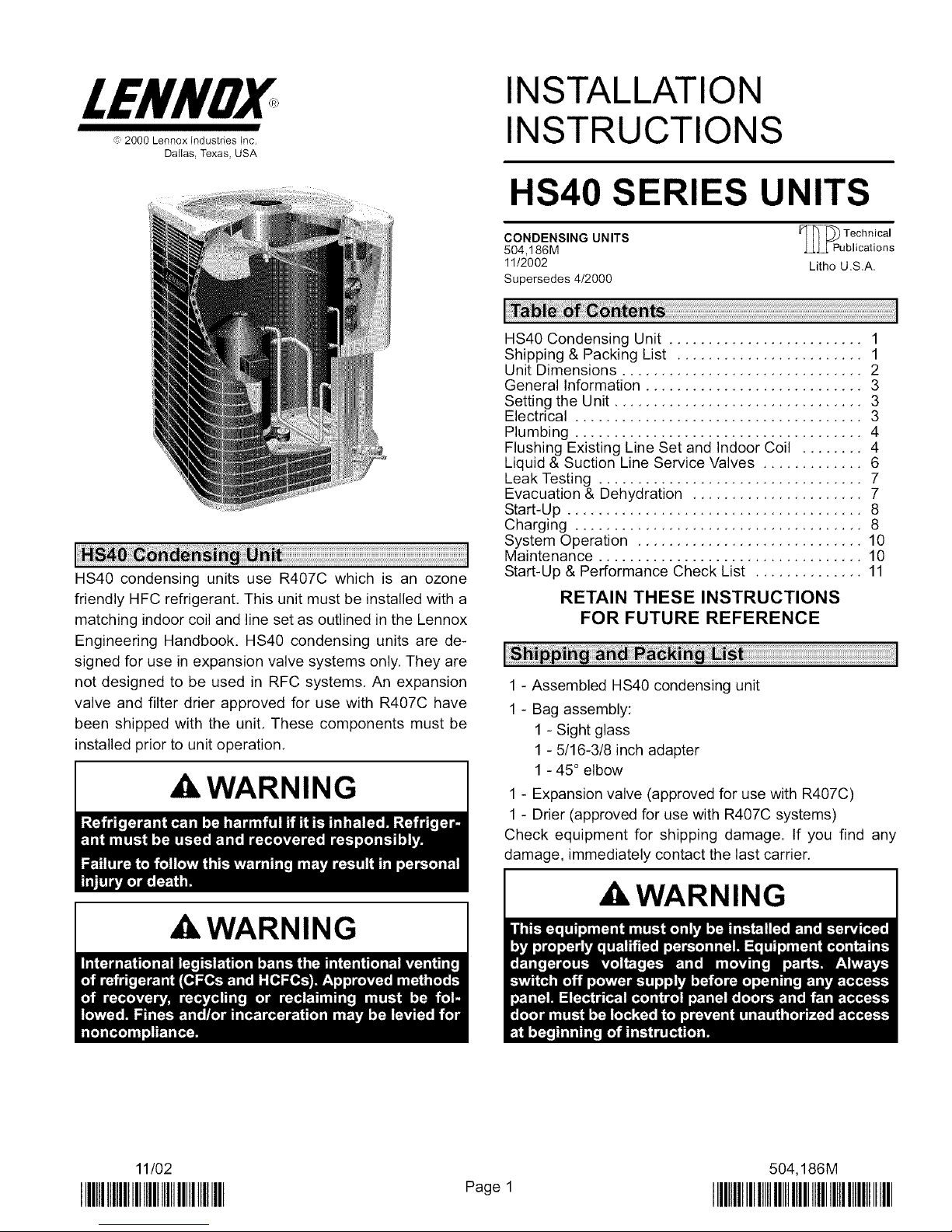
LENNDX
INSTALLATION
,1,_2000 Lennox Industries Inc.
Dallas, Texas, USA
HS40 condensing units use R407C which is an ozone
friendly HFC refrigerant. This unit must be installed with a
matching indoor coil and line set as outlined in the Lennox
Engineering Handbook. HS40 condensing units are de-
signed for use in expansion valve systems only. They are
not designed to be used in RFC systems. An expansion
valve and filter drier approved for use with R407C have
been shipped with the unit. These components must be
installed prior to unit operation.
