
mightyZAP
User Manual
Robust Mini Linear Servo Motor ------
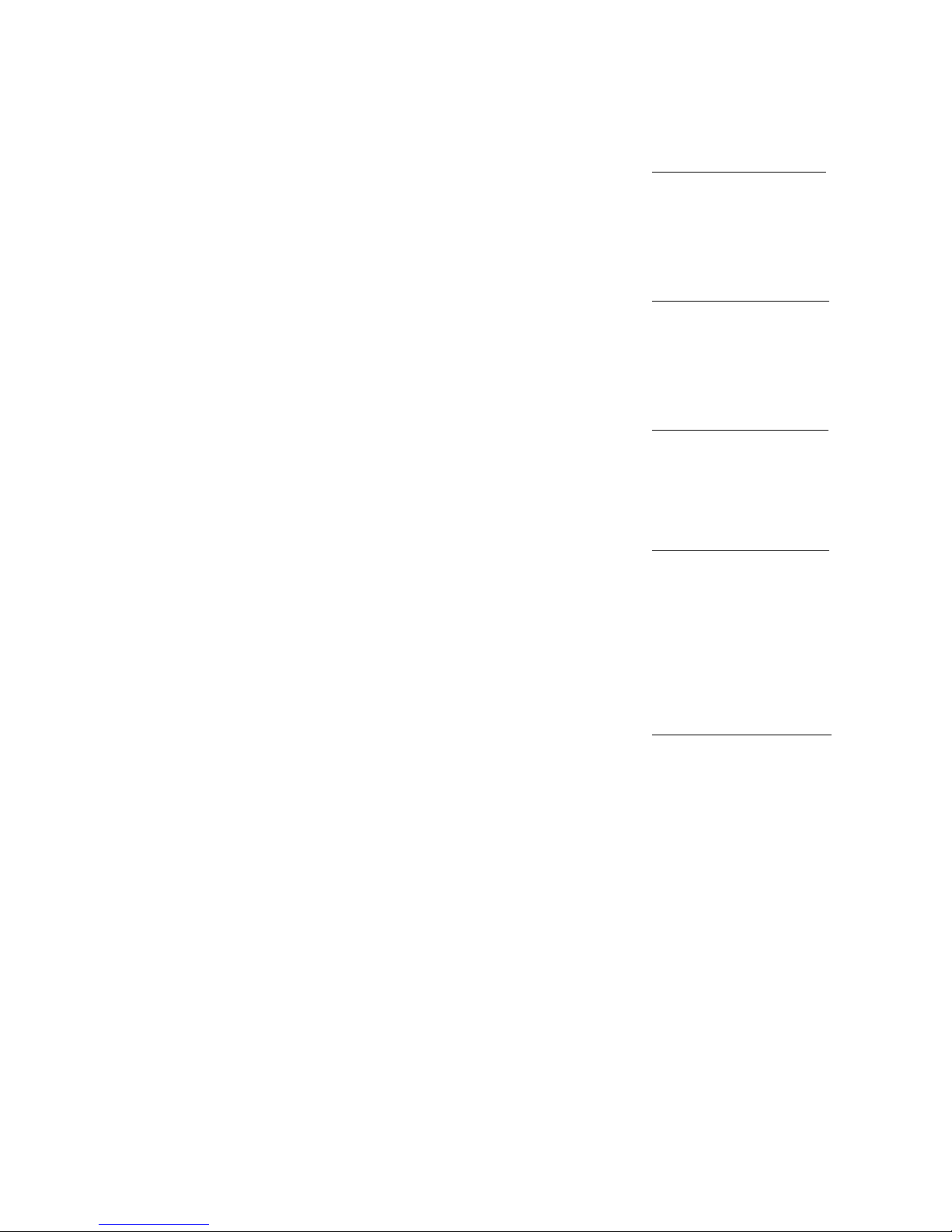
mightyZAP USER MANUAL V.1.02
2
INDEX
01 Before USE 3
Introduction
For Safety
For Storage
02 Basic Info 4
Component
Dimension
Specification
03 Application 6
Manipulator
Stewart Platform
Installation
04 Servo Control 8
Circuit Connection
Communication
Specification
Packet Description
Data Map
Command Example
05 Warranty Service 26

mightyZAP USER MANUAL V.1.02
3
1.1. Introduction
Thank you for purchasing mightyZAP mini Linear servo motors! Please peruse this manual before use to prevent
any unexpected damage of product or serious injury of users.
mightyZAP mini Linear servo motors have been developed to provide reliable, high quality linear solution in
compact space. mightyZAP mini Linear servo motors can be applied in various fields such as factory automation,
medical devices, robotics, professional UAV and radio control hobby.
