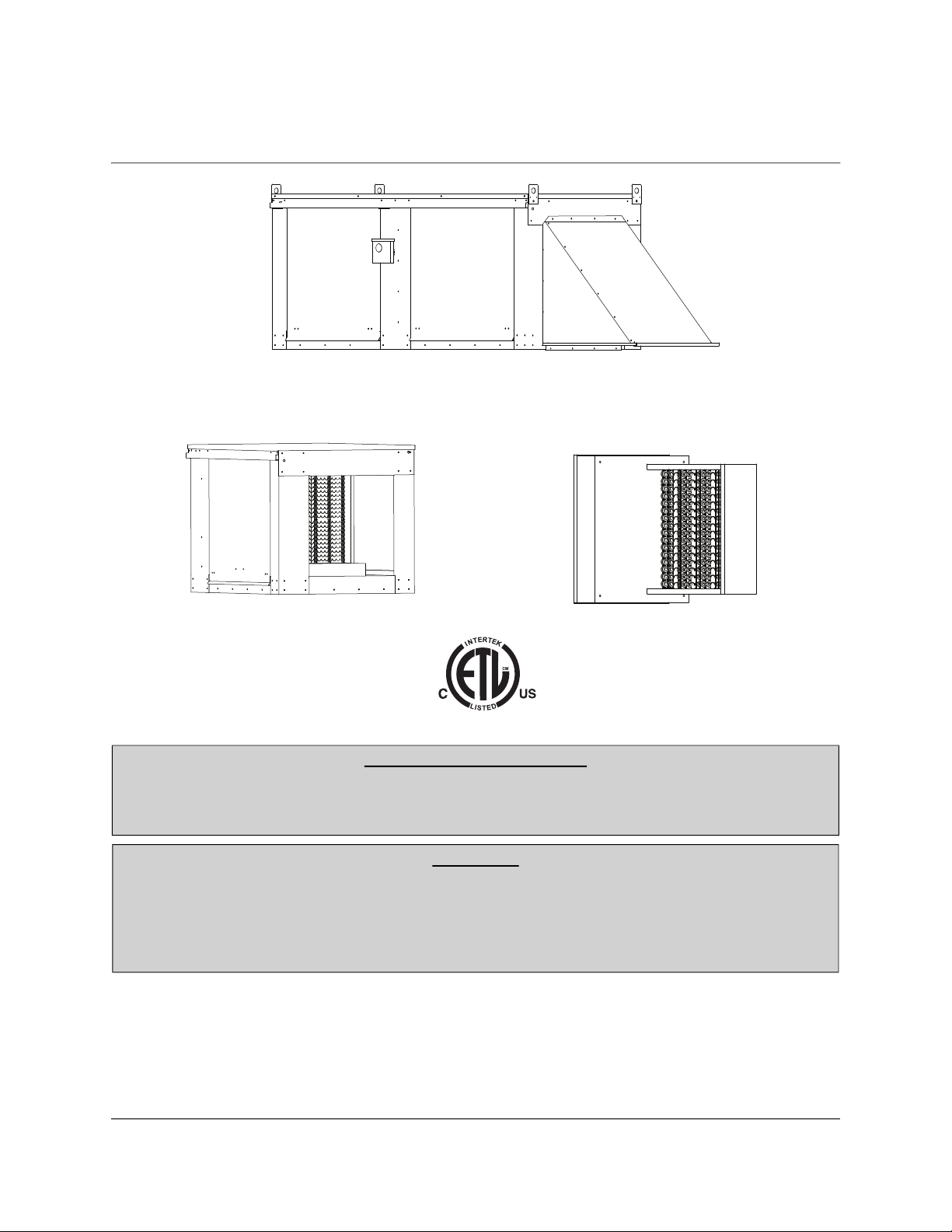
Standard and Modular Electric Heater and Inserts
Installation, Operation, and Maintenance Manual
Modular Electric Heater
Electric Heat Module
RECEIVING AND INSPECTION
Upon receiving unit, check for any interior and exterior damage, and if found, report it
immediately to the carrier. Also check that all accessory items are accounted for and are
damage free.
WARNING!!
Installation of this equipment should only be performed by a qualified professional who has
read and understands these instructions and is familiar with proper safety precautions.
Improper installation poses serious risk of injury due to electric shock and other potential
hazards. Read this manual thoroughly before installing or servicing this equipment. ALWAYS
disconnect power prior to working on equipment.
