
T
ECHNICAL INFORMATION
Models No.
Description
BTP140
Cordless 4 Mode Impact Driver
CONCEPT AND MAIN APPLICATIONS
Model BTP140 has been developed as the 18V sister tool to Model BTP130.
Uses BL1830, 18V slide-on type Li-ion battery as a power unit,
and features the same high performance and versatility as Model BTP130.
This new product is available in the following variations.
Model No.
BTP140SFE
BTP140*
BTP140RFE BL1830 DC18RA2 Yes
BTP140Z No No No
Specification
Voltage: V 18
Capacity: Ah
Battery
Max. fastening torque:
N.m (in.lbs)
No load speed:
min-1=rpm
Impacts per minute:
min-1=ipm
Torque setting on clutch (screwdriver) mode
Clutch torque range: N.m (in.lbs) 0.5 - 2.0 (4.4 - 17.7)
Capacity
Net weight: kg (lbs) [with BL1830]
Cell
Charging time: min.
Drilling:
mm (")
Fastening
Drill mode
Percussion-drill mode
Screwdriver mode
Impact-driver mode
Battery
type quantity
BL1830 DC18SC
*Model name for USA, Canada, Mexico, Panama
Impact-driver mode
Drill mode
Impact-driver mode 0 - 2,300
Drill mode
Screwdriver mode 0 - 2,300
Impact-driver mode 0 - 3,200
Percussion-drill mode
2 Yes
Small screw M4
Small screw
Standard bolt
High tensile bolt
Coarse-thread
Charger
Soft joint
Hard joint 50 (443)
Lock torque 10 (88.5)
Low
High
Wood 21 (13/16)
Steel
Masonry
Plastic
carrying case
3.0
Li-ion
approx. 45 with DC18SC
approx. 22 with DC18RA
140 (1,240)
10 (88.5)
0 - 700
0 - 2,300
0 - 27,600
16
10 (3/8)
8 (5/16)
M4 - M8
M5 - M14
M5 - M12
22 - 125mm
1.8 (3.9)
W
Dimensions: mm (")
Length (L)
Width (W)
Height (H)
PRODUCT
P 1 /16
L
H
186 (7-3/8)
79 (3-1/8)
246 (9-11/16)
Standard equipment
Belt clip ................................... 1
Plastic carrying case ................ 1
Keyless chuck .......................... 1 (for North American countries only)
Note: The standard equipment for the tool shown above may differ by country.
Optional accessories
Assorted bits, Assorted drill chucks, Adjustable locator, Keyless chuck, Bit piece
