©©
/
©©©
Make sure you have everything necessary for proper installation.
1. GROUNDED ELECTRICAL OUTLET is required. See Electrical Requirements starting on page 6.
2. POWER CORDS for electric dryers (except Canada).
3. GAS LINES (if a gas dryer) must meet National and Local Codes.
4. EXHAUST SYSTEM - use rigid metal or flexible metal exhaust ducting. See Exhaust Requirements in
this section.
5. UTILITIES SHUT OFFS (electric, gas and water) must be accessible after installation.
NOTE: Door reversal instructions are on page 14.
Location
of Canadian
terminal
block
Connection
Gas Manifold
711/2"
81.6 cm
3/8"min.
398/32"
99.5
Exit
washer drain hose
valve connections
.95 cm
Location of
washer water
I_ 69.9 cm -_,4
8/8"
1.6 cm Dryer
Loca!ion of,dryer terminal /
OIOCKon electric models
and power supply cord _ "-"
on gas models
l 69.9 cm "_
271/2"
Washer
271/2''
11/8"
2.9 cm
Page 1
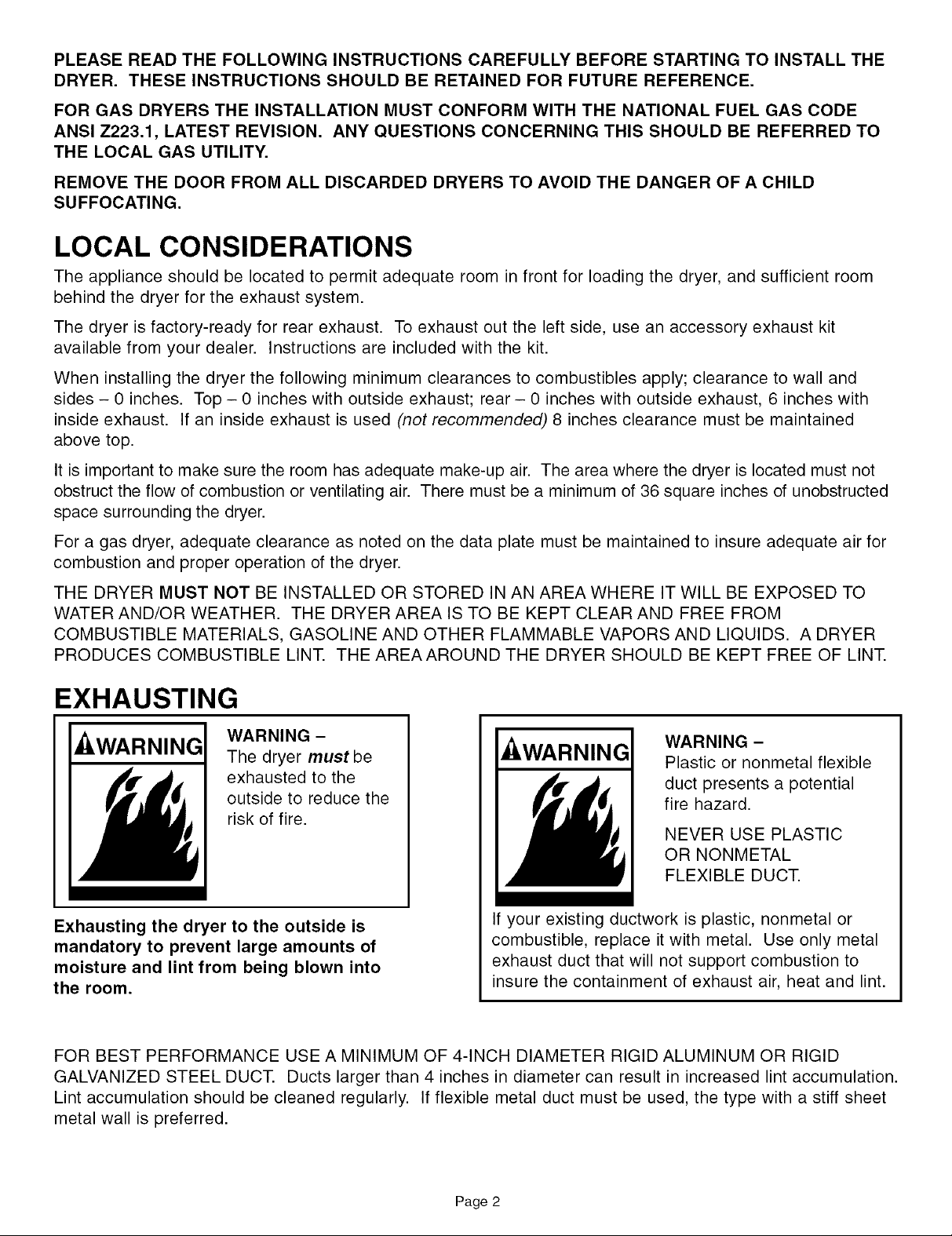
PLEASE READ THE FOLLOWING INSTRUCTIONS CAREFULLY BEFORE STARTING TO INSTALL THE
DRYER. THESE INSTRUCTIONS SHOULD BE RETAINED FOR FUTURE REFERENCE.
