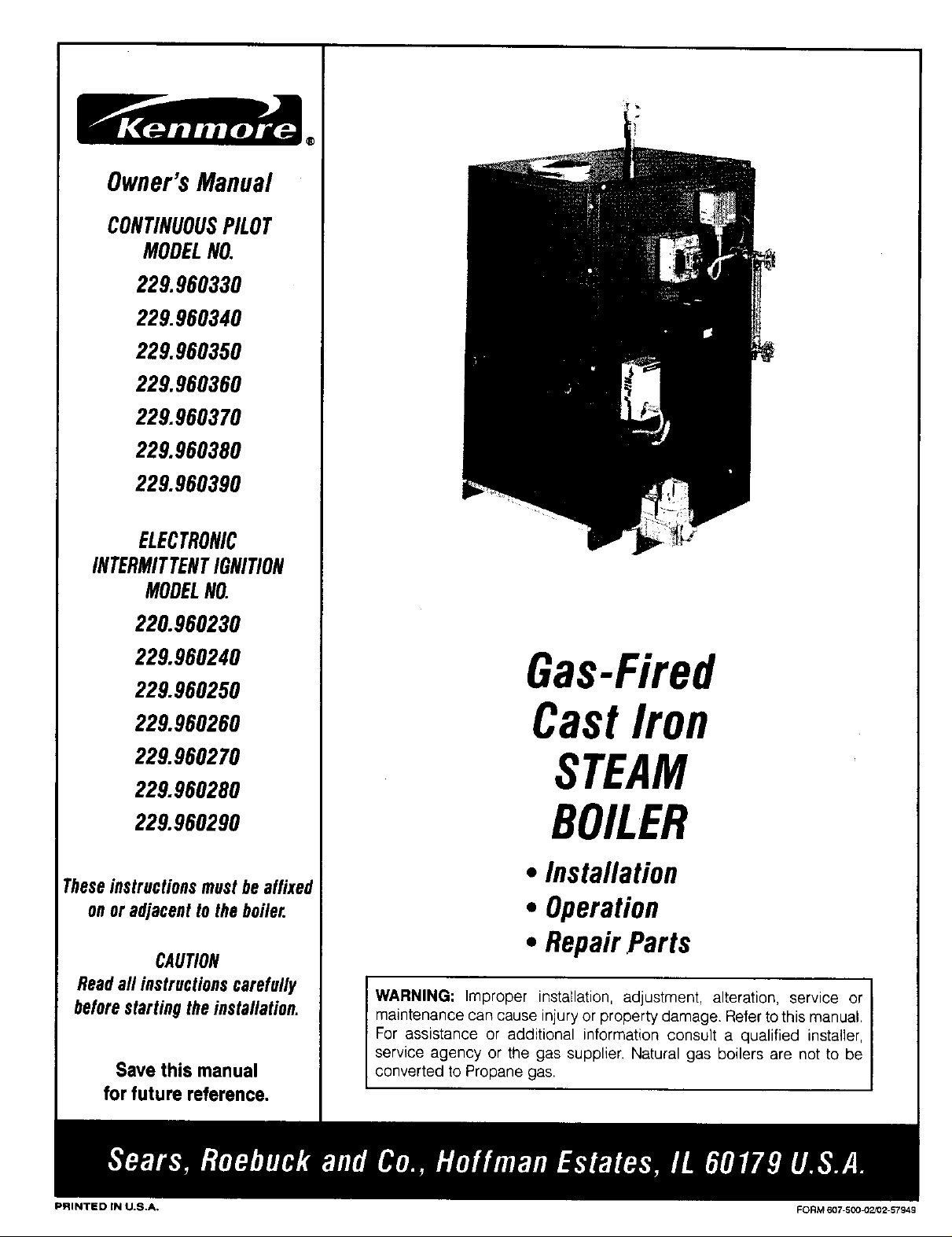
Owner'sManual
CONTINUOUSPILOT
MODELNO.
229.960330
229.960340
229.960360
229.960360
229.960370
229.960380
229.960390
ELECTRONIC
INTERMITTENTIGNITION
MODELNO.
®
220.960230
229.960240
229.960260
229.960260
229.960270
229.960280
229.960290
Theseinstructionsmustbeaffixed
onor adjacenttotheboiler.
CAUTION
Readall instructionscarefully
beforestartingtheinstallation.
Save this manual
for future reference.
Gas-Fired
CastIron
STEAM
BOILER
• Installation
• Operation
• RepairParts
WARNING: Improper installation, adjustment, alteration, service or
maintenance can cause injury or property damage. Refer to this manual.
For assistance or additional information consult a qualified installer,
service agency or the gas supplier. Natural gas boilers are not to be
converted to Propane gas.
PRINTED IN U.S.A. FOAM e37-_00-02_02-6"7949
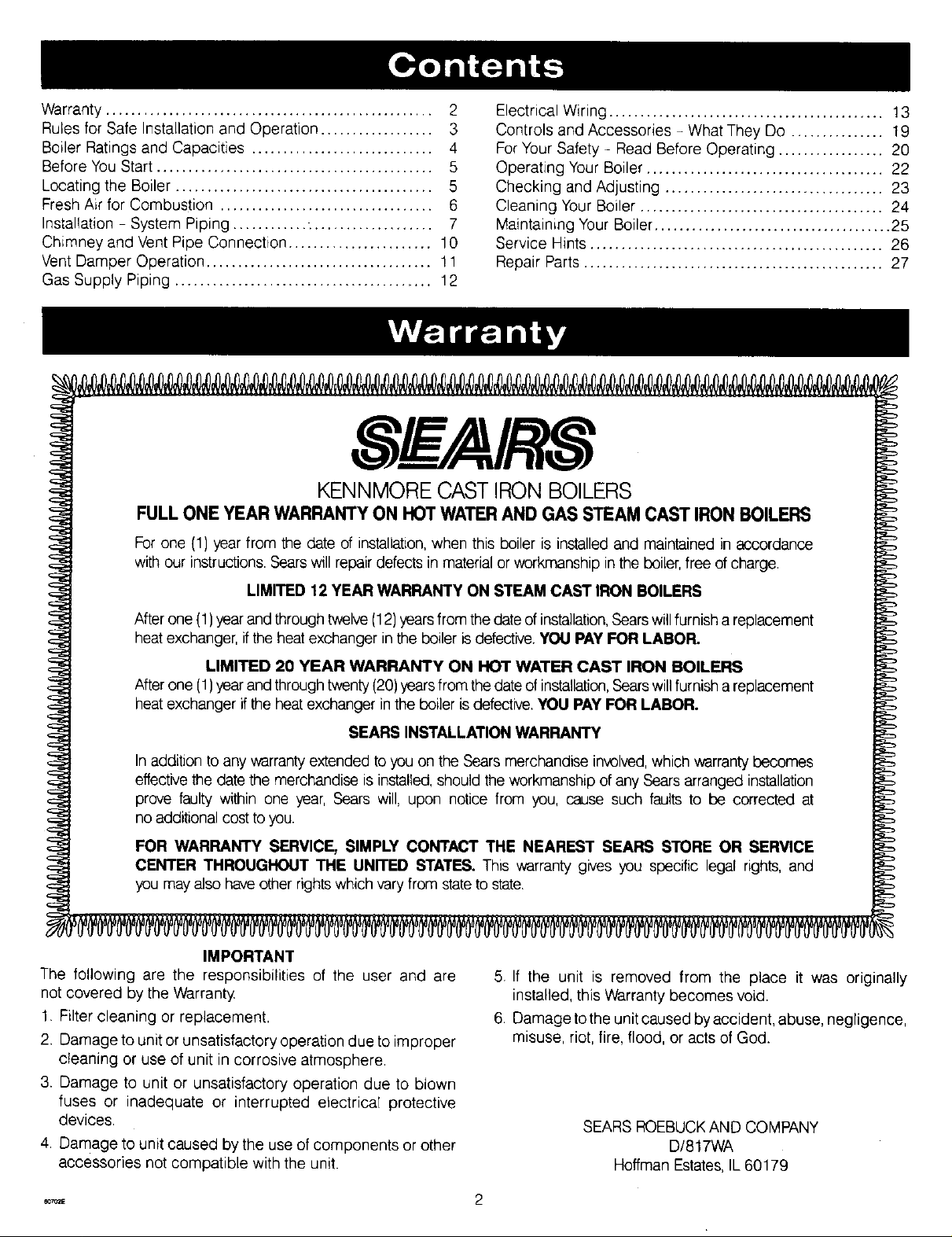
Warranty .................................................... 2
Rules for Safe Installation and Operation .................. 3
Boiler Ratings and Capacities ............................. 4
Before You Start ............................................ 5
Locating the Boiler ......................................... 5
Fresh Air for Combustion .................................. 6
Installation - System Piping ............ : ................... 7
Chimney and Vent Pipe Connection ....................... 10
Vent Damper Operation .................................... ! 1
Gas Supply Piping ......................................... 12
E_ AIRS
KENNMORE CAST IRON BOILERS
FULLONEYEARWARRANTYON HOTWATERANDGAS STEAMCASTIRONBOILERS
For one {1) year from the date of installation,when this boiler is installed and maintained in accordance
with our instructions. Searswill repair defects in material or workmanship in the boiler, free of charge.
