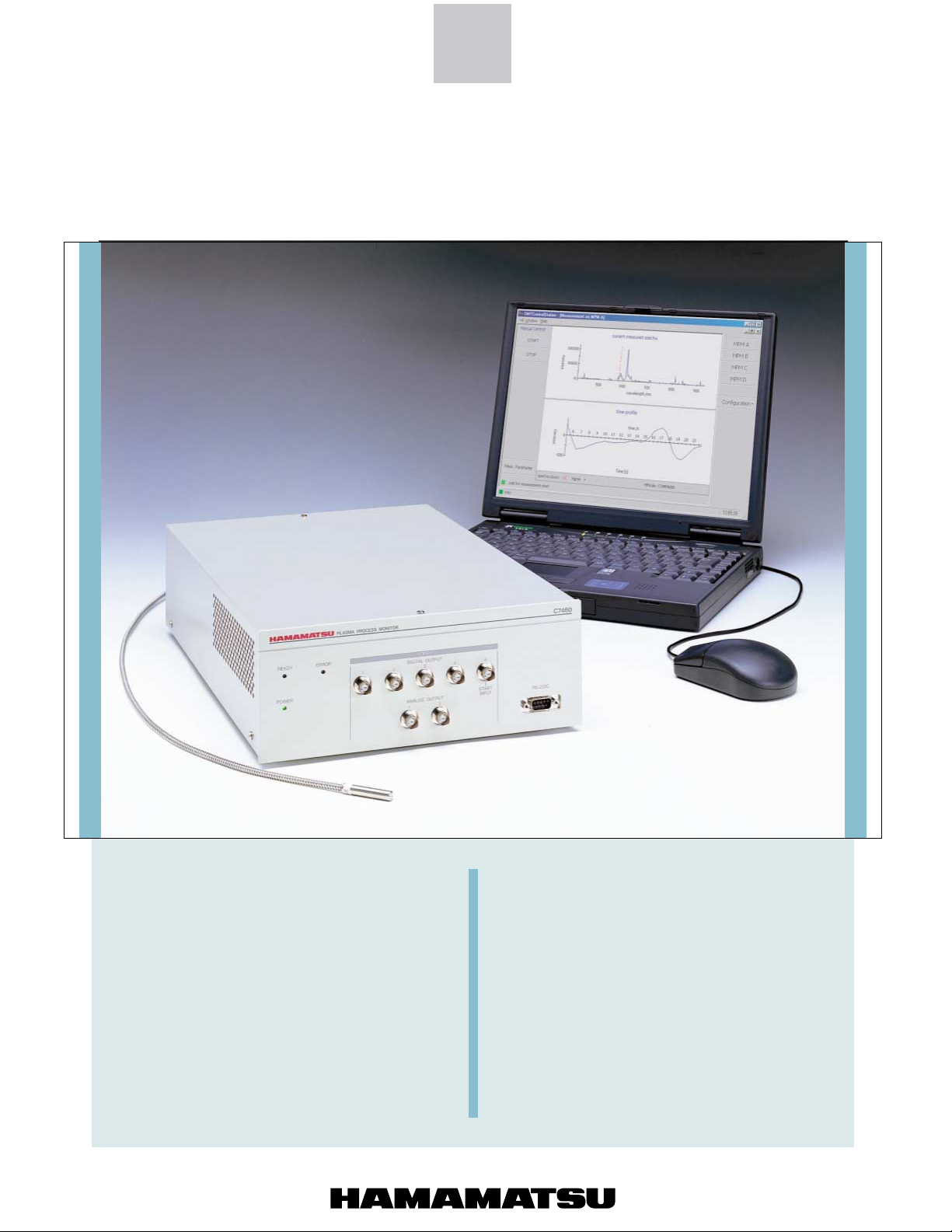
Multiband Plasma-Process Monitor
Model C7460
The Multiband Plasma-Process Monitor
(MPM) is a system specifically designed for
monitoring the optical plasma emissions that
are created during the various manufacturing
processes of semiconductors including
etching, sputtering, cleaning, and CVD.
The MPM can handle multi-channel recording
in real-time.