Save these instructions. This document is the property of the owner of this equipment and is required
for future maintenance. Leave this document with the owner when installation or service is complete.
Electric Insert
A0011031
May 2020 Rev. 24
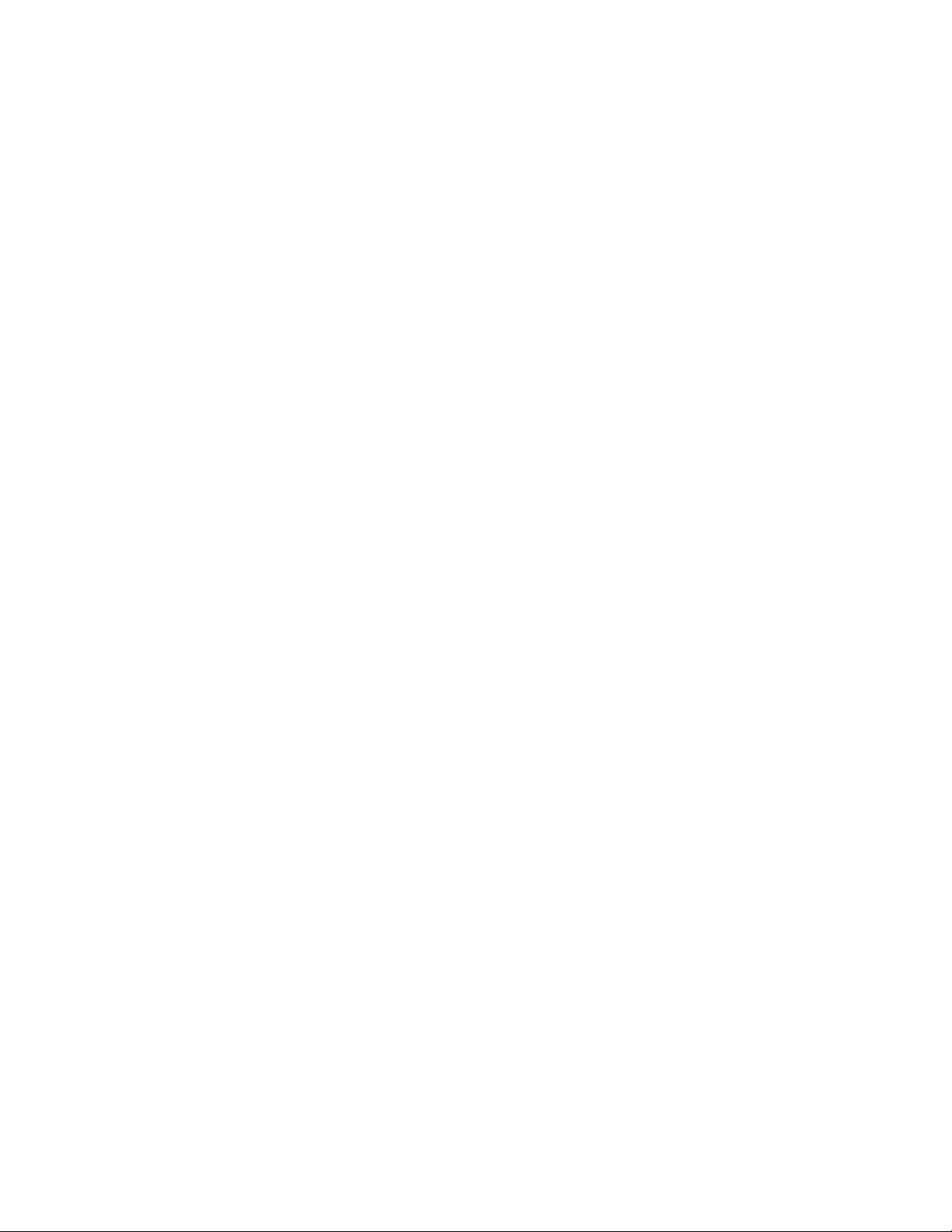
Table of Contents
WARRANTY ............................................................................................................................................................................. 3
INSTALLATION ........................................................................................................................................................................ 4
Mechanical ........................................................................................................................................................................ 4
Service Clearance ..................................................................................................................................................... 4
Common Electric Heater Calculations ....................................................................................................................... 4
Applied vs Rated KW Factors ....................................................................................................................................4
Curb and Ductwork ............................................................................................................................................................ 6
Roof Mount Installation .............................................................................................................................................. 7
Installation with Exhaust Fan ..................................................................................................................................... 7
Duct Mount Installation .............................................................................................................................................. 8
Indoor (Inline) Installation .......................................................................................................................................... 8
Heat Module Add-On Installation ...............................................................................................................................9
ELECTRICAL ..........................................................................................................................................................................10
Fan to Building Wiring Connection .................................................................................................................................. 12
Remote Control Panel ..................................................................................................................................................... 12
Electric Cabinet Heater ............................................................................................................................................13
AC Interlock .............................................................................................................................................................13
Motorized Intake Damper ........................................................................................................................................ 13
Permanent Split Capacitor (PSC) Motor Speed Control ................................................................................................. 13
Electronically Commutated Motor (ECM) Speed Control ................................................................................................ 14
External PWM Signal ...............................................................................................................................................14
Unit Mount Controller ...................................................................................................................................................... 14
