
Hypertherm, Inc.
Etna Road, P.O. Box 5010
Hanover, NH 03755 USA
603-643-3441 Tel (Main Office)
603-643-5352 Fax (All Departments)
info@hypertherm.com (Main Office Email)
800-643-9878 Tel (Technical Service)
technical.service@hypertherm.com (Technical Service Email)
800-737-2978 Tel (Customer Service)
customer.service@hypertherm.com (Customer Service Email)
Hypertherm Automation
5 Technology Drive, Suite 300
West Lebanon, NH 03784 USA
603-298-7970 Tel
603-298-7977 Fax
Hypertherm Plasmatechnik GmbH
Technologiepark Hanau
Rodenbacher Chaussee 6
D-63457 Hanau-Wolfgang, Deutschland
49 6181 58 2100 Tel
49 6181 58 2134 Fax
49 6181 58 2123 (Technical Service)
Hypertherm (S) Pte Ltd.
No. 19 Kaki Bukit Road 2
K.B. Warehouse Complex
Singapore 417847, Republic of Singapore
65 6 841 2489 Tel
65 6 841 2490 Fax
65 6 841 2489 (Technical Service)
Hypertherm (Shanghai) Trading Co., Ltd.
Unit 1308-09, Careri Building
432 West Huai Hai Road
Shanghai, 200052
PR China
86-21 5258 3330/1 Tel
86-21 5258 3332 Fax
France (Representative office)
15 Impasse des Rosiers
95610 Eragny, France
00 800 3324 9737 Tel
00 800 4973 7329 Fax
Hypertherm S.r.l.
Via Torino 2
20123 Milano, Italia
39 02 725 46 312 Tel
39 02 725 46 400 Fax
39 02 725 46 314 (Technical Service)
Hypertherm Europe B.V.
Vaartveld 9
4704 SE Roosendaal, Nederland
31 165 596907 Tel
31 165 596901 Fax
31 165 596908 Tel (Marketing)
31 165 596900 Tel (Technical Service)
00 800 49 73 7843 Tel (Technical Service)
Hypertherm Japan Ltd.
801 Samty Will Building
2-40 Miyahara 1-Chome,
Yodogawa-ku, Osaka
532-0003, Japan
81 6 6170 2020 Tel
81 6 6170 2015 Fax
HYPERTHERM BRASIL LTDA.
Avenida Doutor Renato de
Andrade Maia 350
Parque Renato Maia
CEP 07114-000
Guarulhos, SP Brasil
55 11 6409 2636 Tel
55 11 6408 0462 Fax
Hypertherm
Branch of Hypertherm, UK, UC
PO Box 244
Wigan, Lancashire, England WN8 7WU
00 800 3324 9737 Tel
00 800 4973 7329 Fax
00 800 4973 7843 (Technical Service)
1/19/07

ELEKTROMAGNETISCHE KOMPATIBILITÄT
Hypertherm Plasmaschneidsysteme i
8-06
Einleitung
Die von Hypertherm mit CE-Kennzeichnung
versehenen Ausrüstungen wurden gemäß der
Norm EN60974-10 hergestellt. Um sicherzustellen,
daß die Anlage auf kompatible Weise mit anderen
Radio(frequenz)- und elektronischen Anlagen
zusammenarbeitet, sollte sie entsprechend den
nachfolgend aufgeführten Informationen installiert
und eingesetzt werden, um elektromagnetische
Kompatibilität zu erreichen.
Die in der EN60974-10 verlangten Limits könnten
ungenügend sein, die Interferenz auszuschließen,
wenn sich die betroffene Anlage in geringer Entfernung
befindet oder in hohem Maße empfindlich ist. In
solchen Fällen kann es erforderlich sein, andere
Maßnahmen zu ergreifen, um die Interferenz zu
verringern.
Diese Plasmaanlage sollte nur im gewerblichen
Bereich eingesetzt werden. Es könnte sich schwierig
gestalten, im Privatbereich elektromagnetische
Kompatibilität sicherzustellen.
Installation und Einsatz
Der Bediener ist für die Installation und den Einsatz der
Plasmaanlage gemäß den Anweisungen des
Herstellers verantwortlich. Sollten elektromagnetische
Störungen festgestellt werden, liegt es in der
Verantwortlichkeit des Bedieners, die Situation mit der
technischen Unterstützung des Herstellers zu lösen.
In einigen Fällen kann die Abhilfe einfach in der Erdung
des Schneidschaltkreises liegen, siehe hierzu Erdung
des Werkstückes. In anderen Fällen kann die
Konstruktion einer elektromagnetischen Abschirmung
in Form eines Gehäuses für Stromquelle und Tisch,
komplett mit den dazugehörigen Eingangsfiltern,
erforderlich sein. In allen Fällen müssen die
elektromagnetischen Störungen auf einen Grad
gebracht werden, bei dem sie sich nicht länger
störend auswirken.
Einschätzung des Bereiches
Vor Installation der Anlage ist vom Bediener eine
Einschätzung möglicher elektromagnetischer Probleme
im Umgebungsbereich vorzunehmen. Folgende Punkte
sind dabei zu berücksichtigen:
a. Andere Versorgungskabel, Steuerkabel, Signal- und
Telefonkabel: über, unter und in der Nähe der
Schneidanlage.
b. Radio- und TV-Sende- und Empfangsgeräte.
c. Computer und andere Steuerungsanlagen.
d. Sicherheitskritische Anlagen: zum Beispiel Schutz-
und Industrieanlagen.
e. Gesundheit der Personen in der Nähe: zum Beispiel
Herzschrittmacher und Hörgeräte.
f. Kalibrier- oder Meßgeräte
g. Störsicherheit anderer Geräte in der Umgebung. Der
Bediener hat sicherzustellen, daß andere im Einsatz
befindliche Geräte kompatibel sind. Hierfür können
zusätzliche Schutzmaßnahmen erforderlich sein.
h. Tageszeit, zu der Schneid- oder andere Tätigkeiten
auszuführen sind.
Die zu berücksichtigende Größe des
Umgebungsbereiches ist abhängig von der
Gebäudestruktur und andere Tätigkeiten, die
vorgenommen werden. Der Umgebungsbereich kann
möglicherweise die Geländegrenzen überschreiten.
Methoden zur Emissionsreduzierung
Hauptstromanschluß
Die Schneidanlage sollte entsprechend den
Herstellerempfehlungen angeschlossen werden.
Sollten Funkstörungen auftreten, kann es notwendig
sein, zusätzliche Vorsichtsmaßnahmen zu ergreifen,
wie die Filtrierung des Hauptstromanschlusses.
Das Stromkabel den fest installierten Schneidanlage
sollte zur Abschirmung in einem Metallkanal oder
ähnlichern verlegt sein. Die elektrische Abschirmung
sollte komplett auf der ganzen Länge erfolgen.
Die Abschirmung sollte an die SchneidHauptversorgung angeschlossen werden, damit
ein guter elektrischer Kontakt zwischen dem
Kanal und der Schneidstromzufuhr-Ummantelung
aufrechterhalten wird.
Wartung der Schneidanlage
Die Schneidanlage sollte routinemäßig entsprechend
den Herstellerempfehlungen gewartet werden. Alle
Zugangs- und Wartungstüren und -abdeckungen
müssen geschlossen und ordnungsgemäß befestigt
sein, wenn die Anlage in Betrieb ist. Die Schneidanlage
sollte in keiner Weise verändert werden, mit Ausnahme
der Änderungen und Anpassungen, die in den
Herstelleranweisungen enthalten sind. Insbesondere
sind die Funkenstrecken und Lichtbogenauftreff- und
stabilisierungseinrichtungen entsprechend den
Herstellerempfehlungen anzupassen und zu warten.

ELEKTROMAGNETISCHE KOMPATIBILITÄT
ii Hypertherm Plasmaschneidsysteme
8-06
Schneidtische
Die Schneidtische sind so kurz wie möglich
auszurichten und sollten nahe beieinander aufgestellt
werden und auf Bodenhöhe oder nahe Bodenhöhe zu
betreiben.
Potentialausgleich
Der Ausgleich aller Metallkomponenten der
Schneidausrüstung selbst und in deren Nähe ist in
Betracht zu ziehen. Jedoch erhöhen
Metallkomponenten mit Potentialausgleich am
Werkstück für den Bediener die Gefahr des
elektrischen Schlages, wenn diese Metallkomponenten
und die Elektrode gleichzeitig berührt werden. Der
Bediener muß von all diesen ausgeglichenen
Metallkomponenten isoliert sein.
Erdung des Werkstückes
In Fällen, in denen das Werkstück aus Gründen der
elektrischen Sicherheit nicht mit der Erdung verbunden
ist, oder wegen seiner Größe oder Position nicht an der
Erdung angeschlossen ist, z. B. bei Schiffsrümpfen
oder Gebäude-Stahlkonstruktionen, kann der Anschluß
des Werkstücks an die Erdung in einigen, jedoch nicht
in allen Fällen die Emissionen verringern. Man muß
Sorgfalt walten lassen, um vorzubeugen, daß die
Erdung des Werkstücks das Verletzungsrisiko für die
Bediener oder Beschädigung der anderen elektrischen
Anlagen erhöht. Wo erforderlich, ist der Anschluß des
Werkstücks an die Erdung in Form eines direkten
Anschlusses des Werkstücks vorzunehmen, jedoch ist
die Verbindung in einigen Ländern, in denen direkte
Anschlüsse nicht erlaubt sind, zu erreichen, indem
passende Kapazitäten gemäß den nationalen
Bestimmungen gewählt werden.
Anmerkung: Der Schneidschaltkreis kann aus
Sicherheitsgründen geerdet oder nicht geerdet werden.
Die Veränderung der Erdungsanordnungen darf nur
genehmigt werden von Personen mit entsprechender
Kompetenz für den Zugriff und dem
Einschätzungsvermögen, ob Änderungen die
Verletzungsgefahr erhöhen, zum Beispiel, durch die
Erlaubnis von parallelen SchneidstromRückführpfaden, die die Erdungsschaltkreise anderer
elektrischer Anlagen beschädigen können. Weitere
Richtschnuren sind in IEC/TS 62081
Lichtbogenschweißanlagen-Installation und -Betrieb
enthalten.
Entstörung und Abschirmung
Ausgewählte Entstörung und Abschirmung anderer
Kabel und Anlagen im Umgebungsbereich können
Interferenzprobleme mildern. Die Entstörung der
gesamten Plasmaschneidanlage ist bei bestimmten
Einsätzen in Betracht zu ziehen.

GARANTIE
Hypertherm Plasmaschneidsysteme iii
8-06
Achtung
Hypertherm empfiehlt, für Ihr Hypertherm-System nur
Original-Ersatzteile zu verwenden. Bei Schäden, die
dadurch entstanden sind, dass keine Original-Ersatzteile
verwendet wurden, prüft Hypertherm, ob Garantie
gewährt werden kann oder nicht.
Achtung
Sie sind für die ordnungsgemäße Nutzung des Produkts
selbst verantwortlich. Hypertherm übernimmt keine
Gewähr für die ordnungsgemäße Nutzung des Produkts
in Ihrer Umgebung und kann dafür auch keine Garantie
gewähren.
Allgemein
Hypertherm, Inc. garantiert, dass seine Produkte keine
Material- und Verarbeitungsfehler aufweisen,
vorausgesetzt, Hypertherm wird (i) innerhalb eines
Zeitraumes von zwei (2) Jahren ab dem Liefertag an Sie
über einen Defekt an der Stromquelle informiert,
ausgenommen sind Stromquellen der Powermax-Serie,
für welche ein Zeitraum von drei (3) Jahren ab
Lieferdatum an Sie gilt, und (ii) bezüglich eines Defekts
am Brenner und Schlauchpaket innerhalb eines
Zeitraumes von einem (1) Jahr ab Lieferdatum an Sie
informiert. Von der Garantie ausgeschlossen sing
Produkte, die fehlerhaft installiert, modifiziert oder auf
sonstige Weise beschädigt wurden.
Sämtliche durch diese Garantie abgedeckten defekten
Produkte werden von Hypertherm nach seiner eigenen
Wahl unentgeltlich repariert, ersetzt oder angepasst.
Voraussetzung hierzu ist die Rücksendung der Ware an
die Geschäftsadresse von Hypertherm in Hanover, New
Hampshire, oder an eine von Hypertherm autorisierte
Reparaturwerkstatt. Rücksendungen werden nur
angenommen, wenn sie vorher von Hypertherm
autorisiert wurden – dies geschieht im Normalfall rasch
und unbürokratisch – und wenn die Ware angemessen
verpackt ist. Versicherungs- und Frachtkosten sowie alle
sonstigen bei der Rücksendung anfallenden Kosten trägt
der Absender. Hypertherm haftet außerdem nicht für
Reparaturen, den Ersatz oder Neujustierungen von
Produkten, die von dieser Garantie abgedeckt werden,
außer für diese, die gemäß diesem Absatz
angesprochen wurden oder für die Hypertherm zuvor
eine schriftliche Einverständniserklärung abgegeben hat.
Die obigen Garantie-Bestimmungen sind verbindlich
und gelten anstelle von allen anderen GarantieBestimmungen, seien sie ausdrücklich festgelegt,
impliziert, gesetzlich festgelegt oder auf andere
Weise in Bezug zu den Produkten oder den
Resultaten, die sich aus der Nutzung dieser
Produkte ergeben, ausgedrückt; sie gelten auch
anstelle von allen implizierten Garantien oder
Qualitäts-Bedingungen oder Aussagen zur MarktTauglichkeit oder zur Eignung für einen bestimmten
Zweck oder bei Rechtsverletzungen. Das vorher
Gesagte gilt einzig und allein als Rechtsmittel für
alle Garantie-Verletzungen, die sich Hypertherm
zuschulden kommen lässt. Großhändler und
Wiederverkäufer mögen andere oder zusätzliche
Garantien anbieten, aber Großhändler und
Wiederverkäufer sind nicht autorisiert, Ihnen
zusätzlichen Garantieschutz zu gewähren oder
Aussagen zu treffen, von denen behauptet wird, sie
seien für Hypertherm verbindlich.
Zertifizierungsprüfzeichen
Zertifizierte Produkte erkennt man an einem oder
mehreren Zertifizierungsprüfzeichen von zugelassenen
Prüflabors. Die Zertifizierungsprüfzeichen befinden sich
auf dem Typenschild oder in dessen Nähe. Jedes
Zertifizierungsprüfzeichen bedeutet, dass das Produkt
und dessen sicherheitsrelevante Komponenten den
maßgeblichen nationalen Sicherheitsstandards
entsprechen, wie sie von diesem Prüflabor nachgeprüft
wurden. Hypertherm bringt Zertifizierungsprüfzeichen
erst dann an seinen Produkten an, wenn das Produkt mit
sicherheitsrelevanten Komponenten von dem
zugelassenen Prüflabor genehmigt wurde.
Hat das Produkt das Werk von Hypertherm verlassen,
werden die Zertifizierungsprüfzeichen ungültig, sobald
eines der folgenden Dinge geschieht:
• Das Produkt wird auf eine Weise so erheblich
verändert, dass es eine Gefahr oder
Nichtübereinstimmung erzeugt.
• Sicherheitsrelevante Komponenten werden durch
ungenehmigte Ersatzteile ersetzt.
• Jeglicher ungenehmigte Zusammenbau oder jegliches
Hinzufügen von Zubehör, das gefährliche Spannung
einsetzt oder erzeugt.
• Jegliche Manipulation an einem Sicherheitsschaltkreis
oder einer sonstigen Einrichtung, die als Teil der
Zertifizierung in das Produkt konstruiert wurde.
Das CE-Zeichen stellt eine Konformitätserklärung des
Herstellers nach den gültigen Europäischen Richtlinien
und Normen dar. Nur die Versionen der HyperthermProdukte mit CE-Zeichen auf dem Typenschild oder in
dessen Nähe wurden auf Einhaltung der Europäischen
Richtlinie für Niederspannung und der Europäischen
EMV-Richtlinie geprüft. EMV-Filter, die erforderlich sind,
um der Europäischen EMV-Richtlinie zu entsprechen,
sind in den Stromquellenversionen mit CE-Zeichen
eingebaut.

GARANTIE
iv Hypertherm Plasmaschneidsysteme
8-06
Patentschutz
Außer in Fällen von Produkten, die nicht von Hypertherm
hergestellt wurden oder die von einer (im juristischen
Sinne) anderen Person als Hypertherm hergestellt
wurden, die sich nicht strikt an die Spezifikationen von
Hypertherm hielt, wird Hypertherm auf eigene Kosten
Prozesse oder Verfahren führen oder beilegen, die
gegen Sie mit der Begründung eingeleitet werden, dass
die Verwendung eines Hypertherm-Produkts – und zwar
die alleinige Verwendung dieses Produkts und nicht in
Verbindung mit irgendeinem anderen Produkt, das nicht
von Hypertherm geliefert wurde – ein Patent einer dritten
Partei verletzt; dasselbe gilt auch bei Verletzungen in
Fällen von Design-, Verarbeitungs- und Formelvorgaben
oder von Kombinationen aus all diesem, die nicht von
Hypertherm entwickelt wurden oder von denen
behauptet wird, dass sie von Hypertherm entwickelt
wurden. Verständigen Sie Hypertherm unverzüglich,
sobald Sie erfahren, dass eine Klage gegen Sie
angestrengt wird oder wenn Ihnen mit einer Klage in
Verbindung mit einer solchen angeblichen
Patentverletzung gedroht wird; Hypertherms
Verpflichtung, Schadensersatz zu leisten, ist abhängig
von Hypertherms alleiniger Kontrolle bei der
Verteidigung des Anspruchs und der Kooperation und
Unterstützung der beklagten Partei.
Haftungs-beschränkung
Hypertherm ist in keinem Fall Personen oder
Körperschaften für zufällig verursachte Schäden,
Folgeschäden, indirekte Schäden oder Schäden, die
aus Strafen resultieren (inbegriffen – aber nicht
darauf beschränkt – sind Gewinneinbrüche) haftbar.
Dabei kommt es nicht darauf an, ob die Haftpflicht
auf einem Vertragsbruch, einem Delikt,
Erfolgshaftung, Garantie-Verletzungen, einem
Versagen des eigentlichen Zweckes oder anderem
basiert. Selbst wenn auf die Möglichkeit solcher
Schäden hingewiesen wurde, ist Hypertherm nicht
haftbar.
Haftungs-obergrenze
In keinem Fall wird Hypertherms Haftpflicht-Leistung
für eine Forderung, eine Klage, einen Prozess oder
ein Verfahren, die aufgrund der Verwendung des
Produktes oder daraus resultierender Folgen
gemacht wird bzw. erhoben wird bzw. anstehen, im
Ganzen die Summe übersteigen, die für die Produkte
bezahlt wurde, die den Anlass für solche
Forderungen geben. Dabei spielt es keine Rolle, ob
die Haftpflicht auf einem Vertragsbruch, einem
Delikt, Erfolgshaftung, Garantie-Verletzungen, einem
Versagen des eigentlichen Zweckes oder anderem
basiert.
Versicherung
Sie sind dazu verpflichtet, Versicherungen in solchen
Mengen und Arten abzuschließen bzw. jederzeit
beizubehalten, und Sie sind weiter dazu verpflichtet, die
Deckungssumme für Schadensansprüche genügend
hoch und angemessen zu gestalten, dass Hypertherm,
sollte es in Zusammenhang mit seinen Produkten zu
Klagen kommen, so wenig wie möglich belastet wird.
Nationale und lokale
Nutzungsbestimmungen
Die Nutzungsbestimmungen für nationale und lokale
Wasserleitungs- oder elektrische Leitungssysteme
haben Vorrang vor den Anweisungen, die dieses
Handbuch enthält. Hypertherm wird in keinem Fall für
Personen- oder Sachschäden haften, die von einer
unsachgemäßen Nutzung dieser Systeme stammen
oder die von unzulänglichen Arbeitspraktiken herrühren.
Übertragung von Rechten
Sie können etwaig verbliebene Rechte, die Sie hierunter
noch haben, nur in Verbindung mit dem Verkauf all oder
wesentlich all Ihrer Aktiva und all oder wesentlich all
Ihres Aktienkapitals an einen interessierten Nachfolger
übertragen. Dieser muss sich außerdem bereit erklären,
alle Bedingungen und Auflagen dieses GarantieVertrages als verbindlich anzuerkennen.
Ordnungsgemäße Entsorgung von
Hypertherm-Produkten
Wie alle elektronischen Produkte, können HyperthermPlasmaschneidanlagen Materialien oder Komponenten,
z. B. Leiterplatten, enthalten, die nicht in den
gewöhnlichen Abfall geworfen werden können. Es liegt
in Ihrer Verantwortung, jegliche Produkte oder
Bauelemente von Hypertherm in umweltgerechter Weise
entsprechend den nationalen und regionalen
Vorschriften zu entsorgen.
• In den USA sind alle Bundes-, Landes- und regionalen
Gesetze zu prüfen.
• In der Europäischen Gemeinschaft sind die EURichtlinien, die nationalen und regionalen Gesetze zu
prüfen.
• In anderen Ländern sind die nationalen und regionalen
Gesetze zu prüfen.
Registrieren Sie Ihr Produkt online bei:
www.hypertherm.com/warranty.htm

