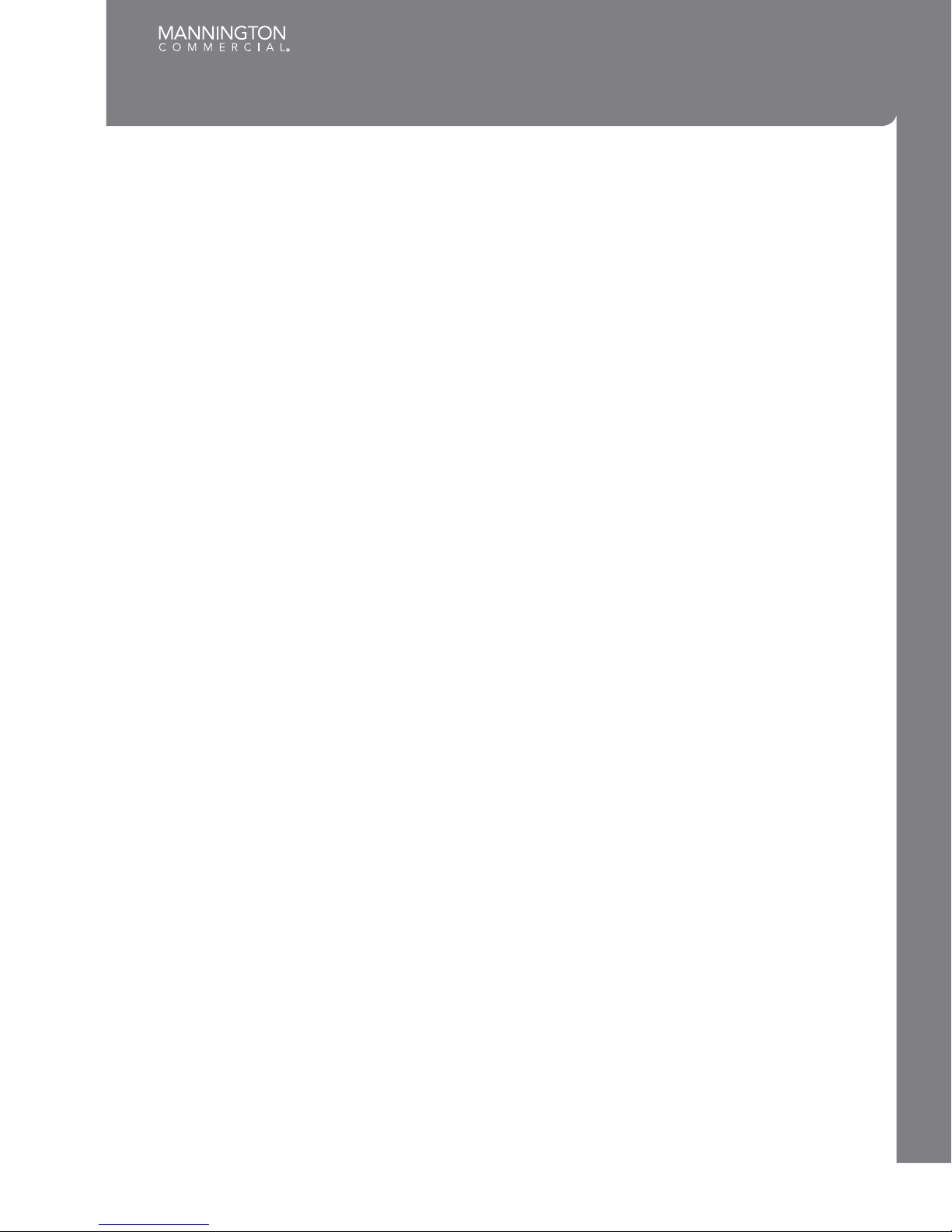
ColorFields Smooth Rubber Sheet Flooring
Installation
PRODUCTS
Mannington’s ColorFields Sheet Rubber Flooring
Because Mannington Commercial Rubber Sheet Flooring products are intended for use in high-traffic areas, underfloor selection
and preparation are especially important. In most cases, remove all existing floor coverings before installing these commercial
products. (You must strictly follow all federal, state, and local regulations regarding the removal of existing flooring.) Furthermore,
all concrete under floors must be tested for moisture before starting the installation. Mannington requires that the concrete be
tested for moisture using either the anhydrous calcium chloride test following ASTM F 1869 procedures and or the in-situ relative
humidity test following ASTM F 2170. Maximum permissible MVER are determined by product construction and adhesive type.