Motor Speed Controller (MSC) Installation ...................................................................................................................... 15
MSC Controls Overview .................................................................................................................................................. 16
MSC Menu ...............................................................................................................................................................16
Input Threshold ........................................................................................................................................................18
MSC Menu Tree ...................................................................................................................................................... 19
Heater Controller ..................................................................................................................................................... 20
Variable Frequency Drive (VFD) ..................................................................................................................................... 21
Variable Frequency Drive (VFD) Installation ........................................................................................................... 22
Input AC Power ........................................................................................................................................................ 22
VFD Output Power ................................................................................................................................................... 22
VFD Programming ................................................................................................................................................... 23
ACTECH SMV VFD ................................................................................................................................................. 24
START-UP OPERATION ........................................................................................................................................................25
Start-up Procedure .......................................................................................................................................................... 25
Pulley Adjustment ............................................................................................................................................................ 26
Pulley Alignment/Proper Belt Tension .............................................................................................................................27
Pulley Combination Chart ................................................................................................................................................ 28
Sequence of Operation ................................................................................................................................................... 29
Main Circuit ..............................................................................................................................................................29
Optional Remote Panel Circuit ................................................................................................................................ 30
Silicon Controlled Rectifier (SCR) Electrical Control ....................................................................................................... 31
Modulating Coil Thermostat Settings .............................................................................................................................. 31
Thermostat with Dip Switch Settings ....................................................................................................................... 31
