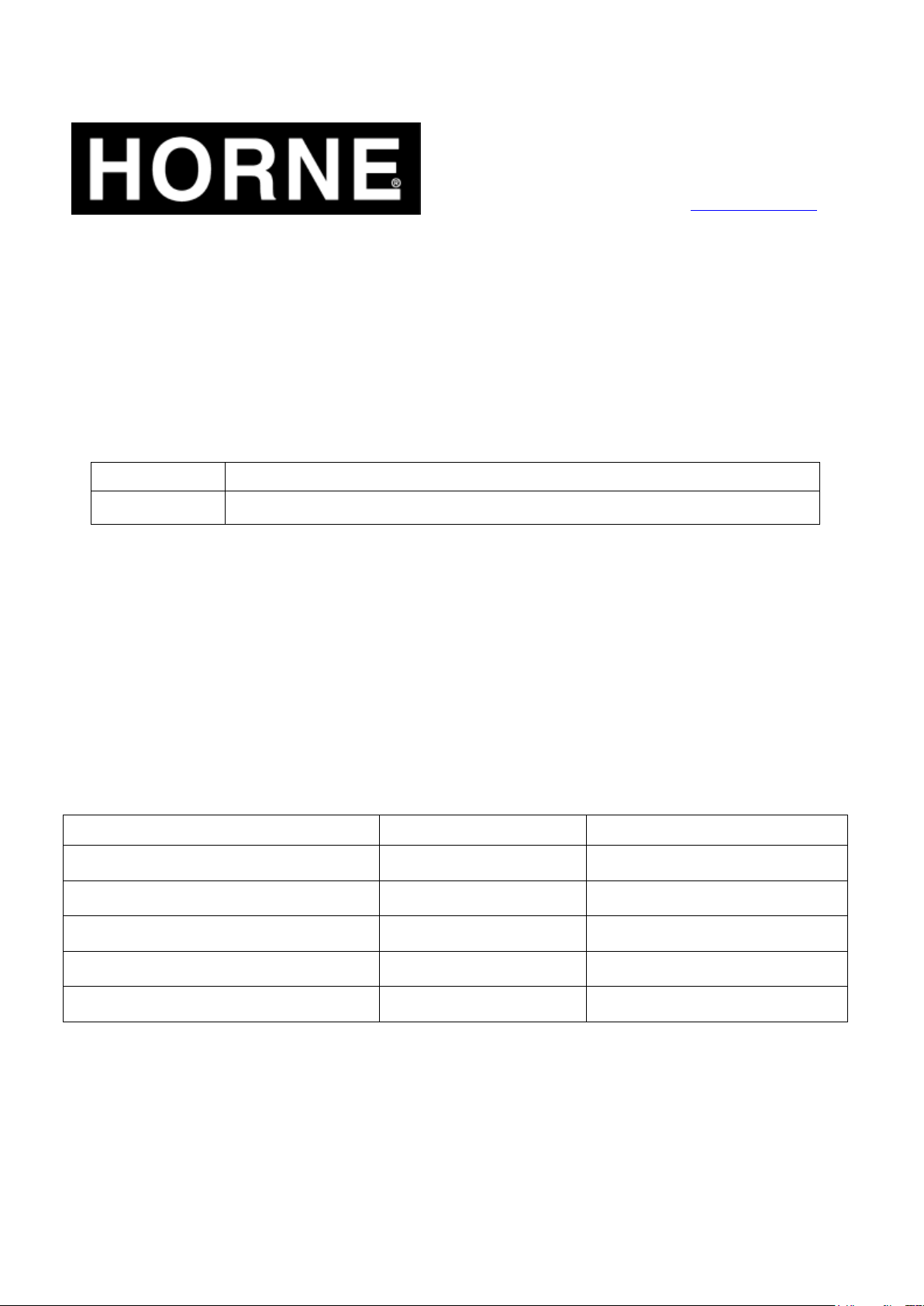
Horne Engineering Ltd
Horne Engineering Ltd
Po Box 7, Rankine Street
Johnstone, Renfrewshire
Scotland, PA5 8BD
Tel: 01505 321455
Fax: 01505 336287
Email: technical@horne.co.uk
Web: www.horne.co.uk
Shower with supply pressures of 1 – 5 bar and unrestricted flow rate
Shower with supply pressures of 0.2 – 1 bar and unrestricted flow rate
Flow Pressure, Hot & Cold
Hot Water Supply Temperature
Cold Water Supply Temperature
Minimum Temperature Differential
HORNE T105A/106A/107A/108A THERMOSTATIC SHOWER PANEL
FOR SURFACE MOUNTING WITH DUAL CONTROLS
INSTALLATION, OPERATING & MAINTENANCE INSTRUCTIONS
Note that these instructions feature the T108A shower panel. The T105A, T106A and T107A feature the
same TSV1-3 thermostatic valve but differ in the water outlet fittings. All comments relating to the T108A
also apply to the other shower panels mentioned above and their variants.
