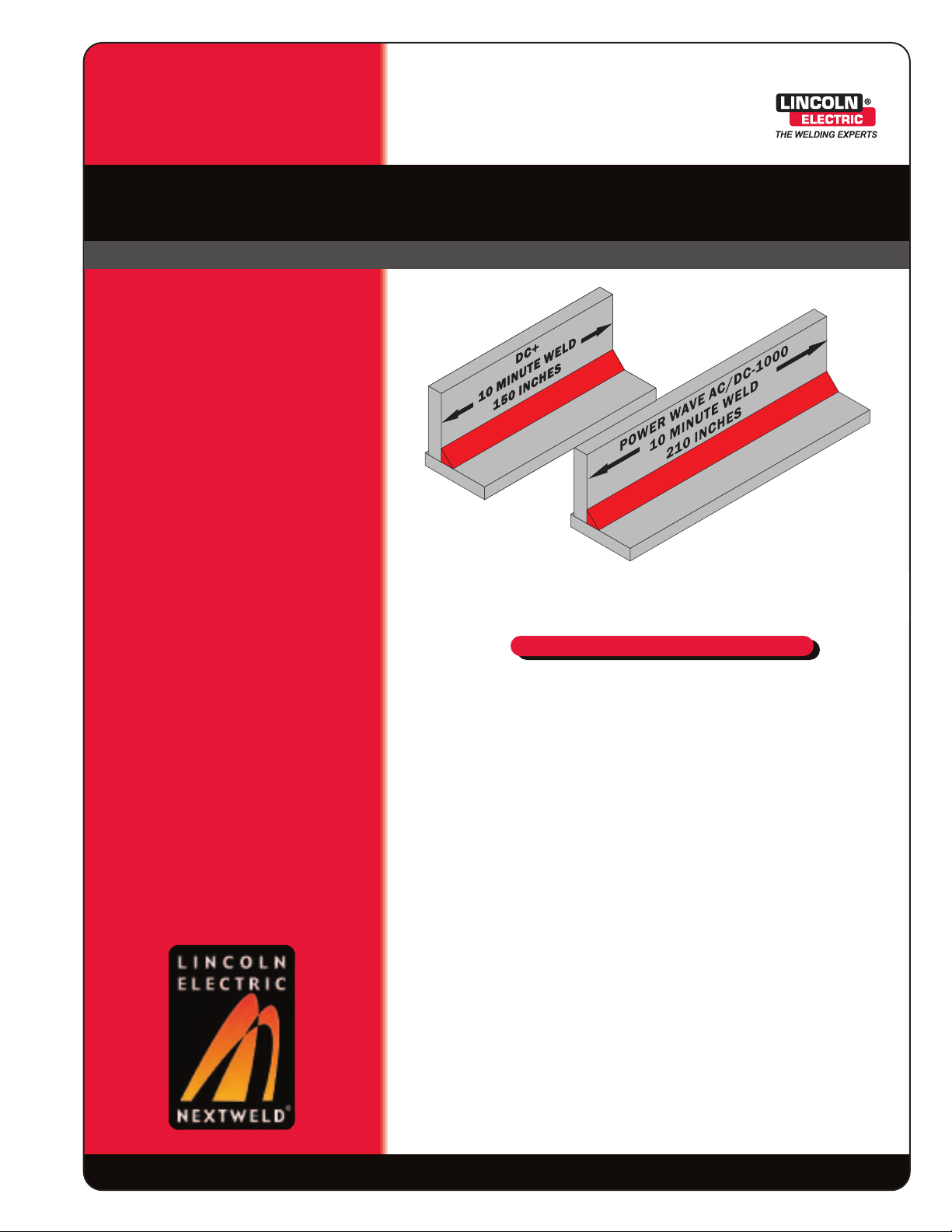
APPLICATION
WAVEFORM CONTROL TECHNOLOGY
TM
Making Fillet Welds with Power Wave AC/DC 1000™ System
Welding Guide
Now from Lincoln - the power
to increase productivity with
Power Wave technology!
Lincoln Power Wave technology
based upon the new Power Wave
AC/DC 1000™ power source
provides the opportunity to
significantly lower the cost of
making fillet welds and at the
same time, makes many of the
issues that cause weld defects
a thing of the past. In some
respects, the Power Wave AC/DC
1000™ describes both a new
generation of equipment and
a new technology for
controlled welding.
