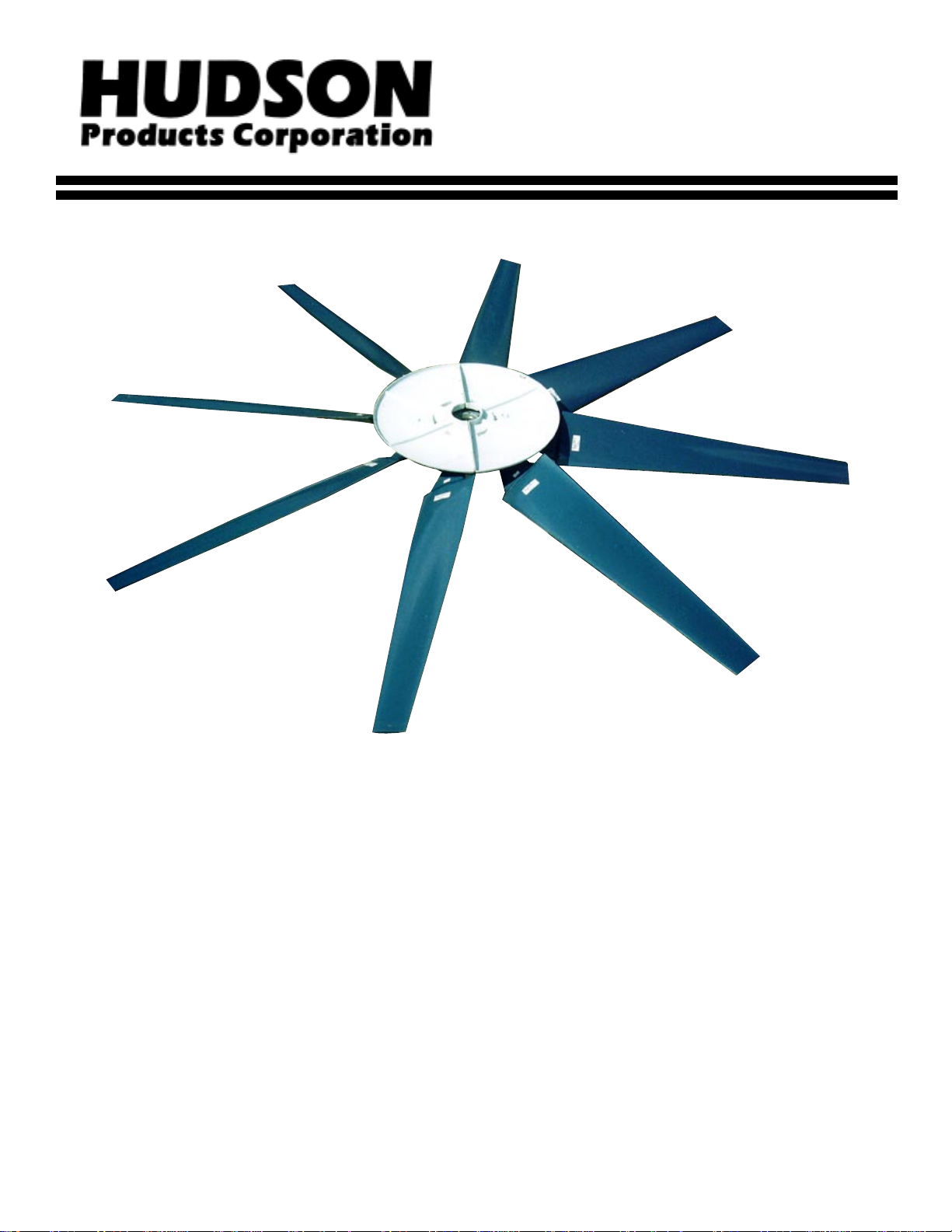
Tuf-Lite
Tuf-Lite II
and
Fans
8000 Series Hub
INSTALLATION MANUAL
Adjustable Pitch Fan Assembly
34’ through 40’ Diameter
Hudson Tuf-Lite® and Tuf-Lite II® fan blades
Hudson Tuf-Lite® (black) fan blades are made from fiberglass reinforced epoxy resin having a very high
strength-to-weight ratio and corrosion resistance (not shown).
Hudson Tuf-Lite II® (blue) fan blades are made from fiberglass reinforced vinyl-ester resin having a very
high strength-to-weight ratio and superior ultra-violet and corrosion resistance. An elastomeric blade/holder
joint cover (not shown) prevents moisture from entering the blade (shown above).
