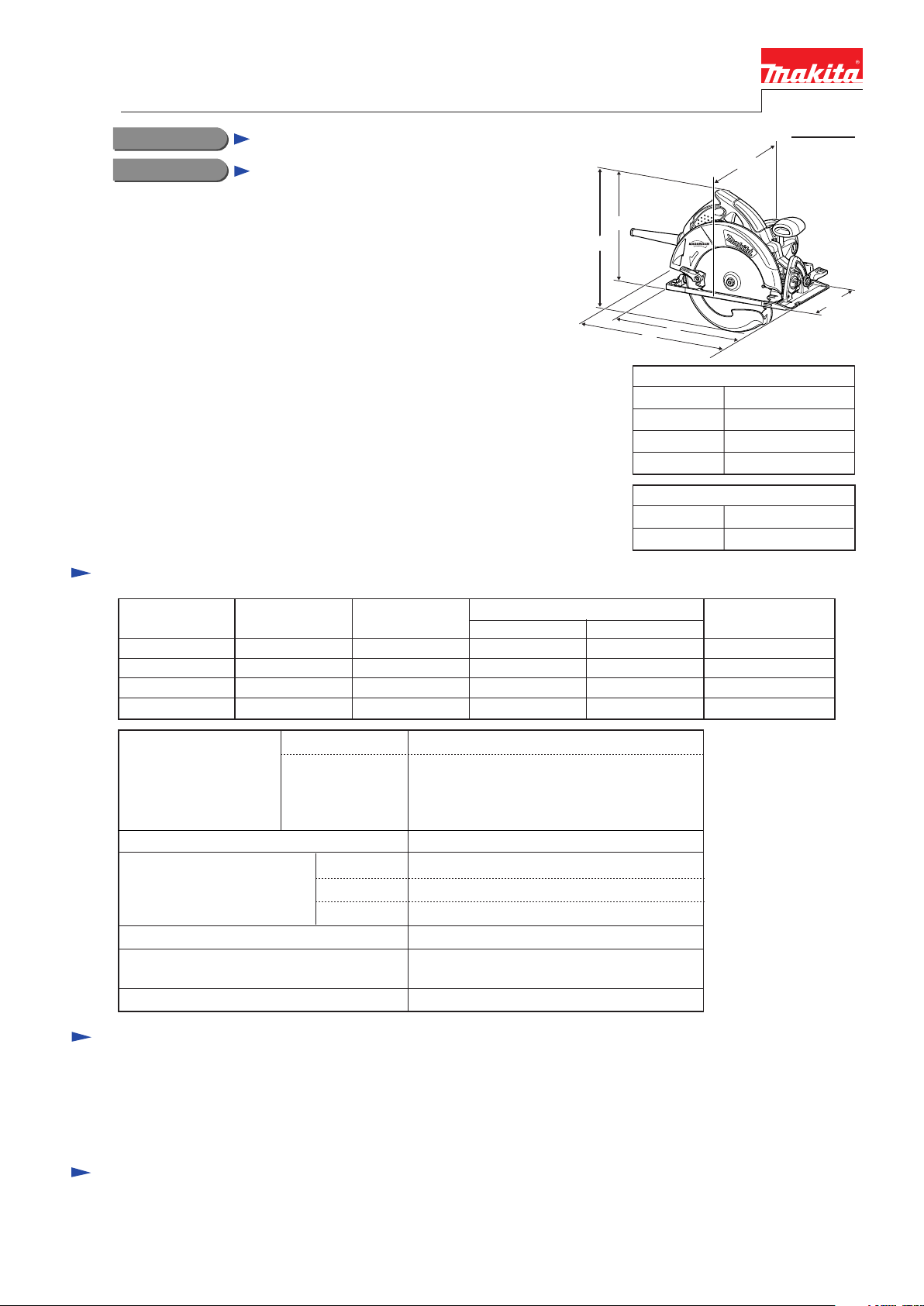
T
Description
ECHNICAL INFORMATION
Models No.
5008MG, 5008MGA
Circular Saw 210mm (8-1/4")
PRODUCT
P 1/10
W1
CONCEPT AND MAIN APPLICATIONS
Model 5008MG and 5008MGA have been developed
as 210mm (8-1/4") version of Models 5007MG/5007MGA,
185mm (7-1/4") Circular saws.
Feature new design, increased convenience, and cutting depth
capacity of 75.5mm (3").
