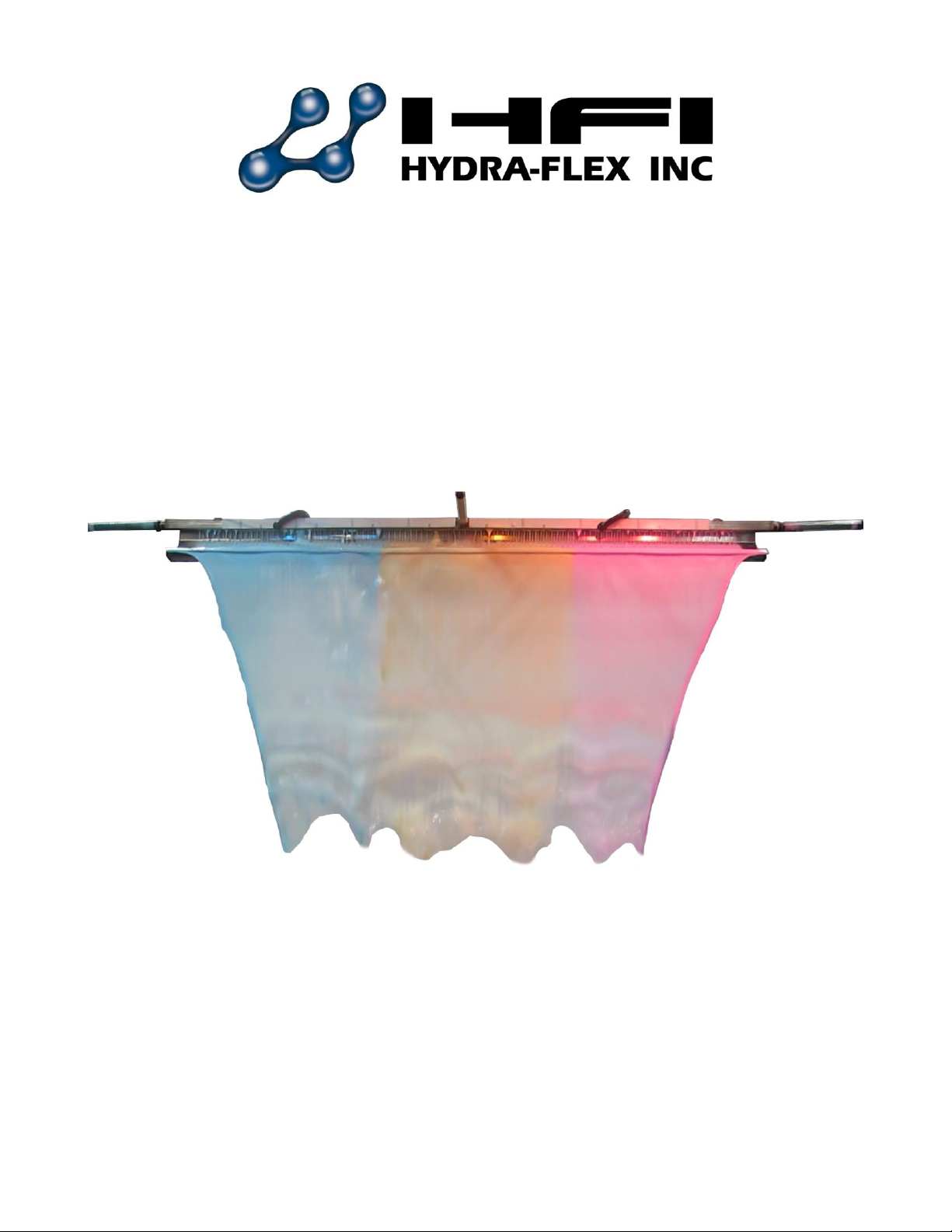
Tsunami™ Dispensing Arch
Using
™
AQUA-LAB
Chemical Dispensing System
REV A
© Hydra-Flex Inc 2011
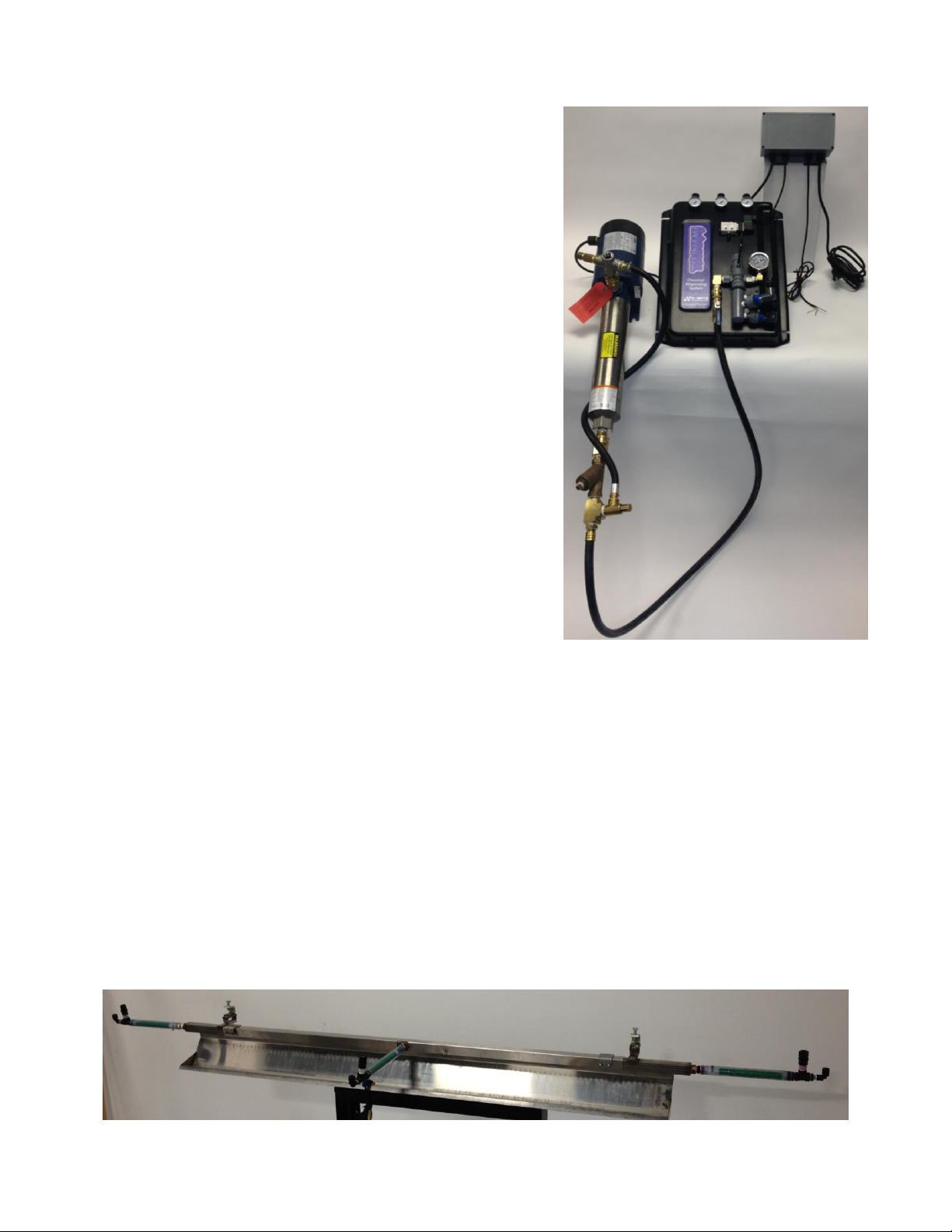
Chemical Dispensing Specifications
1. Operating water pressure: 200 psi (Factory set)
2. Maximum water source temperature 140° F
3. Operating ambient temperature: 40-120° F
4. Electrical supply
a. 120 / 208 Single Phase
b. 1.5 hp pump 20 amps @ 120 volts or 10 amps @ 208
volts
5. Operate valves with 24VAC, 24VDC, 120VAC
a. < .5 amp
6. Water supply
a. 3/4” ID flooded inlet required
b. Inlet pressure: 2-60 psi
7. Air supply
a. Pneumatics inlet pressure: 60 - 100 psi
b. 3/8” feed per system
c. 20 CFM @ 100 psi supply
d. 3 x 3/8” poly lines to applicator
8. Chemical Solution lines
a. 3x ½” poly lines to applicator