The individually balanced blades can be replaced independently – matched sets are not required.
Installation Manual 8000 Page 1 of 8 January 2004
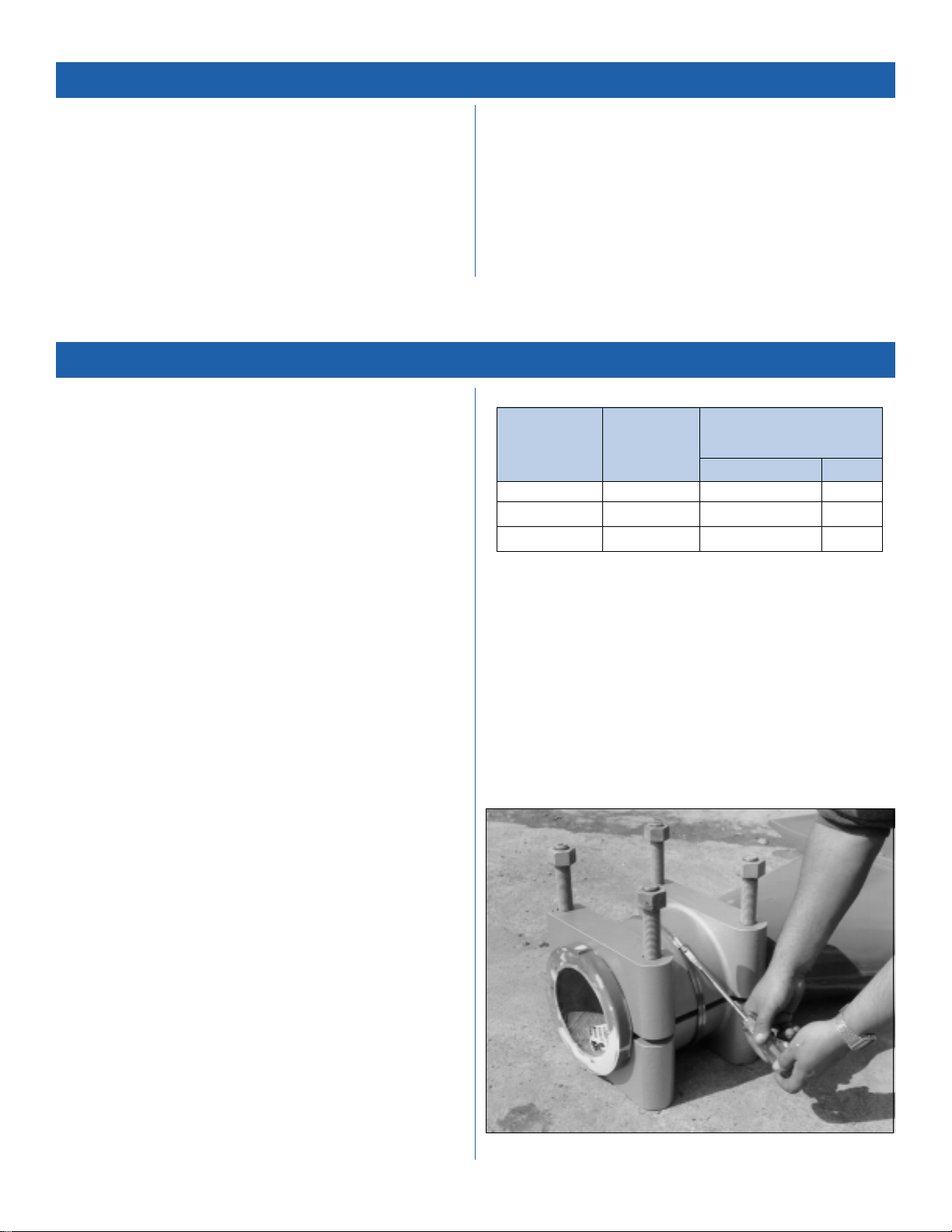
RECOMMENDED TOOLS
z Long T-Handle Allen Wrench Set (3/16” to 3/8”)
z Medium Size Flat Head Screw Driver
z Brass Ball Peen Hammer
z Flat Bastard File
z 240 Grit Sand Paper
z Anti-Seize Lubricant
z WD-40
z 12” Crescent Wrench
INSTALLATION PROCEDURES
ASSEMBLY WITH BUSHING
Clean all mating surfaces between hub, bushing and shaft. If there
is no shoulder on shaft to prevent bushing from sliding down shaft,
slide spacer/sleeve (not provided) on shaft before bushing. Slide
bushing and key onto shaft until flush with end of shaft. Lock W-2
bushing on shaft by tightening set screw in flange with 1/4” Allen
Wrench. (Note: setscrew is not present on all bushings) Line up
key and set hub on bushing. Engage the four (4) 3/4” cap screws in
flange of bushing into hub spool. Using a torque wrench with a
1-1/8” socket, tighten evenly to recommended standard of 250 ft-lb
(dry).