Approvals
The TSV1-3 Thermostatic Shower valve has been independently tested by WRc-NSF and approved to all
the requirements of NHS Model Engineering Specifications D08 Thermostatic Mixing Valves (Healthcare
Premises) to the following designations and for the following applications:
Supply Water Pressure requirements
The minimum water pressure required to achieve a spray at the spray head is a dynamic head of 2m (3
psi, 0.2 bar) at the spray head. Note that for very low head installations, both hot and cold water supplies
must be at the same pressure.
Note that dynamic head is measured with the water running.
Where the TSV1-3 panel is fed by supplies with differing pressures, use the following to determine
whether a pressure-reducing valve (PRV) is required on the side with the higher pressure. Note that
output flow-rate is always determined by the lower of the two inlet pressures. If the lower inlet pressure is
low enough (typically 0.2 to 1Bar dynamic) that the flow-regulator in the outlet fitting (see pages 11,12,13)
can be removed, then a PRV should not be required. If the lower of the 2 supply pressures is higher than
around 1Bar, then a flow-regulator will be required to restrict flow. If the flow-regulator is needed, and the
supply pressures are substantially unbalanced, then a PRV will also be needed to prevent pulsing of the
flow. Although thermostatic performance is unaffected by this, the flow pulsing is undesirable.
Temperature Adjustment Range
The mixed water temperature can be adjusted from cool through to a top limit (which can be preset during
installation – factory set to approx. 41°C - with full anti-scald protection throughout the range).
Water and Energy Conservation
The TSV1 range shower panels are fitted at the factory with flow regulators at the shower outlet to reduce
