
BG Series
GAS
Micro-Processor Controlled
CONVEYOR DRYER
OWNER’S MANUAL
Visit www.hixcorp.com
ext. 209, ext. 211, ext. 220, ext.221 or
For Customer Service, Call 1-800-835-0606
Installation / Set Up.................................................................................2-3
Initial Gas Startup ...................................................................................4-5
Temperature Control ..................................................................................6
High Limit Temperature Reset ...................................................................7
CONTENTS
Call 1-800-835-0606
BEFORE warranty repair you MUST get Prior Authorization:
Belt Speed Controller.................................................................................8
Recirculating Air......................................................................................... 8
Door Adjustment ........................................................................................9
Belt Tracking Adjustment ......................................................................... 10
Operating Precautions ............................................................................. 11
Maintenance ............................................................................................ 12
Applications ........................................................................................13-15
Troubleshooting ..................................................................................16-18
Warranty .................................................................................................. 20
(Effective January 1, 2007)
HIX will automatically register the equipment on the date it was shipped to you or your
WARRANTY
distributor. If the equipment was not purchased directly from HIX, but through a distributor
(either domestic or foreign), please keep a copy of their sales invoice showing the serial
number and date it was sold/shipped to you with this warranty. In this case, we will use the
distributor’s invoice date as the beginning warranty date. STAPLE A COPY OF YOUR RE-
CEIPT TO THIS WARRANTY and keep in a safe place to provide verification of your warranty
should a problem occur. Thank you.
Please fill in the following information and attach a copy of your receipt for your records.
Date Purchased: _____________________ From: _________________________________
This warranty applies to equipment manufactured by the HIX Corporation (HIX), Pittsburg,
Model #: ____________________________ Serial #: ________________________________
Kansas, U.S.A. HIX warrants to the original purchaser, its Conveyor Dryers, Heat Transfer
Presses, Mug Presses, Mug Glazer, Retensionable Screen Frames, Textile Printers, Spot
Heaters, and Exposure Units against defects in workmanship and material, except for wear
In the event of a defect, HIX, at its option, will repair, replace or substitute the defective item
and tear for a period of “One Year” from the date of purchase. HIX warrants its Accessories,
Reten Splines/Hardware/Tool Kit, and Shuttle for a period of 90 days from the date of pur-
chase. DoughXpress and Thermatrol products are covered under separate warranty.
In the case of heat transfer presses (except the Mug Press, Hobby Lite), HIX warrants the
at no cost during this period subject to the limitations of insurance and shipping costs stated
below.
heat casting for the “Life” of the machine for the original purchaser. If a part becomes obsolete
at the time for repair, and/or cannot be reasonably substituted for, HIX will credit, at half the
This warranty does not cover belts, pads, mug wraps, mug press liners, canvas, rubber
then current list price or last recorded price, only that part toward a new machine or any
product HIX offers. This credit offer shall be the sole responsibility of the HIX Corporation in the
event of an obsolete part.
blankets, bulbs, glass, PTFE or finish, rod ends, turn buckles on printers, or mug press or
damages due to accident, misuse/abuse, alterations or damage due to neglect, shipping or
lack of proper lubrication or maintenance. HIX shall not be responsible for repairs or alterations
made by any person without the prior written authorization by HIX. This warranty is the sole
E-Mail: sales@hixcorp.com • Fax: (866) 563-4600
1201 E. 27th Terrace • Pittsburg, KS 66762 • U.S.A.
Web site: www.hixcorp.com • Phone: (800) 835-0606
E-Mail: customerservice@hixcorp.com • Fax: (866) 561-0894
In the case of a problem with the equipment identified herein, HIX Corporation should be
and exclusive warranty of HIX and no person, agent, distributor, or dealer of HIX is authorized
to change, amend or modify the terms set forth herein, in whole or in part.
contacted during regular business hours to discuss the problem and verify an existing war-
ranty. HIX personnel will assist the customer to correct any problems which can be corrected
through operation or maintenance instructions, simple mechanical adjustments, or replace-
of the customer, and not that of HIX, and HIX shall not be responsible for improper handling or
ment of parts. In the event the problem cannot be corrected by phone, and upon the issuance
of a return authorization by HIX, the equipment shall be returned to HIX or an authorized
service representative. All insurance and shipment/freight costs are solely the responsibility
This expressed warranty is given in lieu of any and all other warranties, whether ex-
In no event shall HIX’s liability for breach of warranty extend beyond the obligation to repair
This warranty gives you specific legal rights and you may also have other rights which
damage in transit. HIX offers a reconditioning service and a core exchange/credit policy on
some models. HIX customer service personnel may be contacted for complete return authori-
zation and reconditioning information.
pressed or implied, including but not limited to those of merchantability and fitness for a
particular purpose, and constitutes the only warranty made by HIX Corporation.
or replace the nonconforming goods. HIX shall not be liable for any other damages, either
incidental or consequential, or the action as brought in contract, negligence or otherwise.