NOTE: While either of the industry accepted moisture-testing methods may be used, the results are not exchangeable, if both
tests are performed they must both be in the acceptable range to be considered valid.
HANDLING INSTRUCTIONS
It is imperative to maintain the material, adhesive, and job site at a minimum temperature of 65°F and a maximum temperature of
85°F for 48 hours before, during, and after the installation. To acclimate properly, the flooring material must be unrolled and
allowed to relax overnight before proceeding with the installation. Remember; maintain the adhesive, floor covering, and job site
between 65°F and 85°F for a minimum of 48 hours before, during, and after the installation.
SUBSTRATE CONSIDERATIONS AND PREPARATION
Concrete Subfloor Requirements:
The General Contractor must provide a finished concrete subfloor ready to receive Mannington’s ColorFields Rubber Flooring.
Subfloors must be smooth and level within a tolerance of 1/8" (3 mm) in a 10' (3.05 m) radius.
ColorFields Smooth Rubber Sheet Flooring Installation
Minor surface cracks or grooves must be filled with a good quality Portland cement based patching or leveling compound with a
minimum compressive strength of 3,500 psi. High spots, bumps and peaks must be repaired prior to installation.
Concrete subfloors must be dry, sufficiently porous, smooth, clean and free of paint, wax, dust, oil, sealers, grease, curing agents,
surface hardeners, old adhesives and any other contaminants that could inhibit or reduce bond strength. Concrete surfaces that
are powdery or scaly are not acceptable.
Although a smooth, flat concrete surface is required, a shiny, slick, nonporous surface is to be avoided. To roughen up a concrete
substrate, remove sealers and increase the porosity of the substrate, mechanical abrasion options are recommended. A “shot
blaster “or “blast track machine” using a No. 275 shot is recommended. Also, scarifiers, of various descriptions, are also
acceptable. Nonporous surfaces must be mechanically roughen or “opened” up. Chemical methods, of any description, are not
recommended.
An over-porous surface is to be corrected with a Portland cement based patching or leveling compound with a minimum
compressive strength of 3,500 psi.
As a general rule, a Concrete Surface Profile (CSP), as defined by the American Concrete Institute, of about 1 is recommended.
Mannington requires that the concrete be tested for moisture. The use of the anhydrous calcium chloride test, following ASTM F
1869 procedures, is acceptable. The test should generate results not exceeding 3 pounds of moisture transpiration for 1,000 Sq.
Ft. within 24 hours. In-situ relative humidity tests following ASTM F 2170 is also acceptable and should generate results not
exceeding 75 percent.
Never execute moisture tests until the building’s HVAC has been operational for at least 7 days. It is imperative that the site
conditions (temperature and humidity) are constant in the building and reflective of in-service conditions.
Adhesion (Bond) Test
• Adhesive Bond Tests should be performed as a final and authoritative “real world” check.
• A bond test of at least 24-hour duration should be performed.
• ColorFields Rubber Sheet Flooring can be cut into 9"x 9" sample sizes.
• Install samples using the recommended adhesive and procedures.
• After 24 hours, removing the test samples should be difficult.
• Most of the cured adhesive should remain bonded to the subfloor.
• If proper bond is not accomplished, do not proceed with the installation.
Choices that Work.
For more information, please contact Mannington Technical Services at
800 241 2262 Ext. 3 or visit www.manningtoncommercial.com.