LIMITED 12 YEAR WARRANTY ON STEAM CAST IRON BOILERS
Electrical Wiring ............................................ !3
Controls and Accessories - What They Do ............... 19
For Your Safety - Read Before Operating ................. 20
Operating Your Boiler ...................................... 22
Checking and Adjusting ................................... 23
Cleaning Your Boiler ....................................... 24
Maintaining Your Boiler ...................................... 25
Service Hints ............................................... 26
Repair Parts ................................................ 27
After one {1)yearand through twelve (12}yearsfrom the date of installation,Searswillfurnish a replacement
heatexchanger, ifthe heat exchanger in the boiler is defective. YOU PAY FOR LABOR.
LIMITED 20 YEAR WARRANTY ON HOT WATER CAST IRON BOILERS
After one (1)year and through twenty(20) years from the date of installation,Searswill furnish a replacement
heat exchanger ifthe heat exchanger in the boiler isdefective. YOU PAY FOR LABOR.
SEARS INSTALLATION WARRANTY
Inaddition to any warranty extended to you on the Sears merchandise involved,which warranty becomes
effective the date the merchandise is installed,should the workmanship of any Sears arranged installation
prove faulty within one year, Sears will, upon notice from you, cause such faults to be corrected at
no additional cost to you.
FOR WARRANTY SERVICE, SIMPLY CONTACT THE NEAREST SEARS STORE OR SERVICE
CENTER THROUGHOUT THE UNITED STATES. This warranty gives you specific legal rights, and
you mayalso haveother rights which vary from state tostate.
IMPORTANT
The following are the responsibilities of the user and are
not covered by the Warranty
1. Filter cleaning or replacement.
2. Damage to unit or unsatisfactory operation due to improper
cleaning or use of unit in corrosive atmosphere.
3. Damage to unit or unsatisfactory operation due to blown
fuses or inadequate or interrupted electricaI protective
devices.
4. Damage to unit caused by the use of components or other
accessories not compatible with the unit.
5. If the unit is removed from the place it was originally
installed, this Warranty becomes void.
6. Damage tothe unit caused by accident, abuse, negligence,
misuse, riot, fire, flood, or acts of God.
SEARS ROEBUCKAND COMPANY
D/817WA
Hoffman Estates, IL 60179
®,_E 2
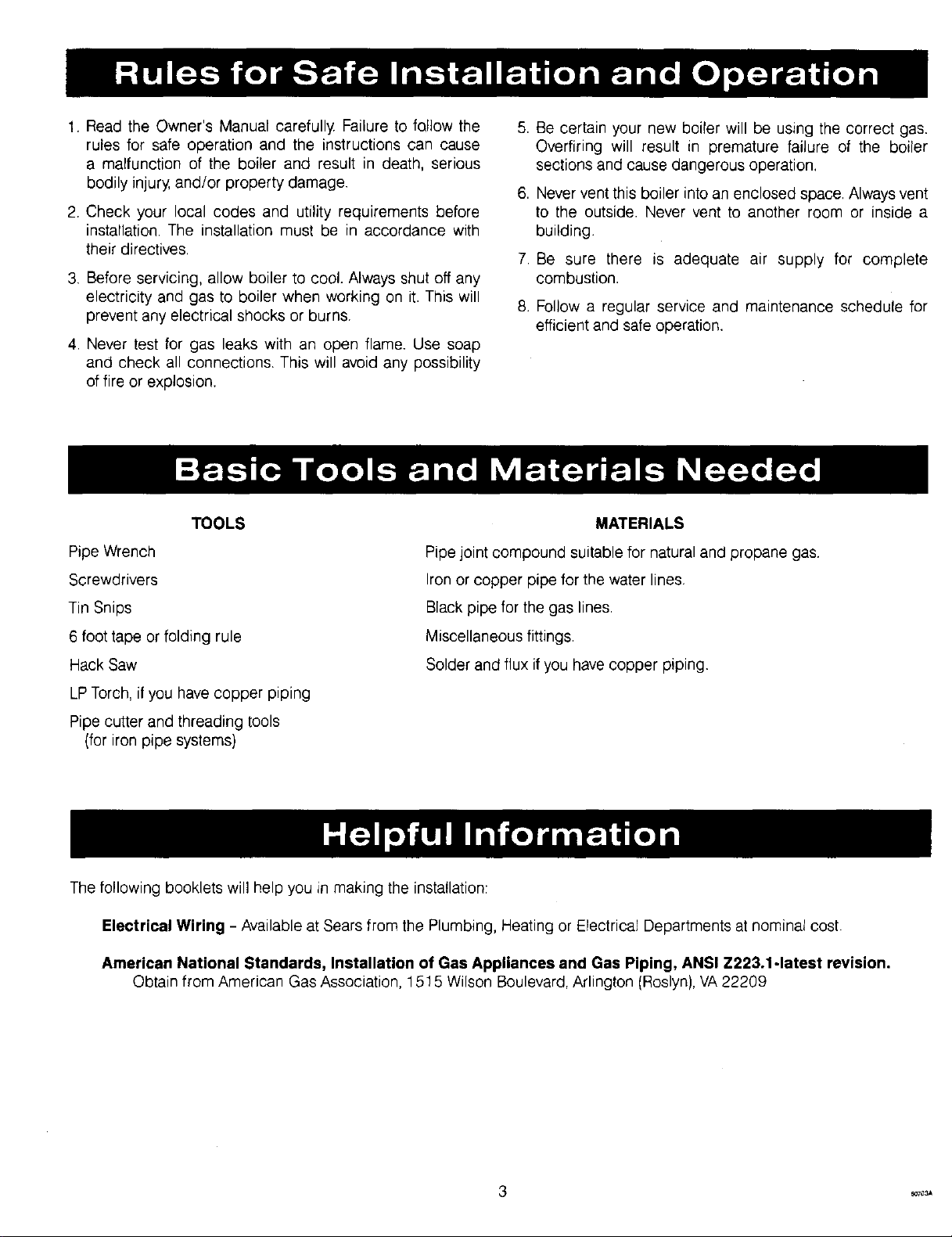
1. Read the Owner's Manual carefully Failure to fallow the
rules for safe operation and the instructions can cause
a malfunction of the boiler and result in death, serious
bodily injury, and/or property damage.
