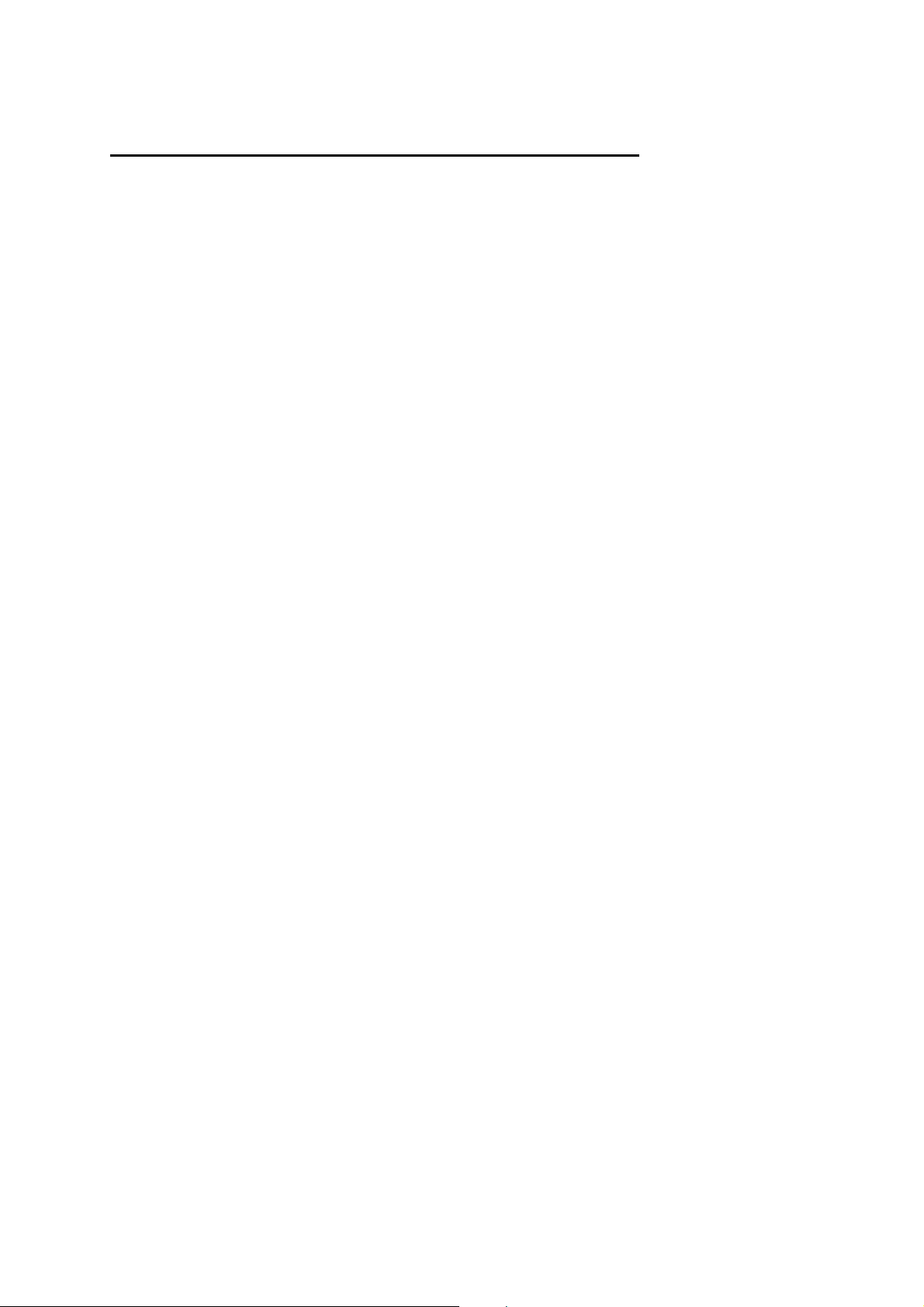
SYSTEM DESCRIPTION TPM KOMFORT ECU
1.1 TPM FUNCTIONALITY
The main function of the TPM system is to monitor all four tyre pressures during driving
operation and at standstill.
