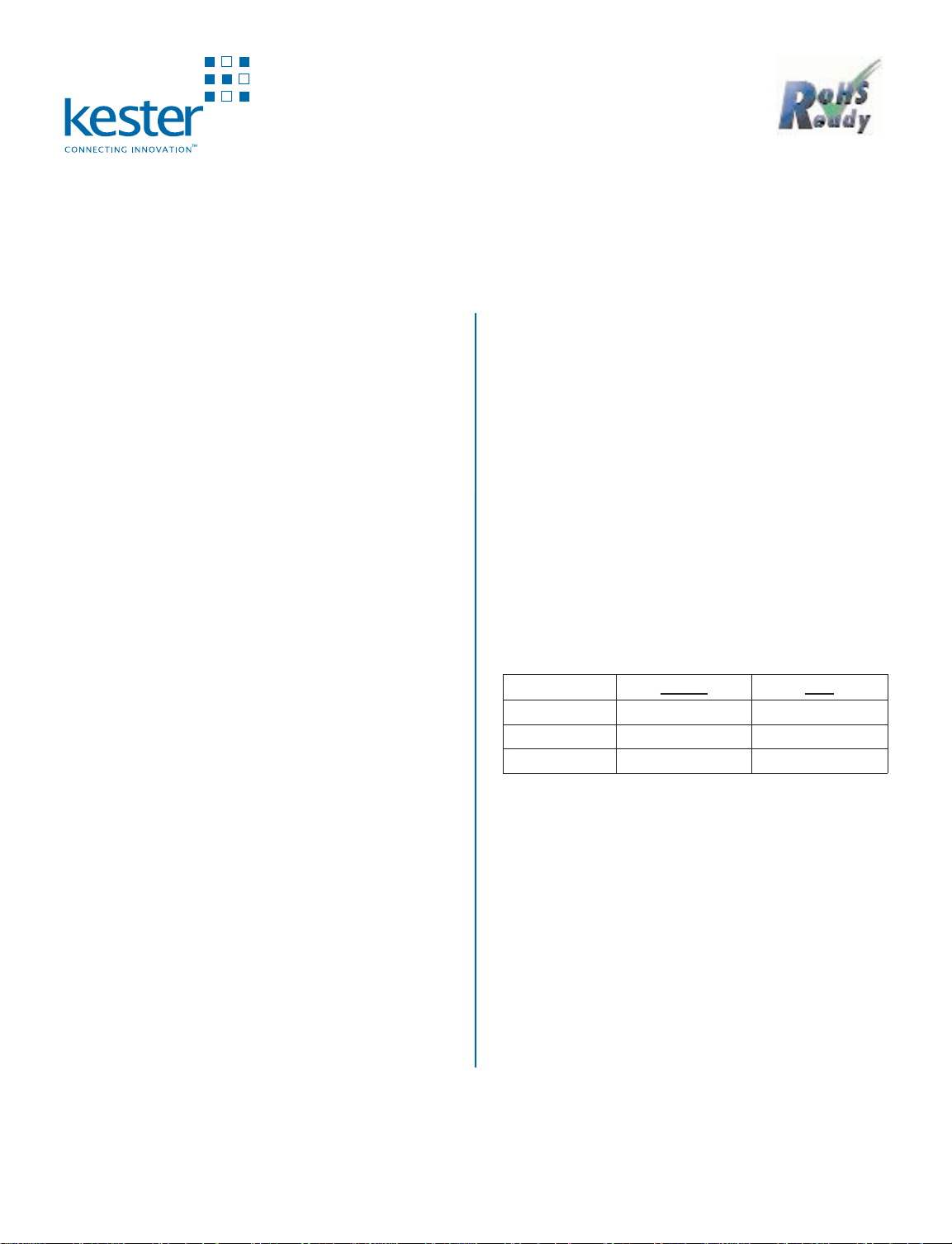
®
275
275
No-Clean Cored W
No-Clean Cored W
For Lead-bearing and Lead-free alloys
For Lead-bearing and Lead-free alloys
Product Description
Kester 275 No-Clean Flux for cored solder wire
was developed to provide superior wetting
performance for hand soldering in the electronics
industry. The chemistry is based on some of the
same principles that have been safely used for
years in mildly activated rosin fluxes. The use of
275 No-Clean Flux results in an extremely clear
post-soldering residue without cleaning. The
unique chemistry in Kester 275 was also designed
to reduce spattering common to most core fluxes.
