
PROCESS
WAVEFORM CONTROL TECHNOLOGY
®
Surface Tension Transfer®(STT®)
Surface Tension Transfer
®
(STT®) welding is a GMAW,
controlled short circuit transfer
process developed and
patented by The Lincoln
Electric Company.
Unlike standard CV GMAW
machines, the STT
®
machine
has no voltage control knob.
STT®uses current controls to
adjust the heat independent of wire
feed speed, so changes in electrode
extension do not affect heat.The STT
process makes welds that require low
heat input much easier without
overheating or burning through, and
distortion is minimized. Spatter and
fumes are reduced because the
electrode is not overheated–even with
larger diameter wires and 100% CO
2
shielding gas. This gas and wire
combination lowers consumable costs.
®
Conventional CV short circuit transfer
using CO2and .045" solid wire.
STT®using CO2and
.045" solid wire.
advantages
GOOD PENETRATION AND LOW HEAT
INPUT CONTROL
Ideal for welding on joints with open root, gaps, or on thin material with
no burnthrough.
REDUCED SPATTER AND FUMES
Current is controlled to achieve optimum metal transfer.
REDUCED COSTS
Ability to use 100% CO2or argon shielding gas blends with larger
diameter wires.
GOOD BEAD CONTROL AND FASTER
TRAVEL SPEEDS
Can replace GTAW in many applications without sacrificing appearance.
Patented.This product is protected by one or more of the following United States patents: 4,717,807;
4,897,523; 4,866,247; 4,835,360; 4,954,691; 4,972,064; 5,001,326; 5,003,154; 5,148,001;5,961,863;
6,051,810; 6,160,241; 6,274,854; 6,172,233; 6,215,100; 6,204,478.The application of the STT process for
root pass pipe welding and wallpapering of industrial vessels with nickel alloy sheets are patented.The
application of processes marketed by other welding manufacturers that are similar to STT may infringe on
these patents: 5,676,857; 5,742,029; 5,981,906; 6,093,906.
NX-2.20 11/06
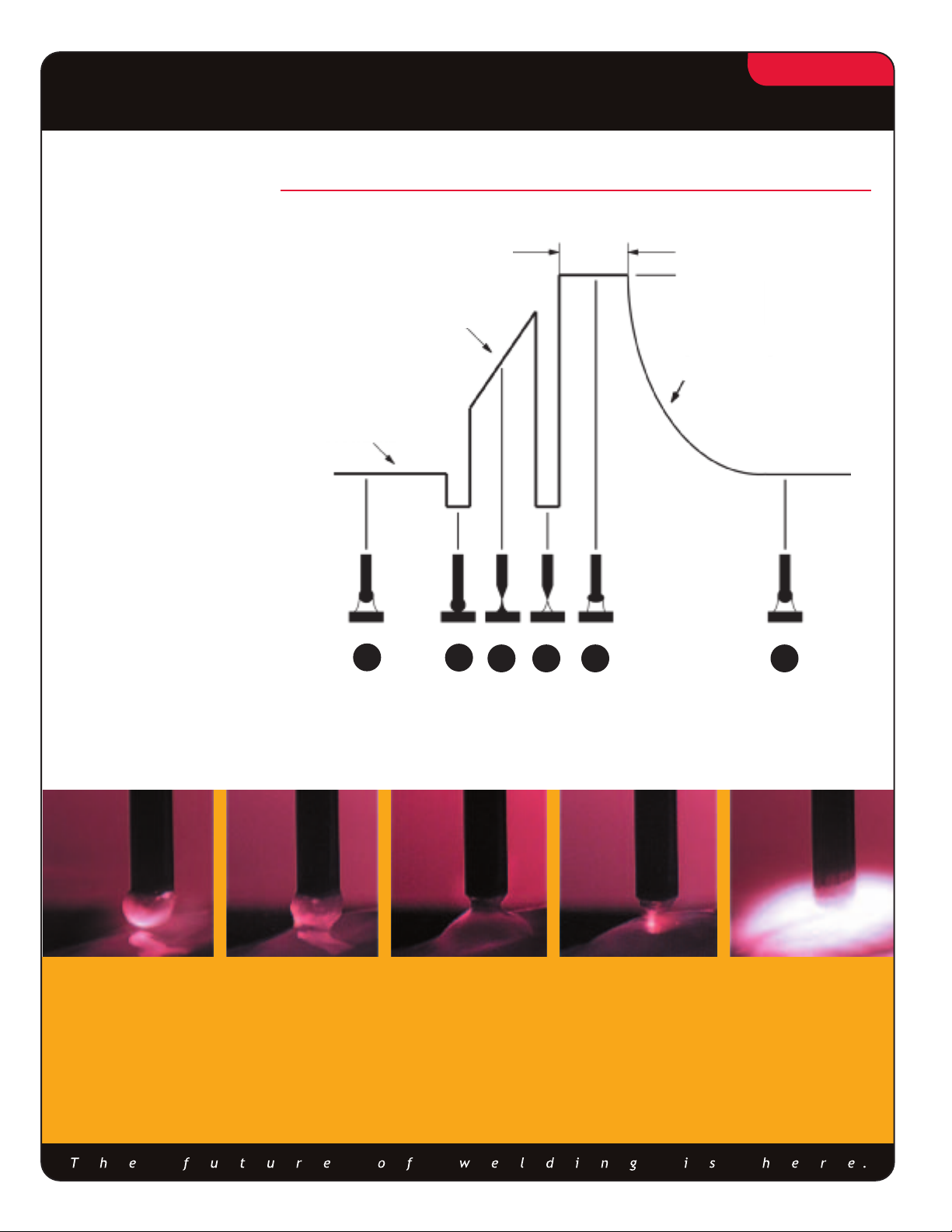