Thermostat without Dip Switch Settings .................................................................................................................. 31
SCR Electrical Circuit Check ...........................................................................................................................................32
Components .................................................................................................................................................................... 33
Remote Panel Option .............................................................................................................................................. 34
Troubleshooting ............................................................................................................................................................... 35
MSC Troubleshooting .............................................................................................................................................. 37
MAINTENANCE ......................................................................................................................................................................38
General Maintenance ...................................................................................................................................................... 38
2 Weeks After Start-up .................................................................................................................................................... 38
Every 3 Months ............................................................................................................................................................... 38
Yearly .............................................................................................................................................................................. 38
Unit Filters ....................................................................................................................................................................... 39
Start-Up and Maintenance Documentation ..................................................................................................................... 40
2
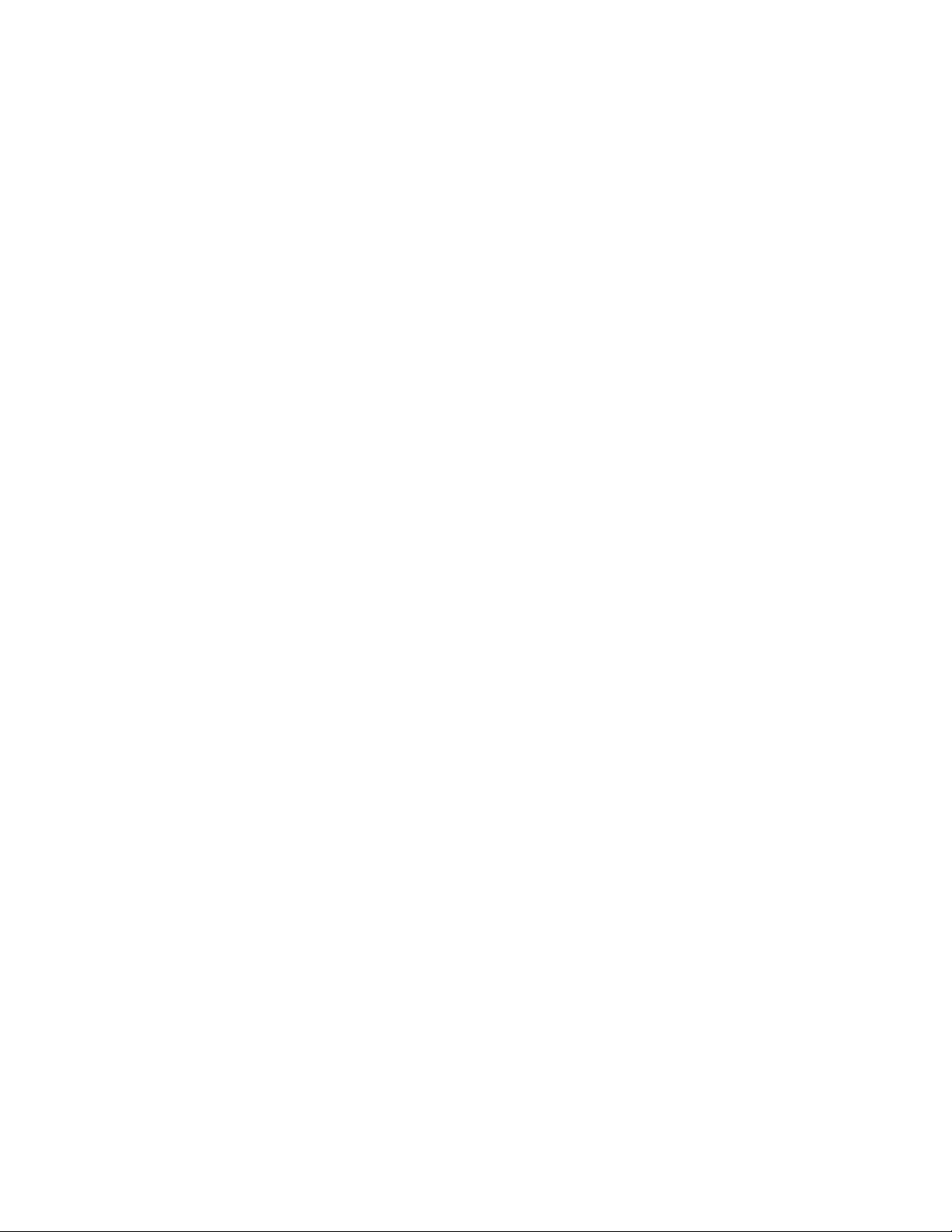
WARRANTY
This equipment is warranted to be free from defects in materials and workmanship, under normal use and
service, for a period of 2-years from date of shipment. This warranty shall not apply if:
1. The equipment is not installed by a qualified installer per the MANUFACTURER’S installation
instructions shipped with the product.
2. The equipment is not installed in accordance with Federal, State, or Local codes and regulations.
3. The equipment is misused or neglected, or not maintained per the MANUFACTURER’S maintenance
instructions.
4. The equipment is not installed and operated within the limitations set forth in this manual.
5. The invoice is not paid within the terms of the sales agreement.
The MANUFACTURER shall not be liable for incidental and consequential losses and damages potentially
attributable to malfunctioning equipment. Should any part of the equipment prove to be defective in
material or workmanship within the 2-year warranty period, upon examination by the MANUFACTURER,
such part will be repaired or replaced by MANUFACTURER at no charge. The BUYER shall pay all labor
costs incurred in connection with such repair or replacement. Equipment shall not be returned without
MANUFACTURER’S prior authorization, and all returned equipment shall be shipped by the BUYER,
freight prepaid to a destination determined by the MANUFACTURER.
NOTE: To receive warranty coverage for this product, copy and print out the “Start-Up and
Maintenance Documentation” on page 40. Fill in all details required. Fax the page to 1-919-516-8710
or call 1-866-784-6900 for email information within thirty (30) days of purchase.