Now, from a single power source
it is possible to choose the very
best type of arc characteristic for
the particular job at hand. The
Power Wave AC/DC 1000™
system allows the choice of the
appropriate voltage-current
relationship at the mere “flick
of a switch”.
advantages
CHOICE AT THE “FLICK OF A SWITCH”
• Constant current (sometimes referred to as variable voltage).
• Constant voltage.
• Square Wave AC.
UNLIMITED AC OUTPUT TAILORING
• Choice of AC frequency (from 10 Hz to 100 Hz).
• Wave balance control to allow more or less DC
positive component.
• Offsetting the AC wave to change the magnitude of the
negative or positive component.
40% Increase in Travel Speed
5/16” (8mm) Horizontal Fillet Weld
5/32” (4mm) Dia. Electrode
525 Amperes (Both Welds)
REDUCTION IN DEFECTS
• Virtual elimination of arc-striking problems.
• Virtual elimination of arc blow.
LOWER COSTS
• Documented productivity increases over conventional
submerged arc welding.
Patented. This product is protected by one or more of the following United States patents: 6,809,292;
6,795,778; 6,700,097; 6,697,701; 6,683,278; 6,660,966; 6,600,134; 6,683,278; 6,596,570; 6,570,130;
6,536,660; 6,489,952; 6,472,634; 6,636,776; 6,486,439; 6,441,342; 6,365,874; 6,291,798; 6,207,929;
6,111,216; 4,927,041; 4,861,965 and other pending U.S. patents. Similar patents are maintained in
other countries.
The future of welding is here.
NX-3.50 5/05© Copyright 2005 The Lincoln Electric Company. All rights reserved.
®
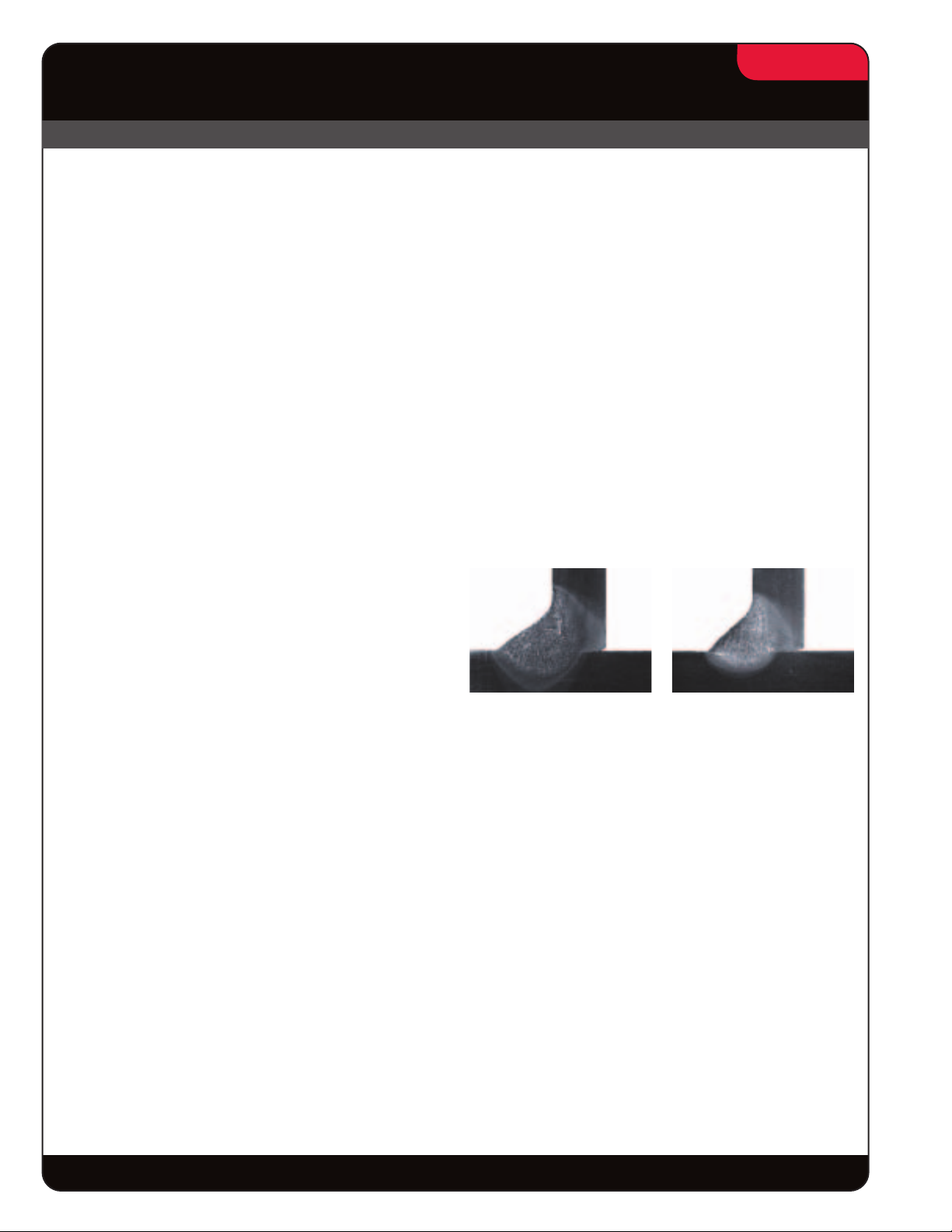
WAVEFORM CONTROL TECHNOLOGY
TM
Making Fillet Welds with Power Wave AC/DC 1000™ System
Welding Guide
APPLICATION
2/10
DC welding has almost always been the preferred
choice for producing submerged arc welds. Some of
these reasons are:
contaminants, organic and/or inorganic contaminants