Charger DC18SC, Charger DC18RA, Charger DC24SA, Charger DC24SC, Li-ion battery BL1830
Shoulder belt for plastic carrying case
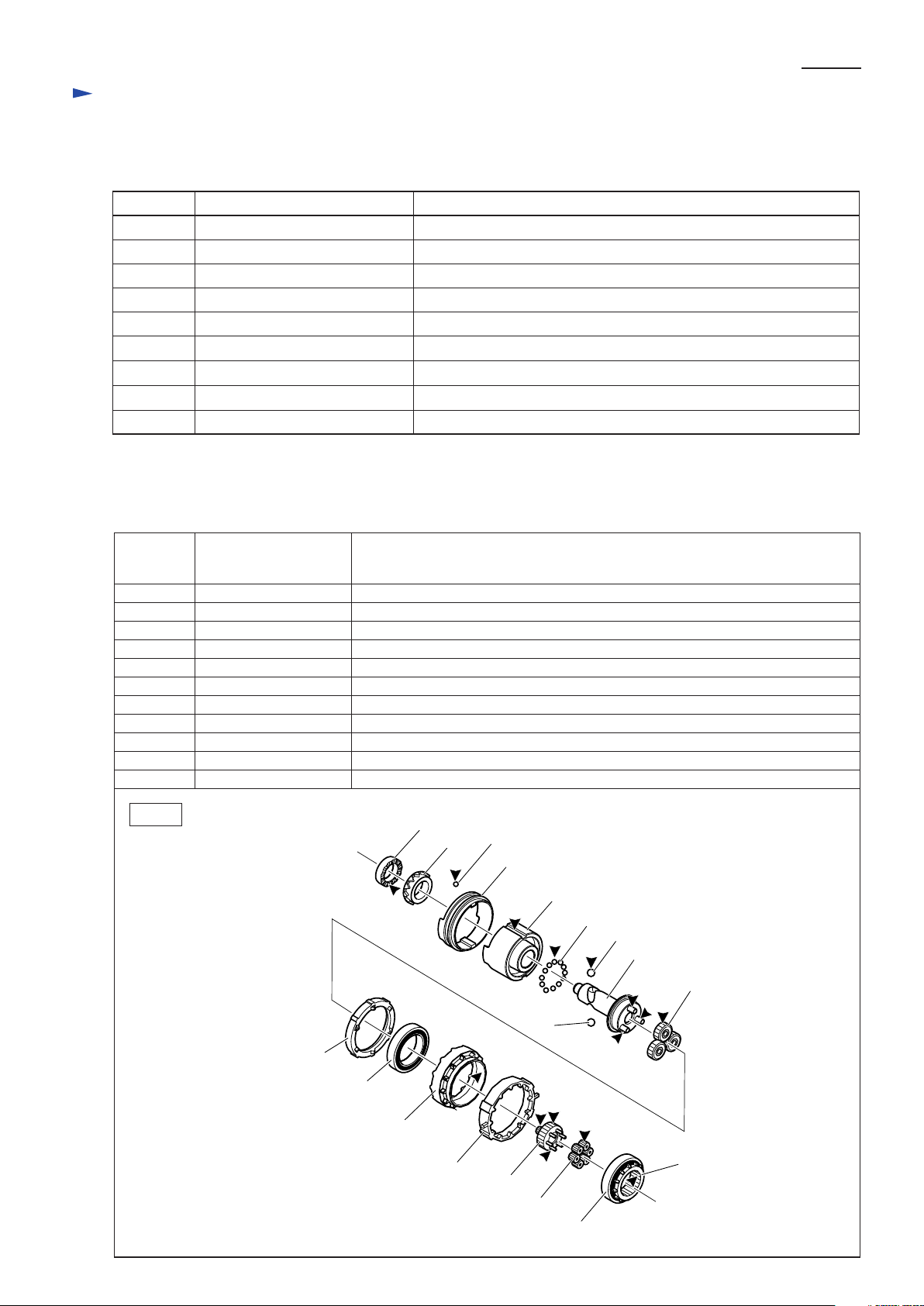
P 2 /16
Repair
CAUTION: Remove the saw blade from the machine for safety before repair/ maintenance !
[1] NECESSARY REPAIRING TOOLS
DescriptionCode No. Use for
1R003 Retaining ring pliers for shaft Removing/attaching Retaining ring from/to Shaft
1R045 Gear extractor (large) Disassembling Hammer section
1R212 Tip for retaining ring pliers Modular use with 1R003
1R282 Round bar for arbor 8-50 Modular use with 1R045
1R288 Screwdriver magnetizer Magnetizing screwdriver with which Steel balls are removed.
1R291 Retaining ring S and R pliers Disassembling Bit holder section
1R346 Center attachment for 1R045 Modular use with 1R045
1R351 Anvil holding jig Removing Anvil from Gear case
1R357 Cam A setting jig Assembling Cam A
[2] LUBRICATION
Apply Makita grease N. No.2 to the following portions designated with the black triangle to protect
parts and product from unusual abrasion.
Item No. Description Portion to lubricate
40
42
58
59
63
64
68
70
71
72
75
Fig. 1
Cam A Surface that contacts Cam B
Steel ball 3.5 (16 pcs) Whole surface
Hammer Groove that contacts Ring 40
Steel ball 3.5 (23 pcs) Whole surface
Steel ball 5.6 (2 pcs) Whole surface
Spindle complete Three axes for (70) Spur gear 22
Internal gear 50
Spur gear 22 (3 pcs)
Spur gear 7 complete
Spur gear 10 (6 pcs)
Internal gear 38
Inside surface that contacts (70) Spur gear 22
Teeth portion
Teeth portion and six axes for (72) Spur gear 10
Teeth portion
Teeth portion
40
Cam B
42
Ring 40
58
59
63
64
70
Clutch cam
Ball bearing 6805LLB
Clutch change lever
63
68
75
71
72
Ball Bearing 6805LLB

P 3 /16
Repair
[3] DISASSEMBLY/ASSEMBLY
[3] -1. Impact Assembly
DISASSEMBLING
1) Remove Rear cover by unscrewing two 3x16 Tapping screws and Housing R by unscrewing nine 3x16 Tapping screws.
