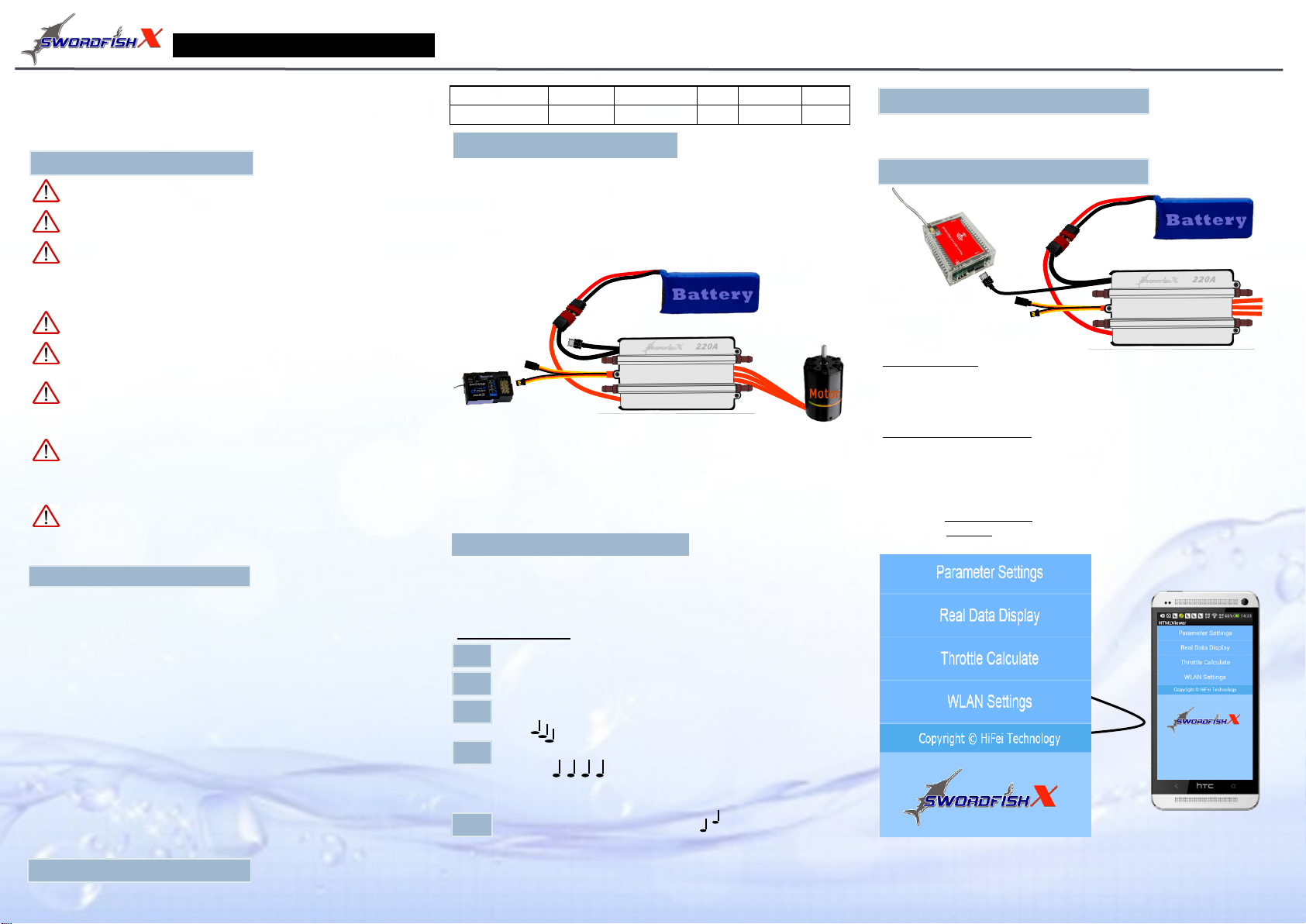
BRUSHLESS ESC INSTRUCTIONS
www.hifei.com
Thanks for purchasing SwordfishX brushless speed controllers manufactured
by HIFEI Technology Co., Ltd. SwordfishX series ESC are specifically developed to supply stable and strong power for R/C model boats beyond your expected.