9. Space requirements:
a. AQUA-LAB Systems
i. Valve panel – 1.5’ wide x 2’ tall
ii. Pump – 1’ wide x 4’ tall
b. Pump assemblies – pumps need to be within 6’ of the
system to allow connection with the connection hose
included (longer connections can be run with customer
supplied hose)
c. Electrical enclosures
i. Motor starter – 12” wide x 6” tall
Tsunami Applicator Specifications
1. Operating water pressure: 100 psi max
2. Pneumatics inlet pressure: 0-60 psi
3. Maximum water source temperature 140° F
4. Operating ambient temperature: 40-120° F
5. Water supply
a. 4 – 10 GPM
b. Inlet pressure: 10-65 psi
6. Air supply
a. 3x 3/8” feed per system
b. ~20 CFM
7. Solution lines
a. 3x ½” poly lines to applicator
8. Mounting requirements
a. This Applicator requires an arch to mount to
b. Must be level
c. Recommend roughly centering on car or slightly favoring the driver’s side
© Hydra-Flex Inc 2011
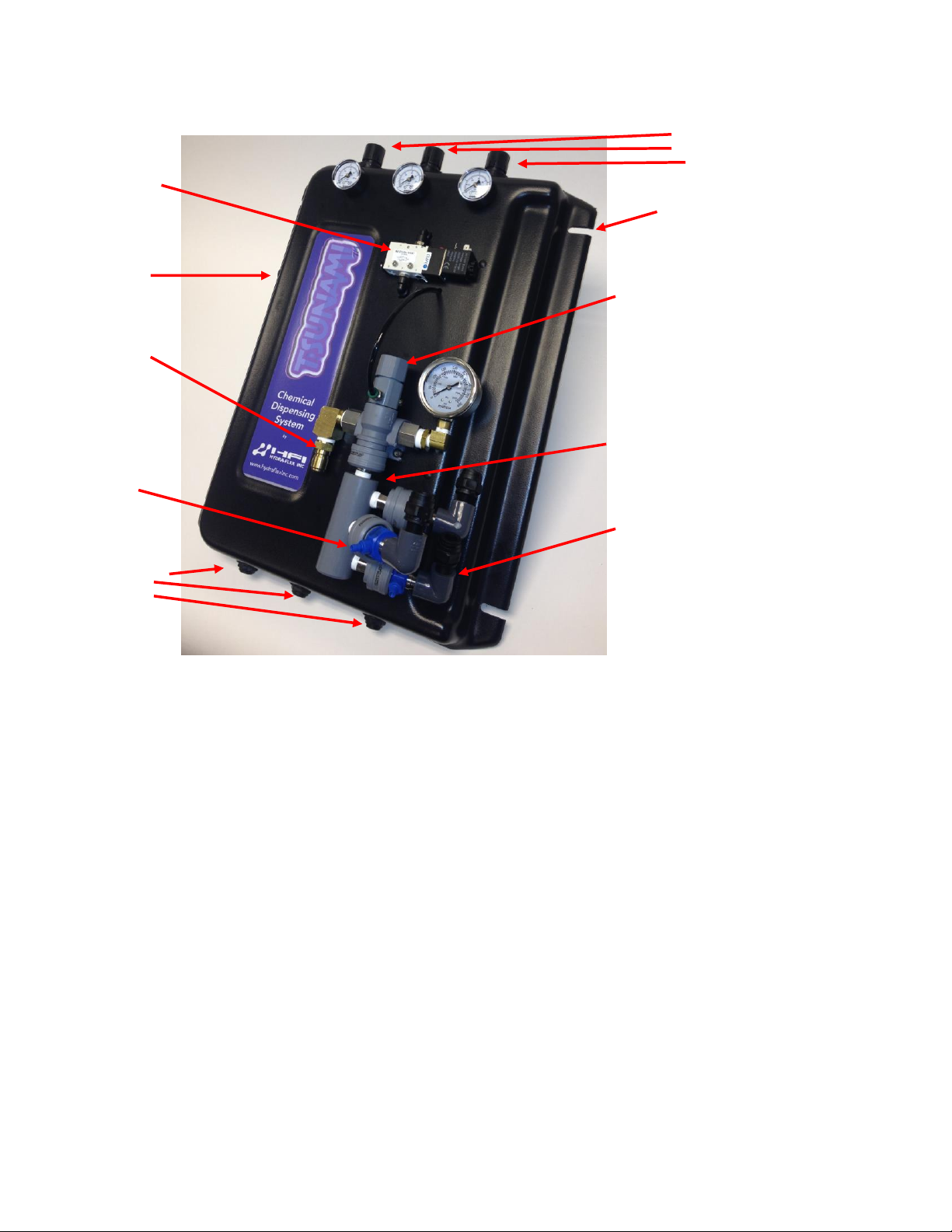
System Component Identification
Air Regulator 1, 2, 3
Air Solenoid
Valve Board Mounting Slots
Air Inlet
(3/8” Poly) Pneumatically
Actuated Valve
Water Feed
From Pump
(200psi)
Triple Foam
Manifold
Chemical
Injector
3x Outlet to Applicator
Air Outlet 1,
2, 3
© Hydra-Flex Inc 2011
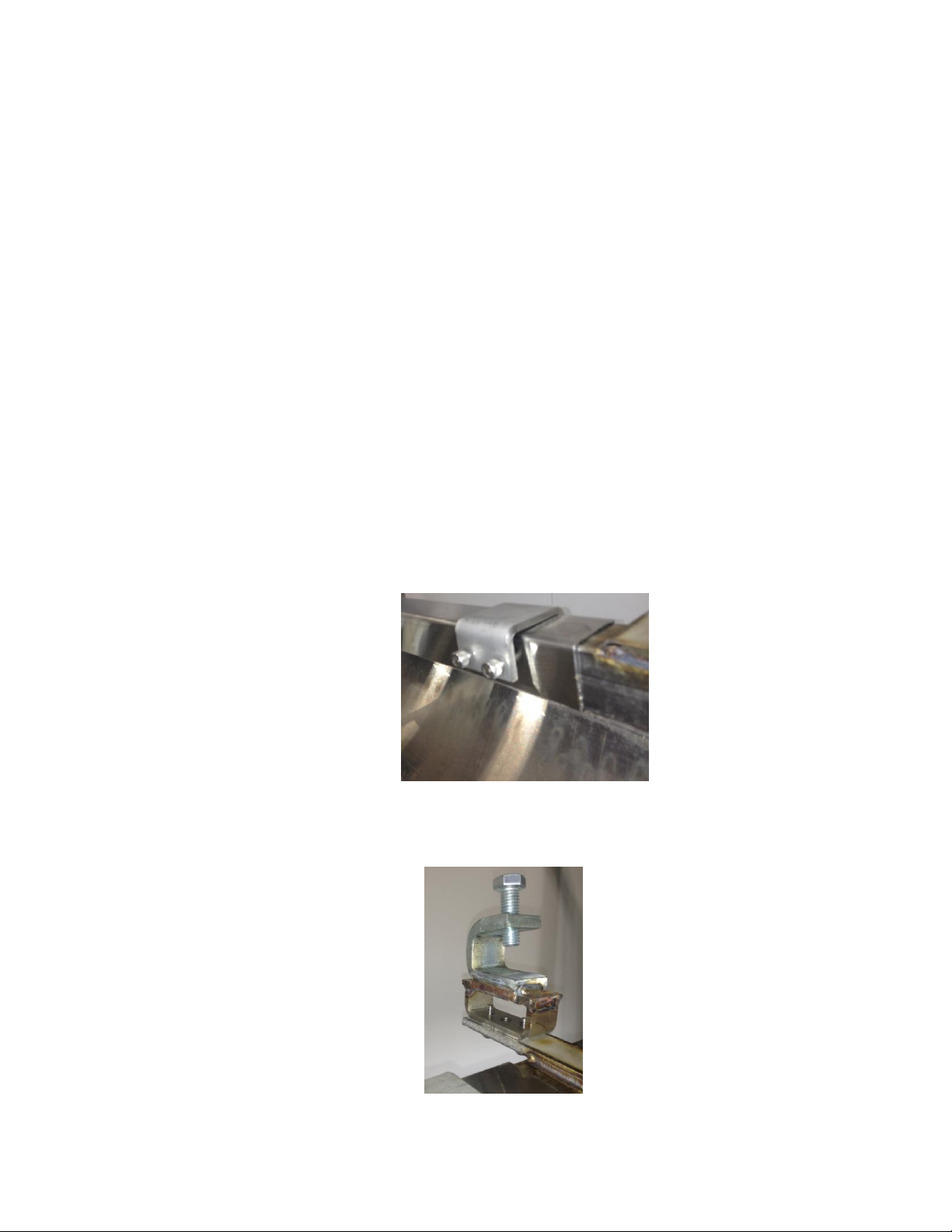
1. Mount pump using 4x 3/8” wedge Anchors provided (3/8” hammer drill required)
a. Mounting slots 3.75”W x 3.38”H
2. Mount electrical box and delivery panel using Tapcon anchors provided (5/32” hammer drill
required)
a. Electrical Box – Hole spacing 7.4”W x 3.5”H
b. Panel – Slot spacing 17.5”W x 15”H
3. Run ¾” water line to the inlet of the pump
