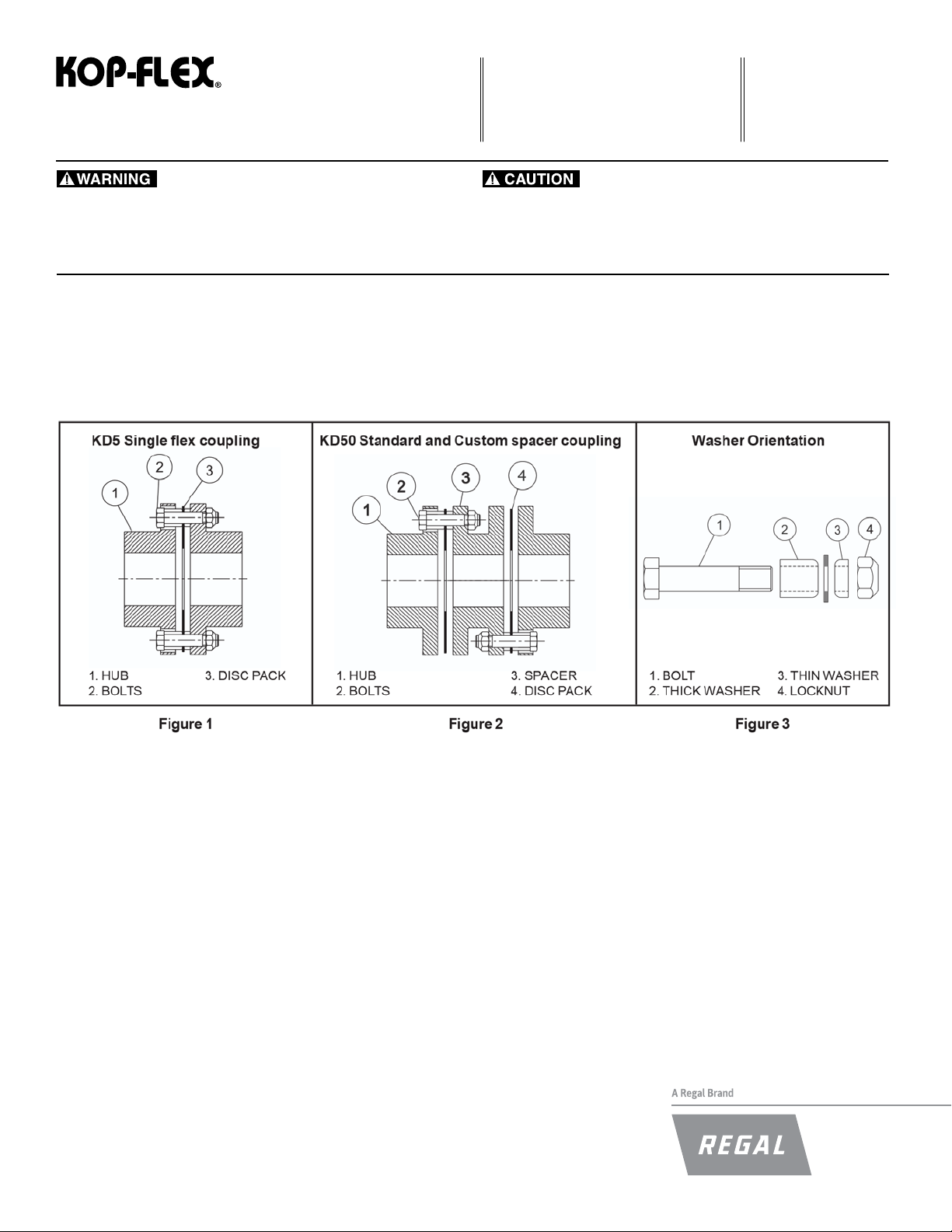
KD5 & KD50 Disc Coupling Single & Spacer Type
Sizes 022 Through 362
F O R M
8499-BE
Revised
November 2015
• Read and follow all instructions carefully.
• Disconnect and lock-out power before installation and maintenance.
Working on or near energized equipment can result in severe injury or death.
• Do not operate equipment without guards in place. Exposed equipment can
result in severe injury or death.
• Periodic inspections should be performed. Failure to perform proper maintenance
can result in premature product failure and personal injury.