LF trigger transmitters request periodically the wheel electronics to send datagrams
containing information about tyre pressure and temperature. The system is able to detect the
wheels fitted to the vehicle and their relative installation positions. This is achieved by
analysing the triggering position and by performing a statistical analysis of the received
information.
1.1.1 TPM System Interfaces
The trigger transmitter interfaces with the TPM Komfort ECU by means of a dedicated &
proprietary LIN bus. The TPM control unit diagnoses the individual system components.
The TPM control module interfaces with the Driver Information Panel (DIP) and the
Infotainment Unit (ZAB) by means of the Komfort CAN network.
1.1.2 TPM User Interface
The interface with the user is made via the ZAB and the DIP. The DIP shows to the driver
any warnings in the form of TPM specific symbols and text. The ZAB presents information
regarding the state and condition of each tyre pressure. The driver requests a system
calibration (system learning) through the ZAB (shown below).
1.1.3 TPM System Configuration
There are two possible system configurations, dependent on radio frequency (RF) used:
- 315 MHz configuration for some Asian and African markets
- 433 MHz configuration for ROW (including NAR & Europe).
1.2 WHEEL MANAGEMENT
1.2.1 Overview
The TPM system detects automatically the wheels fitted into the vehicle. The system
performs a statistical analysis of the received data in order to recognize which wheel
electronics and in which position are the wheels installed in the vehicle.
In order to prevent other vehicles with TPM systems from causing interference at standstill,
the "learning" or calibration is performed only when the vehicle is in motion.
The TPM system achieves wheel management by performing the following actions:
1) Wheel Detection During this phase the system wheels are learned. If all wheel
electronics respond with at least 2 datagrams to a trigger
request, then all wheel electronics are marked as system
wheels
2) Wheel Position Detection The wheel position detection is done by using the response to
the trigger signal. Once the positions of the wheel electronics
have been clearly identified, the positions are stored in a nonvolatile memory (EEPROM)
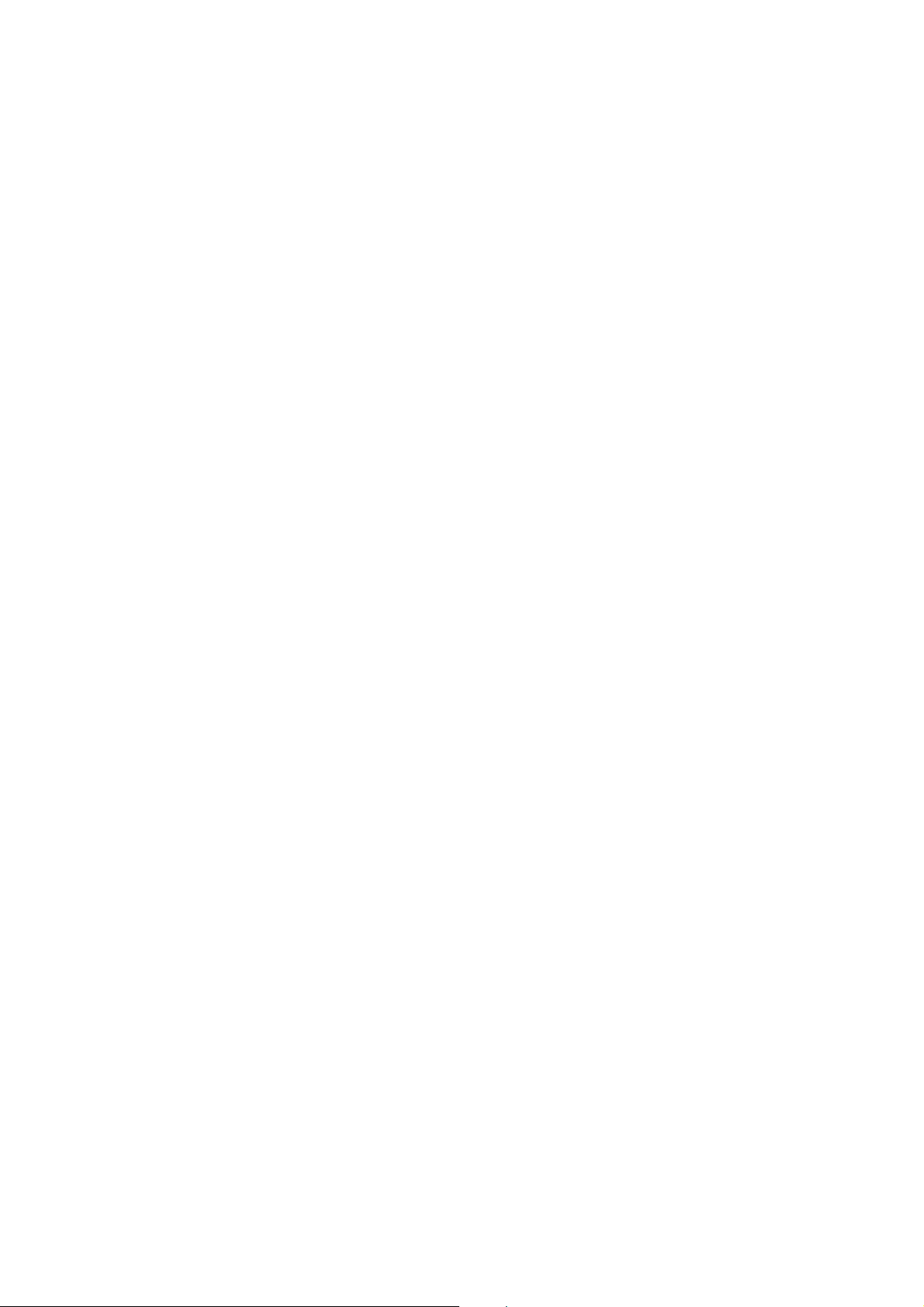
3) Running Wheel Detection In order to support the wheel position detection a distinction is