z Shop Towels
z Exact-A-Pitch
z 25 ft. Measuring Tape
z Pencil or Marker
z Open/Box End Wrench Set (1/2” - 1-1/2”)
z Socket Set for 1/2” Drive (1/2” - 1-1/2”)
z Torque Wrench(s) Rated for 0-250 ft-lb.
®
Digital Protractor (P/N 62375)
Torque Value
Cap Screw Socket (ft-lb)
Size Size Lubricated Dry
5/8” NC 15/16” 100 110
3/4” NC 1-1/8” 125 130
1” NC 1-1/2” 150 160
NOTE: Retaining arrangement varies with gear shaft design.
ASSEMBLE BLADE CLAMP ON BLADE NECK
ASSEMBLY WITH STRAIGHT SHAFT
(NO BUSHING)
Clean all mating surfaces between the hub and the shaft. If there is
no shoulder on shaft to prevent hub from sliding down shaft, slide
spacer/sleeve (not provided) on shaft before hub or use a thrust
retainer (optional equipment) on top of hub. Install key in shaft.
Line up key and keyway and set hub on shaft. Tighten two (2) set
screws in hub.
ASSEMBLY WITH TAPERED SHAFT
(NO BUSHING REQUIRED)
Clean all mating surfaces between hub and shaft. Coat all mating
surfaces with an anti-seize or lubricating compound.
Align keyways and install hub. Install retainer plate and cap screw(s)
with lock washer(s). Shaft size determines what size cap screw is
necessary. Using a torque wrench with a socket, evenly tighten cap
screw to recommended standard per table below.
Remove blade clamp studs, lock washers, and blade clamp halves
from hub. Assemble blade clamp halves over groove in blade neck,
with thick leading edge to left and thin trailing edge to right as you
stand at end of blade. Use a band clamp to hold the two blade
clamp halves in position on the blade for installation in the hub
body (See Figure 1).
Figure 1
Installation Manual 8000 Page 2 of 8 January 2004
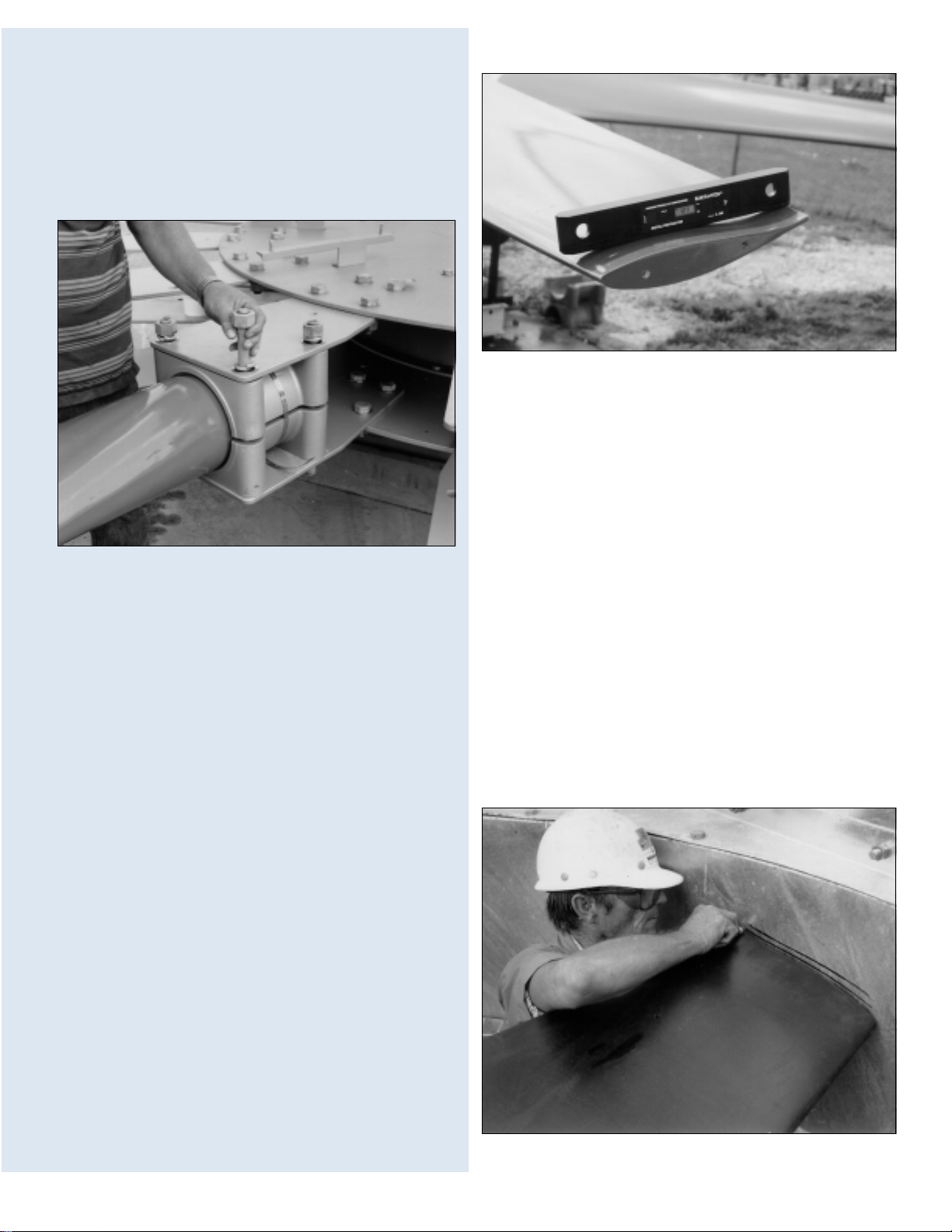
INSTALL BLADE INTO HUB
Hoist the blade into position. (Blade and clamp halves weight about
300 lbs.) Slide blade clamp into blade arm plates and install four
(4) blade studs, eight (8) lockwashers and eight (8) nuts (See
Figure 2). Tighten lightly.
