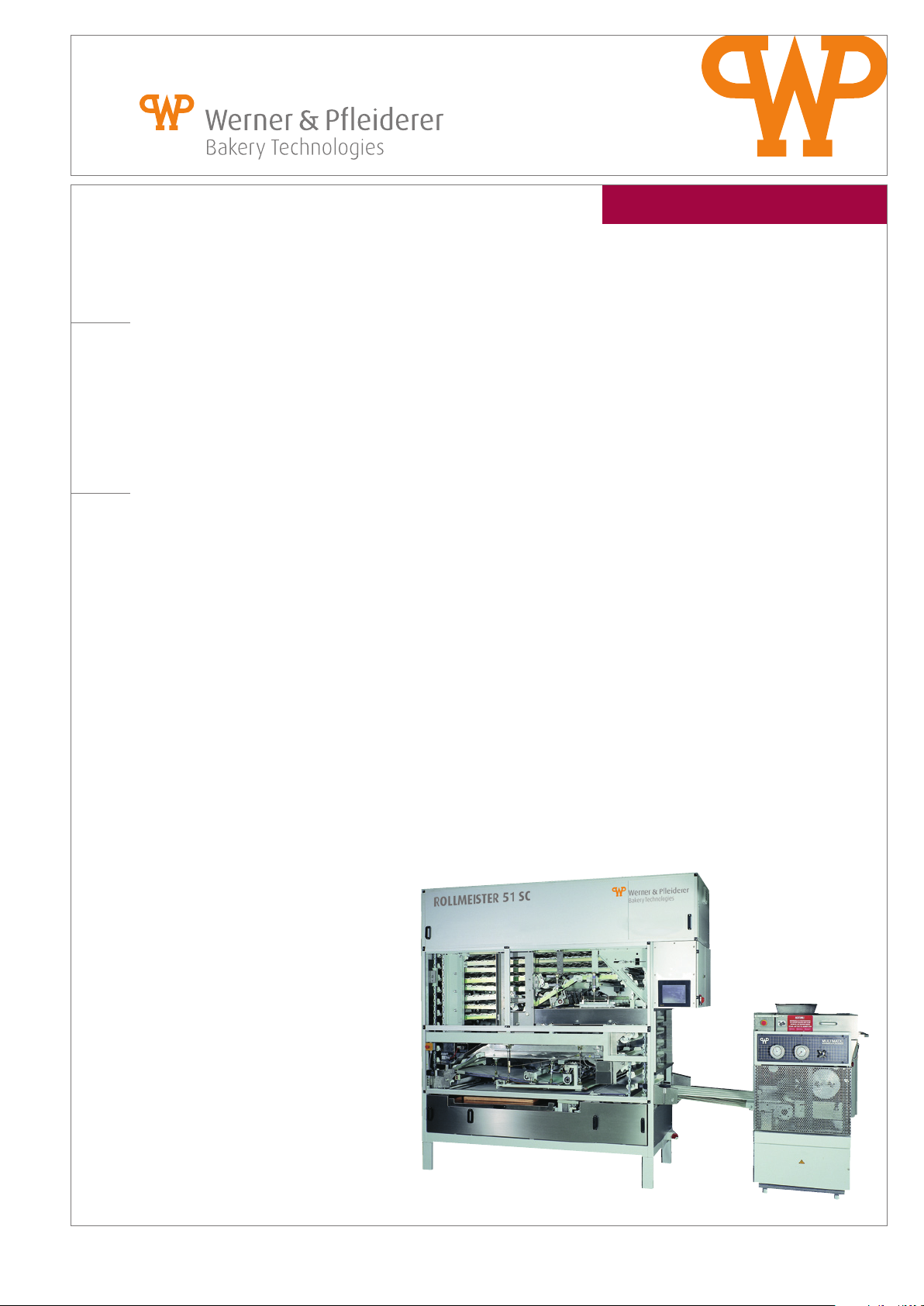
ROLLMEISTER
CUT ROLL SYSTEM
The ideal cut roll system for maximum quality demands
Application
4 or 6-row compact system for the production of cut
products in a weight range of 35 – 85 g*– cut rolls
– Seamless long-rolled products – Hamburger double rolls
– Smooth round rolls
– Long-rolled double pieces
– Double rolls
– Saxony double rolls
– Crusty rolls
*depending on the number of rows and the shape of product
Advantages
Head machine MULTIMATIC
– with its known advantages
Extended pre-proofing
– High volume exploitation
– Low structure influence
– Craftsman quality
Adjustable cutting station
– Optimum baking optics
– Product versatility
Variable depositing unit
– Use of nearly all standard commercial proofing trays (per Euro-dimensions) possible
Interchangeable pressure boards
– Product versatility
– Extended area of use
Bypass belt (non-proofing operation)