A, WARNING
INSTRUCTIONS
HS40 S UNITS
CONDENSING UNITS lIE_ :.)
504,186M .LU_ Publications
11/2002 Lithe U.S.A.
Supersedes 4/2000
HS40 Condensing Unit ......................... 1
Shipping & Packing List ........................ 1
Unit Dimensions ............................... 2
General Information ............................ 3
Setting the Unit ................................ 3
Electrical ..................................... 3
Plumbing ..................................... 4
Flushing Existing Line Set and Indoor Coil ........ 4
Liquid & Suction Line Service Valves ............. 6
Leak Testing .................................. 7
Evacuation & Dehydration ...................... 7
Start-Up ...................................... 8
Charging ..................................... 8
System Operation ............................. 10
Maintenance .................................. 10
Start-Up & Performance Check List .............. 11
RETAIN THESE INSTRUCTIONS
FOR FUTURE REFERENCE
1 - Assembled HS40 condensing unit
1 - Bag assembly:
1 - Sight glass
1 - 5/16-3/8 inch adapter
1 - 45° elbow
1 - Expansion valve (approved for use with R407C)
1 - Drier (approved for use with R407C systems)
Check equipment for shipping damage. If you find any
damage, immediately contact the last carrier.
Technical
WARNING
11/02
IIIIIIIIIIIIIIIIIIIIIIIIIIIIIIIIIIIIIIll
Page 1
A, WARNING
504,186M
IIlIIIIIIIIIIIIIIIIIIIIIIIHIIIIIIIIIIIII
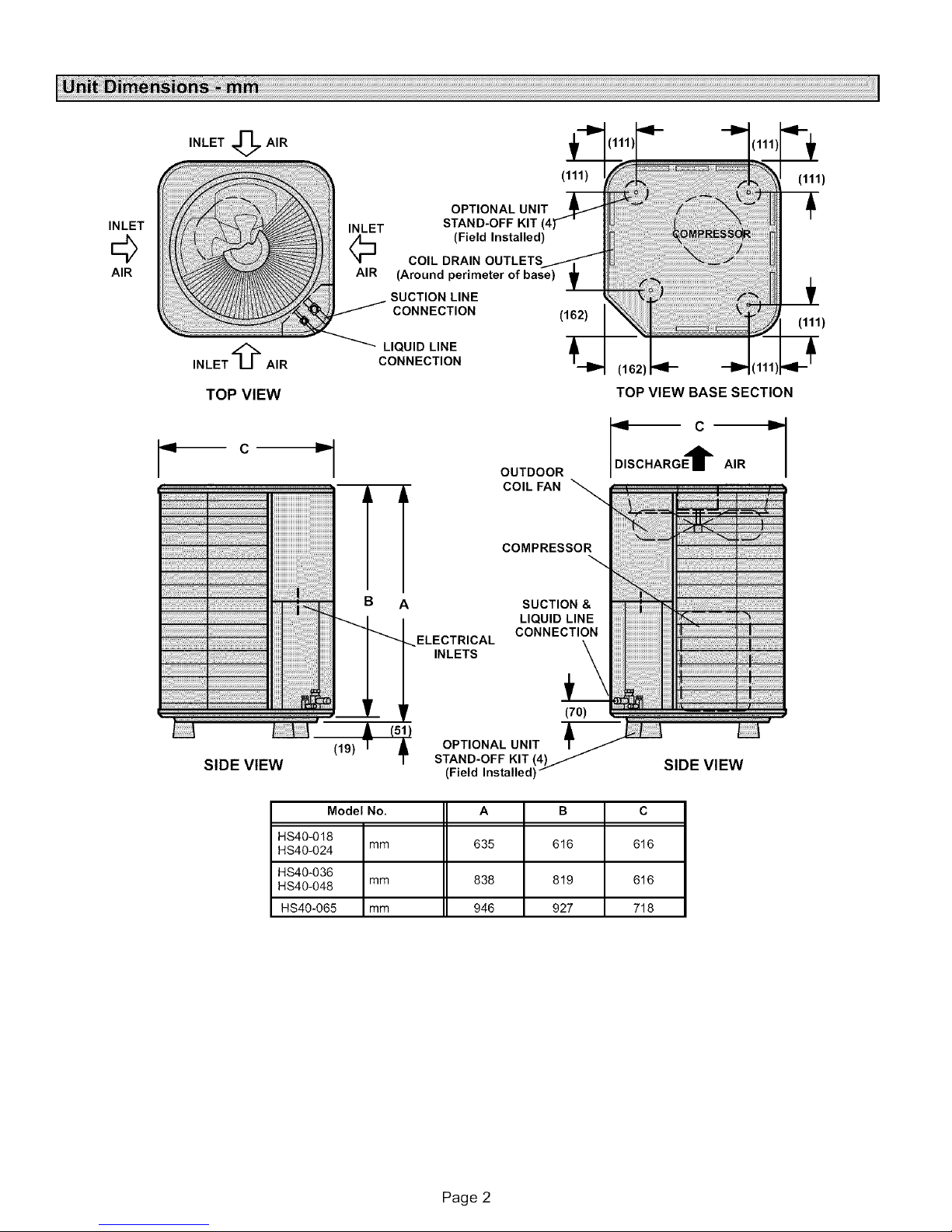
INLET
©
AIR
INLET _AIR
OPTIONAL UNIT
INLET
©
AIR
SUCTION LINE
CONNECTION (162)
STAND-OFF KIT (4)_ "
(Field Installed)
COIL DRAIN OUTLETS_""_I
(Around perimeter of base)
(111)
/
INLET'_AIR
TOP VIEW
=_ C ,v
SIDE VIEW
HS40-018
HS40-024 mm 635 616 616
HS40-036
HS40-048 mm 838 819 616
HS40-065 mm 946 927 718
LIQUID LINECONNECTION
h._l
OUTDOOR
COIL FAN
COMPRESSOR
SUCTION &
LIQUID LINE
ELECTRICAL
INLETS
(19)
Model No, A B C
OPTIONAL UNIT
STAND-OFF KIT (4)_
(Field Installed) /
CONNECTION
(70)
TOP VIEW BASE SECTION
SIDE VIEW
Page 2
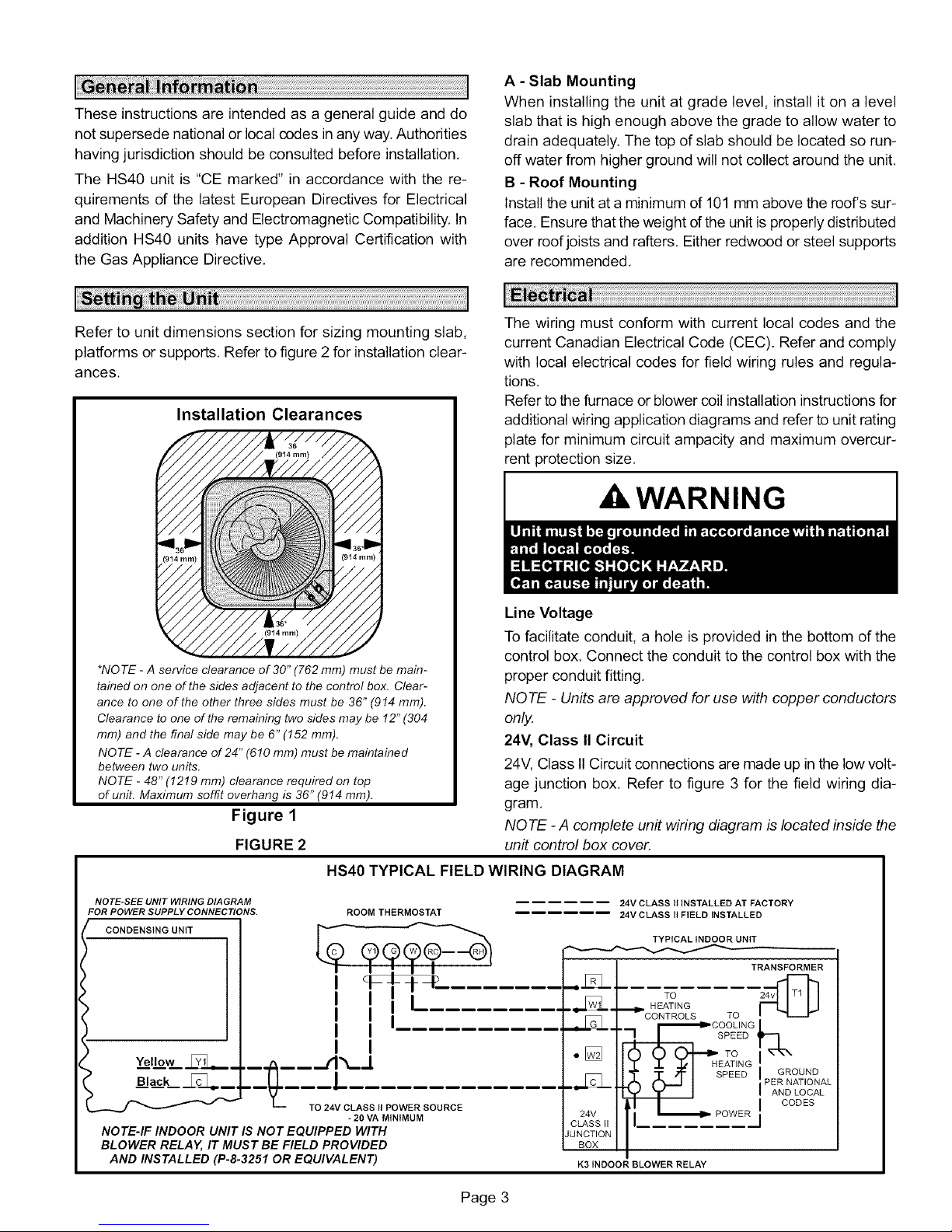
Theseinstructionsareintendedasageneralguideanddo
notsupersedenationalorlocalcodesinanyway,Authorities
havingjurisdictionshouldbeconsultedbeforeinstallation,
TheHS40unitis "CEmarked"inaccordancewiththere-
quirementsd the latest European Directives for Electrical
and Machinery Safety and Electromagnetic Compatibility. In
addition HS40 units have type Approval Certification with
the Gas Appliance Directive.
A - Slab Mounting
When installing the unit at grade level, install it on a level
slab that is high enough above the grade to allow water to
drain adequately. The top of slab should be located so run-
