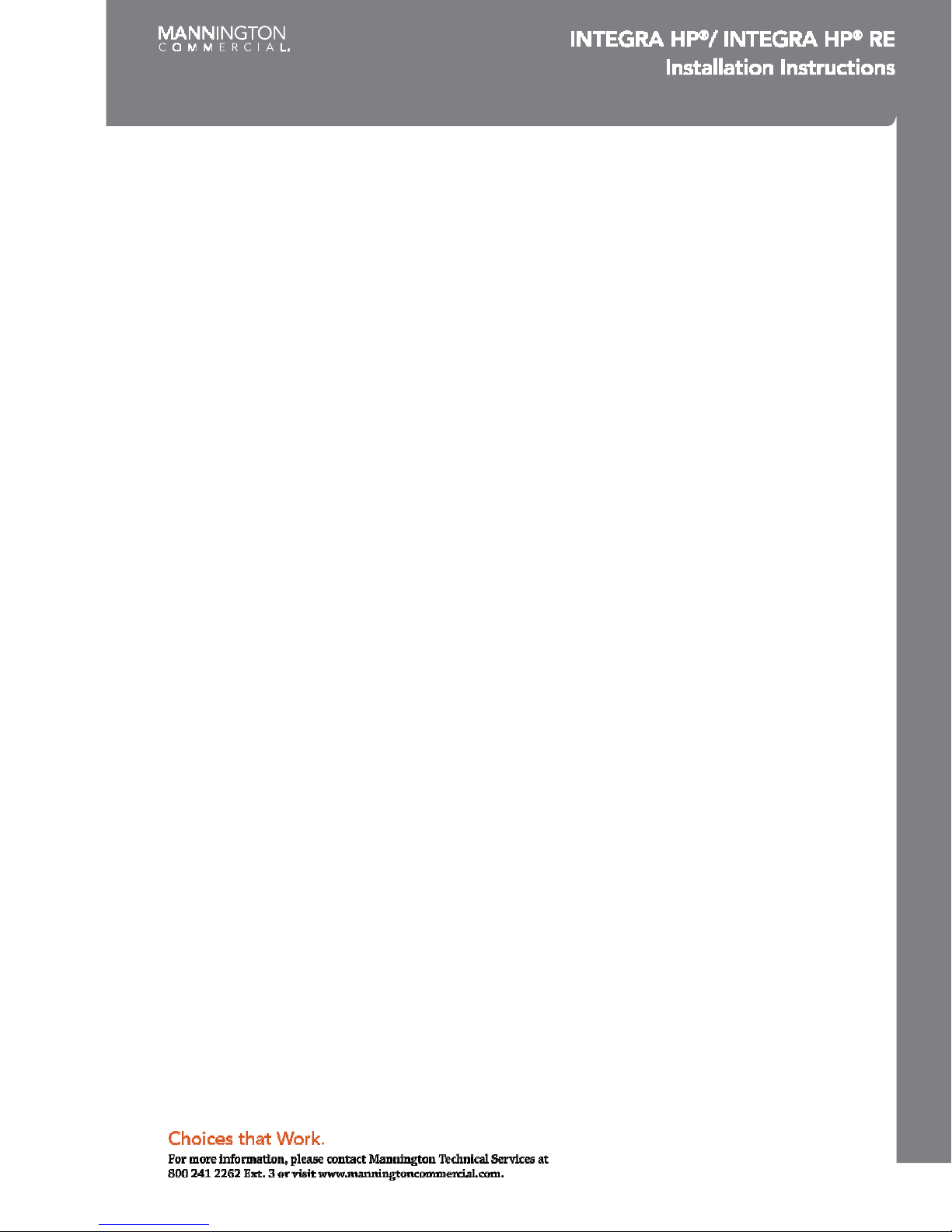
GENERAL INFORMATION
Integra HP® and Integra HP® RE are Mannington Commercial’s high performance integrated backing systems for broadloom
carpet. Mannington adheres to the Carpet and Rug Institute’s (CRI) Installation Standard which details minimum
requirements for site conditions, floor preparation and installation. Mannington’s Installation Guide provides additional
details specifically for carpet styles with Integra HP backings. These details are necessary to help assure a successful
installation with full warranty coverage.