2. Check your local codes and utility requirements before
installation, The installation must be in accordance with
their directives,
3. Before servicing, allow boiler to cool. Always shut off any
electricity and gas to boiler when working on it. This will
prevent any electrical shocks or burns.
4. Never test for gas leaks with an open flame. Use soap
and check all connections. This will avoid any possibility
of fire or explosion.
5. Be certain your new boiler will be using the correct gas.
Overfiring will result in premature failure of the boiler
sections and cause dangerous operation.
6. Never vent this boiler into an enclosed space. Always vent
to the outside. Never vent to another room or inside a
building.
7. Be sure there is adequate air supply for complete
combustion.
8. Follow a regular service and maintenance schedule for
efficient and safe operation.
TOOLS
Pipe Wrench
Screwdrivers
Tin Snips
6 foot tape or folding rule
Hack Saw
Pipe joint compound suitable for natural and propane gas.
Iron or copper pipe for the water lines,
Black pipe for the gas lines.
Miscellaneous fittings.
Solder and flux if you have copper piping.
MATERIALS
LP Torch, if you have copper piping
Pipe cutter and threading tools
(for iron pipe systems)
The following booklets will help you in making the installation:
Electrical Wiring - Available at Sears from the Plumbing, Heating or Electrical Departments at nominal cost.
American National Standards, Installation of Gas Appliances and Gas Piping, ANSI Z223.1-1atest revision.
©btain from American Gas Association, 1515 Wilson Boulevard, Arlington (Roslyn), VA22209
e07_3,_
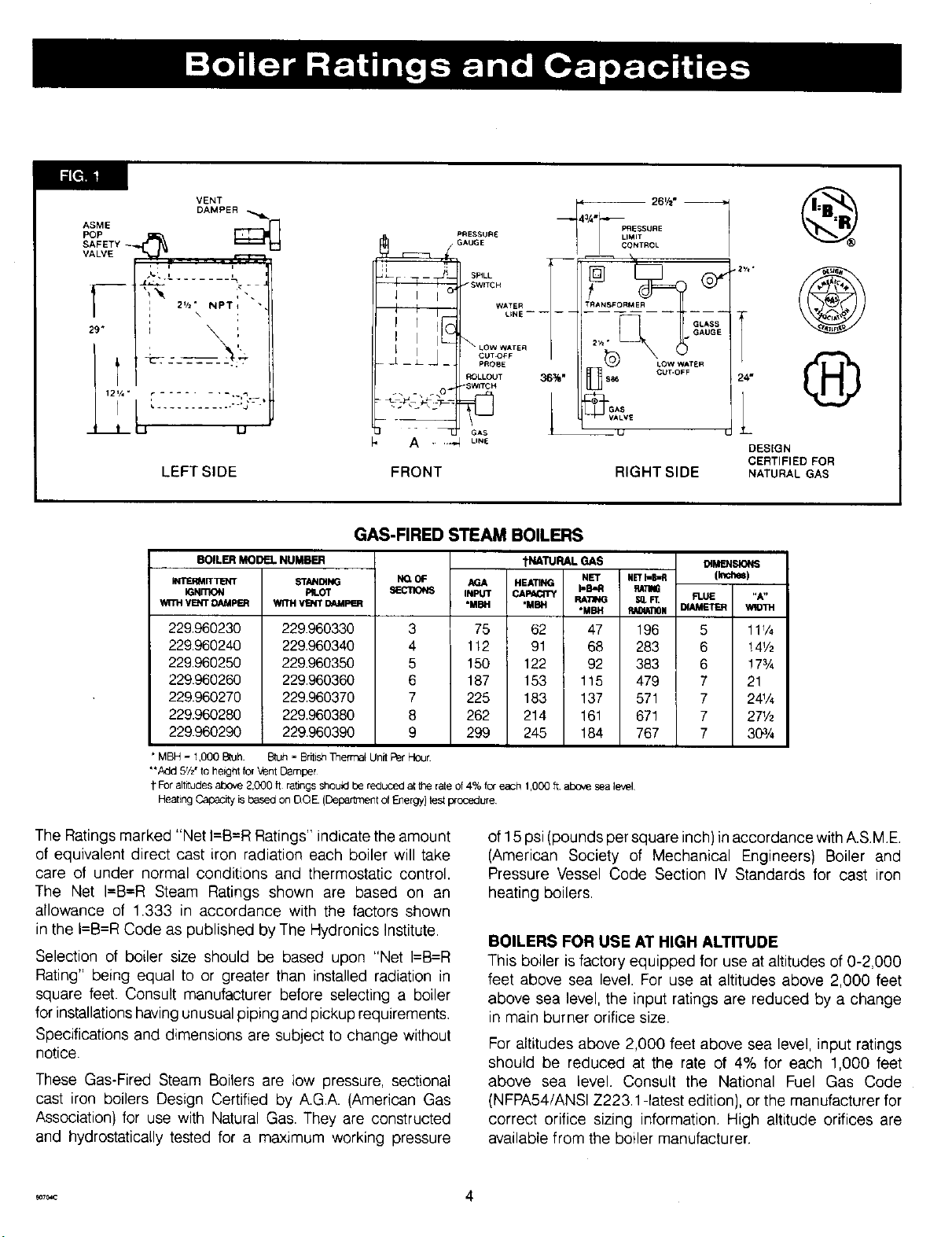
VENT
DAMPER
POP
ASME
SAFETY
VALVE
, ; J i
: 2'/2" NPT _ ",
\ :
29" ; \ :
; LEFT SIDE
I
i
BOILER MODEL NUMBER DgMENSlO_
INTERMrr_NT s'rANOING NO.OF (_)
IGNITION PLOT SECTIONS
Wr_l VIg_IT I_MPER WiTH vl_rr DAMPER DIAMErE_ WlEI].I
229960230
22996024O
229960250
229960260
229.960270
229.960280
229.960290
* MBH = 1,000 8tuh. Btuh = British Tnermat Unit Per Hour
**Add 5Vz"to height for Vent Damper
1"For altitudes above 2,000 ft rabngs should be reduced a[ the rate of 4% fc_ each 1,000 ft above sea level
Heating Capacity is based on DOE. (Department of Energy) test prc_edure
229.960330
229.960340
229.960350
229960360
229.960370
229.960380
229.960390
J I I
I iL
_ -, _o _ _
A ...._ UNE
PRESSURE
GAUGE
/ SWITCI-€
WATER
LiNE -- __ --
SPILL '_
PROBE
ROLLOUT 36_e"
-SWITCH
GAS
43/,=. 261/="
_$8 6 CUT'OFF
GAS
FRONT RIGHT SIDE
GAS-FIRED STEAM BOILERS
"[h_TURALG/_
AGA HEATING _B-R RARN6
INPUT CAPAQ'rY
"MW'I *MOH RA'J_NG SO.
