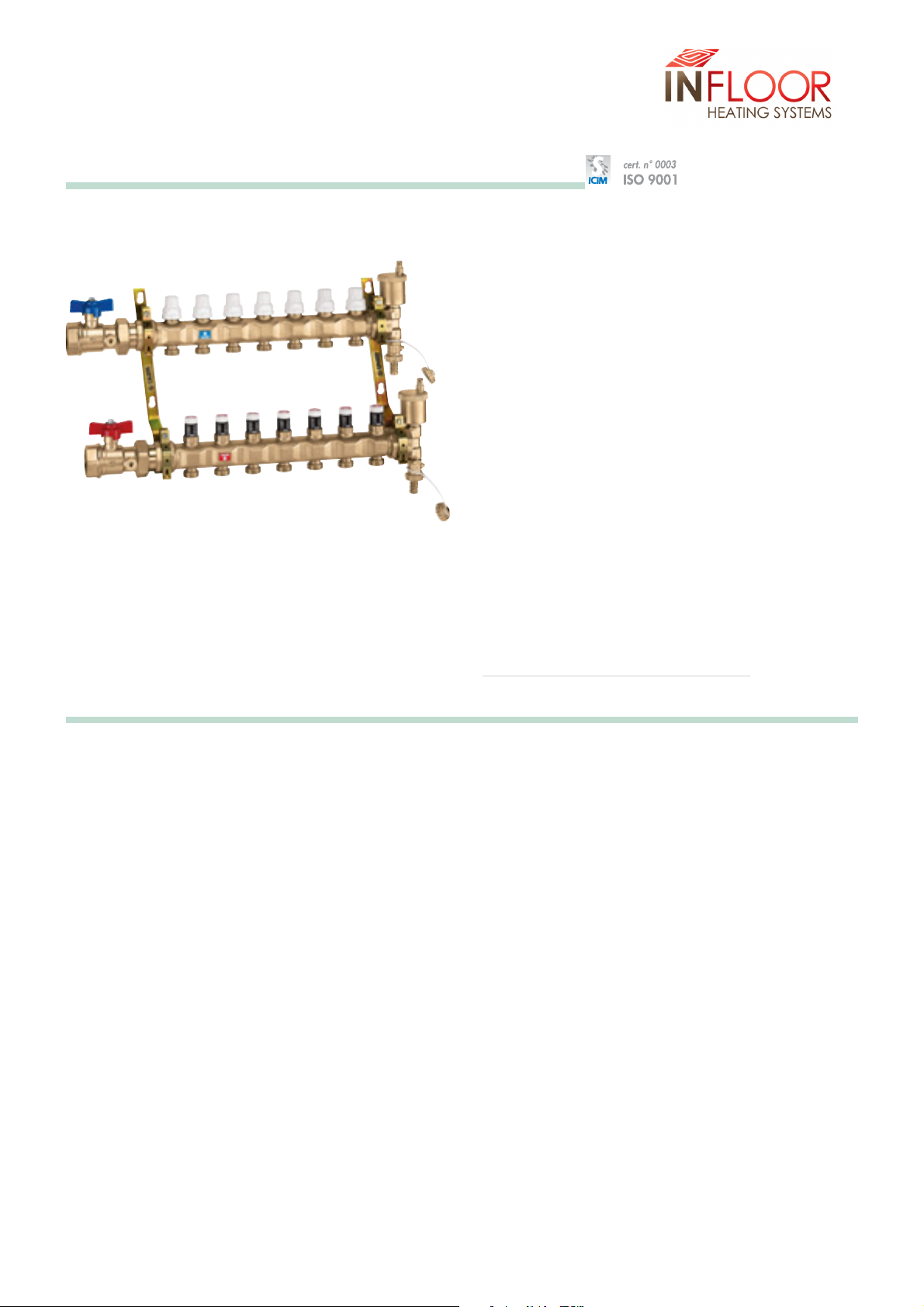
Pre-assembled distribution manifolds
for radiant panel systems
Function
Distribution manifolds for radiant panel systems are used to
optimally distribute the heating uid in oor heating system circuits
and ultimately improve the control of heat emission from the panels.
