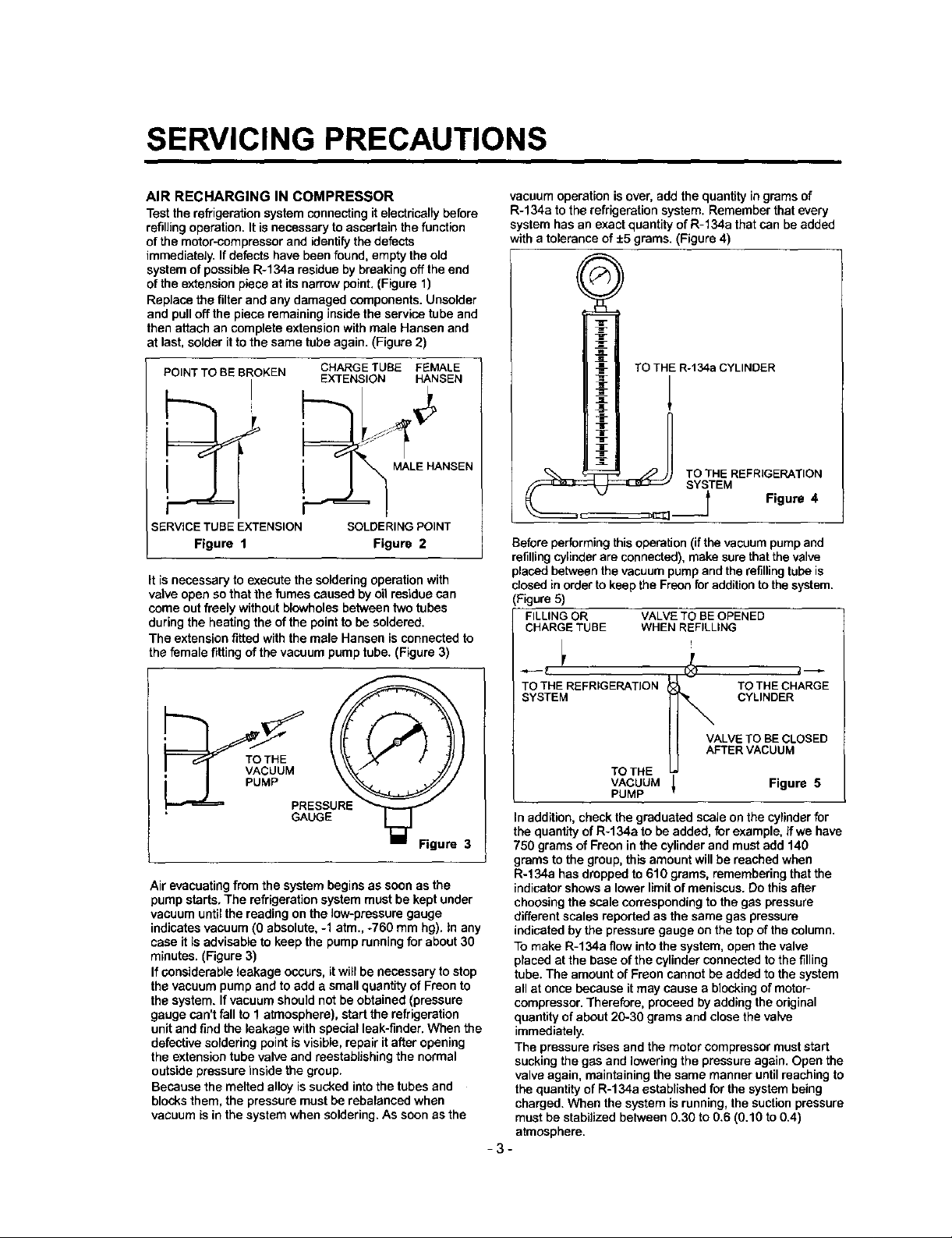
SERVICING PRECAUTIONS
AIR RECHARGING IN COMPRESSOR
Test the refrigeration system connecting it electrically before
refilling operation. It is necessary to ascertain the function
of the motor-compressor and identify the defects
immediately. If defects have been found, empty the old
system of possible R_134a residue by breaking off the end
of the extension piece at its narrow point. (Figure 1)
Replace the filter and any damaged components. Unsolder
and pull off the piece remaining inside the service tube and
then attach an complete extension with male Hansen and
at last, solder it to the same tube again. (Figure 2)
POINT TO BE BROKEN
SERVICE TUBE EXTENSION
Figure 1
It is necessary to execute the soldering operation with
valve open so that the fumes caused by oil residue can
come out freely without blowholes between two tubes
during the heating the of the point to be soldered.