FOR GAS DRYERS THE INSTALLATION MUST CONFORM WITH THE NATIONAL FUEL GAS CODE
ANSI Z223.1, LATEST REVISION. ANY QUESTIONS CONCERNING THIS SHOULD BE REFERRED TO
THE LOCAL GAS UTILITY.
REMOVE THE DOOR FROM ALL DISCARDED DRYERS TO AVOID THE DANGER OF A CHILD
SUFFOCATING.
LOCAL CONSIDERATIONS
The appliance should be located to permit adequate room in front for loading the dryer, and sufficient room
behind the dryer for the exhaust system.
The dryer is factory-ready for rear exhaust. To exhaust out the left side, use an accessory exhaust kit
available from your dealer. Instructions are included with the kit.
When installing the dryer the following minimum clearances to combustibles apply; clearance to wall and
sides - 0 inches. Top - 0 inches with outside exhaust; rear - 0 inches with outside exhaust, 6 inches with
inside exhaust. If an inside exhaust is used (not recommended) 8 inches clearance must be maintained
above top.
It is important to make sure the room has adequate make-up air. The area where the dryer is located must not
obstruct the flow of combustion or ventilating air. There must be a minimum of 36 square inches of unobstructed
space surrounding the dryer.
For a gas dryer, adequate clearance as noted on the data plate must be maintained to insure adequate air for
combustion and proper operation of the dryer.
THE DRYER MUST NOT BE INSTALLED OR STORED IN AN AREA WHERE IT WILL BE EXPOSED TO
WATER AND/OR WEATHER. THE DRYER AREA IS TO BE KEPT CLEAR AND FREE FROM
COMBUSTIBLE MATERIALS, GASOLINE AND OTHER FLAMMABLE VAPORS AND LIQUIDS. A DRYER
PRODUCES COMBUSTIBLE LINT. THE AREAAROUND THE DRYER SHOULD BE KEPT FREE OF LINT.
EXHAUSTING
-&WARNING
Exhausting the dryer to the outside is
mandatory to prevent large amounts of
moisture and lint from being blown into
the room.
WARNING -
The dryer must be
exhausted to the
outside to reduce the
risk of fire.
-&WARNING
If your existing ductwork is plastic, nonmetal or
combustible, replace it with metal. Use only metal
exhaust duct that will not support combustion to
insure the containment of exhaust air, heat and lint.
WARNING -
Plastic or nonmetal flexible
duct presents a potential
fire hazard.
NEVER USE PLASTIC
OR NONMETAL
FLEXIBLE DUCT.
FOR BEST PERFORMANCE USE A MINIMUM OF 4-INCH DIAMETER RIGID ALUMINUM OR RIGID
GALVANIZED STEEL DUCT. Ducts larger than 4 inches in diameter can result in increased lint accumulation.
Lint accumulation should be cleaned regularly. If flexible metal duct must be used, the type with a stiff sheet
metal wall is preferred.
