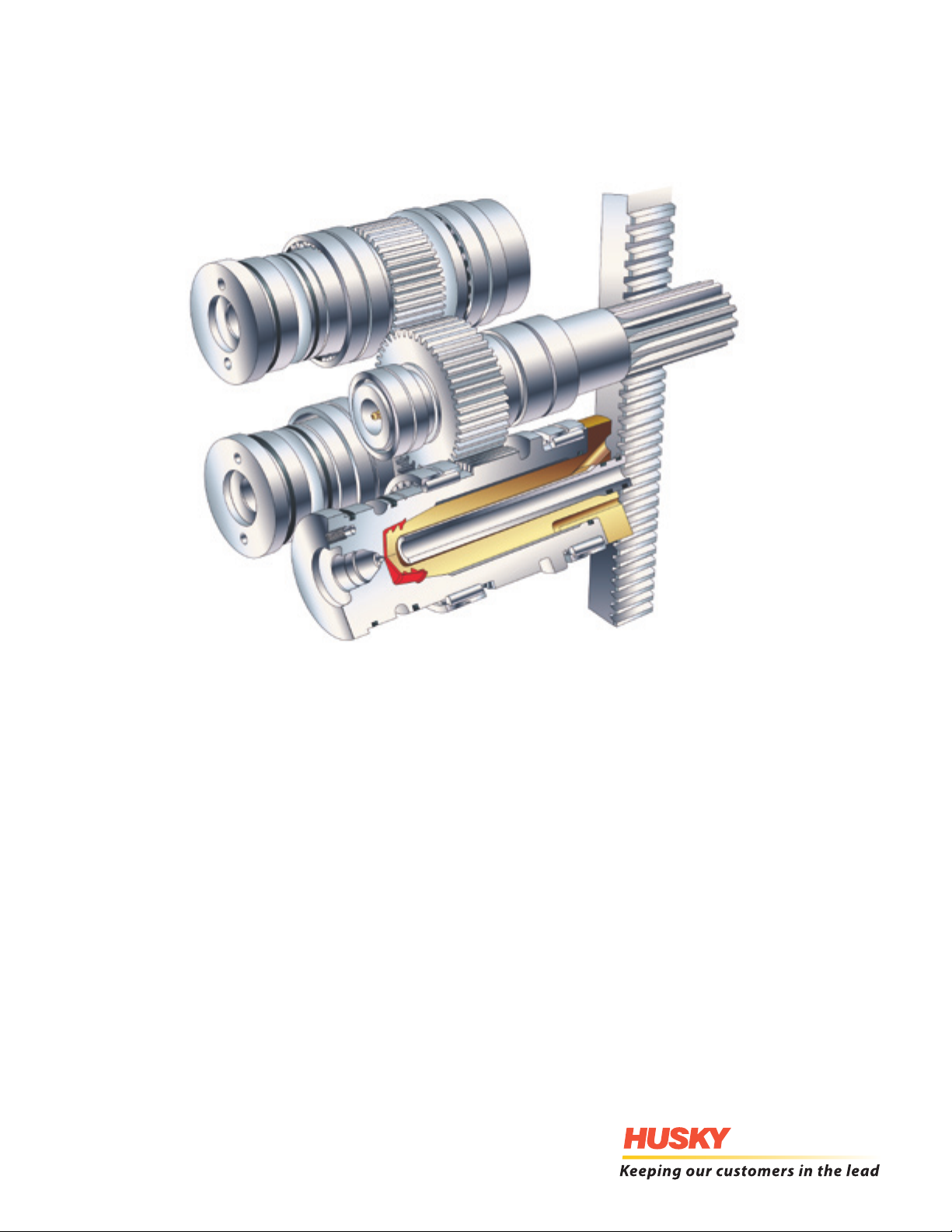
Rotating Ratchet Ring
Advanced Unscrewing Technology
Our Rotating Ratchet Ring (RRR) design offers a unique
solution for unscrewing closures. In conventional unscrewing
molds, the core rotates as the stripper plate moves forward,
releasing the closure thread for ejection. With RRR technology,
a rotating ratchet ring unscrews the closure from a stationary
core. This design offers several important benefits.
FASTER CYCLES
Since the closure is unscrewed from a stationary core, a
small diameter drive gear is not necessary on the core. This
permits larger cooling channels and the use of more thermally
conductive core materials. Also, the ratchet ring gear incorporates a unidirectional clutch to prevent the ratchet rings
turning in the reset direction. In addition the reverse cam
permits rack reset after mold close to further reduce cycle time.
LESS MAINTENANCE
Rotary seals, a common source of leakage and corrosion
damage, are not required with RRR technology; the stationary
core utilizes conventional o-rings. Together with built-in
spring bumpers, this design also ensures that the core and
ratchet ring tapers are never in contact with each other while
rotating, virtually eliminating taper wear.
COMPLETE MOLD BASE
We provide a fully engineered complete mold base-including
hydraulic cylinders, air pistons, racks, cams, a hot runner,
and the drive system for the ratchet rings. This allows the
moldmaker to concentrate on the molding surfaces.