– Depositing of all products from the MULTIMATIC® with variable depositing layout on all
types of proofing trays
Intensive degermination station
– Hygienic, CE conformity, LMHV
Variable performance
– Optimum proofing and resting times for all types of dough
Automated production process
– Constant reproducible quality even with changing personnel
Screen control / Touch
– User friendly
– Reproducible quality
Stainless steel design
– Long service life
– Hygienic
– High re-sale value
®
WP BAKERYGROUP
ROLLMEISTER 1/2
CUT ROLL SYSTEM 14.10.2008
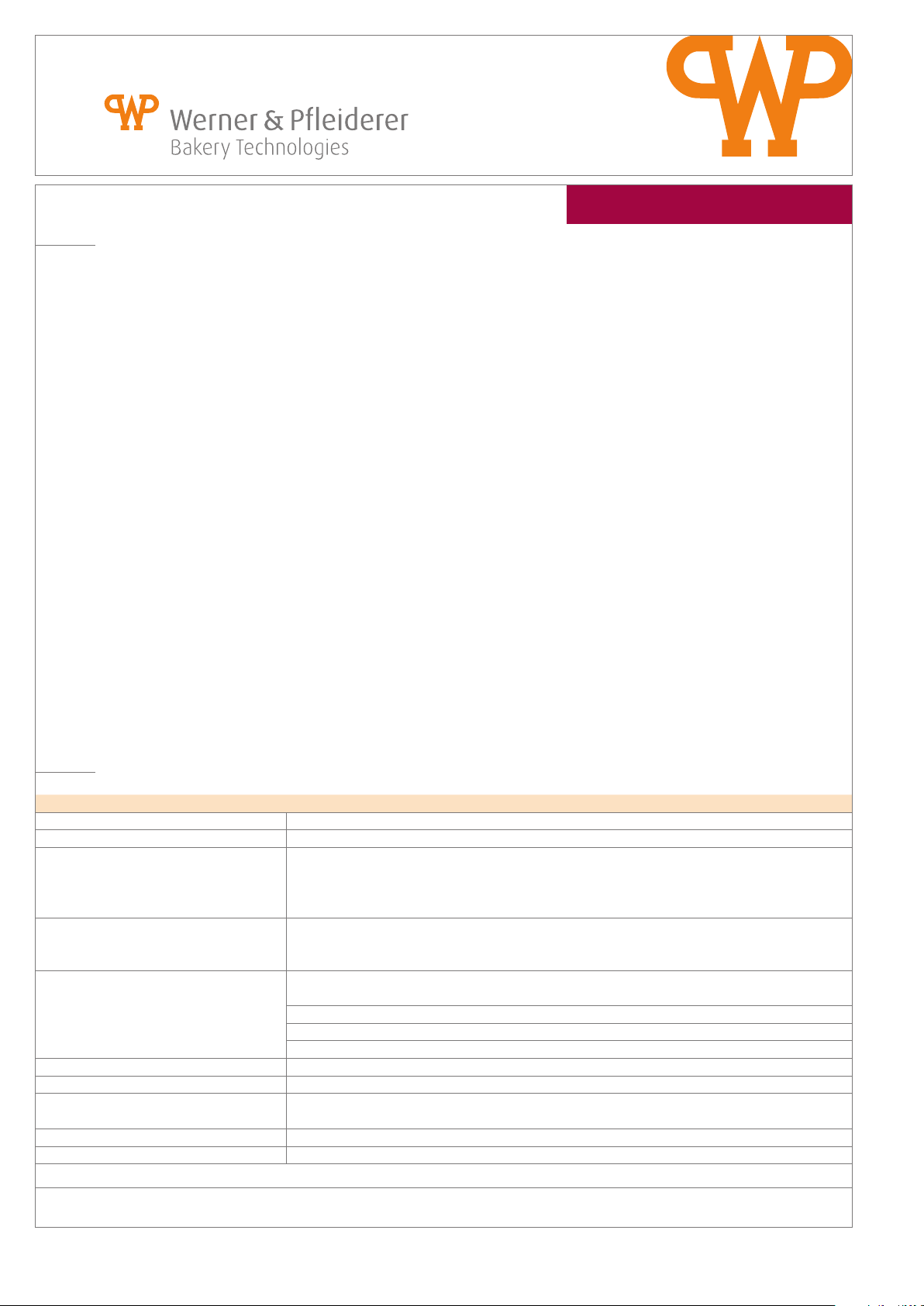
WP BAKERYGROUP
ROLLMEISTER
Equipment
In standard design: Head machine MULTIMATIC
MULTIMATIC® S – 4-row or MULTIMATIC® C 4-row
ROLLMEISTER
– Stainless steel construction in compact design with basin trays
– Proofing time between input and long roller of 6 min. and a
further proofing time between long roller and cutting machine
of also 6 min.