I. Pre-installation Checks
1. Inspect carton contents to make sure all components are as ordered.
2. Check for damage during shipment.
3. Remove any burrs, aws, and rust from driver and driven shafts, also make sure that keys t properly in shaft.
4. Do not remove tape holding discs together; if tape is broken, make sure the number of discs are correct before installing disc pack.
Lightly re-tape to hold the disk pack together during installation if necessary.
II. Pre-assembly Alignment - Spacer Couplings Only
NOTE: For Single ex couplings, only assembly and post assembly alignment checks are required, but both shafts need to be in reasonable alignment to
permit assembly.
1. Mount hubs onto driver and driven shaft with keys in place, but do not install spacer or disc pack.
2. Correct for angular misalignment by mounting an indicator on one hub and indicate on the other hub as shown in Figure 5. Rotate coupling hub with the indicator
base, while holding the other hub steady, to nd the minimum and maximum indicator reading. Determine the difference between the minimum and maximum
reading. This difference should be less than or equal to the “Installation Angular” T.I.R. shown in table B.
3. If the difference is larger than the value given in table B, adjust the connected equipment until indicator reading is less than or equal to the “Installation Angular”
T.I.R. shown in Table B.
4. For parallel misalignment, mount indicator on a hub and indicate on the ange of the other hub as shown in Figure 6. Rotate coupling hub with the indicator base,
while holding the other hub steady, to nd the minimum and maximum indicator reading. Determine the difference between the minimum and maximum reading.
This difference should be less than or equal to the “Installation Parallel” T.I.R. shown in table B.
5. If the difference is larger than the value given in table B, adjust the connected equipment until indictor reading is less than or equal to the
“Installation Parallel” T.I.R. shown in Table B.
6. Once the pre-assembly alignment is complete, the disc packs and spacer can be assembled.
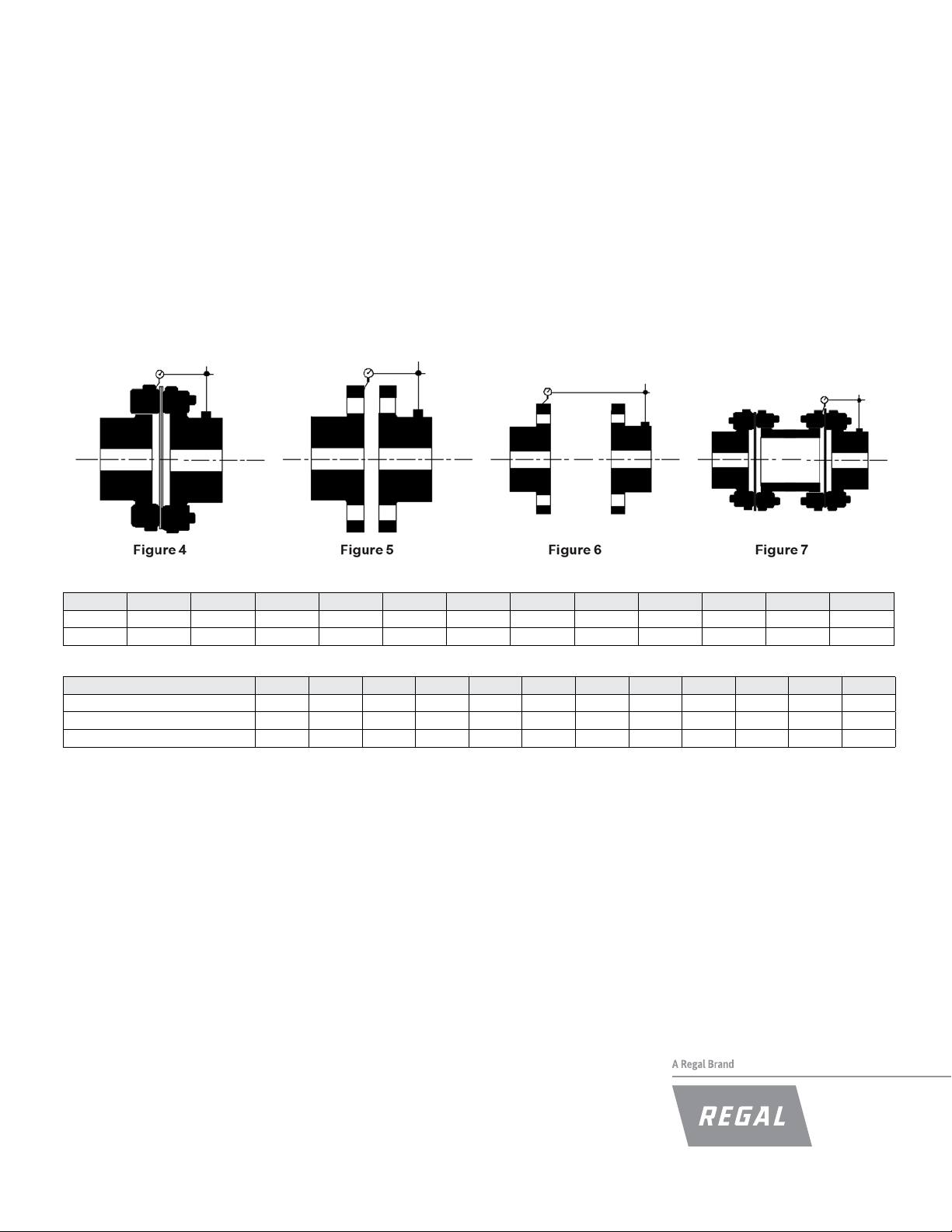
III. Assembly
1. Assemble the coupling using gures 1,2, and 3 as a guide. The curved face of both washers must be adjacent to the disc packs as shown in Figure 3.