[Features]
Position Control (Positional Accuracy 100um)
Embedded Drive circuit
4096 Step High Resolution
High Performance Coreless Motor
Minimized Mechanical Backlash (50um)
Excellent Substitute for pneumatic cylinder which does not support position control
Reasonable Cost
1.2. For Safety
Do not disassemble servo motor at user's discretion. Maintenance should be done by authorized
engineer.
Use designated input power to prevent damage of product.
Use within the force at rated power(Peak Efficiency Point) for better lifespan & proper performance.
Be careful to touch the servo case right after operation. It may be hot.
Be sure to keep servo motor away from water, dust, sand, oil.
This product is designed for indoor use. Do not use it outdoor condition.
Do not push / pull the servo rod by excessive force.
Keep out of reach of Children.
1.3. For Storage
Do NOT store/use servo motor under below extreme condition. It may cause malfunction or damage of product.
Direct light and High temperature more than 60 ˚C or Low temperature lower than minus 20˚C.
Highly Humid space
Space having Vibrating condition
Space having Dust
Space causing Electrostatic
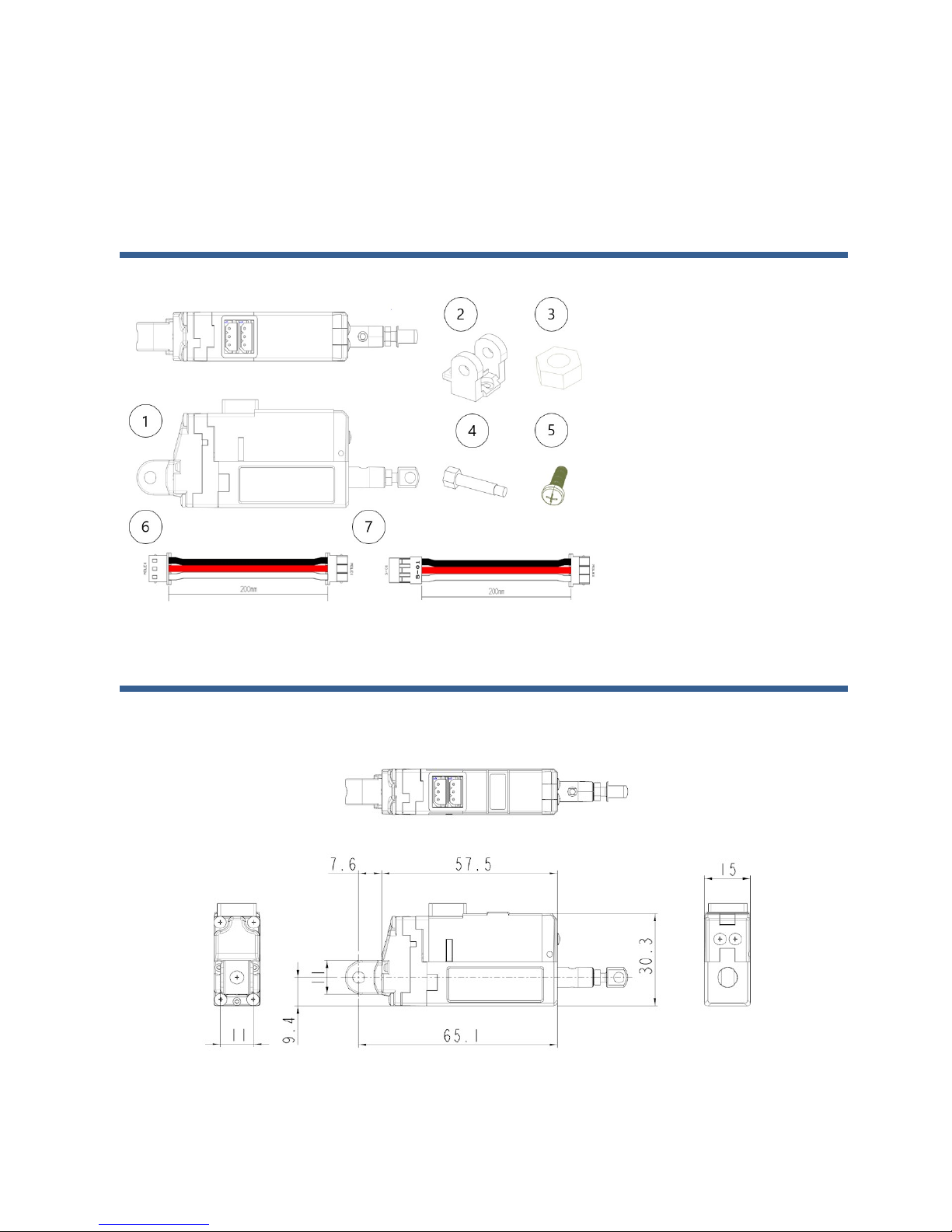
mightyZAP USER MANUAL V.1.02
4
2.1. Component
2.2. Dimension
Basic Information
① mightyZAP Linear servo motor
② Hinge Base 1pc
③ M3 NUT
④ Hinge Shaft
⑤ M2.5x6
⑥ 200mm Molex to Molex Wire
⑦ 200mm S-01 to Molex Wire
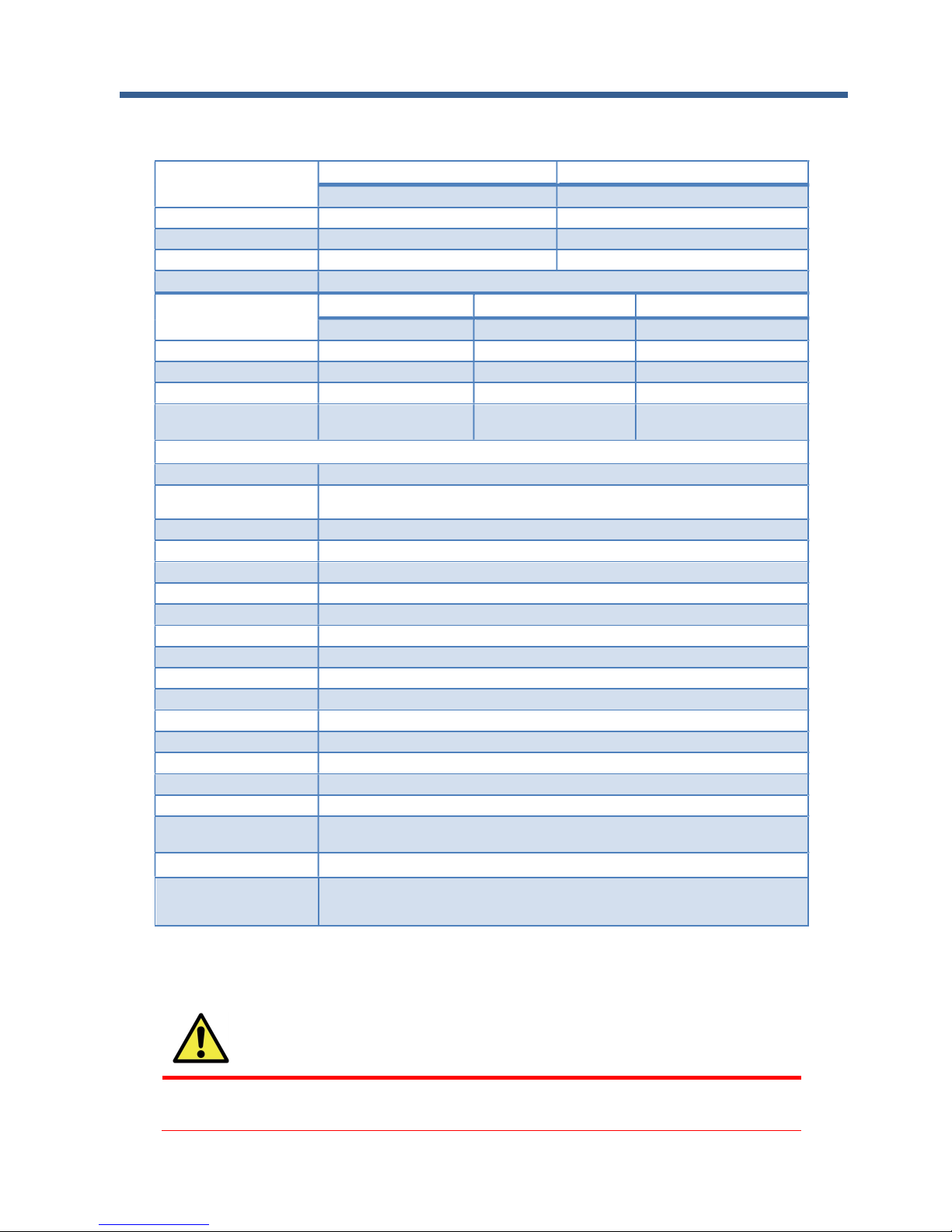
mightyZAP USER MANUAL V.1.02
5
2.3. Specification
Stock Item
L(7)12-20PT-3 L(7)12-40PT-3
High Speed High Force
Peak Power Point 40N@55mm/s 80N@16mm/s
Peak Efficiency Point
20N@90mm/s 40N@28mm/s
Max. Speed(no load) 110mm/s 37mm/s
Gear Type Super Engineering Plastic
Order Made Item
L(7)12-13PT-3 L(7)12-64PT-3 L(7)12-100PT-3
Ultra Speed High Force Ultra Force
Peak Power Point 26N@70mm/s 128N@6mm/s 200N@3.7mm/s
Peak Efficiency Point
13N@112mm/s 64N@10mm/s 100N@6mm/s
Max. Speed(no load) 149mm/s 12.4mm/s 7.46mm/s
Gear Type Super Engineering Plastic
2 Metal & 4 Super
Engineering Plastic
4 Metal & 2 Super
Engineering Plastic
Common Specification
Motor Type High Performance Coreless motor
Gear Type Super Engineering Plastic
Stroke 30mm
Positional Accuracy Under 0.1mm (100μ