The machine can now be disassembled as illustrated in Fig. 2.
2) Remove Ring spring 11 from the groove on Anvil. Component parts of Chuck section can now be removed from Anvil.
(Fig. 3)
3) Remove Bumper and two M4x16 Pan head screws. Hammer case can now be removed together with Ball bearing
6802LLB and Retaining ring R-24. (Fig. 4)
Fig. 2
Impact assembly
Housing L
Fig. 3
Chuck section
Compression spring 13
Ring spring 11 Sleeve
Motor section
Steel ball 3.5
groove
Anvil
Tapping screw 3x16 (9 pcs)
Housing R
Rear Cover
Tapping screw 3x16 (2 pcs)
Impact assembly
Anvil
Flat washer 12
Fig. 4
Pan head screw M4x16 (2 pcs)
Bumper
Hammer case Impact assembly
Steel ball 3.5
Two M4 Hex nuts are press-fitted in Gear case of
Impact assembly. Be careful not to get them out
of place when removing the Pan head screws.
Forcing the Pan head screws out of Gear case will
cause the Nuts to fall inside of gear case.
Hex nut M4 Gear case
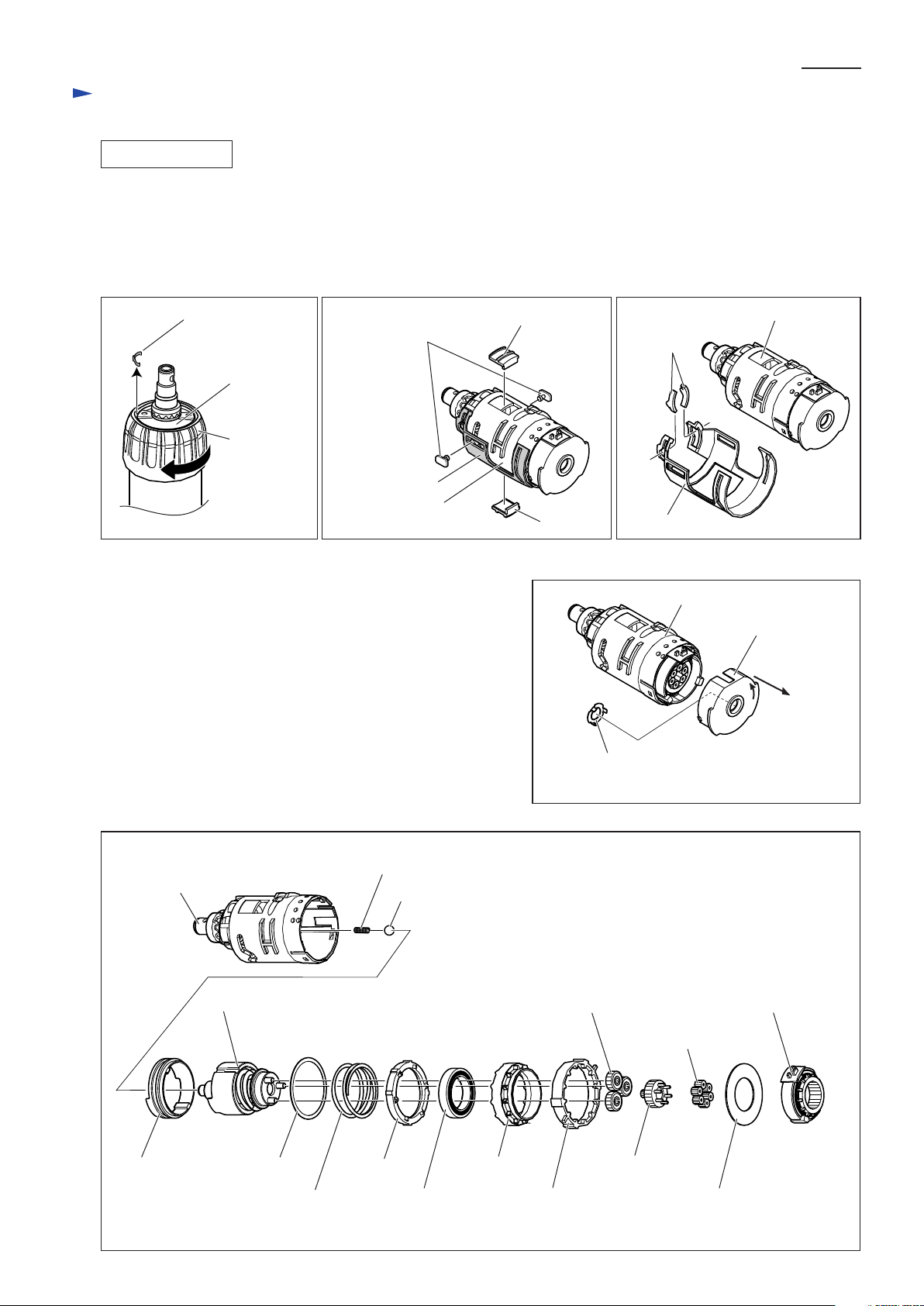
P 4 /16
Repair
[3] -1. Impact Assembly (cont.)
DISASSEMBLING