Safety
Please always keep in safe when use ESC
Strongly recommend to calibrate the throttle range of transmitter when you first
use controller or when using a new /different transmitter or receiver
Before begin the running, turn on the transmitter BEFORE powering on the receiver.
When finish the running, power off the receiver BEFORE turning off the
transmitter.
Please DO NOT run Swordfish ESC without water flow.
Swordfish ESC is water-resistant, and thus cannot be soaked in water, which may
cause ESC failure or be burned.
Never disconnect the battery pack while the brushless motor is running, as this
could cause damage to the speed controller and/or motor. And such damage would
not covered under manufacturer’s WARRANTY.
It is suggest to add additional capacitor bank (such as HIFEI capacitor-bank 63V)
in the flowing two situations:
A: When run Swordfish X HV ESC with high KV motor with 10s or more lipos.
B: When run Swordfish X HV ESC at max current for a long time.
Swordfish ESC is preset with default parameters in factory, which can be assembled for running directly. In order to get optimum power performance and well
compatible to work with brushless motor, it is suggested to program ESC parameters before first run.
Features
·32-bit Microprocessor with up to 80Mhz frequency.
·Aluminum PCB process makes the heat dissipation efficient
·High Power Ultra-Low Internal Resistance 263-7 MOSFETS
·Telemetry Real Data By Wireless WIFI.
·ESC is with built-in data logging, Pro is without data logging.
·ESC is water-proof to prevent spill water , and aluminum water-cooler pipe is
pre-mounted.
·Full protection soft, include signal lose protection (in 100ms), temperature protection, motor block protection.
·ESC has Auto detect Lipo cells feature. Forward running mode is developed for
competitions.
·ESC is fully programmable by Hifei software on computer, or by Hifei Wifi
dongle
·ESC firmware is upgradeable by Hifei software on computer when a new version
firmware becomes available.
Specifications
ESC Voltage Current / Max BEC Size (mm)
SwordfishX 220A-6S
Install your ESC
Please solder good quality connectors to ESC’s motor wires and power wires before
connect ESC to motor and battery. When connect power wires to battery, it is IMPORTANT to correctly connect positive to positive, and negative to negative. Swap
any two motor wires’ connecting can change the rotation direction.
In order to prevent and reduce any signal disturbance generated by ESC hardware,
please install the ESC far away from receiver.
Step ①:Connect ESC to brushless motor;
Step ②:Connect receiver to the throttle channel of receiver;
Step ③:Connect receiver to ESC‟s receiver cable;
Step ④:Connect negative(-) cable of ESC to the negative of battery;
Step ⑤:Then connect positive (+) cable of ESC to the positive of battery.
Step ⑥: Switch on the ESC, after two beeps ♪ ♪ ,it is ready to run.
2-6 Lipos
Calibrate throttle of TX
Note: In the following 3 situations, it is required to calibrate the throttle range of transmitter.
-When it is the first time to use a new speed controller.
-When change a new TX or RX, or a set of new radio system.
-When upgrade the ESC into a new version of firmware.
220/ 300 4A,6V 110X55X28
Weight
240g
Board Transmitter
Connect ESC to motor, plug receiver lead of ESC to throttle channel of RX.
1st:
Push joystick of transmitter to max throttle position, power on TX.
2nd:
Power on receiver, connect ESC to battery. Motor emits three beeps in
3rd:
drop tones.
In the following, motor will emit four long beeps in flat tones.
4th:
After any one beep of the four long beeps, pull joystick to
zero immediately.
Then motor emits two beeps in up tones.
5th:
Calibrating is completed, it’s ready to go.
Note:SwordfishX ESC can not run in reverse. If throttle range were calibrated from reverse
to neutral, the calibrating range will be invalid.
Page 1
Program the ESC
SwordfishX ESC supports to be more easily programmed the parameters by Hifei programming
devices, such as ‘Hifei Wifi dongle’ and ‘Hifei USB Adoptor’(connection to PC).
Connect Wifi Dongle to SwordfishX
Hardware Request
• Keep the length of USB cable no more than 500mm
• Compatible to any kind of smart mobile phone,PAD or PC with iOS/Android/Windows
Operation System
• Support all kind of browsers such as: Chrome, IE, Safia, Firefox, etc.