3
4
5
6
7
8
9
75 62 47 196 5 111_
112 91 68 283 6 14V_
150 122 92 383 6 !7¾
187 153 115 479 7 21
225 183 137 571 7 24%
262 214 161 67! 7 2_/_
299 245 184 767 7 303/4
NET N_ _B_
°MBH PJ_4ATIQ#
LIMIT
RESSURE
ONTROL
24"
DESIGN
CERTIFIED FOR
NATURAL GAS
FLUE "A"
The Ratings marked "Net I=B=R Ratings" indicate the amount
of equivalent direct cast iron radiation each boiler will take
care of under normal conditions and thermostatic control.
The Net I=B=R Steam Ratings shown are based on an
allowance of 1.333 in accordance with the factors shown
in the I=B=R Code as published by The Hydronics Institute.
Selection of boiler size should be based upon "Net I--E_R
Rating" being equal to or greater than installed radiation in
square feet. Consult manufacturer before selecting a boiler
for installations having unusual piping and pickup requirements,
Specifications and dimensions are subject to change without
notice.
These Gas-Fired Steam Boilers are low pressure, sectional
cast iron boilers Design Certified by A.G.A. (American Gas
Association} for use with Natural Gas. They are constructed
and hydrostatically tested for a maximum working pressure
r_7_c 4
of 15 psi (pounds per square inch) in accordance with A.S.M.E.
(American Society of Mechanical Engineers) Boiler and
Pressure Vessel Code Section IV Standards for cast iron
heating boilers.
BOILERS FOR USE AT HIGH ALTITUDE
This boiler is factory equipped for use at altitudes of 0-2,000
feet above sea level. For use at altitudes above 2,000 feet
above sea level, the input ratings are reduced by a change
in main burner orifice size.
For altitudes above 2,000 feet above sea level, input ratings
should be reduced at the rate of 4% for each 1,000 feet
above sea level. Consult the National Fuel Gas Code
(NFPA54/ANSl Z223.1 -latest edition}, or the manufacturer for
correct orifice sizing information. High altitude orifices are
available from the boiler manufacturer.
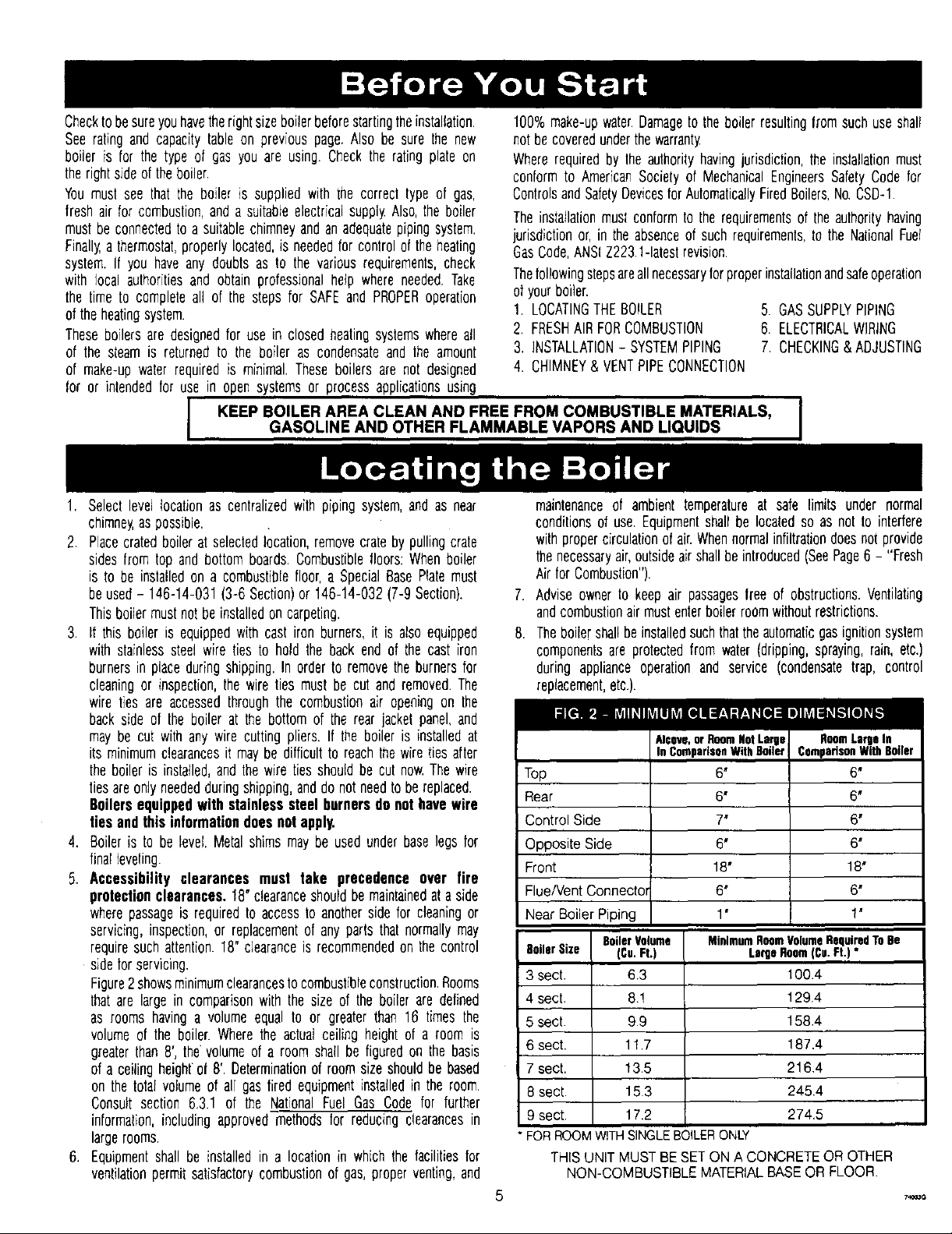
Checktobesureyouhavetherightsizeboilerbeforestartingtheinstallation.
Seeratingand capacitytableon previouspage.Alsobe surethe new
boiler is for the type of gas youare using.Checkthe ratingplate on
therightsideof theboiler.
Youmustsee that the boiler is suppliedwith the correct type of gas,
fresh air for combustion,anda suitableelectricalsupplyAlso,the boiler
mustbe connectedtoa suitablechimneyandanadequatepipingsystem.
Finallya thermostat,properlylocated,is neededfor controlof theheating
system.If you haveany doubtsas to the variousrequirements,check
with local authoritiesandobtainprofessionalhetp whereneeded.Take
the time to completeall of the stepsfor SAFEandPROPERoperation
oftheheatingsystem.
Theseboilersare designedfor usein closedheatingsystemswhereall
of the steam is returnedto the boileras condensateandthe amount
of make-upwater requiredis minimal.Theseboilersare not designed
for or intendedforuse in opensystemsor processapplicationsusing
KEEP BOILER AREA CLEAN AND FREE FROM COMBUSTIBLE MATERIALS,
I
GASOLINE AND OTHER FLAMMABLE VAPORS AND LIQUIDS
100%make-upwater.Damageto theboilerresultingfromsuchuseshall
notbecoveredunderthewarranty
Whererequiredby the authorityhavingjurisdiction,the installationmust
conformto AmericanSocietyof MechanicalEngineersSafetyCodefor
ControlsandSafetyDevicesforAutomaticallyFiredBoilers,No.CSD-1.
