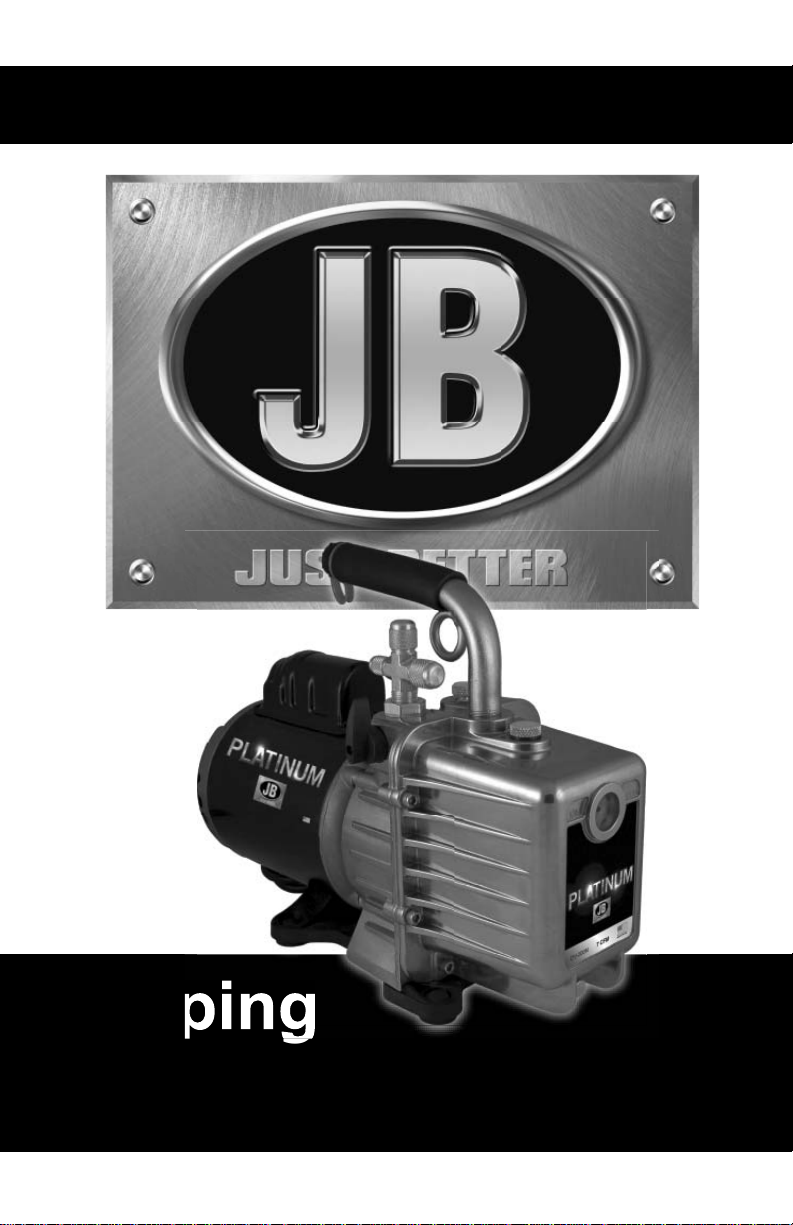
Tech tips from the pros
Keeping
the Life in Your Pump
Copyright© 2009, JB Industries Inc.