off water from higher ground will not collect around the unit,
B - Roof Mounting
Install the unit at a minimum of 101 mm above the roof's sur-
face. Ensure that the weight of the unit is properly distributed
over roof joists and rafters. Either redwood or steel supports
are recommended.
Refer to unit dimensions section for sizing mounting slab,
platforms or supports. Refer to figure 2 for installation clear-
ances.
Installation Clearances
(914 mm)
*NO TE - A service clearance of 30" (762 mm) must be main-
tained on one of the sides adjacent to the control box. Clear-
ance to one of the other three sides must be 36" (914 mm).
Clearance to one of the remaining two sides may be 12" (304
mm) and the final side may be 6" (152 mm).
NOTE - A clearance of 24" (610 mm) must be maintained
between two units.
NOTE - 48" (1219 mm) clearance required on top
of unit. Maximum soffit overhang is 36" (914 mm).
Figure 1
FIGURE 2
HS40 TYPICAL FIELD WIRING DIAGRAM
The wiring must conform with current local codes and the
current Canadian Electrical Code (CEC). Refer and comply
with local electrical codes for field wiring rules and regula-
tions.
Refer to the furnace or blower coil installation instructions for
additional wiring application diagrams and refer to unit rating
plate for minimum circuit ampacity and maximum overcur-
rent protection size.