The manifolds ensure that the ow to each circuit is regulated
precisely and also control the shut-o, venting and automatic
removal of air from the system.
Special solutions devised during sizing have also enabled depth to
be reduced and connection between manifold and branches
facilitated.
Reference Documents
Product guides for additional components, such as thermal
actuators, ow meters, pressure dierential bypass valves
and darcel ttings.
range
Product
Pre-assembled distribution manifold for radiant panel systems Sizes 1” and 1 1/4”
Technical specication
Materials:
Flow manifold
- body: brass EN 1982 CB753S
Micrometric balancing valve
- body: PA
- control device upper part: brass EN 12164 CW614N
- obturator: POM
- obturator seal: EPDM
- knob: ABS
Return manifold
- body: brass EN 1982 CB753S
Shut-o valve
control device upper part:
-
- obturator stem: stainless steel
- obturator: EPDM
- springs: stainless steel
- seals: EPDM
- knob: ABS
Ball valve
- body: brass EN 12165 CW617N
- ball: brass EN 12164 CW614N, chrome plated
- handle: aluminium EN AB 46100
brass EN 12164 CW614N
and PA
End tting
Automatic air vent valve
- obturator stem: brass EN 12164 CW614N
- spring: stainless steel
- seals: EPDM
- oat: PP
Performance:
Medium: water, glycol solutions
Max. percentage of glycol: 30%
Max. working pressure: 10 bar
Max. end tting discharge pressure: 2,5 bar
Working temperature range: 0–80°C
Nr. adjustment curves: 10
Micrometric regulating valve scale: 0–10
Accuracy: ± 5%
Main connections: 1”, 1 1/4” F
Connection centre distance: 195 mm
Outlets: 3/4”M - Ø 18
Outlet centre distance: 50 mm
N716WC 56121 NE ssarb:ydob -
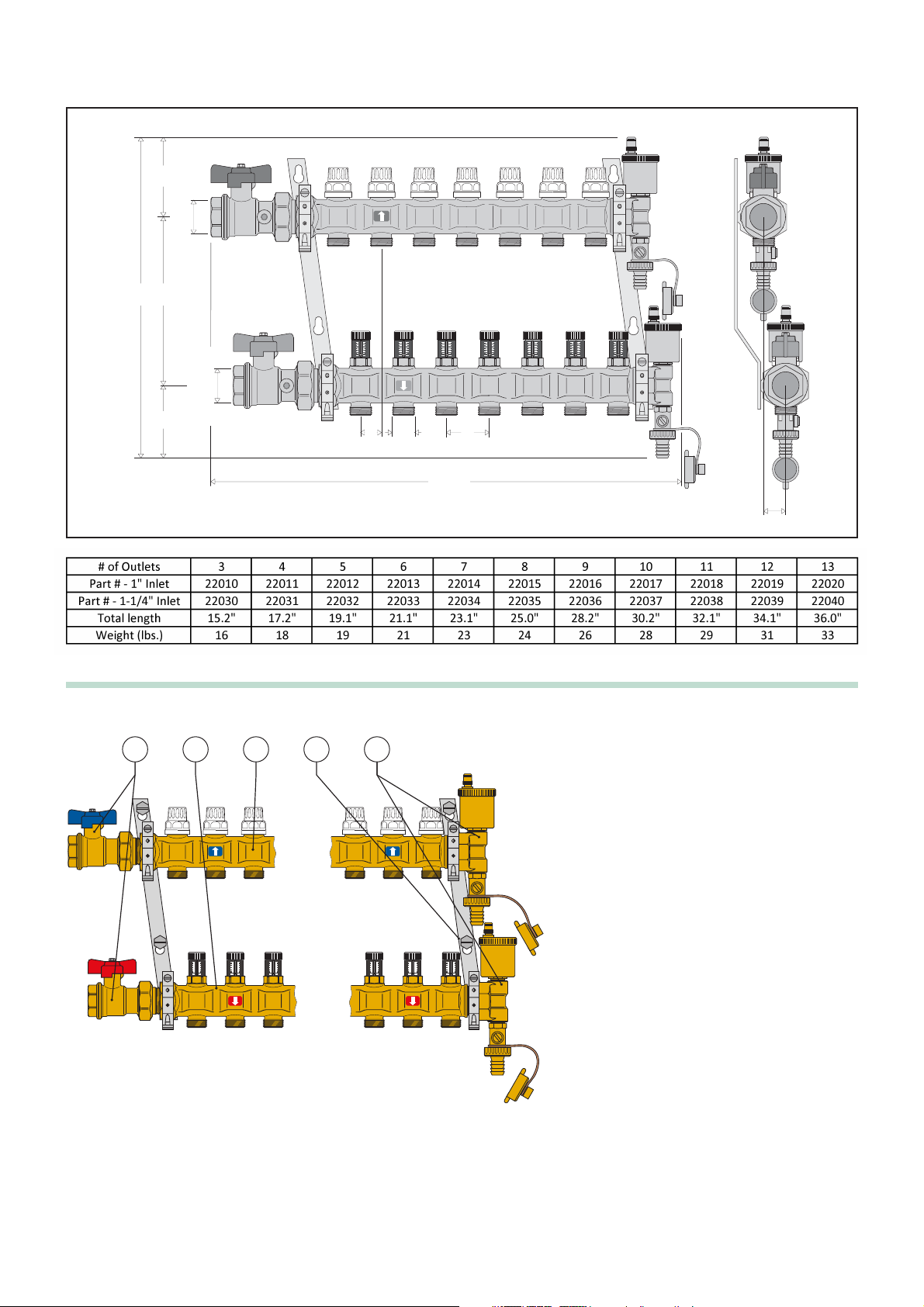
Characteristic components
1 Flow manifold complete with micrometric pre
regulating valves with flow curve number
indicator.
2 Return manifold complete with shut-off valves
that can be used with thermoelectric actuators.
3 Pair of shut-off ball valves
4 End fittings consisting of a 3-way end fitting,
automatic air vent valve and drain cock.
5 Pair of mounting brackets for use with series 659
boxes or direct wall installation.
383
