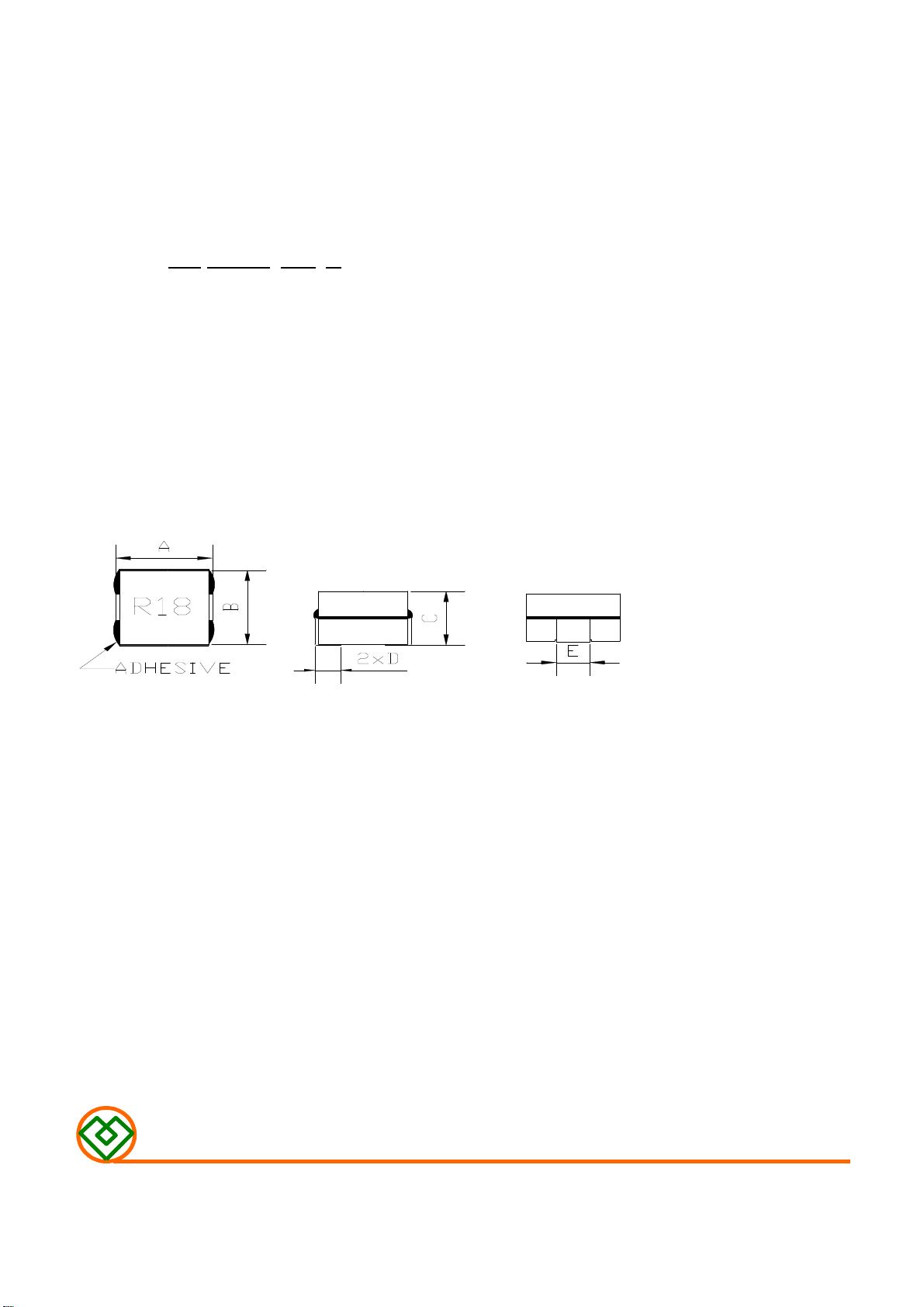
This specification applies to the Pb Free high current type SMD inductors for
MSI-121006-SERIES
PRODUCT INDENTIFICATION
(1) SHAPES AND DIMENSIONS
A: 12.1 Max. mm
B: 10.0 Max. mm
C: 6.0 Max. mm
D: 2.54±0.25 mm
E: 3.94±0.25 mm
(2) ELECTRICAL SPECIFICATIONS
SEE TABLE 1
TEST INSTRUMENTS
L : HP 4284A PRECISION LCR METER (or equivalent)
RDC : CHROMA MODEL 16502 MILLIOHMMETER (or equivalent)
(3)-1 Operate temperature range ...... -40℃~+125℃
(Including self temp. rise)
(3)-2 Storage temperature range ...... -40℃~+125℃
