
SD4030B3-M02D
Bipolar micro step driver for 2-phase stepping motor
Low cost
Low vibration
RoHS compliant
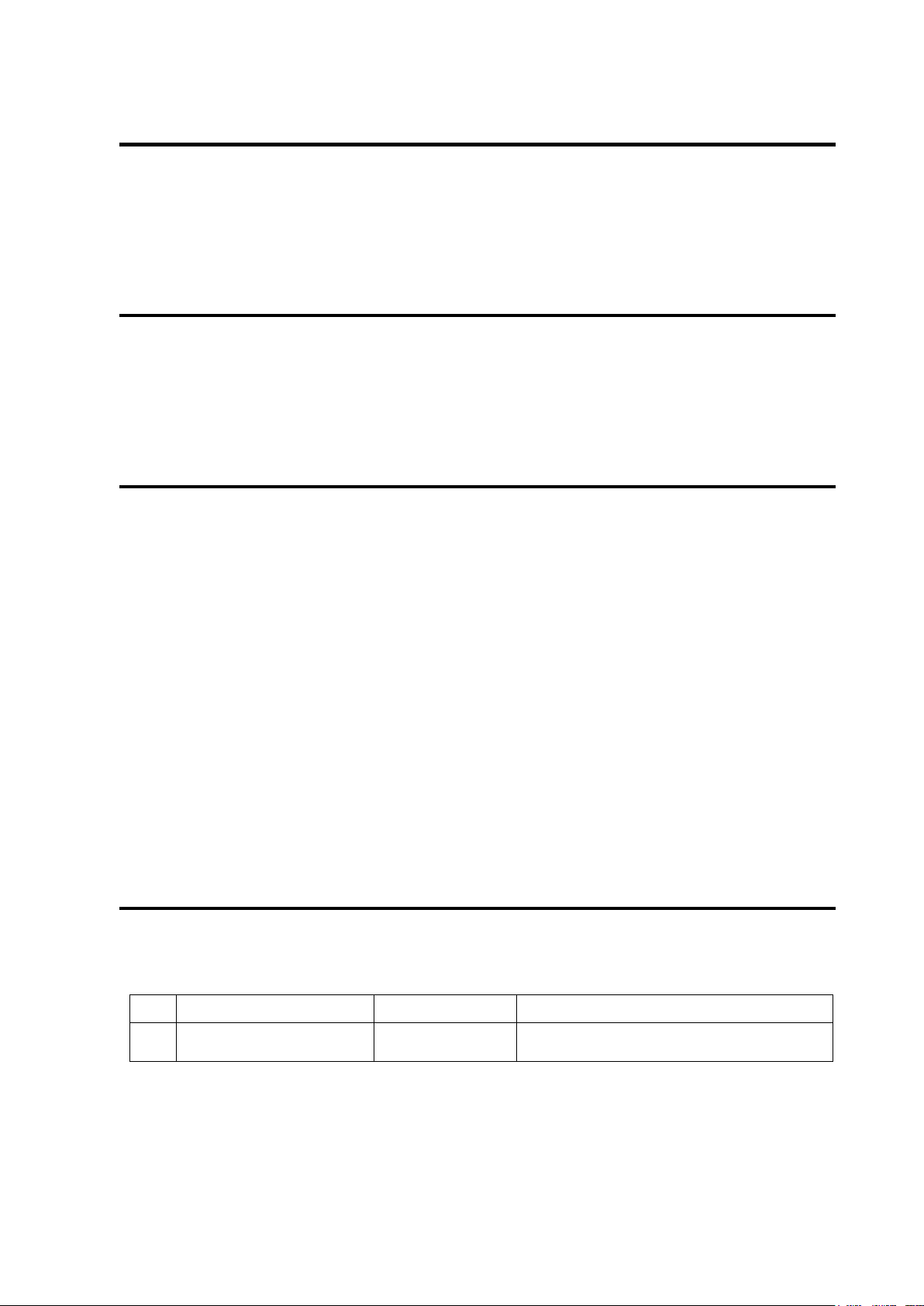
Electrolytic capacitor in
main circuit
Load factor: less than 50% of rating.