Connecting the WiFi Dongle
• Connecting the cable to ESC and WiFi dongle ( Figure 1)
• Power on the ESC ( the red LED of dongle will light a while and then black out) , waiting
more than 20 seconds till the green led on dongle start to blink.
• Option SwordfishX in the WLAN list of your smart terminal
• Open your browser and input the default IP address & password as following:
IP address 192.168.1.16:2015
Password 12345678
• Entered into the Home Page
Please read Wifi Dongle user manuals for more information
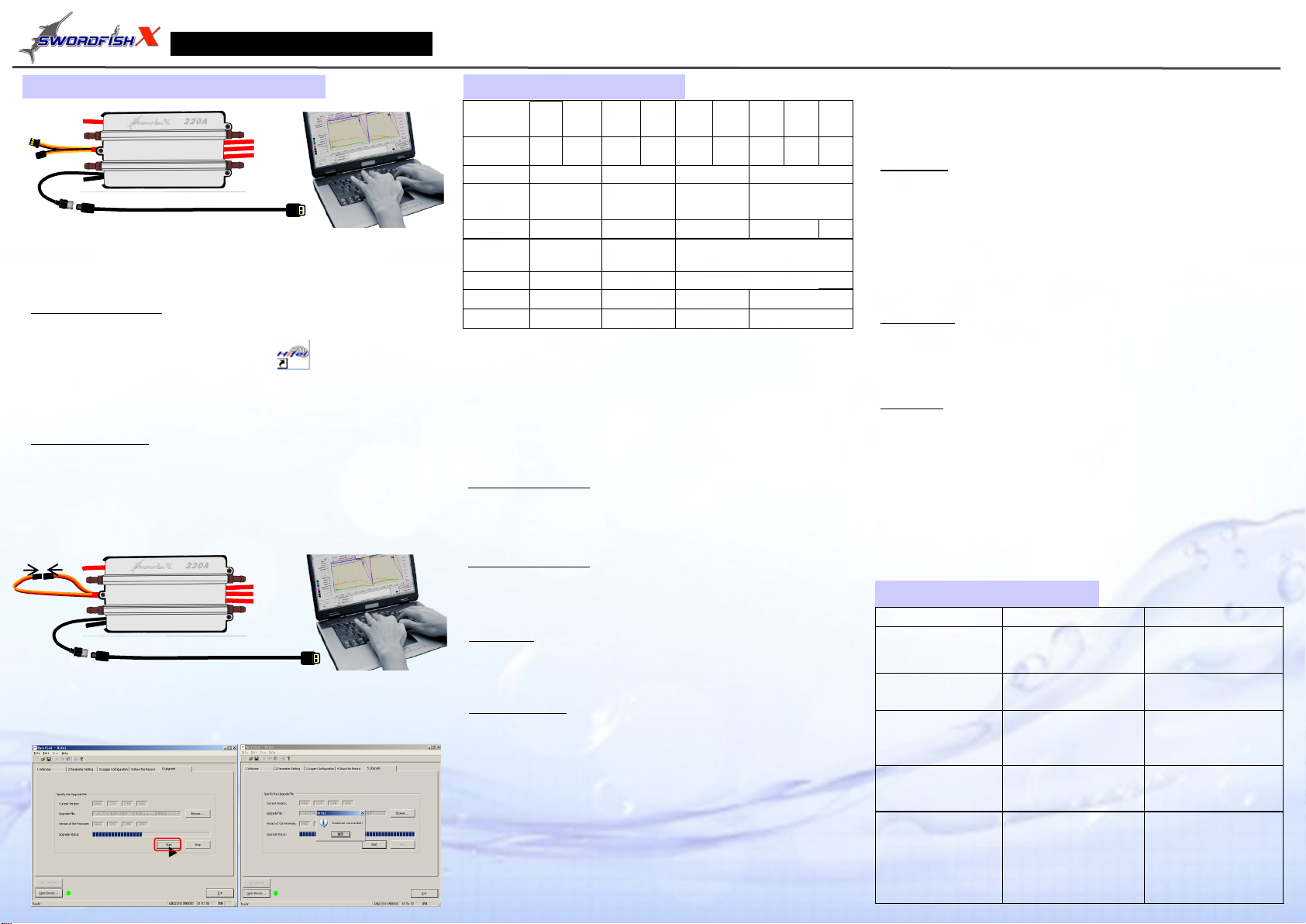
BRUSHLESS ESC INSTRUCTIONS
www.hifei.com
Connect ESC to PC
③
②
①
Step①: Correctly connect ESC‟s Wifi wire/to USB adaptor wire to USB adaptor
Step②:Plug the USB side of USB Linker to one of computer‟s USB ports
Step③:Run software “Hifei V6.xx”.
