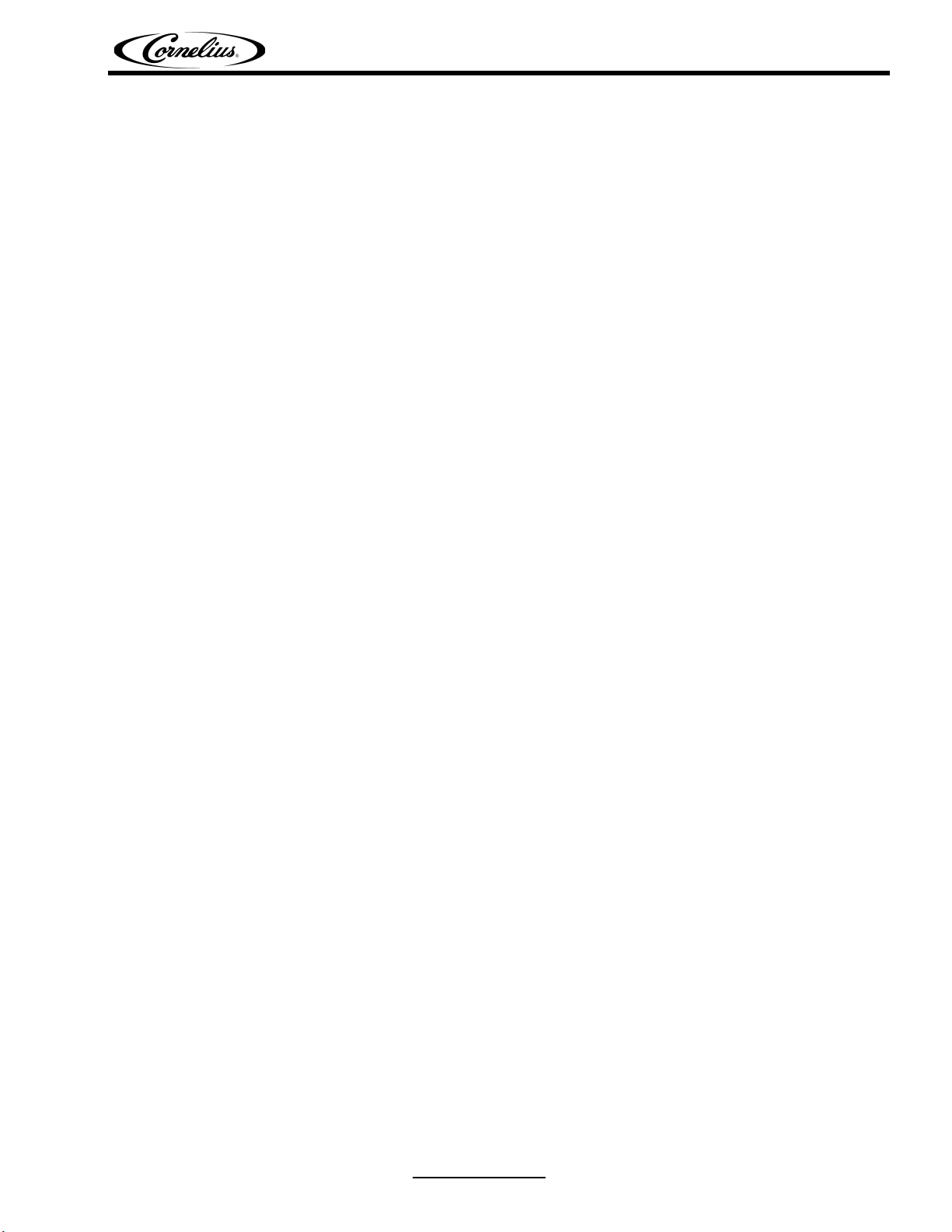
Continuous Flow Icemaker Installation Manual
INSTALLATION MANUAL
CONTINUOUS FLOW ICEMAKERS SERIES 500, 700, 1000, AND 2000
This manual covers unpacking and inspection, selecting location, installing unit, and preparing for
operation.
REMOVE ICEMAKER FROM CARTON
1. Keep unit in the upright position, remove carton and pallet from unit and inspect unit for damage.
Upon inspection of unit, if any damage is found, file a claim with carrier immediately.