The only one difference between 5008MG and 5008MGA is;
5008MG: Without electric brake
5008MGA: With electric brake
Specification
Voltage (V) Cycle (Hz)
120
220
230
240
Current (A)
15
8.6
8.2
7.9
50/60
50/60
50/60
50/60
H2
H1
L1
Length (L1)
Width (W1)
Height (H1)
Height (H2)
Length (L2)
Width (W2)
Continuous Rating (W)
Input Output
---
1,800
1,800
1,800
900
1,000
1,000
1,000
W2
L2
Dimensions: mm (")
332 (13-1/8)
243 (9-9/16)
277 (10-7/8)
192 (7-9/16)
Base size: mm (")
320 (12-5/8)
170 (6-11/16)
Max. Output (W)
2,300
2,300
2,300
2,300
Diameter
Size of blade: mm (")
Hole diameter
No load speed: rpm= min.-1
Max cutting capacity: mm (")
Cord length: m (ft)
Net weight: kg (lbs)
North America: 15.88 (5/8)
0 degree
45 degrees
210 (8-1/4)
Australia: 25.0
Europe: 30.0
Other countries: 25.4 (1)
5,200
75.5 (3)
57 (2-1/4)
51.5 (2)50 degrees
Double insulationProtection against electric shock
Australia, Chile: 2 (6.6)
Other countries: 2.5 (8.2)
4.8 (10.6)
Standard equipment
Hex wrench ....................... 1
Guide rule ............................ 1
TCT saw blade 210 ............. 1
Dust nozzle and Pan head screw M5x16 .... 1 (Europe only)
Note: The standard equipment for the tool shown above may differ by country.
Optional accessories
Saw blades
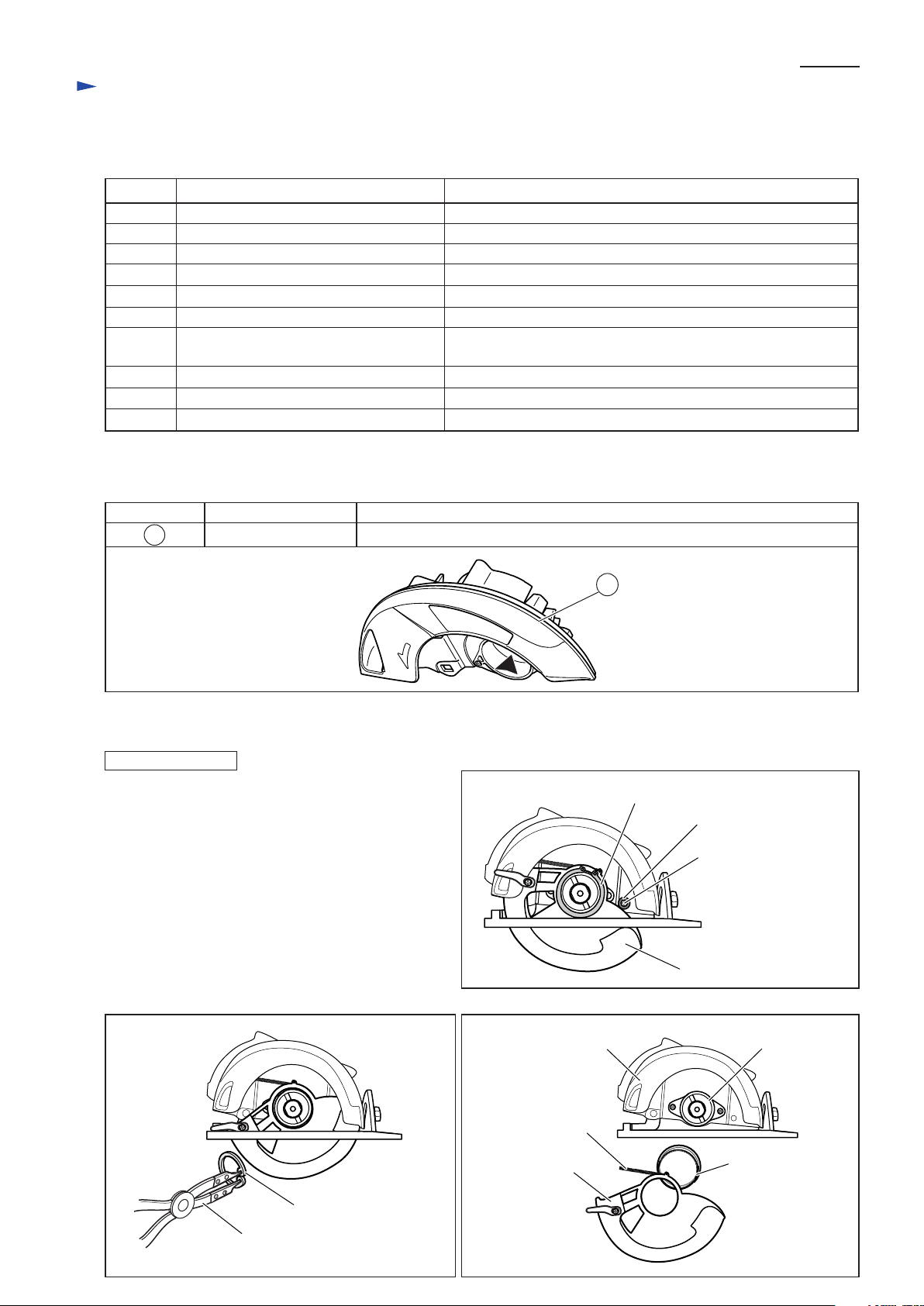
Repair
CAUTION: Unplug the machine and remove the saw blade from the machine for safety
before repair/ maintenance in accordance with the instruction manual!
