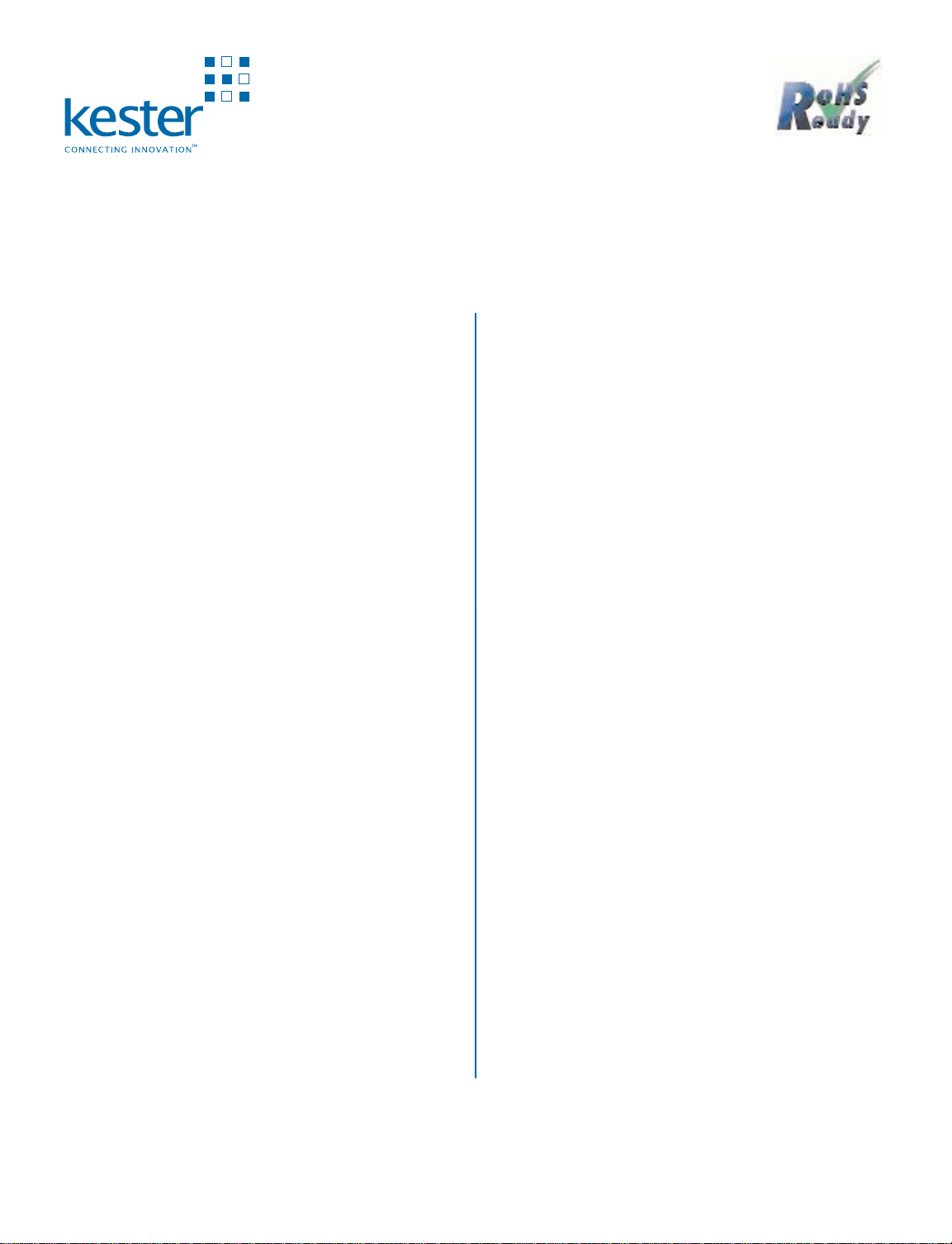
®
OR421
OR421
Organic Cored W
Organic Cored W
ire
ire
For Lead-bearing and Lead-free alloys
For Lead-bearing and Lead-free alloys
Product Description
Kester OR421 is a high activity , water soluble,
cored wire flux. The OR421 is more heat st able,
exhibits better wetting cap abilities and has less
odor than competitive product s. The residues left
by OR421 are near neutral pH and therefore also
less corrosive. The OR421 is classified as ORH1
per J-STD-004.