in or on the steel and greater potential for slag
entrapment because of the larger and “colder” weld
puddle. DC negative has always been the method of
1. Lowest capital cost for equipment.
2. Greater arc stability than with AC.
3. Virtual elimination of arc striking problems.
4. Power issues (single phase vs. three phase
balanced power)
choice for welding off-analysis steel or dirty steel
where it is desirable to have minimum dilution. But
with Power Wave AC/DC 1000™ technology, this is
no longer the best option. The Power Wave AC/DC
1000™ provides the capability of easily using the best
welding mode for the job at hand.
While DC negative may offer the highest deposit rate
per ampere, it is seldom used for automatic welding
that must meet stringent code requirements. This is
because DC negative is more prone to magnetic arc
interference (arc blow), porosity resulting from
Understanding Power Wave AC/DC 1000
To fully understand the potential for possible
productivity gains using the Power Wave AC/DC
1000™ system, understanding the major AC
components and what they contribute is helpful.
The major components consist of:
1. Square wave (vs. a conventional sine wave)
2. Square wave balance
3. Square wave offset
4. Square wave frequency
Figure 1 shows photographs of two 5/16” (8mm)
1
horizontal fillet welds
. One is made using a good
DC+ procedure and one using a square wave 25%
balanced, (-)10% offset and 30 Hz. Both are excellent
fillets but the square wave procedure is forty percent
faster! Note that the amperage used is virtually the
same, 520 vs. 527 amperes.
40% faster travel speeds by using Power Wave AC/DC
1000™ Square Wave procedures over DC+ procedures.
DC+
527 Amps
Figure 1
™
AC/DC
520 Amps
1
These welds comply with the geometry requirements for leg and throat dimensions of all AWS codes.
The future of welding is here.