WAVEFORM CONTROL TECHNOLOGY®™
PROCESS
Surface Tension Transfer®(STT®)
How
STT®works
A BACKGROUND CURRENT
between 50 and 100 amps
maintains the arc and
contributes to base metal
heating. After the electrode
initially shorts to the weld
pool, the current is quickly
reduced to ensure a solid
short. PINCH CURRENT is
then applied to squeeze
molten metal down into the
pool while monitoring the
necking of the liquid bridge
from electrical signals. When
the liquid bridge is about to
break, the power source
reacts by reducing the current
to about 45-50 amps.
Immediately following the arc
re-establishment, a PEAK
CURRENT is applied to
produce plasma force pushing
down the weld pool to prevent
accidental short and to heat
the puddle and the joint.
Finally, exponential TAIL-OUT
is adjusted to regulate overall
heat input. BACKGROUND
CURRENT serves as a fine
heat control.
THE STT PROCESS
PINCH
CURRENT
BACKGROUND
CURRENT
A
PEAK TIME
B
C D E A
PEAK
CURRENT
TAIL-OUT
SPEED
2/4
The TAIL-OUT
CONTROL adjusts
the rate that the
current is changed
from PEAK to
BACKGROUND.
Basically, the TAILOUT is a coarse
heat control.
A. STT®produces a
uniform molten ball and
maintains it until the “ball”
shorts to the puddle.
B. When the “ball” shorts to
the puddle, the current is
reduced to a low level
allowing the molten ball to
wet into the puddle.
C. Automatically, a precision
PINCH CURRENT waveform
is applied to the short. During
this time, special circuitry
determines that the short is
about to break and reduces
the current to avoid the
spatter producing “explosion”.
D. STT®circuitry re-
establishes the welding arc
at a low current level.
E. STT®circuitry senses that
the arc is re-established, and
automatically applies PEAK
CURRENT, which sets the
proper arc length. Following
PEAK CURRENT, internal
circuitry automat-ically
switches to the
BACKGROUND
CURRENT, which serves as
a fine heat control.