Page 2
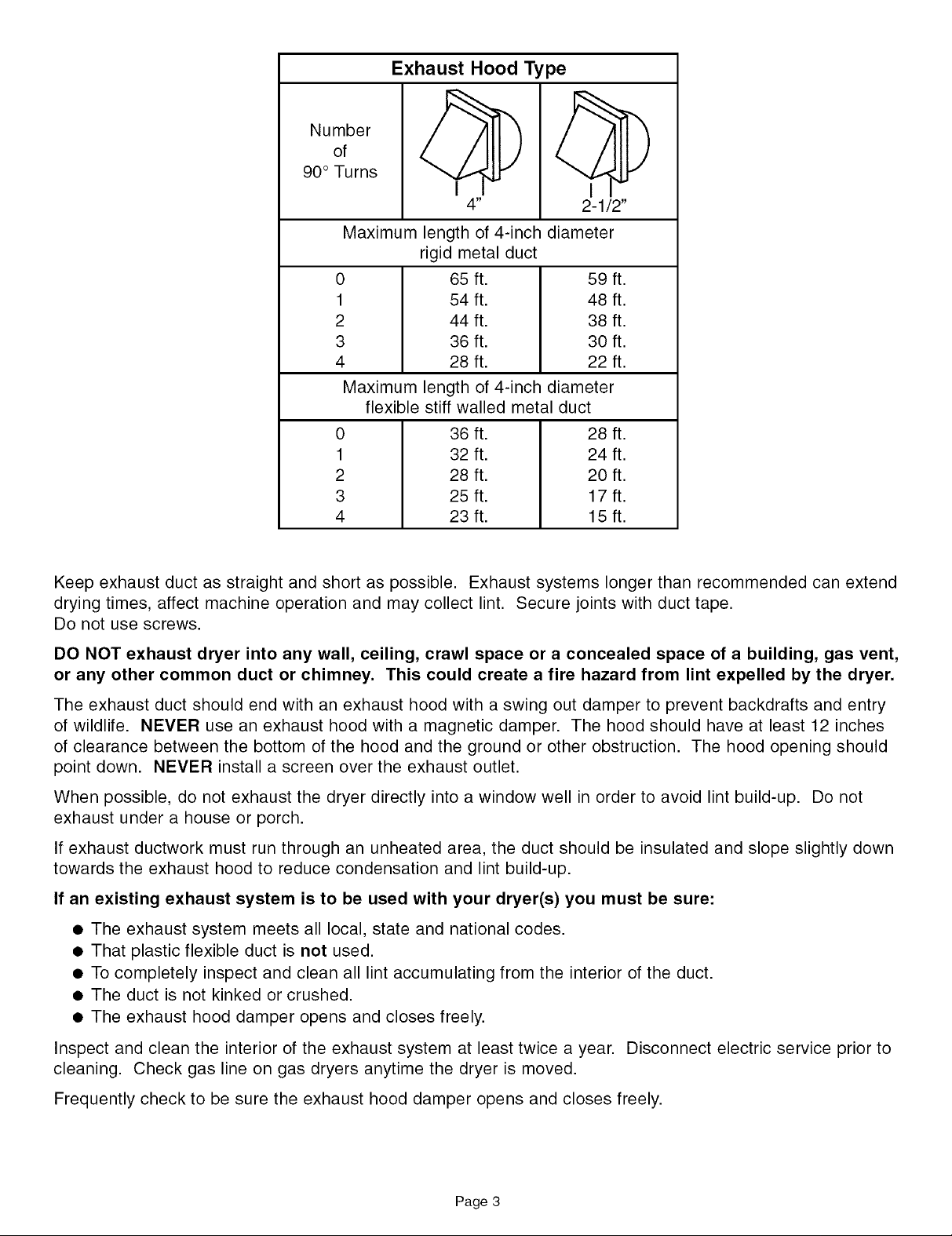
Exhaust Hood Type
Number
of
90 ° Turns
Maximum length of 4-inch diameter
rigid metal duct
0
1
2
3
4
Maximum length of 4-inch diameter
flexible stiff walled metal duct
0
1
2
3
4
65 ft.
54 ft.
44 ft.
36 ft.
28 ft.
36 ft. 28 ft.
32 ft. 24 ft.
28 ft. 2O ft.
25 ft. 17 ft.
23 ft. 15 ft.
59ft.
48 ft.
38 ft.
30 ft.
22 ft.
Keep exhaust duct as straight and short as possible. Exhaust systems longer than recommended can extend
drying times, affect machine operation and may collect lint. Secure joints with duct tape.
Do not use screws.
DO NOT exhaust dryer into any wall, ceiling, crawl space or a concealed space of a building, gas vent,
or any other common duct or chimney. This could create a fire hazard from lint expelled by the dryer.