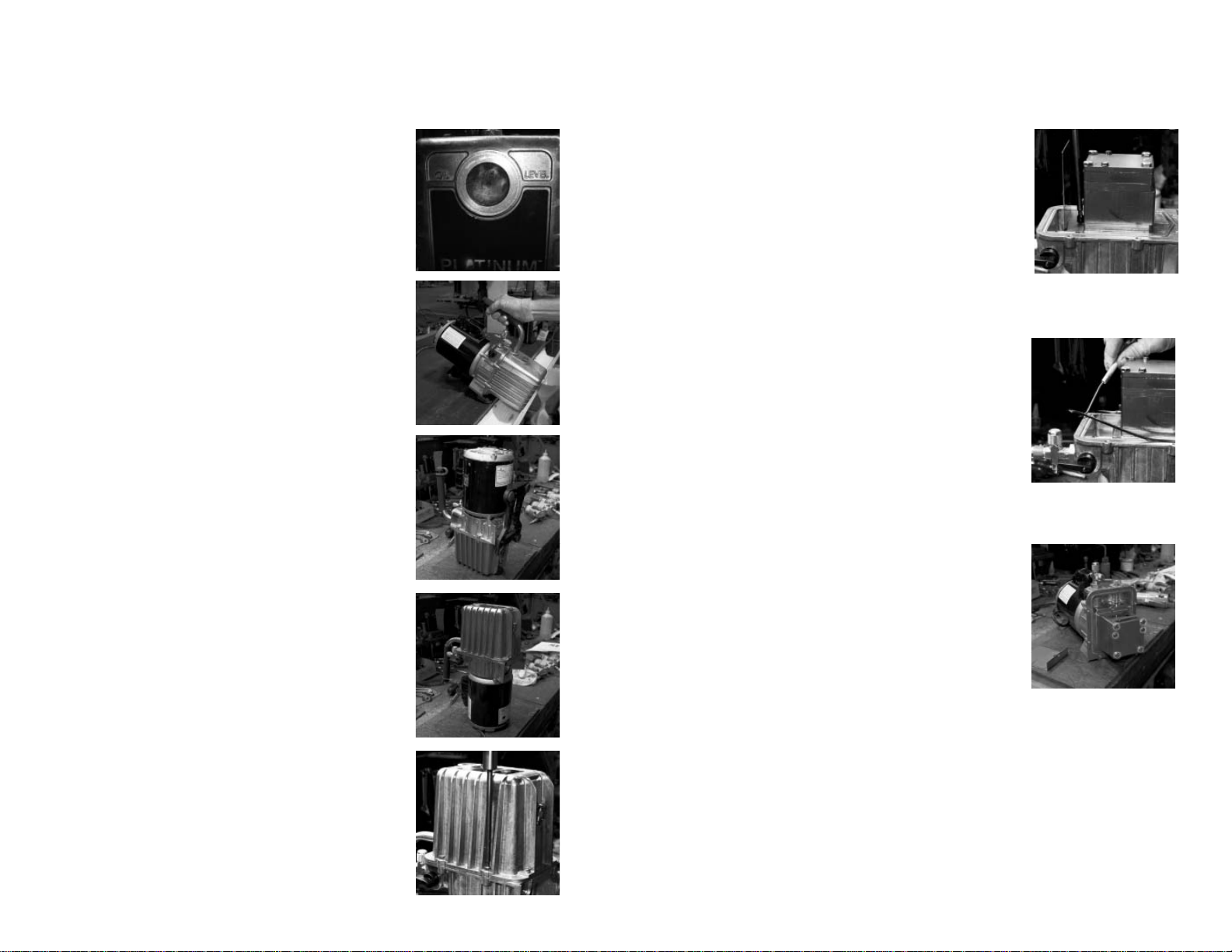
2 3
IMPORTANT
JB PUMPS ARE NOT TO BE USED ON AMMONIA OR LITHIUM BROMIDE
(salt water) SYSTEMS. Pump maintenance is the responsibility of the owner.
Remember to change the oil. JB recommends
changing oil after every evacuation and for larger
jobs, you may need to change the oil a few times.
Hydrofl ouric and hydrochloric acids and moisture
collect in the oil. Left sitting in a pump, they act
as an abrasive on internal surfaces, rusting and
corroding them.
Figure 1
Cleaning and Testing Your Vacuum Pump
One of the easiest ways to spot if your pump is
in need of a good cleaning is to look at the sight
glass. If the oil looks milky, rusty, or full of
debris, then the inside of the pump is in worse
shape (Figure 1).
To clean, start the vacuum pump and allow
it to run for about 15 minutes to warm up the
oil. Make sure that you have allowed enough
working room to safely drain and capture the oil.
After the oil has stopped dripping, tilt the pump
forward to remove any remaining excess oil (Figure 2). Then, stand the pump on the nose of the
cover (Figure 3) to allow any trapped oil in the
wells and stators to drain. Let sit for a few minutes and return the pump to its normal running
position. Repeat tilting forward. Close drain
valve. Dispose of contaminated oil properly.
Once the oil has been completely removed,
return the pump to the position in fi gure 3 and
remove either the 2 rubber feet from the bottom
of the pump or remove pump base (depends on
the age of the pump which option is available).
Next, turn the pump on to the motor end (Figure
4) and remove the 6 socket head cover screws
holding the cover in place (Figure 5). Remove
the cover from the pump and wipe the inside
surface with a dry, clean rag. The sight glass
is more diffi cult to clean. Try pouring in some
solvent and using a pipe cleaner.