INHALT
powermax30 Wartungshandbuch v
Elektromagnetischer interferenz-filter ......................................................................................................................i
Garantie .....................................................................................................................................................................iii
Abschnitt 1 SICHERHEIT
Sicherheitsrelevante Informationen ..........................................................................................................................1-2
Sicherheitsvorschriften einhalten..............................................................................................................................1-2
Plasmaschneiden kann Brände und Explosionen verursachen................................................................................1-2
Elektrische Schläge sind lebensgefährlich ...............................................................................................................1-3
Statische elektrizität kann platinen Beschädigen......................................................................................................1-3
Giftige Dämpfe können zu Verletzungen oder tod führen.........................................................................................1-4
Ein Plasmalichtbogen kann Verletzungen und Verbrennungen verursachen...........................................................1-5
Lichtbogenstrahlen können Augen und Haut verbrennen.........................................................................................1-5
Sichere Erdung .........................................................................................................................................................1-5
Sicherheit beim Umgang mit Gasdruckausrüstungen ..............................................................................................1-6
Beschädigte Gasflaschen können explodieren.........................................................................................................1-6
Lärm kann zu Gehörschäden führen ........................................................................................................................1-6
Störung von Herzschrittmachern und Hörgeräten ....................................................................................................1-6
Der Plasmalichtbogen kann gefrorene Rohre beschädigen .....................................................................................1-6
Warnschilder.............................................................................................................................................................1-7
Abschnitt 2 SPEZIFIKATIONEN
Stromquelle...............................................................................................................................................................2-2
Abmessungen und Gewicht .............................................................................................................................2-2
T30v Brennerwerte ...................................................................................................................................................2-3
Abmessungen ..................................................................................................................................................2-3
Symbole und Markierungen......................................................................................................................................2-4
-Zeichen ......................................................................................................................................................2-4
CE-Zeichen ......................................................................................................................................................2-4
IEC-Zeichen .....................................................................................................................................................2-4
Abschnitt 3 WARTUNG
Regler und Anzeigeleuchten.....................................................................................................................................3-2
Bedienelemente an der Vorderseite und LEDs................................................................................................3-2
Bedienelemente auf der Rückseite ..................................................................................................................3-2
Theorie des Betriebs.................................................................................................................................................3-3
Allgemeines......................................................................................................................................................3-3
Funktionsbeschreibung ....................................................................................................................................3-3
Betriebsablauf ..................................................................................................................................................3-4
Vorbereitung für die Fehlerbeseitigung.....................................................................................................................3-5
Testausrüstung.................................................................................................................................................3-5
Verfahren und Ablauf bei der Fehlerbeseitigung..............................................................................................3-5
Untersuchung – außen.....................................................................................................................................3-5
Untersuchung – innen ......................................................................................................................................3-6
Anfangswiderstandsprüfung .....................................................................................................................................3-7
Stromquellenübersicht ..............................................................................................................................................3-8
Richtschnur zur Fehlerbeseitigung ...........................................................................................................................3-9
Steuerbaukarten-LEDs ...........................................................................................................................................3-12
Verwendung der Steuerbaukarten-Fehler- und Neustart-LEDs zur Fehlerbeseitigung..................................3-13

INHALT
vi powermax30 Wartungshandbuch
Gerätetests .............................................................................................................................................................3-14
Test 1 – Netzspannung ..................................................................................................................................3-15
Test 2 – Strombaukarten-Spannungsprüfungen ............................................................................................3-16
Test 3 – VBUS und Spannungsgleichgewicht................................................................................................3-17
Test 4 – Magnetventil .....................................................................................................................................3-18
Test 5 – Brenner klemmt in offenem Zustand ................................................................................................3-19
Test 6 – Plasmastart.......................................................................................................................................3-20
Test 7 – Brennerkappensensor ......................................................................................................................3-20
Test 8 – Lüfter ................................................................................................................................................3-21
Test 9 – Druckschalter....................................................................................................................................3-21
Komponentenaustausch .........................................................................................................................................3-22
Entfernen einer Endkappe .............................................................................................................................3-22
Austausch der Brennerleitung........................................................................................................................3-24
Austausch des Werkstückkabels ...................................................................................................................3-26
Austausch des Netzkabels (CSA) ..................................................................................................................3-27
Austausch des Netzkabels (CE) ....................................................................................................................3-28
Austausch des Lüfters....................................................................................................................................3-30
Austausch des Luftfilterelements ...................................................................................................................3-31
Austausch von Luftfilter und Regler ...............................................................................................................3-32
Austausch der Steuerbaukarte.......................................................................................................................3-33
Austausch der Strombaukarte........................................................................................................................3-34
Austausch des Bodens ..................................................................................................................................3-37
Abschnitt 4 TEILELISTE
Stromquellenteile ......................................................................................................................................................4-2
Außen...............................................................................................................................................................4-2
Innenseite, Strombaukartenseite .....................................................................................................................4-3
Innere Lüfterseite .............................................................................................................................................4-4
T30v-Handbrennerteile .............................................................................................................................................4-5
Sicherheitsentscheidende Teile ................................................................................................................................4-6
Empfohlene Ersatzteile.............................................................................................................................................4-7
Abschnitt 5 VERDRAHTUNGSDIAGRAMM
Verdrahtungsdiagramm ............................................................................................................................................5-3
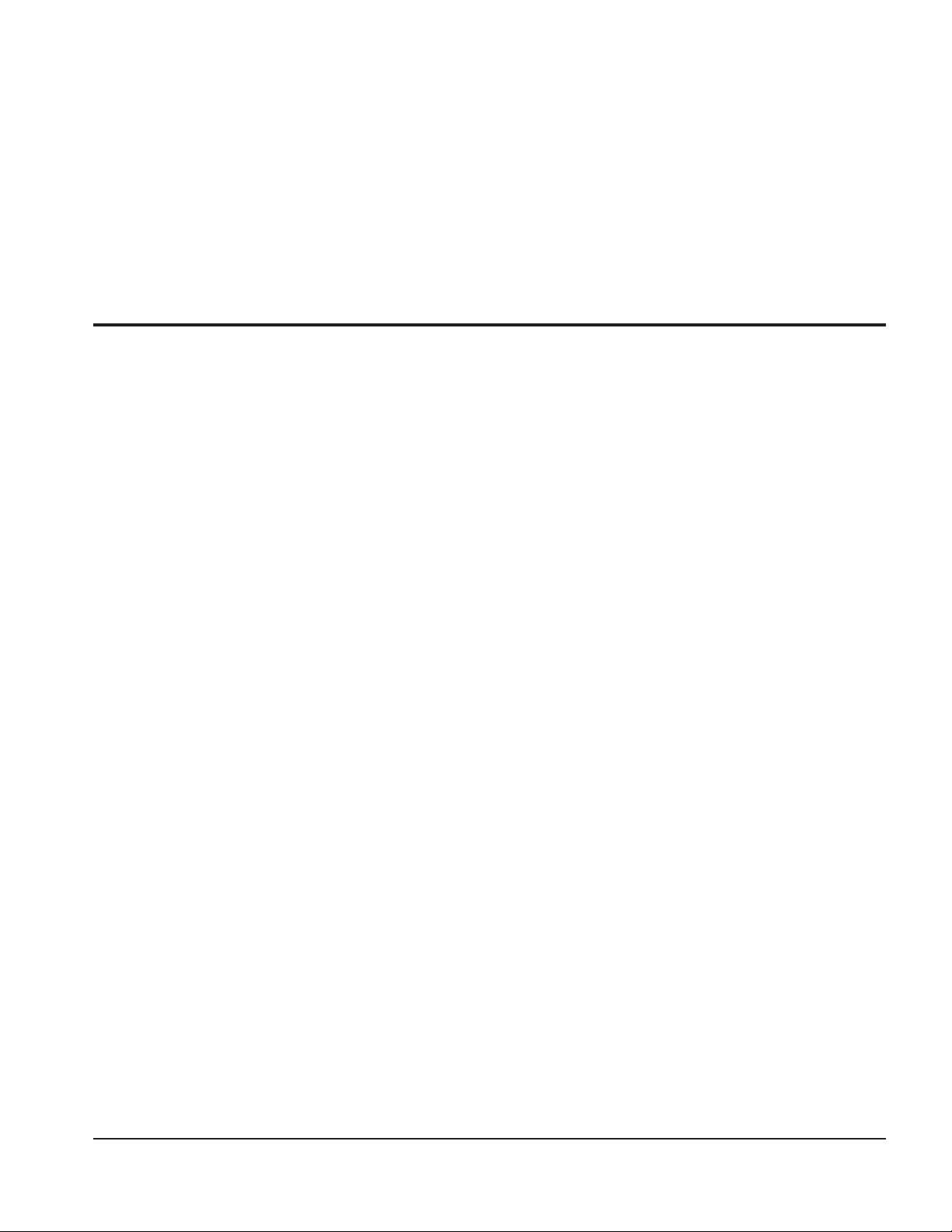
HYPERTHERM Plasmasysteme 1-1
8/06
Abschnitt 1
SICHERHEIT
Inhalt:
Sicherheitsrelevante Informationen ..........................................................................................................................1-2
Sicherheitsvorschriften einhalten..............................................................................................................................1-2
Plasmaschneiden kann Brände und Explosionen verursachen................................................................................1-2
Elektrische Schläge sind lebensgefährlich ...............................................................................................................1-3
Statische elektrizität kann platinen Beschädigen......................................................................................................1-3
Giftige Dämpfe können zu Verletzungen oder tod führen.........................................................................................1-4
Ein Plasmalichtbogen kann Verletzungen und Verbrennungen verursachen...........................................................1-5
Lichtbogenstrahlen können Augen und Haut verbrennen.........................................................................................1-5
Sichere Erdung .........................................................................................................................................................1-5
Sicherheit beim Umgang mit Gasdruckausrüstungen ..............................................................................................1-6
Beschädigte Gasflaschen können explodieren.........................................................................................................1-6
Lärm kann zu Gehörschäden führen ........................................................................................................................1-6
Störung von Herzschrittmachern und Hörgeräten ....................................................................................................1-6
Der Plasmalichtbogen kann gefrorene Rohre beschädigen .....................................................................................1-6
Warnschilder.............................................................................................................................................................1-7

SICHERHEIT
1-2 HYPERTHERM Plasmasysteme
12/15/99
SICHERHEITSRELEVANTE
INFORMATIONEN
Die Symbole in diesem Abschnitt dienen zur Identifizierung
von potentiellen Gefahren. Wenn ein Sicherheitssymbol in
diesem Handbuch erscheint oder eine Maschine damit
gekennzeichnet ist, die angegebenen Anweisungen strikt
einhalten, um potentielle Verletzungsgefahren zu
vermeiden.
SICHERHEITSVORSCHRIFTEN
EINHALTEN
Alle Sicherheitshinweise in diesem Handbuch und die
Warnschilder auf der Maschine durchlesen.
• Die Warnschilder auf der Maschine in gutem Zustand
halten. Fehlende oder beschädigte Schilder sofort
ersetzen.
• Die Bedienung der Maschine und die richtige Verwendung
der Bedienungselemente erlernen. Die Maschine nicht
von ungeschultem Personal bedienen lassen.
• Die Maschine stets in funktionstüchtigem Zustand halten.
Unzulässige Modifikationen der Maschine können die
Sicherheit und Nutzungsdauer der Maschine
beeinträchtigen.
GEFAHR WARNUNG VORSICHT
Die Signalworte GEFAHR bzw. WARNUNG werden
zusammen mit einem Sicherheitssymbol verwendet.
GEFAHR identifiziert die größte Gefahr.
• Die Warnschilder GEFAHR bzw. WARNUNG an der
Maschine befinden sich stets in der Nähe der jeweiligen
Gefahrenstelle.
• Der Sicherheitshinweis WARNUNG ist den
entsprechenden Anweisungen in diesem Handbuch
vorangestellt, die bei Nichteinhaltung zu schweren oder
tödlichen Verletzungen führen können.
• Der Sicherheitshinweis VORSICHT ist den
entsprechenden Anweisungen in diesem Handbuch
vorangestellt, die bei Nichteinhaltung zu
Maschinenschäden führen können.
Brandverhütung
• Sicherstellen, daß im Arbeitsbereich sicher geschnitten
werden kann. Einen Feuerlöscher in unmittelbarer
Umgebung verfügbar halten.
• Alles brennbare Material im Umkreis von 10 m aus dem
Schneidbereich entfernen.
• Heiße Metallteile abschrecken oder abkühlen lassen,
bevor sie weiterverarbeitet werden oder mit brennbaren
Materialien in Berührung kommen.
• Keine Behälter schneiden, die möglicherweise brennbare
Materialien enthalten – sie müssen zuerst entleert und
gründlich gereinigt werden.
• Vor dem Plasmaschneiden möglicherweise
feuergefährliche Bereiche entlüften.
• Beim Schneiden mit Sauerstoff als Plasmagas ist eine
Belüftungsanlage erforderlich.
Explosionsverhütung
• Die Plasmaschneidanlage nicht in Betrieb nehmen, wenn
die Umgebungsluft explosiven Staub oder Gase enthält.
• Keine unter Druck stehenden Zylinder, Rohre oder
geschlossene Behälter schneiden.
• Keine Behälter schneiden, in denen brennbare Materialien
aufbewahrt wurden.
PLASMASCHNEIDEN KANN BRÄNDE UND EXPLOSIONEN VERURSACHEN
WARNUNG
Explosionsgefahr
Argon-Wasserstoff und Methan
Wasserstoff und Methan sind feuergefährliche Gase, die
eine Explosionsgefahr darstellen. Flammen von Behältern
und Schläuchen fernhalten, die Methan- oder WasserstoffMischungen enthalten. Ebenso Flammen und Funken vom
Brenner fernhalten, wenn Methan oder Argon-Wasserstoff
als Plasmagas verwendet wird.
WARNUNG
Wasserstoff-Verpuffung beim
Aluminium-Schneiden
• Beim Unterwasserschneiden von Aluminium oder bei
Wasserberührung der Aluminiumunterseite kann sich
freies Wasserstoffgas unter dem Werkstück sammeln und
während des Plasmaschneidbetriebes verpuffen.
• Einen Belüftungsverteiler am Boden des Wassertisches
installieren, um die Gefahr einer Wasserstoff-Verpuffung
zu beseitigen. Siehe Abschnitt „Anhang“ dieses
Handbuches bezüglich Einzelheiten zum
Belüftungsverteiler.

SICHERHEIT
HYPERTHERM Plasmasysteme 1-3
8/06
Das Berühren stromführender Teile kann tödliche
elektrische Schläge oder schwere Verbrennungen
verursachen.
• Der Betrieb der Plasmaanlage schließt einen elektrischen
Schaltkreis zwischen Brenner und Werkstück. Das
Werkstück und jegliche Teile, die mit dem Werkstück
Kontakt haben, sind Bestandteil des elektrischen
Schaltkreises.
• Brennerkörper, Werkstück oder Wasser im Wassertisch
während des Betriebs der Plasmaanlage nicht berühren.
Verhütung von elektrischen Schlägen
Bei allen Hypertherm-Plasmaanlagen wird im Schneidprozeß Hochspannung eingesetzt (200 bis 400 Volt
Gleichstrom sind üblich). um den Plasmalichtbogen zu
zünden. Folgende Sicherheitsmaßregeln beim Betrieb der
Schneidanlage beachten:
• Isolier-Handschuhe und -Schuhe tragen und Körper und
Kleidung trocken halten.
• Während der Bedienung der Plasmaanlage muß darauf
geachtet werden, daß keine nassen Flächen – auf welche
Weise auch immer – berührt werden.
• Die Isolierung vom Werkstück und Boden mit trockenen
Isoliermatten oder -abdeckungen gewährleisten; diese
müssen groß genug sein, um jeglichen Kontakt mit
Werkstück oder Boden zu verhindern. Äußerst vorsichtig
sein, wenn in einer Umgebung mit hohem
Feuchtigkeitsanteil gearbeitet werden muß.
• Es ist ein Trennschalter mit ausreichend dimensionierten
Sicherungen in der Nähe der Stromquelle anzubringen.
Mit diesem Schalter kann die Anlage im Notfall von der
Bedienperson schnell ausgeschaltet werden.
• Beim Schneiden am Wassertisch ist sicherzustellen, daß
der Schutzleiter korrekt angeschlossen ist.
ELEKTRISCHE SCHLÄGE SIND LEBENSGEFÄHRLICH
• Diese Anlage entsprechend den Anweisungen der
Betriebsanleitung und den nationalen und regionalen
Vorschriften installieren und erden.
• Das Eingangsnetzkabel der Anlage häufig auf eventuelle
Beschädigungen der Isolierung untersuchen. Beschädigte
Kabel sofort ersetzen. Blanke Drähte sind
lebensgefährlich.
• Das Brenner-Schlauchpaket untersuchen und
verschlissene oder beschädigte Kabel austauschen.
• Während des Schneidens dürfen das Werkstück und
sich lösender Schneidabfall nicht aufgehoben werden.
Während des Schneidvorgangs das Werkstück mit
angeschlossenem Werkstückkabel am Platz oder auf
der Werkbank lassen.
• Vor dem Prüfen, Reinigen oder Auswechseln von
Brennerverschleißteilen den Hauptschalter ausschalten
oder den Netzstecker der Stromquelle ziehen.
• Den Sicherheitsschalter am Gerät niemals umgehen
oder außer Kraft setzen.
• Vor dem Abnehmen von Abdeckungen der Stromquelle
oder der Anlage die Eingangsnetzspannung unterbrechen.
Nach dem Unterbrechen der Netzspannung 5 Minuten
lang warten, damit sich die Kondensatoren entladen.
• Die Plasmaanlage niemals mit abgenommener
Stromquellen-Abdeckung in Betrieb nehmen.
Ungeschützte Stromquellenanschlüsse stellen eine
ernsthafte elektrische Gefahr dar.
• Bei der Installation von Netzeingangsanschlüssen zuerst
den Schutzleiter anschließen.
• Hypertherm-Plasmaschneidanlagen dürfen nur mit den
jeweiligen Hypertherm-Brennern verwendet werden.
Keine anderen Brenner verwenden, da diese überhitzen
können und eine Sicherheitsgefahr darstellen.
Beim Umgang mit Leiterplatten sind angemessene
Vorsichtsmaßnahmen zu treffen.
STATISCHE ELEKTRIZITÄT KANN PLATINEN BESCHÄDIGEN
•
Leiterplatten in antistatischen Behältern aufbewahren.
•
Beim Umgang mit Leiterplatten sind geerdete
Gelenkbänder zu tragen.

SICHERHEIT
1-4 HYPERTHERM Plasmasysteme
8/06
Der Plasmalichtbogen selbst ist die beim Schneiden
eingesetzte Wärmequelle. Entsprechend kann das Material,
das geschnitten wird, eine Quelle giftiger Dämpfe oder
Gase darstellen, die Sauerstoff verringern, auch wenn der
Plasmalichtbogen nicht als Quelle giftiger Dämpfe ermittelt
wurde.
Die erzeugten Dämpfe variieren abhängig von dem Metall,
das geschnitten wird. Zu den Metallen, die giftige Dämpfe
freisetzen können, auf die dies aber ist nicht beschränkt ist,
gehören rostfreier Stahl, unlegierter Stahl, Zink (verzinkt)
und Kupfer.
In manchen Fällen kann das Metall mit einer Substanz
beschichtet sein, die giftige Dämpfe freisetzen könnte. Zu
den giftigen Beschichtungen gehören Blei (in manchen
Farben), Kadmium (in manchen Farben und Füllstoffen) und
Beryllium, es ist jedoch nicht auf diese beschränkt.
Die beim Plasmaschneiden erzeugten Gase variieren je
nach dem zu schneidenden Material und dem
Schneidverfahren, dies kann jedoch Ozon, Stickoxide,
sechswertiges Chrom, Wasserstoff und sonstige
Substanzen umfassen, wenn diese im geschnittenen
Material enthalten sind oder von diesem freigesetzt werden.
Es sind Vorsichtsmaßnahmen zu treffen, um bei jeglichen
Betriebsabläufen eine Belastung durch diese Dämpfe zu
minimieren. Abhängig von der chemischen
Zusammensetzung und der Konzentration der Dämpfe
(sowie anderen Faktoren, z. B. Be- und Entlüftung) kann ein
Risiko für körperliche Erkrankungen, z. B. Geburtsfehler
oder Krebs, bestehen.
Es ist die Verantwortung des Ausrüstungs- und
Betriebseigentümers, die Luftqualität des Bereichs, in dem
die Ausrüstung eingesetzt wird, zu überprüfen und
sicherzustellen, dass die Luftqualität am Arbeitsplatz den
regionalen und nationalen Normen und Vorschriften
entspricht.
Das Niveau der Luftqualität an jedem betroffenen
Arbeitsplatz ist abhängig von betriebsspezifischen
Variablen, z. B.:
• Tischkonstruktion (nass, trocken, Unterwasser).
GIFTIGE DÄMPFE KÖNNEN ZU VERLETZUNGEN ODER TOD FÜHREN
• Materialzusammensetzung, Oberflächenbeschaffenheit
und Zusammensetzung der Beschichtungen.
• Menge des zu entfernenden Materials.
• Dauer des Schneidens bzw. Fugenhobelns.
• Größe, Luftvolumen, Be- und Entlüftung und Filtrierung
des Arbeitsbereiches.
• Personenschutzausrüstung.
• Anzahl der sich in Betrieb befindlichen Schweiß- und
Schneidanlagen.
• Sonstige Betriebsabläufe, die Dämpfe erzeugen können.
Muss der Arbeitsplatz nationalen oder regionalen
Vorschriften entsprechen, kann nur durch im Betrieb
vorgenommene Überwachung und Prüfung ermittelt
werden, ob der Betrieb oberhalb oder unterhalb des
zulässigen Niveaus liegt.
Zur Verringerung des Risikos der Belastung durch Dämpfe:
• Vor dem Schneiden alle Beschichtungen und Lösemittel
vom Metall entfernen.
• Vor Ort eine Entlüftung vornehmen, um Dämpfe aus der
Luft zu entfernen.
• Dämpfe nicht einatmen. Beim Schneiden von Metall, das
mit giftigen Elementen beschichtet ist, das solche enthält
oder bei dem der Verdacht besteht, dass es giftige
Elemente enthält, Atemschutzmaske mit Luftzufuhr
tragen.
• Es ist sicherzustellen, dass diejenigen, die Schweiß- oder
Schneidausrüstungen bedienen und
Atemschutzvorrichtungen mit Luftzufuhr einsetzen, für
den ordnungsgemäßen Einsatz solcher Ausrüstungen
qualifiziert und ausgebildet sind.
• Niemals Behälter schneiden, in deren Innerem sich
möglicherweise giftige Materialien befinden. Die Behälter
sind vorher ordnungsgemäß zu entleeren und zu reinigen.
• Die Luftqualität erforderlichenfalls überwachen und
überprüfen.
• Den örtlichen Experten für die Umsetzung eines
Lageplanes zur Gewährleistung einer sicheren
Luftqualität zu Rate ziehen.