10119587
1” o 1 1/4”
1” o 1 1/4”
10
10
10
8
8
8
6
6
6
4
4
4
2
2
2
0
0
0
25
3/4”
10
10
10
8
8
6
6
4
4
2
2
0
0
10
10
8
8
6
6
4
4
2
2
0
0
10
10
8
8
6
6
4
4
2
2
0
0
10
10
8
8
6
6
4
4
2
2
0
0
10
10
8
8
8
6
6
6
4
4
4
2
2
2
0
0
0
50
total
L
27
21345
10
10
8
6
4
2
0
10
10
8
8
6
6
4
4
2
2
0
0
10
10
8
8
8
6
6
6
4
4
4
2
2
2
0
0
0
10
10
8
6
4
2
0
10
10
8
8
6
6
4
4
2
2
0
0
10
10
8
8
8
6
6
6
4
4
4
2
2
2
0
0
0
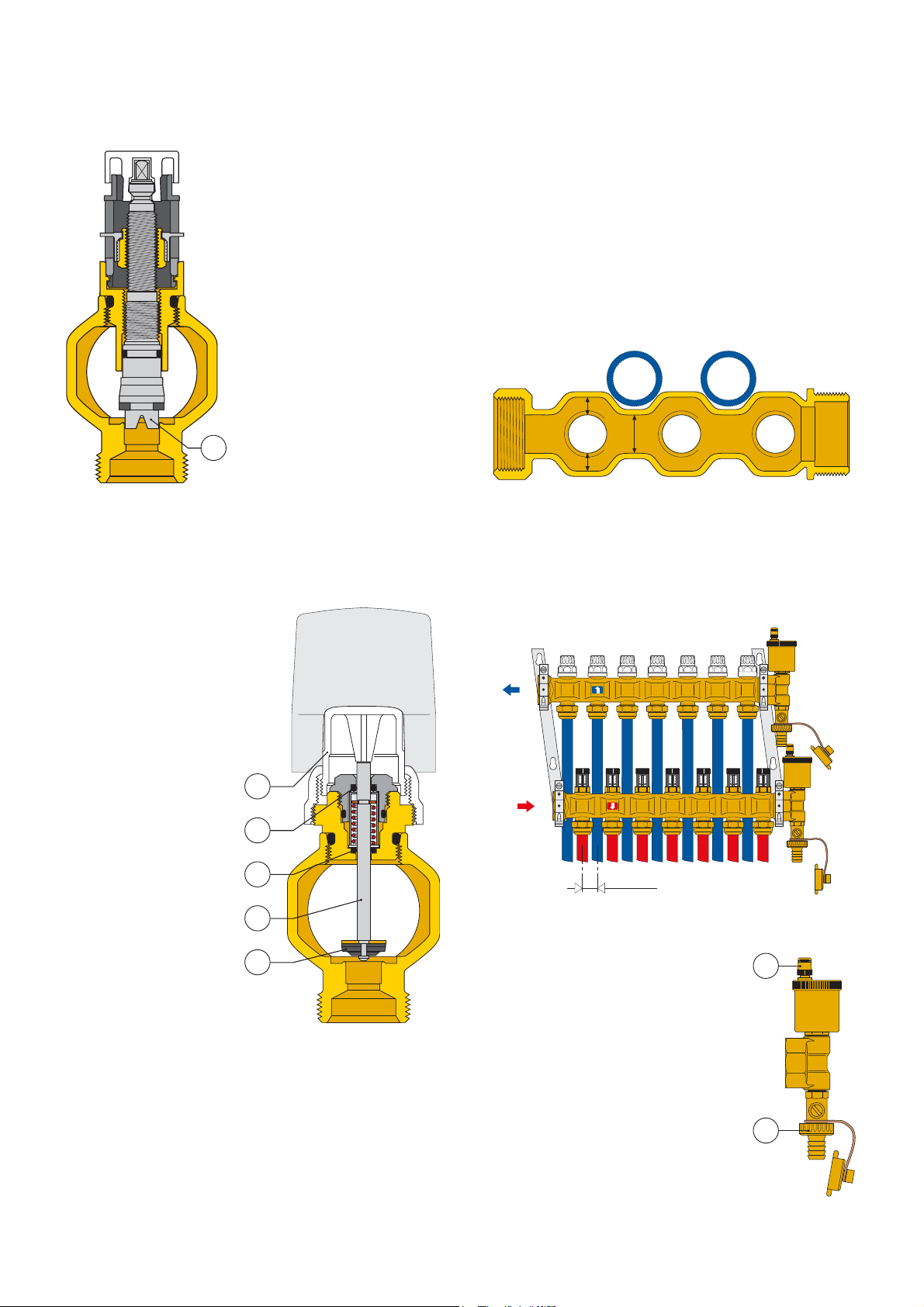
Construction details
Flow manifold
The micrometric regulating valve
obturator is made of plastic (POM)
and features an upside down V
channel (1) to provide greater
precision when regulating the flow
delivered to the floor system circuits.
This solution offers the following
advantages with respect to the
traditional conically shaped
obturator:
- greater precision, particularly for
the low flow rates usually
encountered in this kind of system.
- proportional flow rates due to the
ability to mould the fluid passage
profiles.
- absolute dimensional consistency
during manufacture due to the
die-cast obturator.
