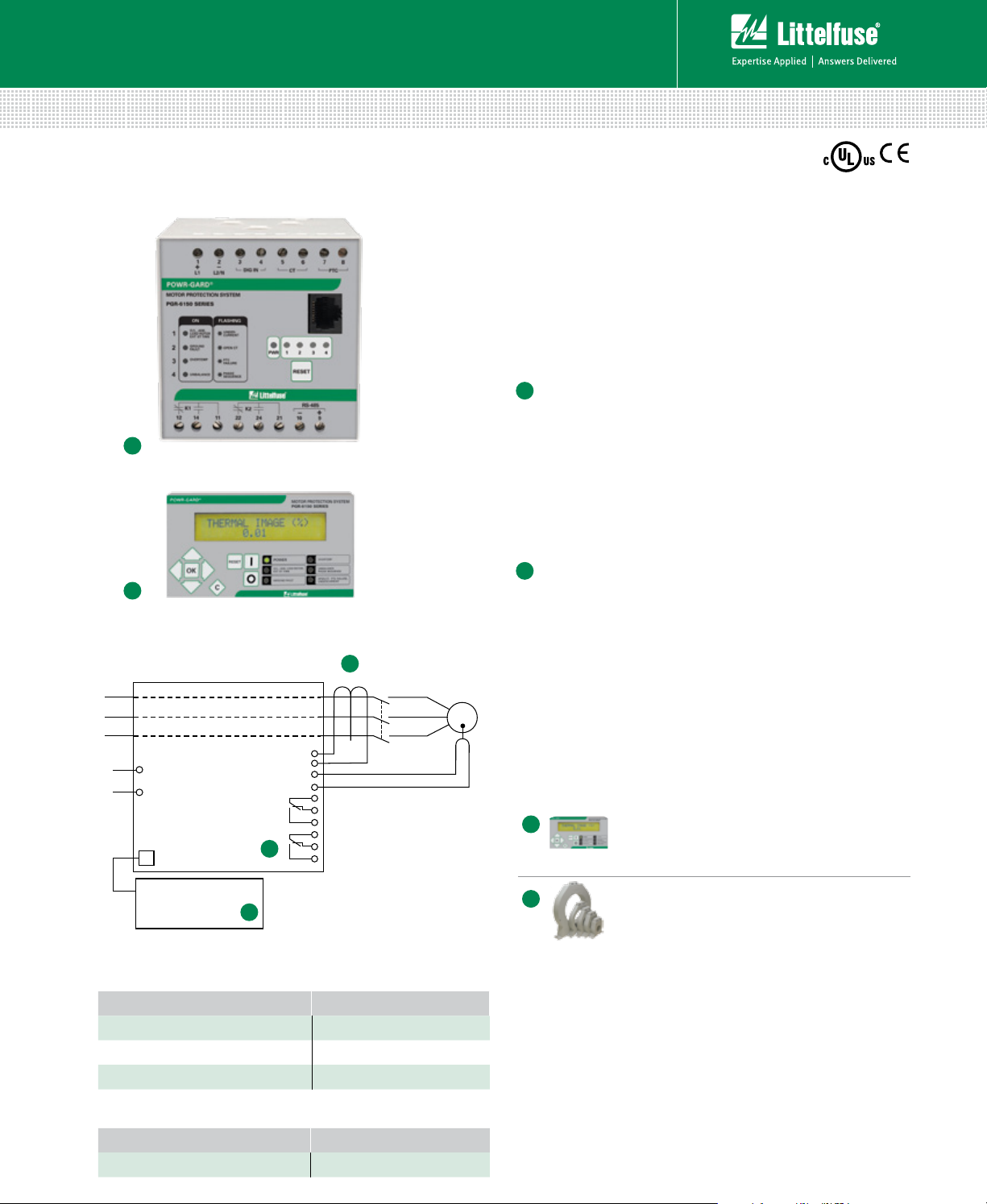
Protection Relays & Controls
M
PGR-6150
PTC
(Operator Interface)
(Motor Protection System)
PGR-6150-OPI
L2
L1
GF CT
Motor Protection–Standard (PGR 6000 Family)
PGR-6150 SERIES
Motor Protection System
1
Description
The PGR-6150 Motor Protection System provides 13 protective
functions by utilizing both current and temperature inputs. It is
a modular system consisting of the control unit and an operator
interface (PGR-6150-OPI). The OPI allows programming and
displays metered values. The PGR-6150 is used to provide
current- and temperature-based protection, metering and data
logging for three-phase motors used in industrial environments.