SICHERHEIT
HYPERTHERM Plasmasysteme 1-5
05/02
Sofortstartbrenner
Der Plasmalichtbogen wird sofort gezündet, nachdem der
Brennerschalter betätigt wird.
EIN PLASMALICHTBOGEN KANN VERLETZUNGEN UND
VERBRENNUNGEN VERURSACHEN
Der Plasmalichtbogen kann Handschuhe und Haut schnell
verbrennen.
• Von der Brennerspitze fernhalten.
• Metall aus dem Schneidbereich fernhalten.
• Den Brenner niemals auf Personen richten.
Augenschutz Die Strahlung des Plasmalichtbogens
erzeugt starke sichtbare und unsichtbare (ultraviolette und
infrarote) Strahlen, die Augen und Haut verbrennen können.
• Augenschutz entsprechend den zutreffenden nationalen
und regionalen Vorschriften verwenden.
• Augenschutz (Sicherheitsbrillen mit Seitenschutz und ein
Schweißschutzschild) mit entsprechend getönter
Schweißglas-Stufe verwenden, um die Augen vor den
Ultraviolett- und Infrarotstrahlen des Lichtbogens zu
schützen.
Schweißglas-Stufe
Brennerstrom WS (USA) ISO 4850
Bis 100 A Nr. 8 Nr. 11
100-200 A Nr. 10 Nr. 11-12
200-400 A Nr. 12 Nr. 13
Über 400 A Nr. 14 Nr. 14
Hautschutz Schutzkleidung tragen, um die Haut vor UVStrahlung, Funkenflug und heißem Metall zu schützen.
LICHTBOGENSTRAHLEN KÖNNEN AUGEN UND HAUT VERBRENNEN
• Schutzhandschuhe, Sicherheitsschuhe und
Kopfbedeckung tragen.
• Flammverzögerte Kleidung tragen, die eine vollständige
Abdeckung bietet.
• Hosen ohne Umschläge tragen, so daß sich keine Funken
oder Schlacken fangen können.
• Vor dem Schneiden jegliche Brennstoffe, wie z. B.
Feuerzeuge oder Streichhölzer, aus den Taschen
entfernen.
Schneidbereich Den Schneidbereich so gestalten, daß
die Reflektion und Übertragung von ultraviolettem Licht
reduziert wird:
• Wände und andere Oberflächen dunkel anstreichen, um
die Reflektion zu verringern.
• Schutzabschirmungen und Sicherheitstrennwände
installieren, um andere Personen vor grellen
Schneidfunken und Blendlicht zu schützen.
• Andere Personen warnen, nicht in den Lichtbogen zu
schauen. Plakate oder Schilder verwenden.
Werkstückkabel Das Werkstückkabel sicher am Werkstück
oder Arbeitstisch anbringen, indem ein guter Metall-zuMetall-Kontakt hergestellt wird. Das Kabel nicht an Teilen
befestigen, die nach dem Schnitt abfallen.
Arbeitstisch Den Arbeitstisch gemäß den entsprechenden
nationalen oder regionalen Erdungsrichtlinien an einen
Schutzleiter anschließen.
SICHERE ERDUNG
Netzeingang
• Sicherstellen, daß das Schutzleiter des Netzkabels an
den Schutzleiter im Verteilerkasten bzw. im Stecker
angeschlossen ist.
• Ist bei der Installation der Plasmaanlage der Anschluß
des Netzkabels an die Stromquelle erforderlich,
sicherstellen, daß der Schutzleiter des Netzkabels den
Vorschriften entsprechend angeschlossen ist.
• Den Schutzleiter des Netzkabels am Bolzen anbringen.
Die Sicherungsmutter fest anziehen.
• Alle elektrischen Anschlüsse fest anziehen, um
übermäßige Erhitzung zu vermeiden.

SICHERHEIT
1-6 HYPERTHERM Plasmasysteme
2/12/01
• Gasflaschenventile oder Druckregler nicht mit Öl oder Fett
schmieren.
• Nur funktionstüchtige Gasflaschen, Druckregler,
Schläuche und Anschlußstücke verwenden, die für die
jeweilige Anwendung zugelassen sind.
• Alle Gasdruckbehälter und Zubehörteile in
funktionstüchtigem Zustand halten.
• Alle Gasschläuche mit Beschilderungen und
Farbcodierungen versehen, damit der Gastyp in jedem
Schlauch eindeutig identifiziert werden kann. Dabei die
entsprechenden nationalen und regionalen Codierungen
zu Rate ziehen.
BESCHÄDIGTE GASFLASCHEN
KÖNNEN EXPLODIEREN
SICHERHEIT BEIM UMGANG MIT
GASDRUCKAUSRÜSTUNGEN
Gasflaschen enthalten unter hohem Druck stehendes Gas.
Beschädigte Gasflaschen können explodieren.
• Gasdruckbehälter gemäß den entsprechenden nationalen
und regionalen Sicherheitsbestimmungen einsetzen.
• Gasflaschen müssen immer aufrecht stehen und gegen
Umfallen gesichert sein.
• Den Schutzventildeckel nur entfernen, wenn die
Gasflasche eingesetzt oder vor dem Einsatz
angeschlossen wird.
• Zwischen Gasflaschen und Plasmaanlage darf kein
elektrischer Kontakt bestehen.
• Gasflaschen vor übermäßiger Hitze, Funken, Schlacke
oder offenem Feuer schützen.
• Ein festgeklemmtes Gasventil niemals mit einem
Hammer, einer Zange oder anderen Werkzeugen öffnen.
Der Geräuschpegel beim Schneiden oder Fugenhobeln
kann über längere Zeit zu Gehörschäden führen.
• Bei Verwendung der Plasmaanlage stets einen
angemessenen Gehörschutz tragen.
• Andere Personen vor der Lärmgefahr warnen.
LÄRM KANN ZU
GEHÖRSCHÄDEN FÜHREN
Die Funktion von Herzschrittmachern und Hörgeräten kann
durch die Magnetfelder hoher Ströme gestört werden.
Personen, die Herzschrittmacher oder Hörgeräte tragen,
sollten sich vor Arbeiten in der Nähe von Plasmaschneidanlagen, die Schneid- und Fugenhobelarbeiten ausführen,
von ihrem Arzt beraten lassen.
Zur Minimierung von Gefahren durch Magnetfelder:
• Brenner-Schlauchpaket und Werkstückkabel auf einer
Seite verlegen und vom Körper entfernt halten.
• Das Brenner-Schlauchpaket so nahe wie möglich am
Werkstückkabel verlegen.
• Brenner-Schlauchpaket oder Werkstückkabel nicht um
den Körper legen.
• So weit wie möglich von der Stromquelle entfernt bleiben.
STÖRUNG VON HERZSCHRITTMACHERN
UND HÖRGERÄTEN
Gefrorene Rohre können bei dem Versuch, diese mit einem
Plasmabrenner aufzutauen, beschädigt werden oder
bersten.
DER PLASMALICHTBOGEN
KANN GEFRORENE ROHRE
BESCHÄDIGEN
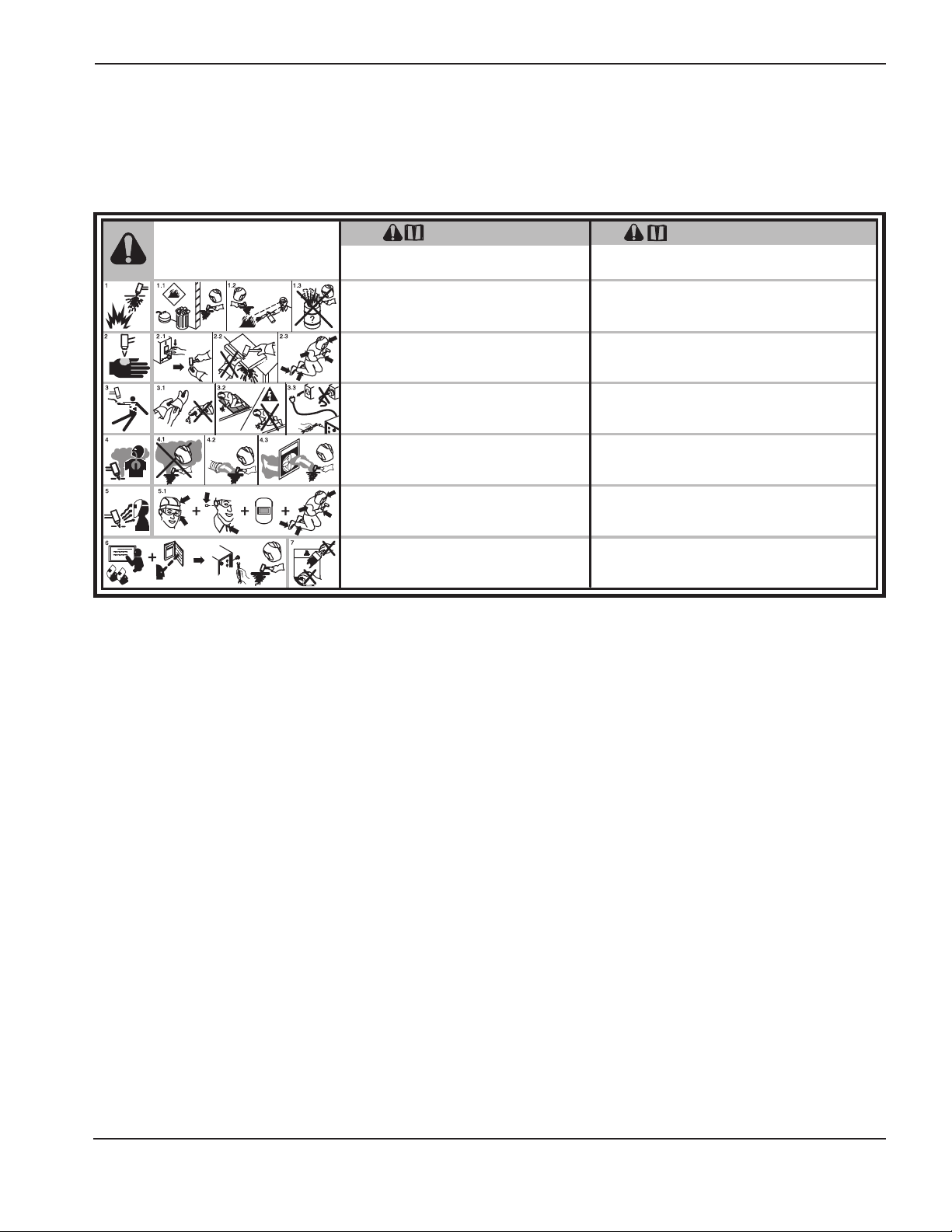
SICHERHEIT
HYPERTHERM Plasmasysteme 1-7
2/12/01
Warnschild
Dieses Warnschild ist an der Stromquelle angebracht. Es ist sehr wichtig, daß der
Bediener und Wartungsmechaniker die Bedeutung der beschriebenen Warnsymbole
kennt. Die Numerierung der Beschreibung entspricht den Ziffern auf dem Schild.
1. Schneidfunken können Explosionen oder Brände
verursachen.
1.1 Brennbares Material beim Schneiden fernhalten.
1.2 Einen Feuerlöscher verfügbar halten und eine zweite
Person mit der Bedienung beauftragen.
1.3 Keine geschlossenen Behälter schneiden.
2. Der Plasmalichtbogen kann Verletzungen und
Verbrennungen verursachen.
2.1 Vor dem Öffnen des Brenners die Stromzufuhr
ausschalten.
2.2 Das Material nicht im Schneidbereich festhalten.
2.3 Komplette Schutzkleidung tragen.
3. Elektrischer Schlag durch schadhaften oder
unsachgemäß verwendeten Brenner – oder blanker
Verkabelung ist lebens
gefärlich. Vor elektrischem Schlag
schützen.
3.1 Isolier-Handschuhe tragen. Keine feuchten oder
beschädigten Handschuhe tragen.
3.2 Isolierung vom Werkstück und Boden gewährleisten.
3.3 Vor Arbeiten an der Anlage das Netzkabel abziehen oder
den Trennschalter ausschalten.
4. Einatmen von Schneidrauch ist gesundheitsschädlich.
4.1 Kopf von Dämpfen fernhalten.
4.2 Dämpfe durch Entlüftungs- oder Absaugsysteme
entfernen.
4.3 Dämpfe durch einen Ventilator entfernen.
5. Lichtbogenstrahlen können die Augen verbrennen und
Haut verletzen.
5.1 Kopfbedeckung und Schutzbrille tragen. Gehörschutz
tragen und Kragenknopf schließen. Schweißschutzschild
mit entsprechend getönter Schweißglas-Stufe
verwenden. Komplette Schutzkleidung tragen.
6. Vor Arbeiten an der Anlage oder vor Schneidarbeiten die
Bedienung der Anlage erlernen und die
Betriebsanleitung lesen.
7. Die Warnschilder nicht entfernen, lackieren oder
anderweitig abdecken.
Read and follow these instructions, employer safety
practices, and material safety data sheets. Refer to
ANS Z49.1, “Safety in Welding, Cutting and Allied
Processes” from American Welding Society
(http://www.aws.org) and OSHA Safety and Health
Standards, 29 CFR 1910 (http://www.osha.gov).
Plasma cutting can be injurious to operator and persons
in the work area. Consult manual before operating. Failure
to follow all these safety instructions can result in death.
1. Cutting sparks can cause explosion or fire.
1.1 Do not cut near flammables.
1.2 Have a fire extinguisher nearby and ready to use.
1.3 Do not use a drum or other closed container as a cutting table.
2. Plasma arc can injure and burn; point the nozzle away
from yourself. Arc starts instantly when triggered.
2.1 Turn off power before disassembling torch.
2.2 Do not grip the workpiece near the cutting path.
2.3 Wear complete body protection.
3. Hazardous voltage. Risk of electric shock or burn.
3.1 Wear insulating gloves. Replace gloves when wet or damaged.
3.2 Protect from shock by insulating yourself from work and ground.
3.3 Disconnect power before servicing. Do not touch live parts.
4. Plasma fumes can be hazardous.
4.1 Do not inhale fumes.
4.2 Use forced ventilation or local exhaust to remove the fumes.
4.3 Do not operate in closed spaces. Remove fumes with ventilation.
5. Arc rays can burn eyes and injure skin.
5.1 Wear correct and appropriate protective equipment to protect
head, eyes, ears, hands, and body. Button shirt collar. Protect ears
from noise. Use welding helmet with the correct shade of filter.
6. Become trained. Only qualified personnel should operate this
equipment. Keep non-qualified personnel and children away.
7. Do not remove, destroy, or cover this label.
Replace if it is missing, damaged, or worn (PN 110584 Rev A).
WARNING
AVERTI SSE ME NT
Le coupage plasma peut être préjudiciable pour l’opérateur et les personnes qui se
trouvent sur les lieux de travail. Consulter le manuel avant de faire fonctionner. Le
non respect des ces instructions de sécurité peut entraîner la mort.
1. Les étincelles de coupage peuvent provoquer une explosion
ou un incendie.
1.1 Ne pas couper près des matières inflammables.
1.2 Un extincteur doit être à proximité et prêt à être utilisé.
1.3 Ne pas utiliser un fût ou un autre contenant fermé comme table de coupage.
2. L’arc plasma peut blesser et brûler; éloigner la buse de soi.
Il s’allume instantanément quand on l’amorce;
2.1 Couper l’alimentation avant de démonter la torche.
2.2 Ne pas saisir la pièce à couper de la trajectoire de coupage.
2.3 Se protéger entièrement le corps.
3. Tension dangereuse. Risque de choc électrique ou de brûlure.
3.1 Porter des gants isolants. Remplacer les gants quand ils sont humides ou
endommagés.
3.2 Se protéger contre les chocs en s’isolant de la pièce et de la terre.
3.3 Couper l’alimentation avant l’entretien. Ne pas toucher les pièces sous tension.
4. Les fumées plasma peuvent être dangereuses.
4.1 Ne pas inhaler les fumées
4.2 Utiliser une ventilation forcée ou un extracteur local pour dissiper les fumées.
4.3 Ne pas couper dans des espaces clos. Chasser les fumées par ventilation.
5. Les rayons d’arc peuvent brûler les yeux et blesser la peau.
5.1 Porter un bon équipement de protection pour se protéger la tête, les yeux, les
oreilles, les mains et le corps. Boutonner le col de la chemise. Protéger les oreilles
contre le bruit. Utiliser un masque de soudeur avec un filtre de nuance appropriée.
6. Suivre une formation. Seul le personnel qualifié a le droit de faire
fonctionner cet équipement. Le personnel non qualifié et les enfants doivent
se tenir à l’écart.
7. Ne pas enlever, détruire ni couvrir cette étiquette.
La remplacer si elle est absente, endommagée ou usée (PN 110584 Rev A).

SICHERHEIT
1-8 HYPERTHERM Plasmasysteme
10/6/98
Warnschild
Dieses Warnschild ist an der Stromquelle angebracht. Es ist sehr
wichtig, daß der Bediener und Wartungsmechaniker die Bedeutung
der beschriebenen Warnsymbole kennt. Die Numerierung der
Beschreibung entspricht den Ziffern auf dem Schild.
1. Schneidfunken können Explosionen oder
Brände verursachen.
1.1 Brennbares Material beim Schneiden
fernhalten.
1.2 Einen Feuerlöscher verfügbar halten und
eine zweite Person mit der Bedienung
beauftragen.
1.3 Keine geschlossenen Behälter schneiden.
2. Der Plasmalichtbogen kann Verletzungen
und Verbrennungen verursachen.
2.1 Vor dem Öffnen des Brenners die
Stromzufuhr ausschalten.
2.2 Das Material nicht im Schneidbereich
festhalten.
2.3 Komplette Schutzkleidung tragen.
3. Elektrischer Schlag durch schadhaften
oder unsachgemäß verwendeten Brenner
– oder blanker Verkabelung ist lebensgefärlich. Vor elektrischem Schlag schützen.
3.1 Isolier-Handschuhe tragen. Keine feuchten
oder beschädigten Handschuhe tragen.
3.2 Isolierung vom Werkstück und Boden
gewährleisten.
3.3 Vor Arbeiten an der Anlage das Netzkabel
abziehen oder den Trennschalter
ausschalten.
4. Einatmen von Schneidrauch ist
gesundheitsschädlich.
4.1 Kopf von Dämpfen fernhalten.
4.2 Dämpfe durch Entlüftungs- oder
Absaugsysteme entfernen.
4.3 Dämpfe durch einen Ventilator entfernen.
5. Lichtbogenstrahlen können die Augen
verbrennen und Haut verletzen.
5.1 Kopfbedeckung und Schutzbrille tragen.
Gehörschutz tragen und Kragenknopf
schließen. Schweißschutzschild mit
entsprechend getönter Schweißglas-Stufe
verwenden. Komplette Schutzkleidung
tragen.
6. Vor Arbeiten an der Anlage oder vor
Schneidarbeiten die Bedienung der Anlage
erlernen und die Betriebsanleitung lesen.
7. Die Warnschilder nicht entfernen, lackieren
oder anderweitig abdecken.
Rev. D

powermax30 Wartungshandbuch 2-1
Abschnitt 2
SPEZIFIKATIONEN
Inhalt:
Stromquelle...............................................................................................................................................................2-2
Abmessungen und Gewicht .............................................................................................................................2-2
T30v Brennerwerte ...................................................................................................................................................2-3
Abmessungen ..................................................................................................................................................2-3
Symbole und Markierungen......................................................................................................................................2-4
-Zeichen ......................................................................................................................................................2-4
CE-Zeichen ......................................................................................................................................................2-4
IEC-Zeichen .....................................................................................................................................................2-4

SPEZIFIKATIONEN
2-2 powermax30 Wartungshandbuch
Stromquelle
Nennleerlaufspannung (U0) 240 VDC
Nennausgangsstrom (I2) 15 A bis 30 A
Nennausgangsspannung (U2) 83 VDC
Einschaltdauer bei 40° C, U1=120 VAC 35 % (I2 = 30 A, U2 = 83 V)
(Siehe Typenschild auf der Stromquelle 60 % (I2 =2 3 A, U2 = 83 V)
bezüglich weiterer Informationen zu 100 % (I2 = 18 A, U2 = 83 V)
Einschaltdauer und IEC-Werten.)
Einschaltdauer bei 40° C, 50 % (I2 = 30 A, U2 = 83 V)
U1=200–240 VAC 75 % (I2 = 24 A, U2 = 83 V)
100 % (I2 = 21 A, U2 = 83 V)
Betriebstemperatur -10° bis 40° C
Lagertemperatur -25° bis 55° C
Leistungsfaktor (120 V – 240 V) 0,99 – 0,97
Eingangsspannung (U1)/ Eingangsstrom (I1) 120 V / 26 A
bei Nennleistung (U
2 MAX
, I
2 MAX
) 200-240 V / 15,5-13 A
Gas Luft Stickstoff
Gasqualität Sauber, trocken, ölfrei 99,995 % rein
Mindestens erforderlicher Gaseinlassdruck und Durchfluss 99,1 l/min bei 4,5 bar
Empfohlener Gaseinlassdurchfluss und -druck 113,3 l/min bei 5,5 bar
Abmessungen und Gewicht
Das Gewicht umfasst den
Handbrenner und die 4,57 m
lange Leitung.
9,37 kg
330 mm
140 mm
267 mm
292,1 mm