CABINET REMOVAL
1. Front Panel—Remove 4 screws and pull forward.
2. Top Panel—Remove screws and lift upward. 4 screws 500/700, 6 screws 1000.
3. Side Panel—Remove 4 screws and pull forward.
4. Back Panel—Should not be removed.
PREPARATION OF INSTALLATION SITE
1. The refrigeration system on air cooled units requires airflow, so a well ventilated area should be
chosen. A minimum of 6 inches must be maintained, free of any obstructions, for air intake. A
minimum of 4 inches clearance is required for air exhaust.
2. The unit can be installed either on an ice storage bin or ice d ispenser using the p roper a dapter kits.
(Refer to sales literature for information.) The install is kit provided with each icemaker and adapter
kits will supply everything to locate unit correctly. In all cases the icemaker should be sealed all
around the base with an NSF listed sealant. (63804815 B)
WATER INLET HOOK UP
1. Water Inlet—fitting is a 1/4 SAE male flare located at the rear of the unit. Connect water supply
with a 1/4 SAE flare nut and 1/4” copper or flexible tubing or larger.
2. Water Pressure—Unless otherwise specified, the unit is designed to operate on water pressures
between 10 P.S.I. and 90 P.S.I. (NOTE: for pressures above 90 P.S.I. a regulator must be installed.)
3. Condenser Inlet Connections—Use a separate 3/8” copper line or larger water line. Connect to 3/
8 FPT fitting on water modulating valve.
4. Filter/Conditioners are recommended on supply lines to icemakers. Never run the water supply to
water cooled condenser through filter/conditioner, it uses up the cartridge unnecessarily and a
saturated cartridge can starve the icemaker causing premature component damage. Separate
water supplies are recommended.
NOTE: Unit must be installed per local plumbing code BOCA.
DRAIN CONNECTION
1. Overflow Line—is a 3/8” I.D. flexible tube located at the rear of the unit. Extend this line to proper
drain.
2. Condenser Outlet—is a 3/8” FPT located on the rear panel.
NOTE: Unit must be installed per local plumbing code. BOCA.
ELECTRICAL SUPPLY
1. Power Access—is provided with a 7/8” diameter. knockout hole in the rear panel. Route incoming
power in conduit, through rear panel to icemaker electrical control box. Make connections to wires
provided in the control box and ground lug/screw.
2. Fused Line—should be checked and sized according to electrical rating shown on unit nameplate.
Release Date: July 1, 2008 www.cornelius.com Revision: C