Ambient temp: less than 40 C in average.
Introduction
Thank you for purchasing SD4030B3. This manual describes on the specification and the usage of
SD4030B3. Please review the material in this manual thoroughly before using SD4030B3.
― Warranty ―
●The product is guaranteed against functional failure in the case it occurs during one (1) year from the date
of the original delivery, and in spite of your correct usage. In such case we will supply replacement unit free
of charge.
― Cautions for Proper Use ―
●Please use the product under the absolute maximum ratings and the environment recommendation.
●This product is neither designed nor manufactured to be used in a machine or system that may cause
death or injury of person when it is failed.
Consult us in advance if you are planning to use this product for applications under such special conditions
and environments.
●We are making best efforts on to ensure the highest quality of the products. However, it is highly
recommended that you should make enough safety design such as a redundant design, an anti-fire design
or a fail-safe design in order to avoid an accident causing injury or death of person, fire accident, or damage
of social.
●Contents of this manual are subject to change without prior notice for functional improvement and other
purpose.
― Product lifetime ―
●Please recognize that some parts has product lifetime due to aging degradation. Be sure to change the
following parts when the product lifetime is expired.
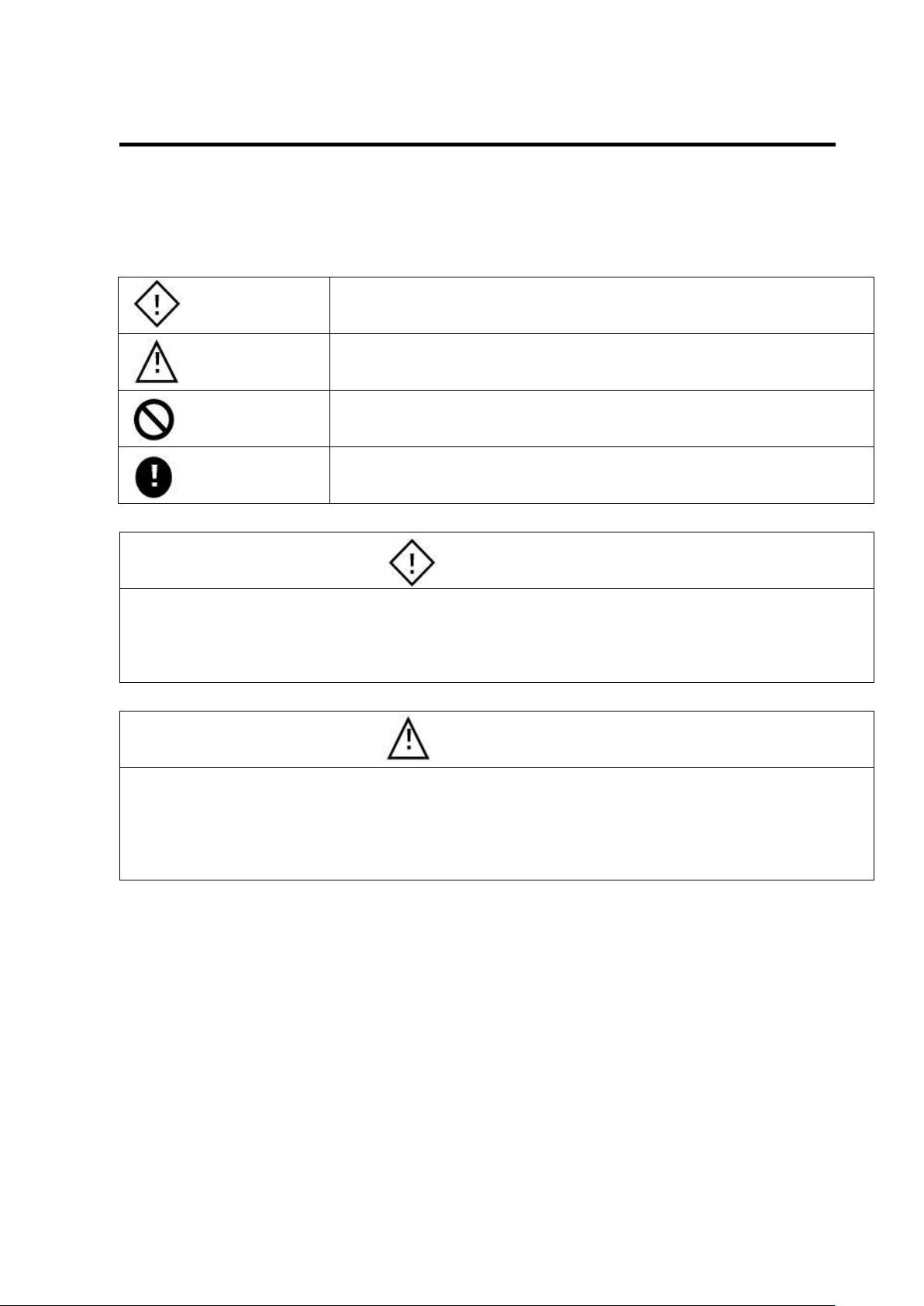
In case of incorrect handling, it indicates possibility of dangerous
situation could arise and that the possibility of death or serious illness
of a person is assumed.
In case of incorrect handling, it indicates possibility of dangerous
situation could arise and that the possibility of personal injury or