Electric al Stroke 30mm
Feedback Potentiometer
10KΩ /mm +/- 1% linearity
Input Voltage Optional - 7.4V or 12.1V (Rated)
Stall Current 3.4A at 7.4V / 2.3A at 12.1V (Premium line)
Operating Temperature -10℃ ~ 50℃
Mechanical Backlash 0.05mm (50μ
Control System TTL Half Duplex (Daisy Chain) and PWM with Position Feedback
Microcontroller 32bit ARM Core, 4096 Resolution (AC/DC converter)
Pulse Range 900 ㎲(Retracted)~1500 ㎲(Center)~2100 ㎲(Extended)
Parameter Setting Programmable
Ingress Protection IP-54 (Dust & Water Tight)
Dimension / Weight 57.5(L)x29.9(W)x15(H)mm / 45g
LED Indication 7 Errors Indication
(Overload, Checksum, Range, Overheat, Stroke Limit, Input voltage, Instruction Error)
Standard Accessory 1 Mounting Bracket, 2 types Rod end (Detachable linkage and Metal nut(M2.5) type)
Wire/Connector Molex to S-01(Hitec and Futaba compatible) and
Molex to Molex Type(Molex 50-37-5033) / 200mm length, 0.08x60(22AWG)
Caution
Use within Rated Force
For proper performance and better lifespan of mightZAP, it is stronlgy requested to
use it within the rated force range(Rated Force = Peak Efficiency Point).
