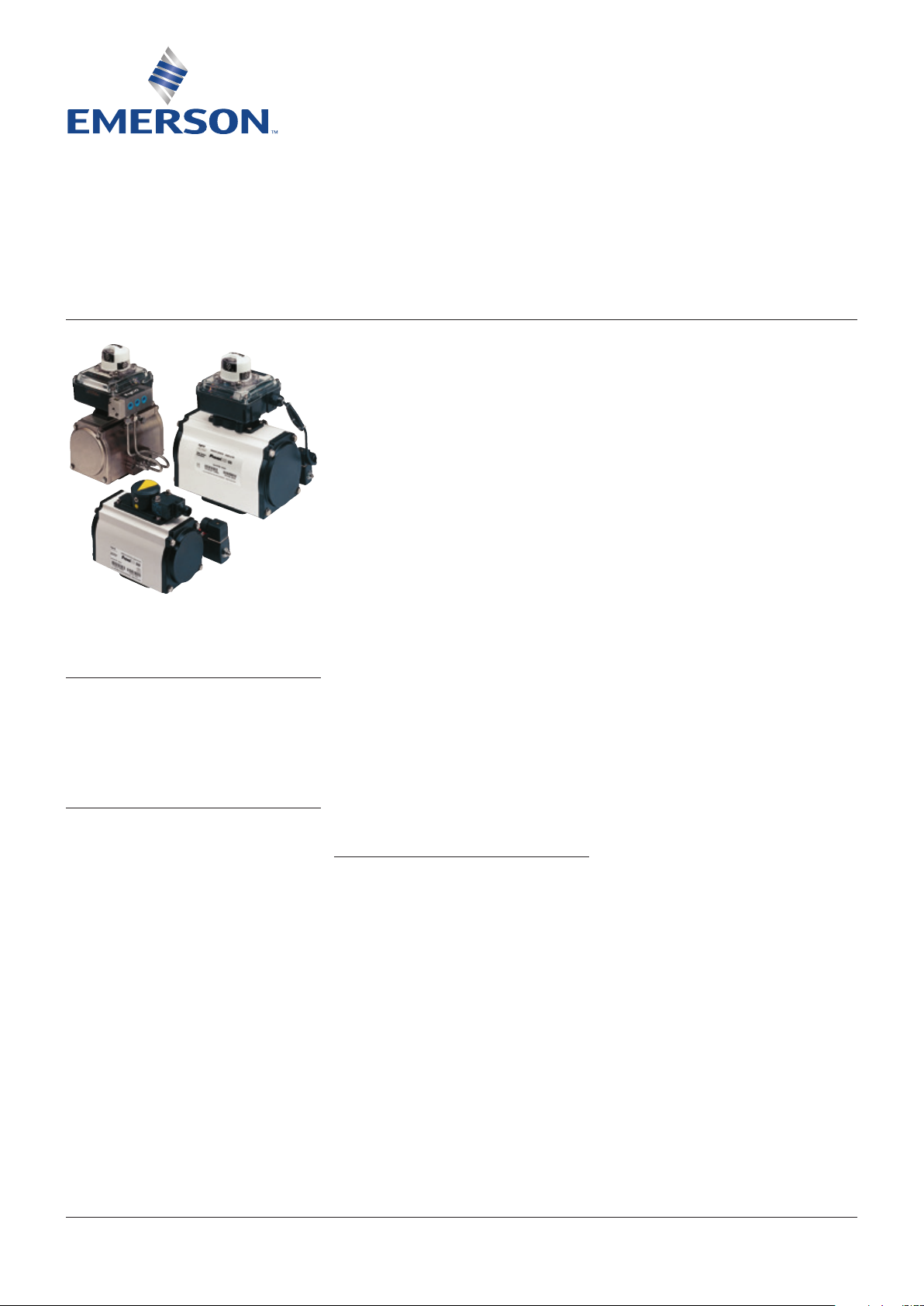
KEYSTONE PREMIAIR PNEUMATIC ACTUATOR
InstallatIon and maIntenance InstructIons
Before installation these instructions must be fully read and understood
DOUBLE ACTING AND SPRING RETURN
ACTUATORS ARE THE SAME SIZE
INTRODUCTION
The Keystone PremiAir Pneumatic Actuator is
a compact, rack and pinion design, conforming
to European and International standard
EN ISO5211 (preferred dimensions).