property damage is assumed.
This symbol is used to indicate a practice that shall not be attempted
This symbol is used to indicate a practice that shall be done.
● Never touch any terminals and internal parts that is in active status. Could cause electric shocks.
● Do not pull or bend the cable, or place heavy objects on it. Could cause electric shocks or a fire.
● Never touch part of rotating. Could cause personal injury by involving to the rotor.
● Never touch surface of motors or power elements because those are may become abnormally high
temperature while driving. Could cause burns.
● Don't use in the place where water, oil, or chemicals is splashed, or in the place where is corrosive
environment or flammable gas.
● Use the rated power supply voltage. Could cause a fire.
● Do not touch the surface-mounted component on the board, as it may be hot while turning on the power
or while after just shutting off the power. Could cause burn injury.
● Wiring work should be done correctly.
― Safety Precautions ―
For safe use of SD4030B3, following icons and messages are used in this manual to indicate safety
precautions. The precautions given here indicates serious safety contents. You are recommended to
observe the safety precautions fully.
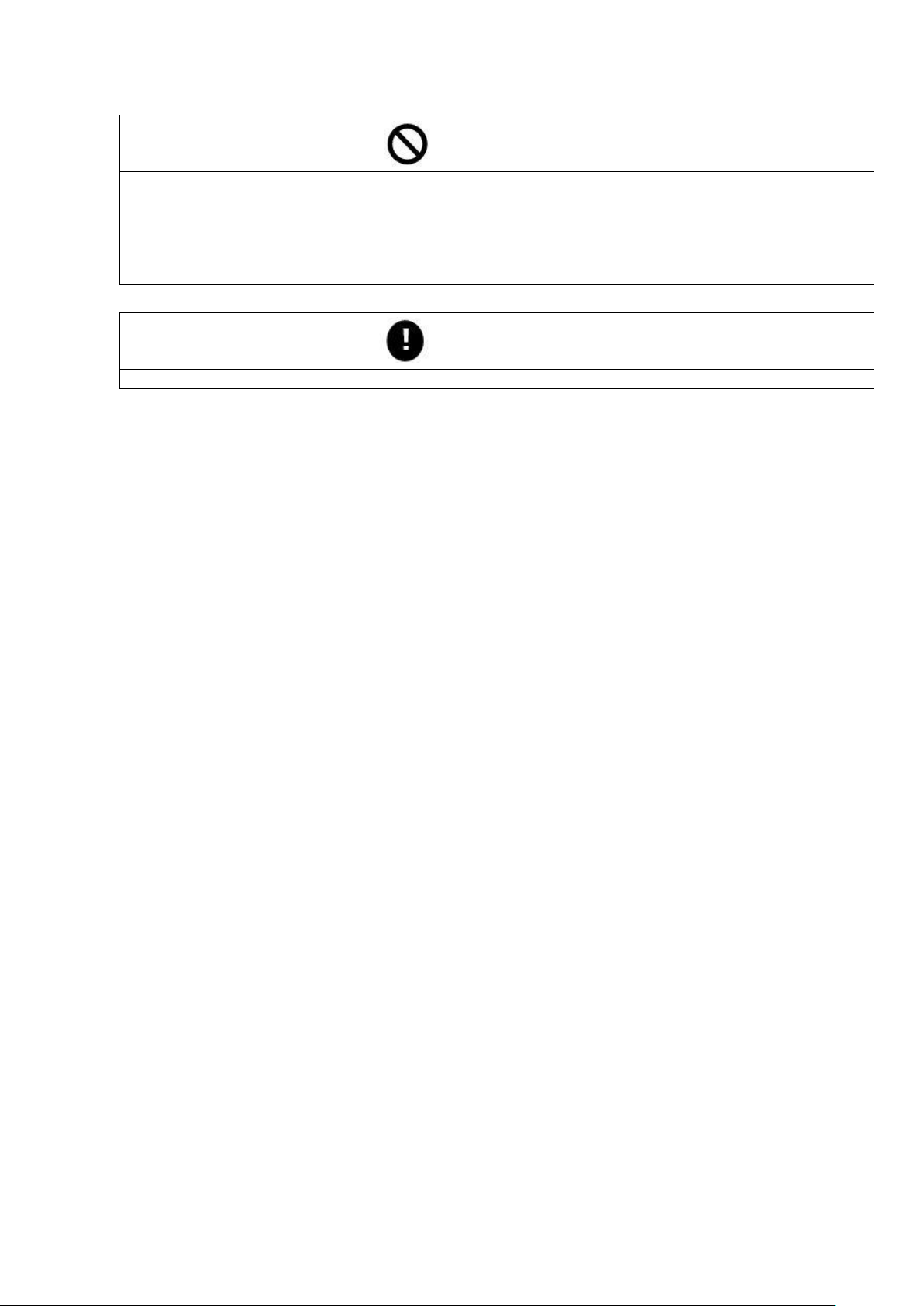
● Don't use or store in the place under direct sunshine.
● Don't use or store in the place where may be beyond the range of ambient temperature and relative
humidity specification.
● Do not use or store in the place with many dust, dirt and others.
● Do not use or store in the place subject to direct vibration or shock.
● Never attempt to perform repair and modification by yourself.
● Install an emergency stop circuit outside to be able to stop the system operation immediately.
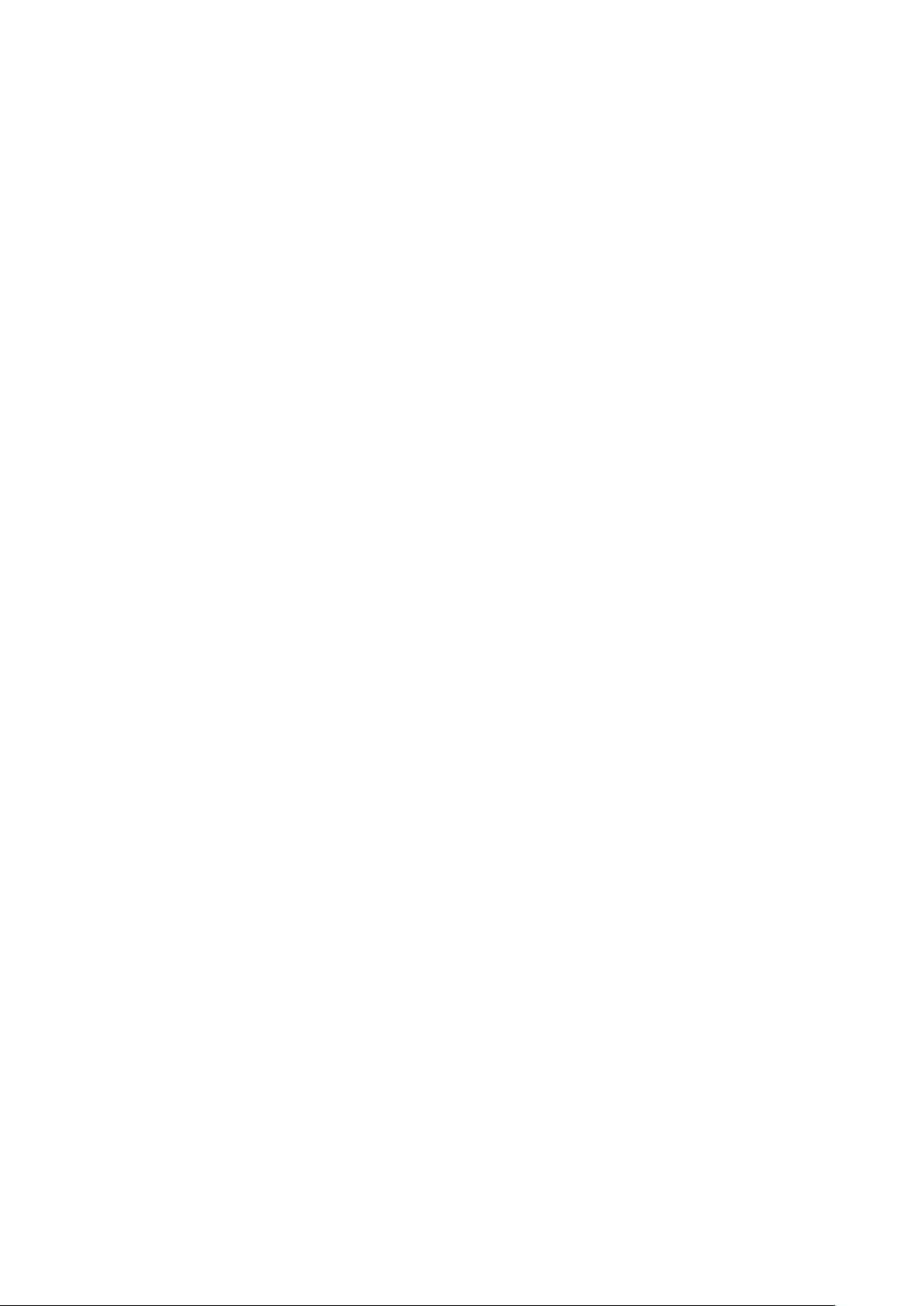
Table of Contents