Return manifold
The return manifold is equipped with manual shut-off valves (1)
which are used to shut off the flow to individual circuits.
They can also be used with a
thermoelectric actuator
which, when used with an
ambient thermostat,
maintains the ambient
temperature at the set limits
when thermal load varies.
The obturator stem (2) is
made of polished stainless
steel to minimise friction and
prevent harmful encrustation
from forming.
The control device upper part
features a double EPDM
O-ring seal (3) – (4) on the
sliding stem.
The obturator (5) is made of
EPDM and is moulded to
optimise the hydraulic
characteristics of the valve
and reduce noise to a
minimum as the fluid
passes through and as it
gradually opens and closes
when operating with a
thermo-electric actuator.
1
Exterior shape of the manifolds and mounting brackets
The exterior of the manifold deserves special mention because it
can be cast in any shape to meet any requirements.
In the example shown below, indentations have been created in the
manifold to correspond to the plastic pipes exiting from the upper
manifold, thus partially accommodating the pipes and reducing
their overall thickness. This does not interfere with the pressure loss
values because the sections with the indentations (a) are equal to
the sections in which the pipes are branched (b) and (c) and where
the regulating parts (micrometric regulating and shut-off valve
obturators) obstruct the passage of the fluid.
b
a
c
The partial accommodation of the pipes in the indentations created
in the manifold is further enhanced by the shape of the mounting
brackets, which are slanted to create a 3/4 in. offset between the
upper and lower manifolds.
1
3
4
2
5
As shown in the figure below, this offset positions the pipes so that