Note: ‘Please read USB adaptor user manuals for more information.
Install Hifei software
Download the setup software of „Hifei V6.xx‟ from website (Support column) and finish the
installation according to the popped-up window guide.
When installation is finished, „Hifei V6.xx‟ software icon is auto saved on computer
desktop.
Note: a. If PC OS is Windows 7,8,10, it is suggested to install V6.xx to administrator.
b. If you once changed PC font to big size, then it needs to change it to normal size. Because big size
font would possibly cause software interface cannot be showed in full.
V6.0 tab 5 Upgrade
In tab 5, you can upgrade ESC‟s firmware if there is a new firmware for the ESC be
released.
When upgrade the ESC, it needs to connect the cable to receiver with upgrade
cable together. (Pls refer to the below diagram)
Each ESC has specific firmware and be different. You have to make sure the firmware
you chose is correct. Otherwise possibly causing ESC damage.
①
③
②
Step①: Short upgrade cable with receiver wire.
Step②: Connect ESC‟s Wifi wire/to USB adaptor wire to USB adaptor
Step③: Plug the USB Adapter to an USB port of PC.
Parameters features
LVC (1)
Cutoff
voltage/ cell
Brake Type
Current
limitation
Timing
Active Free
Wheeling
Cutoff Type
Startup
PWM Rate
Note: a. The parameters with * behind are the ESC’s default settings.
b. When the ‘LVC’ of ESC is set at ‘Auto’ detect, after the two power beeps the ESC will beep
the number of Lipo cells which the auto detect feature detects, and the red LED on ESC will
blink in accompany with the beeps. ‘3.0v’ is the default cut-off voltage of per Lipo cell when
the LVC is set at ‘Auto’ detect.
Eg: If you connect the ESC to a 4s Lipo battery pack, the motor will firstly emit ♪ ♪ , then
detect the Lipo numbers ♪ ♪ ♪ ♪ , and the red LED will blink four times. The low voltage
cut-off is calculated as ‘12.0V’.
c. Please ensure only when the battery packs is fully charged and it can set the LVC at ‘Auto’,
it is recommended to set the LVC at actual Lipo cells once the battery pack is over 4S cells.
5.0V 2s
Auto
2.5V 2.6V 2.7V 2.8V 2.9V 3.0V* 3.1V 3.2V 3.3V
Close * Soft brake Hard brake
Low Medium High
Low Middle High Auto *
ON OFF*
Hard cutoff * Soft cutoff
Soft start Standard * Fast start
8KHz * 12KHz 16KHz
Lipos*
7.2V 8.4V 3s
Lipos
4s
Lipos
5s
Lipos
Disabled*
6s
Lipos
0~30
Low voltage cut-off
The setting of LVC can protect battery from discharging too low and causing
permanent damage to battery, especially for Lithium polymer cells. It is
strongly recommended to set the LVC carefully before running.
Cutoff voltage/ cell
The setting is to set the low voltage cut-off of each Lipo cell.
e.g. If set the LVC of per Lipo cell at „2.8v‟, the LVC is set at „2s cells‟, then
the cut-off voltage of the whole battery pack is “2.8*2”=5.6v.
Brake type
‘Brake disabled’ setting will close the brake function;
‘Soft brake’ will provide 20% of full braking power.
‘Hard brake’ will provide 100% of full braking power.