MSI-121006-SERIES Page 1/8
IDC1 :WK3255B+3265B (or equivalent)
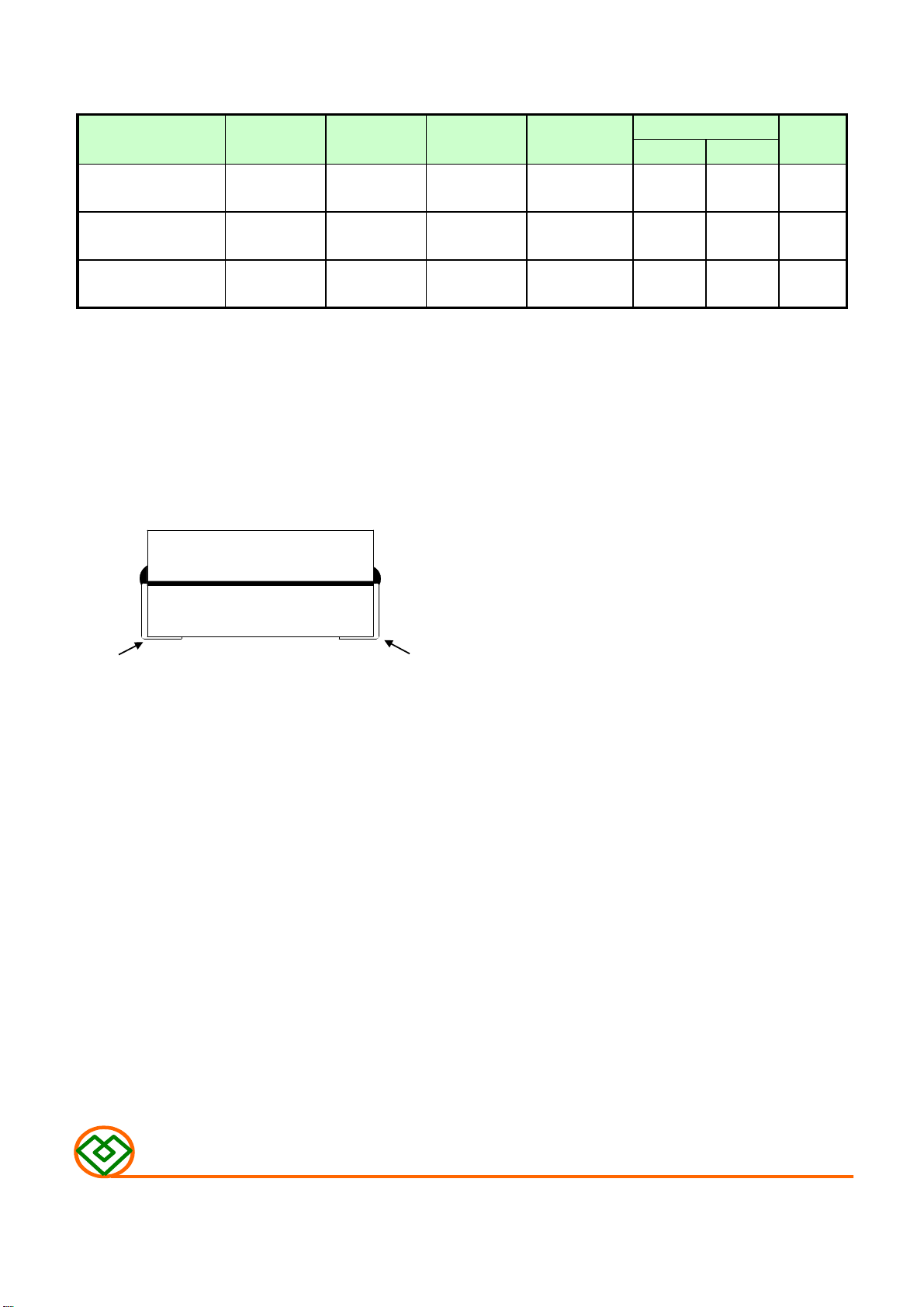
Inductance Percent Test Resistance Rated DC Current
L(μH) Tolerance Frequency RDC(mΩ) IDC1(A) IDC2(A)
0.18 L,M 100kHz/0.1V 0.48 ±6.5% 55 36 R18
0.23 L,M 100kHz/0.1V 0.48 ±6.5% 47 36 R23
0.36 L,M 100kHz/0.1V 0.48 ±6.5% 30 36 R36
※ □ specify the inductance tolerance,L(±15%),M(±20%)
※ IDC1: Based on inductance change (△L/Lo:drop 20% Typ.)@ ambient temp. 25℃
IDC2: Based on temperature rise (△T: 40℃ TYP.)
