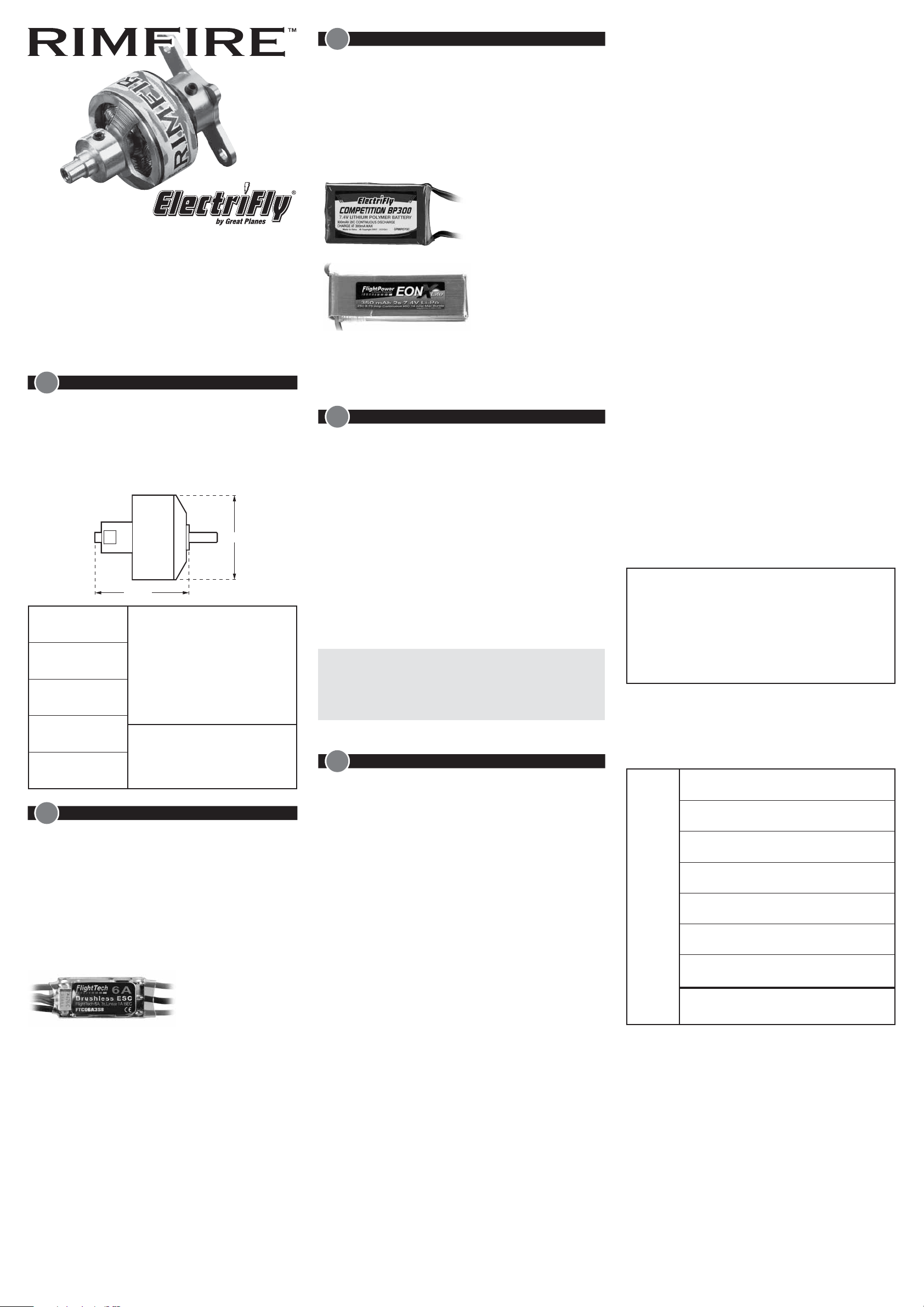
200 POWER
SYSTEM
Thank you for purchasing the RimFire 200 brushless outrunner
motor! You’ll be pleased with the performance of this micro
motor. We’ve carefully designed this motor to give you the
best performance while using the most popular propellers and
batteries. To get the most out of your RimFire 200, please use
only a 7.4V (2S) LiPo battery. The following instructions will
help you mount your motor and select the right components
to complete your power system.