SPEZIFIKATIONEN
2-4 powermax30 Wartungshandbuch
O
l
Symbole und Markierungen
S -Zeichen
Die -Zeichen bedeutet, daß die Stromquelle und der Brenner in Bereichen mit erhöhter elektrischer
Gefährdung
verwendet werden dürfen.
CE-Zeichen
Das CE-Zeichen ( ) stellt eine Konformitätserklärung des Herstellers mit allen geltenden europäischen
Richtlinien und Standards dar. Nur diejenigen Ausführungen an Hypertherm-Produkten mit einem CE-Zeichen auf
oder nahe dem Datenschild wurden auf Einhaltung der Europäischen Niederspannungs-Richtlinie und der
Europäischen EMV-Richtlinie geprüft. Die zur Befolgung der Europäischen EMV-Richtlinie erforderlichen
EMV-Filter sind in den Stromquellenausführungen mit CE-Zeichen eingebaut.
IEC-Zeichen
Die folgenden Symbole können auf dem Datenschild der Stromquelle, den Reglerbeschriftungen, Schaltern und LEDs
erscheinen.
Gleichstrom (DC)
Anschluß für den
externen Schutzleiter
(geerdet)
Wechselstromanschluß
Schneiden mit dem
Plasmabrenner
Wechselstrom (AC)
Stromquelle auf InverterBasis
Strom ausgeschaltet
Strom eingeschaltet
Strom steht auf EIN (LED)
Einlassgasdruck ist
niedrig
Fehlende oder lose
Verschleißteile
Stromquelle ist überhitzt
Volt/Ampere-Kurve,
fallende Kennlinie
1~
f
1
f
2
AC

powermax30 Wartungshandbuch 3-1
Abschnitt 3
WARTUNG
Inhalt:
Regler und Anzeigeleuchten.....................................................................................................................................3-2
Bedienelemente an der Vorderseite und LEDs................................................................................................3-2
Bedienelemente auf der Rückseite ..................................................................................................................3-2
Theorie des Betriebs.................................................................................................................................................3-3
Allgemeines......................................................................................................................................................3-3
Funktionsbeschreibung ....................................................................................................................................3-3
Betriebsablauf ..................................................................................................................................................3-4
Vorbereitung für die Fehlerbeseitigung.....................................................................................................................3-5
Testausrüstung.................................................................................................................................................3-5
Verfahren und Ablauf bei der Fehlerbeseitigung ..............................................................................................3-5
Untersuchung – außen.....................................................................................................................................3-5
Untersuchung – innen ......................................................................................................................................3-6
Anfangswiderstandsprüfung .....................................................................................................................................3-7
Stromquellenübersicht ..............................................................................................................................................3-8
Richtschnur zur Fehlerbeseitigung ...........................................................................................................................3-9
Steuerbaukarten-LEDs ...........................................................................................................................................3-12
Verwendung der Steuerbaukarten-Fehler- und Neustart-LEDs zur Fehlerbeseitigung..................................3-13
Gerätetests .............................................................................................................................................................3-14
Test 1 – Netzspannung ..................................................................................................................................3-15
Test 2 – Strombaukarten-Spannungsprüfungen ............................................................................................3-16
Test 3 – VBUS und Spannungsgleichgewicht ................................................................................................3-17
Test 4 – Magnetventil .....................................................................................................................................3-18
Test 5 – Brenner klemmt in offenem Zustand ................................................................................................3-19
Test 6 – Plasmastart.......................................................................................................................................3-20
Test 7 – Brennerkappensensor ......................................................................................................................3-20
Test 8 – Lüfter ................................................................................................................................................3-21
Test 9 – Druckschalter....................................................................................................................................3-21
Komponentenaustausch .........................................................................................................................................3-22
Entfernen einer Endkappe .............................................................................................................................3-22
Austausch der Brennerleitung........................................................................................................................3-24
Austausch des Werkstückkabels ...................................................................................................................3-26
Austausch des Netzkabels (CSA) ..................................................................................................................3-27
Austausch des Netzkabels (CE) ....................................................................................................................3-28
Austausch des Lüfters....................................................................................................................................3-30
Austausch des Luftfilterelements ...................................................................................................................3-31
Austausch von Luftfilter und Regler ...............................................................................................................3-32
Austausch der Steuerbaukarte.......................................................................................................................3-33
Austausch der Strombaukarte........................................................................................................................3-34
Austausch des Bodens ..................................................................................................................................3-37

WARTUNG
3-2 powermax30 Wartungshandbuch
Regler und Anzeigeleuchten
Das Powermax30 hat einen EIN/AUS-Kippschalter, einen Stromregler-Drehknopf und vier Anzeige-LEDs, die
nachfolgend beschrieben werden.
Bedienelemente auf der Rückseite
EIN (I)/AUS (O)-Netzschalter
Aktiviert die Stromquelle und ihre
Steuerstromkreise.
Strom-EIN-LED (grün)
Wenn sie leuchtet, zeigt diese LED an, dass der
Stromschalter in Stellung I (EIN) gebracht worden
ist und dass die Sicherheitsschalter
zufriedengestellt sind.
Gasdruck-LED (gelb)
Wenn diese LED leuchtet, zeigt dies an, dass der
Gasdruck unter 2,8 Bar liegt. Dieser Umstand ist
zu korrigieren, bevor der Betrieb fortgesetzt wird.
Brennerkappen-LED (gelb)
Wenn diese LED leuchtet, zeigt dies an, dass die
Verschleißteile lose sind, nicht ordnungsgemäß
installiert sind oder fehlen.
Bedienelemente an der Vorderseite und LEDs
Temperatur-LED (gelb)
Wenn diese LED leuchtet, zeigt dies an, dass die
Temperatur der Stromquelle außerhalb
des akzeptablen Betriebstemperaturbereiches
liegt.
Stromregelknopf
Dieser Knopf dient der Einstellung des
Ausgangsstroms zwischen 15 und 30 A. Für den
Einsatz bei 120 V und einem 15 A-Schaltkreis ist
dieser auf 20 oder niedriger einzustellen (durch
den dunkleren Bereich um den Knopf herum
dargestellt).
Vorderseite
Rückseite
Einige Fehlerbedingungen verursachen, dass eine oder mehrere LEDs blinken. Für Informationen darüber, um
welche Fehlerbedingungen es sich handelt und wie man sie korrigiert, siehe
Grundlegende Fehlerbeseitigung
in
diesem Abschnitt.
A
15
120V
A
20
120V
A
0
2
240V
AC
I
O

WARTUNG
powermax30 Wartungshandbuch 3-3
Theorie des Betriebs
Allgemeines
Siehe
Funktionsbeschreibung
und
Betriebsabfolge
in diesem Abschnitt sowie in Abschnitt 5 Verdrahtungsdiagramme.
Funktionsbeschreibung
Wechselstrom tritt über den Netzschalter (S1) zur Eingangsdiodenbrücke (D24,30) in die Anlage ein. Die Spannung
von der Diodenbrücke versorgt den Leistungsfaktor-Kompensations (PFC)-Spannungserhöhungsumsetzer, der
eine 375 V=-Sammelschienenspannung liefert. Die Busspannung versorgt den Inverter und die RückkopplungsSchaltkreis-Stromquelle (DC-DC-Umwandler) auf der Strombaukarte (PCB2) mit Spannung und Strom. Die
Strombaukarte sorgt für die Geräuschunterdrückung und den Schutz vor Spannungsspitzen. Ein „Softstart” wird
über den Strombaukartenwiderstand und das Relais (K1) realisiert.
Der PFC-Spannungserhöhungsumsetzer besteht aus einem isolierten bipolaren-Gate-Transistor (IGBT Q1), dem
Drosselwiderstand und einem Steuerschaltkreis. Er liefert eine 375 V-Gleichstromsammelschienenspannung, wenn
die Wechselstrom-Netzspannung zwischen 120 und 240 VAC liegt.
Der Wechselrichter besteht aus einem IGBT (Q2), dem Stromtransformator, einem Stromabtasttransformator und
Abschnitten auf der Strombaukarte. Der Inverter arbeitet als pulsbreitenmodulatorgesteuerte Brückenschaltung und
wird von der Ausgangsdiode (D27) gleichgerichtet.
Die Ausgangsschaltung besteht aus 2 Stromsensoren, die sich auf der Strombaukarte, dem Pilotlichtbogen-IGBT
(im Modul D27) und der Ausgangsdrossel befinden.
Der Mikroprozessor der Steuerbaukarte überwacht und reguliert den Betrieb der Anlage und der
Sicherheitsschaltkreise. Der Stromregler-Drehknopf wird zum Einstellen des Ausgangsstroms auf den
gewünschten Wert zwischen 15 und 30 A verwendet. Die Anlage vergleicht den Einstellpunkt mit dem
Ausgangsstrom, indem sie den Stromsensor überwacht und den Pulsweitenausgang des Inverters IGBT (Q2)
anpasst.

WARTUNG
3-4 powermax30 Wartungshandbuch
Betriebsablauf
Netzstrom AUS
• Gaszufuhr an den Luftanschluss der Stromquelle
anschließen.
• Werkstückkabel am Werkstück anschließen.
• Stromzufuhr am Hauptschaltkasten herstellen.
• EIN/AUS-Schalter (S1) auf EIN (I) schalten.
Stromschalter (S1) auf AUS (O)
stellen.
• Das Gasmagnetventil (V1) schließt.
• Der Gasdurchfluss wird gestoppt.
• Der Lichtbogen erlischt.
• Die Nachströmung erfolgt
20 Sekunden lang.
• Um einen Schnitt vorzunehmen, den
Brenner leicht über das Werkstück ziehen.
• Das Werkstück fällt nach dem Schnitt
herunter.
• Plasmastart-Wippentaster am
Handbrenner loslassen.
• Das Gasmagnetventil (V1) öffnet.
• Der Gasdurchfluss startet.
• Der Schneidlichtbogen startet.
• Brenner auf dem Werkstück positionieren.
• Plasmastart-Wippentaster am Brenner betätigen.
Die Stromschaltkreise sind bereit.
• Stromregler-Drehknopf auf den gewünschten Ausgangsstromwert
einstellen (zwischen 15 und 30 A) basierend auf der
Eingangsspannung und der Schaltkreisgröße.
• Die grüne Strom EIN-LED leuchtet und zeigt damit an,
dass das Gerät betriebsbereit ist.
• Alle Fehler-LEDs sollten erloschen sein (siehe Richtschnur
zur Fehlerbeseitigung für weitere Informationen).

WARTUNG
powermax30 Wartungshandbuch 3-5
Vorbereitung für die Fehlerbeseitigung
Die Komplexität der Schaltkreise macht erforderlich, dass Servicetechniker Grundkenntnisse über die Theorie der
Inverterstromquellen haben. Zusätzlich zur technischen Qualifikation müssen Techniker sämtliche Tests unter
Berücksichtigung der Sicherheit durchführen.
Wenn während der Wartung Fragen oder Probleme auftauchen, bitte mit dem vorn im Handbuch aufgelisteten
Technische Dienste-Team von Hypertherm in Verbindung setzen.
Testausrüstung
• Multimeter mit einer Auswahl von Überbrückungskabeln, einschließlich E-Z Hooks®.
Verfahren und Ablauf bei der Fehlerbeseitigung
Beim Durchführen von Verfahren zur Fehlerbeseitigung
• Abschnitt 1,
Sicherheit,
lesen.
• Siehe Abschnitt 5 bezüglich des elektrischen Schaltplans des Gerätes.
• Siehe Abschnitt 4 zur Bestimmung der Anordnung von Stromquellen- und Brenner-Komponenten.
Nachdem der Fehler gefunden und repariert worden ist, siehe
Betriebsablauf
-Flussdiagramm in diesem Abschnitt,
um den korrekten Betrieb der Stromquelle zu testen.
Externe Untersuchung
1. Äußeres der Stromquelle auf Beschädigungen an der Abdeckung und den äußeren Komponenten, z. B.
Netzkabel und Stecker, untersuchen.
2. Brenner und Brennerschlauchpaket auf Schäden untersuchen.
Strom AUS und unterbrochen
Untersuchung außen
Strom EIN
Untersuchung innen
Widerstandsprüfungen
Richtschnur zur
Fehlerbeseitigung
Tests zur Fehlerbeseitigung

WARTUNG
3-6 powermax30 Wartungshandbuch
GEFAHR
ELEKTRISCHE SCHLÄGE KÖNNEN TÖDLICH SEIN
• Stromzufuhr abschalten und Netzstecker aus der Steckdose ziehen, bevor die Abdeckung
von der Stromquelle abgenommen wird. Ist die Stromquelle direkt an einen Hauptschalter
angeschlossen, ist der Hauptschalter auf AUS (O) umzuschalten. In den USA ist ein
Verriegelungs- und Kennzeichnungsverfahren zu verwenden, bis der Service bzw. die
Wartungsarbeiten abgeschlossen sind. In anderen Ländern sind die nationalen bzw.
örtlichen Sicherheitsverfahren zu befolgen.
• Keine unter Strom stehenden elektrischen Teile berühren! Wenn für die Wartung Strom
benötigt wird, ist bei der Arbeit in der Nähe von unter Strom stehenden elektrischen
Schaltkreisen äußerst vorsichtig vorzugehen. Es können gefährliche Spannungen innerhalb
der Stromquelle vorhanden sein, die schere Verletzungen oder Tod herbeiführen können.
• Es darf nicht versucht werden, die Strom-Baukarte oder Steuer-Baukarte zu reparieren.
Nicht den Schutzschichtüberzug von den Baukarten wegschneiden. Erfolgt dies, riskiert
man Kurzschlüsse zwischen dem Wechselstrom-Eingangsschaltkreis und dem
Ausgangsschaltkreis, was zu ernsten Verletzungen oder Tod führen kann.
HEISSE TEILE KÖNNEN SCHWERE VERBRENNUNGEN VERURSACHEN
• Stromquelle vor der Wartung abkühlen lassen.
SICH BEWEGENDE VENTILATOREN KÖNNEN VERLETZUNGEN VERURSACHEN
• Hände von beweglichen Teilen fernhalten.
STATISCHE ELEKTRIZITÄT KANN SCHALTKARTEN BESCHÄDIGEN
• Vor dem Umgang mit PC-Baukarten geerdetes Band am Handgelenk anlegen.
Interne Untersuchung
1. EIN/AUS-Schalter (S1) auf O (AUS) stellen, Netzkabel aus der Steckdose ziehen und Gaszufuhr unterbrechen.
2. Mit einem Kreuzschraubenzieher Nr. 2 die 2 Schrauben vom Griff der Stromquelle entfernen. Endkappen leicht
zurückneigen, so dass sich die Griffkanten unter den Endkappen herausnehmen lassen. Griff entfernen und
dann die Abdeckung von der Stromquelle abheben.
3. Es befindet sich eine Nomex®-Isolierung zwischen der Abdeckung und der Strombaukarte. Isolierung aus der
Stromquelle herausheben und zur Seite legen. Es ist darauf zu achten, dass die Isolierung nach Beendigung
der Arbeiten an der Stromquelle wieder eingebaut wird.
4. Das Innere der Stromquelle untersuchen, insbesondere die Seite mit der Strombaukarte. Es ist nach
gebrochenen oder losen Verdrahtungsanschlüssen, Brand- und Schmorflecken, beschädigten Bauteilen etc.
zu schauen. Reparieren oder austauschen, je nach Erfordernis.

WARTUNG
powermax30 Wartungshandbuch 3-7
74.5 kΩ
3. Widerstand von den Eingangsleitungen zur Erdung überprüfen, um nachzuprüfen, ob diese als unterbrochen
anzeigt.
Anmerkung: EIN/AUS-Schalter (S1) bei unterbrochener Stromzufuhr auf AUS (O) stellen, es sollte alles als
unterbrochen anzeigen.
Der angezeigte elektrische Wert beträgt ± 25 %.
Wenn bei der Sichtkontrolle oder bei der Anfangs-Widerstandsüberprüfung keine Probleme gefunden wurden und
die Stromquelle noch immer nicht einwandfrei arbeitet, siehe R
ichtschnur zur Fehlerbeseitigung.
Anmerkung: Die
Anleitung zur Fehlerbeseitigung
nennt die wahrscheinlichsten Ursachen und Lösungen.
Lesen Sie das Anlagen-Verdrahtungsdiagramm und verstehen Sie die Theorie des Betriebes,
bevor Sie die Fehlerbeseitigung vornehmen. Überprüfen Sie vor dem Kauf einer größeren
Ersatzkomponente das Problem noch einmal zusammen mit dem Technischen Service von
Hypertherm oder der nächstgelegenen Hypertherm-Reparaturstelle.
Anfangswiderstandsprüfung
Alle Widerstandswerte müssen mit unterbrochenem Netzkabel und allen internen Stromquellendrähten befestigt
vorgenommen werden.
Untersuchung – innen
durchführen, bevor in diesem Abschnitt weitergemacht wird.
• Wenn die Widerstandswerte nicht annähernd den in diesem Abschnitt angegebenen Werten (±25 %)
entsprechen, ist das Problem durch Entfernen der an den Widerstandsprüfpunkten bzw. Komponenten
angebrachten Drähte einzugrenzen, bis das Problem gefunden wurde.
• Nachdem das Problem gefunden und repariert wurde, siehe das Flussdiagramm Betriebsabfolge in diesem
Abschnitt, um die Stromquelle auf ordnungsgemäßen Betrieb zu testen.
1. Bei unterbrochener Stromzufuhr EIN/AUS-Schalter (S1) auf EIN (I) stellen.
2. Widerstand durch die Eingangsleitungen prüfen.
Schwarz (CSA), Braun (CE)
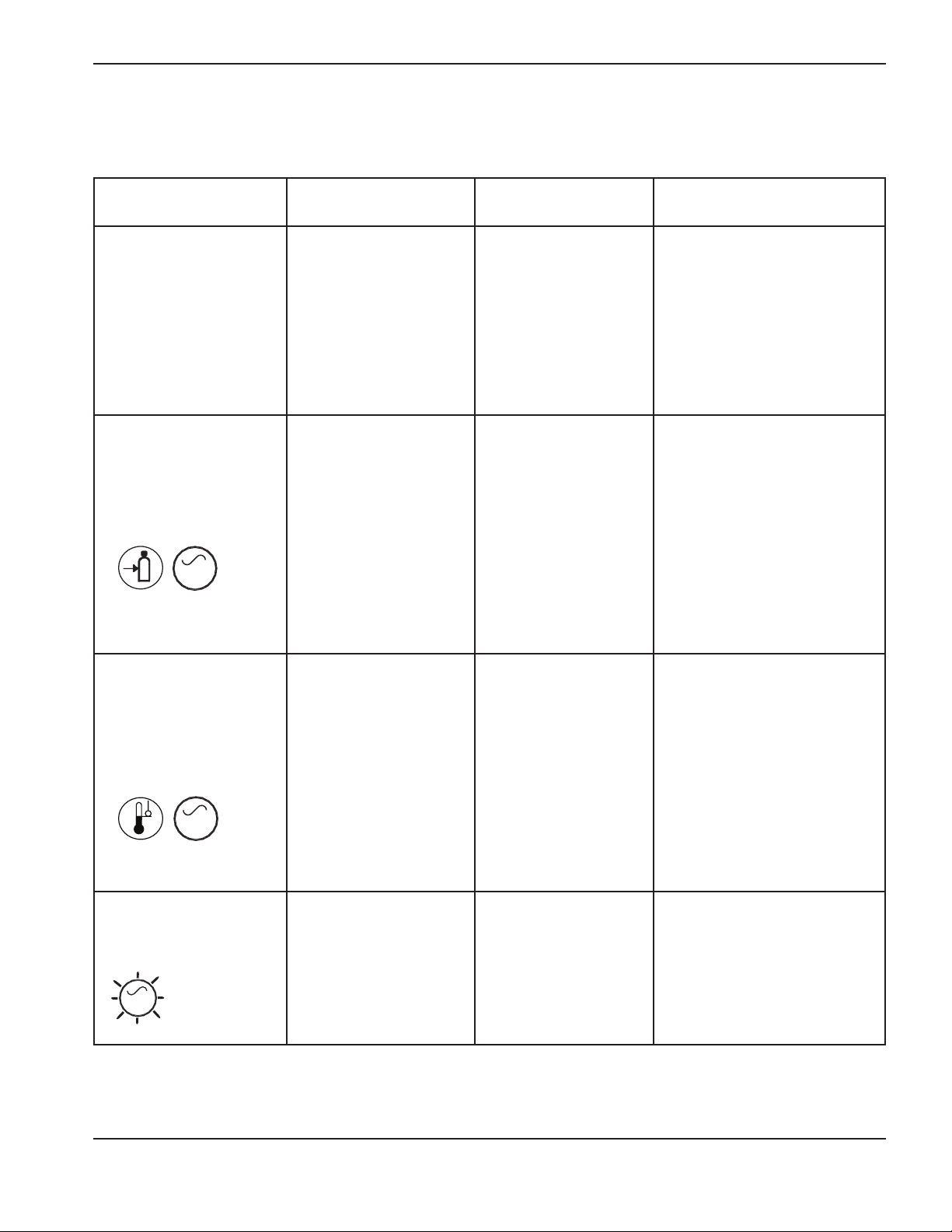
WARTUNG
powermax30 Wartungshandbuch 3-9
Anleitung zur Fehlerbeseitigung
Siehe Anlagentests an späterer Stelle in diesem Abschnitt bezüglich detaillierter Testverfahren.
Problem
Dies kann
folgendes bedeuten Ursache Abhilfe
Der EIN/AUS-Netzschalter
wurde in Stellung EIN (I)
gebracht, aber die Strom
EIN-LED leuchtet nicht.
Es besteht nicht
genügend Spannung zu
den Steuerschaltkreisen
oder eine
Stromkomponente hat
einen Kurzschluss.
• Das Gerät hat keine
oder eine inkorrekte
Netzspannung.
• Die Strombaukarte ist
fehlerhaft.
• Es ist zu überprüfen, ob das
Gerät an einen angemessen
dimensionierten Schaltkreis
angeschlossen und der
Schalter nicht abgeschaltet
ist.
• Test 1 durchführen, um die
Netzspannung und den
Netzschalter zu überprüfen.
Strom-EIN-LED und
Gasdruck-LED leuchten.
Der Gasdruck zur
Maschine ist
ungenügend.
• Es ist am Gerät kein
Gas angeschlossen.
• Die Gaszufuhrleitung
hat eine Verengung
oder das
Luftfilterelement ist
verschmutzt.
• Der Druckwächter
zeigt nicht mindestens
2,8 Bar auf der
Gaszufuhrleitung an.
• Sicherstellen, dass die
Gaszufuhr korrekt
angeschlossen ist.
• Gaszufuhrleitung auf
Verengungen oder
Beschädigungen überprüfen.
• Luftfilterelement überprüfen
und bei Bedarf austauschen.
• Test 9 durchführen, um
nachzuprüfen, ob der
Druckwächter
ordnungsgemäß funktioniert.
Die Strom-EIN-LED und
die Temperatur-LED
leuchten.
Das Gerät ist überhitzt.
• Die Einschaltdauer
wurde überschritten.
(Für weitere
Informationen über die
Einschaltdauer siehe
Abschnitt 4 der
Powermax30Betriebsanleitung.)
• Bereich um das Gerät herum
prüfen, um sicherzustellen,
dass der Luftstrom nicht
behindert ist.
• Wurde die Einschaltdauer
überschritten, Gerät erst
abkühlen lassen, bevor es
wieder eingesetzt wird.
• Test 8 durchführen, um
sicherzustellen, dass der
Lüfter ordnungsgemäß
funktioniert.
Die Strom-EIN-LED blinkt.
Die Netzspannung ist
nicht korrekt.
• Die Netzspannung
liegt unter 90 VAC
oder über 285 VAC.
• Test 1 durchführen, um die
ankommende Netzspannung
zu überprüfen.
AC
AC
AC