Rated DC Current: The less value which is IDC1 or IDC2 .
The nominal DCR is measured from point 〝a〞to point〝b〞.
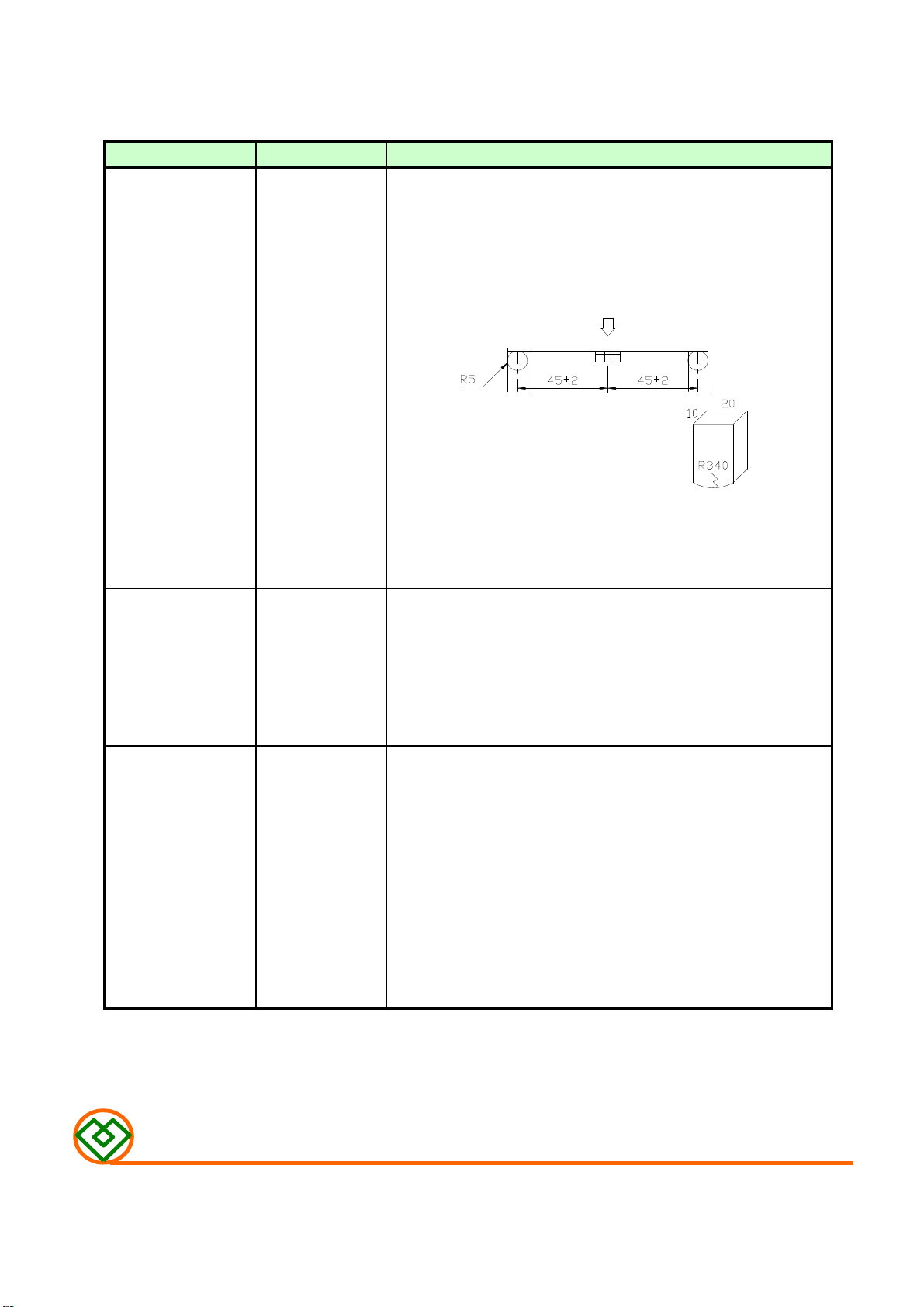
(4) RELIABILITY TEST METHOD
MECHANICAL
TEST ITEM SPECIFICATION TEST DETAILS
Substrate bending
△L/Lo≦±5%
The sample shall be soldered onto the printed circuit board
in figure 1 and a load applied unitil the figure in the arrow
There shall be direction is made approximately 3mm.(keep time 30 seconds)
no mechanical PCB dimension shall the page 7/9
damage or elec- F(Pressurization)
trical damege.