MOTOR SPECIFICATION
1
Model Stock #
RimFire 200 (18-19-2400) GPMG4455
The RimFire motors are labeled to provide the most information
at a glance. For example: the RimFire 200 (18-19-2400) is
18mm in diameter, 19mm long, and has a kV (rpm-per-1volt)
of 2400 rpm.
18 mm
19 mm
Motor
0.71 in
Diameter
Overall
Length
Diameter
Length
Length
2
An ESC is basically the device that controls your motor through
your radio system. Never run any RimFire motors with a brushed
ESC. It will not work and you may damage both the motor and
the ESC. Always use a brushless ESC. When choosing an ESC,
choose one that is rated to handle at least the maximum current
your power system will draw during full-throttle operation.
ElectriFly offers Brushless ESCs that will work with the RimFire
200 motor.
Shaft
Shaft
Lead
(18mm)
0.74 in
(18.8mm)
0.079 in
(2.0mm)
0.20 in
(5mm)
1.57 in
(40 mm)
Max. Constant Current 4.9 A
Max. Surge Current 6.3 A
Max. Constant Watts 36W
Weight
0.38 oz (10.7g) 0.44 oz (12.4g)
ELECTRONIC SPEED CONTROL (ESC)
For the RimFire 200 we recommend this high quality,
lightweight ESC:
Connectors 3-pin micro
Burst Watts 47W
No Load Current 0.35A
Input Voltage 7.4V
motor
only
FlightPower
6A Brushless ESC w/BEC
(FPWM0206)
Weight = 0.20oz [5.7g]
motor, mount,
& prop adapter
®
(2S LiPo)
BATTERIES
3
Cells can be connected in series or in parallel. Usually batteries are
labeled by their number of cells, such as a 2-cell LiPo. This means
the cells are connected in SERIES (S). Arranging batteries in series
gives you more power (higher voltage).
Each LiPo battery has 3.7V, so a 2-cell LiPo
•
battery has 3.7 x 2 = 7.4V
When selecting batteries, please consider weight. Because of this,
we recommend the following batteries:
Great Planes® ElectriFly
300mAh 7.4V 2S 20C LiPo
(GPMP0700)
Weight = 0.7oz [19.6g]
FlightPower EON-X Lite
350mAh 7.4V 2S 25C LiPo
(FPWP4014)
Weight = 0.8oz [23g]
Due to the constantly changing battery technology, check out the
ElectriFly web site at www.electrifl y.com for the most up-to-date
listing of the ElectriFly battery line.
PROPELLER
4
For any given voltage, an electric motor’s load is determined by
the propeller chosen. A propeller that is too small will not take
advantage of the power that the motor can produce. A propeller
that is too large will cause current draw to exceed the maximum
allowed continuous current. This can catastrophically damage the
motor and/or ESC.
The fi rst number in a propeller designation is the diameter in inches.
The second number refers to the theoretic pitch in inches traveled
for one complete rotation of the prop. So, a 6x3 propeller measures
6" [152mm] in diameter and travels 3" [76mm] forward for one
complete revolution (360°). Generally, when sizing up a prop, going
up in diameter gains more thrust (immediate punch-out power).
Going up in pitch results in a higher top speed.
For the RimFire 200 we recommend the following propellers.
™
Best all-around performance
GWS 7x3.5 Propeller (GWSQ2008), 4.9A @ 7.4V, 8760rpm
Sport performance
GWS 6x3 Propeller (GWSQ2007), 4.0A @ 7.4V, 10620rpm
DETERMINE WHAT YOU NEED to BUILD YOUR POWER SYSTEM
5
Now that you have one component for your power system, there
are several different ways to select the rest. In time, experience will
help you to determine what works best for you, but an easy way to
determine what you need now is the following.
Procedure #1: If you know the size of the propeller you want to
turn and the rpm, then:
1. Find the combination that delivers the closest performance to what
❏
you want (refer to the ElectriFly web site for typical combinations),
or refer to the airplane manufacturer’s recommendations.
2. Note the recommended battery voltage.
❏
3. Determine the battery capacity needed based on the current
❏
draw of your system and your desired fl ight time.
4. Determine the ESC you need based on the system current
❏
draw. See the ESC section.