made between the spare wheel and the running wheels. This is
achieved by using the information from the roll switch in the
wheel electronics.
4) Confirmation The confirmation phase enables the system to learn
automatically any change of the wheel positions. This check is
performed while the vehicle is in motion in order to avoid
potential timeout because of non-reception while the vehicle is
at standstill.
1.2.2 Wheel Detection
With the aim to perform wheel detection the system counts the number of responses to a
trigger request. The system detects that a wheel is a system wheel when a wheel electronic
(with its unique ID) has given at least two positive responses (2 or more) to trigger events at
the same position and when the control unit has analyzed the result.
The system shall detect the wheels fitted within 3 minutes from the moment the vehicle is set
in motion. If at least one of four wheels are not detected within three minutes then a DTC is
recorded in memory and “System Fault” message is issued to the kombi.
1.2.3 Wheel Position Detection
An association matrix (ZOM), relating wheel electronics position and ID, is used to count the
number of immediate responses that a wheel electronic (with unique ID) gives to the request
of a trigger device. The counting is done in increments of 1.
Since the effective low frequency radio transmission sphere of a trigger device is limited, only
one wheel electronic will normally respond to the request signal.
The wheel position detection is completed when:
- There is exactly one wheel ID with maximum counter value for each of the trigger
positions, and if this counter value is higher or equal than a preset limit
(parameter)
- The four running wheels have been clearly identified, i.e. no counter value for a
certain trigger position will be higher than a preset value in the init- phase after
the TSS sees first power supply.
The status “Assigned” is then reached.
The management of a spare wheel is not implemented.
1.2.4 Running Wheel Detection
The information of the roll switch contained in the wheel electronics is used to identify the
running wheels.
The roll switch is designed in a way so that the wheel rotation will be detected above a
tangential speed of typically approx. 20 to 30 km/h. This causes the corresponding bit in the
wheel electronics datagram to be set to 1. The running wheel bit is used to distinguish
between running wheel and spare wheel (wheel at rest).