Manufacturers of the Finest Quality Textile and Graphics Screen Printing and Heat Transfer Equipment
vary from state to state.
©2007 HIX Corp. 20 BG080907
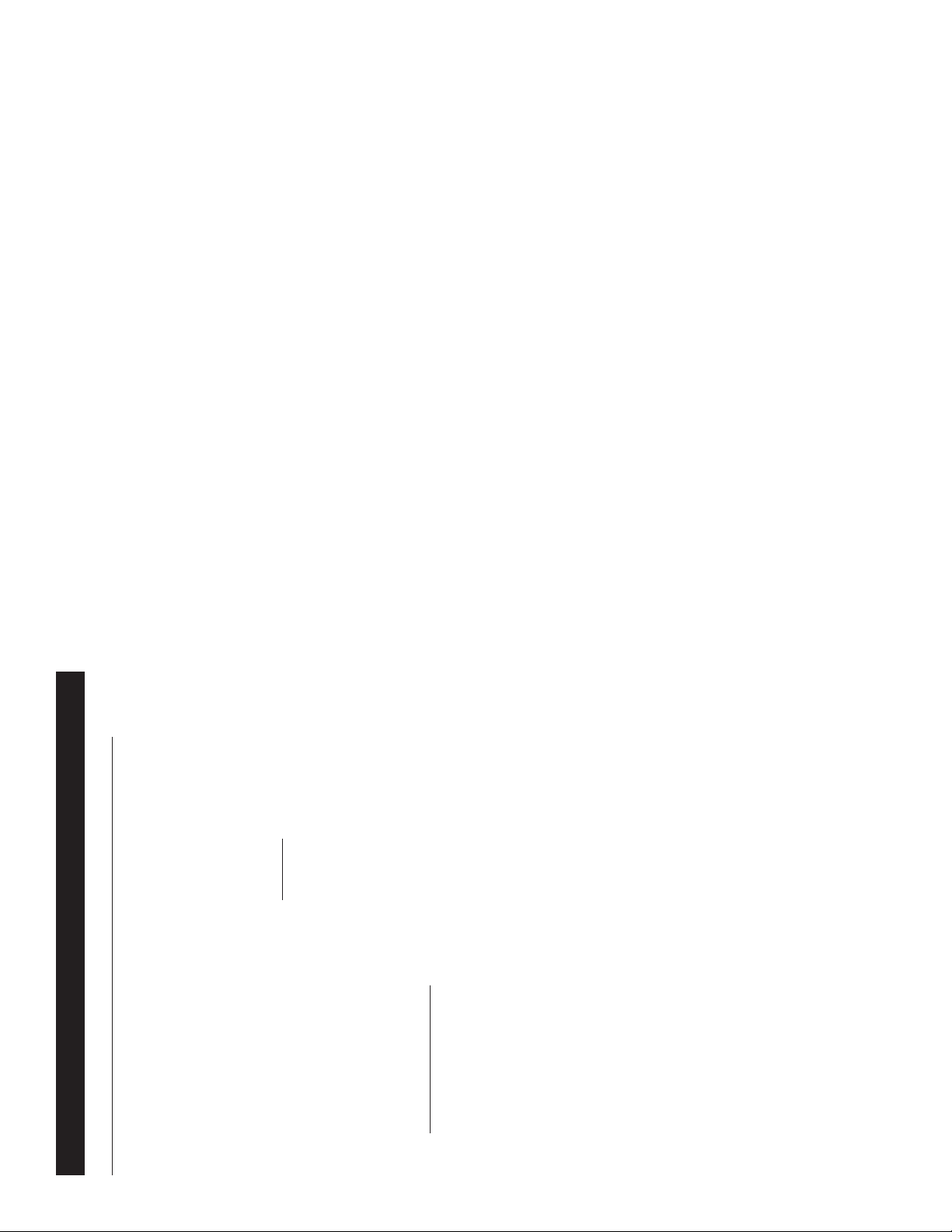
19
(This page intentionally left blank.)
NOTICE: Belt height must be a
only (no wood or carpet). Also maintain the following minimum
distances to other structures: Back - 18 inches, Ends - 40 inches,
Front - 48 inches, Exhaust Flue To Surface - 18 inches.
INSTALLATION / SET UP
BASIC INSTALLATION AND SETUP INSTRUCTIONS
NOTE: This unit is designed for installation on non-combustionable flooring
the oven only enough to allow the casters to be unbolted off of the frame
(One on each corner). Keep the oven level during the lifting and lowering
process.
