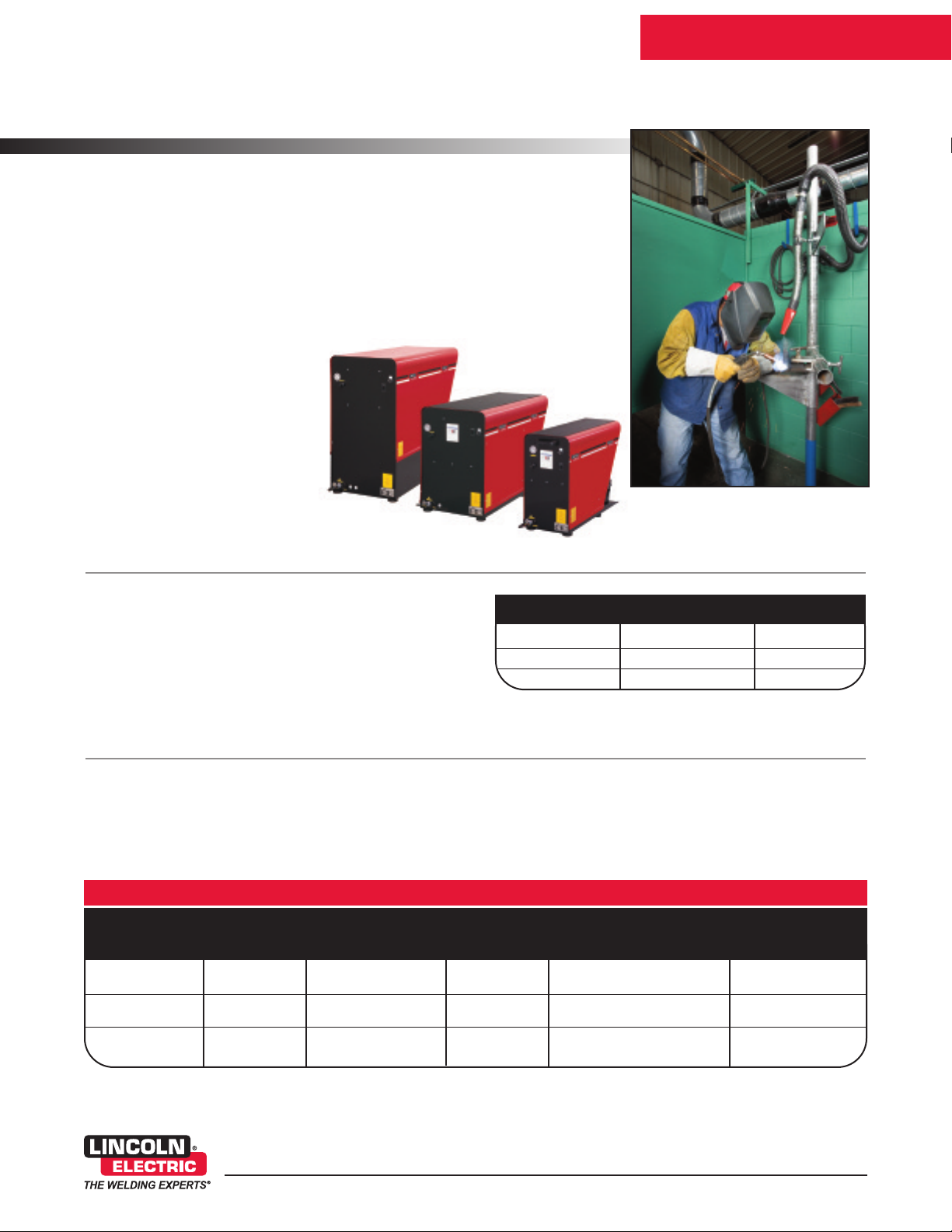
X-Tractor 3A, 5A & 8A
Welding Fume Extractor
Lincoln’s self contained X-Tractor units are specifically designed for the removal and
filtration of welding fume. They feature a high vacuum, low volume system with an
automatic self-cleaning filter system. They are suitable for heavy duty welding
applications and continuous use, powered by three phase AC motors.
These units are designed to supply suction for up to 8 fume guns or 5 suction heads.
Air enters the system through a connection on the rear side of the machine. It then
passes through the filter and the fume particles are captured in the filter media. The
air then passes through the blower and exits through an internal silencer. A timer
signals a pulse of compressed air that
loosens the particulate from the
outside surface of the filter so that
it falls to the bottom of the particulate
bin canister.
