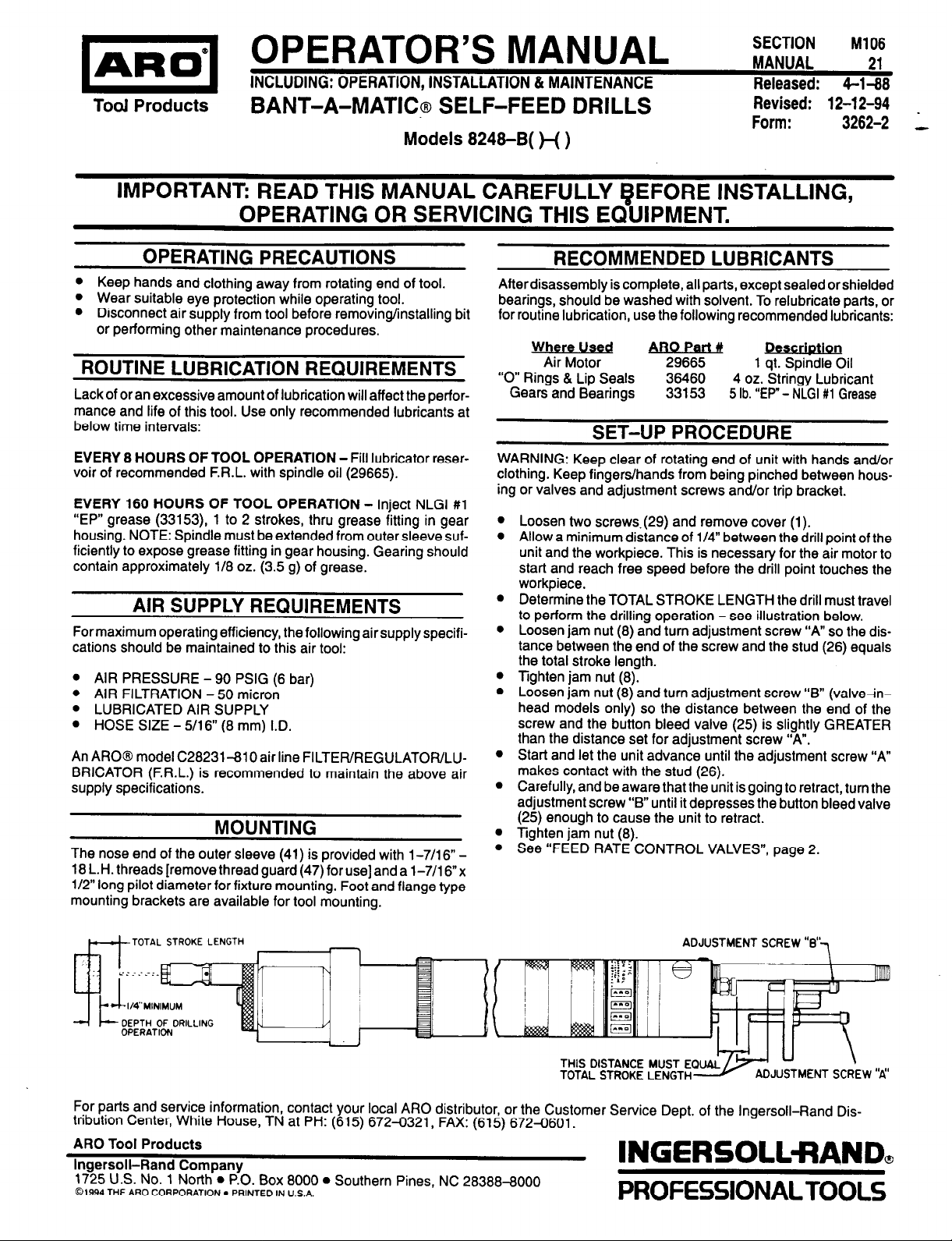
SECTION
Tool
Products
OPERATOR’S MANUAL
INCLUDING: OPERATION, INSTALLATION & MAINTENANCE
BANT-A-MATIC® SELF-FEED DRILLS
MANUAL
Released: 4-1-68
Revised: 12-12-94
Form: 3262-2
Models 8248-B( )-( )
IMPORTANT: READ THIS MANUAL CAREFULLY BEFORE INSTALLING,
OPERATING OR SERVICING THIS EQUIPMENT.
M106
21
OPERATING PRECAUTIONS
l
Keep hands and clothing away from rotating end of tool.
l
Wear suitable eye protection while operating tool.
l
Disconnect air supply from tool before removing/installing bit
or performing other maintenance procedures.