®
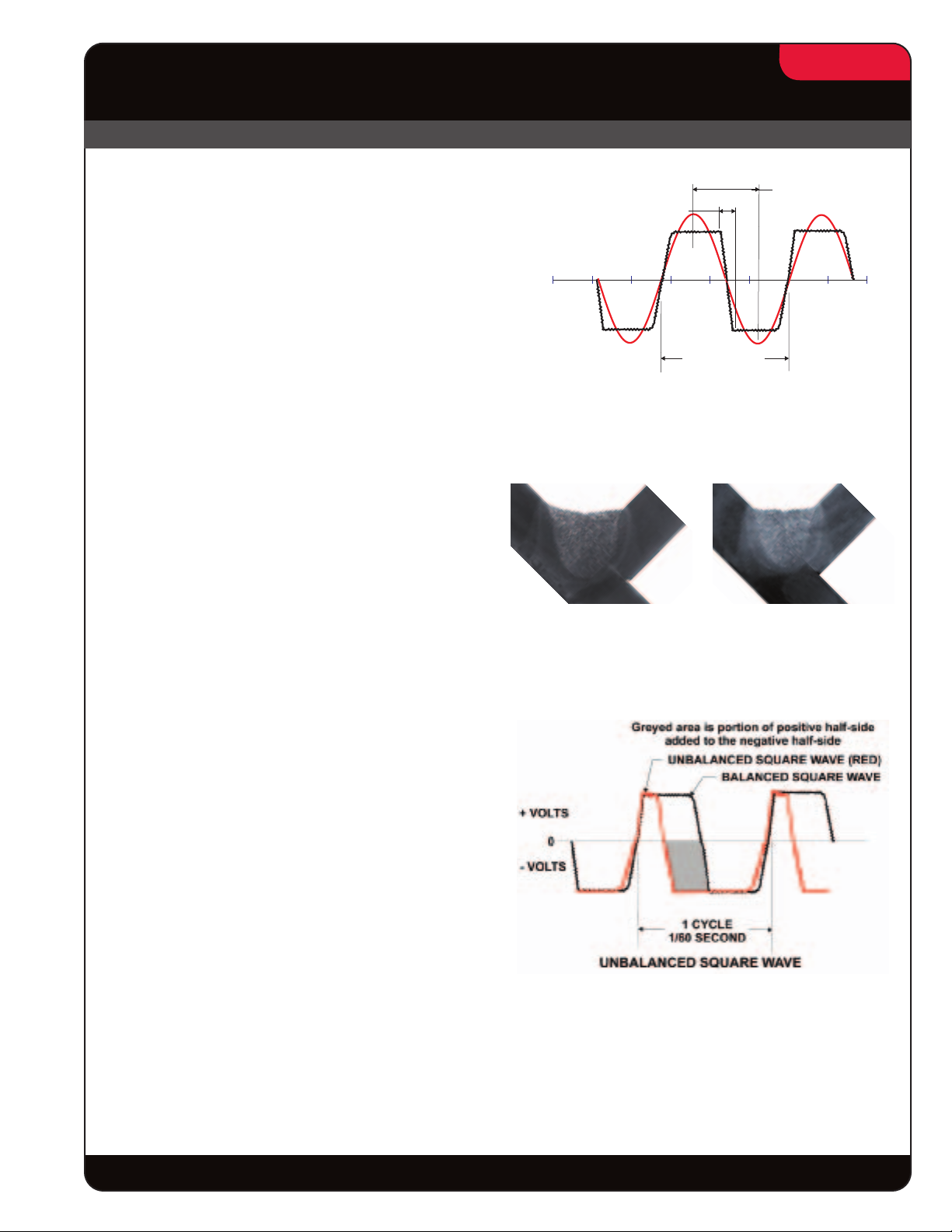
WAVEFORM CONTROL TECHNOLOGY
TM
Making Fillet Welds with Power Wave AC/DC 1000™ System
Welding Guide
APPLICATION
3/10
Square Wave vs. Sine Wave
Figure 2 shows one cycle of a true 60 Hz sine wave
with a square wave superimposed upon it. Note that
while the rms2value and the peak values are the same
for both waves, the transition time for peak-to-peak is
much shorter for the square wave. The transition
period is what has always caused instability with
conventional AC welding but with the rapid transition
associated with the Power Wave AC/DC 1000™, arc
stability is increased.
Square Wave Balance
Square wave balance can allow the arc to act more
as a DC negative or DC positive arc, thus increasing
deposition rate or increasing penetration. This is
always expressed as a percentage of the DC +
component. i.e., (25% Balance means that only 25%
of the cycle will be positive while 75% of the cycle will
be negative, etc.)
Figure 3 shows two 3/8” (10mm) flat positioned fillet
welds. Both were made at 814 amperes but the square
wave AC 25% balance wave is made 17% faster.
Figure 4 graphically shows the significance that square
wave balance can and does play. Note that only 25%
of the time is the arc positive while 75% of the time
it is negative. This flexibility can be used to tailor the
arc to achieve best results by increasing deposition,
decreasing penetration or decreasing deposition and
increasing penetration.
SQUARE WAVE
TRANSITION
REGION
+ VOLTS
0
- VOLTS
1 CYCLE
1/60 SECOND
60 Hz SINE WAVE vs 60 Hz SQUARE WAVE
Figure 2
DC+ AC 25% Balanced
Figure 3
SINE WAVE
TRANSITION
REGION
Figure 4
2
Rms: root-mean-square value of current or voltage. For example, when someone refers to, “110 volts,” this is actually an rms value as is
“30 volts AC”, etc.
The future of welding is here.
®