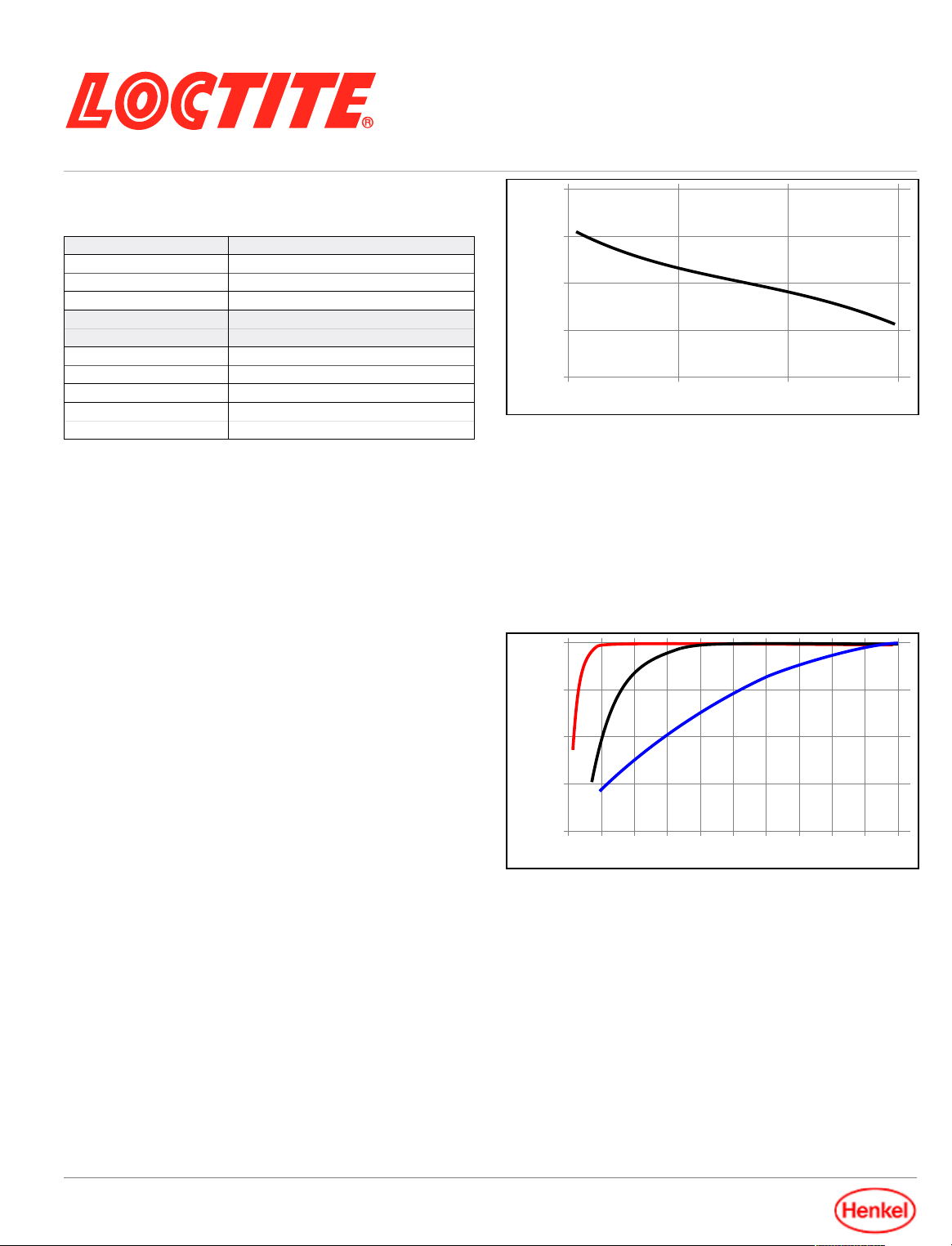
Technical Data Sheet
LOCTITE®3609™
March-2008
PRODUCT DESCRIPTION
LOCTITE®3609™ provides the following product
characteristics:
Technology Epoxy
Chemical Type Epoxy
Appearance (uncured) Dark, red viscous gel
LMS
Components One component - requires no mixing
Cure Heat cure
Application Surface mount adhesive
Key Substrates SMD components to PCB
Other Application Areas Small parts bonding
Dispense Method Syringe
Dispense Speed Medium 15,000 -25,000 dots/h
Wet Strength High
LOCTITE®3609™ is designed for the bonding of surface
mounted devices to printed circuit boards prior to wave
soldering. Particularly suited for applications where medium to
high dispense speeds, high dot profile, high wet strength and
good electrical characteristics are required. LOCTITE®3609™
has been used successfully in lead free processes with water
and alcohol based fluxes under conditions outlined in the
Environmental Resistance section.