Kester OR421 cored wire solder can be utilized
with an open torch or a soldering iron. OR421 will
solder copper as well as more dif ficult to solder
materials such as brass and nickel. OR421 can
be used on pipes or tubing for applications such as
refrigeration coils and heat exchangers. The heat
stability of Kester OR421 makes it ideal for high
temperature alloys such as 95Sn/5Sb,
10Sn88Pb2Ag and 10Sn90Pb.
Performance Characteristics:
• Highest activity available
• Compatible with high temperature alloys
• Easy to clean
• Classified as ORH1 per J-STD-004
RoHS Compliance
This product meets the requirements of the RoHS
(Restriction of Hazardous Subst ances) Directive,
2002/95/EC Article 4 for the st ated banned
substances. (Applies only if this core flux is
combined with a lead free alloy)
Reliability Properties
Copper Mirror Corrosion: High
Tested to J-STD-004, IPC-TM-650, Method 2.3.32
Corrosion Test: High
Tested to J-STD-004, IPC-TM-650, Method 2.6.15
Silver Chromate: Fail
Tested to J-STD-004, IPC-TM-650, Method 2.3.33
Chloride and Bromides: 6.95%
Tested to J-STD-004, IPC-TM-650, Method 2.3.35
Fluorides by Spot Test: Pass
Tested to J-STD-004, IPC-TM-650, Method 2.3.35.1
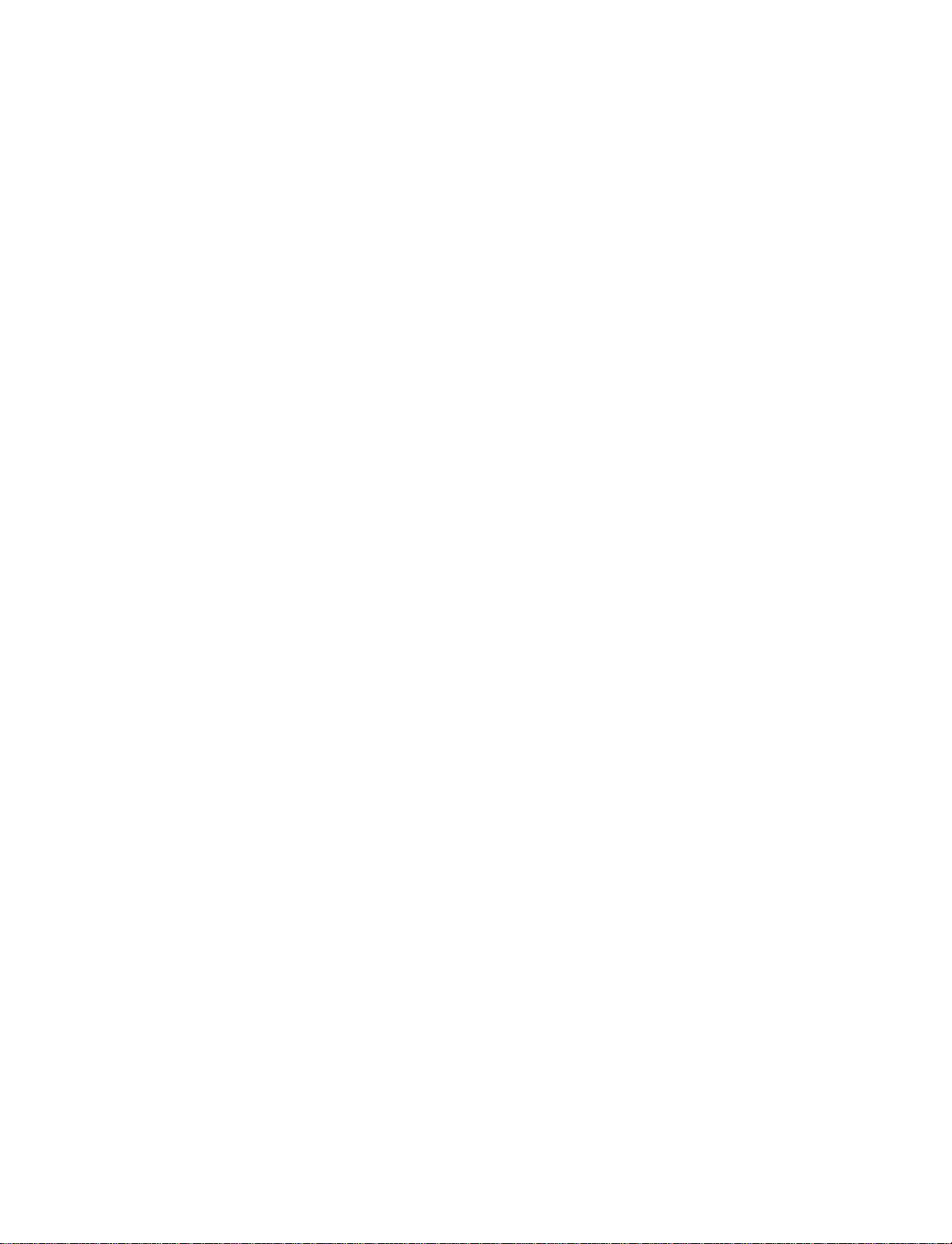
Application Notes
Availability:
Kester OR421 is available in a wide variety of alloys, wire diameters and flux percent ages. For most
applications, Sn63Pb37 or Sn96.5Ag3.0Cu0.5 is used. Consult the alloy temperature chart in Kester’s product
catalog for a comprehensive alloy list. The standard wire diameter for most applications is 1.00mm (0.031in).
Wire diameters range from 0.25 - 6.00mm (0.010 to 0.250in). A "Standard Wire Diameters" chart also is also
included in Kester ’s product cat alog. The amount of flux in the wire dict ates the ease of soldering for an
application. For most applications, core 66 (3.3% flux by weight) is recommended. Other core sizes, 50 and