Theinstallationmus_conformto therequirementsof theauthorityhaving
jurisdictionor,in theabsenceof suchrequirements,to the NationalFuel
GasCode,ANSIZ223.1-1atestrevision.
Thefollowingstepsareallnecessaryforproperinstallationandsafeoperation
ol yourboiler.
1. LOCATINGTHEBOILER 5. GASSUPPLYPIPING
2. FRESHAIRFORCOMBUSTION 6. ELECTRICALWIRING
3. INSTALLATION- SYSTEMPIPING 7. CHECKING& ADJUSTING
4. CHIMNEY& VENTPIPECONNECTION
1. Selectlevellocationas centralizedwith pipingsystem,andas near
chimney,aspossible.
2. Placecratedboilerat selectedlocation,removecrateby pullingcrate
sidesfromtop and bottom boards.Combustiblefloors:Whenboiler
is to be installedon a combustiblefloor,a SpecialBasePlatemust
beused- 146-14-031(3-6Section}or 146-14-032(7-9 Section}.
Thisboilermustnotbeinstalledoncarpeting.
3. If this boileris equippedwithcast iron burners,it is alsoequipped
with stainlesssteel wire ties to hold the backend of the cast iron
burnersin placeduringshipping.In orderto removetheburnersfor
cleaningor inspection,the wireties mustbe cut andremoved.The
wire ties are accessedthroughthe combustionair openingon the
backside of the boiler at the bottom of the rearjacketpanel,and
maybe cut withanywire cutting pliers. I1the boileris installedat
its minimumclearancesit maybe difficultto reachthewiretiesafter
the boileris installed,and lhe wire ties shouldbe cutnow.Thewire
tiesareonlyneededduringshipping,anddo notneedtobereplaced.
Boilersequippedwithstainlesssteelburnersdonothavewire
ties andthis informationdoesnotapply.
4. Boiler is to be level.Metalshimsmaybe usedunderbaselegsfor
finalleveling.
5. Accessibility clearances must take precedence over fire
protectionclearances.18"clearanceshouldbemaintainedata side
wherepassageis requiredto accessto anotherside for cleaningor
servicing,inspection,or replacementof any partsthat normallymay
requiresuchattention.18" clearanceis recommendedon thecontrol
sidefor servicing.
Figure2showsminimumclearancestocombustibleconstruction.Rooms
thatare largein comparisonwith the size of the boiler are defined
as rooms havinga volumeequalto or greaterthan16 times the
volumeof the boiler. Wherethe actualceilingheightof a room is
greaterthan8', the volumeof a roomshaftbe figuredon the basis
of a ceilingheighto18'. Determinationof roomsizeshouldbebased
on thetotal volumeof air gas fired equipmentinstalledin the room.
Consuttsection 6.3.1 of the NationalFuel Gas Code for further
information,includingapprovedmethodsfor reducingclearancesin
largerooms.
6. Equipmentshallbe installedin a locationin whichthe facilitiesfor
ventilationpermitsatisfactorycombustionof gas,properventing,and
maintenanceof ambienttemperatureat safe limits under normal
conditionsof use.Equipmentshall be locatedso as not to interfere
withpropercirculationofair.Whennormalinfiltrationdoesnotprovide
thenecessaryair,outsideairshallbeintroduced(SeePage6 - "Fresh
Airfor Combustion").
7. Adviseownerto keepair passagesfree of obstructions.Ventilating
andcombustionairmustenterboilerroomwithoutrestrictions.
8. Theboilershallbeinstalledsuchthattheautomaticgasignitionsystem
componentsare protectedfrom water(dripping,spraying,rain,etc.)
during applianceoperationand service (condensatetrap, control
replacement,etc.).
Alcove,orRoomNMLarge
InComparisonWithBoiler
Top
Rear
Control Side
Opposite Side
Front
Flue/Vent Connecto_
Near Boiler Piping
BoilerSize
3 sect.
4 sect.
5 sect.
6 sect.
7 sect.
8 sect.
9 sect.
* FORROOMWITHSINGLEBOILERONLY
THIS UNIT MUST BE SET ON A CONCRETE OR OTHER
BoilerVolume
(Cu.Ft.)
63
8!
99
11.7
13.5
153
17.2
NON-COMBUSTIBLE MATERIAL BASE OR FLOOR.
6'
6' 6*
7' 6*
6' 6'
18" 18'
6" 6"
1" 1"
MinimumRoomVolumeRequiredToBe
LargeRoom(Cu.Ft.)*
RoomLargeIn
ComparisonWithBoiler
6'
100.4
129.4
158.4
187.4
216,4
245.4
274,5
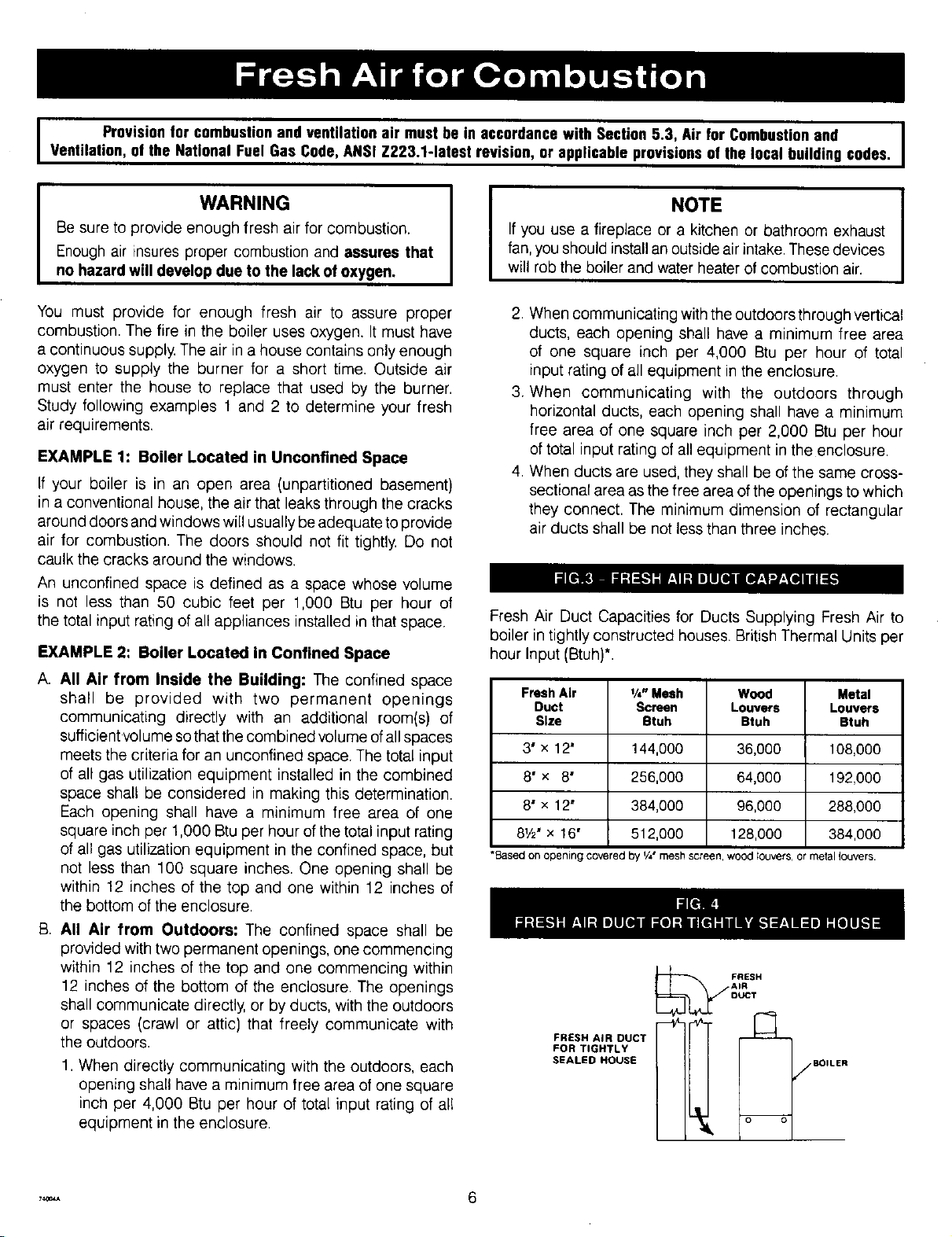
Provision for combustion and ventilation air must be in accordancewith Section 5.3, Air for Combustionand
Ventilation, of the National Fuel Gas Code,ANSI Z223.1-1atest revision, or applicable provisionsof the local buildingcodes.