© 2004-2008, IMI Cornelius Inc. - 1 - Publication Number: 630460174INS
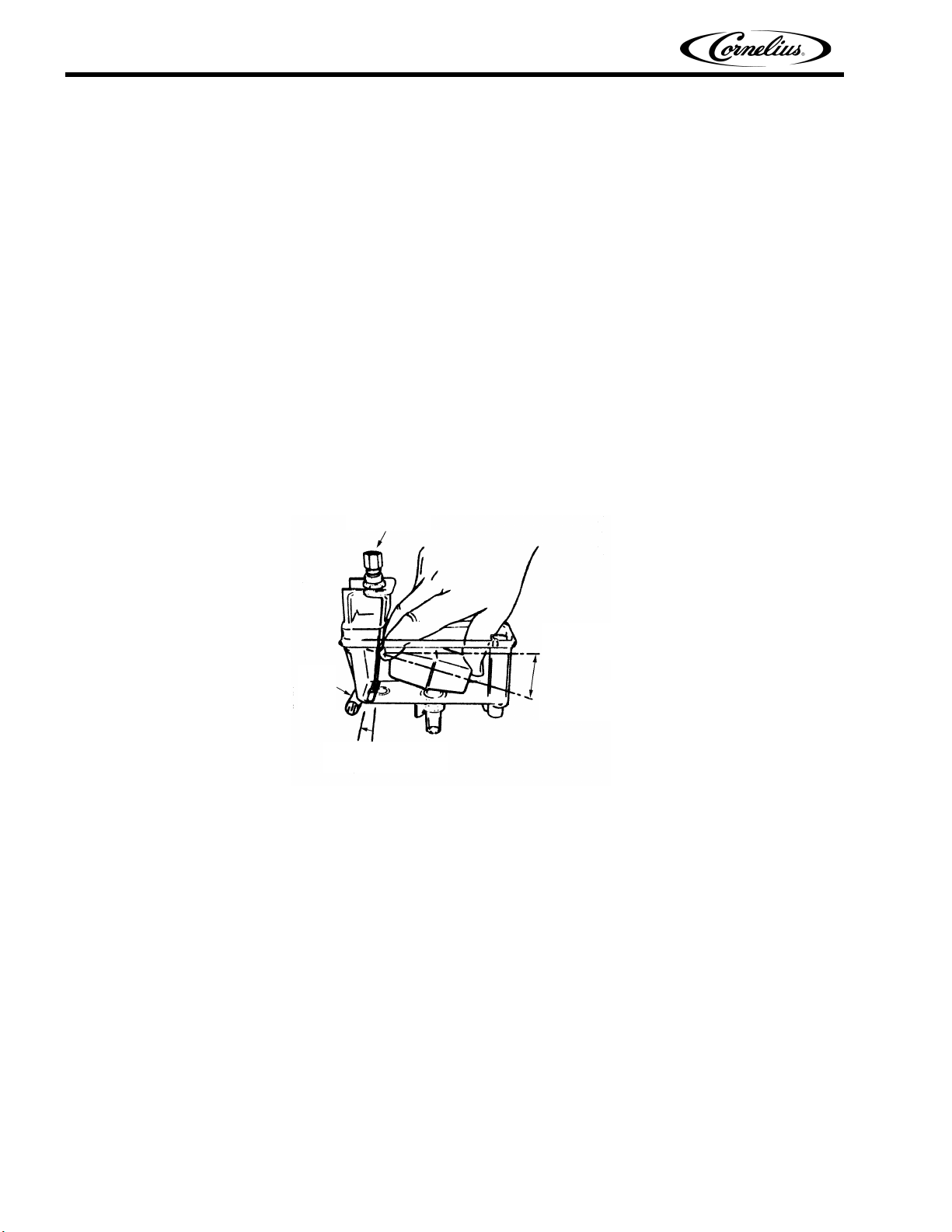
Continuous Flow Icemaker Installation Manual
AUGER ENGAGEMENT
Be certain that auger is fully engaged to lower drive and extruding head is fully engaged into evaporator.
INITIAL START UP, CHECKS AND ADJUSTMENT INSTRUCTIONS
NOTE: Do not start unit before completing installation steps on the previous page.
Turn on water supply (if unit is water cooled turn water on to condenser also) turn on main power switch
(located on top of electrical box), and make the following system checks:
NOTE: If unit will not start be sure water reservoir is full. Low water safety control must be
properly adjusted to start and shut down unit. If water level drops below bottom of reservoir, unit
must shut down. Adjustment is made by moving magnet up or down.
Water Level—If necessary adjust float by bending float arm up or down as needed, push float
assembly down until unit stops running. Release float and unit will restart. Keep water in reservoir at level
line while unit is in operation.
Low Water Safety Control—Adjust magnet by bending magnet arm as needed to shut unit down if
water level drops below bottom of reservoir.
Bin Control—Place ice around probe, unit should shut down in one minute. Remove ice from around
probe, unit should start in two minutes.
Inlet Fitting
Low Water
Safety
Water modulating valve (water cooled units only)—Opening point of condenser water modulating
valve should be set to maintain proper operating pressure in the refrigeratio n system high side. Closing
point of valve should be set low enough to close valve du ring compressor st and by pe riods. To raise, turn
counterclockwise, to lower turn clockwise.
NOTE: If any of these checks or adjustments cannot be achieved, refer to Service Manual or call
for factory assistance at 1-800-238-3600.
For WCC2001QT-R Only:
1. The WCC2001QT-R is equipped with a compressor start delay. The auger motors will run before
compressor start for approximately two minutes. This is to clear out the evaporators and is normal.
2. The WCC2001QT-R is equipped with an auger motor run delay. The auger motors will run after
compressor shut down for approximately two minutes. This is to clear out the evaporators and is
normal.
Bend up to
Raise Water Level
Bend Down to
Lower Water Level
Bend in this Direction to
Shut Down Unit Sooner
FIGURE 1. ICEMAKER FLOAT ASSEMBLY
Publication Number: 630460174INS - 2 - © 2004-2008, IMI Cornelius Inc.