Current transformers are not required for currents up to 25 A.
1
Control Unit
g
Integrated phase CTs (external for applications > 25 A)
g
Ground-fault CT input
g
One PTC input and one programmable input
g
Two programmable output contacts
g
Eight status LEDs
g
RS-485 Communications
g
DIN-rail mountable
g
PC interface software
A
Simplified Circuit Diagram
B
1
A
Ordering Information
ORDERING NUMBER CONTROL POWER
PGR-6150-24 (Control Unit) 24/48 Vdc
PGR-6150-120 (Control Unit) 120/240 Vac/dc
PGR-6150-OPI (Operator Interface) Powered by Control Unit
NOTE: External CTs can be used for full-load currents >25 A.
Operator Interface (optional)
A
g
Large, bright, LCD display
(2 x 20 alphanumeric characters)
g
Keypad for menu selection (system parameters,
measurements, and fault reports)
g
Displays metered values
g
Six user-programmable LEDs
g
Powered by Control Unit
g
1 meter (39-inch) connection cable included
Accessories
A
B
PGR-6150-OPI Operator Interface
Optional Operator Interface for displaying
metered values and programming
PGC-6000 Series Ground-Fault Transformer
Optional zero-sequence current transformer,
used to measure ground-fault current.
Required for applications >25 A.
ACCESSORIES REQUIREMENT
PGC-6000 Series Optional
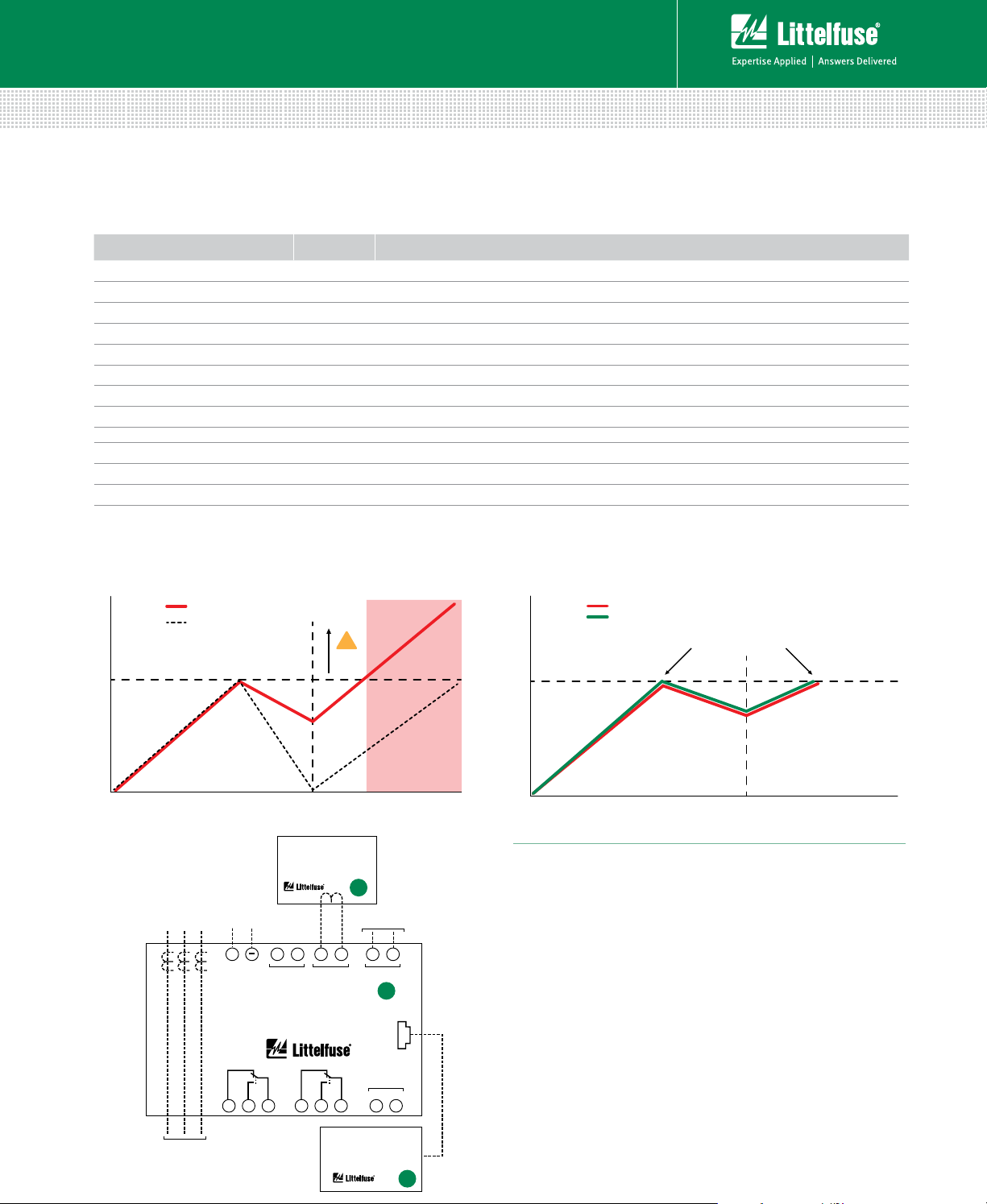
Protection Relays & Controls
Motor Protection–Standard (PGR 6000 Family)
PGR-6150 SERIES
Motor Protection System
Features & Benefits
FEATURES IEEE # BENEFITS
No CTs required 49, 51 No current transformers are required for currents < 25 A
Adjustable trip settings Adjustable overload trip class setting from 5 to 45 to match motor characteristics
Digital input Programmable digital input
Output contacts Two programmable Form C output contacts for operation of separate annunciation and trip circuits
Overload
Overcurrent/Jam 50, 51 Detects catastrophic failures and fires; extends motor life
Undercurrent 37 Detects low level or no-load conditions
Unbalance (current)
Phase loss/