3
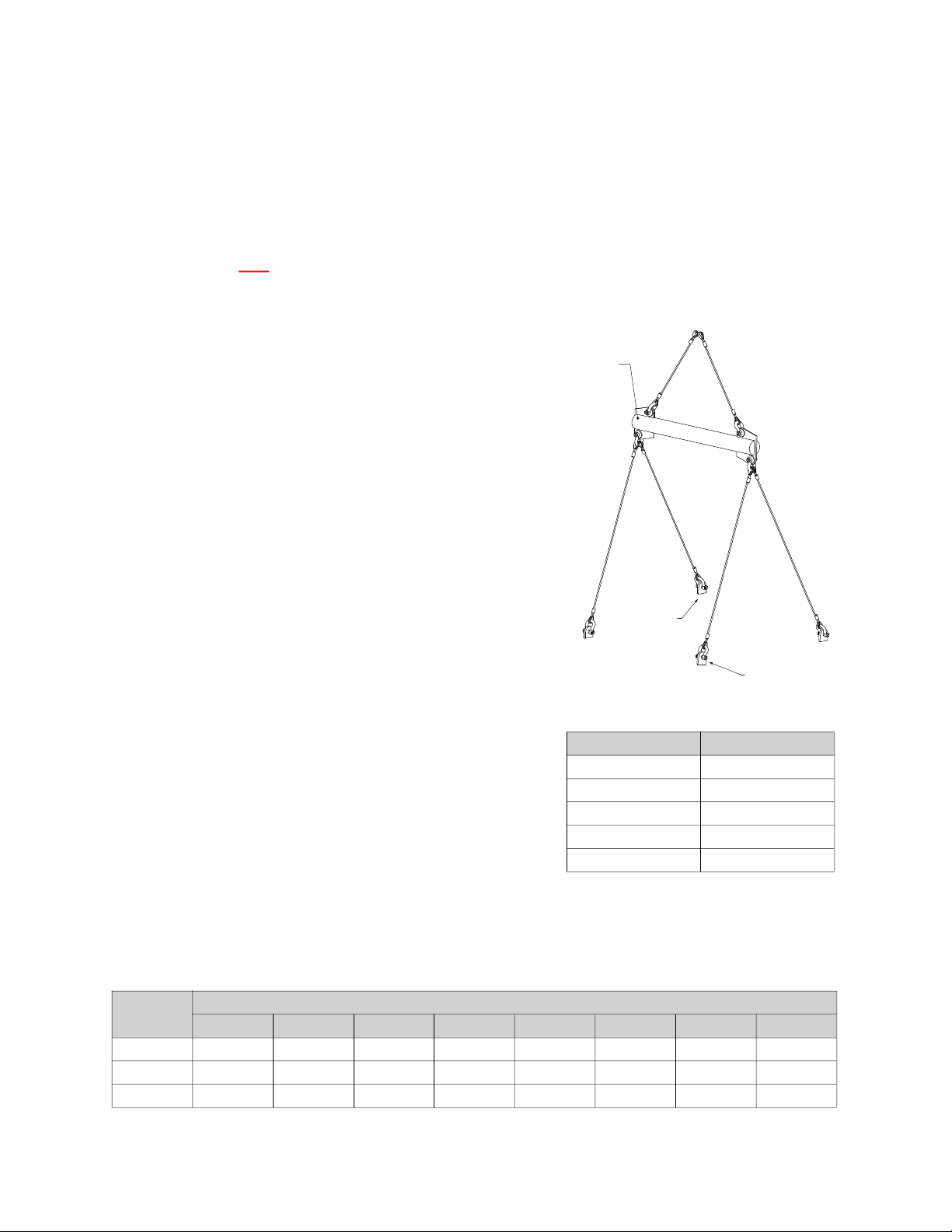
INSTALLATION
Spreader
Bar
Lifting Lugs
Lifting Lugs
It is imperative that this unit is installed and operated with the designed airflow and electrical supply in
accordance with this manual. If there are any questions about any items, please call the service
department at 1-866-784-6900 for warranty and technical support issues.
Mechanical
WARNING: DO NOT RAISE UNIT BY THE INTAKE HOOD, BLOWER, MOTOR SHAFT, OR
BEARINGS. USE ALL LIFTING LUGS PROVIDED WITH A SPREADER BAR OR SLING UNDER THE
UNIT.
Figure 1 - Spreader Bar
Site Preparation
1. Provide clearance around installation site to safely rig and
lift equipment into its final position (Figure 1). Supports
must adequately support equipment. Refer to
manufacturer’s estimated weights.
2. Locate unit close to the space it will serve to reduce long,
twisted duct runs.
3. Consider general service and installation space when
locating unit.