WARNING
Besure to provideenough fresh air for combustion.
Enoughair insuresproper combustionand assuresthat
nohazardwilldevelopdueto the lackofoxygen.
You must provide for enough fresh air to assure proper
combustion. The fire in the boiler uses oxygen. It must have
a continuous supply. The air in a house contains only enough
oxygen to supply the burner for a short time. Outside air
must enter the house to replace that used by the burner.
Study following examples 1 and 2 to determine your fresh
air requirements,
EXAMPLE 1: Boiler Located in Unconfined Space
If your boiler is in an open area (unpartitioned basement)
in a conventional house, the air that leaks through the cracks
around doors and windows will usually be adequate to provide
air for combustion. The doors should not fit tightly. Do not
caulk the cracks around the windows,
An unconfined space is defined as a space whose volume
is not less than 50 cubic feet per 1,000 Btu per hour of
the total input rating of all appliances installed in that space.
EXAMPLE 2: Boiler Located in Confined Space
A. All Air from Inside the Building: The confined space
shall be provided with two permanent openings
communicating directly with an additional room(s) of
sufficient volume sothat thecombined volume of all spaces
meets the criteria for an unconfined space. The total input
of all gas utilization equipment installed in the combined
space shall be considered in making this determination.
Each opening shall have a minimum free area of one
square inch per 1,000 Btu per hour of thetotal input rating
of all gas utilization equipment in the confined space, but
not less than 100 square inches. One opening shall be
within 12 inches of the top and one within 12 inches of
the bottom of the enclosure,
B, All Air from Outdoors: The confined space shall be
provided with two permanent openings, one commencing
within 12 inches of the top and one commencing within
12 inches of the bottom of the enclosure. The openings
shall communicate directly, or by ducts, with the outdoors
or spaces (crawl or attic) that freely communicate with
the outdoors.
1. When directly communicating with the outdoors, each
opening shall have a minimum free area of one square
inch per 4,000 Btu per hour of total input rating of alt
equipment in the enclosure.
NOTE
If you use a fireplace or a kitchen or bathroom exhaust
fan, you should install an outside air intake.These devices
will rob the boiler and water heater of combustion air.
2. When communicating with the outdoorsthrough vertical
ducts, each opening shall have a minimum free area
of one square inch per 4,000 Btu per hour of total
input rating of all equipment in the enclosure.
3. When communicating with the outdoors through
horizontal ducts, each opening shall have a minimum
free area of one square inch per 2,000 Btu per hour
of total input rating of all equipment inthe enclosure.
4. When ducts are used, they shall be of the same cross-
sectional area as the free area of the openings to which
they connect. The minimum dimension of rectangular
air ducts shall be not less than three inches.
Fresh Air Duct Capacities for Ducts Supplying Fresh Air to
boiler in tightly constructed houses. British Thermal Units per
hour Input (Btuh)*.
Fresh Air 1/,-Mesh Wood Metal
Duct Screen Louvers Louvers
Size Btuh Btuh Btuh
3' x 12' 144,000 36,000 108,000
8" x 8' 256,000 64,000 192,000
8' x 12" 384,000 96,000 288,000
8V2' x 16' 512,000 128,000 384,000
*Basedon opening covered by V4"meshscreen,woodIouvers,ormetallouvers.
AIR
DUCT
FRESH
FRESH AIR DUCT
FOR TIGHTLY
SEALED HOUSE
,_,* 6
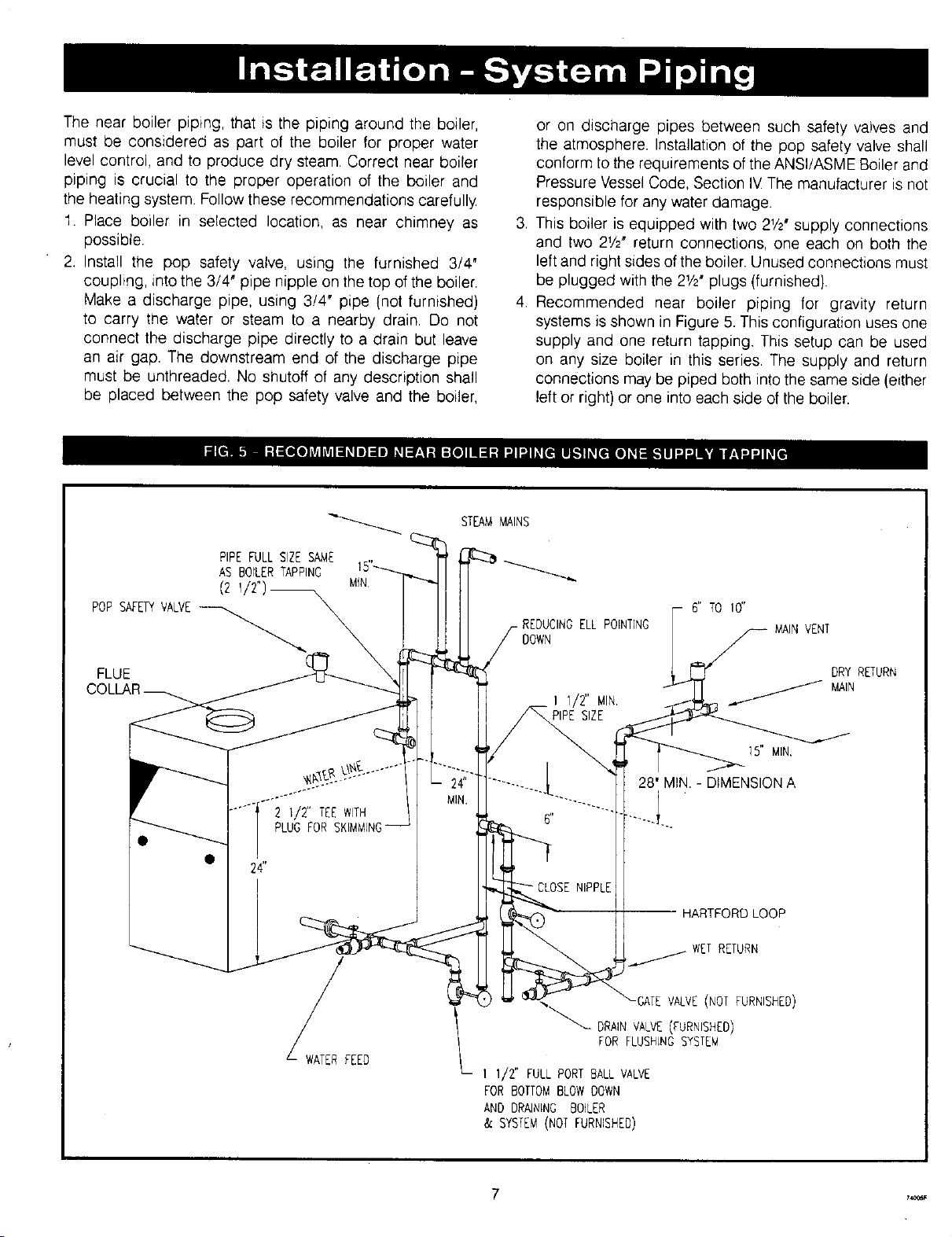
The near boiler piping, that is the piping around the boiler,
must be considered as part of the boiler for proper water
level control, and to produce dry steam. Correct near boiler
piping is crucial to the proper operation of the boiler and
the heating system. Follow these recommendations carefully
1 Place boiler in selected location, as near chimney as
possible.