The extension fitted with the male Hanson is connected to
the female fitting of the vacuum pump tube. (Figure 3)
CHARGE TUBE FEMALE
EXTENSION HANSEN
MALE HANSEN
SOLDERING POINT
Figure 2
vacuum operation is over, add the quantify in grams of
R-134a to the refrigeration system. Remember that every
system has an exact quantity of R-134a that can be added
with a tolerance of +5 grams. (Figure 4)
TO THE R-t34a CYLINDER
L
_r _ " TOTHE REFRIGERATION
Before performing this operation(if the vacuum pump and
refilling cylinder are connected), make sure that the valve
placed between the vacuum pump and the refilling tube is
closed in order to keep the Freon for addition to the system.
(Figure 5)
FILLING OR VALVE TO BE OPENED
CHARGE TUBE WHEN REFILLING
SYSTEM
I Figure 4
Figure 3
Air evacuating from the system begins as soon as the
pump starts, The refrigeration system must be kept under
vacuum until the reading on the low-pressure gauge
indicates vacuum (0 absolute, -1 atm., -760 mm hg). tn any
case it is advisable to keep the pump running for about 30
minutes. (Figure 3)
If considerable leakage occurs, it will be necessary to stop
the vacuum pump and to add a small quantity of Froon to
the system. If vacuum should not be obtained (pressure
gauge can't fall to 1 atmosphere), start the refrigeration
unit and find the leakage with special leak-finder. When the
defective soldering point is visible, repair itafter opening
the extension tube valve and reestablishing the normal
outside pressure inside the group.
Because the melted alloy is sucked into the tubes and
blocks them, the pressure must be rebalancod when
vacuum is in the system when soldering. As soon as the
TO THE REFRIGERATION TO THE CHARGE
SYSTEM CYLINDER
VALVE TO BE CLOSED
AFTER VACUUM
TO THE
VACUUM _ Figure 5
PUMP
In addition, check the graduated scale on the cylinder for
the quantity of R-134a to be added, for example, if we have
750 grams of Freoo in the cylinder and must add 140
grams to the group, this amount will be reached when
R-134a has dropped to 610 grams, remembering that the
indicator shows a lower limit of meniscus. Do this after
choosing the scale corresponding to the gas pressure
different scales reported as the same gas pressure
indicated by the pressure gauge on the top of the column.
To make R-134a flow into the system, open the valve
placed at the base of the cylinder connected to the filling
tube. The amount of Freon cannot be added to the system
all at once because it may cause a blocking of motor-
compressor. Therefore, proceed by adding the original
quantify of about 20-30 grams and close the valve
immediately.
The pressure rises and the motor compressor must start
sucking the gas and lowering the pressure again. Open the
valve again, maintaining the same manner until reaching to
the quantity of R-134a established for the system being
charged. When the system is running, the suction pressure
must be stabilized between 0.30 to 03 (0.10 to 0.4)
atmosphere.