WARNING
Line Voltage
To facilitate conduit, a hole is provided in the bottom of the
control box. Connect the conduit to the control box with the
proper conduit fitting,
NOTE- Units are approved for use with copper conductors
only,
24V, Class II Circuit
24V, Class II Circuit connections are made up in the low volt-
age junction box, Refer to figure 3 for the field wiring dia-
gram,
NOTE -A complete unit wiring diagram is located inside the
unit control box cover,
NOTE-SEE UNIT WIRING DIAGRAM
FOR POWER SUPPLY CONNECTIONS.
CONDENSING UNIT
Yellow
Black
NOTE-IF INDOOR UNIT IS NOT EQUIPPED WITH
BLOWER RELAY, IT MUST BE FIELD PROVIDED
AND INSTALLED (P-8-3251 OR EQUIVALENT)
'=_'= _124vLc_A_S It POWER SOURCE
ROOM THERMOSTAT
'
I
- 20 VA MINIMUM
Page 3
24V CLASS II INSTALLED AT FACTORY
24V CLASS It FIELD INSTALLED
TYPICAL INDOOR UNIT
TOHEATING
24V
CLASS II
JUNCTION
BOX
K3 INDOOR BLOWER RELAY
TRANSFORMER
TO
SPEED
TO I
HEATING
SPEED PER NATIONAL
GROUND
AND LOCAL
I CODES
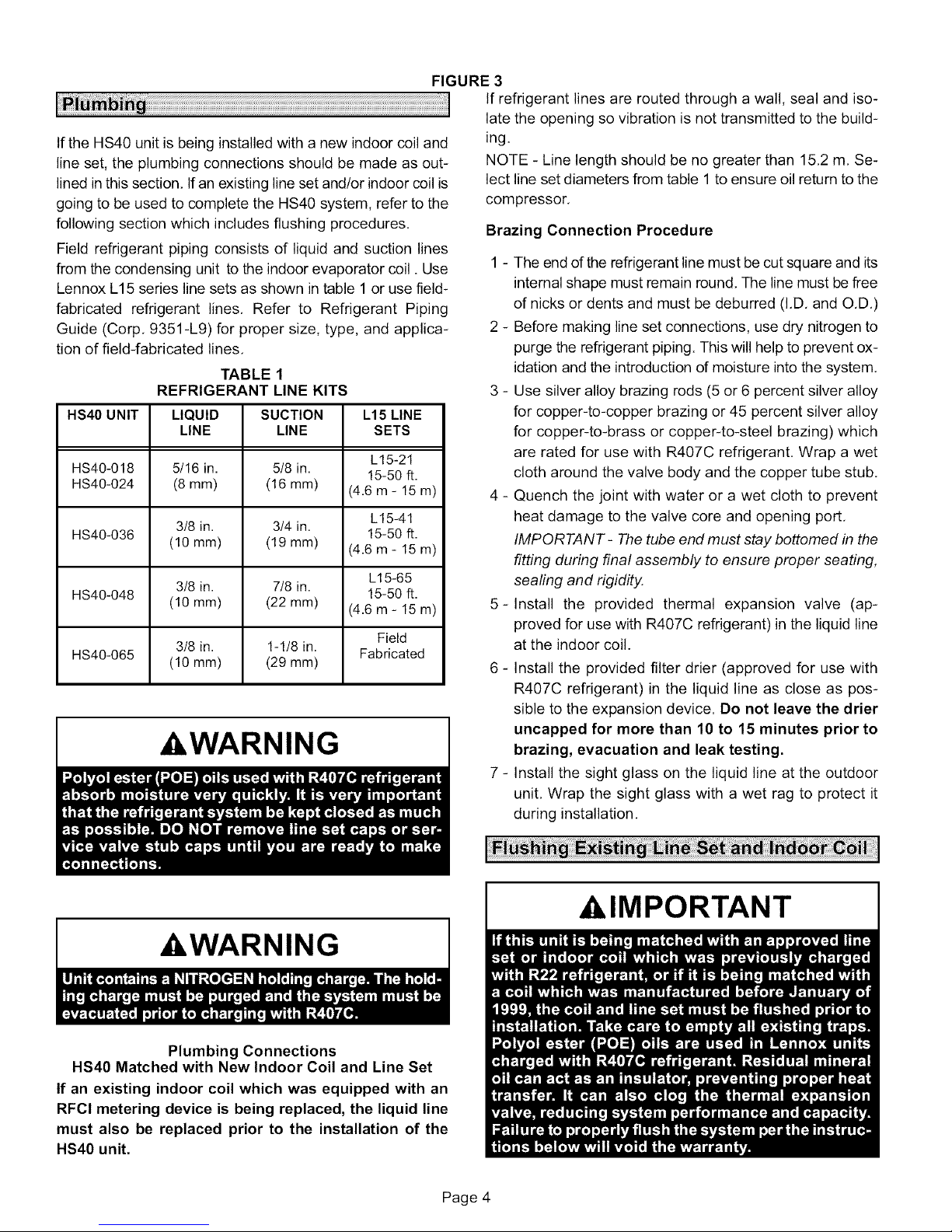
FIGURE 3
IftheHS40unitisbeinginstalledwithanewindoorcoiland
lineset,theplumbingconnectionsshouldbemadeasout-
linedinthissection.Ifanexistinglinesetand/orindoorcoilis
goingtobeusedtocompletetheHS40system,refertothe
followingsectionwhichincludesflushingprocedures.