WARTUNG
3-10 powermax30 Wartungshandbuch
Problem
Dies kann
folgendes bedeuten Ursache Abhilfe
Die Strom-EIN-LED und
die Brennerkappen-LED
leuchten.
Der Kappensensor-Sch
altkreis ist nicht
zufriedengestellt.
• Die Verschleißteile
sind lose, inkorrekt
installiert oder fehlen
ganz.
• Der Kappensensorschalter ist fehlerhaft.
• Verschleißteile
ordnungsgemäß installieren.
• Test 7 durchführen, um den
Kappensensorschalter zu
überprüfen.
Die Strom-EIN-LED
leuchtet und die
Brennerkappen-LED
blinkt.
Die Verschleißteile
klemmen in offener oder
geschlossener Stellung,
oder Düse und Elektrode
berühren sich nicht, wenn
der Wippentaster des
Brenners betätigt wird.
• Die Verschleißteile
sind nicht
ordnungsgemäß
installiert oder
abgenutzt.
• Der Brennerkolben
klemmt.
• Der Brenner oder die
Leitung hat einen
gebrochenen Draht.
• Verschleißteile auf Abnutzung
überprüfen und bei Bedarf
austauschen. Es ist
sicherzustellen, dass sie
ordnungsgemäß installiert
sind.
• Test 5 durchführen und
Brennerkopf bei Bedarf
austauschen.
Die Gasdruck- und
Temperatur-LEDs blinken,
wenn die Maschine in EINStellung geschaltet wird.
Das Gerät wurde
eingeschaltet, während
das Plasmastartsignal
gesendet wurde.
• Das Gerät wurde
eingeschaltet,
während der BrennerWippentaster betätigt
wurde.
• Der Startschaltkreis
klemmt in
geschlossenem
Zustand.
• Brenner-Wippentaster
loslassen und Stromquelle in
AUS-Stellung bringen und
dann wieder in EIN-Stellung
bringen, um das Gerät
zurückzusetzen.
• Test 6 durchführen, um das
Startsignal zu überprüfen.
Alle vier LED blinken,
wenn das Gerät
eingeschaltet wird.
Ein bedeutender Fehler
ist in der Stromquelle
aufgetreten.
• Es können sowohl der
Lüfter, das
Magnetventil, die
Steuerbaukarte oder
die Strombaukarte
fehlerhaft sein.
• Die Fehler-LED auf der
Steuerbaukarte sollte blinken.
Wie oft sie zwischen den
Pausen blinkt, bestimmt,
welche Komponenten zu
testen sind. Siehe
Steuerbaukarten-LEDs in
diesem Abschnitt.
Die Strom-EIN-LED
leuchtet und keine FehlerLEDs leuchten, aber es
strömt kein Gas, wenn der
Brenner-Wippentaster
betätigt wird.
Das Startsignal erreicht
die Steuerbaukarte nicht.
• Der Brenner oder die
Brennerleitung kann
beschädigt sein.
• Die Strombaukarte
kann fehlerhaft sein.
• Die Steuerbaukarte
kann fehlerhaft sein.
• Brenner und Brennerleitung
auf Beschädigungen
untersuchen.
• Nachprüfen, ob die Start-LED
der Steuerbaukarte leuchtet,
wenn der Wippentaster
betätigt wird. Ist das nicht der
Fall, Test 6 durchführen, um
das von der Strombaukarte
kommende Startsignal zu
überprüfen.
Anleitung zur Fehlerbeseitigung (Fortsetzung)
AC
AC

WARTUNG
powermax30 Wartungshandbuch 3-11
Problem
Dies kann
folgendes bedeuten Ursache Abhilfe
Gas strömt, wenn das
Gerät in EIN-Stellung
geschaltet wird. Der Eingangsgasdruck ist
zu hoch.
• Der vom Kompressor
oder von der
Gasflasche
kommende Gasdruck
kann zu hoch sein.
• Das Gasmagnetventil
kann fehlerhaft sein.
• Gaszufuhr überprüfen, um
sicherzustellen, dass sie
9,3 Bar nicht überschreitet.
Bei Bedarf Druck reduzieren.
• Test 4 durchführen, um zu
überprüfen, ob das
Gasmagnetventil einwandfrei
funktioniert.
Beim Betätigen des
Brenner-Wippentasters
strömt Gas aus dem
Brenner, aber der Brenner
zündet nicht oder zündet
nur für kurze Zeit.
Verschleißteile, Brenner
oder Brennerleitung
funktionieren nicht
einwandfrei. Der
Gasdruck kann zu niedrig
sein, oder es besteht ein
Spannungsungleichgewicht auf der
Strombaukarte.
• Die Verschleißteile
können abgenutzt
oder beschädigt sein.
• Der Brenner oder die
Brennerleitung kann
beschädigt sein.
• Der Gasdruck ist zu
niedrig oder die
Gaszufuhr ist verengt.
• Die Strombaukarte ist
fehlerhaft.
• Verschleißteile, Brenner und
Leitung untersuchen. Bei
Bedarf beschädigte Teile
austauschen.
• Nachprüfen, ob die Gaszufuhr
mindestens 4,5 Bar liefert.
Jegliche Verengungen in der
Zufuhrleitung beheben.
• Test 3 durchführen, um das
Spannungsgleichgewicht auf
der Strombaukarte zu
überprüfen.
Der Lichtbogen erlischt
während des Schneidens
oder setzt zwischendurch
aus.
Der Lichtbogen hat den
Kontakt zum Werkstück
verloren.
• Das Werkstückkabel
oder der Werkstückkabelanschluss kann
fehlerhaft sein.
• Auf lose Verbindungen an der
Werkstückklemme und an der
Stromquelle überprüfen.
• Werkstückkabel erneut am
Werkstück anbringen.
• Schnittfläche reinigen, um
eine bessere Verbindung mit
dem Werkstückkabel
sicherzustellen.
Beim Betätigen des
Brenner-Wippentasters
startet der Pilotlichtbogen,
aber er erlischt vor Ablauf
der 5-SekundenZeitabschaltungsfrist.
Verschleißteile, Brenner
oder Brennerleitung
funktionieren nicht
einwandfrei, der
Gasdruck kann zu niedrig
sein, die Luftqualität kann
schlecht sein, oder es
besteht ein
Spannungsungleichgewicht auf der
Strombaukarte.
• Der Brenner oder die
Brennerleitung kann
beschädigt sein.
• The torch or torch lead
may be damaged.
• Der Gasdruck ist zu
niedrig oder die
Gaszufuhr ist verengt.
• Das Luftfilterelement
ist verschmutzt.
• Die Strombaukarte ist
fehlerhaft.
• Verschleißteile, Brenner und
Leitung untersuchen. Bei
Bedarf beschädigte Teile
austauschen.
• Nachprüfen, ob die Gaszufuhr
mindestens 4,5 Bar liefert.
Jegliche Verengungen in der
Zufuhrleitung beheben.
• Test 3 durchführen, um das
Spannungsgleichgewicht auf
der Strombaukarte zu
überprüfen.
Anleitung zur Fehlerbeseitigung (Fortsetzung)
AC
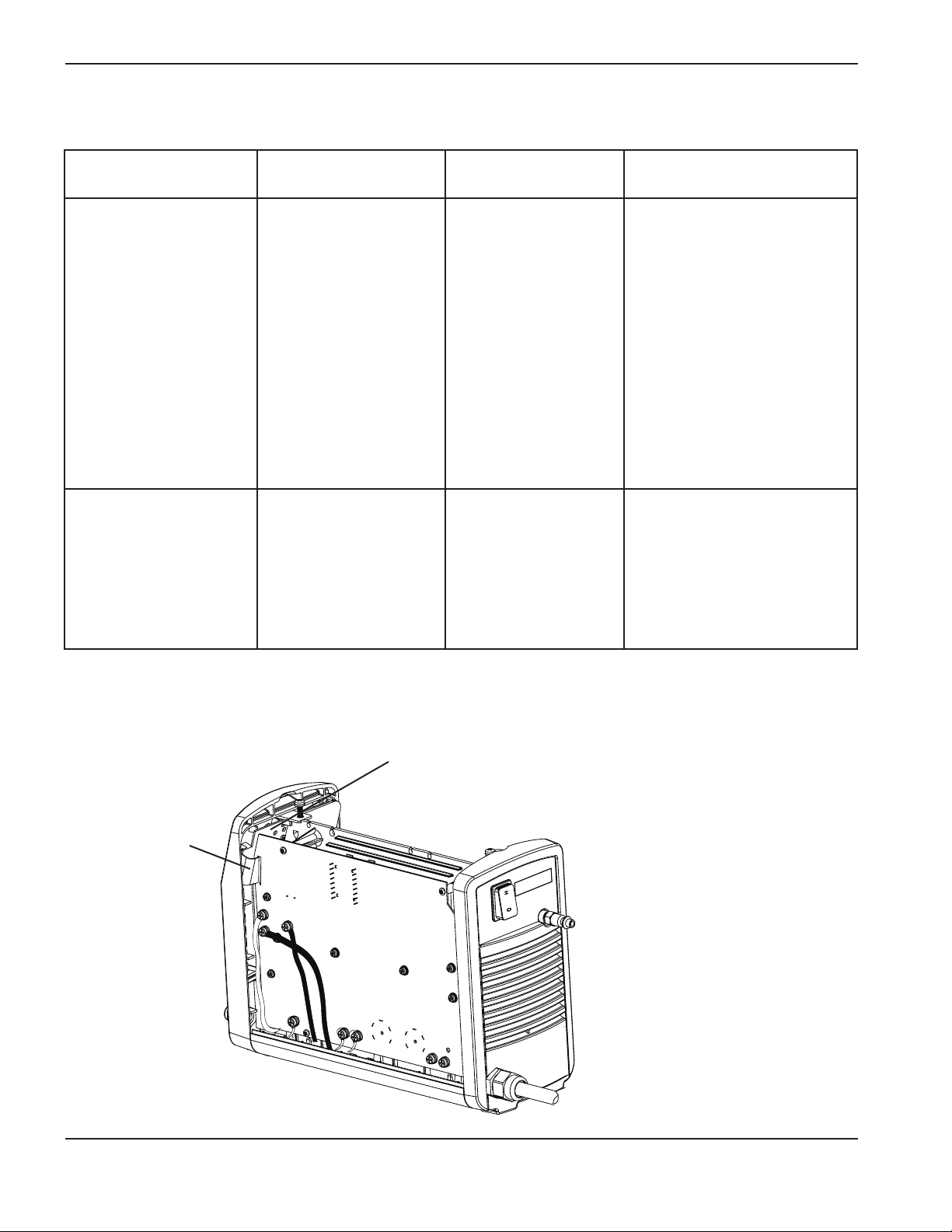
WARTUNG
3-12 powermax30 Wartungshandbuch
Problem
Dies kann
folgendes bedeuten Ursache Abhilfe
Die Schnittqualität ist
schlecht bzw. der Schnitt
trennt das Metall nicht
durch.
Die Verschleißteile
sind abgenutzt, die
Werkstückkabelverbindung ist schlecht,
die Stromzufuhrleistung
ist zu schwach oder die
Strombaukarte erzeugt
zu schwachen Strom.
• Die Verschleißteile
müssen ausgetauscht
werden.
• Das Werkstückkabel
kann beschädigt sein
oder ist nicht
ordnungsgemäß am
Werkstück
angebracht.
• Der StromreglerDrehknopf kann zu
niedrig eingestellt
sein.
• Die Strombaukarte
kann fehlerhaft sein.
• Verschleißteile untersuchen
und bei Bedarf austauschen.
• Werkstückkabel auf
Beschädigungen untersuchen.
Werkstückkabel erneut
anbringen und Werkstückoberfläche reinigen, um einen
guten Kontakt herzustellen.
• Einstellung des StromreglerDrehknopfes überprüfen.
Wenn der Eingangsschaltkreis
120 V, 20 A; 120 V, 30 A; oder
240 V, 20 A beträgt, Knopf auf
die höchste Einstellung
drehen.
Der Pilotlichtbogen
erlischt, wenn der
Plasmalichtbogen vom
Werkstück wegbewegt
wird, während der
Brenner-Wippentaster
noch immer betätigt wird.
Die Einstellung für den
Dauerpilotlichtbogen
funktioniert nicht.
Die Strombaukarte oder
die Steuerbaukarte kann
fehlerhaft sein.
• Tests 2 und 3 durchführen, um
zu überprüfen, ob die
Strombaukarte
ordnungsgemäß funktioniert.
Ist die Strombaukarte
fehlerhaft, ist diese
auszutauschen. Anderenfalls
Steuerbaukarte austauschen.
Anleitung zur Fehlerbeseitigung (Fortsetzung)
Steuerbaukarten-LEDs
Die Powermax30-Steuerbaukarte (PCB1) hat 4 Diagnose-LEDs.
Steuerbaukarte
Flachbandkabel

WARTUNG
powermax30 Wartungshandbuch 3-13
Neustart/Wächter
Fehler
Übertragung (XFR)
Start
Flachbandkabel
Die Steuerbaukarten-LEDs sind wie folgt:
• Start — Die Stromquelle verfügt über ein Startsignal. Diese LED leuchtet, wenn die Stromquelle ein Startsignal
erhält, und bleibt während des Normalbetriebs erleuchtet.
• Übertragung — Diese LED leuchtet, wenn eine ordnungsgemäße Lichtbogen-Übertragung zwischen Brenner
und Werkstück stattfindet, und blinkt während des Dauer-Pilotlichtbogen-Betriebs (z. B. beim
Schneiden von Streckmetall oder wenn der Lichtbogen vom Blech weg- und dann wieder auf es
zurückbewegt wird.
• Fehler — Die Fehler-LED leuchtet, wenn die Gasdruck-, Brennerkappen- oder Temperatur-LED an der
Stromquellenvorderseite leuchtet. Wenn alle 4 LEDs an der Stromquellenvorderseite blinken, blinkt die
Fehler-LED ebenfalls. Wie oft sie zwischen den Pausen blinkt, bestimmt, welche Komponente
fehlerhaft sein kann.
• Neustart — Diese LED leuchtet, wenn der Spannungsmesswert nicht im zulässigen Bereich liegt oder die
Neustart-LED blinkt.
Während des Normalbetriebs leuchtet die Strom-EIN-LED an der Stromquellenvorderseite und die Start- und
Übertragungs-LEDs auf der Steuerbaukarte leuchten ebenfalls. Wenn am Gerät ein Problem auftritt, blinkt eine
oder mehrere Fehler-LEDs an der Stromquellenvorderseite und die Fehler-LED oder die Neustart-LED auf der
Steuerbaukarte können leuchtet oder blinkt.
Verwendung der Steuerbaukarten-Fehler- und Neustart-LEDs zur Fehlerbeseitigung
Die Fehler- und Neustart-LEDs geben Informationen, die bei der Beseitigung von Gerätefehlern Verwendung
finden. Blinken die LEDs an der Stromquellenvorderseite, ist an der Fehler-LED auf der Steuerbaukarte
nachzusehen, um zu bestimmen, wo der Fehler liegen könnte. Anzahl der Blinksignale zählen und dann auf der
Tabelle auf der folgenden Seite nachsehen, um die Korrekturmaßnahme zu bestimmen.
Neustart-LED
Wenn die Neustart-LED der Steuerkarte leuchtet, können die Spannungen auf der Strombaukarte inkorrekt sein.
Es sind folgende Tests an J7 auf der Strombaukarte durchzuführen (siehe Test 2 – StrombaukartenSpannungsprüfungen an späterer Stelle in diesem Abschnitt):
• Stift 5 zur Erdung auf 3,3 VDC (± 10 %) prüfen.
• Stift 7 zur Erdung auf 5 VDC (± 10 %) prüfen.
• Stift 12 zur Erdung auf 2,2 VDC (± 10 %) prüfen.
Liegen die festgestellten Werte nicht innerhalb eines Bereichs von ± 10 % der obigen Werte, Flachbandkabel von
der Steuerbaukarte trennen und Tests nochmals durchführen. Werden beim zweiten Mal korrekte Werte
festgestellt, Steuerbaukarte austauschen. Anderenfalls Strombaukarte austauschen.

WARTUNG
3-14 powermax30 Wartungshandbuch
Gerätetests
Es gibt eine Erdungsklemme nahe der Oberseite der rückwärtigen Endkappe, die als Erdung bei allen Tests, die
eine Erdung des Multimeters erfordern, verwendet werden kann. Außerdem gibt es eine Erdung auf dem
Kühlkörper, auf die durch die Strombaukarte hindurch zugegriffen werden kann, wie in Test 1 gezeigt.
Fehler-LED
Die Anzahl der Blinksignale der Fehler-LED zeigt das gefundene Problem an. Jedes Blinksignal dauert eine halbe
Sekunde und eine jede Serie von Blinksignalen wird durch eine Pause von 2 Sekunden getrennt. Siehe
Gerätetests an späterer Stelle in diesem Abschnitt bezüglich der detaillierten Testverfahren.
Anzahl der
Blinksignale der
Fehler-LED
Angezeigtes Problem Abhilfe
1 Fehlerhafte Steuerbaukarte Steuerbaukarte austauschen.
2 Fehlerhafte Strombaukarte Strombaukarte austauschen.
3
Entweder die Strombaukarte
oder die Steuerbaukarte ist
fehlerhaft.
• Test 3 durchführen. Wenn einer der Werte inkorrekt ist,
Strombaukarte austauschen.
• Test 2 durchführen. Wenn einer der Werte der Stifte 5,
7 oder 12 inkorrekt ist, Steuerbaukarte entfernen und
nochmals testen. Sind die Werte korrekt, Steuerbaukarte
austauschen.
• Sind beim Durchführen von Test 2 die Werte für die Stifte
5, 7 und 12 korrekt, andere Werte jedoch inkorrekt,
Strombaukarte austauschen.
4
Fehlerhaftes
Gasmagnetventil
Gasmagnetventil austauschen.
5 Fehlerhafter Lüfter Lüfter austauschen.
Erdungsleitungsklemme
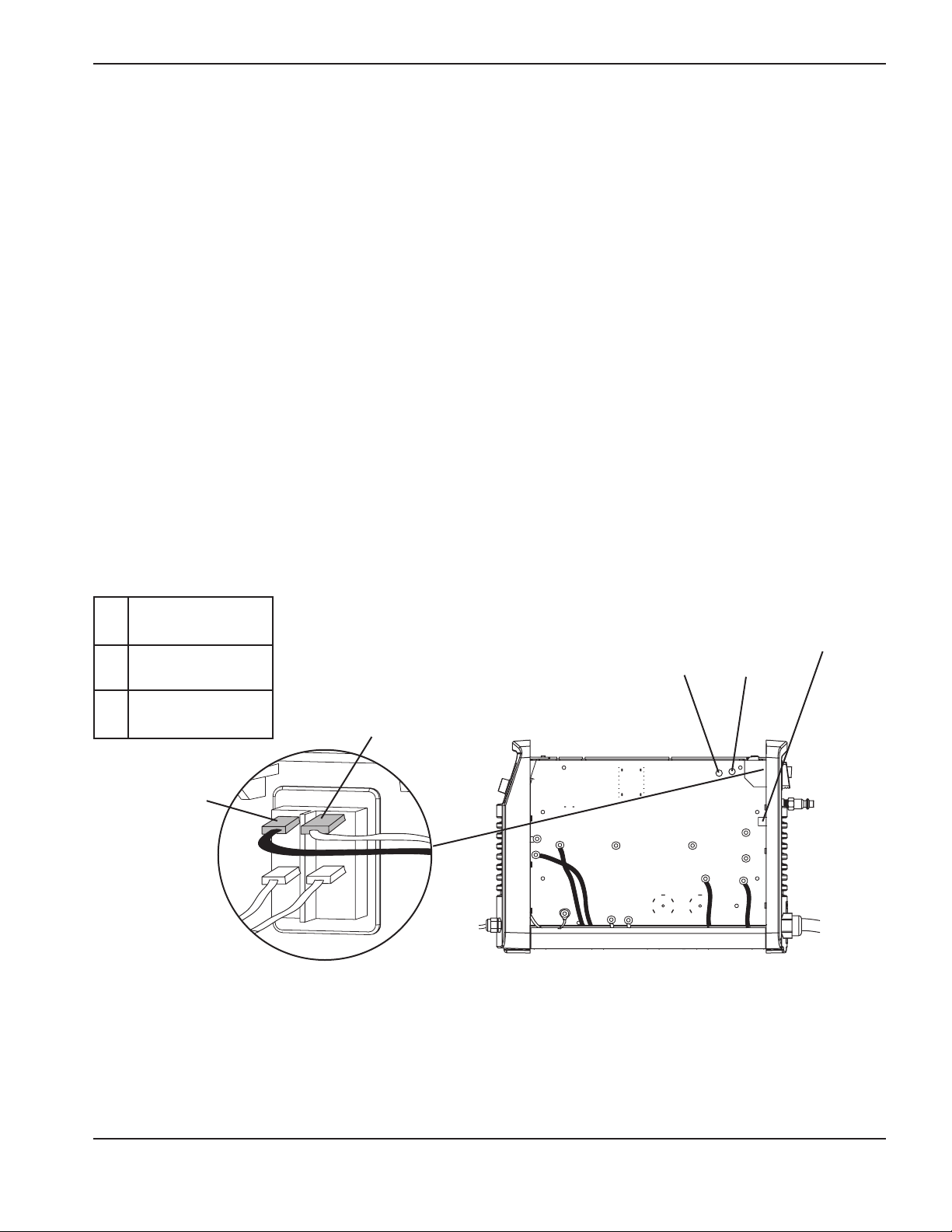
WARTUNG
powermax30 Wartungshandbuch 3-15
1-phasig
L Schwarz (CSA)
Braun (CE)
N Weiß (CSA)
Blau (CE)
PE Grün (CSA)
Grün/Gelb (CE)
L
N
PE (Erdung)
J2
J1
Test 1 – Netzspannung
Eingangsspannung und Netzspannung zur Oberseite des Netzschalters (S1) überprüfen.
1. Stromzufuhr unterbrechen und EIN/AUS-Schalter auf AUS (O) stellen.
2. Die 2 oberen Drähte des EIN/AUS-Schalters etwas aus den Laschen herausziehen, damit die Testkabel auf den
Laschen zur Prüfung der Wechselstromspannung angebracht werden können.
3. Sobald die Testkabel angebracht sind, elektrischen Strom wieder anschließen. EIN/AUS-Schalter in AUSStellung belassen. Die Spannung sollte der Netzspannung des Eingangsschaltkreises entsprechen, z. B. 120 V
oder 240 V.
4. Ist die Wechselstromspannung inkorrekt, nachprüfen, ob die Einheit Strom erhält. Ist Strom vorhanden,
Netzkabel auf Beschädigung überprüfen.
5. Funktionieren Stromzufuhr und Netzkabel einwandfrei, elektrischen Strom wieder unterbrechen und die Drähte
wieder anschließen.
6. Elektrischen Strom wieder anschließen. Dann EIN/AUS-Schalter auf EIN (I) stellen und die
Wechselstromspannung von J1 zu J2 (beschriftet mit „AC” auf der Strombaukarte) messen. Dieser Wert sollte
der gleiche sein, wie die hereinkommende Netzspannung. Ist dies nicht der Fall, EIN/AUS-Schalter überprüfen.
7. Leuchtet die AC-LED noch immer, Test 2 durchführen, um zu bestimmen, ob die Strombaukarte oder die
Steuerbaukarte fehlerhaft ist.
Anmerkung: Alle Werte können ±15 % betragen.