Kester 275 can be used for both lead bearing and
lead-free soldering.
Performance Characteristics:
• Colorless translucent residues
• Improves wetting performance
• Excellent solderability and fast wetting to a
variety of surface finishes
• Eliminates the need and expense of cleaning
• Low smoke and odor
• Low spattering
• Compatible with leaded and lead-free alloys
• Classified as ROL0 per J-STD-004
• Compliant to Bellcore GR-78
RoHS Compliance
This product meets the requirements of the RoHS
(Restriction of Hazardous Subst ances) Directive,
2002/95/EC Article 4 for the stated banned
substances. (Applies only if this core flux is
combined with a lead free alloy)
ire
ire
Reliability Properties
Copper Mirror Corrosion: Low
Tested to J-STD-004, IPC-TM-650, Method 2.3.32
Corrosion Test: Low
Tested to J-STD-004, IPC-TM-650, Method 2.6.15
Silver Chromate: Pass
Tested to J-STD-004, IPC-TM-650, Method 2.3.33
Chloride and Bromides: None Detected
Tested to J-STD-004, IPC-TM-650, Method 2.3.35
Fluorides by Spot Test: Pass
Tested to J-STD-004, IPC-TM-650, Method 2.3.35.1
SIR, IPC (typical): Pass
Tested to J-STD-004, IPC-TM-650, Method 2.6.3.3
Blank 275
Day 1
Day 4
Day 7
Spread Test (typical):
Tested to J-STD-004, IPC-TM-650, Method 2.4.46
Flux Core Solder
285 Mildly Activated Rosin 213 (0.33) 335 (0.52)
245 No-Clean 200 (0.31) 348 (0.54)
275 No-Clean 219 (0.34) 361 (0.56)
1.6 ×1010Ω 1.1 × 1010Ω
1.2 ×1010Ω 9.2 × 10
9
Ω
1.1 ×1010Ω 8.6 × 109Ω
Area of Spread mm2(in2)
Sn96.5Ag3.0Cu0.5 Sn63Pb37
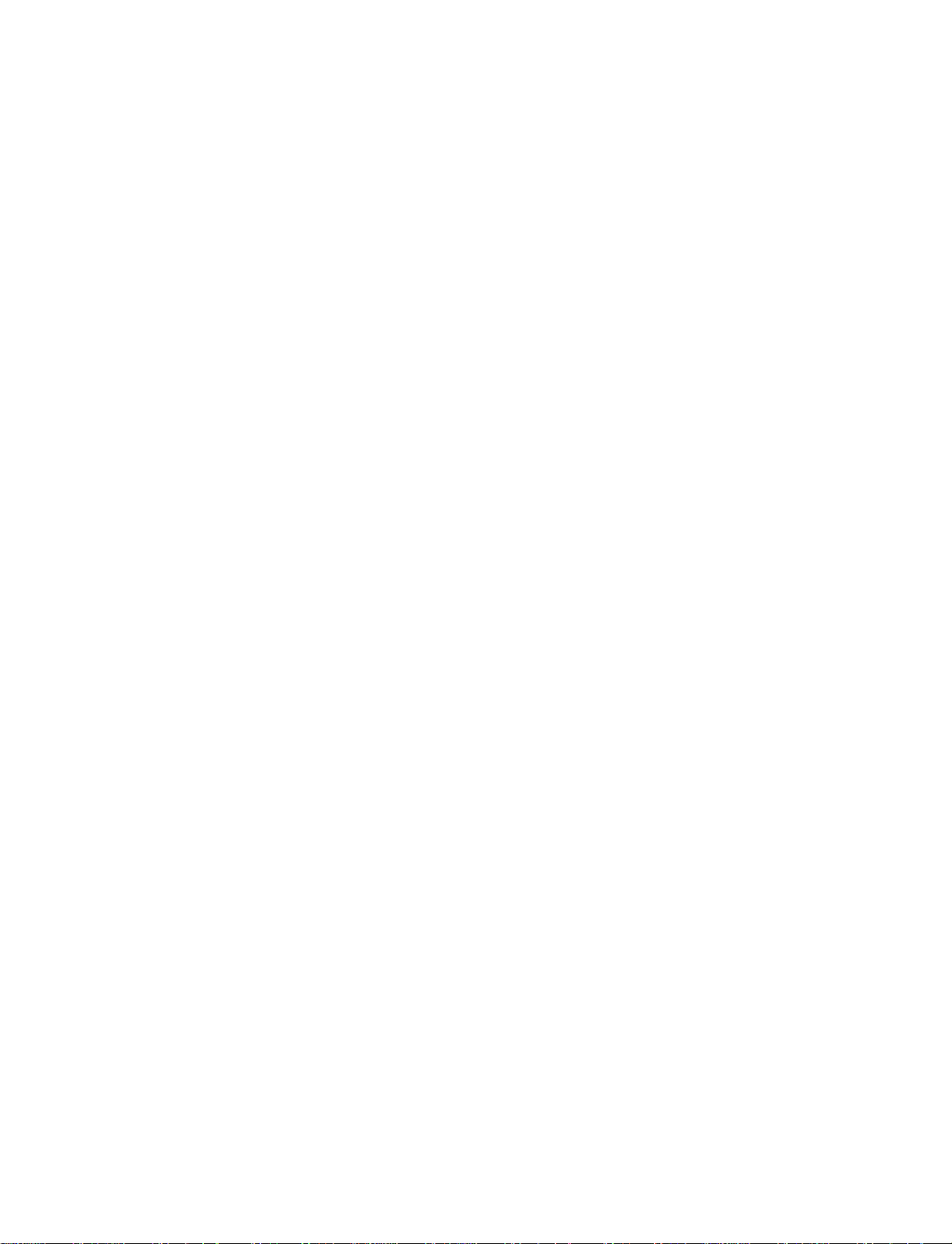
Application Notes
Availability:
Kester 275 is available in a wide variety of alloys, wire diameters and flux percentages. For most applications,
Sn63Pb37or Sn96.5Ag3.0Cu0.5 is used. Consult the alloy temperature chart in Kester’s product catalog for
a comprehensive alloy list. The st andard wire diameter for most applications is 1.00mm (0.031in). Wire