The exhaust duct should end with an exhaust hood with a swing out damper to prevent backdrafts and entry
of wildlife. NEVER use an exhaust hood with a magnetic damper. The hood should have at least 12 inches
of clearance between the bottom of the hood and the ground or other obstruction. The hood opening should
point down. NEVER install a screen over the exhaust outlet.
When possible, do not exhaust the dryer directly into a window well in order to avoid lint build-up. Do not
exhaust under a house or porch.
If exhaust ductwork must run through an unheated area, the duct should be insulated and slope slightly down
towards the exhaust hood to reduce condensation and lint build-up.
If an existing exhaust system is to be used with your dryer(s) you must be sure:
• The exhaust system meets all local, state and national codes.
• That plastic flexible duct is not used.
• To completely inspect and clean all lint accumulating from the interior of the duct.
• The duct is not kinked or crushed.
• The exhaust hood damper opens and closes freely.
Inspect and clean the interior of the exhaust system at least twice a year. Disconnect electric service prior to
cleaning. Check gas line on gas dryers anytime the dryer is moved.
Frequently check to be sure the exhaust hood damper opens and closes freely.
Page 3
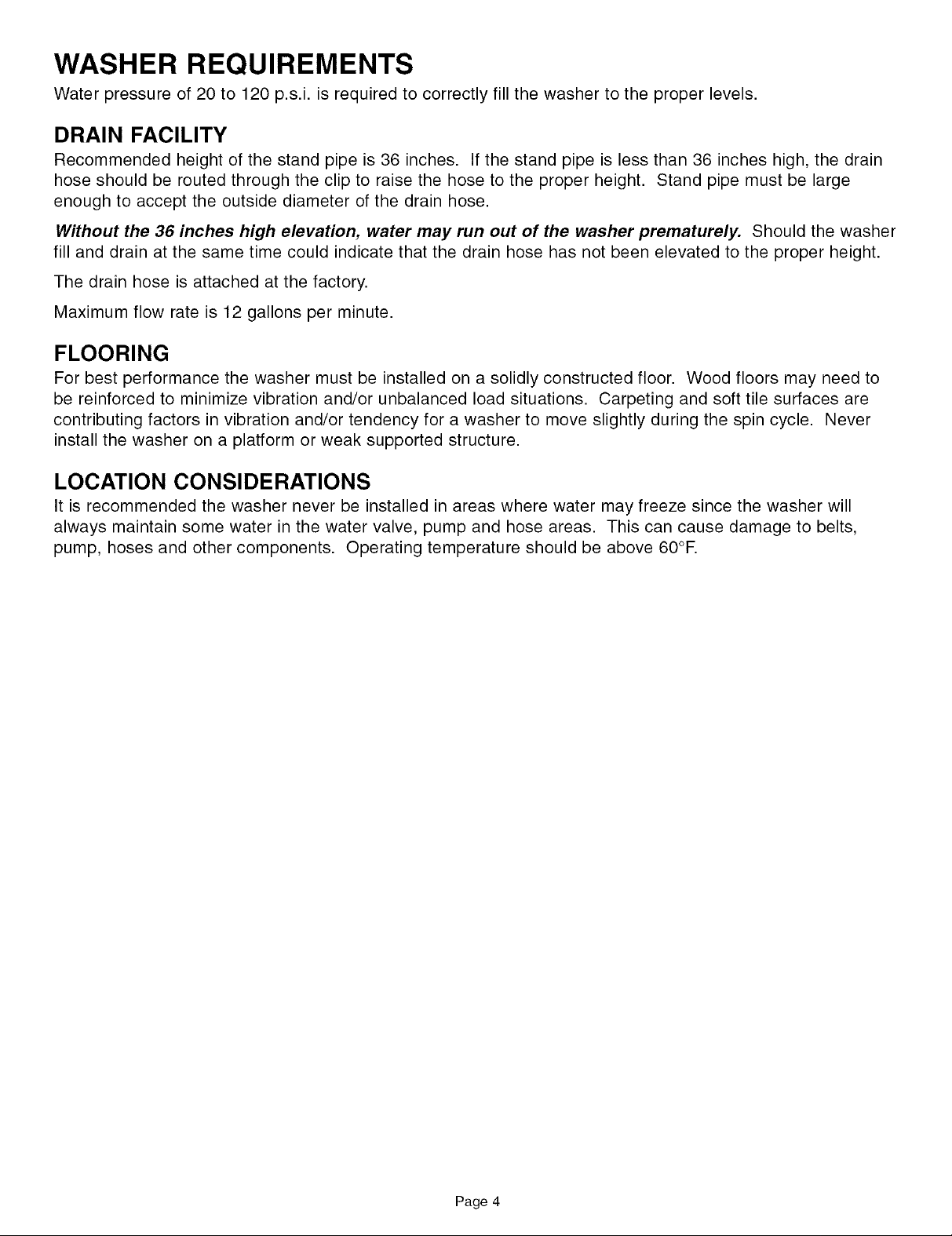
WASHER REQUIREMENTS
Water pressure of 20 to 120 p.s.i, is required to correctly fill the washer to the proper levels.
