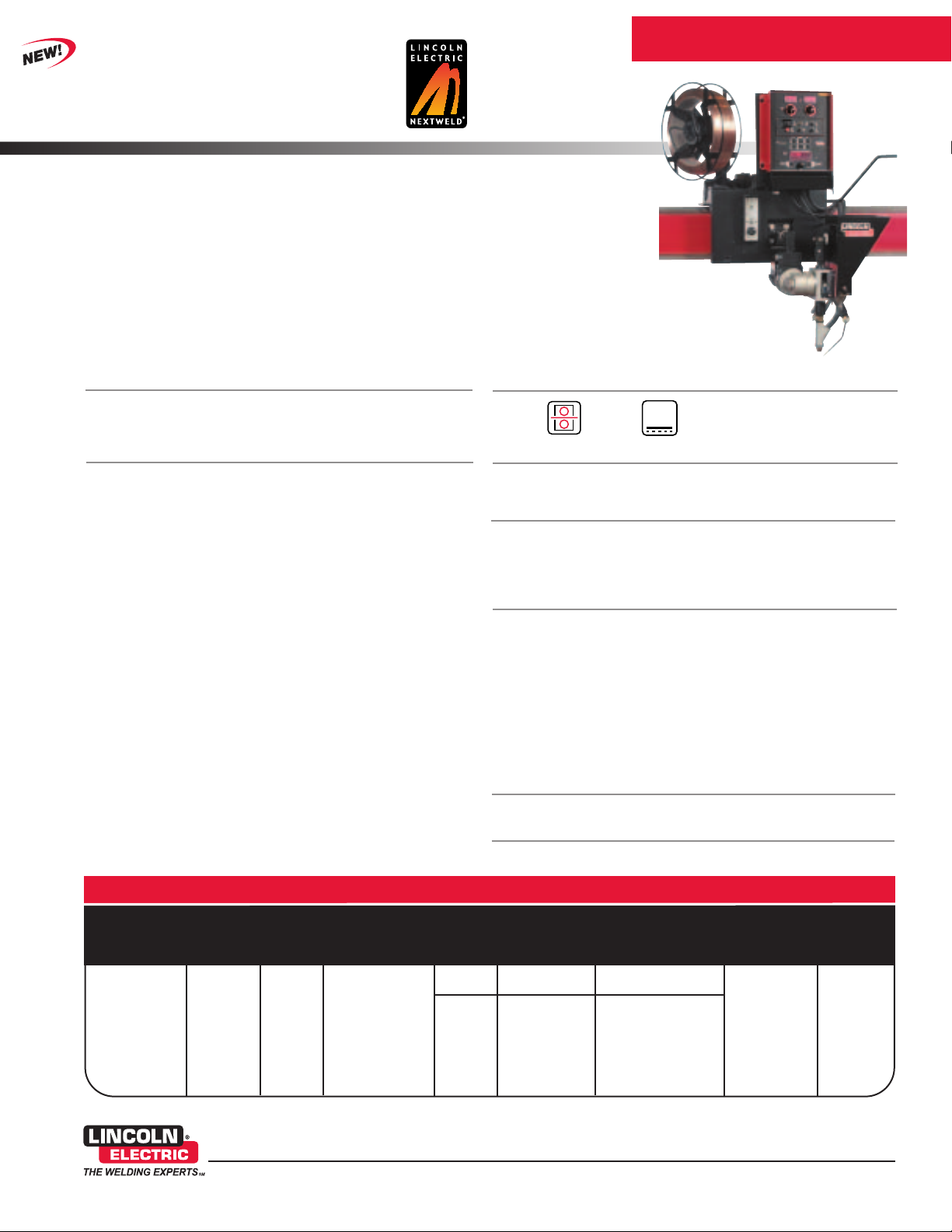
Power Feed™
10A Controller
ArcLink Controller for Power Wave AC/DC Systems.
Built on the enduring and trusted foundation of the NA-5 controller and the innovations of the
new Power Feed 10M wire feeder, the Power Feed 10A Controller is the next generation in
automatic submerged arc feeding. Designed for use with the Power Wave AC/DC 1000 power
source, the Power Feed 10A eliminates the need for a separate AC and DC controller, making this
powerful hard automation system controllable, adaptable and easy to use. The user-friendly
control panel offers a single-point of control over the entire welding cell, including the Power
Wave's Waveform Control Technology™, delivering an unprecedented level of control over wave
balance, amplitude and frequency.
AUTOMATIC WIRE FEEDERS
Processes
Submerged Arc
Advantage Lincoln
• Versatile system set-up options for stand-alone or PLC
configurations help you customize the weld cell to make your
operations as efficient as possible.
• Lincoln’s Waveform Control Technology™ gives you the ability
to select the right waveform for each application.
• The Power Feed 10A Controller provides clear dual digital display
of set-up and weld modes, six memories, AC controls,
strike/start/end options, travel stop/start, and timers.
• Controls can be adjusted on-the-fly to change penetration and/or
deposition rates with Variable Frequency, Variable Amplitude and
Variable Balance.
• Easy-to-use switch panel can be removed and used as a Remote
Control Pendant to create a versatile work station set-up.
• The Power Feed 10SF and Power Feed 10S wire drive systems
are reliable and durable.
• The motor conversion kit allows the use of existing NA-3, NA-4,
and NA-5 feed head mounting hardware.
• Manufactured under a quality system certified to ISO 9001
requirements and ISO 14001 environmental standards.
• Three-year warranty on parts and labor.