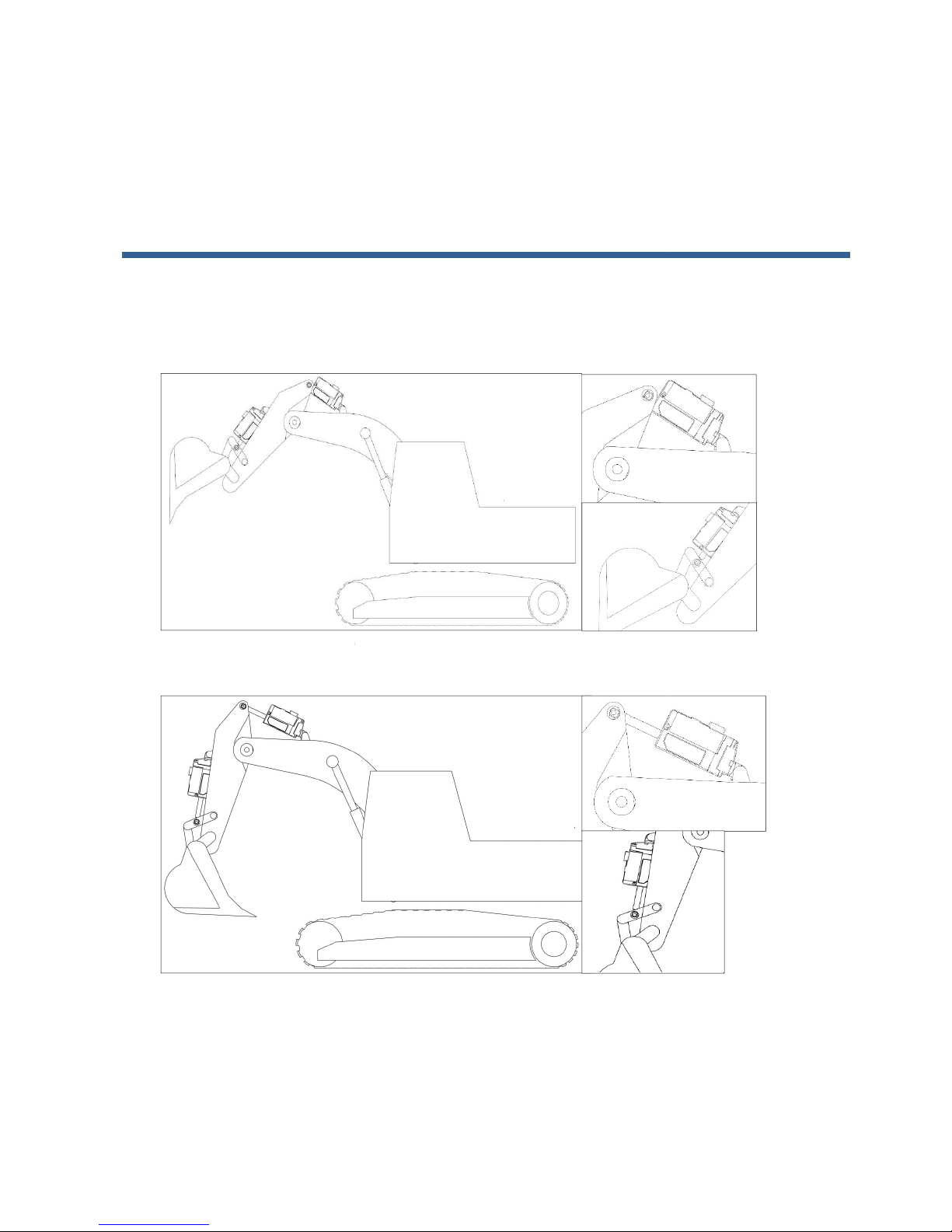
mightyZAP USER MANUAL V.1.0
Blow picture shows excavator arm using mightyZAP.
4 joint link structure and 2 joint
picture to make a rotating movement.