GENERAL PNEUMATIC SYSTEMS
RECOMMENDATIONS
All Keystone PremiAir Actuators are factory
lubricated with Molyrace LT2, which is a
molybdenum disulphide (MoS2) grease
and, unless the operating environment is
extremely harsh, do not require re-lubrication.
For applications where the environmental
temperature is between -40°C to -30°C,
AeroShell Grease 7 is specified.
To maintain maximum efficiency with this, or
other pneumatic actuators, we advise that the
following basic system recommendations are
followed:
1. Where air pipelines are subjected to
extremes of temperature, the system should
be fitted with suitable air drying equipment.
2. When working at low temperatures, it is
important that the compressed air has been
dried to a dew point of less than the ambient
temperature. If this is not the case, water
will be condensed from the compressed
air and freeze causing damage to the seals
inside the actuator, which could result in
actuator failure.
3. Air control lines should be fitted in
accordance with a ‘Recommended Piping
Practice’ and should not have loops, which
may trap condensate.
4. All air connection pipe ends should be
thoroughly cleaned and deburred after
cutting, to ensure that the pipeline is clear
of debris.
5. If pipelines are hydraulically tested, then
the lines should be 'blown down' with
pressurized air to clear all traces of water,
prior to connecting lines to the actuator.
6. Where pipe fitting sealants are used, they
should be applied to the male threads only,
to avoid excess compound being forced into
the actuator control lines.
7. Where Air Filter Equipment is used, the air
filters should be situated in positions that
allow easy access to maintain and/or drain.
8. Where pneumatic valve positioners, or
pneumatic controllers are fitted to valve
actuator assemblies, oil mist lubricated air
should not be used unless the manufacturer
states specifically that the controllers are
compatible with lubricated air.
Note: PremiAir actuators are rated for air
pressure in the range 2.75 barg (40 psig)
to 8.3 barg (120 psig) and will withstand a
maximum of 10.3 barg (150 psig).
CONSTRUCTION
PremiAir actuators are designed to be mounted
to quarter turn valves either directly or using
the correct mounting brackets/adaptors and
sizing procedures.
All models are of the opposed piston type. Each
piston incorporates an integral rack which
engages with a one piece drive pinion shaft. The
drive shaft is Nitrotech™ treated for maximum
protection and fitted with 'engineered polymer'
bearings. The actuator body is of extruded
aluminium, hard anodized and electrostatic
powder coated.
The design features bolt on mounting plate and
air connection plate for maximum adaptability.
O-rings are used for piston and shaft seals.
For Spring Return actuators, up to four springs
per piston can be fitted between the piston
head and end cap to suit the available operating
air pressure.
Adjustable travel stops are provided for each
end of travel to ensure that the actuator will
open and close the valve precisely.
The output drive is a female double square
(star), conforming to EN ISO5211.
NOTE
These instructions refer to all the range, except
size 180.
For Installation and Maintenance instructions relating
to size 180, please refer to document HDLDS-0012.
VCIOM-00036-EN 17/11Emerson.com/FinalControl © 2017 Emerson. All Rights Reserved.

KEYSTONE PREMIAIR PNEUMATIC ACTUATOR
InstallatIon and maIntenance InstructIons
STANDARD INSTALLATION - DOUBLE AND
SINGLE ACTING UNITS
These instructions assume that the actuators
are installed with the cylinder axis parallel to
the axis of the valve bore (In Line) and are fitted
to Resilient Seated Butterfly Valves having
mounting pads conforming to EN ISO5211.
Single acting actuators are supplied as FAILCLOSE units as standard.
Reverse acting, (FAIL-OPEN), must be specified
at the time of order.
1. Ensure that the valve and actuator are in
the following corresponding positions:
•DoubleActingunitsandSpringReturn
units, (Fail-closed):
Valve closed, actuator fully clockwise.
•DoubleActingunitsandSpringReturn
units, (Fail-open):
Valve open, actuator fully counter-
clockwise
Mounting to ball and high performance
butterfly valves (via bracket)
2a. Secure the mounting bracket to the
underside of the actuator, using four bolts
and washers, as shown in Figure 1.