[1] NECESSARY REPAIRING TOOLS
Code No. Description Use for
1R003
1R004
1R008
1R041
1R045
1R208
1R229
1R236 Round bar for arbor 7-100
1R269
1R316
[2] LUBRICATION
Apply Makita grease N. No.1 to the following portions designated with the black triangle to protect
parts and product from unusual abrasion.
Item No. Description Portion to lubricate
Retaining ring S pliers ST-2N Removing/installing Retaining ring S-42 from/on Spindle
Retaining ring S pliers ST-2
Tips for retaining ring pliers (90 degrees)
Vise plate
Gear extractor (large)
90-degree Set square
1/4" Hex shank bit for M5
Bearing extractor
Adjustable bearing retainer wrench
32
Blade case complete Gear room for Helical gear 47 (Apply approximately 6g.)
Pulling off Sleeve 6 from the hinge portion of Angular guide
(modular use with 1R004)
Fixing Bearing box section in vise
Removing Spindle from Bearing box
Squaring Saw blade to Base plate
Removing Hex socket head bolt M5x40 from the hinge portion of
Angular guide
Removing Spindle from Helical gear 47
Removing Ball bearing 608LLB from Spindle
Removing/installing Bearing retainer from/on Bearing box
P 2/10
[3] DISASSEMBLY/ASSEMBLY
[3] -1. Safety Cover
DISASSEMBLING
1) Remove Pan head screw M6x20 and Rubber sleeve 6.
(Fig. 1)
2) Remove Retaining ring S-42 with 1R003. (Fig. 2)
3) Remove Torsion spring 4 and Safety cover
from Blade case.
Then remove Spacer from Bearing box. (Fig. 3)
Fig. 2 Fig. 3
Fig. 1
32
Retaining ring S-42
Rubber sleeve 6
Pan head screw M6x20
Safety Cover
1R003
Retaining ring S-42
Blade case
Tension spring 4
Safety cover
Bearing box
Spacer
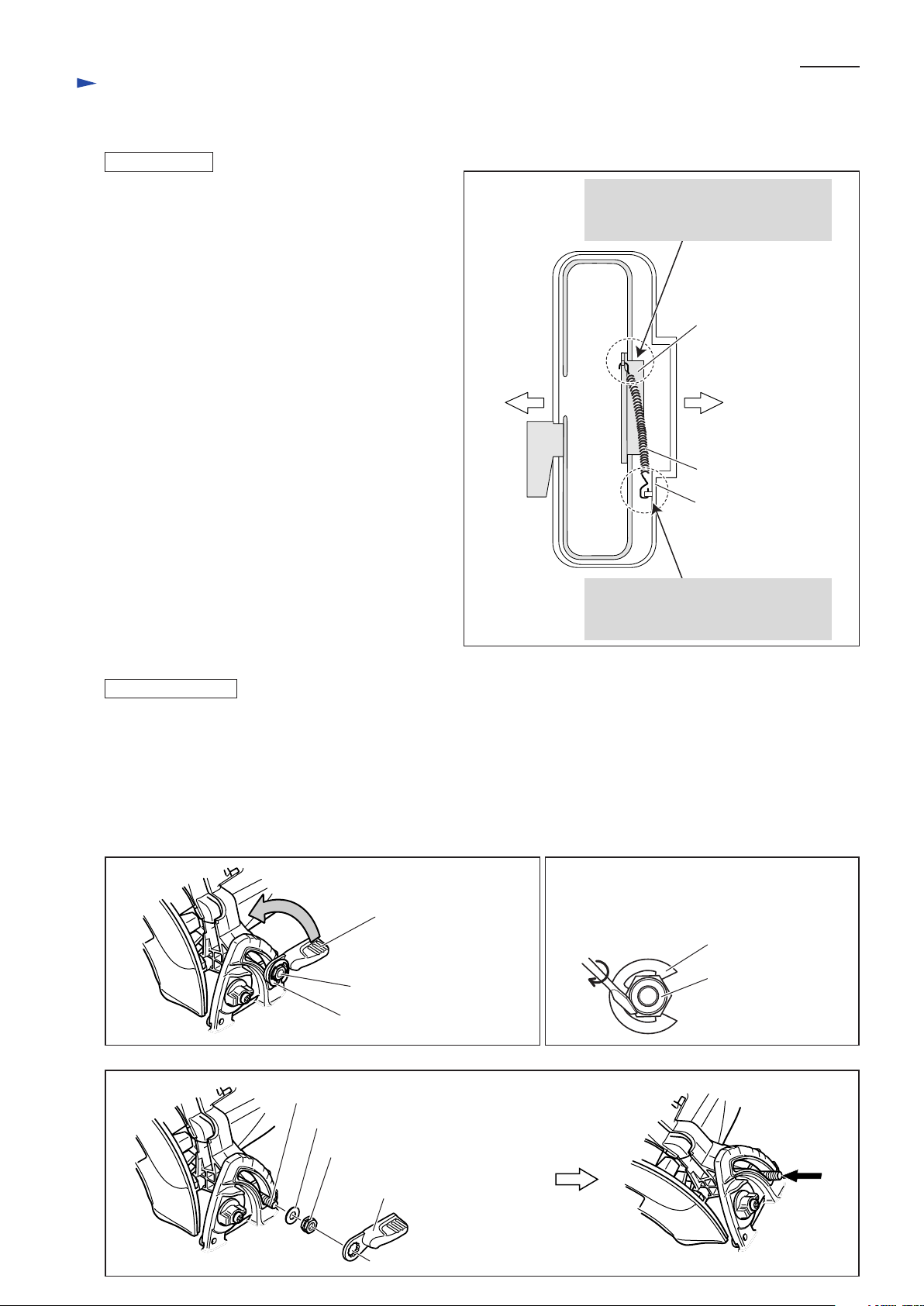
Repair
[3] DISASSEMBLY/ASSEMBLY
[3] -1. Safety Cover (cont.)
ASSEMBLING
1) Assemble Spacer and Safety cover to Bearing box.