-3-
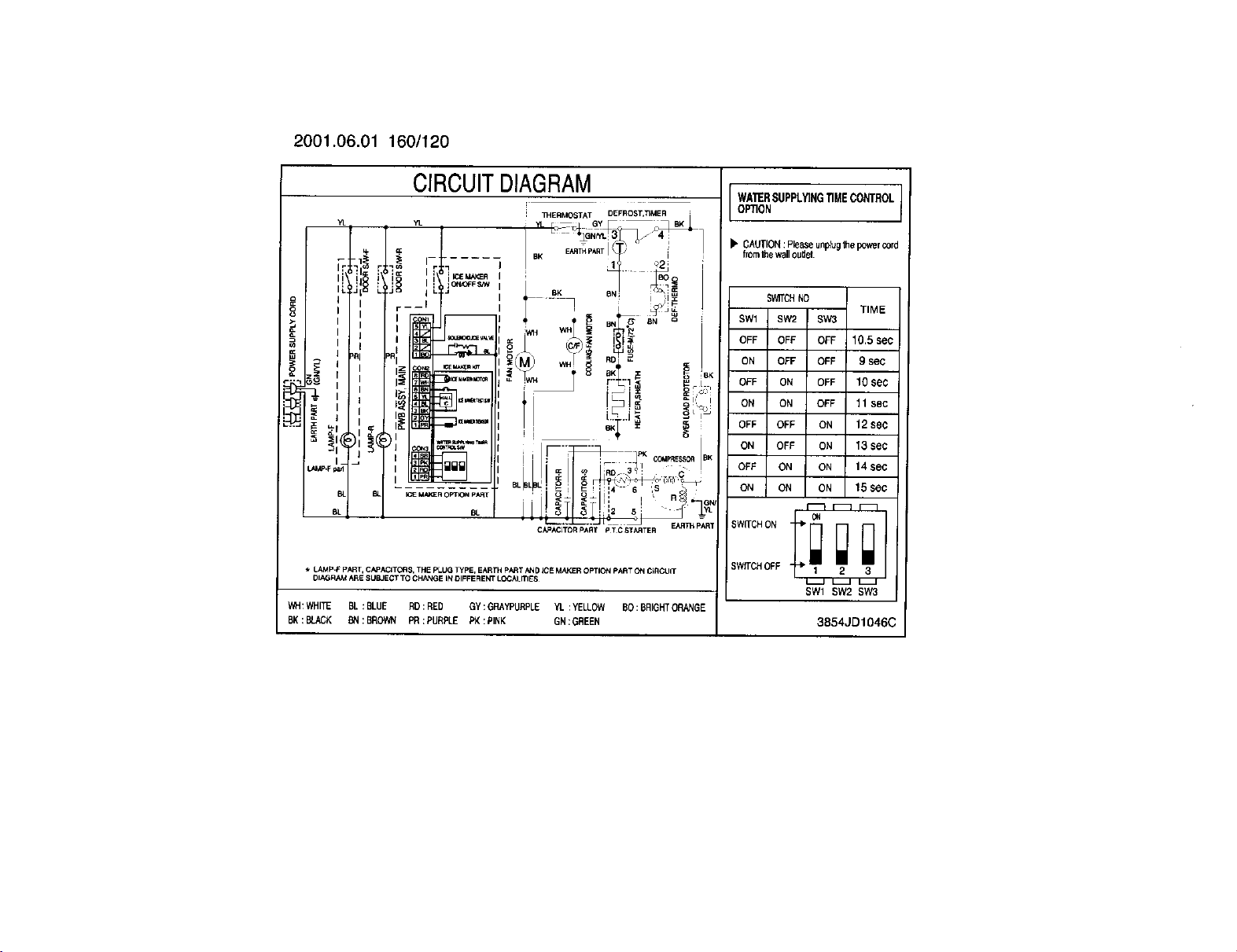
2001.06.01 160/120
CIRCUITDIAGRAM
r
YL YL yi. L TX GYP ....
= _,_,,._IC_"_" /
ir;l_ r.l= .;_ I ji ?2: i
: : t I i I Ii._.v*- :s,w 7_
IL J_ L Jg L J I BK _,_ %_?= l
o I " I _ - "" I i!_
o
I i _ I Im _,_ I LT-..I< 9 i
I i1(_') i(b')l .... i ! , • _ i
* LA_Ap-F pART IC_PACITCR$, THE PLUG TYPe, EART_ pART AND ICE MAKER OPTI(_N pART O_ CIRCUIT
DIAGR_J_ ARE SUBJECT TO CHANGE IN OIFFERENT LOCALITI[S
WH:WHITE BL:BLUE RD:RED GY:GRAYPURPLE YL :YELLOW BO: BRIGHTORANGE
BK:BLACK 8N : BROWN PR:PURPLE P_ :PINK GN:GREEN
I - r wit w8 !1 !"