the flow rate and conserve water and energy. The drawings at the end of this document provide
information for accessing the flow restrictors/regulators for removal or replacement.
Issue 7, November 2018 1
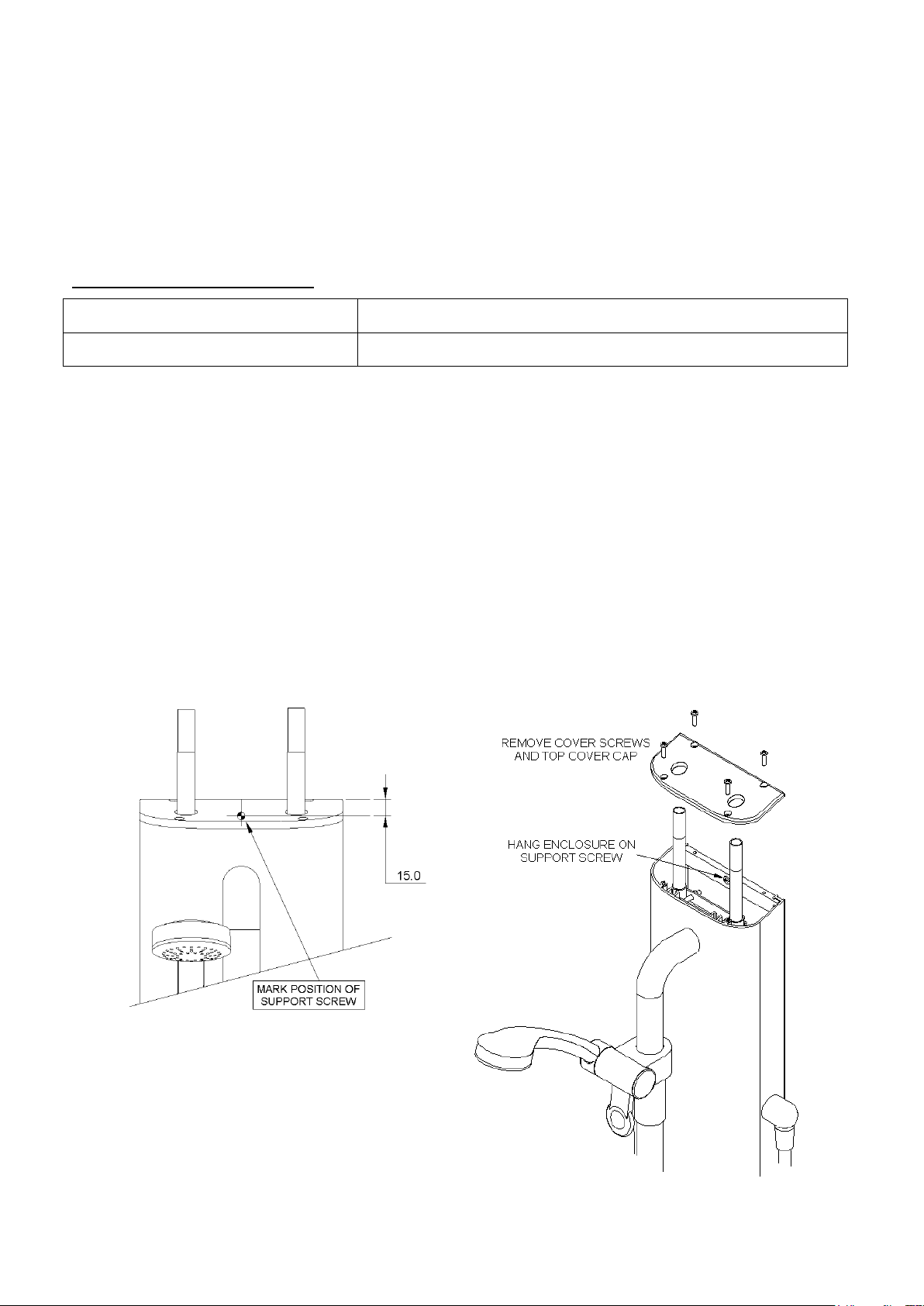
Horne Engineering Ltd
Bottom of panel should be 1.0 metre from finished floor level.
T016 Panel (swivel-head, shown p13)
Bottom of panel should be 1.1 metres from finished floor level.
1) Position the Pre-Plumbed Enclosure
Identify a suitable position for the Enclosure and mark a line on the wall level with the top of the
casing. Mark a point on the wall which is on the required centreline for the Casing 15mm below
the line of the top of the casing for the support screw (See Fig 1).
2) Install the Support Screw
Drill a 7.0mm dia. hole in the wall and insert a wallplug and screw, leaving the head of the screw
11-13mm from the wall surface. Note that a stainless steel screw is supplied for this (corrosion
resistant).
3) Hang the Enclosure on the Support Screw
Release the top cover of the pre-plumbed enclosure by removing the four screws. Hang the preplumbed enclosure on the support screw by the larger hole in the middle of the back strap and let
this take the weight of the enclosure. See Fig 2.
Every HORNE TSV1-3 is supplied with an integral WRAS approved single check valve and integral large
surface area strainer. The Shower Panel terminates in 15mm copper pipes for hot and cold supplies. The
hot pipe is on the left, and cold on the right, when viewed from the user’s perspective.
INSTALLATION
The surface mounting enclosure is supplied with fixings to attach it to a wall. However consideration
should be given to the type of wall fittings required, as different substrates will require different fittings.