• Raise oven off floor by positioning a forklift at each end of the oven. Raise
1. LEVELING PAD INSTALLATION
adjust leveling pads as needed.
• Lower oven almost to floor level. Check belt height above floor and
Lower forklift to allow machine leveling pads to rest on the floor. Check for clearance
between the burner box and floor. There must be a minimum clearance of
1/2”. Do not allow the burner box to rest on the floor. It is not designed to
suppport the weight of the oven. Tighten all leveling pad jam nuts.
IMPORTANT NOTICE: DO NOT operate this oven without ductwork in
place. All gas ovens give off Carbon Dioxide and dangerous Carbon
minimum of 34” above floor. Attempting to adjust the leveling
pads for lower than 34” belt height will cause interference between
the floor and the burner box mounted under the oven.
•
2. EXHAUST DUCT WORK
Monoxide fumes as a by-product of combustion. Operating any gas-
• Run duct from the exhaust stack on the oven to the outside of the building.
•
2
fired equipment without proper ducting in place could result in serious
risk to workers health or even death.
and local codes for venting gas-fired equipment.
the two blower openings are at the bottom.
opposite the control box.
bolts and lock washers.
opening in the oven wall using the provided #14x2” sheet metal lag screws
and flat washers.
• All duct installation must be done in compliance with Federal, State
• Set the transfer plenum upright so that the rectangular slot is at the top and
• Align the plenum openings with the openings on the back side of the oven
• Attach the plenum to the burner box using the provided 3/8”x1-1/4” hex
• Seal the rectangular slot in the upper part of the plenum to the rectangular
3. TRANSFER AIR PLENUM (May be preinstalled on some units)
metal lag screws.
• Attach the plenum door to the plenum box using the provided #14x2” sheet
• Unscrew casters from the belt extension legs if present.
4. CONVEYOR BELT
(with gearmotor assembly) normally goes into the left-hand end of the oven as
viewed facing the control panel on standard models. Note: The oven exit end
will have a receptacle box mounted under the fume hood to receive the power
cables for the gear motor and speed control sensor.
• Assemble leveling pads with provided threaded rod and (2) jam nuts
• Screw one leveling pad into each extension leg.
• Insert each belt extension into the matching oven end. The exit end extension
extensions plug in.
• Tighten the clamping bolts on each corner of the oven frame where the
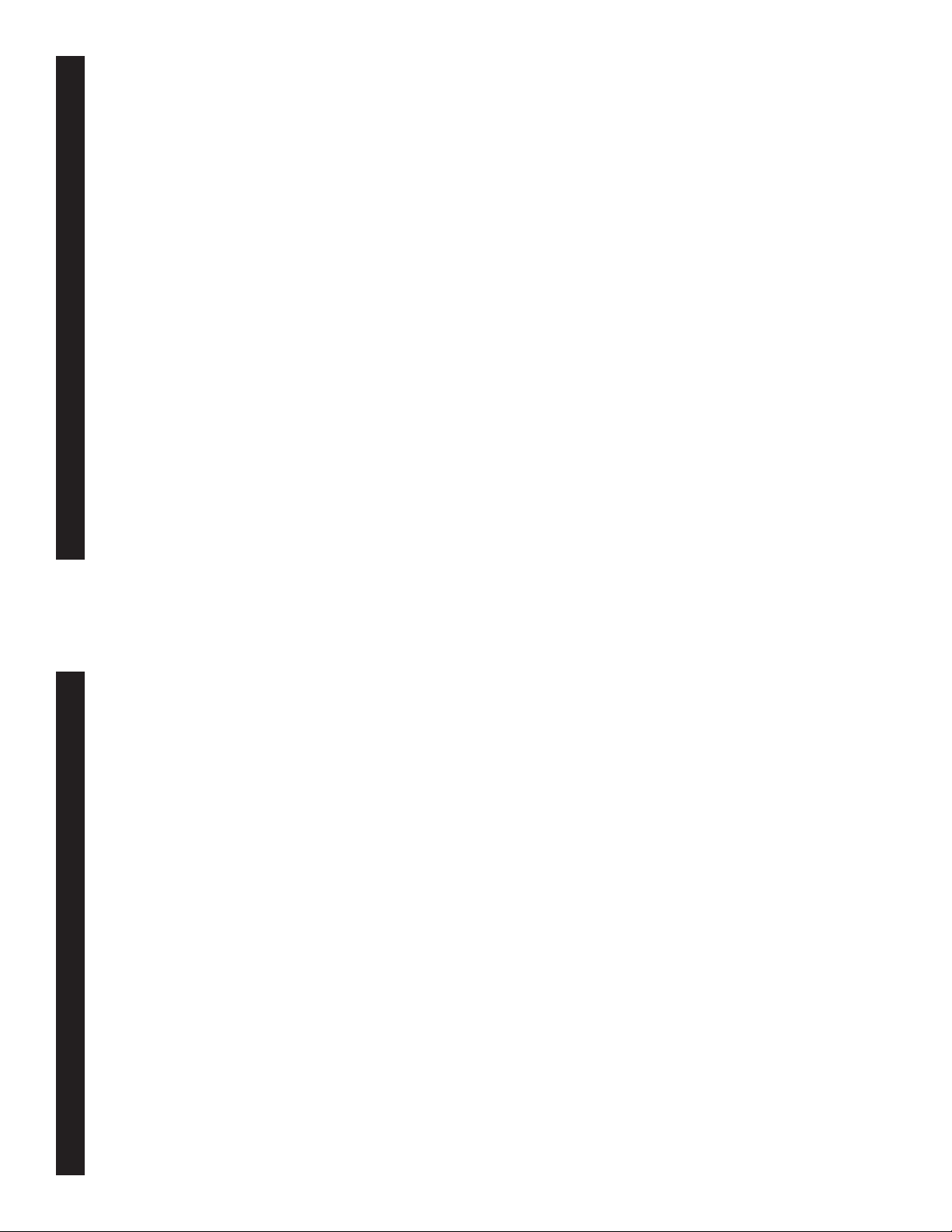
the fume hood on the oven exit end.
from the oven.
the frame extension on each end of the oven.
easier if a couple of long rods or poles are first pushed through the oven
and the belt is temporarily attached to the ends of the poles. This will allow
the belt to be pulled through the oven chamber from one end.
position. Refer to the Belt Tracking Adjustment section of this manual.
end of the belt and insert the provided splicing rod. Make certain the alligator
clips stay together while inserting the rod. Do not force the rod and make