_______ L_LI2i _l _ 14_ 6 s
_HERMOSTAT DEFROST,TIME R
MU
CAPACITOR PAR¥ p T O STARTER _'R_ PART
WA_R SUPPLYINGTIMECONTROL
OPTION
CAUTION:PleaseunphJgthepowerCOl
fromthewallouter.
SWITC/_NO
GWl Sw2 SW3
OFF OFF OFF 10.5 sec
ON OFF OFF 9 sec
OFF ON OFF 10 SeC
ON ON OFF 11sec
OFF OFF ON 12 SeC
ON OFF ON 13 sec
OFF ON ON 14 sec
ON ON ON 15 $ec
SWITCH ON "il*[_ [_ i_
SWffCH OFF ÷ 1 2 3
SWl SW2 SW3
TIME
3854JD1046(
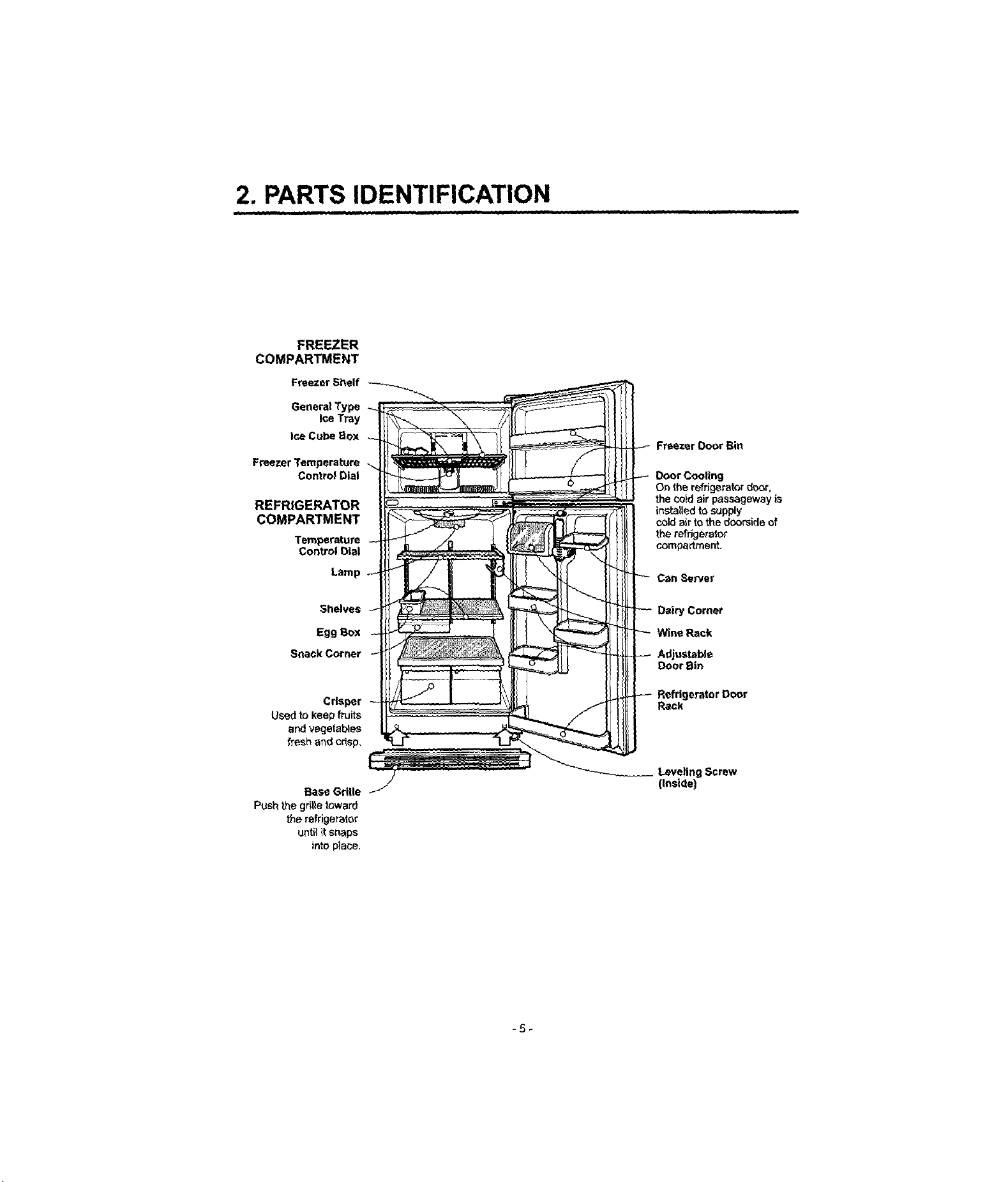
2. PARTS IDENTIFICATION
ii i ii ii i i1|1 ii
FREEZER
COMPARTMENT
Freezer Shelf
General Type
Ice Tray
Ice Cube Box
Freezer Temperature
REFRIGERATOR
COMPARTMENT
Control Dial
Temperetum
ControlDial
Freezer Door Bin
Door Cooling
On the refrigeratordoor,
the co}dair passageway is
installed to supply
cold_ir to the doors(deof
the refrigerator
compartment.