Procedure #2: If you know the approximate weight of your
airplane, including the motor and battery, and the performance
you want from it, answer the questions below to determine the
correct power system for your plane. You may need to make
more than one calculation using different motors and battery
combinations. See the battery section for some of the battery
weights for the suggested batteries.
1. Perform the following calculation to determine the wattage
❏
required:
If you expect trainer-like performance then multiply
•
75 x Airplane Weight (lbs).
If you expect aerobatic or high speed-like
•
performance then multiply 100 x Airplane
Weight (lbs).
If you expect 3D or extreme performance multiply
•
150 x Airplane Weight (lbs).
Note: To conver t gr ams to lbs, divide by 454. To conver t ounces
to lbs, divide by 28.
2. The number you get is the minimum wattage you will need
❏
for your plane to perform as you wish. Watts = current (A) ×
voltage (V). Using suggested power system combinations
for reference, determine what combination gives you the
performance you want based on wattage and maximum
propeller size that will fi t on the plane.
3. Note the recommended battery voltage.
❏
4. Determine the battery capacity needed based on the
❏
current draw of your system and your desired fl ight time.
5. Determine the ESC you need based on the system current
❏
draw. In addition to these two procedures, you can also
visit the Great Planes ElectriFly web site for descriptions
of the power systems recommended for our line of
electric airplanes as well as more detailed explanation
on the subject.
Essentially when using this rule, the maximum weight of
your model (fully equipped w/ battery, radio, etc.) should
be as follows when using this motor.
Trainer 7.7oz [219g ]
Sport 5.8oz [165g]
3D 3.9oz [110g]
To help you plan your power system requirements for your
project, use the following table to come up with a total weight.
Keep in mind that weight is critical in this size range.
RimFire 200
12.4 grams
Prop
Battery
Servos
Receiver
ESC
WEIGHT TABLE
Airframe
Total Weight
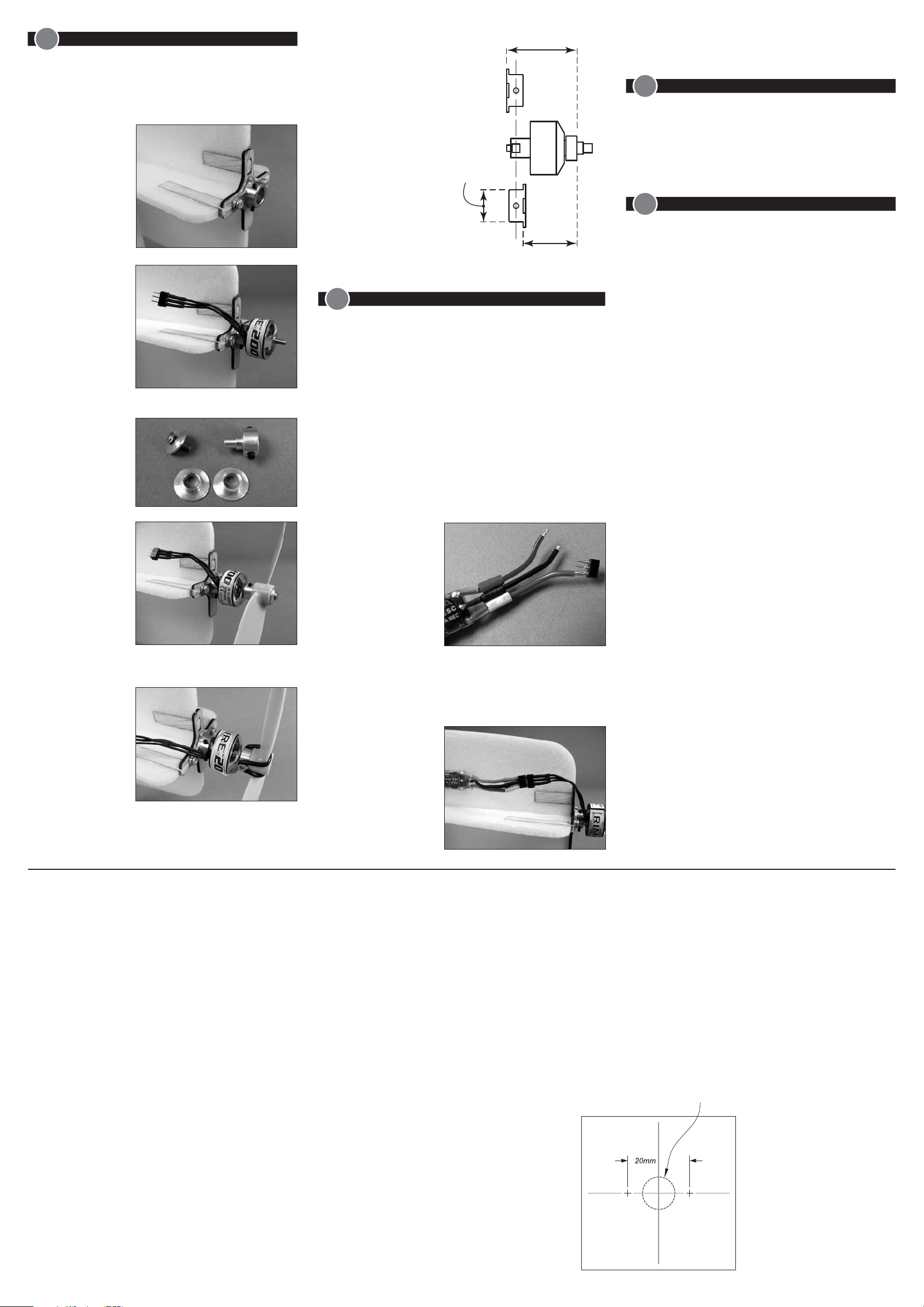
MOTOR INSTALLATION
6
1. Cut out the mounting template at the end of this manual. Line
up the crosshair alignment marks on the template with the
marks on the fi rewall of your model. Stick the template in place.
Drill two mounting screw holes in the fi rewall using a 1/16"
[1.6mm] drill.
2. Install the mount
onto the fi rewall using
two #2 x 3/16" [4.8mm]