Fieldrefrigerantpipingconsistsofliquidandsuctionlines
fromthecondensingunittotheindoorevaporatorcoil.Use
LennoxL15serieslinesetsasshownintable1orusefield-
fabricatedrefrigerantlines.Referto RefrigerantPiping
Guide(Corp.9351-L9)forpropersize,type,andapplica-
tionoffield-fabricatedlines.
TABLE 1
REFRIGERANT LINE KITS
HS40 UNIT LIQUID SUCTION L15 LINE
LINE LINE SETS
HS40-018 5/16 in. 5/8 in.
HS40-024 (8 mm) (16 mm) (4.6 m - 15 m)
3/8 in. 3t4 in.
HS40-036 (10 mm) (19 mm) (4.6 m - 15 m)
318in. 7/8 in. 15-50 ft.
HS40-048 (10 mm) (22 mm) (4.6 m - 15 m)
318in. 1-1/8 in.
HS40-065 (10 mm) (29 mm) Fabricated
L15-21
15-50 ft.
L15-41
15-50 ft.
L15-65
Field
AWARNING
If refrigerant lines are routed through a wall, seal and iso-
late the opening so vibration is not transmitted to the build-
ing.
NOTE - Line length should be no greater than 15.2 m. Se-
lect line set diameters from table 1 to ensure oil return to the
compressor.
Brazing Connection Procedure
1 - The end of the refrigerant line must be cut square and its
internal shape must remain round. The line must be free
of nicks or dents and must be deburred (I.D. and O.D.)
2 - Before making line set connections, use dry nitrogen to
purge the refrigerant piping. This will help to prevent ox-
idation and the introduction d moisture into the system.
3 - Use silver alloy brazing rods (5 or 6 percent silver alloy
for copper-to-copper brazing or 45 percent silver alloy
for copper-to-brass or copper-to-steel brazing) which
are rated for use with R407C refrigerant. Wrap a wet
cloth around the valve body and the copper tube stub.
4 - Quench the joint with water or a wet cloth to prevent
heat damage to the valve core and opening port.
IMPORTANT - The tube end must stay bottomed in the
fitting during final assembly to ensure proper seating,
sealing and rigidity.
5-Install the provided thermal expansion valve (ap-
proved for use with R407C refrigerant) in the liquid line
at the indoor coil.
6 - Install the provided filter drier (approved for use with
R407C refrigerant) in the liquid line as close as pos-
sible to the expansion device. Do not leave the drier
uncapped for more than 10 to 15 minutes prior to
brazing, evacuation and leak testing.
7 - Install the sight glass on the liquid line at the outdoor
unit. Wrap the sight glass with a wet rag to protect it
during installation.
&WARNING
Plumbing Connections
HS40 Matched with New Indoor Coil and Line Set
If an existing indoor coil which was equipped with an
RFCI metering device is being replaced, the liquid line
must also be replaced prior to the installation of the
HS40 unit.
&IMPORTANT
Page 4