Lamp
Shelves
Egg Box
Snack Corner
Cdsper
Used tokeep fruits
and vegetables
fresh and crisp,
Base Grille
Pushthe grilletoward
the refrigerator
untilit snaps
into place.
Can SeP/er
Corner
Wine Rack
Adjustable
Door Bin
Rack
Leveling Screw
(Inside)
-5-
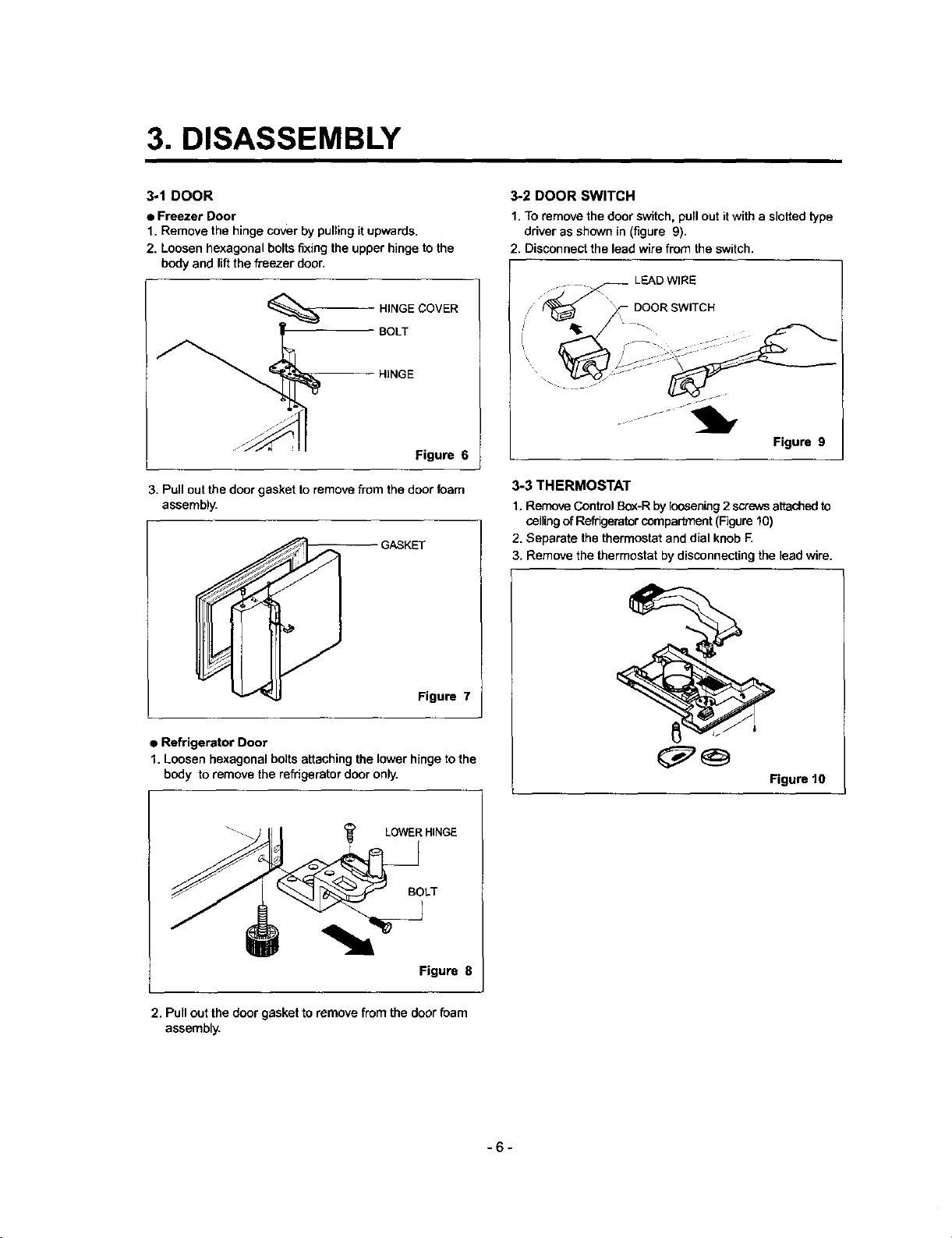
3. DISASSEMBLY
3.1 DOOR
• Freezer Door
1. Remove the hinge cover by pulling it upwards.
2. Loosen hexagonal bolts fixing the upper hinge to the
body and lift the freezer door.
BOLT
HINGE
HINGE COVER
Figure 6
3. Pull out the door gasket to remove from the door foam
assembly.
GASKET
3-2 DOOR SWITCH
1. To remove the door switch, pull out itwith a slotted type
driver as shown in (figure 9).
2. Disconnect the lead wire from the switch.
LEAD WIRE
'i/ _ DOOR SWITCH
12 _ i i
Figure 9
3-3 THERMOSTAT
1. Remove Control Box-R by loosening 2 screws attached to
ceiling of Refrigerator compartment (Figure 10)
2. Separate the thermostat and dial knob F.
3. Remove the thermostat by disconnecting the lead wire.