certain the ends of the rod are flush with the ends of the alligator clip.
on the top edge of the end plates with the punch marks on the frame
extension. Tighten the end plate bolts.
• Connect the gearmotor to the outlet located on the receptacle box under
• Unroll the conveyor belt from each end of the oven. Do not remove the belt
• Pull the end of the conveyor belt around the end pulley and over the top of
• Push or pull one end of the belt through the oven chamber. This may be
• Loosen the end plate bolts and adjust the end plates in to their closest
• Bring the ends of the belt together. Align the teeth of the alligator clips on each
• Adjust the end plates back to their original positions. Align the punch marks
the instructions in the Belt Tracking Adjustment section of this manual.
• Run the belt and check for belt tracking. If necessary, adjust according to
gas type of “natural” or “propane”. NOTE: The dryer is set up from the
factory to run only on the gas type indicated on the I.D. tag.
gas inlet pressure. Normally 1-5 PSI for natural gas or 0.5-2 PSI for
• GAS TYPE: Refer to the serial number I.D. plate to identify the proper
propane gas.
• GAS PRESSURE: Refer to the serial number I.D. plate to identify proper
• The Main gas regulator is provided with a vent port. Depending on the size
3
of the room where the oven is installed, this port may need to be vented to
the outside of the building. Install in accordance with applicable State and
Local codes.
and protect the opening outdoors to guard against any blocking of the vent
line.
• If venting to the outdoors is required, vent to an approved location. Screen
installation of gas service to the oven is the responsibility of the end user.
• Compliance with all relevant Federal, State & Local building codes in the
State & Local building codes. Refer to the nameplate on the side of the
control box just above the electrical service entrance for voltage, phase
and rated full load amperage requirements.
to assure they are turning in the correct direction as indicated by arrows
placed on the motor housing. If the recirculating blower fan motors were
correctly wired during installation, then all motors would either be turning
in the right direction or would be running in reverse. To correct, reverse any
• Electrical service to the oven must be installed according to applicable
• Upon first applying power to the oven check the recirculating air fan motors
two wires on the 3-phase line-input side of the main contactor.
5. GAS HOOKUP AND REGULATOR VENTING
6. ELECTRICAL SERVICE
18
amp clamp to ensure it is within it’s ratings (refer to
the wiring diagram or motor nameplate for ratings).
Determine if motor is being overloaded. Never re-
place fuse with higher amperage than indicated on
wiring diagram.
TROUBLESHOOTING INSTALLATION / SET UP
clamp. If higher than stated on the nameplate, de-
termine the cause for the overloading of the motor
or replace the motor.
Problem: Motor starter kicks out.
Solution: Verify amperage drawn by the motor with an amp