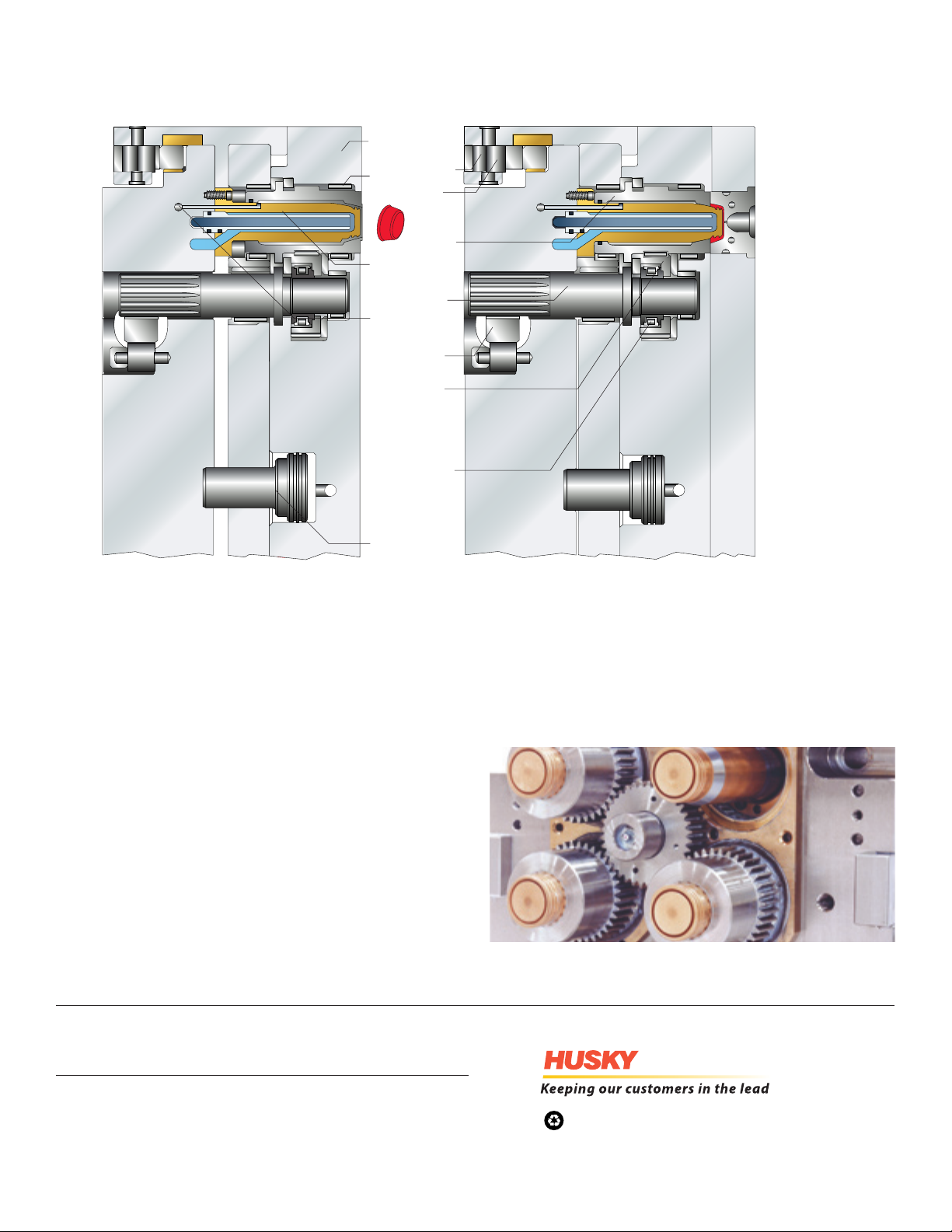
MOLD OPERATION
Stripper
plate
Bearings
Stationar
y
core
Compressed
air
Ca
m
follower
Ca
m
Rotating
ratchet
ring
Pinion
Rack
Gear
Unidirectional
clutch
Air piston
STAGE 1
1. As the mold opens, air pistons move the stripper plate
forward, taking up a small space between the cam and
cam follower. This provides initial clearance between the
core tapers and the rotating ratchet rings.
2. A hydraulic cylinder (not shown) pulls the cams and
rack(s), driving a series of pinions. Each pinion drives a
cluster of rotating ratchet rings that turn the closures
by means of small teeth embedded in the skirt of the
closure. The forward movement of the stripper plate
maintains this grip as the part is unscrewed. The rate at
which the stripper plate moves is controlled by the cam
and cam follower design.
3. At the end of the stripper plate movement, compressed
air aids in part ejection.
www.husky.ca
www.hotrunners.com
Americas & Asia
288 North Road
Milton, Vermont, USA 05468
Toll Free (800) 516 9590
Tel. (802) 859 8000
Fax (802) 859 8321
Europe
Hot Runner Mold Building
B.P. 231, L-3403 Dudelange,
Luxembourg
Tel. (352) 52 11 51
Fax (352) 52 11 5 4458
STAGE 2
1. Prior to mold close, the air pistons return the stripper
plate to close position before the rack/cam mechanism is
repositioned.
2. The unidirectional clutch in the pinion’s gear allows the
rack and cam structure to be reset after the mold closes.
All major components are accessible from the front for easy maintenance.
Rec ycled pape r, contai ning a mi nimum of 2 0% po st co nsume r fib er.
®/©2 003 H usky Inje ction Mold ing S ystem s Ltd. Printe d in Canad a. May 2003
Husk y ac tively prot ects its techni cal and d esign innov ations thro ugh a glo bal i ntelle ctual prop erty
stra tegy. Hu sky c urren tly h as mo re th an 90 0 pat ents and p atent appl icatio ns wo rldwi de.
The equip ment shown in t his p ublic ation may be co vered by o ne or more of these paten ts.
“Husky” is a trademark owned by Husky Injection Molding Systems Ltd.
Oth er co mpany, pr oduct , and servi ce na mes m ay be trad emark s of their resp ectiv e own ers.