MANNINGTON OFFERS TWO OPTIONS FOR IN-SLAB MOISTURE CONCERNS
OPTION 1:
Requires full range of ASTM moisture and pH testing, but does not require the use of Mannington’s Universal Primer.
OPTION 2:
subfloor chemical pH is 9 or lower.
Before starting the installation you must first determine which option is best for your specific project. Select Option 1 or 2
and then proceed to site condition.
SUBFLOOR TESTING FOR OPTION 1
Concrete subfloors must be tested in accordance with ASTM protocol to determine whether chemical pH and moisture
emission levels are suitable. Test methods, locations and results must be fully documented for future reference.
Independent certification is recommended. Results should be as follows for full warranty coverage.
•
pH test, ASTM F-710, should be 9 or less.
•
Relative Humidity, ASTM F-2170 is the preferred method and should be 85 percent or less.
•
Calcium Chloride, ASTM F-1869, should be 8 pounds or less.
SUBFLOOR TESTING FOR OPTION 2
Integra HP backing installations using Mannington’s Universal Primer, Integra 2 wet set adhesive and MT-800 seam sealer
will no longer require moisture vapor emission rate (MVER) or Relative Humidity (RH) testing, but only when meeting the
following conditions.
•
No free liquids present.
•
No evidence of moisture staining.
•
pH is 9 or less. pH tests are required for all installations of Integra HP backings.
Requires the use of Mannington’s Universal Primer, but eliminates the need for concrete moisture testing when
Note: Testing must show the concrete surface has a chemical pH of 9.0 or lower at the time of installation and must
maintain a pH of 9.0 or lower throughout the life of the carpet. Experience has shown that test accuracy is improved for
moisture vapor emission, Relative Humidity and chemical pH when temperature and humidity levels are maintained within
ranges expected during occupancy for two full weeks prior to testing. Even so, these tests indicate moisture and pH
levels only at time of testing. Moisture and pH levels can increase over time. Mannington is not responsible for product or
installation failures caused by such changes in subfloor conditions occurring after installation.
SITE CONDITIONS: Regardless of option chosen for moisture warranty, these conditions and standards must also be met.
•
Integra HP should not be used on concrete slabs that do not have a vapor retardant membrane properly placed below
the concrete slab.
•
Control the environment. The building should be fully enclosed with an HVAC system functioning to maintain temperature
within a range similar to when space is occupied.
•
Maintain temperature between 60-85 degrees Fahrenheit with ambient humidity between 40-60 percent for 48-72 hours
before, during and after installation.
•
Levelness of finish. Must meet or exceed American Concrete Institute standards, ACI 301.
•
Use only leveling compounds containing Portland based cement. Latex is included in some levelers and should be mixed
with water according to manufacturer’s instructions. Avoid all Gypsum based patching compounds.
•
Curing agents. Mechanically remove any concrete curing agent determined incompatible with adhesives or sealers
required for installing HP backed carpets. Many concrete curing compounds can inhibit or prevent an adhesive from
developing an adequate bond with the subfloor. If concrete curing agents have been used, determine whether that
specific curing agent is compatible with sealers and adhesives necessary for the installation. Determining compatibility
may require involving manufacturers of each product.
•
Chemical removers. Avoid using chemical agents to remove curing compounds or old adhesives. That includes citrus
based removers. These solvents can absorb into the subfloor and prevent an adequate bond with sealer or adhesives.
TESTING FOR SUBFLOOR pH: All concrete subfloors must be tested for pH and found to have a pH range of 9 or less
before starting the installation. The test must be performed on bare concrete surface according to standards set in ASTM
F-710 with careful attention to the following:
•
Clean test site. Mechanically clean away adhesives, primers, curing compounds and contaminants to expose the thin
carbonation layer on the concrete surface.
January, 2018

•
Caution: Over cleaning or scraping can remove or damage the thin carbonation layer and cause higher pH readings.
•
Slightly wet the prepared site with a small amount of distilled water and allow the water to stand for one minute.
•
Apply pH test strips or pH meter to the wet concrete surface and leave intact for one full minute so the test paper can
absorb some of the distilled water.
•
The pH test strip will change colors depending upon the pH of the concrete.