Description
Output Input
Unit Includes:
Power Feed 10A Control Box, Remote Pendant, 10-ft. Remote Pendant
Cable
Unit Requires:
Power Wave AC/DC 1000 power source, and either the K2312-1 Power
Feed 10SF Wire Feed Head for fixed hard automation, or the K2370-1
Power Feed 10S Head for mounting to a Lincoln TC-3 Travel Carriage.
(other options may apply.)
Recommended General Options
Power Feed 10SM Motor Conversion Kit (converts Lincoln NA-style wire
drives), ArcLink Cable, Flux Hopper, Feeder Control Cable (14-pin to 14pin and 5-pin to 5-pin), Contact Nozzle Assembly, Contact Jaw
Assembly, Positive Contact Assembly, Linc-Fill Attachments, Narrow
Gap Deep Groove Nozzle, Concentric Flux Cone Assembly, Tandem Arc
Framework, Tandem Reels, Twinarc Contact Assemblies, Tiny Twinarc
Assemblies, Tiny Twinarc Solid Wire Straightener, TC-3 Travel Carriage,
Vertical Lift Adjuster, Horizontal Adjuster, Wire Reel Assembly for 50-60
lb. Coils, Spindle Kit – 2 in. hub, SpreadArc Oscillator, Flux Screen,
Magnetic Flux Screen Separator
Recommended Power Source Option
Power Wave AC/DC 1000
Order
K2362-1 Power Feed 10A Controller
TECHNICAL SPECIFICATIONS
Product Product Input Rated Output Gear Speed Range
Name Number Power
Power Feed 10A K2362-1 40 VDC 1000A/100% 142:1
Controller with (381 x 259 x 102)
Wire Drive 95:1
(1) 142:1 gear box is standard. Conversion Kit supplied for conversion to 95:1 with Wire Drive (K2370-1, K2312-1, or K2311-1)
(1)
Current / Duty Cycle Box ipm (m/min) Solid Inches (mm) lbs (kg)
(1)
(1)
Wire Feed Wire Size Range
10-200 (.25-5.08) 5/32 - 7/32 (4.0 - 5.6) 15 x 13 x 4 25 (11.3)
10-300 (.25-7.62) 1/8 - 5/32 (3.2 - 4.0)
(1)
Inches (mm) H x W x D Net Weight
(1)
Dimensions
Publication E9.165 1/05
www.lincolnelectric.com

A CLOSER LOOK
FEATURES
A Closer Look
Power Feed 10A Control Panel
The Power Feed 10A control panel controls and monitors the advanced
capabilities of the Power Wave AC/DC 1000 in a single, simple, easyto-understand user interface display panel. The Power Feed 10A communicates using ArcLink, and can easily integrate with custom controls
and PLCs, in multiple configurations.
3.
Dual Display Dual Encoder Panel
1. Wire feed speed (WFS) or amps.
1.
2.
2. Voltage
3. Arc Established Indicator - illuminates when a true arc has been established.
4. Status LED - indicates system component ArcLink communication
4.
1.
5.
4.
status. Normal operation is a steady green light.
Switch Panel
®
1. START – Starts the weld sequence, using strike controls.
2.
3.
2. STOP – Stops the weld sequence, using crater/burnback controls.
3. INCH – Up/Down. Inches wire up or down without welding current
4. FLUX FILL– Activates flux hopper.
5. TRAVEL– Controls motion in either manual or automatic modes.
Remote Pendant - The switch panel can be removed and used as a
handheld pendant for remote control.
1. 14-PIN Remote Control Connector
2. 4-PIN TC-3 Carriage Connector
3. 3-PIN Flux Hopper Receptacle
4. 5-PIN ArcLink Connector
5. Auxiliary Circuit Access Holes
2.
1.
3.
4.
5.
Power Feed 10A Controller
[2]
www.lincolnelectric.com

A CLOSER LOOK
PERFORMANCE
WHAT IS NEXTWELD®?
Nextweld integrates Lincoln’s technologies, processes and products to create a comprehensive, flexible, user-friendly
welding system that can increase efficiency and reduce fabrication costs.
MSP4 and Memory Panel
Memory panel
Up to six user settings and two procedure settings can be saved and
retrieved using the Memory Panel. Allows the operator to save weld
parameters and set-up options, such as Timers, Start Options, End
Options, AC Controls, etc., before welding begins.
Weld Procedure Limit Controls
The MSP4 panel can be configured to limit the operator’s range of control of weld procedure settings (Wire Feed Speed, Crater Time,
Burnback Time, etc.)
Lockout/Security Controls
Configurations that prevent the operator from changing authorized weld settings can be set at four different lockout levels to provide a
custom level of control.
Mode Select Lockout
Locks START/END Options, AC Controls, Weld Modes and Wave
Options – or various combinations of each.
Memory Panel Lockout
Locks any or all of six memories saved.
Encoder Panel Lockout
Locks either right, left or both control knobs.
Full Lockout
Locks all functions listed above.
Infrared IR Port
Weld Manager™, the Lincoln Electric Palm® OS-based software product, builds upon the usability and efficiency of the Power Feed 10M
user interface design. It offers remote access and availability to system information, set-up, and configuration, allowing you to manage your
Power Wave system from the palm of your hand. The versatile design allows for wireless communication with the Infrared Port on the
Power Feed 10A Controller or through a serial connection and your cradle - the decision is yours.
• Quick and easy user interface set-up that can be transferred
across Power Feed/Power Wave systems.
• Ensure parameters are maintained by locking out numerous
options on the user interface panel.
• Easily set-up the system and ensure repeatability between
multiple cells by transferring memory through a
'back-up'/'restore' or a memory 'clone'.
• Verify current system information right on the production floor.
• Ensure security of the loaded settings through password
protection.
• Any Palm Operating System version 3.5 or higher.
[3]
Power Feed 10A Controller
www.lincolnelectric.com