●
Simultaneous measurement
from 200 to 950 nm
●
Easy measurement using
optical fiber input
●
High levels of accuracy and
reliability
Software for measurement,
●
analysis and factory integration

Real-Time Plasma Monitoring
Real-Time Plasma Monitoring
BACKGROUND
Up to 60 percent of the time that a piece of semiconductor manufacturing equipment spends in operation is generally for non productive jobs like plasma cleanup, chamber stabilization (seasoning) and
system diagnosis. Typical approaches for reducing
down-time and repetitive processes like these are to
PLASMA ETCHING
utilize Advanced Process Control (APC) and Sensor
PLASMA ETCHING
Based Process Control (SBPC) technologies with
factory LAN services. The MPM allows you to gain
full control over processes using information provi-
SPUTTERING
SPUTTERING
ded by the MPM regarding plasma spectra, etching
end-point detection status, plasma fault status, etc.
The MPM opens the possibility of significantly increasing the efficiency of manufacturing equipment.
CONFIGURA TION OF APC WITH MPM (EXAMPLE)
FEATURES
Ethernet
● Highly Accurate and Reliable
The MPM employs a high-resolution compact spectrograph and a highly sensitive detector which diagnose plasma with elevated levels of precision.
Along with these superior photometric characteristics, the MPM is compact, sturdy and offers the high
standards of reliability that are required in a manufacturing environment.
● Easy to Operate
The MPM is equipped with a sturdy fiber optic bundle, which can conveniently be combined with the
plasma chamber. Due to this, and due to its easy-to
use software, the MPM is easy to setup and operate.
● Intelligent Sensor System
The MPM is not just a spectrograph. It also contains internal data processing capabilities which allow to extract and compress the relevant infomation from the
data.
● Easy Fab Integration
The MPM is equipped with several interfaces including Ethernet and a TCP/IP protocol stack. Together with its very verstile software framework this
allows the easy integration into existing fab IT infrastructure.
Ethernet
HUB
Ethernet
MPM
C7460
12
34
5
POWER
POWER
POWER
POWER
RS-232C
1
2
C7460
12
34
5
RS-232C
1
2
C7460
12
34
5
RS-232C
1
2
C7460
12
34
5
RS-232C
1
2
Script output (end point, plasma fault status, etc)
Optical fiber
STANDARD CONFIGURATION
MPM Standard Configuration
12
POWER
Fiber input optics
34
1
2
Main unit