1. Notes (Please be sure to read before using)·············································································· 1
1-1 Installation ····················································································································· 1
1-2 Connection of Connector ·································································································· 1
1-3 Division of Micro step······································································································· 1
1-4 Heat generation of a motor ······························································································· 1
1-5 Electric current value of Micro Step ···················································································· 1
1-6 Unipolar type motor drive ································································································· 1
1-7 Compatibility notice to the customers using SD4030B2. ·························································· 1
2. Specifications ····················································································································· 2
3. Connector pin assignment ····································································································· 3
3-1 CN1 ····························································································································· 3
3-2 CN2 ····························································································································· 3
4. I/O circuit diagram ················································································································ 4
4-1 Command pulse or CW pulse (P+, P-), Direction Command or CCW pulse (D+, D-) Input ············· 4
4-2 Excitation off (OFF) input ·································································································· 4
4-3 Alarm (ALM) Output········································································································· 4
5. Logic of Command Input pulse ······························································································· 5
5-1 In case of 1-pulse mode ··································································································· 5
5-2 In case of 2-pulses mode ································································································· 5
6. Connection of Motor ············································································································· 6
6-1 In the case of Bipolar type motor ························································································ 6
6-2 In the case of Unipolar type motor ······················································································ 6
7. Setting of switch SW 1 ·········································································································· 7
8. Setting of switch SW 3(MIX) ·································································································· 8
9. Settings of Jumper JP1 ········································································································· 9
10. LED“POW” ····················································································································· 10
11. JOG operation ················································································································· 10
12. Setting of potentiometers ··································································································· 10