58, (1.1% and 2.2% respectively) are available. Kester OR421 is p ackaged on spools of dif ferent sizes to
accommodate a variety of applications.
Process Considerations:
Solder iron tip temperatures are most commonly between 315-371°C (600-700°F) for Sn63Pb37 and
Sn62Pb36Ag02 alloys and 371-427°C (700-800°F) for lead-free alloys. Heat both the land area and component
lead to be soldered with the iron prior to adding Kester OR421 cored wire. Apply the solder wire to the land
area or component lead. Do not apply the wire directly to the soldering iron tip. If needed, Kester 2331-ZX
organic flux may be used as a comp atible liquid flux to aid in reworking soldered joint s.
Cleaning:
Kester OR421 Flux leaves a residue after soldering that is hygroscopic and ionizable. Removal of ionizable
salts can best be accomplished by washing the assembly with a 2-5% solution of Kester 5760 Neutralizer in
water, followed by a thorough warm water rinse. The recommended water temperature is 54 ± 6°C (130 ±
10°F). If the residue is charred due to excessive heating during soldering, mechanical scrubbing can be
used to remove the decomposed char.
Storage, Handling, and Shelf Life:
Storage must be in a dry , non-corrosive environment. The surface may lose it s shine and appear a dull
shade of grey. This is a surface phenomena and is not detrimental to product functionality. Flux cored solder
wire has a limited shelf life determined by the alloy used in the wire. For alloys cont aining > 70% lead, the
shelf life is two years from date of manufacture. Other alloys have a shelf life of three years from date of
manufacture.
Health & Safety:
This product, during handling or use, may be hazardous to health or the environment. Read the Material
Safety Data Sheet and warning label before using this product.