WARTUNG
3-16 powermax30 Wartungshandbuch
Test 2 – Strombaukarten-Spannungsprüfungen
Bei Stromzufuhr in EIN-Stellung ist ein Messgerät zur Prüfung der Spannungen an den J7-Stiften, die in folgender
Tabelle aufgelistet sind, zu verwenden, um sich zu vergewissern, ob die Strombaukarte einwandfrei funktioniert.
Sind Werte inkorrekt, Strombaukarte austauschen.
Anmerkung: Alle Werte können ±10 % betragen.
J7-Stift-Nummer
zur Erdung
Test Erwarteter Wert
19
VACR (gleichgerichteter
Wechselstrom)
0,86 V bei 120 V Netzspannung
1,87 V bei 230 V Netzspannung
21 VBUS (Gleichstrom-Bus-Spannung) 2,28 VDC bei 375 VBUS
18 IPFC (Eingangsspannung) < 0,1 VDC
20 IFB (Ausgangsspannung) < 0,1 VDC
22 ITF (Übertragungsspannung) < 0,1 VDC
5 3,3 VDC 3,3 VDC ± 5 %
7 5 VDC 5 VDC ± 5 %
12 24 V Fühler-Stift 2,2 VDC
16 Startsignal
3,2 VDC geschlossen
0 VDC offen
Anmerkung: Um die Werte an Stift 16 testen zu können, müssen Brenner und Stromquelle so aufgestellt
sein, das man den Brenner-Wippentaster sicher betätigen und loslassen kann.
Zur Erdungsdrahtklemme
oder zum Kühlkörper erden.
Vorsicht!: Keinen -VBUS als Erdung verwenden. Dadurch könnte die Stromquelle zerstört
werden. Die Erdung ist stattdessen entweder zur Erdungsdrahtklemme an der
rückwärtigen Endkappe oder zum Kühlkörper, wie unten gezeigt, vorzunehmen.
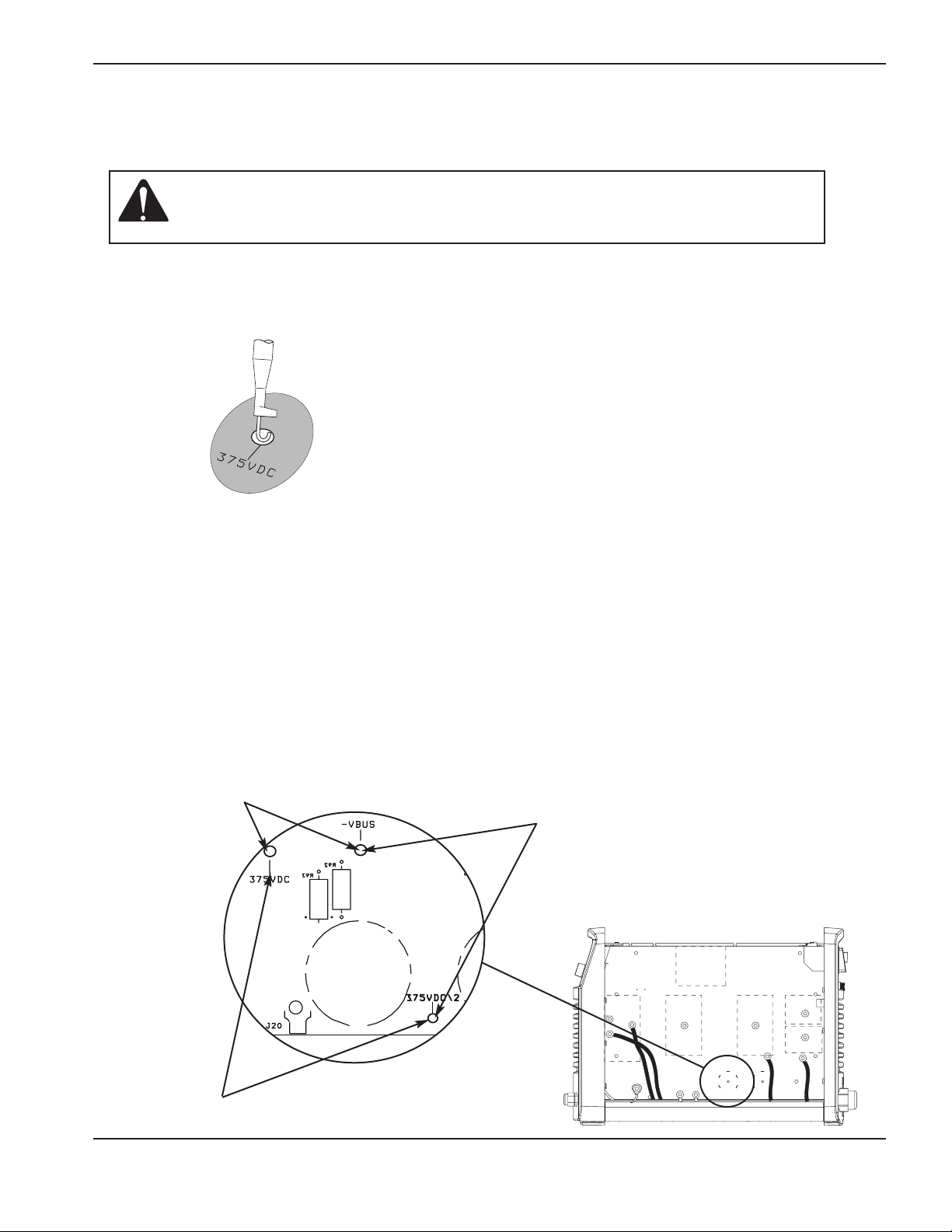
WARTUNG
powermax30 Wartungshandbuch 3-17
Test 3 — VBUS und Spannungsgleichgewicht
Strombaukarte testen, um sicherzustellen, dass die Schaltkreise ausgeglichen sind.
Schritt 3
Schritt 2
Schritt 4
Vorsicht!: Kein Multimeter mit Messsonden verwenden, die einen Kurzschluss
zwischen dem BUS und dem Kühlkörper verursachen können. Statt
dessen sind E-Z Hook
®
Kabel zu verwenden.
1. Strom in AUS-Stellung bringen.
2. Multimeterkabel anbringen, um die Spannung vom -VBUS zu den 375 VDC auf der Strombaukarte zu messen.
E-Z Hooks sorgfältig an den Kanten der Bohrungen in der Strombaukarte anschließen, damit der Haken den
Kontakt mit dem Ring an er Rückseite der Strombaukarte herstellt.
Nach dem Anschluss der E-Z-Hooks Strom auf EIN schalten. Das Multimeter sollte 375 VDC anzeigen.
Wenn ein anderer Wert als 375 VDC erhalten wird, Ablesewert mit 0,00601 multiplizieren, um ihn in mV
umzurechnen. Stift 21 auf J7 testen. Er sollte den gleichen Wert haben (± 10 %).
3. Strom auf AUS stellen und E-Z-Haken an VBUS und 375 VDC/2 anbringen. Strom in EIN-Stellung bringen,
nachdem das Multimeter angeschlossen worden ist. Dieser Wert sollte 187,5 VDC bzw. die Hälfte desjenigen
Wertes betragen, der in Schritt 2 ermittelt wurde.
4. Strom auf AUS stellen und E-Z-Haken an 375 VDC und 375 VDC/2 anbringen. Strom in EIN-Stellung bringen,
nachdem das Multimeter angeschlossen worden ist. Dieser Wert sollte 187,5 VDC bzw. die Hälfte des Wertes
betragen, der in Schritt 2 gefunden wurde.
5. Die in den Schritten 3 und 4 ermittelten Werte sollten in etwa gleich sein. Wenn sie um mehr als 30 V
differieren, Strombaukarte austauschen.
Anmerkung: Alle Werte können ± 10 % betragen.

WARTUNG
powermax30 Wartungshandbuch 3-19
Test 5 – Brenner klemmt in offenem Zustand
Vor Betätigung des Brenner-Wippentasters und Beginn des Gasstroms sollten Düse und Elektrode geschlossen
sein. Ist das nicht der Fall, so erkennt die Stromquelle ein TSO bzw. Fehler: „Brenner klemmt in offenem Zustand”.
Folgender Test ist zu verwenden, um zu bestimmen, ob der Brenner in offenem Zustand klemmt.
1. EIN/AUS-Schalter in AUS (O)-Stellung bringen.
2. Widerstand von der weißen Drahtgruppe und dem roten Draht der Brennerleitung zu den Plus- und MinusAnschlüssen an der Stromquelle messen. Der Widerstand sollte als geschlossen anzeigen.
3. Zeigt der Widerstand als offen an, berühren sich Düse und Elektrode nicht, oder einer der Drähte in der
Brennerleitung ist gebrochen. Es ist sicherzustellen, dass der Brennerkolben sich frei im Brennerkopf bewegt.
Ist das nicht der Fall, Brennerkopf austauschen. Funktionieren die Brennerteile einwandfrei, Brennerleitung
austauschen.
Weiße
Drahtgruppe
Roter Draht
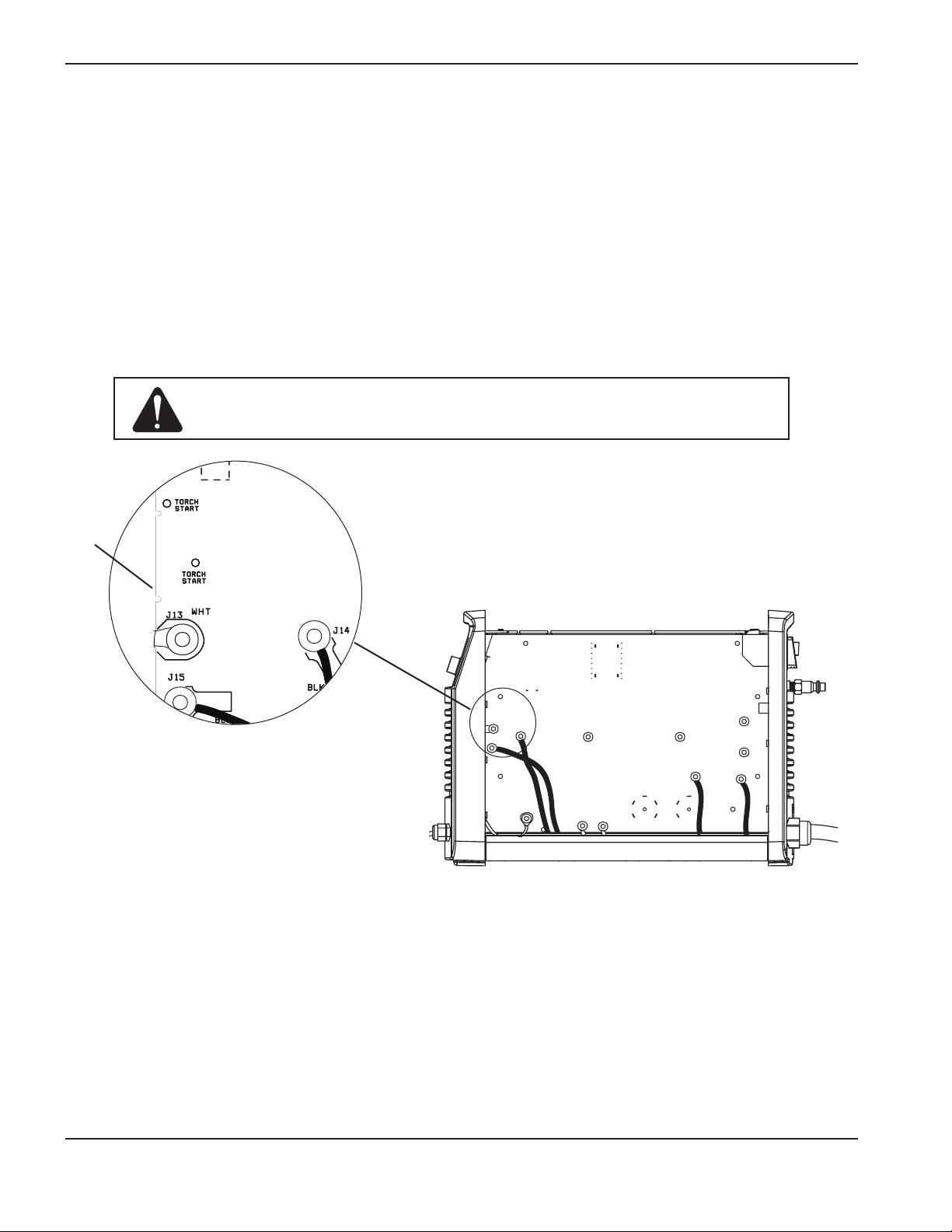
WARTUNG
3-20 powermax30 Wartungshandbuch
Test 6 — Plasmastart
Nachprüfen, ob die Steuerbaukarten-LED ein gültiges Startsignal erhält.
1. Die Start-LED auf der Steuerbaukarte bei Strom in EIN-Stellung beobachten. Sie sollte aufleuchten, sobald der
Brenner-Wippentaster betätigt wird.
2. EIN/AUS-Schalter in AUS (O)-Stellung bringen. Widerstand an den 2 Brennerstart-Testpunkten auf der
Strombaukarte prüfen. Bei aktiviertem Wippentaster sollte der Widerstand 10 Ω oder weniger betragen. Bei
deaktiviertem Wippentaster sollte der Schaltkreis ca. 3 kΩ anzeigen. Wird dieser Test nicht bestanden, den
Brennerstartschalter und die Brennerdrähte überprüfen.
3. EIN/AUS-Schalter in EIN (I)-Stellung bringen. Stift 16 von J7 zur Erdung messen (siehe Test 2 an früherer Stelle
in diesem Abschnitt). Er sollte 0 VDC bei offenem Schaltkreis bzw. 3,2 VDC bei geschlossenem Schaltkreis
anzeigen. Sind die Werte nicht korrekt, Strombaukarte austauschen.
Test 7 — Brennerkappensensor
Kappensensorschalter und Brennerleitungen testen.
1. EIN/AUS-Schalter in AUS (O)-Stellung bringen.
2. Vordere Endkappe sanft von der Stromquelle wegziehen. J12 von der Strombaukarterückseite trennen (direkt
unterhalb der Brennerstart-Testpunkte).
3. Widerstand vom orangefarbenen Draht zum blauen Draht messen. Er sollte weniger als 10 Ω betragen. Zeigt er
als offen an, ist der Kappensensorschalter-Schaltkreis nicht zufriedengestellt.
4. Bewegt sich der Brennerkolben reibungslos und sind die Verschleißteile korrekt installiert, dann ist entweder der
Kappensensorschalter fehlerhaft oder die Brennerleitung hat einen gebrochenen Draht.
J12
Vorsicht!: Während des Prüfens ist jeder Kontakt mit der Brennerspitze zu
vermeiden.

WARTUNG
powermax30 Wartungshandbuch 3-21
Test 8 — Lüfter
Lüfter auf einwandfreie Funktion testen.
• Drahtbrücke von der Erdung zu Stift 3 von J5 anbringen. Funktioniert der Lüfter nicht, Lüfter austauschen.
Test 9 — Druckschalter
Druckwächter testen, um sicherzustellen, dass das Gerät den korrekten Gasdruck erhält.
1. Strom in AUS-Stellung bringen.
2. Widerstand zwischen den Stiften 1 und 2 von J4 überprüfen. Er sollte ca. 4,7 kΩ anzeigen, wenn kein Gasdruck
vorhanden ist. Liegt der Gasdruck innerhalb der Gerätetoleranzen, sollte der Schaltkreis als geschlossen
anzeigen.
J5
Erdung zur
Erdungsdrahtklemme
oder zum Kühlkörper
vornehmen.

WARTUNG
3-22 powermax30 Wartungshandbuch
Komponentenaustausch
Entfernen einer Endkappe
Die Endkappen können entfernt werden, um sie auszutauschen. Auch lassen sich manche Reparaturen leichter mit
abgenommenen Endkappen durchführen.
1. Stromzufuhr auf AUS stellen, Netzkabel unterbrechen und Gaszufuhr unterbrechen.
2. Mit einem Kreuzschraubenzieher Nr. 2 die 2 Schrauben vom Griff auf der Stromquelle entfernen. Endkappen
leicht zurückkippen, so dass sich die Griffkanten unter den Endkappen herausnehmen lassen. Griff entfernen
und dann Abdeckung von der Stromquelle abnehmen.
GEFAHR
ELEKTRISCHE SCHLÄGE KÖNNEN TÖDLICH SEIN
• Man muss äußerste Vorsicht walten lassen, wenn man in der Nähe von unter Strom
stehenden elektrischen Schaltkreisen arbeitet. Es können gefährliche Spannung in der
Stromquelle bestehen, die ernste Verletzungen oder Tod verursachen können.
• Vor weiterem Vorgehen siehe Warnungen auf Seite 3-6.

WARTUNG
powermax30 Wartungshandbuch 3-23
3. Stromquelle auf die Seite legen oder sie auf den Kopf stellen. Jede der Endkappen hat in der Mitte eine
Halteschraube.Die an der Unterseite der Einheit herausragenden Füße haben Bohrungen für den Zugriff auf die
Schnappverschlüsse, die die Endkappen festhalten. Neben jedem Fuß befindet sich eine erhöhte Rippe.
4. Halteschraube von der Unterseite der abzunehmenden Endkappe entfernen.
5. Es gibt Schnappverschlüsse auf jeder Seite der Endkappe, die diese festhalten. Spitzzange in die Öffnung eines
der Schnappverschlüsse einführen und Zange benutzen, um ihn zusammenzudrücken.
6. Schlitzschraubendreher an die erhöhte Rippe neben dem Schnappverschluss ansetzen und den
Schraubendreher sanft drehen, um die Endkappe von der Grundplatte wegzudrücken.
Schnappverschluss
Schnappverschluss
Schnappverschluss
Schnappverschluss
Rippe
Rippe
Rippe
Rippe
Halteschraube
Halteschraube
Rückwärtige Endkappe Vordere Endkappe

WARTUNG
3-24 powermax30 Wartungshandbuch
7. Einen weiteren Schraubendreher oder einen ähnlichen
Gegenstand in die Öffnung zwischen Endkappe und Grundplatte
anbringen, um die erste Ecke der Endkappe davon abzuhalten, in
ihre ursprüngliche Stellung zurückzukehren, wenn die nächste
Ecke angehoben wird.
8. Schritte 5 und 6 mit der anderen Ecke der Endkappe wiederholen.
9. Wird die Endkappe für deren Austausch vollständig entfernt, statt
sie nur für einen leichteren Zugriff in das Innere der Stromquelle zu
entfernen, muss zusätzlich die Brennerleitung, das Werkstückkabel
und die Erdungsklemme von der vorderen Endkappe getrennt
werden bzw. das Netzkabel und der Gaszufuhranschluss von der
rückwärtigen Endkappe getrennt werden.
10. Um die Endkappe wiedereinzusetzen, ist sie an die Grundplatte zu drücken, um die Schnappverschlüsse
wieder einzurasten und dann die Halteschraube wieder anzubringen. Bei der rückwärtigen Endkappe ist
sicherzustellen, dass die Bohrung in der Erdungsklemme mit den Schraubenbohrungen in der Endkappe und
der Stromquelle ausgerichtet ist, bevor der Versuch unternommen wird, die Halteschraube einzuführen.
Austausch der Brennerleitung
1. Strom auf AUS stellen, Netzkabel unterbrechen und Gaszufuhr unterbrechen.
2. Mit einem Kreuzschraubenzieher Nr. 2 die 2 Schrauben vom Griff auf der Stromquelle entfernen. Endkappen
leicht zurückneigen, damit sich die Kanten des Griffes unter ihnen herausnehmen lassen. Griff entfernen und
dann die Abdeckung von der Stromquelle abnehmen. Die Nomex-Isolierung, welche die Strombaukarte
schützt, entfernen.
3. Manschette auf die Schlauchverbindung drücken und den Schlauch aus der Verbindung herausziehen, um den
Gasschlauch vom Magnetventil zu entfernen
Gasschlauch
Schlauchverbindungsmanschette
Magnetventil