4. Do not allow air intake to face prevailing winds. Support
unit above ground or at roof level high enough to prevent
precipitation from being drawn into its inlet. The inlet must
also be located at least 10 feet away from any exhaust
vents. The fan inlet shall be located in accordance with the
applicable building code provisions for ventilation air.
Service Clearance
Refer to Table 1 for unit size clearance specifications. This will
allow for enough clearance in the front, back and sides of the
unit for servicing and maintenance of the unit.
Table 1 - Clearance Chart
Unit Size Clearance
1 24”
2 36”
3 42”
4 48”
5 54”
Common Electric Heater Calculations
Conversion:
1 KW = 3413
Load Requirement:
KW = (CFM x Temperature Rise) / 3160
Line Current (1 Phase):
Amperage = (KW x 1000) / Volts
Applied vs Rated KW Factors
Rated
Voltage
208 .92 1.00 1.12 1.22 1.33 - - -
460 - - - - - .91 1.00 1.09
480 - - - - - .84 .92 1.00
200 208 220 230 240 440 460 480
Applied Voltage
4
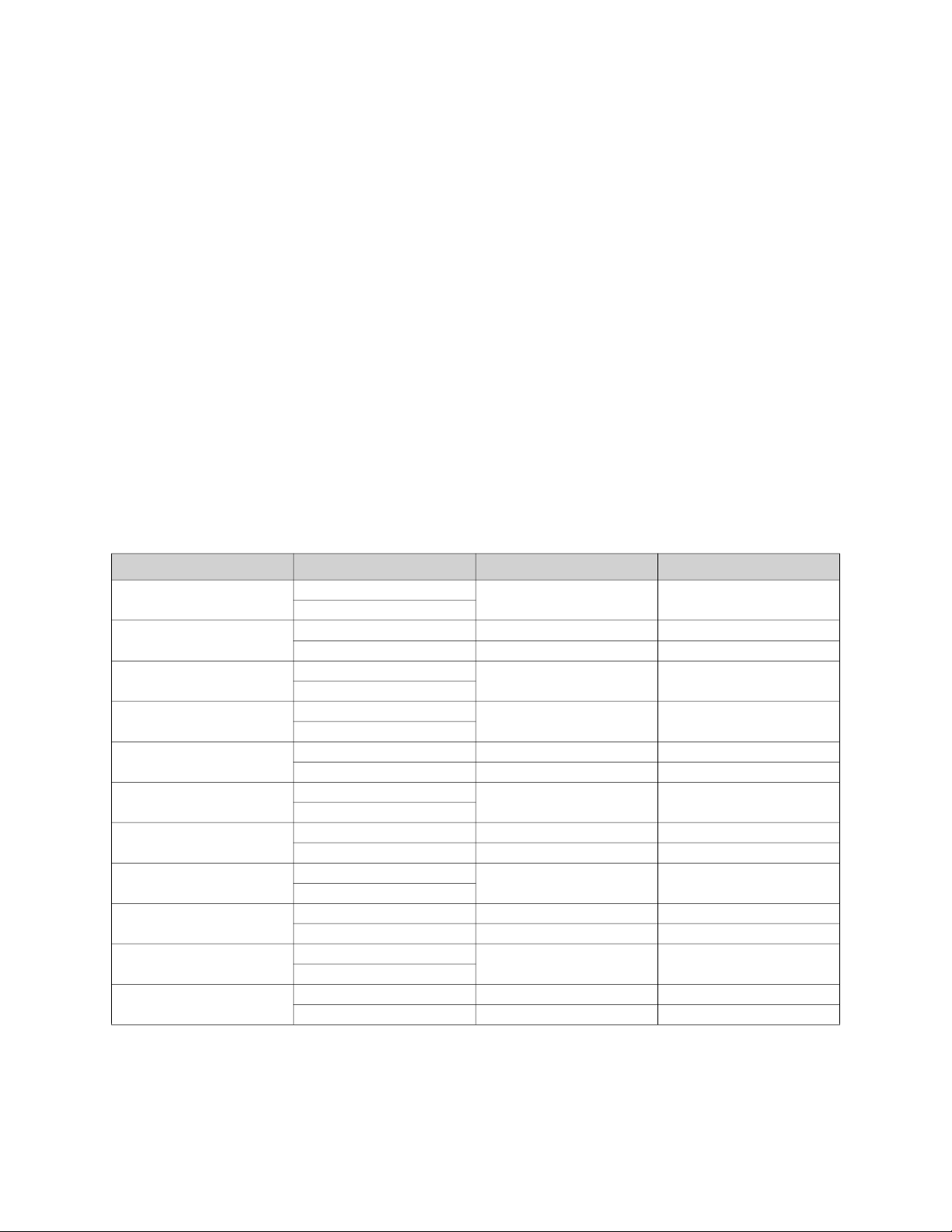
Curb and Ductwork
This fan was specified for a specific CFM and static pressure. The ductwork attached to this unit will
significantly affect airflow performance. When using rectangular ductwork, elbows must be radius throat,
radius back with turning vanes. Flexible ductwork and square throat/square back elbows should not be
used. Any transitions and/or turns in the ductwork near the fan outlet will cause system effect. System
effect will drastically increase the static pressure and reduce airflow.