DRAIN FACILITY
Recommended height of the stand pipe is 36 inches. If the stand pipe is less than 36 inches high, the drain
hose should be routed through the clip to raise the hose to the proper height. Stand pipe must be large
enough to accept the outside diameter of the drain hose.
Without the 36 inches high elevation, water may run out of the washer prematurely. Should the washer
fill and drain at the same time could indicate that the drain hose has not been elevated to the proper height.
The drain hose is attached at the factory.
Maximum flow rate is 12 gallons per minute.
FLOORING
For best performance the washer must be installed on a solidly constructed floor. Wood floors may need to
be reinforced to minimize vibration and/or unbalanced load situations. Carpeting and soft tile surfaces are
contributing factors in vibration and/or tendency for a washer to move slightly during the spin cycle. Never
install the washer on a platform or weak supported structure.
LOCATION CONSIDERATIONS
It is recommended the washer never be installed in areas where water may freeze since the washer will
always maintain some water in the water valve, pump and hose areas. This can cause damage to belts,
pump, hoses and other components. Operating temperature should be above 60°F.
Page 4
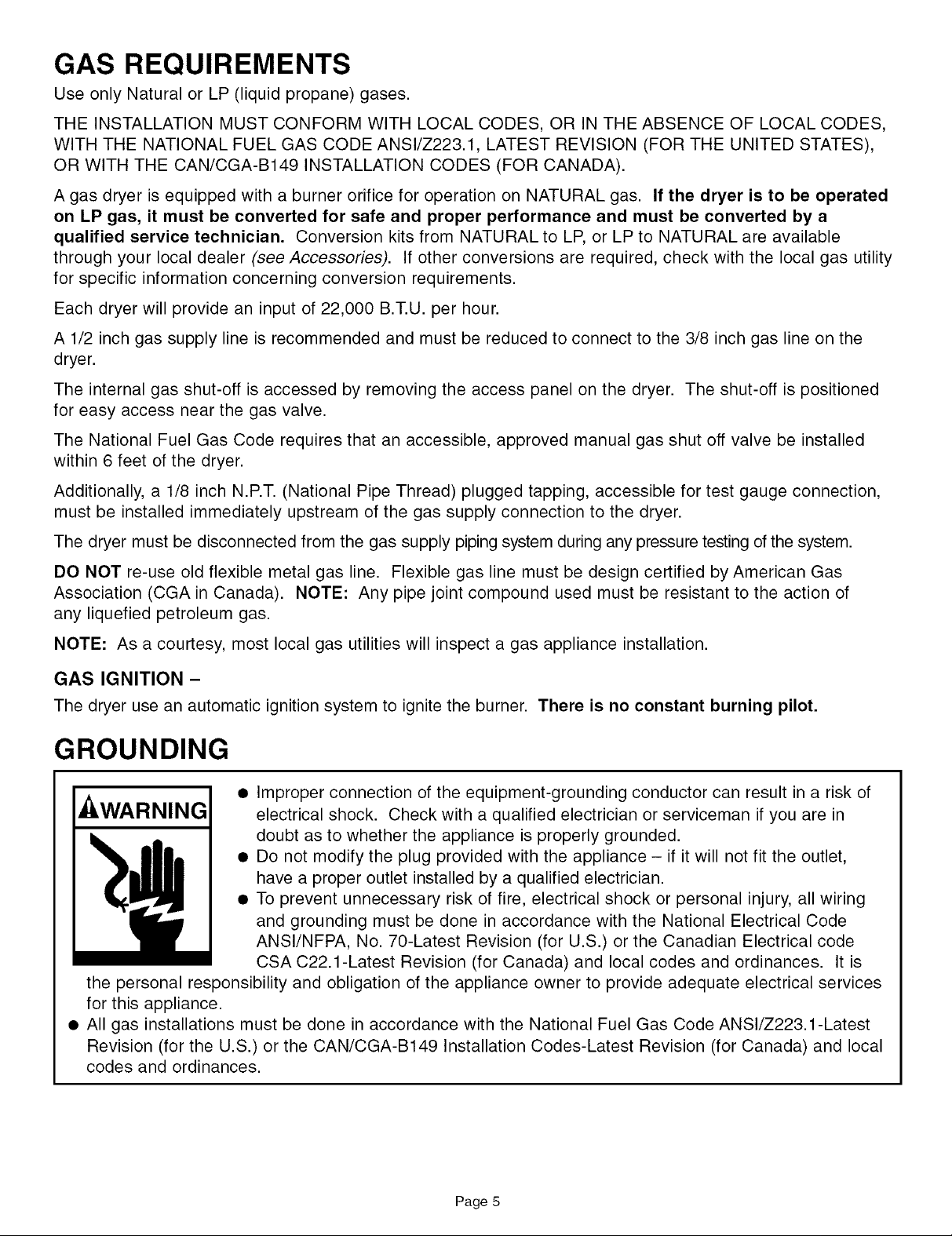
GAS REQUIREMENTS
Use only Natural or LP (liquid propane) gases.
THE INSTALLATION MUST CONFORM WITH LOCAL CODES, OR IN THE ABSENCE OF LOCAL CODES,
WITH THE NATIONAL FUEL GAS CODE ANSI/Z223.1, LATEST REVISION (FOR THE UNITED STATES),
OR WITH THE CAN/CGA-B149 INSTALLATION CODES (FOR CANADA).
A gas dryer is equipped with a burner orifice for operation on NATURAL gas. If the dryer is to be operated
on LP gas, it must be converted for safe and proper performance and must be converted by a
qualified service technician. Conversion kits from NATURAL to LP, or LP to NATURAL are available
through your local dealer (see Accessories). If other conversions are required, check with the local gas utility
for specific information concerning conversion requirements.
Each dryer will provide an input of 22,000 B.T.U. per hour.