Recommended Mounting Heights
Issue 7, November 2018 2
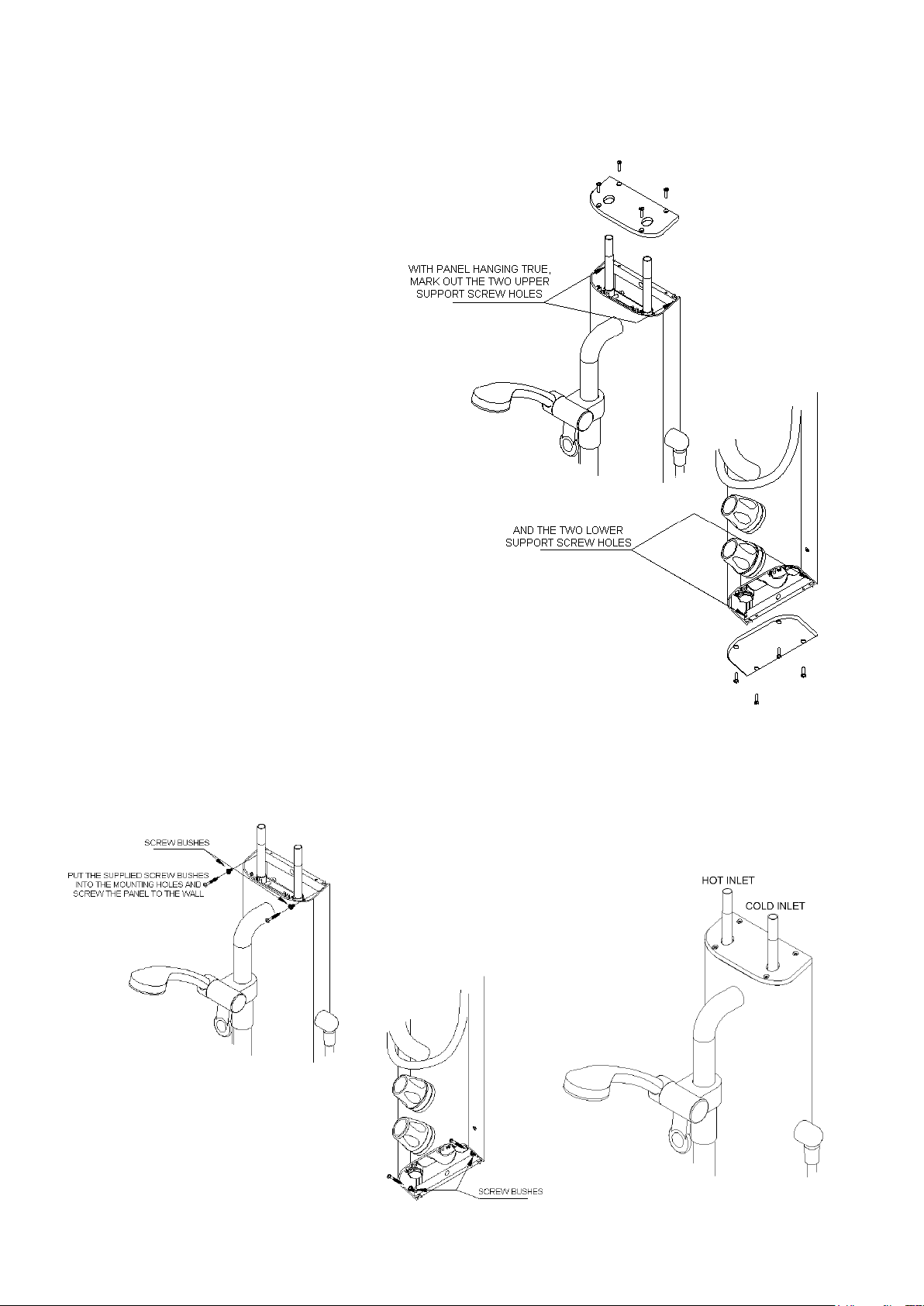
Horne Engineering Ltd
4) Mark out the 4 Support Holes
Ensure that the enclosure is
hanging true and then mark out the
holes for the 2 upper support
screws. Remove the bottom cover
of the pre-plumbed enclosure and
mark out the 2 lower support
screws (See Fig 3).
5) Drill Support Holes
Carefully remove the pre-plumbed
enclosure from the temporary
support screw and, being careful
not to scratch the enclosure or its
covers, lay it down where it will not
be damaged. Drill the 4 holes and
install the wall plugs.
6) Attach the Pre-Plumbed Enclosure
to the Wall
Carefully re-hang the pre-plumbed
enclosure on the temporary screw.