Jan-2017
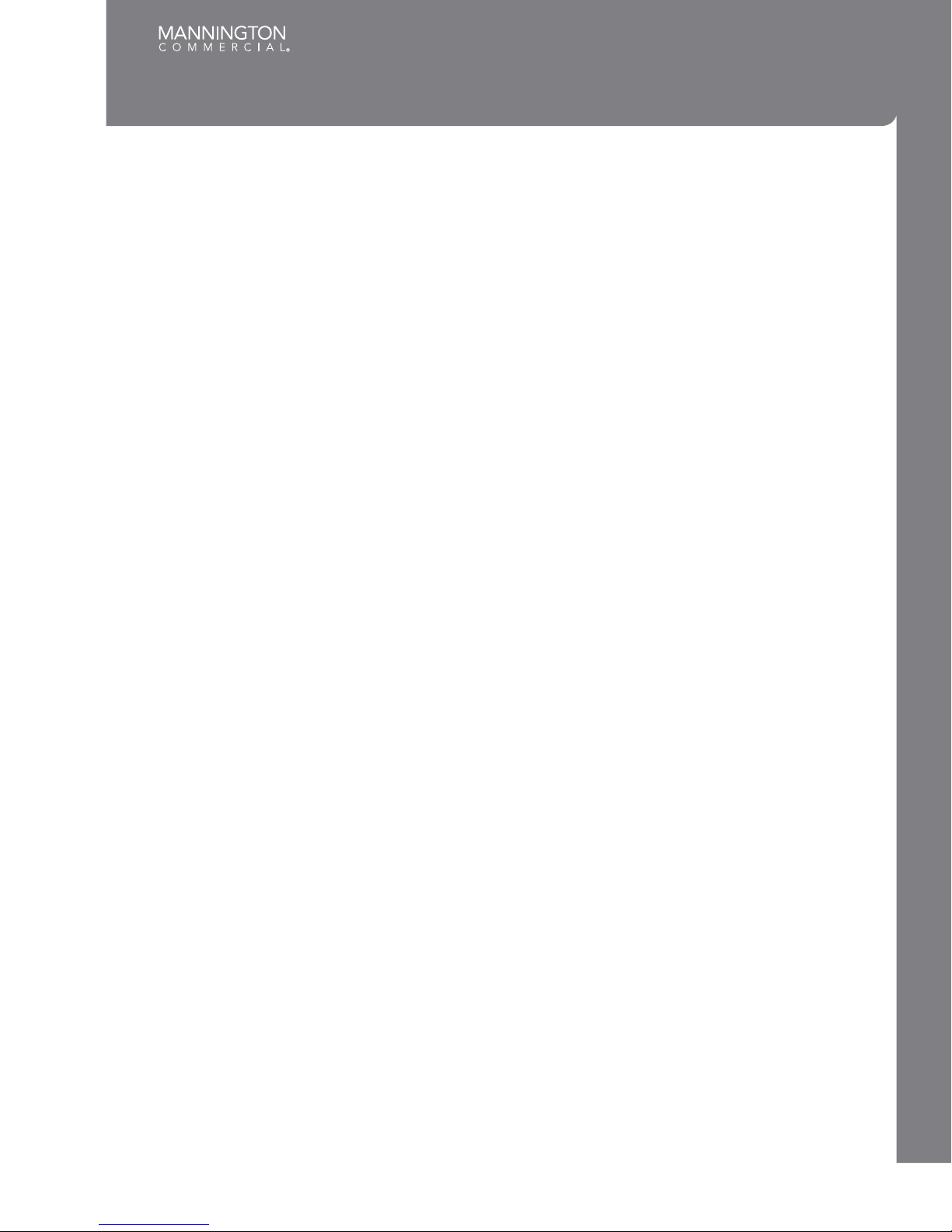
ColorFields Smooth Rubber Sheet Flooring
Installation
NOTE: If the flooring contractor elects to install new floor covering over an existing floor covering, the flooring contractor
assumes all responsibility as to the suitability and continued performance of the existing floor covering. If removal of existing
resilient floor covering is required, follow all recommended Resilient Covering Flooring Institute (RFCI) work practices at
www.rfci.com. Please be aware that installing ColorFields Rubber Flooring over existing floor covering may reduce its excellent
indentation and wear resistance and will negate its warranty.