WARTUNG
3-26 powermax30 Wartungshandbuch
Austausch des Werkstückkabels
1. Strom auf AUS stellen, Netzkabel unterbrechen und Gaszufuhr unterbrechen.
2. Die zwei Schrauben vom Griff an der Oberseite der Stromquelle entfernen. Griff entfernen und dann die
Abdeckung von der Stromquelle abnehmen. Die Nomex-Isolierung, welche die Strombaukarte schützt,
entfernen.
3. Schraube und Unterlegscheibe von J22 auf der Strombaukarte entfernen (zusätzlich mit „WORK LEAD”
(Werkstückkabel) beschriftet), welche die Leitung an der Baukarte festhält.
4. Entweder die vordere Endkappe entfernen oder sie vorsichtig von der Stromquelle wegneigen
Sicherungsmutter der Zugentlastung entfernen. Werkstückkabel durch die Bohrung in der Endkappe ziehen.
6. Auf der Innenseite der vorderen Endkappe die Sicherungsmutter der Zugentlastung für die Brennerleitung
abschrauben, so dass die Brennerleitung frei beweglich ist. Die Brennerleitung durch Ziehen der Drähte und
der Gaszufuhrleitung durch die Bohrung in der Endkappe entfernen.
7. Drähte und Gaszufuhrleitung für die neue Brennerleitung durch die Bohrung in der Endkappe führen und dann
durch die Sicherungsmutter der Zugentlastung.
8. Sicherungsmutter der Zugentlastung für die Brennerleitung an der Zugentlastung festziehen.
9. Den Gaszufuhrschlauch ca. 16 mm in das Anschlussstück an der Unterseite des Magnetventils drücken.
10. Abschlussring für die weiße Drahtgruppe über den linken Bolzen (auf der Mittelplatte mit „WHT” beschriftet)
schieben. Abschlussring für den roten Draht auf den Bolzen zur Rechten (auf der Mittelplatte mit „RED”
beschriftet) schieben. Schraubenmutter auf jedem Bolzen festziehen.
11. Die Drahtgruppe mit dem orangefarbenen, blauen und violetten Draht über die Mittelplatte führen, wobei die
Drähte in der Aussparung der Platte ruhen. Steckverbindung in den Steckplatz auf der Strombaukarte drücken.
12. Unter Beachtung, dass keine Drähte eingeklemmt werden, Abdeckung auf die Stromquelle zurückschieben.
Sicherstellen, dass die unteren Kanten sich in den Schienen befinden.
13. Endkappe wieder in ihre Position zurückbringen. Es ist sicherzustellen, dass die Schraubenbohrung in der
Erdungsklemme mit den Schraubenbohrungen in der Endkappe und der Stromquelle ausgerichtet ist.
14. Elektrischen Strom und Gaszufuhr wieder anschließen.
Werkstückkabel
Werkstückkabelanschluss an
die Strombaukarte (J22)
Vordere Endkappe
Zugentlastung

WARTUNG
powermax30 Wartungshandbuch 3-27
5. Steckverbindungsseite des neuen Werkstückkabels durch die Bohrung in der Endkappe und dann durch die
Sicherungsmutter führen.
6. Schraubenmutter auf der Zugentlastung festziehen, um sie an Ort und Stelle zu halten.
7. Werkstückkabel an der Strombaukarte an J22 mit der Schraube und der Unterlegscheibe anbringen, die zuvor
in Schritt 3 entfernt wurden. Die Drehmomenteinstellung für diesen Anschluss beträgt 23,04 kg cm.
8. Endkappe austauschen bzw. wieder ausrichten.
9. Unter Beachtung, dass keine Drähte eingeklemmt werden, Nomex-Barriere wieder anbringen und Abdeckung
wieder auf die Stromquelle schieben. Sicherstellen, dass die unteren Kanten sich in den Schienen befinden.
10. Griff über die Bohrungen in der Abdeckungsoberseite positionieren, dann die zwei Schrauben zur Sicherung
der Abdeckung verwenden.
11. Elektrischen Strom und Gaszufuhr wieder anschließen.
1-phasig
CSA-Einheit
L Schwarz
N Weiß
Erdung Grün
L
Schwarzer
Draht
N
Weißer Draht
Austausch des Netzkabels (CSA)
1. Strom auf AUS stellen, Netzkabel unterbrechen und Gaszufuhr unterbrechen.
2. Die zwei Schrauben vom Griff an der Oberseite der Stromquelle entfernen. Griff entfernen und dann die
Abdeckung von der Stromquelle abnehmen. Die Nomex-Isolierung, welche die Strombaukarte schützt,
entfernen.
Das Netzkabel hat einen schwarzen Draht und einen weißen Draht, welche am Stromschalter angeschlossen
sind, sowie einen grünen Erdungsdraht, der an den Kühlkörper angeschlossen ist.
3. Rückwärtige Endkappe entfernen oder sanft von der Stromquelle wegbiegen.
4. Anschlussstück für den weißen Draht vorsichtig vom Stromschalter wegziehen, um ihn zu unterbrechen. Man
kann bei Bedarf zur Vereinfachung eine Spitzzange oder einen Schlitzschraubendreher verwenden.
5. Schwarzen Draht auf die gleiche Weise entfernen.
6. Schraube, die den grünen Draht am Kühlkörper festhält, entfernen. In der Strombaukarte befindet sich eine
Aussparung für einfachen Zugriff auf die Schraube.
7. An der Außenseite der Stromquelle die Sicherungsmutter an der Zugentlastung lösen, damit die Drähte frei
beweglich sind. Beim Austausch der Zugentlastung ist zusätzlich ein Rollgabelschlüssel zum Lösen der
Schraubenmutter an der Innenseite der Stromquelle zu verwenden.

WARTUNG
3-28 powermax30 Wartungshandbuch
8. Drähte durch die Zugentlastung oder durch die Bohrung in der Endkappe ziehen, um das alte Netzkabel zu
entfernen.
9. Verfügt man über eine neue Zugentlastung, ist diese auf das neue Netzkabel zu schieben und die Drähte für
das neue Netzkabel durch Bohrung in der Endkappe zu führen. Ist die alte Zugentlastung noch an Ort und
Stelle, sind die Drähte durch die Zugentlastung zu führen.
10. Schraubenmutter der Zugentlastung über die Drähte schieben und von der Innenseite der Endkappe aus an
die Zugentlastung schrauben.
11. Anschlussstück für den schwarzen Draht auf den Stift auf der oberen linken Seite des Stromschalters drücken.
12. Anschlussstück für den weißen Draht auf den Stift auf der oberen rechten Seite des Stromschalters drücken.
13. Grünen Erdungsdraht mit einer Drehmomenteinstellung von 17,28 kg cm an den Kühlkörper schrauben.
14. Drähte in der Drahtaussparung an der Seite der Endkappe hinaufverlegen, so dass sie der Stromkarte nicht im
Weg sind. Sobald die Drähte an Ort und Stelle sind, Sicherungsmutter der Zugentlastung festziehen.
15. Endkappe wieder einsetzen oder in ihre Position zurückbringen. Es ist sicherzustellen, dass die
Schraubenbohrung in der Erdungsklemme mit den Schraubenbohrungen in der Endkappe und der
Stromquelle ausgerichtet ist.
16. Unter Beachtung, dass keine Drähte eingeklemmt werden, Nomex-Barriere wieder anbringen und Abdeckung
wieder auf die Stromquelle schieben. Sicherstellen, dass die unteren Kanten sich in den Schienen befinden.
Griff über die Bohrungen in der Abdeckungsoberseite positionieren, dann die zwei Schrauben zur Sicherung
der Abdeckung verwenden.
17. Elektrischen Strom und Gaszufuhr wieder anschließen.
Austausch des Netzkabels (CE)
1. Strom auf AUS stellen, Netzkabel unterbrechen und Gaszufuhr unterbrechen.
2. Die zwei Schrauben vom Griff an der Oberseite der Stromquelle entfernen. Griff entfernen und dann die
Abdeckung von der Stromquelle abnehmen. Die Nomex-Isolierung, welche die Strombaukarte schützt,
entfernen.
Das Netzkabel hat einen braunen Draht sowie einen blauen Draht, beide sind an den Netzschalter
anzuschließen, sowie einen grünen und einen gelben Erdungsdraht, diese beiden sind an den Kühlkörper
anzuschließen.
3. Rückwärtige Endkappe entfernen oder sanft von der Stromquelle wegbiegen.
4. Anschluss für den blauen Draht sorgfältig vom Netzschalter wegziehen, um ihn zu unterbrechen. Man kann bei
Bedarf zur Vereinfachung eine Spitzzange oder einen Schlitzschraubenzieher verwenden.
5. Braunen Draht auf die gleiche Weise entfernen.
1-phasig
CE-Einheit
L Braun
N Blau
Erdung Grün / Gelb
L
Brauner
Draht
N
Blauer Draht

WARTUNG
powermax30 Wartungshandbuch 3-29
6. Die Schraube, welche den grünen und den gelben Erdungsdraht am Kühlkörper sichert, entfernen. In der
Strombaukarte befindet sich eine Aussparung für einfachen Zugriff auf die Schraube.
7. An der Außenseite der Stromquelle die Sicherungsmutter an der Zugentlastung lösen, damit die Drähte frei
beweglich sind. Beim Austausch der Zugentlastung ist zusätzlich die Mutter an der Innenseite der Stromquelle
abzuschrauben.
8. Stecker des alten Netzkabels entfernen.
9. Von der Innenseite der Stromquelle aus die Drähte durch die Zugentlastung und die Bohrung in der Endkappe
ziehen, um das alte Netzkabel zu entfernen.
10. Steckerdrähte des neuen Netzkabels durch die Schraubenmutter für die Zugentlastung und dann durch die
Bohrung in der Endkappe führen. Die röhrenförmige Ferritperle am Netzschalterende des braunen und blauen
Drahtes nicht entfernen.
11. Wird eine neue Zugentlastung verwendet, ist diese auf das neue Netzkabel zu schieben. An der Innenseite der
Endkappe ist die Mutter auf die Zugentlastung zu schrauben.
12. Anschluss für den braunen Draht auf den Stift an der oberen linken Seite der Stromquelle drücken.
13. Anschluss für den blauen Draht auf den Stift an der oberen rechten Seite der Stromquelle drücken.
14. Grünen und gelben Erdungsdraht mit einer Drehmomenteinstellung von 17,28 kg cm an den Kühlkörper
schrauben.
15. Drähte in der Drahtaussparung an der Seite der Endkappe hinaufverlegen, so dass sie der Stromkarte nicht im
Weg sind.
16. Endkappe wieder einsetzen oder in ihre Position zurückbringen. Es ist sicherzustellen, dass die
Schraubenbohrung in der Erdungsklemme mit den Schraubenbohrungen in der Endkappe und der
Stromquelle ausgerichtet ist.
17. Sicherungsmutter der Zugentlastung an der Außenseite der Endkappe befestigen.
18. Unter Beachtung, dass keine Drähte eingeklemmt werden, Nomex-Barriere wieder anbringen und Abdeckung
wieder auf die Stromquelle schieben. Sicherstellen, dass die unteren Kanten sich in den Schienen befinden.
Griff über die Bohrungen in der Abdeckungsoberseite positionieren, dann die zwei Schrauben zur Sicherung
der Abdeckung verwenden.
19. Elektrischen Strom und Gaszufuhr wieder anschließen.
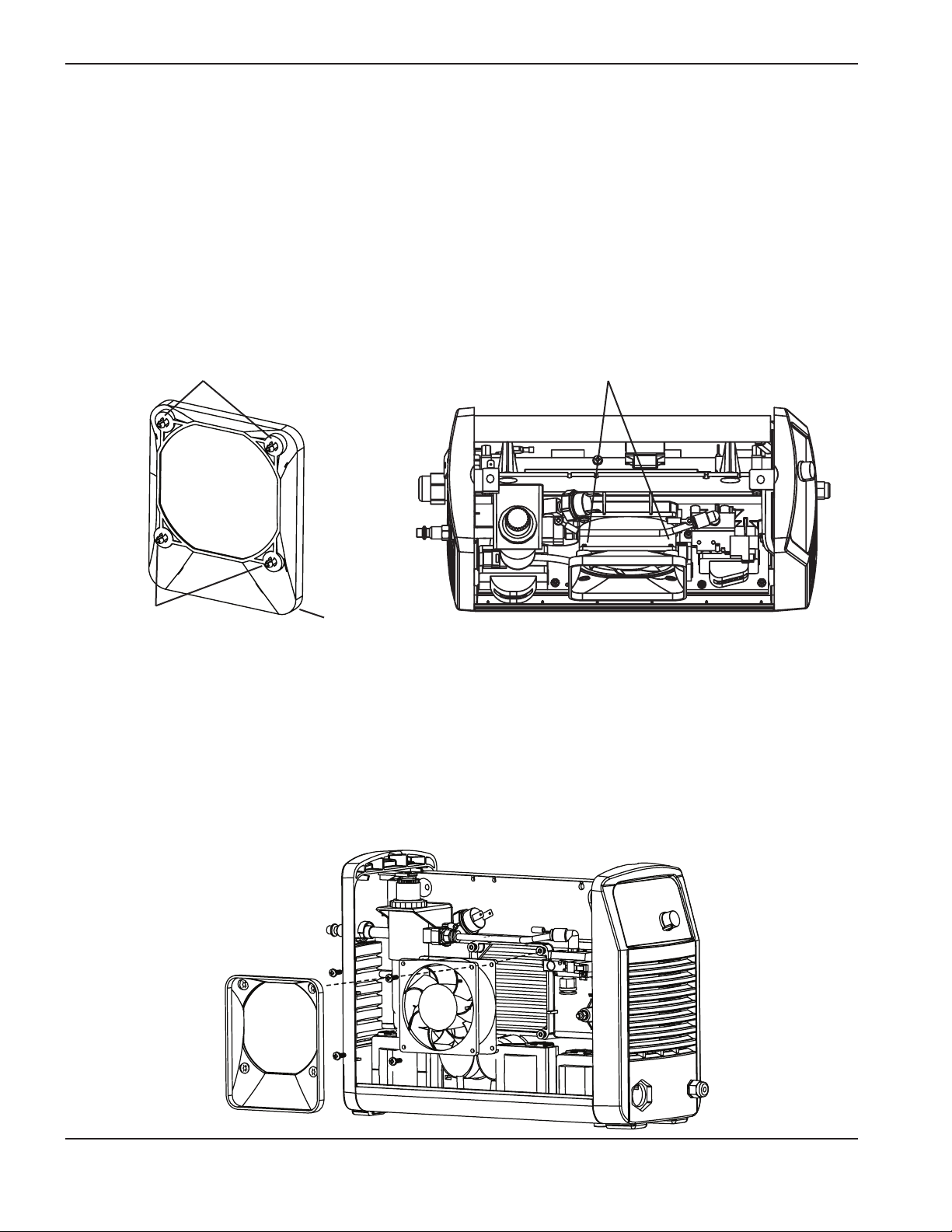
WARTUNG
3-30 powermax30 Wartungshandbuch
5. Kreuzschraubenzieher Nr. 1 durch die Bohrungen in der Lüfterverkleidung einführen, um die Halteschrauben
von jeder Ecke des Lüfters zu entfernen.
6. Alten Lüfter aus der Stromquelle schieben.
7. Neuen Lüfter an seinen Platz schieben.
8. Die 4 Halteschrauben wieder anbringen.
9. Lüftergehäuse so ausrichten, dass die breitere Seite am Boden ist, und es an Ort und Stelle einrasten lassen.
10. Steckverbindung für den roten und schwarzen Draht auf der linken Lüfterseite an J5 auf der Strombaukarte
anbringen.
Austausch des Lüfters
1. Strom auf AUS stellen, Netzkabel unterbrechen und Gaszufuhr unterbrechen.
2. Die zwei Schrauben vom Griff an der Oberseite der Stromquelle entfernen. Griff entfernen und dann die
Abdeckung von der Stromquelle abnehmen.
3. Steckverbindung von J5 auf der Strombaukarte trennen. Es kann erforderlich sein, die Oberkante der NomexIsolierung anzuheben, um die Steckverbindung zu sehen.
4. Von der Stromquellenoberseite aus mit einer Spitzzange die 4 Eckklammern des Lüftergehäuses
zusammendrücken und lösen. Nachdem die oberen Klammern gelöst worden sind, kann das Gehäuse von der
Stromquelle weggedreht werden, um die 2 unteren Klammern zu erreichen. Gehäuse aus der Verkleidung des
Lüfters herausheben.
Eckklammern
Obere Eckklammern
Boden
Eckklammern

WARTUNG
powermax30 Wartungshandbuch 3-31
6. Element vom Filterhauptteil abschrauben, während man darauf achtet, dass das Element sich nicht dreht.
7. Neues Element an den Filterkörper schrauben.
8. Filtergehäuse wieder befestigen.
9. Luftfilterbaugruppe wieder in die Klammer einsetzen und Sicherungsmutter wieder anbringen.
10. Ablassschlauch durch die Bohrung im Stromquellenboden führen.
11. Gaszufuhr wieder anschließen, um auf Undichtigkeiten zu überprüfen.
12. Unter Beachtung, dass keine Drähte eingeklemmt werden, Abdeckung auf die Stromquelle zurückschieben.
Sicherstellen, dass die unteren Kanten sich in den Schienen befinden. Griff über die Bohrungen in der
Abdeckungsoberseite positionieren, dann die zwei Schrauben zur Sicherung der Abdeckung verwenden.
13. Elektrischen Strom wieder anschließen.
Austausch des Luftfilterelements
1. Strom auf AUS stellen, Netzkabel unterbrechen und Gaszufuhr unterbrechen.
2. Die zwei Schrauben vom Griff an der Oberseite der Stromquelle entfernen. Griff entfernen und dann die
Abdeckung von der Stromquelle abnehmen.
3. Ablassschlauch von der Bohrung im Boden der Stromquellen-Grundplatte entfernen.
4. Schraubenmutter, welche den Luftfilter in der Klammer festhält, abschrauben. Boden des Luftfilters von der
Stromquelle wegkippen.
5. Filtergehäuse vom Hauptteil abschrauben und entfernen.
Schraubenmutter
Klammer
Filtergehäuse
Ablassschlauch
11. Unter Beachtung, dass keine Drähte eingeklemmt werden, Nomex-Barriere wieder anbringen und Abdeckung
wieder auf die Stromquelle schieben. Sicherstellen, dass die unteren Kanten sich in den Schienen befinden.
Griff über die Bohrungen in der Abdeckungsoberseite positionieren, dann die zwei Schrauben zur Sicherung
der Abdeckung verwenden.
12. Elektrischen Strom und Gaszufuhr wieder anschließen.

WARTUNG
3-32 powermax30 Wartungshandbuch
Austausch von Luftfilter und Regler
1. Strom auf AUS stellen, Netzkabel unterbrechen und Gaszufuhr unterbrechen.
2. Die zwei Schrauben vom Griff an der Oberseite der Stromquelle entfernen. Griff entfernen und dann die
Abdeckung von der Stromquelle abnehmen.
3. Gasanschlussstück von der Stromquellenrückseite entfernen.
4. Ablassschlauch von der Bohrung im Boden der Stromquellen-Grundplatte entfernen.
5. Roten und schwarzen Draht vom Drucksensor trennen.
6. Gaszufuhrschlauch vom Filter trennen.
7. Schraubenmutter, welche den Luftfilter in der Klammer festhält, abschrauben. Boden des Luftfilters von der
Stromquelle wegkippen.
8. Neuen Luftfilter in den Halter einsetzen und Sicherungsmutter wieder anbringen.
9. Ablassschlauch durch die Bohrung im Stromquellenboden führen.
10. Steckverbindung des schwarzen Drahtes auf den Stift an der linken Seite des Drucksensors drücken und die
Steckverbindung des roten Drahtes auf den Stift an der rechten Seite des Drucksensors drücken.
11. Gaszufuhrschlauch an den neuen Filter anschließen. Wird der Schlauch ausgetauscht, neuen Schlauch auf die
gleiche Länge wie die des alten Schlauches zuschneiden.
12. Gasanschlussstück wieder anschließen und dann die Gaszufuhr wieder anschließen, um sie auf
Undichtigkeiten zu überprüfen.
13. Unter Beachtung, dass keine Drähte eingeklemmt werden, Abdeckung auf die Stromquelle zurückschieben.
Sicherstellen, dass die unteren Kanten sich in den Schienen befinden. Griff über die Bohrungen in der
Abdeckungsoberseite positionieren, dann die zwei Schrauben zur Sicherung der Abdeckung verwenden.
14. Elektrischen Strom wieder anschließen.
Roter und schwarzer Draht
Gasanschlussstück
Filter und
Regler
Gaszufuhrschlauch
Drucksensor
Schraubenmutter
Klammer
Ablassschlauch

WARTUNG
powermax30 Wartungshandbuch 3-33
Austausch der Steuerbaukarte
1. Strom auf AUS stellen, Netzkabel unterbrechen und Gaszufuhr unterbrechen.
2. Die zwei Schrauben vom Griff an der Oberseite der Stromquelle entfernen. Griff entfernen und dann die
Abdeckung von der Stromquelle abnehmen. Die Nomex-Isolierung, welche die Strombaukarte schützt,
entfernen.
3. Vordere Endkappe entfernen oder sanft vom Boden wegneigen.
4. Flachbandkabel von der Strombaukarte trennen.
5. Neue Steuerbaukarte vor dem Installieren testen, indem deren Flachbandkabel an die Strombaukarte
angeschlossen wird. Strom wieder anschließen, Gerät einschalten und nachprüfen, ob die Start-LED auf der
Steuerbaukate die einzige LED ist, die leuchtet. Die Fehler-LEDs auf der Frontplatte sollten außerdem
erloschen sein.
6. Elektrischen Strom und Flachbandkabel wieder trennen und die neue Steuerbaukarte zur Seite legen.
7. Die 3 Halteschrauben von der alten Steuerbaukarte entfernen und Steuerbaukarte aus der Stromquelle
herausheben.
8. Neue Steuerbaukarte mit den 3 Halteschrauben an Ort und Stelle festschrauben und dann Flachbandkabel
anschließen.
9. Vordere Endkappe wieder in ihre Position zurückbringen. Es ist sicherzustellen, dass die Schraubenbohrung in
der Erdungsklemme mit den Schraubenbohrungen in der Endkappe und der Stromquelle ausgerichtet ist.
10. Unter Beachtung, dass keine Drähte eingeklemmt werden, Nomex-Barriere wieder anbringen und Abdeckung
wieder auf die Stromquelle schieben. Sicherstellen, dass die unteren Kanten sich in den Schienen befinden.
Griff über die Bohrungen in der Abdeckungsoberseite positionieren, dann die zwei Schrauben zur Sicherung
der Abdeckung verwenden.
11. Elektrischen Strom und Gaszufuhr wieder anschließen.
Steuerbaukarte
Flachbandkabel
Vorsicht!: Statische elektrizität kann platinen Beschädigen.
• Beim Umgang mit Leiterplatten sind angemessene Vorsichtsmaßnahmen zu
treffen.
– Leiterplatten in antistatischen Behältern aufbewahren.
– Beim Umgang mit Leiterplatten sind geerdete Gelenkbänder zu tragen.