12-1 RUN potentiometer ······································································································ 10
12-2 STOP potentiometer ····································································································· 11
12-3 JOG potentiometer ······································································································· 11
13. How to adjust the RUN potentiometer precisely ······································································ 12
14. Need of a rated output current reduction at a higher power supply voltage area ···························· 12
15. Troubleshooting ··············································································································· 13
16. Component layout ············································································································ 14
17. Dimension ······················································································································ 15
18. Difference between SD4030B2 and SD4030B3 ······································································ 16
18-1 Difference in how to set Mix Decay ················································································· 16
18-2 Difference on the maximum frequency of Command pulse ·················································· 16
19. CE Marking ····················································································································· 17
20. Caution for ESD damage ··································································································· 17
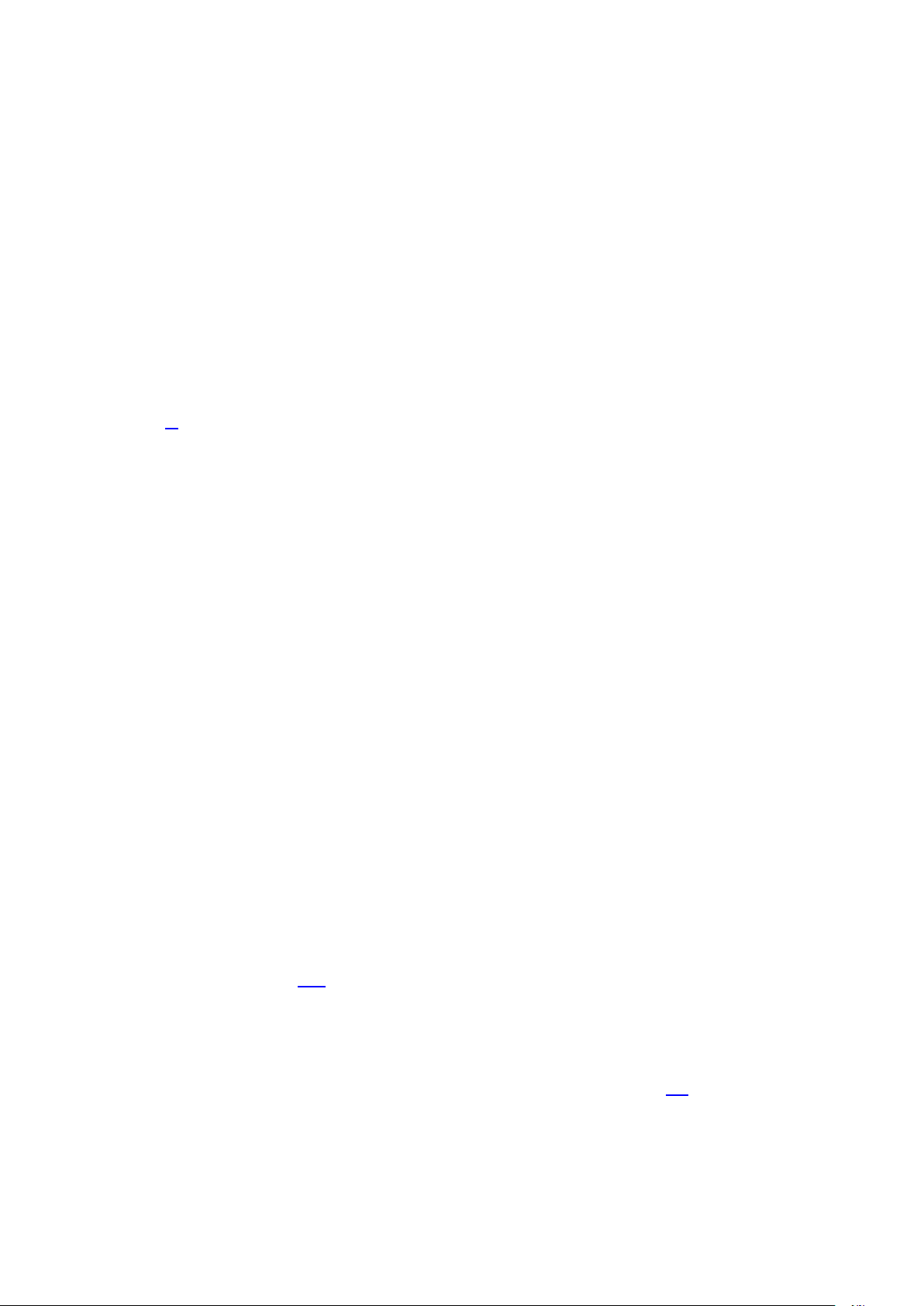
1.Notes (Please be sure to read before using)
1-1 Installation
You shall observe the following installation method when installing this driver.