diameters range from 0.25 - 6.00mm (0.010 to 0.250in). A "Standard Wire Diameters" chart also is also
included in Kester’s product cat alog. The amount of flux in the wire dict ates the ease of soldering for an
application. For tin/lead applications, core 50 or 58 (1.1 and 2.2% flux by weight) are recommended. For
Lead-free and high-lead applications, core 58 or 66 (2.2 and 3.3% flux by weight) are recommended. Kester
275 is packaged on spools of different sizes to accommodate a variety of applications.
Process Considerations:
Solder iron tip temperatures are most commonly between 315-371°C (600-700°F) for Sn63Pb37 and
Sn62Pb36Ag02 alloys and 371-427° C (700-800° F) for lead-free alloys. Heat both the land area and
component lead to be soldered with the iron prior to adding Kester 275 cored wire. Apply the solder wire to
the land area or component lead. Do not apply the wire directly to the soldering iron tip. If needed, Kester
959T no clean, liquid flux may be used as a compatible flux to aid in reworking soldered joints. Kester 959T
is also available in Flux-Pens
Cleaning:
The 275 residues are non-conductive, non-corrosive and do not require removal in most applications. The
flux residues are comparable to a conventional RMA except that the 275 residue is clear and colorless.
Storage, Handling, and Shelf Life:
Storage must be in a dry , non-corrosive environment. The surface may lose it s shine and appear a dull
shade of grey. This is a surface phenomena and is not detrimental to product functionality. Flux cored solder
wire has a limited shelf life determined by the alloy used in the wire. For alloys cont aining > 70% lead, the
shelf life is two years from date of manufacture. Other alloys have a shelf life of three years from date of
manufacture.
®
for optimum board cleanliness.
Health & Safety:
This product, during handling or use, may be hazardous to health or the evironment. Read the Material
Safety Data Sheet and warning label before using this product.