4) Remove Leaf spring from the space between Gear case and Change ring. Remove Change ring from Gear case
while turning clockwise. (Fig. 5)
5) Remove Pusher U from Gear case, and Pusher L from Change case. Remove two assemblies of Guide and Shoulder
pin-3-6. (Fig. 6)
6) Remove Change case from Gear case. Remove two Plate A's from Change case. (Fig. 7)
Fig. 5 Fig. 6 Fig. 7
Leaf spring
Gear case
Change ring
7) Pull off Motor bracket from Gear case by turning a little bit
counterclockwise. (Fig. 8)
8) Impact assembly can now be disassembled as illustrated in Fig. 9.
assembly of Guide
and Shoulder pin 3-6
Change case
Gear case
Pusher U
Pusher L
Fig. 8
Gear case
Plate A
Change case
Gear case
Motor bracket
Washer 10 comes with Motor bracket
when Motor bracket is removed.
Fig. 9
Ring 40
Anvil
Hammer section
Flat washer 40
Compression Spring 4, removed from Anvil
Steel ball 7.1, removed from Anvil
Spur gear 22 (3pcs)
Clutch cam
Ball bearing 6805LLBCompression spring 41
Internal gear 50
Clutch change lever Flat washer 25
Speed change lever complete
Spur gear 10 (6pcs)
Spur gear 7 complete
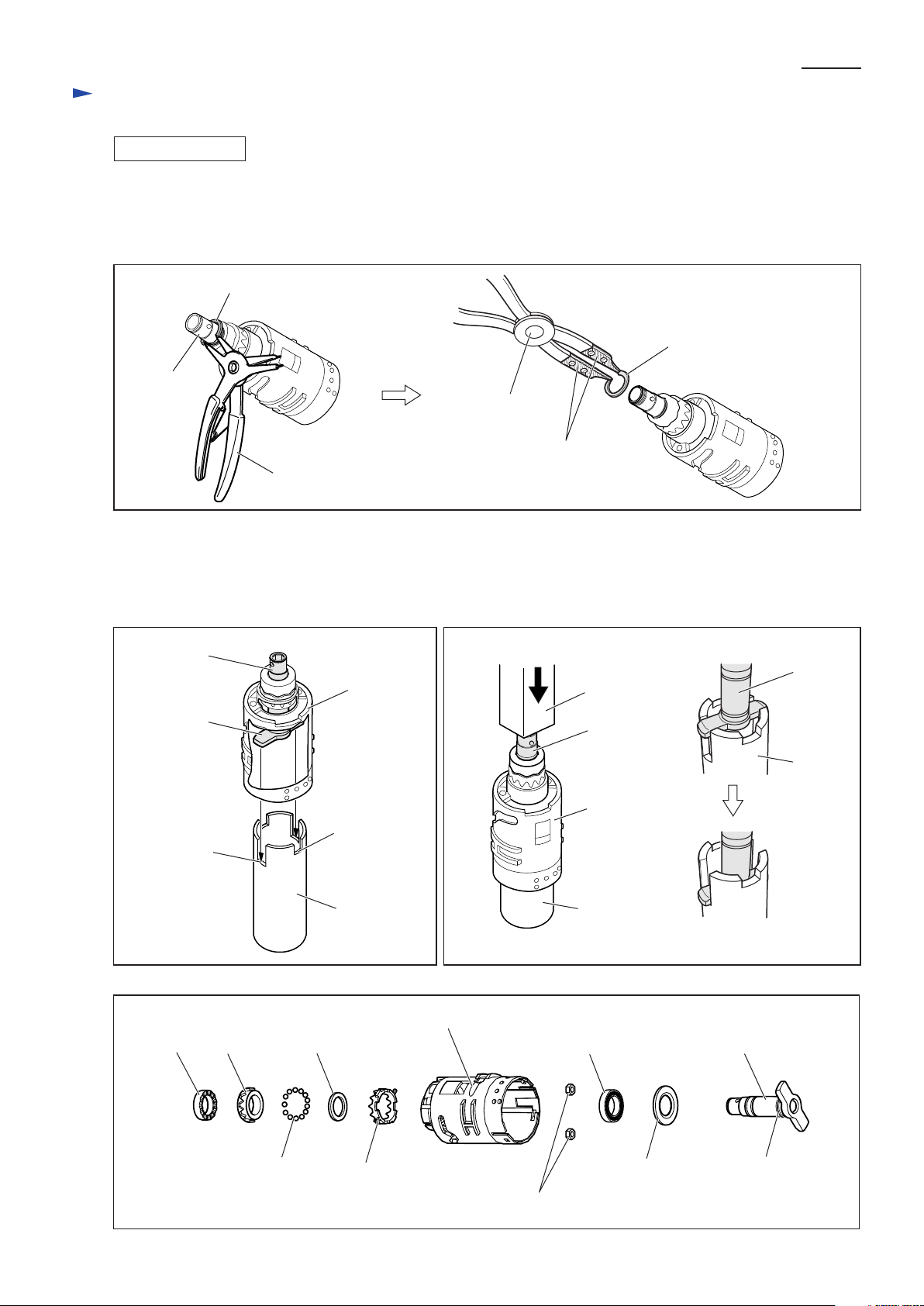