3a. Install the appropriate coupling onto the
valve stem. The coupling should be lightly
tapped or pressed onto the valve stem.
The use of a lubricant is recommended.
4a. Mount the actuator and bracket onto the
valve top flange using the appropriate bolts.
Mounting to resilient seated butterfly valves
(with EN ISO5211 mounting)
2b. Screw the actuator mounting studs tightly
into the actuator base plate.
3b. Mount the actuator onto the valve top flange
and secure using a lockwasher and nut on
each mounting stud.
All ¼ turn valve types
5. Before installing the valve/actuator
assembly in a piping system, the valve
operation should be verified and adjusted,
if necessary, using the travel stop screws
(see detailed instructions for travel setting)
6. When installing the valve/actuator assembly
into pipeline, ensure that the specific
instructions relating to the valve installation
are followed.
Note: some valves may require to be fitted
into the pipeline prior to mounting the
actuator.
Fail Safe butterfly valves are an example
of this.
NON STANDARD INSTALLATION - DOUBLE
AND SINGLE ACTING UNITS
All ¼ turn valve types
In circumstances where the actuator is
required to be installed in the transverse
position i.e. at right angles to the valve bore
(Across Line), the actuator must be rotated
through 90°.
This is achieved in the following manner:
1. Remove the actuator from the valve or the
bracket by removing the 4 fixing bolts/nuts
and withdraw it vertically from the valve.
2. Rotate the actuator through 90°.
3. Refit actuator to the top of the valve or to
the bracket. The output drive of the actuator
is a double square (star) design, with the
squares being at 90° to each other.
FIGURE 1
Typical installation on ball or high performance
butterfly valves, using bracket mounting
Actuator
Lockwasher
Bolt
Bolt
Coupling
if required
Bracket
if required
FIGURE 2
Typical installation on resilient seated butterfly
valves, with direct EN ISO5211 mounting