Timing advance
‘Low timing’ setting adjusts the timing at the range of 0º~15º, recommended
for more lower pole count brushless motors (such as 2 poles, or 4 poles). It
gives more power and slightly less efficient;
‘Middle timing’ adjusts the timing at the range of 5º~20º, recommended for
most brushless motors. It gives a good balance of power and efficiency;
‘High timing’ adjusts the timing at the range of 15º~30º, recommended for
higher pole count motors. (such as 8, 10, 12, 14 poles or higher brushless
‘Auto timing’ setting is automatically adjust the timing degree according to
motor‟s rotating demand. 0º; 2º; 4º; 6º; 8º; 10º; 12º; 14º; 16º; 18º; 20º; 22º;
24º; 26º; 28º; 30º. (This setting can be only set via software „Hifei V4.xx . If
you want to upgrade your old software .please download Hifei software from
Page 2
‘Auto timing’ setting is automatically adjust the timing degree according to motor’s
rotating demand. 0º; 2º; 4º; 6º; 8º; 10º; 12º; 14º; 16º; 18º; 20º; 22º; 24º; 26º; 28º; 30º.
(This setting can be only set via software ‘Hifei V4.xx . If you want to upgrade your
old software .please download Hifei software from www.hifei.com.)
Cutoff type
Cutoff type settings decide the way in which the ESC cutoff output to brushless
motor when the LVC works, or temperature/ signal-lost protection works.
‘Hard cutoff’ : when the battery volts discharges to the set LVC value or soft protection works, the motor will shut down immediately. Motor can be restarted by closing
the throttle to the lowest position and re-move the throttle as normal.
‘Soft cutoff’: when the battery volts discharges to the set LVC value or soft protection
works, the ESC will slowly reduce motor power to zero, you will notice a decrease in
power and it is time to dock.
Startup type
‘Soft start’: very soft and smoothly start the motor, it will take more time.
‘Standard start’: start the motor at normal speed, it depends on the motor’s quality
and dynamic response.
‘Fast start’: start the motor fast, it is recommended for racing.
PWM rate
8KHz is recommended for most brushless motors.
12KHz is recommended for low inductance motors. (e.g. 8,10,12,14 poles brushless
outrunner motors)
16KHz is recommended for very low inductance motors. (e.g. 16,18,20,24 poles
brushless outrunner motors)
Note: a. The poles mentioned above is the magnetic poles of brushless motor, but not the stator
numbers of motor.
b. High PWM rate is easier to make motor produce more heat. Cooling jacket for motor is very
important, and please be more carefully to choose high PWM rate.
c. It is strongly RECOMMENDED to have bench testing and choose appreciate parameters for
your configuration before assembling the ESC to hull for running.
Trouble shooting
Trouble Possible reason Shoot methods
The ESC started to smoke right
after it was powered on.
The ESC was unable to start the m
otorafter it was powered on. And n
o sound was emitted from the moto
When connect ESC to battery,
there is no power beeps emitted
from motor.
Motor shut down suddenly even at
full throttle or when not decrease
the throttle.
The ESC was unable to start the m
otor after it was powered on, but th
e motor beeped "B, B, B, ..."
1. Backward installation of batteries.
2. The input voltage was beyond the ESC
operating voltage.
Poor contact between the ESC and battery
connectors.
1.The battery voltage exceeds the range of
ESC’s working voltage. May it is too low
or too high.
2.Motor is damaged, or the ESC is not
well connected with motor.
1.Battery voltage discharge and drop
down to the set LVC, ESC cut-off output
to motor to protect the battery.
2. Over-heat protection
There was no throttle signal output from
the TH channel of receiver.
1. Refer to the "+, _" mark (on the ESC/
battery) and plug the battery in.
2. Refer to the user manual and plug in a
suitable battery.
Reconnect all the connectors between
ESC and battery or replace those
connectors
1. Check battery’s voltage and change
suitable battery pack.
2.Check the connectors, ensure ESC is
tightly connected with motor. Check
motor whether it is good.
1. Please stop the running and change a
new battery pack.
2. Stop running for a while until ESC is
cool down, check if water-cooling works.
1. Check if the transmitter and receiver
are well bound.
2. Check if the throttle cable has been
plugged into the wrong channel or
reversely plugged into the TH channel on
the receiver.
3. This ESC has no BEC output, a
separate battery or UBEC is needed to
power the receiver.