TYPICAL PROPERTIES OF UNCURED MATERIAL
Specific Gravity @ 25 °C 1.2
Particle Size, µm <150
Flash Point - See MSDS
Yield Point, 25 °C, Pa
Cone & Plate Rheometer:
Haake PK 100, M10/PK 1 2° Cone
Casson Viscosity @ 25 °C, Pa∙s
Cone & Plate Rheometer:
Haake PK 100, M10/PK 1 2° Cone
250 to 700
0.16 to 2.0
LMS
VISCOSITY VS. TEMPERATURE
The following graph shows a typical temperature-viscosity
curve as measured using a Haake rotoviscometer PK100,
M10/PK1 2° Cone system at a shear rate of 2 s
-1
which is
representative of the shear rate in the dispense nozzle.
Increased cabin or nozzle temperature in the 30°C to 35°C
range may aid dispense performance at higher dispense
speeds.
400
300
200
Viscosity, Pa∙s
100
0
20 25 30 35
Temperature, °C
TYPICAL CURING PERFORMANCE
Recommended conditions for curing are exposure to heat
above 100 °C (typically 90-120 seconds @ 150 °C). Rate of
cure and final strength will depend on the residence time at the
cure temperature.
Cure Speed vs. Time, Temperature
The following graph shows the rate of torque strength
developed with time at different temperatures. These times are
defined from the moment the adhesive reaches cure
temperature. In practice, total oven time may be longer to allow
for heat up period. Strength is measured on 1206 capacitors @
22 °C, tested according to IPC SM817, TM-650 Method 2.4.42.
100
75
50
25
% of Full Strength
150°C
0
0 1 2 3 4 5 6 7 8 9 10
125°C
100°C
Time at Temperature, minutes
TYPICAL PROPERTIES OF CURED MATERIAL
Cured for 30 minutes @ 150 °C
Physical Properties:
Coefficient of Thermal Expansion,
ISO 11359-2, K
Coefficient of Thermal Conductivity, ISO 8302,
W/(m·K)
Glass Transition Temperature, ASTM D 4065, °C 73
Specific Heat, kJ/(kg·K) 0.3
Density, BS 5350-B1 @ 25 °C, g/cm³ 1.4
-1
145×10
0.4
-6

TDS LOCTITE®3609™, March-2008
Electrical Properties:
Surface Resistivity, IEC 60093, Ω 2×10
Volume Resistivity, IEC 60093, Ω·cm 2×10
Surface Insulation Resistance, Ω:
SN 59651:
Initial 0.1×10
Aged for 4 days @ 40 °C, 93 % RH 10×10
Aged for 21 days @ 40 °C, 93 % RH 1×10
Electrolytic Corrosion, DIN 53489 AN-1.2
Dielectric Constant / Dissipation Factor, IEC 60250:
1-kHz 3.7 / 0.009
10-kHz 3.3 / 0.03
1,000-kHz 3.2 / 0.03
10,000-kHz 3.1 / 0.03
15
15
9
9
9
TYPICAL PERFORMANCE OF CURED MATERIAL
Adhesive Properties
Cured for 10 minutes @ 110 °C
Push-off Strength:
C-1206 on bare FR4 board N ≥20
(lb) (≥4.5)
Cured for 5 minutes @ 125 °C
Pull-off Strength, Siemens norm SN59651:
C-1206 on bare FR4 board N 40 to 80
(lb) (9 to 18)
Torque Strength, IPC SM817 , TM-650 Method 2.4.42:
C-1206 on bare FR4 board N·mm 30 to 70
(in.oz) (4 to 10)
Cured for 30 minutes @ 150 °C
Lap Shear Strength, ISO 4587:
Steel (grit blasted) N/mm² ≥10
(psi) (≥1,450)
LMS
LMS
Bond strength achieved in practice will vary considerably
depending on the SMD component type, adhesive dot size
and the type, grade and degree of cure of the solder
mask/resist.