(Fig. 3 on page 2)
2) Assemble Safety cover to Bearing box.
(Fig. 3 on page 2)
Link Safety cover to Blade case with Tension spring 4
as illustrated in Fig. 4.
Note: Be sure to follow the instructions in Fig. 4.
Otherwise, pivoting action of Safety cover
will be interfered by Tension spring 4.
3) Secure Safety cover to Bearing box with Retaining
ring S-42. Fasten Rubber sleeve 6 to Blade case with
Pan head screw M6x20. (Figs. 1, 2 on page 2)
P 3/10
Fig. 4
Pass the hook of Tension spring 4
through the hole on Safety cover
from Bearing box side to Blade side.
Safety cover
Blade side
Bearing box side
Tension spring 4
Blade case
Pass the hook of Tension spring 4
through the hole on Blade case
from Blade side to Bearing box side.
[3] -2. Base Complete
DISASSEMBLING
Note: The above illustrations show the conditions after removal of Safety cover.
It is not necessary to remove Safety cover when replacing Base complete.
1) Loosen Hex nut M8-13 by turning Lever 56 (the one used for bevel angle adjustment) in the direction of the arrow
as illustrated in Fig. 5.
2) Remove Bow stop ring E-12 from Hex nut M8-13 using slotted screwdriver as described in Fig. 6.
3) Remove Lever 56, Hex nut M8-13 and Flat washer 8 from Flat-head square-neck bolt M8x24.
Then remove Flat-head square-neck bolt M8x24 by pushing it in the direction of the black arrow. (Fig. 7)
Fig. 5
Lever 56
(the one used for
bevel angle adjustment)
Hex nut M8-13
Bow stop ring E-12
Fig. 6
Remove Bow stop ring E-12 from the groove
of Hex nut M8-13 by twisting the ring using
slotted screwdriver.
Bow stop ring E-12
Hex nut M8-13
Fig. 7
Flat-head square-neck bolt M8x24
Flat washer 8
Hex nut M8-13
Lever 56 (the one used for
bevel angle adjustment)