ROUTINE LUBRICATION REQUIREMENTS
Lack of or an excessive amount of lubrication will affect the performance and life of this tool. Use only recommended lubricants at
below time intervals:
EVERY 8 HOURS OF TOOL OPERATION - Fill lubricator reser-
voir of recommended F.R.L. with spindle oil (29665).
EVERY 160 HOURS OF TOOL OPERATION - Inject NLGI #1
“EP” grease (33153), 1 to 2 strokes, thru grease fitting in gear
housing. NOTE: Spindle must be extended from outer sleeve sufficiently to expose grease fitting in gear housing. Gearing should
contain approximately 1/8 oz. (3.5 g) of grease.
AIR SUPPLY REQUIREMENTS
For maximum operating efficiency, the following air supply specifications should be maintained to this air tool:
l
AIR PRESSURE - 90 PSIG (6 bar)
l
AIR FILTRATION - 50 micron
l
LUBRICATED AIR SUPPLY
l
HOSE SIZE - 5/16” (8 mm) I.D.
An ARO® model C28231-810 air line FILTER/REGULATOR/LUBRICATOR (F.R.L.) is recommended to maintain the above air
supply specifications.
MOUNTING
The nose end of the outer sleeve (41) is provided with 1-7/16” -
18 L.H. threads [remove thread guard (47) for use] and a 1-7/16”x
1/2” long pilot diameter for fixture mounting. Foot and flange type
mounting brackets are available for tool mounting.
RECOMMENDED LUBRICANTS
Afterdisassembly is complete, all parts, except sealed or shielded
bearings, should be washed with solvent. To relubricate parts, or
for routine lubrication, use the following recommended lubricants:
Where Used
Air Motor
“0” Rings & Lip Seals
Gears and Bearings
- Description
29665 1 qt. Spindle Oil
36460 4 oz. Stringy Lubricant
33153
5 lb. “EP” - NLGI #1 Grease
SET-UP PROCEDURE
WARNING: Keep clear of rotating end of unit with hands and/or
clothing. Keep fingers/hands from being pinched between housing or valves and adjustment screws and/or trip bracket.
l
Loosen two screws (29) and remove cover (1).
l
Allow a minimum distance of 1/4” between the drill point of the
unit and the workpiece. This is necessary for the air motor to
start and reach free speed before the drill point touches the
workpiece.
a
Determine the TOTAL STROKE LENGTH the drill must travel
to perform the drilling operation - see illustration below.
l
Loosen jam nut (8) and turn adjustment screw “A” so the distance between the end of the screw and the stud (26) equals
the total stroke length.
l
Tighten jam nut (8).
a
Loosen jam nut (8) and turn adjustment screw “B” (valve-inhead models only) so the distance between the end of the
screw and the button bleed valve (25) is slightly GREATER
than the distance set for adjustment screw “A”.
0
Start and let the unit advance until the adjustment screw “A”
makes contact with the stud (26).
l
Carefully, and be aware that the unit is going to retract, turn the
adjustment screw “B” until it depresses the button bleed valve
(25) enough to cause the unit to retract.
l
lighten jam nut (8).
a
See “FEED RATE CONTROL VALVES”, page 2.
ADJUSTMENT SCREW “6”
DEPTH OF DRILLING
OPERATION
THIS DISTANCE MUST
TOTAL STROKE LENGTH
For parts and service information, contact your local ARO distributor, or the Customer Service Dept. of the Ingersoll-Rand Dis-
tribution Center, White House, TN at PH: (615) 672-0321, FAX: (615) 672-0601.