ENVIRONMENTAL SYSTEMS
Processes
Stick, TIG, MIG, Flux-Cored
Advantage Lincoln
• Integrated automatic filter cleaning
• Automatic operation capability using wire feeder trigger signal
• For 1 to 8 operators simultaneously
• Used as a stationary or mobile installation
• Rugged design for industrial use and impact resistance
• Large range of accessories available
• Compact design for easy installation in narrow spaces
Welding Fume Extractor Suction Nozzle Capacity Fume Gun Capacity
X-Tractor 3A 13
X-Tractor 5A 35
X-Tractor 8A 58
Note: Number of extraction nozzles/fume guns that can be connected to each system
is directly related to the overall lengths of duct and flex hose used for connection.
Base Unit Includes
• Extraction Unit
• Filter Cartridge
• Automatic Filter Cleaning System
TECHNICAL SPECIFICATIONS
Product Product Input H x W x D Net Weight
Name Number Power CFM mm (in.) kg (lbs.)
X-Tractor 3A L12810-1 230/3/60 165 1118 x 711 x 762 75
L12810-2 460/3/60 (44 x 28 x 30) (165)
X-Tractor 5A L12810-3 230/3/60 285 1397 x 711 x 838 129
L12810-4 460/3/60 (55 x 28 x 33) (285)
X-Tractor 8A L12810-5 230/3/60 475 1397 x 711 x 1118 215
L12810-6 460/3/60 (55 x 28 x 44) (475)
• Internal Compressed Air Regulator
• Automatic Operation Connection
• Starter/Overload Switch
Dimensions
Publication E13.19 3/08
www.lincolnelectric.com

A CLOSER LOOK
Automatic Filter Cleaning
The cleaning timer system is factory preset, but can be adjusted
based on the welding application and usage amounts.
The system consists of a holding tank with compressed air, a solenoid
value and a timer mounted directly on the solenoid valve. The tank is
filled with compressed air, the solenoid value opens at intervals set by
the timer, and compressed air is blown into the filter from the clean side.
Particulate stuck on the outside of the filter, drops off and into a dustbin.
The tank is then again filled with compressed air, awaiting the next cycle.
This cycle can be turned off by placing the filter cleaning switch on the
front panel in the OFF position.
Automatic Operation
The extraction unit can be operated in an automatic mode, where
the extraction system will operate based on the welding machine
status. Using an electromechanical relay circuit (provided by the
customer) the welding machine trigger voltage can be used to
operate a relay circuit which would be connected to the automatic
operation circuit of the extraction system. This provides extraction
demand only when welding is taking place.
Off-Line Filter Cleaning
In addition to the automatic cleaning function, there is also a built
in off-line cleaning function that operates the cleaning system when
the machine is shut down. When the unit is shut off, the signal to
the cleaning system solenoid is delayed by an additional timer placed
inside the cabinet. The timer extends the cleaning signal in order to
operate more cleaning cycles after the extraction is shut down. Inside
the filter container there is a backflow damper that closes the inlet in
order to avoid particulate re-entrance in the duct/hose system.
Shown: Front view
Shown: Back view
Easy-Duct System
The Easy-Duct system is specially designed for a leak-proof, simple
installation for up to 8 connection points. The duct system is designed
specifically to the layout of the welding facility. The engineering behind
the design takes into account welding facility layout, the number of
welding stations, welding processes, physical obstacles and overall duct
lengths to maintain specific airflow characteristics and provide an efficient
and effective solution. A requirement is a facility layout that will show
workplace locations, obstacles and extraction equipment location. The
duct system consists of a metal duct and related accessories to build an
extraction system for all types of welding environments.
High Vacuum/Low Volume System
High vacuum welding fume extraction systems utilize higher pressure of
70-90” WG and low volume of 50-100 CFM with an air speed of 40005000 ft/min. The air handling configuration of high vacuum equipment
allows the use of small diameter rigid duct and small diameter flexhose to
easily reach extraction points. It is perfect for applications such as short
welds when using fume suction nozzles or larger fixture welding using
integrated fume extraction guns. This process is designed for close
proximity source extraction from 2-4” to the welding source.
Since the hoses and suction nozzles are smaller than those of low
vacuum systems, it is much easier to carry the fume gun, extraction
nozzle and/or flex hose into confined spaces depending on the type of
welding, base material, consumable used, and length of time. The
mobility of the suction devices allows the main filter unit to be kept at a
central location. Due to the low air volume (CFM) extracted, make-up air
and negative room air pressures are kept to a minimum when exhausting
outside the facility.
Shown: Distribution & Shutoff Valves
Shown: Easy-Duct System
[2]
X-Tractor 3A, 5A & 8A
www.lincolnelectric.com