Put the four supplied screw bushes
in the mounting holes in the panel
and then attach the panel firmly to
the wall by the four supplied
stainless steel screws. A bead of
silicon mastic can be used, if
required, to cover any gaps behind
the panel on uneven walls. Do not
mastic the lower End Cap to the
wall. See Fig 4.
Issue 7, November 2018 3
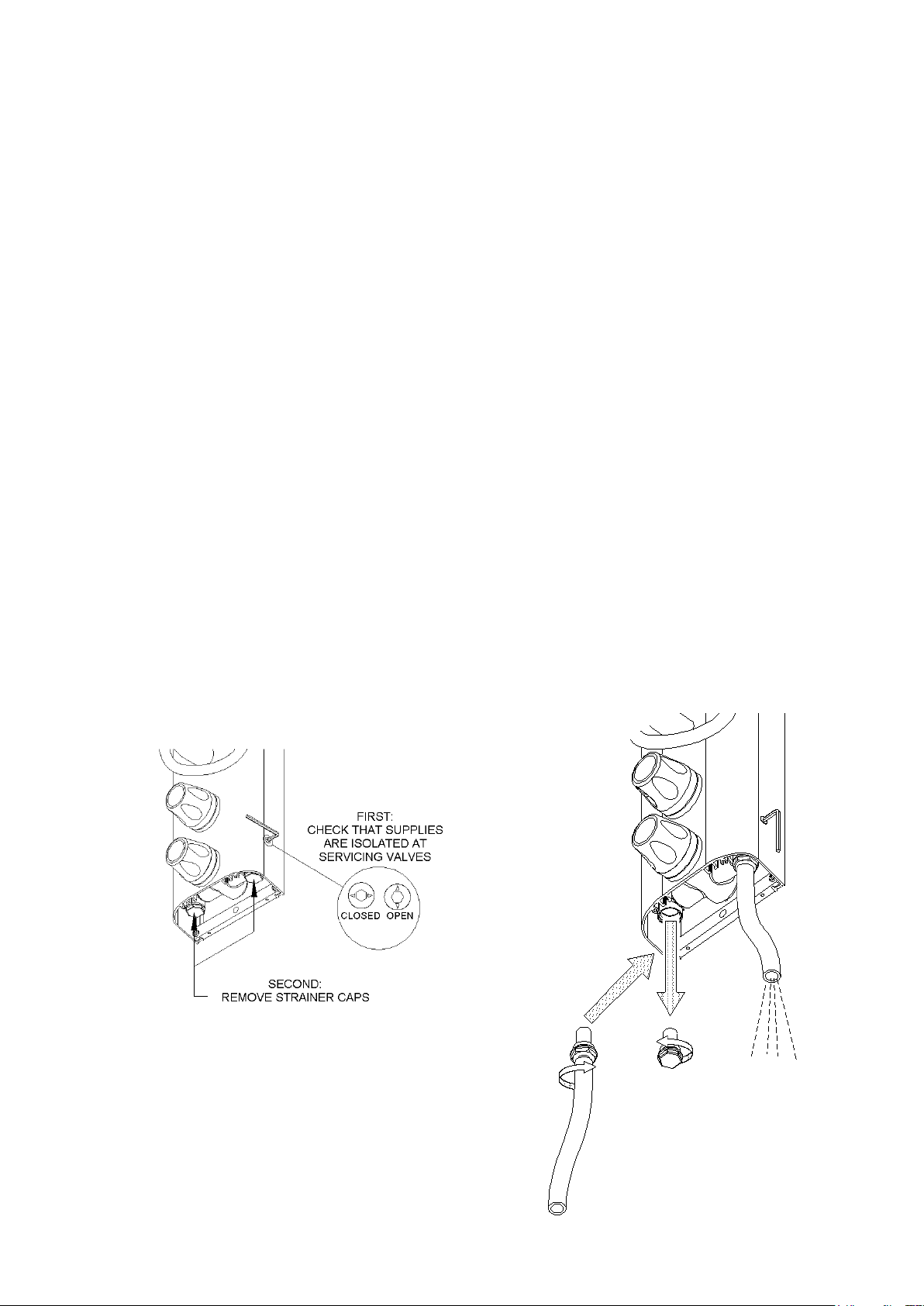
Horne Engineering Ltd
7) Connect the Supply Pipes
N.B. Ensure that the top cover of the pre-plumbed enclosure is replaced prior to connecting up the
supply pipes. The fitting of isolation valves is required as close as practicable to the water supplies
inlets of the shower panel.