In case servo position at 0
In case servo position at
are simplified. Based on basic link structure, you can refer to below
- fully retracted position]
30mm - fully extended position]
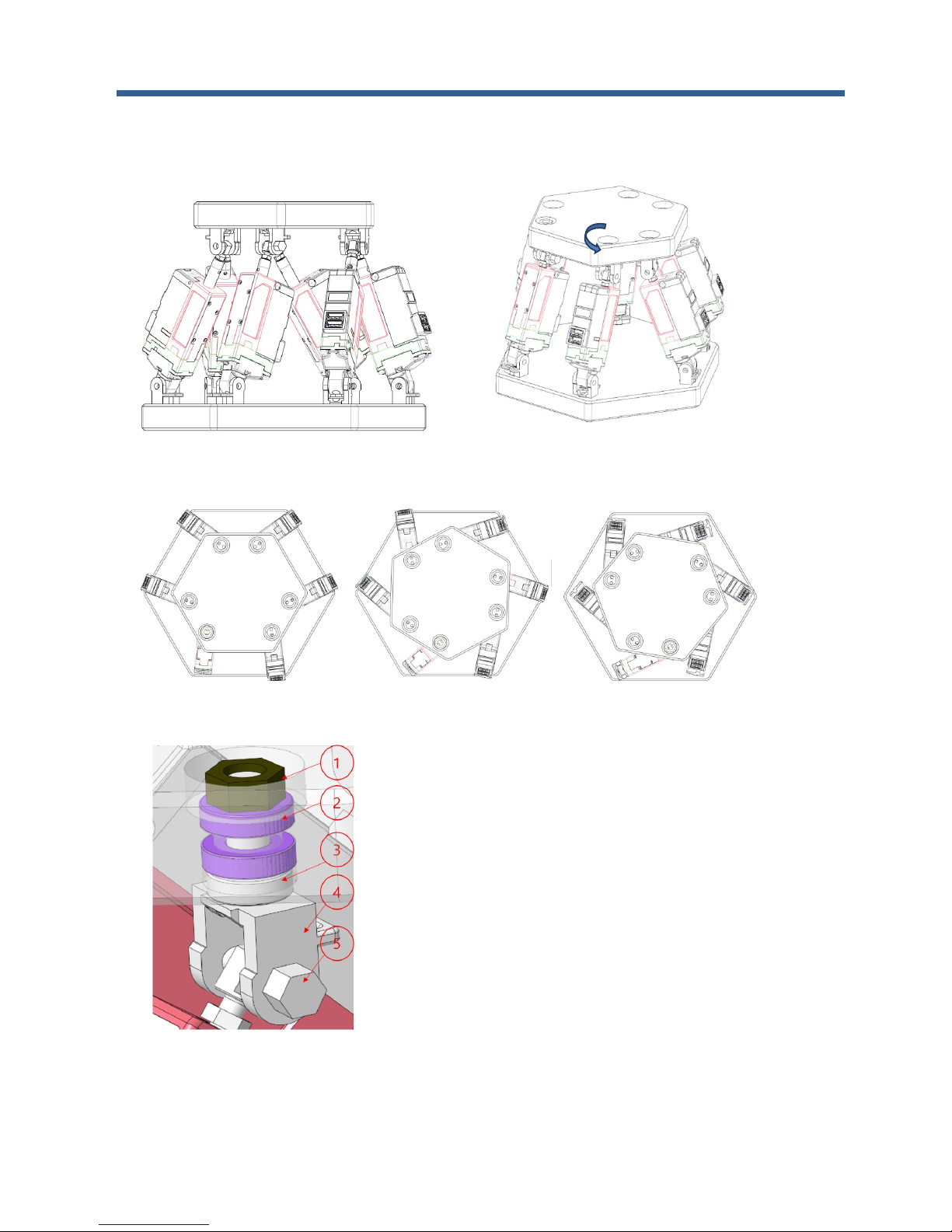
mightyZAP USER MANUAL V.1.02
7
3.2. Stewart Platform
Stewart Platform having 6 rotating axis on both upper and lower panel. You can make X, Y, Z movements and
plus, Z axis rotating movement.
Above shows how to make rotating movement of upper panel.