Please install the driver in the place where the air around the driver within 5 cm has air convection
with a rated temperature (40 ° C or lower temperature).
When using multiple axes please leave a space of 10 mm or more between each driver.
1-2 Connection of Connector
In particular, please pay attention to power wiring. This driver has a power circuit configuration that resists
breaking even with the incorrect polarity of the power supply, but the driver will be damaged if you wire the
power supply to the motor output terminal.
Please observe the instruction about wire materials and a length of stripped bare wire that is shown in the
section 3.. Also, tighten the terminal block screw with a torque of 0.22 to 0.24 Nm. This prevents loosening
of screws and disconnection of wires.
1-3 Division of Micro step
Since a Division of Micro Step is performed by vector splitting currents of Phase A and Phase B of a stepping
motor by approximate sinusoidal wave electrically, a divided one-step-angle does not guarantee a
mechanical position accuracy as is.
The mechanical positional accuracy depends upon the machine accuracy of a motor's own and a driven
device.
1-4 Heat generation of a motor
Since surface of a motor may become extremely high temperature while driving, please care burns.
If a surface temperature of a motor exceeds 100℃, the motor may be damaged. So then reduce the current
value with "RUN “potentiometer or cool the motor by forced air cooling to not exceed 100 ℃.
It also can prevent heat generation by enabling Auto Current Down function and reducing a current during
stop.
1-5 Electric current value of Micro Step
A setting electric current value by "RUN" potentiometer is a peak value of approximate sinusoidal current.
1-6 Unipolar type motor drive
Although this driver is mainly designed for bipolar type motors, it can also drive unipolar type motors.
Please refer to the section 6-2 for wire connection method.
1-7 Compatibility notice to the customers using SD4030B2.
This driver is upward compatible with SD4030B2, but Mix Decay setting has been changed from a
potentiometer to a switch. For more detailed information, Refer to the section 18.
Outer form size and installation mounting pitch has not be changed.

Input power supply
voltage
When the output current is set to 3 A
2-phase stepping motors (bipolar
type)
Unipolar type motors also can be
driven.
Bipolar constant current chopper
method
Auto Current Down
Reduce current to the current value
set by “STOP” potentiometer in 0.25
to 1 second after stopping the pulse.
Function is selectable by the switch
Maximum input pulse
frequency
Adjustment
by the
trimmer
Set the excitation current (0.5 to 3A)
The factory setting is 2A
Set the current of Current Down
mode
10% to 60% of the RUN current
Function
select by
the switch
Select of division number
1/2,1/8,1/10,1/16,1/20,1/32,1/40,1/64
Enable/disable Auto Current Down
ON: Enable, OFF: Disable
The factory setting is Enable.
SW-5 ON: Enable JOG
SW-6 ON: CW, OFF: CCW
Command pulse or Command CW
pulse
1-pulse or 2-pulses is selectable as
command pulse
Inputs are isolated by photo couplers
Command pulse or Command CCW
pulse
Alarm (Power elements overheat
detection)
The signal outputs when the
temperature of inside power
elements reach to 170℃ (Typ).
Output are isolated by photo
couplers
ON: Normal, OFF: Alarm
Including the terminal block socket
Operating temperature,
humidity
Storage temperature,
humidity
2.Specifications