WARNING: Do not sand, dry sweep, dry scrape, drill, saw, bead blast, or mechanically chip or pulverize existing resilient flooring,
backing, lining felt, paint, asphaltic “cutback” adhesives, or other adhesives. These products may contain asbestos fibers or
crystalline silica. Avoid creating dust. Inhalation of such dust is a cancer and respiratory tract hazard. Smoking by individuals
exposed to asbestos fibers greatly increases the risk of serious bodily harm. Unless positively certain that the product is a
non-asbestos-containing material, you must presume it contains asbestos. Regulations may require that the material be tested to
determine asbestos content. The Resilient Floor Covering Institute (RFCI) document “Recommended Work Practices for Removal
of Resilient Floor Coverings” should be consulted for a defined set of instructions addressed to the task of removing all resilient
floor covering structures. For more information visit the Resilient Floor Covering Institute at www.rfci.com.
PATCHING / LEVELING COMPOUNDS
The use of latex / Portland cement based trowelable patch or self-leveling products are recommended for repairing or leveling
concrete subfloors. The minimum psi rating developed should be a 3,500 pounds. Do not use gypsum or mineral based patching
compounds in commercial applications under any circumstances. The responsibility for a warranty and the performance of the
substrate patching and, or leveling products belongs to the concrete or cementitious patching material manufacturer and
the installer.
ColorFields Smooth Rubber Sheet Flooring Installation
CUTTING AND FITTING
Mannington’s ColorFields Sheet Rubber Flooring is dynamic and flexible. It is easy to cut and fit. The installer can achieve good
results using freehand knifing techniques.
If the job site layout or general design is complex and requires a precise fit, use pattern-scribing techniques. The material may
also be fit using direct scribing techniques.
Before starting any installation, verify the product for type, size, thickness, color, visual imperfections or color variations and notify
Mannington of any apparent defects. No claims will be accepted after the material has been cut or installed.
Allow all adhesives and flooring materials to acclimate to job site temperature and humidity conditions prior to dry lay, fitting and
cutting.
To acclimate properly, Mannington ColorFields Rubber Flooring must be unrolled and allowed to relax for a minimum of 12 hours
in an ambient temperature range between 65°F and 85°F before proceeding with the installation.
• Unroll the rubber sheet flooring lengths in the same direction.
• Do not use the “reverse roll” method when laying out lengths of sheet rubber flooring.
• Cut the sheets to the required lengths.
Double Cutting the Colorfields Sheet Rubber Seams is not normally necessary. The Sheet Rubber rolls are manufactured with
precision cut edges on both sides of the roll. However, if job-site conditions, or design plans require custom layouts, use the
following recommendations.
• All seams are to be double-cut and must have a minimum 1 1/4 inch overlap.
• In places, some sheets may have a slight taper near the edge of the sheet.
• When present, tapered edges are to be on the bottom side of the overlap.
• To “double cut seams,” start with a long, true straight edge to be used as a guide.
• Position the straight edge about 1/2 inch from the top edge of the overlap.
• Use a straight blade utility knife. Hold the utility knife as vertical as possible.
• Double cut through the top sheet, and about 3/4 of the way through the bottom sheet.
• Remove material from the bottom cut by pulling it back, under itself, parallel to the cut.
• Double cut seams must have a close, gap free quality of cut without burrs or tears.
• Do not pressure fit poorly cut seams together for a “passable fit.”
Dry lay and “cut to fit” all material prior to adhesion. This includes all perimeters, casework, columns, doorways, et cetera, that
are contained within the space.
• Once the material has been fit, it is necessary to re-roll or “lap back” half of the sheet to expose the underfloor for
adhesive application.
• Take care when folding the material back. Always fold the material in a wide radius to avoid sharp kinks and creases,
which may cause breaks in the product.
Choices that Work.
For more information, please contact Mannington Technical Services at
800 241 2262 Ext. 3 or visit www.manningtoncommercial.com.
Jan-2017