Vibration
△L/Lo≦±5%
The sample shall be soldered onto the printed circuit board
and when a vibration having an amplitude of 1.52mm
There shall be and a frequency of from 10 to 55Hz/1 minute repeated should
no mechanical be applied to the 3 directions (X,Y,Z) for 2 hours each.
damage. (A total of 6 hours)
Solderability
New solder Flux (rosin, isopropyl alcohol{JIS-K-1522}) shall be coated
More than 90% over the whole of the sample before hard, the sample shall
then be preheated for about 2 minutes in a temperature of
130~150℃ and after it has been immersed to a depth 0.5mm
below for 3±0.2 seconds fully in molten solder M705 with
More than 90% of the electrode sections shall be couered
with new solder smoothly when the sample is taken out of
the solder bath.
Page-3/8

MECHANICAL
TEST ITEM SPECIFICATION
Resistance to There shall be Temperature profile of reflow soldering
Soldering heat no damage or
(reflow soldering) problems.
The specimen shall be passed through the reflow oven with the
condition shown in the above profile for 1 time.
The specimen shall be stored at standard atmospheric conditions
for 1 hour, after which the measurement shall be made.
ELECTRICAL
TEST ITEM SPECIFICATION TEST DETAILS
Temperature
△L/L20℃≦±10%
The test shall be performed after the sample has stabilized in
0~2000 ppm/℃ an ambient temperature of -20 to +85℃,and the value
calculated based on the value applicable in a normal
temperature and narmal humidity shall be △L/L20℃≦±10%.
soldering
(Peak temperature 260±3℃ 10 sec
Slow cooling
(Stored at room
temperature)

ENVIROMENT CHARACTERISTICS
TEST ITEM SPECIFICATION
High temperature
△L/Lo≦±5%
The sample shall be left for 96±4 hours in an atmospere with
a temperature of 125℃ and a normal humidity.
There shall be Upon completion of the measurement shall be made after the
no mechanical sample has been left in a normal temperature and normal
damage. humidity for 1 hour.
Low temperature
△L/Lo≦±5%
The sample shall be left for 96±4 hours in an atmosphere with
There shall be Upon completion of the test, the measurement shall be made
no mechanical after the sample has been left in a normal temperature and
damage. normal humidity for 1 hour.
Change of
△L/Lo≦±5%
The sample shall be subject to 5 continuos cycles, such as shown
temperature in the table 2 below and then it shall be subjected to standard
There shall be stmospheric conditions for 1 hour, after which measurement
no other dama- shall be made.
ge of problems
table 2
Temperature Duration
(Themostat No.1)
Standard
atmospheric
(Themostat No.2)
Standard
atmospheric
Moisture storage
△L/Lo≦±5%
The sample shall be left for 96±4 hours in a temperature of
40±2℃ and a humidity(RH) of 90~95%.
There shall be Upon completion of the test, the measurement shall be made
no mechanical after the sample has been left in a normal temperature and
damage. normal humidity more than 1 hour.
The sample shall be reflow soldered onto the printed circuit board in every test.
Page-5/8

(5) LAND DIMENSION (Ref.)
(5)-1 LAND PATTERN DIMENSIONS(mm)
(STANDARD PATTERN)
(5)-2 SUBSTRATE BENDING TEST BENDING TEST BOARD
Page-6/8

(6) PACKAGING
(6)-1 CARRIER TAPE DIMENSIONS (mm)
(6)-2 TAPING DIMENSIONS (mm)
Page-7/8

(6)-3 REEL DIMENSIONS (mm)
(6)-4 QUANTITY
500pcs/Reel
The products are packaged so that no damage will be sustained.
Page-8/8

TYPICAL ELECTRICAL CHARACTERISTICS
INDUCTANCE vs. DC CURRENT@100kHz/0.1V
Ambient Temperature : 25℃
Temperature Rise vs. DC Current
ATTACHMENT-1
0.00
0.05
0.10
0.15
0.20
0.25
0.30
0.35
0.40
0 10 20 30 40 50 60 70
0
10
20
30
40
50
60
0 10 20 30 40 50 60