• Table 2 shows the minimum fan outlet duct sizes and straight lengths required for optimal fan
performance.
• Do not use the unit to support ductwork in any way. This may cause damage to the unit.
• Follow SMACNA standards and manufacturer's requirements for the duct runs. Fans designed
for rooftop installation should be installed on a prefabricated or factory-built roof curb.
• Follow curb manufacturer’s instructions for proper curb installation.
• The unit should be installed on a curb and/or rail that meets local code height requirements.
• Make sure the duct connection and fan outlet are properly aligned and sealed.
• Secure fan to curb through vertical portion of the ventilator base assembly flange. Use a minimum of
eight (8) lug screws, anchor bolts, or other suitable fasteners (not furnished). Shims may be required
depending upon curb installation and roofing material.
• Verify all fasteners are secure. Figure 3 through Figure 6 show different mechanical installations.
Table 2 - Required Supply Ductwork
Blower Size (Inches) Discharge Duct Size Straight Duct Length*
10
15D, 16Z, 18Z
12
15
20D, 20Z, 22Z
18
24D, 25Z
20
30D, 28Z
25
36D
Side
Down
Side 20” x 20” 72”
Down 14” x 14” 48”
Side
Down
Side
Down
Side 26” x 26” 108”
Down 20” x 20” 72”
Side
Down
Side 30” x 30” 108”
Down 24” x 24” 86”
Side
Down
Side 32” x 32” 168”
Down 26” x 26” 108”
Side
Down
Side 36” x 36” 189”
Down 32” x 32” 168”
14” x 14” 48”
16” x 16” 54”
20” x 20” 72”
24” x 24” 86”
26” x 26” 108”
32” x 32” 168”
6
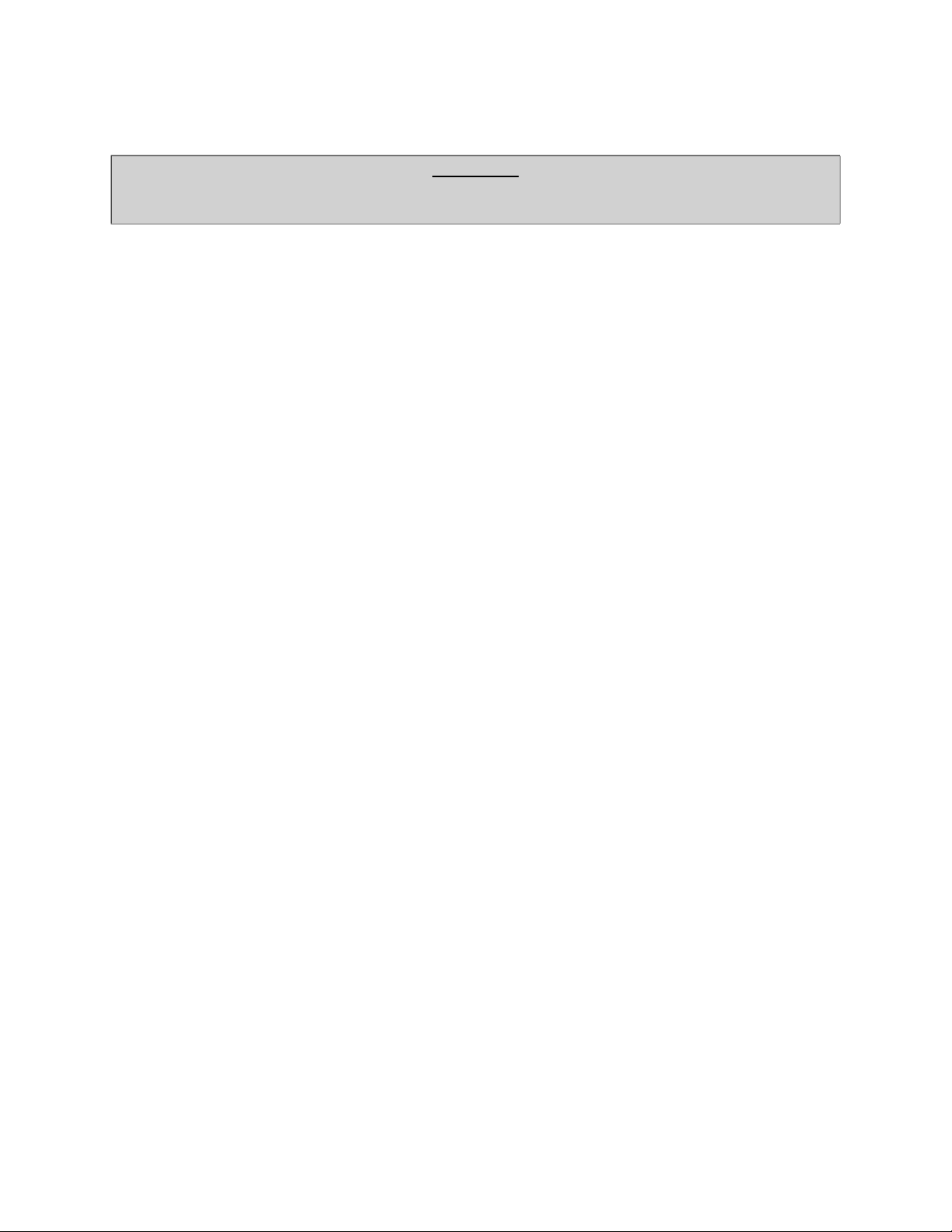
ELECTRICAL
WARNING!!
Disconnect power before installing or servicing unit. High voltage electrical input is needed for
this equipment. A qualified electrician should perform this work.
Before connecting power to the heater, read and understand the entire section of this document. As-built
wiring diagrams are furnished with each unit by the factory and are attached to the control module’s door
or provided with paperwork packet.
Electrical wiring (Table 3) and connections must be made in accordance with local ordinances and the
National Electric Code, ANSI/NFPA 70. Verify the voltage and phase of the power supply, and the wire
amperage capacity is in accordance with the unit nameplate. For additional safety information, refer to