A
R0 Tool Products
Ingersoll-Rand Company
1725 U.S. No. 1 North l P.O. Box 8000 l Southern Pines, NC 283888000
01994 THE ARO CORPORATION. PRINTED IN U.S.A.
INGERSOLL-RAND,
ADJUSTMENT SCREW “‘A’
7
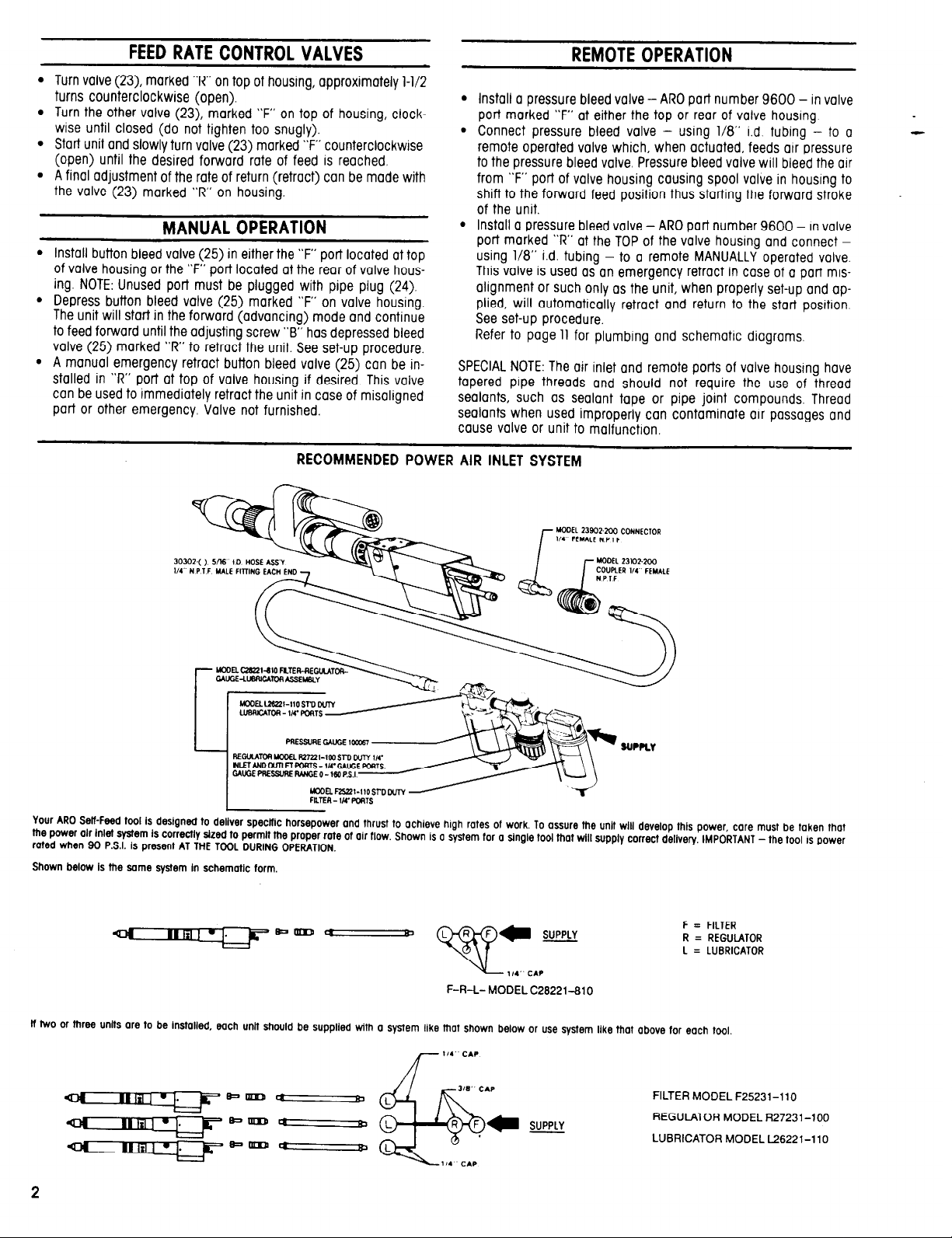
FEED RATE CONTROL VALVES
REMOTE OPERATION
l Turn valve (23), marked “R” an top of housing, approximately 1-1/2
turns counterclockwise (open).
l Turn the other valve (23), marked “F” on top of housing, clock-
wise until closed (do not tighten too snugly).
l Start unit and slowly turn valve (23) marked “F” counterclockwise
(open) until the desired forward rate of feed IS reached.
l A final adjustment of the rate of return (retract) can be made with
the valve (23) marked “R” on housing.
MANUAL OPERATION
install button bleed valve (25) in either the “F” port located at top
of valve housing or the “F” port located at the rear of valve housing. NOTE: Unused port must be plugged with pipe plug (24).
Depress button bleed valve (25) marked “F” on valve housing.
The unit will start in the forward (advancing) mode and continue
to feed forward until the adjusting screw “B” has depressed bleed
valve (25) marked “R” to retract the unit. See set-up procedure.
A manual emergency retract button bleed valve (25) can be installed in “R” port at top of valve housing if desired. This valve
con be used to immediately retract the unit in case of misaligned
part or other emergency. Valve not furnished.