WARTUNG
3-34 powermax30 Wartungshandbuch
Überspannungsschutzwiderstandschraube
Austausch der Strombaukarte
Vor Beginn dieses Verfahrens ist sicherzustellen, dass die für dieses Gerät richtige Strombaukarte vorhanden ist.
Der Austauschsatz für die CSA-Strombaukarte hat die Teilenummer 228094. Der Austauschsatz für die CEStrombaukarte hat die Teilenummer 228102. Obwohl es einige technische Unterschiede zwischen der
Strombaukarte für CSA-Stromquellen und der Strombaukarte für CE-Stromquellen gibt, ist das Verfahren für den
Austausch der Baukarten das gleiche.
1. Strom auf AUS stellen, Netzkabel unterbrechen und Gaszufuhr unterbrechen.
2. Die zwei Schrauben vom Griff an der Oberseite der Stromquelle entfernen. Griff entfernen und dann die
Abdeckung von der Stromquelle abnehmen. Die Nomex-Isolierung, welche die Strombaukarte schützt,
entfernen.
3. Flachbandkabel von der Kühlkörperseite der Strombaukarte trennen. (Siehe Abbildung auf der folgenden Seite
bezüglich der Lage des Flachbandkabels und der in den nächsten Schritten aufgelisteten Komponenten.)
4. Brennerstart- und Kappensensor-Steckverbindung an J12 auf der Kühlkörperseite der Strombaukarte
entfernen.
5. Steckverbindungen an J4, J5 und J6 auf der Kühlkörperseite der Strombaukarte entfernen.
6. Drähte für die Transformatoren und Induktoren an J13, J14, J15, J18, J19, J20 und J21 entfernen.
7. Abschlussring des Werkstückkabels von J22 entfernen.
8. Die 3 Halteschrauben und die 4 Schrauben der Kühlkörperbaugruppe entfernen.
9. Die 5 Schrauben, die die IGBTs am Kühlkörper befestigen, entfernen. In der Strombaukarte befinden sich
Bohrungen, damit sie erreicht werden können.
10. Die Schraube vom Überspannungsschutzwiderstand auf der Oberseite des Kühlkörpers entfernen.
Vorsicht!: Statische elektrizität kann platinen Beschädigen.
• Beim Umgang mit Leiterplatten sind angemessene Vorsichtsmaßnahmen zu
treffen.
– Leiterplatten in antistatischen Behältern aufbewahren.
– Beim Umgang mit Leiterplatten sind geerdete Gelenkbänder zu tragen.

WARTUNG
powermax30 Wartungshandbuch 3-35
11. Die 2 unteren Drähte (beide sind weiß) vom EIN/AUS-Schalter trennen.
12. Die Einheit auf die Seite legen (Strombaukarte nach unten) und mit einem 8 mm Steckschlüssel die
Schraubenmuttern entfernen, die die roten und weißen Drähte sichern, welche unter der Baukarte zu den
Bolzen auf der Lüfterseite der Einheit entlanggeführt werden. Die Bolzen sind mit „RED” (rot) und „WHT”
(weiß) beschriftet.
Flachbandkabel
Brennerstart- und
Kappensensor
(J12)
J4, J5, und J6
J18
J19J20
J21
J13
J14
J15
Werkstückkabelanschluss (J22)
Halteschraube
Halteschraube
Halteschraube
Kühlkörperbaugruppenschraube
Kühlkörperbaugruppenschraube
Kühlkörperbaugruppenschraube
Kühlkörperbaugruppenschraube
IGBTBefestigungsschrauben
Weiß
Rot

WARTUNG
3-36 powermax30 Wartungshandbuch
13. Einheit wieder aufstellen. Alle getrennten Drähte aus dem Weg drücken.
14. Baukarte gerade aus der Stromquelle herausziehen.
15. Vor dem Installieren einer neuen Strombaukarte den Kühlkörper mit Isopropylalkohol reinigen. Sanft jegliche
Wärmeleitpastenrückstände wegrubbeln und dabei darauf achten, dass der Kühlkörper nicht verkratzt wird. Mit
einem sauberen Tuch nachwischen.
16. Eine dünne Schicht Wärmeleitpaste 0,05 mm dick (in etwa die Stärke eines Blattes Papier) auf allen IGBTs
verteilen.
17. Eine Schicht Wärmeleitpaste 0,05 mm dick auf dem Überspannungsschutzwiderstand verteilen, dabei am
Boden beginnen und nach oben ziehen (von den Stiften weg). Es ist wichtig zu vermeiden, dass Paste auf die
Stifte gelangt.
18. Rote und weiße Drähte, die an der neuen Strombaukarte angeschlossen sind, von der Strombaukartenseite
der Stromquelle zur Lüfterseite der Stromquelle durchschieben.
19. Kondensatoren an der Rückseite der Strombaukarte an den Bohrungen in der Mittelplatte der Stromquelle
ausrichten.
20. Strombaukarte gerade hineindrücken.
21. Die 2 weißen Drähte wieder an den EIN/AUS-Schalter anschließen.
22. Die 4 Schrauben der Kühlkörperbaugruppe und die 3 Halteschrauben wieder anbringen. Das Drehmoment für
diese Schrauben beträgt 17,28 kg cm.
23. Die zuvor in Schritt 10 vom Überspannungsschutzwiderstand entfernte Schraube wieder anbringen. Das
Drehmoment für diese Schraube beträgt 8,06 kg cm.
Anmerkung: Drehmomenteinstellungen von mehr als 8,06 kg cm können den Widerstand beschädigen.
24. Die 5 Schrauben, die die IGBTs am Kühlkörper befestigen, wieder anbringen. Die Drehmomenteinstellung für
diese beträgt 17,28 kg cm.
25. Drähte wieder an den Transformatoren und Induktoren an J13, J14, J15, J18, J19, J20 und J21 und den
Abschlussring des Werkstückkabels wieder an J22 anbringen. Mit einem Drehmoment von 23,04 kg cm
befestigen.
26. Brennerstart- und Kappensensor-Steckverbindung wieder an J12 und die Steckverbindungen an J4, J5 und J6
anbringen.
27. Flachbandkabel von der Steuerbaukarte zur Strombaukarte wieder anschließen.
28. Roten und weißen Draht an den Bolzen auf der Lüfterseite der Baukarte anbringen.
29. Unter Beachtung, dass keine Drähte eingeklemmt werden, Nomex-Barriere wieder anbringen und Abdeckung
wieder auf die Stromquelle schieben. Sicherstellen, dass die unteren Kanten sich in den Schienen befinden.
Griff über die Bohrungen in der Abdeckungsoberseite positionieren, dann die zwei Schrauben zur Sicherung
der Abdeckung verwenden.
30. Elektrischen Strom und Gaszufuhr wieder anschließen.

WARTUNG
powermax30 Wartungshandbuch 3-37
5. Typenschild vorsichtig vom Boden ablösen und zur Seite legen. Auf dem Typenschild befindet sich die
Seriennummer des Gerätes, es sollte also nicht verloren gehen oder zerrissen werden.
6. Das hölzerne Ende eines Tupfers, einen steifen Draht oder einen ähnlichen Gegenstand mit 2,3 mm
Durchmesser in jede der 5 Bohrungen auf der Strombaukartenseite des Bodens anbringen. Jeden von ihnen
so lange drücken, bis sich die Klammern lösen und man den Boden von der Mittelplatte abziehen kann.
7. Neuen Boden über die Metallplatte auf dem Boden der Stromquelle positionieren, so dass die
Schraubenbohrungen ausgerichtet sind. Die 6 Schrauben wieder anbringen und das Typenschild auf den
neuen Boden drücken.
8. Endkappen wieder anbringen. Es ist dabei sicherzustellen, dass die Schraubenbohrung in der Bodenklammer
an der vorderen Endkappe mit den Schraubenbohrungen in der Endkappe und der Stromquelle ausgerichtet
ist.
9. Unter Beachtung, dass keine Drähte eingeklemmt werden, Nomex-Barriere wieder anbringen und Abdeckung
wieder auf die Stromquelle schieben. Sicherstellen, dass die unteren Kanten sich in den Schienen befinden.
Griff über die Bohrungen in der Abdeckungsoberseite positionieren, dann die zwei Schrauben zur Sicherung
der Abdeckung verwenden.
10. Elektrischen Strom und Gaszufuhr wieder anschließen.
Austausch des Bodens
1. Strom auf AUS stellen, Netzkabel unterbrechen und Gaszufuhr unterbrechen.
2. Die zwei Schrauben vom Griff an der Oberseite der Stromquelle entfernen. Griff entfernen und dann die
Abdeckung von der Stromquelle abnehmen.
3. Stromquelle auf den Kopf stellen und die 6 Schrauben vom Boden entfernen.
4. Endkappen und Nomex-Isolierung entfernen. Zur Entfernung einer Endkappe siehe frühere Stelle in diesem
Abschnitt.
Schrauben
Bohrungen
Lage des
Typenschilds

powermax30 Wartungshandbuch 4-1
Abschnitt 4
TEILELISTE
Inhalt:
Stromquellenteile ......................................................................................................................................................4-2
Außen...............................................................................................................................................................4-2
Innenseite, Strombaukartenseite .....................................................................................................................4-3
Innere Lüfterseite .............................................................................................................................................4-4
T30v-Handbrennerteile .............................................................................................................................................4-5
Sicherheitsentscheidende Teile ................................................................................................................................4-6
Empfohlene Ersatzteile.............................................................................................................................................4-7
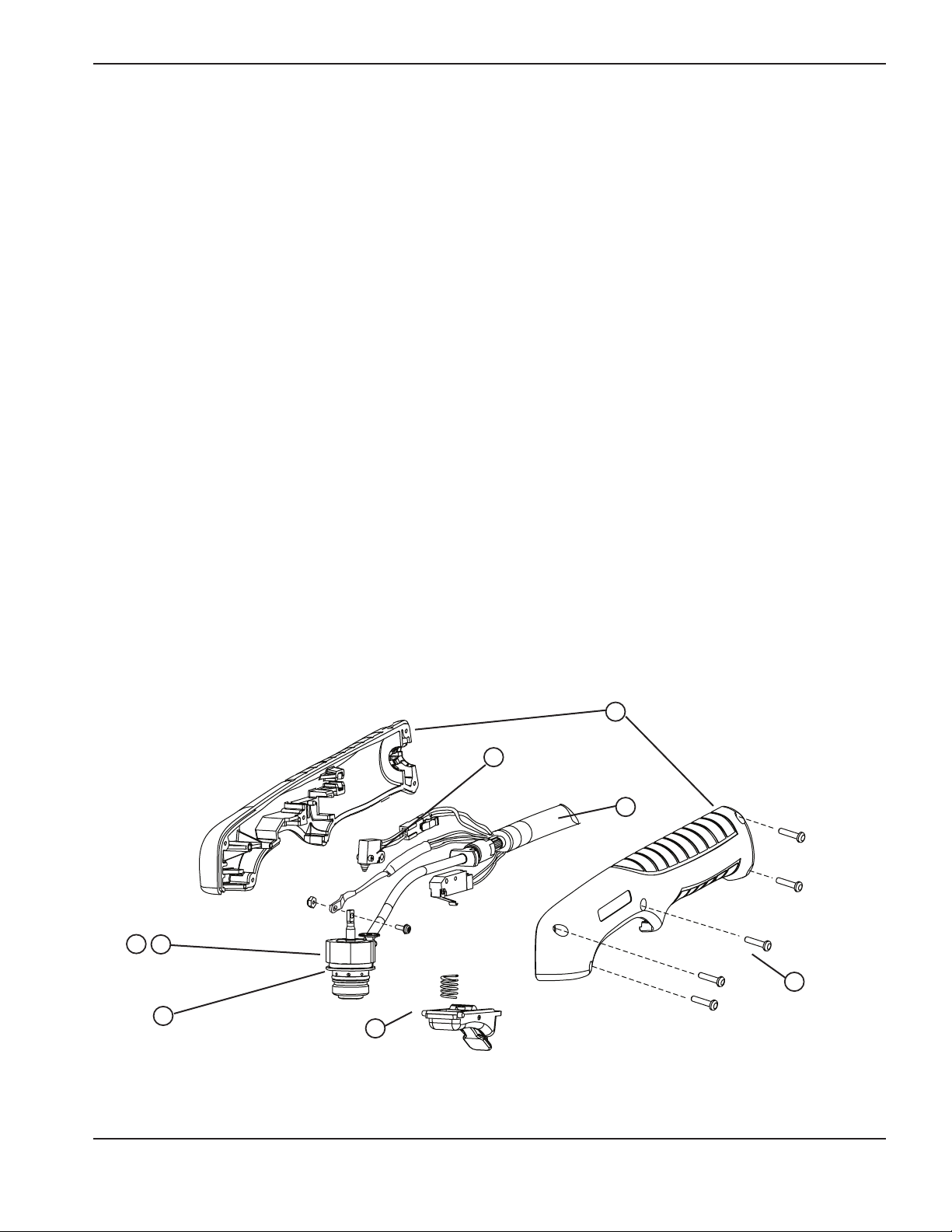
TEILELISTE
powermax30 Wartungshandbuch 4-5
1
T30v-Handbrennerteile
Artikel Teilenummer Beschreibung Menge
088001* T30v hand torch assembly with 15 ft (4.6 m) lead
1 228112 Kit: T30v torch head replacement 1
2 058503 O-ring 1
3 228109 Kit: Cap-off sensor replacement 1
4 228110 Kit: T30v torch head repair kit 1
5 228111 Kit: T30v torch handle replacement 1
6 075714 Screws: #4 x 1/2 SLTD Torx PAN, S/B 5
7 002244 Safety trigger and spring replacement 1
8 228113 Kit: T30v 15 ft (4.6 m) torch lead replacement 1
* Die obere Baugruppe enthält die folgenden Verschleißteile:
220478 Electrode 1
220479 Swirl ring 1
220483 Retaining cap 1
220480 Nozzle 1
5
3
8
4
1
6
2
7

TEILELISTE
4-6 powermax30 Wartungshandbuch
1
Sicherheitsentscheidende Teile
Original-Hypertherm-Teile sind die fabrikmäßig empfohlenen Teile für Ihr Hypertherm-Gerät. Für jegliche
Beschädigungen, die durch den Einsatz von Teile entstehen, bei denen es sich nicht um Original-Hypertherm- Teile
handelt, kann keine Hypertherm-Gewährleistung übernommen werden. Außerdem werden die nachfolgend
aufgelisteten Ersatzteile als sicherheitsentscheidende Teile angesehen, die ausschließlich durch Hypertherm-Teile
ersetzt werden müssen, damit Gewährleistung und alle Gerätezertifizierungen, einschließlich CE-, CSA-, GOSTund CCC-Zertifizierung, aufrechterhalten werden.
Teile-
Artikel nummer Beschreibung
1 228094 Kit: Power board (CSA) and subcomponents
228102 Kit: Power board (CE) and subcomponents
2 228105 Kit: 30 A magnetics
3 005112 Filter/regulator pressure switch
4 228106 Kit: Filter/regulator
5 228107 Kit: Fan
6 005605 Rocker switch
7 228142 Kit: Power cord, 115 VAC (CSA)
228140 Kit: Power cord, (CE)
8 228143 Kit: Strain relief
1
6
3
2
8
4
5
7

JTAG/EMULATION
CONNECTOR
GAS LOW
Vac r
Vbus
CONTROL PWA
041953 (Top Level) 4 LAYER
2.35"h x 5.00"w
26 POS
RIBBON
CABLE
ELECTRODE
NOZZLE
WORK
LEAD
POWER ON
"L/H LINE"
TEMP CAPOFF
"TSO"
POWER PWA
041950 (Top Level)
7.85"h x 11.20"w
2oz plated to 3oz
FAN
110CFM
24v/0.50A
GRNYELYELYEL
AMPS
SERIAL
DATA
Finv=42khz
PRESSURE SW
005112
Low Press=OPEN
CAP SW NC
START
LIFT to
Hipot
Fsw = 66khz
UVLO = 110vdc
(80vac)
OVLO = 495vdc
LOW INDUCTANCE
LAYOUT
TOP247
DSP 2801
4x25Mhz=100Mhz
0.78 x 0.78"
Stayout for
TEST CLIP
MTG4
MTG8
MTG3
CONTROL to
CHASSIS GND
98-264vac
47-63hz
PE
12AWG
LIFT to
Hipot
MTG6
Fpfc=28khz
Iline Limit
37.5arms
FACING COMPONENT SIDE of POWER BD
MACHINE
REAR
MACHINE
FRONT
L
R
Loutput 014309
L0=410uH
L30=270uH
Rdc20C=19mohm
POWER XFMR 014308
Twisted Leads
Lprim=0.75mH Rprim20C=4.8mohm
Rsec20C=10.5mohm
Lleak=0.5uH Typ
14T
Lpfc 014307
L0=350uh
L60=185uh
Rdc20C=21.5mohm
GAS SOL
24v/0.13A
11T
CORD
STD Unit 14/3 SO Dia=0.53"
CE Unit H05VV-F3G2.5 Dia=0.39"
y=2.09"-5.51"
0.472" MAX
Height Zone
5.51"-7.85"
1.72" MAX
Height Zone
y=0.00"-2.09"
1.00" MAX
Height Zone
EXTRA
SPACE
FOR
BD
DEPAN-
IZATION
MPX5700 BACK-UP
PRESSURE SENSOR
NOT USED
1
START
XFR
ERROR
CODE
/RESET or
HDR FLT
1 1
11414
14
15
1515
28 28
28
3333 3636
MUELLER
+
-
E36/18/11
CPLD
44 Pin
32 I/O
WHT WIRE
J12
J7
HEAT
SINK
J4 J5 J6
J16
J17
nc
CM Choke Installed
on CE unit only
-Vbus
375vdc
INPUT BRIDGES
PFC IGBT MODULE
INVERTER IGBT MODULE
OUTPUT DIODE and
PILOT ARC IGBT MODULE
OUTPUT CURRENT SENSOR
TRANSFER SENSOR
WHITE
-VBUS
12AWG UL1015 BLK
ORG
VIOLET
/GAS
RED
BLUE
375VDC
12AWG UL1569 WHT
12AWG UL1569 RED
/OVLO
IGBT TEMP
/INV SAT
/DRV FLT
/CAP UNBAL
/FAN
/SSR
/PFC OC
/UVLO
/PWRFLT
+24
/5 or 24 FLT
4
1
2
3
1
2
3
4
12
34
56
78
910
11 12
13 14
15 16
17 18
19 20
21 22
23 24
25 26
1
2
3
4
8
7
6
5
M
+
-
IN1
IN2
IN3OUT3
OUT1
OUT2
1
2
3
4
5
6
7
89
10
11
12
13
14
15
16
IN2
2
DIAG
3
GND
4
GND
5
GND
6
GND
7
VS
8
IN3
9
EN
11
OUT1
19
IN1
1
OUT2
18
GND
17
GND
16
GND
15
GND
14
OUT3
13
OUT4
12
PRG
20
IN4
10
123
IN OUT
GND
IN15
15
IN9
9
IN8
8
IN7
7
IN13
13
IN12
12
IN11
11
IN10
10
IN6
6
IN16
16
IN3
3
IN2
2
IN1
1
IN5
5
IN14
14
IN4
4
IN17
17
IN18
18
IN19
19
TDO
40
SPI EN
32
TCK
42
TDI
43
VCC
44
TMS
41
OUT1
20
OUT2
21
OUT3
22
OUT4
23
OUT5
24
OUT6
25
OUT7
26
OUT8
27
I/O
28
SPI IN
31
SPI CLK
30
SPI OUT
29
1
2
3
L
2
F5X
3
D
7
C
1
S
4
1
2
3
4
IN OUT
GND
AC
AC
-
+
12
34
56
78
910
11 12
13 14
15 16
17 18
19 20
21 22
23 24
25 26
M
+
-
IN1
IN2
IN3
OUT3
OUT1
OUT2
\CS
1
SD0
2
\WP
3
VSS
4
VCC
8
\HOLD
7
CLK
6
SDI
5
M
+
-
IN1
IN2
IN3
OUT3
OUT1
OUT2
1
2
3
4
8
7
6
5
1
3
5
7
9
11
13 14
2
4
6
8
10
12
AC
AC
-
+
1
2
123
IN
15
IN9V-
8
IN
7
IN
13
IN
12
IN
11
IN
10
IN
6
V+
16
IN
3
IN
2
IN
1
IN
5
IN
14
IN
4
Description
Size Drawing Number Rev
Sheet of
File Name
Box 5010 Hanover, NH 03755-5010 (603) 643-3441
THIS DRAWING AND ALL
INFORMATION CONTAINED
THEREON IS CONSIDERED
PROPRIETARY AND MAY
NOT BE USED FOR
MANUFACTURING OR
FABRICATION PURPOSES
WITHOUT PERMISSION
FROM HYPERTHERM, INC.
Drawn By
Approved By
Date
Date
HYPERTHERM
Stock Number
15
4W
J21
0.01uF
300vac
0.33uF
630VDC
2200uF
250VDC
+
10 150J
t
60A 600V
PFC DIODE
J2
HCPL-7840
+
-
+
-
VDD1
VIN+
VINGND1 GND2
VOUT-
VOUT+
VDD2
CM Choke 16arms
3.9uF
630VDC
LAX100-NP
M5 in Plastic
J13
15
4W
L9338MD
-
+
M5 in Plastic
15 ohm
50W TO247
4.7nF
300vac
Y2
t
-
+
3.3 nF
1000VDC
CPLD
15
4W
CLAMP DIODE
60A 600V
J14
WHT
t
4.7nF
300vac
Y2
2200uF
250VDC
+
600V
90A
1200V
35A
75k 2w
J20
16A/250V DPST
2.21M
1200V
35A
LAX100-NP
.01uF Y2
300vac
2.7uF
630VDC
600V
90A
EE PROM
2.7uF
630VDC
27K
3W
LAX100-NP
HCPL-7840
+
-
+
-
VDD1
VIN+
VINGND1 GND2
VOUT-
VOUT+
VDD2
J15
1200V
35A
RED
J18
3.9uF
630VDC
0.33uF
630VDC
J19
600V
90A
20K
3W
27K
3W
6.8uf 300vac X2
-
+
J22
J1
720
CW
18 INVU
COM INVU
+9
18T
+24
18PA
COMPA
COMT
18REG
+3.3
+3.3
+5
INV IPRIM
SSR
FAN
GAS
/PFC DESAT
/INV DESAT
PFC PWM
INVU PWM
INVL PWM
PA
/PA DESAT
CAPON
GAS OK
REDUNDANT START
START
GAS
SSR
FAN
INVU PWM DRV
INVL PWM DRV
PFC PWM DRV
PA DRV
5
5
4
4
3
3
2
2
1
1
D D
C C
B B
A A
D
11
ELEC SCHEM:PMX30 SYS
013-2-364 013364B1 A
10-6-06
10-5-06 013364