AMCA publication 410-96, Recommended Safety Practices for Users and Installers of Industrial and
Commercial Fans.
1. Always disconnect power before working on or near this equipment. Lock and tag the
disconnect switch and/or breaker to prevent accidental power-up.
2. An electrical drop containing the line voltage power wiring is shipped with every unit. The electrical
drop should be brought through one of the conduit openings located in the base of the unit (Figure 3),
run through the curb, and connected to a junction box inside the building.
3. A dedicated branch circuit should supply the motor circuit with short circuit protection according to the
National Electric Code. This dedicated branch should run to the junction box.
4. A separate power source should supply the electric coil power. Power from the building breaker
should be wired directly to the coil disconnect. This should be done using wire of the proper gauge as
indicated in Table 3. A hole must be drilled in the fan enclosure to properly run the electric coil
power.
5. Verify that the power source is compatible with the requirements of your equipment. The nameplate
identifies the proper phase and voltage of the equipment.
6. Units shipped with a remote HMI will require a second drop through the base of the unit. It is important
to route the motor wires in a separate conduit from the HMI wiring. Refer to Figure 3.
7. Before connecting the unit to the building’s power source, verify that the power source wiring is deenergized.
8. Secure the power cable to prevent contact with sharp objects.
9. Do not kink power cable and never allow the cable to encounter oil, grease, hot surfaces, or chemicals.
10. Before powering up the unit, make sure that the fan rotates freely. Make sure that the interior of the unit
is free of loose debris or shipping materials.
11. If any of the original wire supplied with the unit must be replaced, it must be replaced with type THHN
wire or equivalent.
WARNING: ELECTRIC HEATERS HAVE TWO POWER INPUTS. THE EXTERNAL DISCONNECT
INTERRUPTS POWER TO THE MOTOR AND CONTROLS ONLY. THE ELECTRIC COIL POWER IS
INTERRUPTED BY THE DISCONNECT SWITCH ON THE ELECTRIC COIL DOOR.
10