RECOMMENDED POWER AIR INLET SYSTEM
Install a pressure bleed valve-ARO port number 9600 - in valve
port marked “F” at either the top or rear of valve housing
Connect pressure bleed valve - using 1/8” i.d. tubing - to o
remote operated valve which, when actuated, feeds air pressure
to the pressure bleed valve. Pressure bleed valve will bleed the air
from “F” port of valve housing causing spool valve in housing to
shift to the forward feed position thus starting the forward stroke
of the unit.
Install a pressure bleed valve-ARO port number 9600 - in valve
port marked “R” at the TOP of the valve housing and connect using 1/8” i.d. tubing - to o remote MANUALLY operated valve.
This valve is used OS on emergency retract in case of a port misalignment or such only as the unit, when properly set-up and applied, will automatically retract and return to the start position.
See set-up procedure.
Refer to page 11 for plumbing and schematic diagrams.
SPECIAL NOTE: The air inlet and remote ports of valve housing hove
tapered pipe threads and should not require the use of thread
sealants, such as sealant tape or pipe joint compounds. Thread
sealants when used improperly can contaminate air passages and
cause valve or unit to malfunction.
Your
ARO Self-Feed tool
the power air inlet system is correctly sized to permit the proper rote of air flow. Shown is a system tar o single tool that will supply correct delivery. IMPORTANT -the tool IS power
rated when 90 P.S.I. is present AT THE TOOL DURING OPERATION.
Shown below Is the same system In schematic form.
If two or three units are to be installed, each unit should be supplied with o system like that shown below or use system like that above far each tool.
is
designed to deliver specific horsepower and thrust to achieve high rates of work. To assure the unit will develop this power care must be taken that
F = FILTER
R = REGULATOR
L = LUBRICATOR
F-R-L- MODEL C28221-810
FILTER MODEL F25231-110
REGULATOR MODEL R27231-100
LUBRlCATOR MODEL L26221-110

Fig.1
Y--
--Y
IMPORTANT
RECOMMENDED METHOD FOR HOLDING DRILLS IN SPINDLES
To properly hold drill bit in collet and reduce the chance of slippage,
a flat must be ground on the shank end of the bit. The flat should
be approximately 5/16” (8mm) long and the depth should be 1/3 of
the bit diameter NOTE: If bit
IS
too large to fit into locking insert (smaller
capacity Dual Spindles do not hove insert), a square must be ground
onto the shank end of the bit.
SET-UP PROCEDURE WITH OPTIONAL
HYDRAULIC CHECK
Assemble hydraulic check to mounting bracket and assemble
mounting bracket to tool using washers (Y14-8) and cap screws
(Y154-48).
Measure distance from drill point to work piece - distance “Y”.
Distance “X” between hydraulic check plunger and trip bracket
must be less than distance “Y” to prevent damage to drill point
when it approaches the work piece.
Loosen the cap screws (Y154-48) and position hydraulic check
to obtain correct setting for distance “X”.
Tighten cop screws (Y154-48) securely before operating unit.
Increase the air flow thru the Feed Control Valve marked “F” by
opening two (2) full turns from closed position. This will allow drill
to advance rapidly until the trip bracket contacts plunger of hydraulic check.
Fsg.4
i ’ b
c‘t NT1 v\
’
Insert bit into spindle and into locking insert (where applicable) In-
suring that one of the set screws locates squarely on the flat of the
bit. Tighten collet firmly, then tighten set screws. NOTE: DO NOT over-
tighten collet. NOTE: Intent of set screws is only to keep bit from turn-
ing in collet.
The Hydraulic Feed Rate Adjustment is located at the name plate
end of the Hydraulic Check Rotate extended spindle until the slot
on spindle IS located midway between the highest and the lowest
settings.
Start drill unit and the drill will advance at a rapid rate until the
trip bracket contacts plunger of hydraulic check.
Slowly rotate the Hydraulic Feed Rate counter clockwise for faster
feed rate or clockwise for slower feed rate.
TO CONTROL BREAKTHROUGH
Position hydraulic check so the distance between the plunger and
the trip bracket (distance “X”) is less than the distance from the
drill point to the opposite side of the work piece (distance “W’).
l
Set-up of the self-feed drill unit will be the same as explained in
Set-Up Procedure, page 1.
FEED RATE ADJUSTMENT
* HYDRAULIC CHECK (SEE TABLE)
ADJUSTMENT SCREW “6”
OUNTING BRACKET 40298
PARTS INDICATED BY ASTERISK (*) ARE INCLUDED
IN 40301-( ) HYDRAULIC CHECK ASSEMBLY.
7
3