Figure 7
• Refrigerator Door
1, Loosen hexagonal bolts attaching the lower hinge to the
body to remove the refrigerator door only,
LOWER HINGE
Figure 8
2. Pull out the door gasket to remove from the door foam
assembly.
Figure t0
-6-
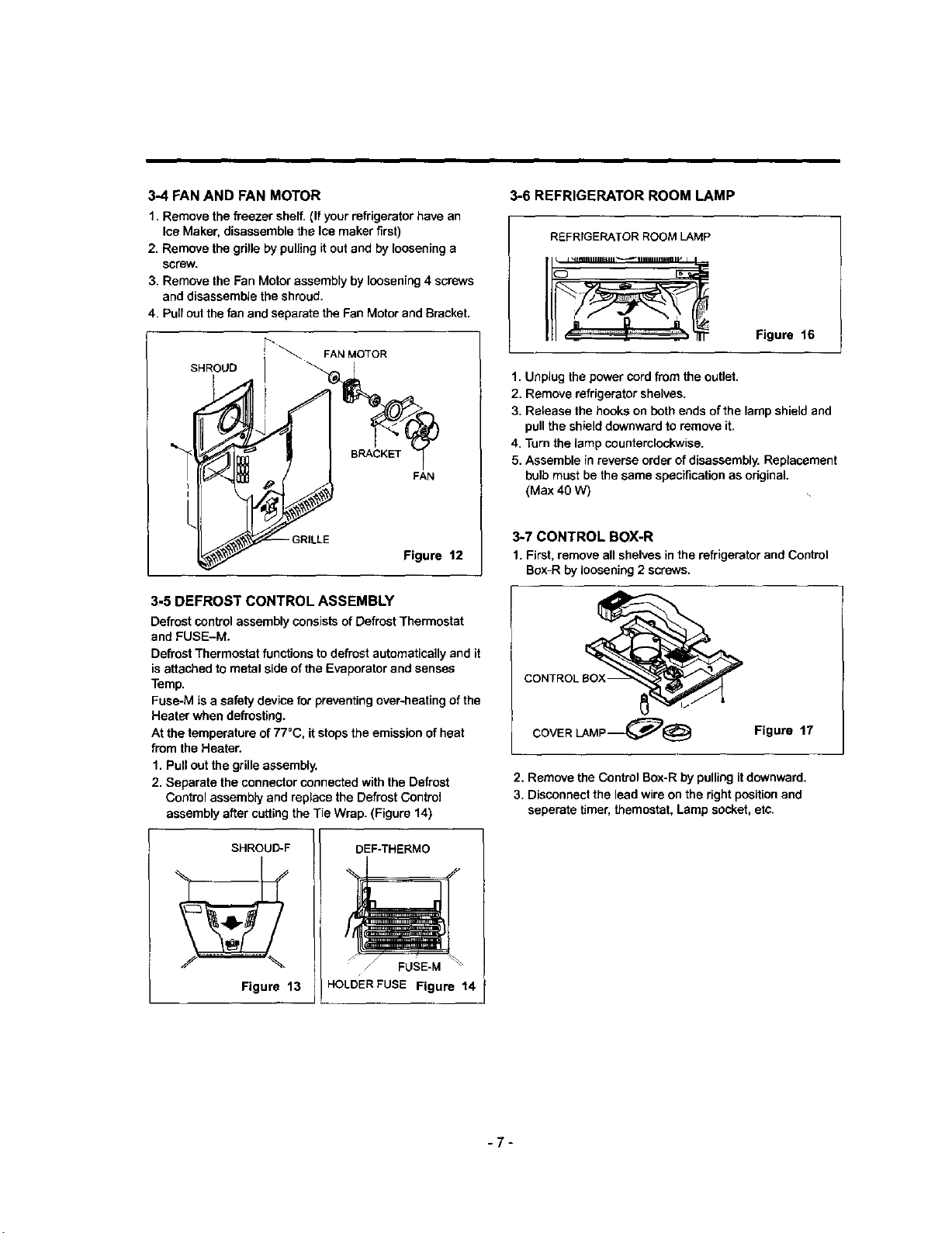
3-4 FAN AND FAN MOTOR
1. Remove the freezer shelf. (If your refrigerator have an
Ice Maker, disassemble the Ice maker first)
2. Remove the grille by pulling it out and by loosening a
screw.
3. Remove the Fan Motor assembly by loosening 4 screws
and disassembJe the shroud.
4. Pull out the fan and separate the Fan Motor and Bracket.
_'_ FAN MOTOR
SHROUD
BRACKET
FAN
I
Figure 12
3-5 DEFROST CONTROL ASSEMBLY
Defrost control assembly consists of Defrost Thermostat
and FUSE-M.
Defrost Thermostat functions to defrost automatically and it
is attached to metal side of the Evaporator and senses
Temp.
Fuse-M is a safety device for preventing over-heating of the
Heater when defrosting.
At the temperature of 77°C, it stops the emission of heat
from the Heater.
1. Pull out the grille assembly.
2. Separate the connector connected with the Defrost
Control assembly and replace the Defrost Control
assembly after cutting the Tie Wrap. (Figure 14)
3-6 REFRIGERATOR ROOM LAMP
REFRIGERATOR ROOM LAMP
Figure 16
1. Unplug the power cord from the outlet.
2. Remove refrigerator shelves.
3. Release the hooks on both ends of the lamp shield and
pull the shield downward to remove it.
4. Turn the lamp counterclockwise.
5. Assemble in reverse order of disassembly. Replacement
bulb must be the same specification as original.
(Max 40 W)
3-7 CONTROL BOX-R
1. First, remove all shelves in the refrigerator and Control
Box-R by loosening 2 screws.
CONTROLBOX-
COVER LAMP _@
2. Remove the Control Box-R by pulling it downward.
3. Disconnect the lead wire on the right position and
seperate timer, themostat, Lamp socket, etc.
Figure 17
SHROUD-F
Figure 13
DEF_HERMO
FUSE-M
HOLDER FUSE Figure 14
-7-