2. Holding disc pack and spacer (for spacer coupling) in between hubs, insert bolts and tighten nuts. Notice that the thick washers sit in the hub/spacer anges.
3. Tighten the lock nuts with a torque wrench to the values in Table A. Re-torque all nuts to the proper value after approximately 2 hours of operation.
IV. Post Assembly Alignment Check
Note: Aligning with the dial indictor method is shown below, but a laser alignment system or a reverse indicator system will produce better results.
1. For single ex couplings, mount dial indicator on one hub and indicate on the other hub as shown in gure 4. Rotate coupling to nd the minimum and
maximum indicator readings. Calculate the difference and check to make sure that it is less than or equal to the “Operation Angular” T.I.R. shown in Table B.
2. If the difference is larger than the value given in table B, adjust the connected equipment until indicator reading is less than or equal to the “Operation Angular”
T.I.R. shown in Table B.
3. For spacer couplings, mount dial indicator on one hub and indicate on the spacer as shown in gure 7. Rotate coupling to nd the minimum and maximum
indicator readings. Calculate the difference and check to make sure that it is less than or equal to the “Operation Angular” T.I.R. shown in Table B.
4. If the difference is larger than the value given in table B, adjust the connected equipment until indicator reading is less than or equal to the “Operation Angular”
T.I.R. shown in Table B.
5. Repeat steps 3 and 4 for the opposite hub.
6. Recheck alignment after approximately 2 hours of actual operation to ensure that the coupling is running under recommended alignment conditions. This will help
increase the life of the coupling.
Table A - NUT TIGHTENING TORQUE & NUMBER OF DISCS PER FLEX ELEMENT
Size 022 042 072 092 102 132 162 212 252 292 322 362
FT-LBS 3 7 7 16 16 31 58 58 130 130 350 485
DISCS 3 3 5 9 13 14 18 18 20 25 27 29
Table B - RECOMMENDED MISALIGNMENT VALUES - TOTAL INDICATOR READING
Size 022 042 072 092 102 132 162 212 252 292 322 362
Installation Angular (in) * 0.010 0.011 0.014 0.016 0.018 0.022 0.024 0.029 0.033 0.037 0.042 0.047
Installation Parallel (in/in) *+ 0.004 0.004 0.004 0.004 0.004 0.004 0.004 0.004 0.004 0.004 0.004 0.004
Operation Angular (in) ** 0.010 0.011 0.014 0.016 0.018 0.022 0.024 0.029 0.033 0.037 0.042 0.047
+ Parallel misalignment is not allowed on single-ex couplings, only spacer couplings
can accommodate parallel misalignment.
“Installation Parallel” values are in inches per inch of spacer length.
“Installation Parallel” T.I.R. = 0.004 x spacer length.
* Other combininations of Angular and Parallel misalignment values are allowable,
but they must yield an “Operation Angular” T.I.R. less than or equal to the value given in Table B.
** The “Operation Angular” T.I.R. is calculated from a recommended 1/4 degree
of misalignment per ex element or disk pack.
Kop-Flex is a trademark of Regal Beloit Corporation or one of its afliated companies.
©2015 Regal Beloit Corporation, All Rights Reserved. MCIM15125E • Form 8499-BE • Printed in USA