U9046 Plasma Process Data Aquisition Software
Windows 98, NT, 2000
2
C7460
5
RS-232C
Ethernet (TCP/IP)
Computer
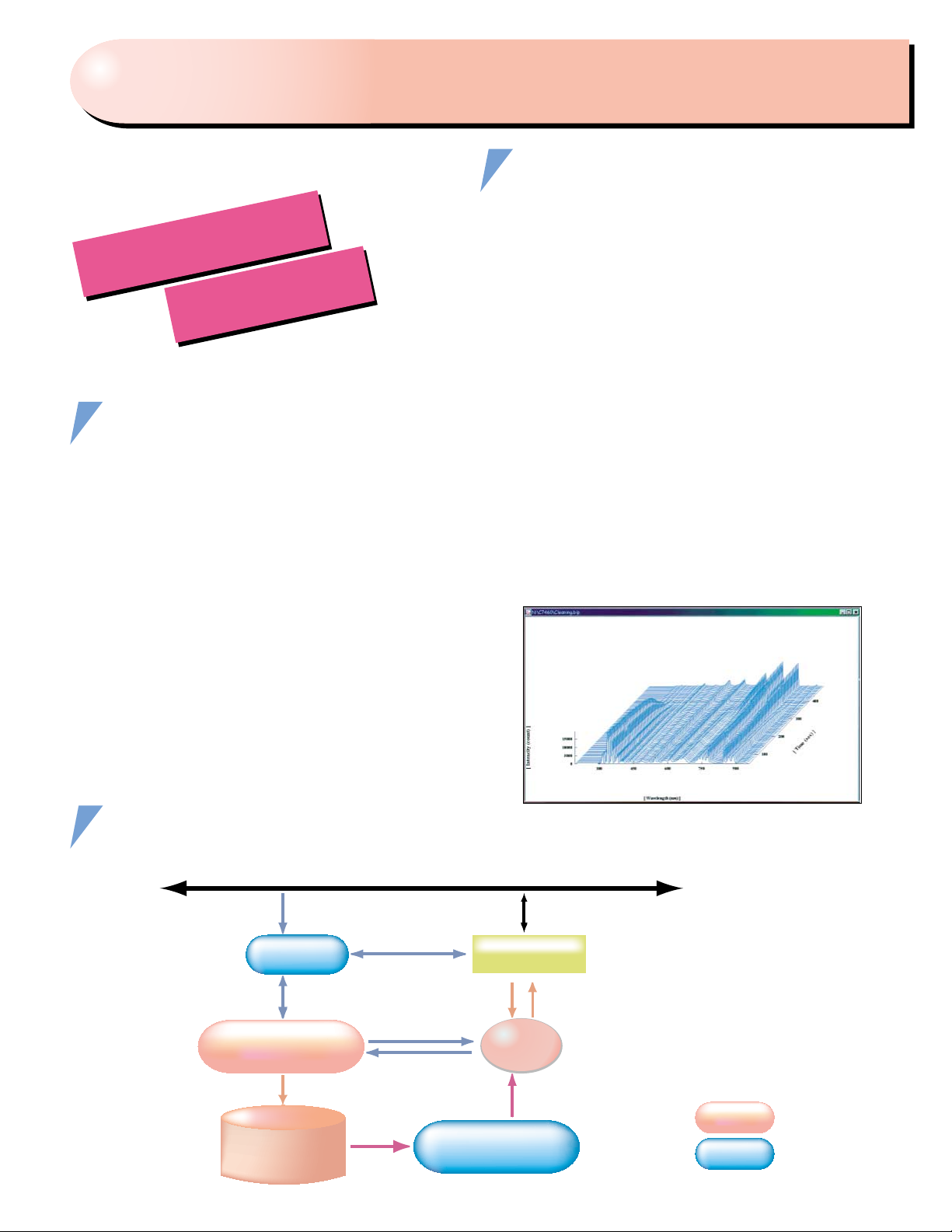
Simultaneous Measurement
Simultaneous Measurement
from 200 nm to 950nm
from 200 nm to 950nm
BENEFITS (EXAMPLES)
● Easy Plasma Status Settings
Real-time monitoring of the plasma process supports easy to
make settings for the volume of introduced gas and plasma power.
PLASMA CVD
PLASMA CVD
CLEANING
CLEANING
APPLICATIONS OVERVIEW
Due to the high versatility of the hardware and the software framework, the MPM is suitable for various different
applications, without any compromise in performance or
convenience. These applications can be grouped into the
following categories:
● Engineering Tasks
Such as process optimization, comparison and matching;
trouble-shooting; etc.
● Endpoint Control
Advanced, highly specific and sensitive end point control.
● Fault Detection
Highly selective automatic fault detection.
● APC Sensor
Automatic extraction of highly specific APC key numbers.
(Under development)
Product yield is increased through improved processing stability,
and the early discovery of abnormalities.
● Advanced Endpoint Detection
Powerful scripts can be defined as recipes for each endpoint
detection. It is possible to use the information in the whole
spectrum by means of the unique spectral patterns method.
This allows for advanced endpoint control with unprecedented
specificity and precision.
● Higher Efficiency through Automatic Cleaning Control
Particularly with CVD, in which the chamber must be cleaned
each time a wafer is processed, cleaning time has a major effect
on actual operating efficiency. The automatic control features
greatly improved throughput, increased productivity, and reduced
costs.
● Monitoring of Impurities and Abnormal Discharges
Monitoring of the emission band, which does not occur in normal
processes, provides warning of impurities and abnormal discharges before they occur, and thus improves yield.
SYSTEM STRUCTURE
Driver Software
control
process data
U9046
Plasma Process
Data Acquisition Software
Database
spectrum data
with process data
Network
Plasma
Emission
control
spectrum
data
U8851
End-point Synthesis Tool
▲3-d display of plasma emission of CVD Cleaning (CF4, O2, Ar) of SiN
Plasma equipment
EPD signal
MPM(C7460)
(Hardware)
formula for
end-point detection
Standard
Optional
3