4. Close the ball valve on the pump outlet line and open the feed to the pump
5. Point the outlet line towards a drain or a container and open the ball valve until water is flowing
freely to prime the pump.
6. Close the ball valve and attach the quick connect to the chemical delivery panel and re-open
the ball valve
7. Run a 3/8” poly airline to the chemical panel and supply with at least 60psi of air pressure
8. Wire the signal wire from the provided electrical box to the box with the signal to fire the
application
9. Connect the DIN I solenoid cable from the electrical box to the air valve.
10. Check that relay installed in the electrical box corresponds with the signal voltage from the car
wash controller (120VAC relay is installed from the factory, 24 VAC and 24VDC relays are
included inside the electrical box)
11. Plug 120VAC power cord into a circuit with 20 amp available capacity
12. Install or identify an existing arch to mount the Tsunami applicator to
IMPORTANT!! The Tsunami applicator requires a level sturdy arch or other
mounting feature as it does not include one
13. Clamp the rain bar into the trough using the provided clamps as shown
14. Center the applicator on the largest vehicle that can safely pass thru the tunnel
15. Make sure that the applicator is level side to side
16. Securely attach the applicator to the arch using the mounting tabs and / or the included
brackets.
17. Run and connect three ½” polyflow lines for the chemical solution and three 3/8” polyflow lines
for the foaming air from the chemical delivery panel to the foam generators on the applicator.
© Hydra-Flex Inc 2011