A 1/2 inch gas supply line is recommended and must be reduced to connect to the 3/8 inch gas line on the
dryer.
The internal gas shut-off is accessed by removing the access panel on the dryer. The shut-off is positioned
for easy access near the gas valve.
The National Fuel Gas Code requires that an accessible, approved manual gas shut off valve be installed
within 6 feet of the dryer.
Additionally, a 1/8 inch N.ET. (National Pipe Thread) plugged tapping, accessible for test gauge connection,
must be installed immediately upstream of the gas supply connection to the dryer.
The dryer must be disconnected from the gas supply piping system during any pressure testing of the system.
DO NOT re-use old flexible metal gas line. Flexible gas line must be design certified by American Gas
Association (CGA in Canada). NOTE: Any pipe joint compound used must be resistant to the action of
any liquefied petroleum gas.
NOTE: As a courtesy, most local gas utilities will inspect a gas appliance installation.
GAS IGNITION -
The dryer use an automatic ignition system to ignite the burner. There is no constant burning pilot.
GROUNDING
• Improper connection of the equipment-grounding conductor can result in a risk of
WARNING electrical shock. Check with a qualified electrician or serviceman if you are in
doubt as to whether the appliance is properly grounded.
• Do not modify the plug provided with the appliance - if it will not fit the outlet,
have a proper outlet installed by a qualified electrician.
• To prevent unnecessary risk of fire, electrical shock or personal injury, all wiring
and grounding must be done in accordance with the National Electrical Code
ANSI/NFPA, No. 70-Latest Revision (for U.S.) or the Canadian Electrical code
CSA C22.1-Latest Revision (for Canada) and local codes and ordinances. It is
the personal responsibility and obligation of the appliance owner to provide adequate electrical services
for this appliance.
• All gas installations must be done in accordance with the National Fuel Gas Code ANSI/Z223.1-Latest
Revision (for the U.S.) or the CAN/CGA-B149 Installation Codes-Latest Revision (for Canada) and local
codes and ordinances.
Page 5