Connect the hot water supply to the left hand inlet, and cold water to the right-hand inlet (See Fig 5).
DO NOT OPEN THE WATER SUPPLIES AT THIS STAGE AS THEY HAVE NOT BEEN FLUSHED
OUT TO REMOVE THE DEBRIS IN THE PIPEWORK. SUCH DEBRIS CAN DAMAGE THE
THERMOSTATIC VALVE.
8) Flush the Pipework
Flush out the pipework in accordance with Water Bylaws 2000 (Scotland) and BS 6700: 1997
(England & Wales). The use of a Horne flushing kit is strongly recommended, because this
connects directly to the water inlets to the mixing valve. Access to the flushing points is gained
from underneath the casing through the lower end cap. Isolate the water supplies and also the
low level servicing valves located on the side of the panel (see Fig 6) using the supplied 4mm hex
key. Remove the strainer cap with the strainer basket and screw in the flushing adapter. Place
the end of the flushing hose in an appropriate drain or container and turn on the supply to flush as
required. After flushing, remove the flushing adapter and replace the strainer cap. Repeat for
both hot and cold supplies. See Figs 6 and 7.
NOTE THAT IF THERE IS ANY DANGER OF FREEZING THEN THE PIPES AND TSV1-3 MUST
BE DRAINED TO AVOID DAMAGE.
Fig 4. NB It is important to use the supplied screw bushes. Fig 5.
Issue 7, November 2018 4

Horne Engineering Ltd
9) Test for Leaks in Pipework
Ensure that the TSV1-3 on/off control is closed (i.e. turned fully clockwise) and open the supplies.
Open the servicing valves on the TSV1 Casing (See Fig 6). Turn on the supplies and adjust the
temperature control and check for any water leaks upstream of the TSV1-3 valve. Make good any
leaks found. The valve is now ready for commissioning.
Note that if the controls, enclosure and shower accessories require cleaning then care must be taken
not the scratch them in the process. Wash off any surface dust with the shower spray before
cleaning with soapy water.
DO NOT USE ANY ABRASIVE CLEANERS OR SOLVENTS OR THE SURFACES MAY BE
DAMAGED.
Backflow Prevention
The hot and cold inlets to the TSV1-3 valve are fitted with single in-line WRAS Approved DN15 Check
Valves.
Supplementary Installation Instructions for T10XB Variants.
TSV1 Panel Mounted Shower Valves are available in versions with flexible braided stainless steel inlet
hoses rather than top entry isolating valves. The hoses used are PEX (cross-linked polyethylene). They
are not EPDM lined. These versions have Product Reference codes with the suffix B, e.g. T108B.
The main difference, from an installation point of view, is that the water supplies may have to be
connected before the pre-plumbed enclosure is attached to the wall.
Accordingly, point 7 on the attached installation instructions (Connect the Supply Pipes) should be
performed before point 6 (Attach the Pre-Plumbed Enclosure to the Wall) unless alternative access is
available to the connections, e.g. via an access panel.
Note that the braided hose inlets are colour coded with BLUE for the Cold Water Supply and RED for the
Hot Water Supply.
Care should be taken to ensure that the weight of the pre-plumbed enclosure is taken by the mounting
screws and NOT by the hoses.
COMMISSIONING
It is essential to commission the valve in order to establish a reference point for future in-service tests.
Ensure that the pipework has been flushed out before commissioning the TSV1-3. (See installation
instructions.)
Ensure that the NHS designation of the valve matches the intended application, that both hot and cold
water supplies are open and at, or near, their design temperatures and pressures and that they are within
the requirements of the valve as outlined on page 1, and within guidance information on the prevention of
legionella, etc. NB Ensure that the servicing valves are also open (see Para 8).
Set the temperature control to the maximum temperature setting (i.e. rotate the control anticlockwise until
it stops).
Fully open the on/off control by turning it anticlockwise. For installations with a fixed shower head, putting
a burst polythene bag over the shower head will help to catch and deflect the spray during commissioning.
Issue 7, November 2018 5