– Air conditioning ROLLMEISTER BASIC LINE SC 37 – Option)
– Pneumatic cutting machine for cutting dough pieces lengthways
– Manual cutting depth adjustment of 3 – 10 mm via the belt
of the cutting machine
– Pressure board for the production of cut rolls
– Driven, height-adjustable pressure roller ahead
of the cutting station
– Rack drying (with ROLLMEISTER BASIC LINE SC 37 – option)
– Depositing unit for proofing trays of the 3 Euro sizes
400 x 600 mm, 580 x 780 mm, 580 x 980 mm,
racking length, 1,000 mm
– Seam position adjuster
– Bypass belt can be driven in-out pneumatically
– Degermination station
– Exhaust air fan for adjustment of the proofing cabinet climate with
continuous operation (only with ROLLMEISTER BASIC LINE SC 37)
– Screen control via touchscreen
– Proofing tray locator as push-in shelf
– Operating side left in running direction
– Frequency controlled long-roller lower belt
(only with ROLLMEISTER MEGA LINE SC 72)
– Maintenance-free trays
– Automatic chain tensioning
– Ready equipped for the connection of a sheet loading robot
®
ROLLMEISTER 2/2
CUT ROLL SYSTEM 14.10.2008
Options
– Side discharge belt
– Driven pressure roller ahead of long roller
– Folding flaps with various divisions
– Offsetting device
– Pneumatically adjustable hold-down rails
– Seam position adjuster at depositing unit
frequency controlled
– Ram shield on operator side
– System height raise by 50 or 100 mm
– Data network for complete control of the MULTIMATIC® S
via the system software
– Pneumatic piston lock from 6 to 5, 6 to 4 or 6 to 3 rows
– Low upper section (minimum room height 2,675 mm)
– Shelf for 2 pressure boards
– Double intensity degermination
– Air conditioning (only with ROLLMEISTER BASIC LINE SC 37)
– Exhaust air fan for adjustment of the proofing cabinet climate with
continuous operation (only with ROLLMEISTER BASIC LINE SC 37)
– Seam position adjuster ahead of cutting station
(only with ROLLMEISTER BASIC LINE SC 37)
– Preparation for air conditioning
(only with ROLLMEISTER BASIC LINE SC 37)
Accessories
– Chamber drum for extended weight range
– Spreading belt 500 mm
– Spreading belt 1,250 mm
– Various pressure boards for the production of:
· Cut rolls
· Stick products and baguette rolls
· Cylindrical products, hot dogs etc.
· Crusty rolls
Technical Data
ROLLMEISTER BASIC LINE SC 37 ROLLMEISTER STANDARD LINE SC 51 ROLLMEISTER MEGA LINE SC 72
Hourly output pcs./h 3,650 ca. 5,100 ca. 7,200
Pre-proofing time min. 12 12 12
Weight range
4-row (cut rolls) g
3-row (baguette rolls) g
via by-pass g
Proofing tray dimensions mm 400 x 600
Electrical data*
Without air condition kW 3 3 3
With air condition kW 7 7 9
With air condition and drying kW 5 5 7
With air condition, heating and drying kW 11 11 13
Cold water connection “ 1/4 1/4 1/4
Water drain in NW 40 40 40
Compressed air – 1/2” plug
connection
Dimensions L x B x H mm 2,400 x 1,000 x 2,470 2,400 x 1,000 x 2,850 2,400 x 1,000 x 3,350
Required minimum room height mm 2,500 2,900 3,400
*plus electrical connection for MULTIMATIC
Werner & Pfleiderer Lebensmitteltechnik GmbH . von-Raumer-Straße 8-18 . 91550 Dinkelsbühl . Germany
Fon +49 (0) 98 51-905-0 . Fax +49 (0) 98 51-905-342 . info@wp-l.de . www.wp-l.de
®
40 – 65
40 – 85
38 – 85
580 x 780
580 x 980
5 Normal m³/h or
84 Nl/min to 6 – 8 bar
40 – 65
40 – 85
35 – 85
400 x 600
580 x 780
580 x 980
5 Normal m³/h or
84 Nl/min to 6 – 8 bar
40 – 65
40 – 85
35 – 85
400 x 600
580 x 780
580 x 980
5 Normal m³/h or
84 Nl/min to 6 – 8 bar
All details non-binding. Subject to change in the course of technical progress. All rights reserved. ® = registered trademark