2. Install the pop safety valve, using the furnished 3/4"
coupling, into the 3/4' pipe nipple on the top of the boiler.
Make a discharge pipe, using 3/4' pipe (not furnished}
to carry the water or steam to a nearby drain. Do not
connect the discharge pipe directly to a drain but leave
an air gap. The downstream end of the discharge pipe
must be unthreaded. No shutoff of any description shall
be placed between the pop safety valve and the boiler,
STEAMMAINS
PiPEFULLSIZESAME
ASBOILERTAPPING
(2
POPSAFETYVALVE
or on discharge pipes between such safety valves and
the atmosphere. Installation of the pop safety valve shall
conform to the requirements of the ANSI/ASME Boiler and
Pressure Vessel Code, Section IMThe manufacturer is not
responsible for any water damage
,
This boiler is equipped with two 2V2' supply connections
and two 2V2" return connections, one each on both the
left and right sides of the boiler. Unused connections must
be plugged with the 2V2" plugs (furnished}
4.
Recommended near boiler piping for gravity return
systems is shown in Figure 5. This configuration uses one
supply and one return tapping. This setup can be used
on any size boiler in this series. The supply and return
connections may be piped both into the same side (either
left or right} or one into each side of the boiler.
6" TO 10"
- REDUCINGELLPOINTING
DOWN
MAINVENT
FLUE
2 1/2" TEEWITH
PLUGFOR
24"
JFEED
DRYRETURN
MAIN
1 1/2" MIN
PIPESIZE
15" MIN.
28' MIN - DIMENSIONA
NIPPLE
)RD LOOP
WETRETURN
-GATE VALVE(NOT FURNISHED)
_" DRAINVALVE(FURNISHED)
FOR FLUSHINGSYSTEM
I 1/2" FULL PORT BALL VALVE
FOR BOTTOMBLOWDOWN
AND DRAINING BOILER
& SYSTEM(NOT FURNISHED)
7,_
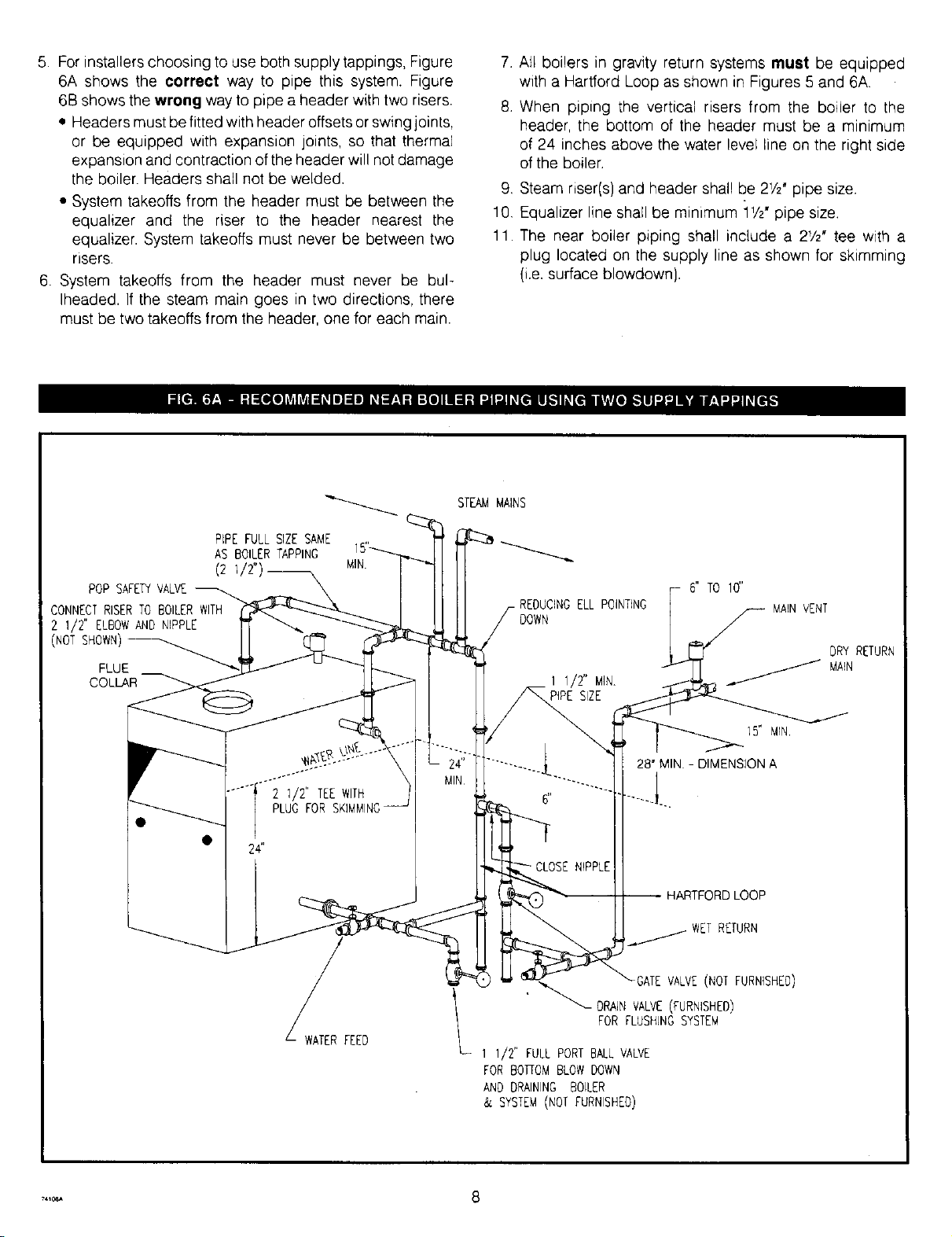
5. For installers choosing to use both supply tappings, Figure
6A shows the correct way to pipe this system. Figure
6B shows the wrong way to pipe a header with two risers.