Figure 3
When bolts are tightened, hold a pencil against top end of blade and
mark the level onto a fixed object, such as a pole or the fan ring.
Install remaining blades at same place as first blade, following procedures above. After tightening bolts, mark top end of each blade
in same place first blade was marked. If marks differ by 1-1/2”or
more, adjust blade.
Figure 2
SET PITCH AND TRACK
Use Hudson EXACT-A-PITCH® digital protractor (Shown in Figure 3) or a bubble protractor to set blade pitch. Mount protractor
on a flat bar as a base and place it approximately 1” from tip of blade.
Note pitch on protractor. Rotate fan 360⋅, noting high and low pitch
readings. Locate place where pitch reading is a mid-point between
high and low readings, and set pitch at that point.
Rotate blade in clamp until digital protractor shows specified pitch
angle to within ±0.2⋅. (Fan pitch angle is shown on fan specifica-
tion sheet for design duty.)
After desired pitch angle is set, raise and lower end of fan blade
and find midpoint of blade travel. Hold blade at the midpoint. Pull
blade back so that it sits against blade clamp. Push blade to the
right to remove all slack.
Use torque wrench to tighten clamp bolts to recommended standard of 280 ft-lb (lubricated) or 300 ft-lb (dry). Recheck pitch
setting. Blade must be set within ± 0.2⋅ of desired pitch angle.
Tighten clamp bolts evenly. DO NOT OVER-TORQUE CLAMP
BOLTS.
CHECK TRACK
After fan is installed in fan ring, outline top end of each blade onto
fan ring with a marker. The difference between levels of highest
and lowest outlines should not be more than 1-1/2”. Correct blade
track by loosening clamp bolts and adjusting blade to match track
of other blades. Retighten bolts and recheck track and pitch angle
setting. Retighten blade clamp bolts to recommended standard of
280 ft-lb (lubricated) or 300 ft-lb (dry) torque (See Figure 4).
Figure 4
Installation Manual 8000 Page 3 of 8 January 2004