Lockwasher
Actuator
Stud
Nut
2
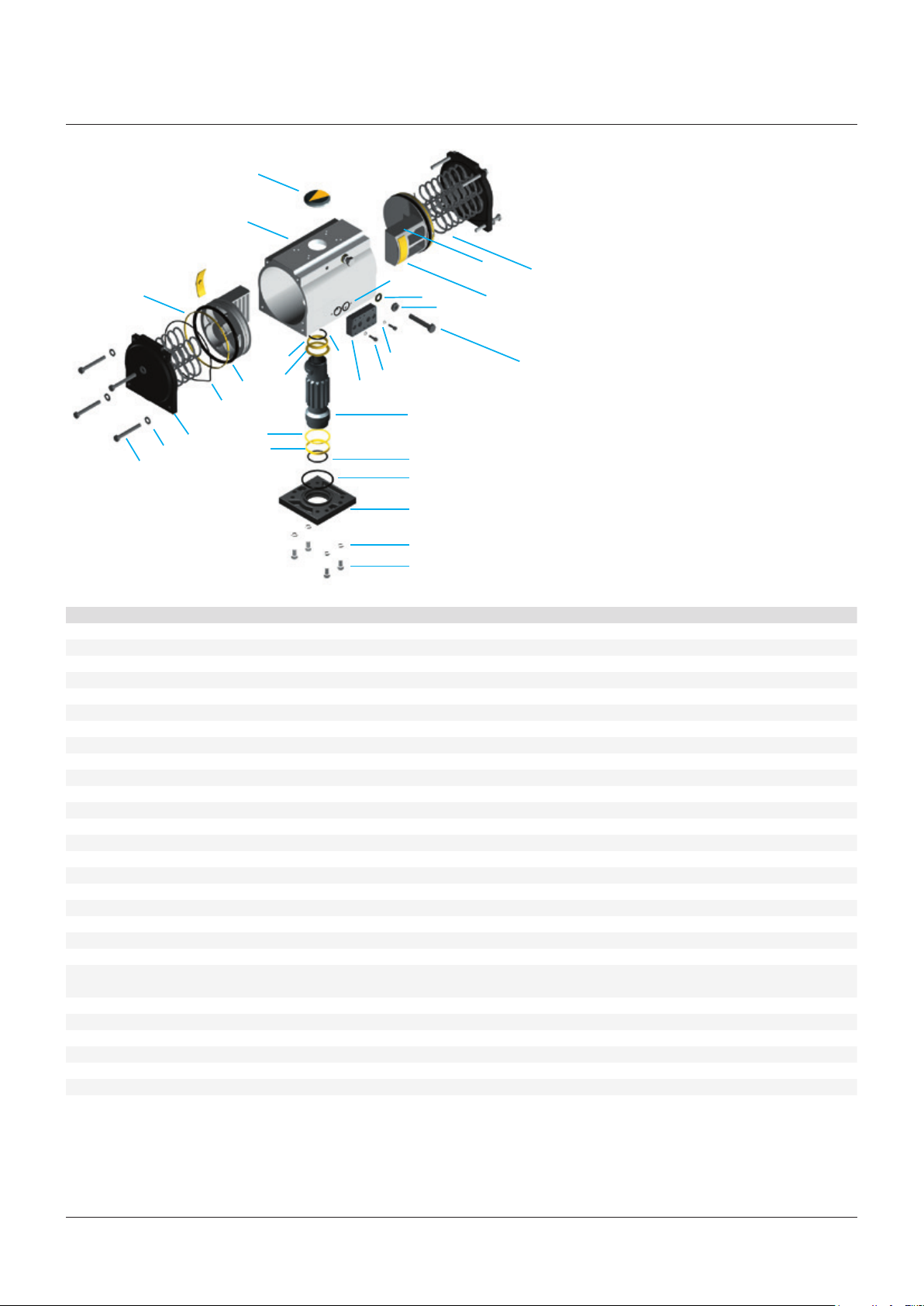
KEYSTONE PREMIAIR PNEUMATIC ACTUATOR
InstallatIon and maIntenance InstructIons - parts IdentIfIcatIon
23
1
8
9
11
24
25
2
17
16
12
10
26
29
15
14
21
20
6
4
27
28
5
19
18
3
7
22
13
MATERIALS OF CONSTRUCTION
Subject Item Material Finish
1 Body Extruded aluminium BS 1474 (6000 series) Hard Anodize + ESPC* or SNP**
2 End cap Die cast aluminium DIN1725 Alloy 231 Chromate + ESPC* or SNP**
3 Piston Die cast aluminium DIN1725 Alloy 231 Anodize or SNP**
4 Pinion shaft Carbon steel BS 1490:1983 212 A42 Nitrotech™*** or SNP**
5 Base plate Die cast aluminium DIN1725 Alloy 231 Chromate + ESPC* or SNP**
6 Air connection plate Aluminium DIN1725 Alloy 231 Chromate + ESPC* or SNP**
7 Piston backing pad Devlon-V™ Natural
8 Piston support ring Devlon-V™ Natural
9 Top bearing Devlon-V™ Natural
10 Bottom bearing Devlon-V™ Natural
11 Top spacer Devlon-V™ Natural
12 Bottom spacer Devlon-V™ Natural
13 Stop bolt Stainless steel A2 / 70 Natural
14 Lock nut Stainless steel A2 / 70 Natural
15 Sealing washer Stainless steel A2 / 70 Natural
16 End cap bolt Stainless steel A2 / 70 Natural
17 End cap washer Stainless steel A2 / 70 Natural
18 Base plate bolt Stainless steel A2 / 70 Natural
19 Base plate washer Stainless steel A2 / 70 Natural
20 Air connection plate bolt Stainless steel A2 / 70 Natural
21 Air connection plate washer Stainless steel A2 / 70 Natural
22 Spring Chrome silicon spring steel
BS 2806 685 A55 HD R2 Oil dip
23 Indicator ABS Natural
24 Piston O-ring Rubber-NBR or FPM Natural
25 End cap O-ring Rubber-NBR or FPM Natural
26 Shaft top O-ring Rubber-NBR or FPM Natural
27 Shaft bottom O-ring Rubber-NBR or FPM Natural
28 Base plate O-ring Rubber-NBR or FPM Natural
29 Air connection plate O-ring Rubber-NBR or FPM Natural
NOTES
* ESPC = Electrostatic powder coating
** SNP = Special nickel protection finish
*** Nitrotech™ = Roprietary corrosion resistant finish
3