Phase sequence 46 Detects unhealthy supply conditions
PTC overtemperature
Dynamic thermal model
Communications
49, 51 Extends motor life and prevents insulation failures and fires
46 Prevents overheating due to unbalanced phases
49 Detect high ambient or blocked ventilation and single phasing; prevents shaft/pump damage
Provides protection through starting, running, overload, and cooling cycles
RS-485 communications to remotely display metered values
Dynamic Thermal Modeling
Motor
Traditional
Overload
Maximum Operating Temperature
Temperature
Traditional Overload resets
before motor has cooled down
Time
Wiring Diagram
GROUND-FAULT
CURRENT TRANSFORMER
PGC-6000 SERIES
3
DIGITAL
INPUTS
(optional)
5
4
3 PHASE CTs
BUILT INTO RELAY.
EXTERNAL CTs
REQUIRED FOR
FLA >25 A.
FEEDER TO MOTOR
CONTROL
POWER
+
L2/NL1
MOTOR PROTECTION SYSTEM
PGR-6150 SERIES
K1 K2
1214 11 2224 21
For every 10°C over
insulation temperature
rating the motor loses
50% of its life span.
!
Damage is caused,
decreases motor life
B
TEMPERATURE
INPUT
7
6
CTGF
8
PTC
1
RS-485
–
10 9
OPERATOR INTERFACE
PGR-6150-OPI
(optional)
With Thermal MemoryWithout Thermal Memory
Motor
PGR-6150
Maximum Operating Temperature
With PGR-6150 the
temperature is not exceeded,
no damage to motor
Temperature
Specifications
Protective Functions
(IEEE Device Numbers)
Overload (49, 51)
Phase sequence (46)
Overcurrent (50, 51)
Jam
Ground fault (50G/N, 51G/N)
Undercurrent (37)
Input Voltage 110-230 Vac/ Vdc; 24/48 Vdc, 5 W
AC Measurements RMS, 16 samples/cycle
Frequency 50, 60 Hz
Dimensions
(Control Unit) H 83 mm (3.3”); W 78 mm (3.1”); D 99 mm (3.9”)
(Operator Interface) H 56 mm (2.2”); W 106 mm (4.2”); D 22.8 mm (0.9”)
+
Output Contacts Two Form C
Communications RS-485 with Modbus
Approvals UL Listed (E353735), CE (European Union)
Warranty 5 years
Mounting DIN (Control Unit); Panel (Operator Interface)
A
PTC overtemperature (49)
Failure to accelerate
RTD temperature (49)
Unbalance (current) (46)
Starts per hour (66)
Phase loss (current) (46)
®
RTU