• Headers must be fitted with header offsets or swing joints,
or be equipped with expansion joints, so that thermal
expansion and contraction of the header will not damage
the boiler. Headers shall not be welded.
• System takeoffs from the header must be between the
equalizer and the riser to the header nearest the
equalizer. System takeoffs must never be between two
risers.
6. System takeoffs from the header must never be bul-
lheaded. If the steam main goes in two directions, there
must be two takeoffs from the header, one for each main.
7. All boilers in gravity return systems must be equipped
with a Hartford Loop as shown in Figures 5 and 6A.
8. When piping the vertical risers from the boiler to the
header, the bottom of the header must be a minimum
of 24 inches above the water level line on the right side
of the boiler.
9. Steam riser(s) and header shall be 2V2"pipe size.
10. Equalizer line shall be minimum iV2" pipe size.
11. The near boiler piping shall include a 21/2, tee with a
plug located on the supply line as shown for skimming
{i.e. surface blowdown).
STEAM MAINS
PIPEFULLSIZESAN_E
AS BOILERTAPPING
(2 1/2"
POP SAFETY VALVE
CONNECTRISERTO BOILERWITH
2 I/2"ELBOWAND NIPPLE
(NOTSHOWN)
FLUE
COLLAR
@ 24"
MIN
2 1/2" TEEWITH
PLUGFOR
W_AfERFEED
6" TO 10"
ELLPOINTING
DOWN
1 1/2" MIN.
PIPESIZE
28" MIN DIMENSIONA
NIPPLE
HARTFORD LOOP
-GATEVALVE(NOTFURNISHED)
_ORAIN VALVE(FURNISHED)
FOR FLUSHINGSYSTEM
MAINVENT
DRY RETURN
MAIN
1S"MIN.
RETURN
I I/2"FULLPORT BALLVALVE
FOR BOTFOMBLOW DOWN
AND DRAININGBOILER
& SYSTEM(NOTFURNISHED)
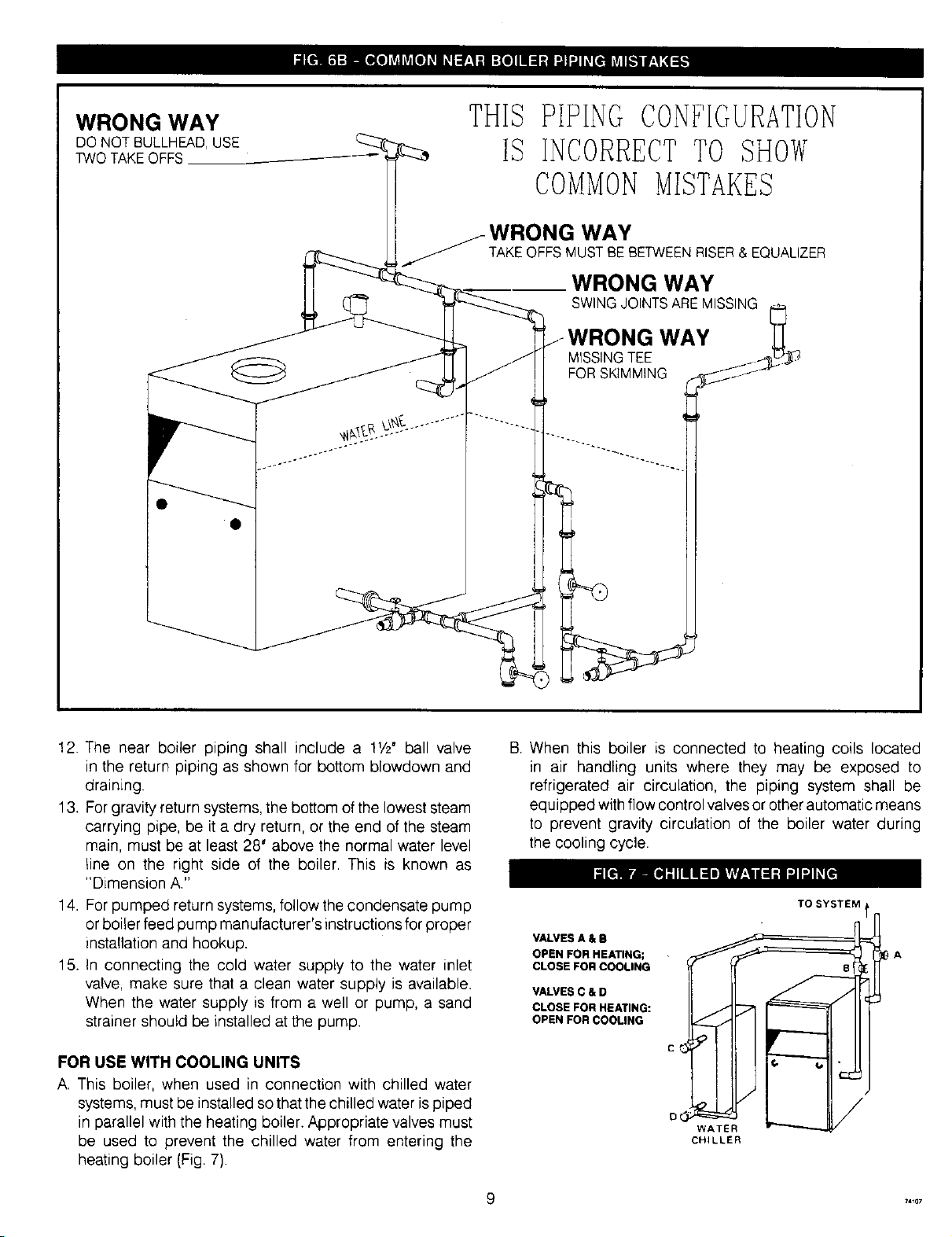
WRONG WAY
DO NOT BULLHEAD,USE
TWO TAKEOFFS
THIS PIPING CONFIGURATION
IS INCORRECTTO SHOW
COMMONMISTANES
WRONG WAY
TAKE OFFS MUST BE BETWEEN RISER & EQUALIZER
WRONG WAY
SWING JOINTS ARE MISSING
)NG WAY
MISSING TEE
FOR SKIMMING
12. The near boiler piping shall include a 1V2" ball valve
in the return piping as shown for bottom blowdown and
draining.
13. For gravity return systems, the bottom of the lowest steam
carrying pipe, be it a dry return, or the end of the steam
main, must be at least 28' above the normal water level
line on the right side of the boiler. This is known as
"Dimension A."
14. For pumped return systems, follow the condensate pump
or boiler feed pump manufacturer's instructions for proper
installation and hookup.
15. In connecting the cold water supply to the water inlet
valve, make sure that a clean water supply is available.
When the water supply is from a well or pump, a sand
strainer should be installed at the pump.
FOR USE WITH COOLING UNITS
A. This boiler, when used in connection with chilled water
systems, must be installed so that the chilled water is piped
in parallel with the heating boiler. Appropriate valves must
be used to prevent the chilled water from entering the
heating boiler (Fig. 7).
B. When this boiler is connected to heating coils located
in air handling units where they may be exposed to
refrigerated air circulation, the piping system shall be
equipped with flow control valves or other automatic means
to prevent gravity circulation of the boiler water during
the cooling cycle.
TO SYSTEM t
VALVES A & B
OPEN FOR HEATING;
CLOSE FOR COOLING
VALVES C & D
CLOSE FOR HEATING:
OPEN FOR COOLING
C
O
CHILLER
_4_o7