TYPICAL ENVIRONMENTAL RESISTANCE
Cured for 30 minutes @ 150 °C
Lap Shear Strength, ISO 4587:
Mild steel (grit blasted)
Hot Strength
Tested at temperature
100
75
50
25
% Initial Strength at 22 °C
0
0 25 50 75 100 125 150 175
Temperature, °C
Chemical/Solvent Resistance
Aged under conditions indicated and tested @ 22 °C.
% of initial strength
Environment °C 100 h 500 h 1000 h
Air 22 100 100 95
Air 150 85 70 70
Heat/humidity 98% RH 40 110 110 100
Resistance to Hot Solder Dip
Cured for 90 seconds @ 150 °C
Hot Solder Dip, IPC SM817, TM-650 Method 2.4.42.1, Pass/Fail:
R-1206 on bare FR4 board:
Supported 60 seconds above solder
bath @ 260°C and dipped for 10
seconds
Pass
Resistance to Process Conditions
Cured for 90 seconds @ 150 °C
Torque Strength, IPC SM817 , TM-650 Method 2.4.42, % of initial
strength retained:
C-1206 on bare FR4 board:
Aged 30 seconds preheat to 100°C
and 3 seconds @ 260°C with flux and
wave solder
100
Resistance to Lead Free Solder
LOCTITE®3609™ can be used in lead free wave solder with
both water based and alcohol based fluxes
Lead Free Solder Test Conditions
Flux Types Multicore MF200 (alcohol based) and
Wave Condition 100°C pre-heat with dual wave at 260°C
Components C1608 bonded with twin dot 0.8mm
Result No component loss in the wave
Multicore MF300 (water based)
SOD 80 bonded with single dot 1.1mm
GENERAL INFORMATION
For safe handling information on this product, consult the
Material Safety Data Sheet (MSDS).
Directions for use
1.
LOCTITE®3609™ is supplied de-aerated in a range of
ready-to-use syringes which fit straight into a variety of air
pressure/time dispensing systems commonly available.
2. After storage in a refrigerator the adhesive must be
allowed to equilibrate to room temperature before use,
typically 2 to 4 hours.
3. Avoid cross contamination with other adhesive residues
by ensuring dispense nozzels, adapters etc. are
thoroughly cleaned.
4. Do not leave dirty nozzles on dispensing equipment while
not in use or soaking in solvents for long periods of time.
5. The quantity of adhesive dispensed will depend on the
dispense pressure, time, nozzle size and temperature.
6. These parameters will vary depending on the type of
dispensing system used and should be optimised
accordingly.
7. Dispensing temperature should ideally be controlled at a
value between 30 °C to 35 °C for optimum results,
however higher dispense temperatures are possible.
8.
LOCTITE®3609™ can also be dispensed using positive
displacement pump systems.
9. The product is not recommended for dispensing by pin
Henkel Americas
+949.789.2500
Henkel Europe
+44.1442.278.000
For the most direct access to local sales and technical support visit: www.henkel.com/electronics
Henkel Asia Pacific
+86.21.2891.8000