①Nut
②Bearing
③Rotating Shaft
④Linkage Base
⑤Linkage Shaft
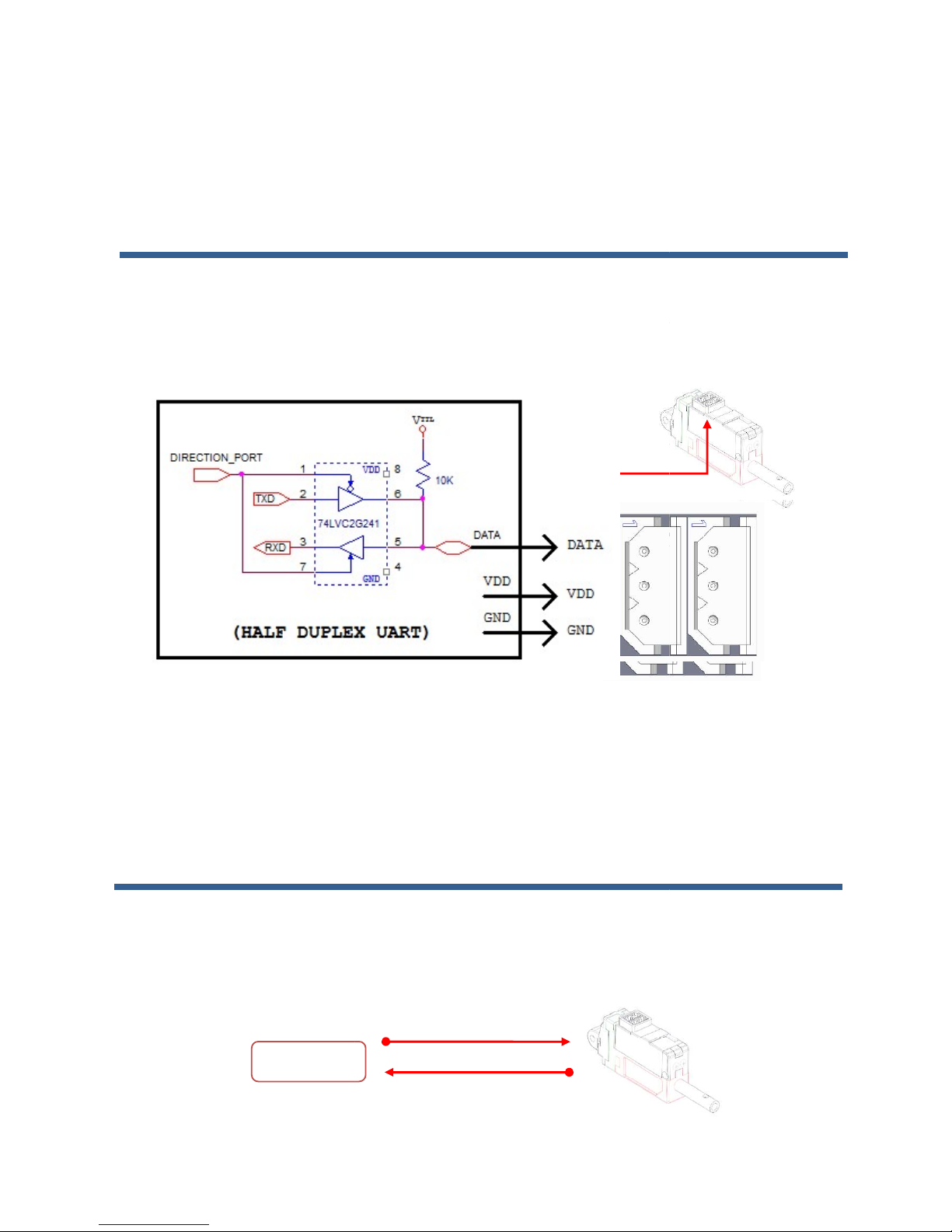
mightyZAP USER MANUAL V.1.0
mightyZAP supports both data communication(Half Duplux
under data communication, UART signal of main board should be converted into Half Duplex Type signal.
Conversion circuit will be as below.
The direction of data signal for TxD and RxD
direction_port as below.
The level of "direction_port" is LOW : TxD signal will be outputted as Data.
The level of "direction_port" is HIGH :
mightyZAP and your main controller will communicate by exchanging data packet. The sorts of
Command packet (Main controller to mightyZAP) and Feedback packet(mightZAP to your main controller)
TTL) as well as simple pulse(PWM) control. For the control
of TTL level will be determined according to the level of
: Data signal will be inputted to RxD.