Repair
[3] -1. Impact Assembly (cont.)
DISASSEMBLING
9) Slide Retaining ring WR-15 a little out of the groove on Anvil using 1R291.
Then remove Retaining ring WR-15 from Anvil using 1R003 to which 2pcs of 1R212 are attached. (Fig. 10)
Note: Retaining ring WR-5 cannot be removed if it is stuck under Cam A.
If so, see Press-fitting Cam A in place on Anvil in page 5.
Fig. 10
Retaining ring WR-15
Retaining ring WR-15
Anvil
1R003
1R212
1R291
P 5 /16
10) Fit the T-shaped end of Anvil in the deep notch in 1R351. (Fig. 11)
11) Remove Anvil from Gear case by pressing down using arbor press. (Fig. 12)
12) The parts around Anvil can now be removed as illustrated in Fig. 13. Two M4 Hex nuts can also removed in this step.
Note: Be careful not to lose small parts such as Steel ball 3.5.
Fig. 11 Fig. 12
Anvil
Anvil
Gear case
T-shaped end
shallow notch
deep notch
1R351
Fig. 13
Arbor press
Anvil
1R351
Gear case
1R351
Cam BCam A
Steel ball 3.5
(16 pcs)
Flat washer 15
Gear case
Ball bearing 6802LLB
Hex nut M4
Anvil
O ring 12.5Nylon washer 15Hammer change lever