they perfectly match the profile of the manifold during installation.
10
10
10
10
10
10
10
10
10
10
10
10
10
8
8
8
8
8
8
8
8
8
6
6
6
6
6
4
4
2
2
0
0
6
4
4
4
4
2
2
2
2
0
0
0
0
8
6
6
6
6
4
4
4
4
2
2
2
2
0
0
0
0
10
8
8
8
8
6
6
6
6
4
4
4
4
2
2
2
2
0
0
0
0
25 mm
End fitting and automatic air vent valve
The end fitting consists of a fill/drain cock (1)
and an automatic air vent valve with a
hygroscopic safety cap (2). It has been
specifically designed to close the air vent valve
automatically if there is water near the vent
itself.
2
1
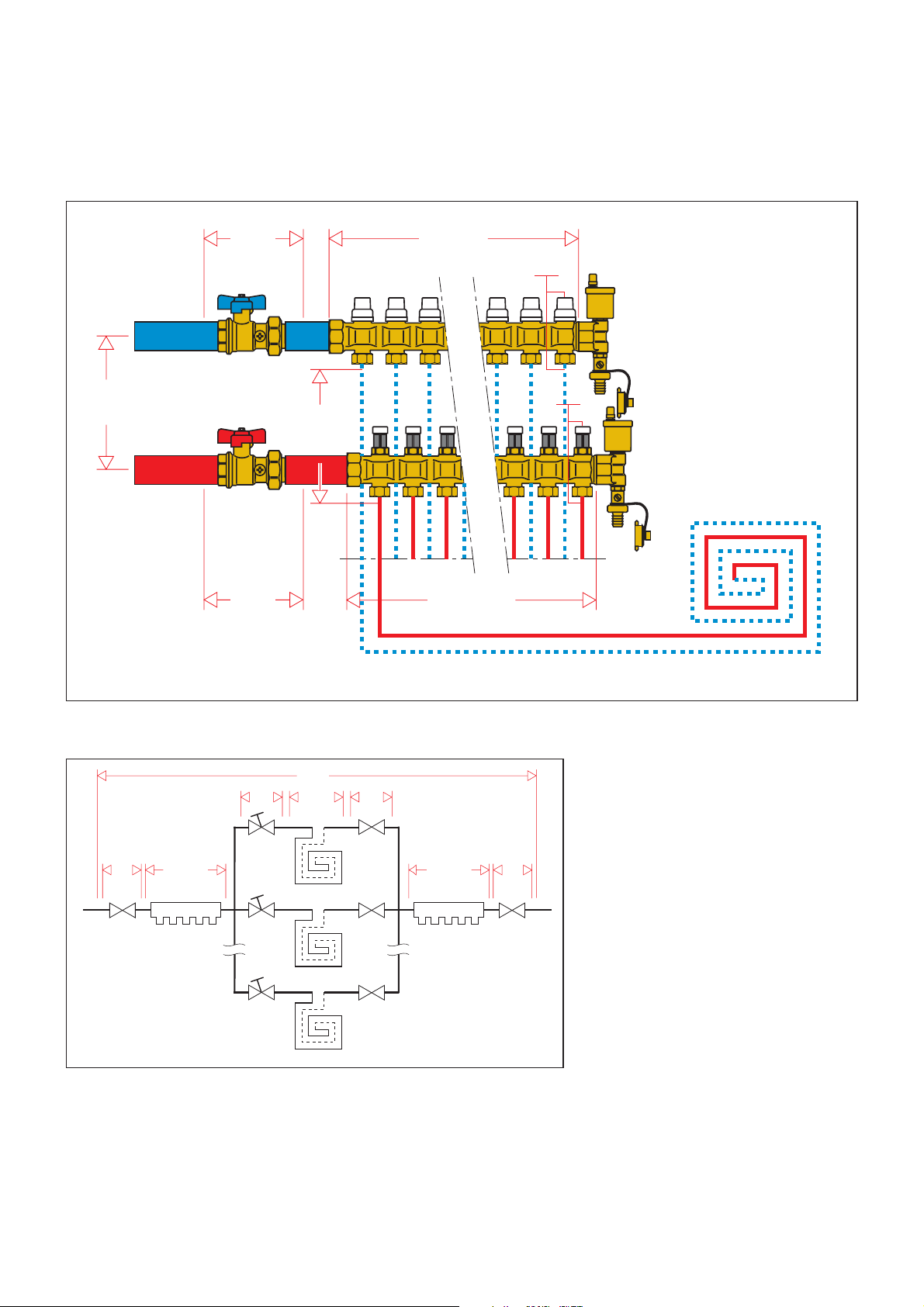
Hydraulic characteristics
To determine the hydraulic characteristics of the circuit, we must calculate the total pressure loss experienced by the flow of fluid as it passes
through the manifold unit parts and the radiant panel circuits.
From a hydraulic standpoint, the manifold unit and circuits can be shown as an assembly of hydraulic elements that are arranged in series and
parallel to each other.
ΔP
Tot = Total loss at the manifold heads
(Flow + Return + Loop)
ΔPMV = Localised loss at the micrometric
regulating valve loop (loop flow)
ΔPLoop = Loop loss (loop flow)
ΔPSV = Localised loss at the shut-off valve in the
panel circuit (loop flow)
ΔPFM = Distributed loss of the flow manifold
(total flow)
ΔPRM = Distributed loss of the return manifold
(total flow)
ΔPBV = Ball valve loss (total flow)
ΔPTo t =
ΔPMV +ΔPLoop+ΔPSV
+ ΔPFM + ΔPRM +ΔPBV x 2
After noting the hydraulic characteristics of the individual components and the design flows, the total loss can be calculated as the sum of the
partial pressure losses of each specific component in the system, as shown in the formula
(1.1)
.
ΔP
BV
To t
ΔP
RM
ΔP
SV
ΔP
VM
ΔP
Loop
ΔP
G
To t
ΔP
BV
ΔP
FM
G
Loop
ΔP
Tot
ΔP
ΔP
BV
G
Tot.
ΔP
FM
MV
ΔP
Loop
ΔP
SV
G
Loop
ΔP
RM
ΔP
BV
G
Tot