LOWERING pH LEVELS: Mannington Commercial Premium Universal Primer is required for all Option 2 installations of HP
backings but can be applied to lower chemical pH levels to 9 or below as required. Primer should be applied and pH
retested as follows:
•
Universal Primer can be applied by pouring directly on the subfloor and spreading evenly with a broom or paint roller.
Primer can also be applied with a garden sprayer, an airless rig or similar spray equipment.
•
pH can be retested after subfloor has fully dried (no transfer when touched). If pH is still testing above 9, a second
application will be necessary.
•
All patched areas must receive a full application of Universal Primer.
•
Coverage is approximately 350-400 square feet per gallon.
Note: Primer required. Mannington Commercial Premium Universal Primer is required for all Option 2 installations of HP
backings on concrete when pH levels are ≤ 9 and no moisture tests are performed. Regardless of installation Option all
patched areas must receive a full application of Mannington’s Universal Floor Primer as well as any subfloor that is
porous, gritty, chalky or dusty. Excessively porous subfloors or those with chemical pH above 9 may require a second
application. Allow the primer to dry completely prior to second application or before applying adhesive. Primer is dry if
there is no transfer when touched.
ADDITIONAL SUBFLOOR TYPES: Any subfloor surface must be smooth, level, clean, and secure prior to installing carpets
with Integra HP backing.
•
Wooden planks. Wooden plank flooring will not provide a stable subfloor and must be covered with a suitable
underlayment such as plywood.
•
Plywood. Make certain plywood is recommended for use as a subfloor underlayment. Plywood seams may also need to be
sanded flat and smooth. Bare wood or plywood subfloors should be sealed with a latex primer.
•
Treated plywood. Chemicals designed to suppress fire or described as a fire retardant in wooden or plywood
underlayment will react with adhesives. Flame suppressing or fire retardant plywood is not recommended as a
suitable underlayment.
•
Terrazzo/marble. Level all grout lines. Glossy finishes may need to be sanded to provide a suitable surface.
•
Vinyl composition tile. Individual tiles must be solidly bonded to the subfloor or removed. Broken, damaged, or loose tiles
must be replaced. Remove any wax.
•
Sheet vinyl. Sheet vinyl is an unsuitable substrate and must be removed before installation.
•
Existing carpet. Existing carpet is an unsuitable substrate and must be removed.
OLD ADHESIVES:
scraped flat and thoroughly encapsulated with an approved sealant prior to introducing new adhesives. Otherwise, an
adverse reaction could occur, voiding applicable warranty coverage and leading to installation or product failure.
•
Multipurpose/pressure sensitive adhesives. Use one of the following methods to prevent possible reaction between the
existing adhesive and the new installation.
1.
Scrape adhesive flat and encapsulate with XL Brands TriSeal (800-367-4583) or equivalent.
2.
Thoroughly remove existing adhesive then skim coat with a Portland cement based patching compound.
•
Cutback adhesive. Wet with a mixture of water and a small amount of liquid soap. Allow to soak for several minutes
before scraping away adhesive. Encapsulate any remaining trace of adhesive residue with TriSeal (800-367-4583) or a
Portland based patching compound. Existing cutback adhesive must be thoroughly removed and encapsulated to avoid
possible installation failure.
ESSENTIAL STEPS: Integra HP backings provide exceptional performance, but like all high performance backings HP
requires special attention to specifics included here. These preliminary steps are essential for a successful installation.
•
Check style and color. Before cutting or installing carpet the installer is responsible for making sure all styles and colors
match samples selected for the project. Mannington cannot be responsible for installation with visible defects, incorrect
colors or styles.
•
Dye lots. Mannington does not recommend mixing dye lots, especially in open areas that would be highly visible. Mix dye
lots only if necessary in natural break areas where dye lot change would be less noticeable. Always get prior approval
before mixing any dye lots.
•
Dry lay/acclimate. All Integra HP carpet must be allowed to acclimate prior to installation. All carpet should be rolled out
and allowed to acclimate for a full 24 hours.
•
Random, non patterned styles. For random or non patterned styles rolls should be sequenced according to roll numbers.
As a general rule for any new installation, existing adhesives from previous installations should always be
January, 2018