Figure 2Figure 3Figure 4Figure 5
Next, remove the oil defl ector which is held in
place with a socket head screw (Figure 6). Wipe
with a clean, dry rag. If needed, a wire brush can
be used to clean any discoloration to metal parts
(this will not affect the pump’s performance once
the cleaning is complete). Remove the cover seal
and clean cover seal (Figure 7). Wipe the outside
of the cartridge’s surfaces with a clean, dry rag. A
wire brush can be used on all surfaces including
the exhaust valve and the intake relief valve. If
they are discolored, they will still perform fi ne.
DO NOT DISTURB THE FOUR CARTRIDGE
BOLTS OR THE TWO SMALLER HEX
HEAD SCREWS (FIGURE 8). These are the
setting screws.
If the intake relief valve set or the exhaust valve
set is damaged and needs replacing, these items
can be ordered through your local wholesaler
under JB Part Number PR-18. It is best to replace
after completing the cleaning of the cartridge. Pay
attention to the order in which they are assembled
for correct reinstallation.
Reassemble the oil defl ector (Figure 6). Clean out
the channel for the cover seal with a clean, dry rag
and smear some grease into the channel. This will
help hold the cover seal in place for reinstallation
of the cover. If the cover seal seems a little tight,
stretch the seal a little and try again. All seals
in JB pumps are designed to be reused. Reset
the cover in place and replace the cover screws.
Tighten in a crisscross pattern. Reattach feet or
base.
Next, return the pump to its normal running position and place where you drained the oil. Open
the drain valve, the 3/8” port on the intake, and the
isolation valve. Have 1/3 cup of clean oil ready.
Start the pump and pour the clean oil into the
intake port. Let the pump run for 5 to 6 seconds
and then shut the pump off. Drain the oil, tipping
the pump forward as in Figure 2 to completely
drain. Close the drain valve and dispose of spent
oil properly after the fl ushing is complete.
Figure 6
Figure 7
Figure 8
DO NOT
DISTURB THESE
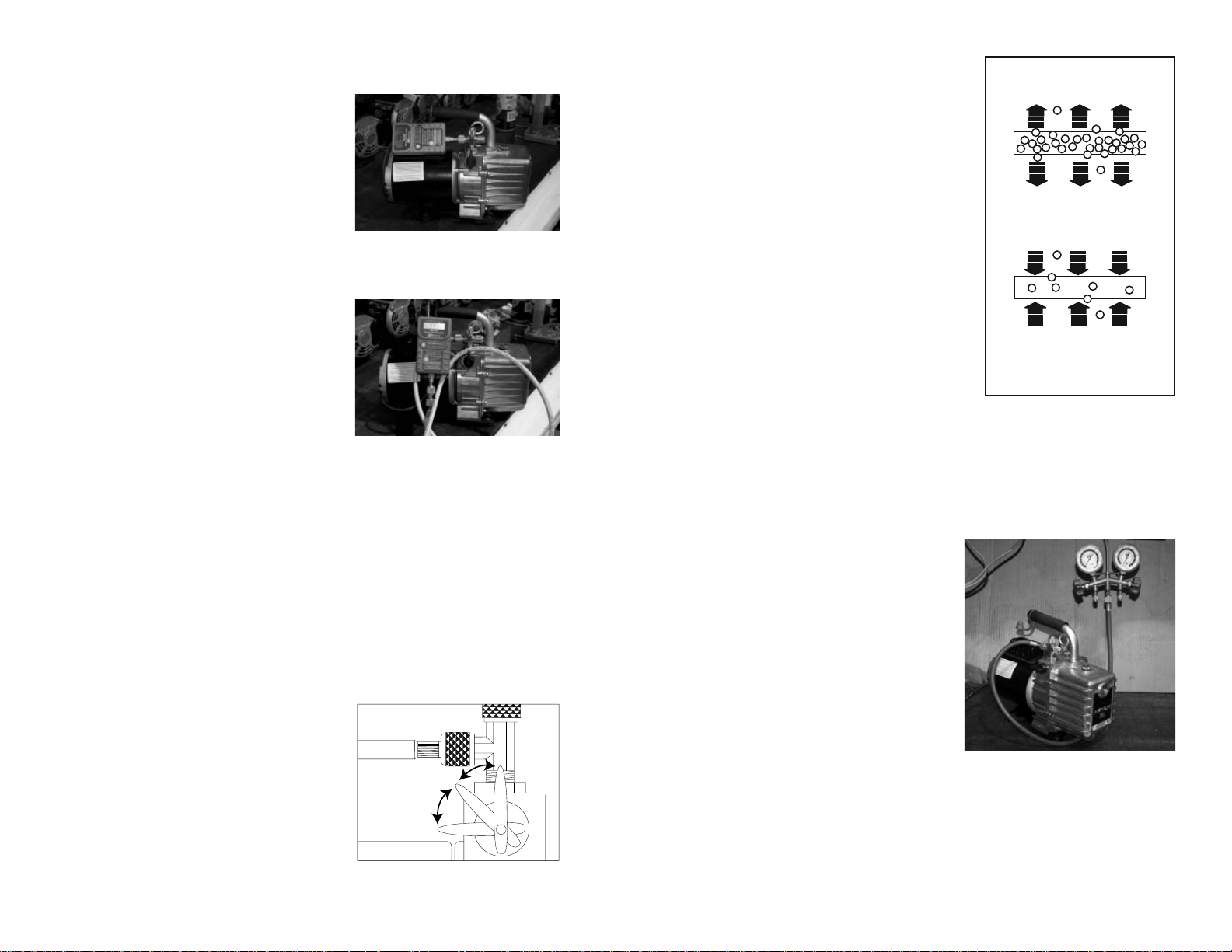
4 5
Cleaning and Testing Your Vacuum Pump Continued
Using Charging and Testing
Hoses for Evacuation
DIRECTION OF PERMEATION
THROUGH HOSE WALL
Now, fi ll the pump to the proper oil
level and allow the pump to run with
the isolation valve closed for 3 or 4
minutes to warm up the oil. Check all
o-ring caps for dirt and proper seal.
Connect a micron gauge (JB recommends the JB DV-22N pictured to the
right) directly to either the 1/4” port or
Figure 9
the 3/8” port on the intake tee (Figure
9). Do not use a charging line. Open
the isolation valve.
Using a charging line, especially a
new line, will give you a higher micron reading because you are reading
the environment inside the hose (see
Figure 10).
Figures 9 and 10 are the same, but
Figure 10
fi gure 9 is a direct connection hook-up
and fi gure 10 is a connection through a new charging line. Both hook-ups are
allowed to run the same length of time, but #9 is at 20 microns while #10 is at
297. If left on, the charging line hook-up will come down in its micron reading,
but it will take a much greater period of time. If the hose is cleaned out with alcohol and vacuumed for a long period of time, the micron reading will go lower.
This test can be performed on a pump with dirty, used oil and then with the
pump cleaned and fl ushed, as described earlier, to see the difference that just
maintaining the cleanliness inside your pump affects the performance for deep
vacuum.
Isolation Valve
It is a quarter turn between on and off.
There is no additional valve needed
to isolate the system. When checking for pressure rise, slowly turn the
handle counter-clockwise. The pause
position is at 45 degrees and the valve
is completely closed at 90 degrees
(Figure 11).
PAUSE
POSITION
CLOSED
POSITION
Figure 11
OPEN
POSITION
You probably think there is a leak. However, an evacuation/ dehydration hook-up
requires a leak-proof design in all of the
components. Only soft copper tubing,
pure rubber hoses, or fl exible metal hoses
are absolutely vacuum tight. Charging
hoses are designed for positive pressure.
CHARGING SYSTEM
Gas under pressure in the hose
will permeate to the lower
pressure of the atmosphere.
Even with the advanced technology of today’s hoses, permeation through the hose
compound still exists (Figure 12).
If you have blanked-off your pump
to check pressure rise and your hoses
and connections are not leak-free, the
atmosphere will permeate to the lower
pressure in the hoses. Your reading will
slowly rise and you will spend time look-
EVACUATION (Hose under Vacuum)
The atmosphere which has a higher
pressure permeates to the lower
pressure in the hose.
Figure 12
ing for system leaks.
Information on Testing the Vacuum Pump’s Isolation Valve
The easiest way to test the isolation valve
for leakage is to turn the pump on with
the isolation valve in the closed position.
Connect a charging line to the center port
of the manifold (Figure 13), and have the
high side capped off and CLOSED and
the low side capped off and OPENED.
Then, connect the charging line to the
intake of the pump and wait. If, within
5 to 10 minutes, you do not see the low
(compound) gauge going into inches of
vacuum, there is no leak in the isolation
valve.
What does happen when a micron gauge
is connected directly to the intake of a vacuum pump with an isolation valve/ It
is all related to the connections to, and including, the intake, the volume of what
is being vacuumed, the depth of vacuum, and the length of time that the volume
is in the deep vacuum.
Figure 13