sheetmetal screws (not
included). Remove the
screws and harden the
screw hole with thin
foam-safe CA. Reinstall
the mount.
3. Fit the motor to the
mount. Rotate the
motor so that the motor
wires can be routed in
the desired direction.
Install the two set
screws using thread
locking compound on
the screw threads. With
the motor in position,
tighten the set screws securely.
4. The prop adapter
is stepped to fi t 3mm
and 4mm prop hubs.
We have also included
a 5mm and a 6mm
bushing.
5. You have two options
when installing the
propeller. To install the
propeller using the
standard method,
install the two set
screws in the prop
adapter hub. Fit the
prop and bushing (if
needed) and install the
prop washer and screw. Use thread locking compound on all
screw threads.
6. If you choose to
use the “prop saver”
attachment method,
install the two M2 x
6mm countersunk
machine screws in the
prop adapter hub. Fit
the prop and bushing
(if needed) and fi t the
prop. Hook the rubber O-ring to one of the countersunk screws.
Stretch it across the hub of the prop and hook it onto the other
countersunk screw to retain the propeller. Use thread locking
compound on all screw threads.
If mounting space is a
concern, you can fl ip the
motor mount around and
decrease the amount of
space you need to mount
the motor. If you want to
do this, use the template
in this manual to help you
grind away a hole to allow
the motor mount to drop in.
22.8mm
9.5mm
17.8mm
ESC INSTALLATION
7
We recommend that you use a variable temperature soldering iron
with a very fi ne tip. We suggest using the Team Checkpoint® TC-950
Soldering Station (TCPR0950) with the 1mm pencil tip. A set of
“helping hands” is also useful for soldering (XACR4214).
1. Strip off about 1/8" [3.2mm] of insulation from the end of each
motor wire on the ESC. Apply some soldering fl ux to the bare wires
and twist the end of each wire to neatly tighten the strands. Do this for
each individual wire. Tin the tips of each wire using electrical solder.
2. Cut three pieces of heat shrink tubing to a length that completely
covers each bare wire. Generally, you’ll need about 5/16" [7.9mm]
of heat shrink to cover each wire, but enough material is provided
for you if you need more. Apply fl ux and tin each pin of the female
connector as well.
3. Fit the heat shrink tubing
to each wire and slide it as
far away from the tip of the
wire as you can. Solder
each ESC lead to each pin of
the included female 3-pole
micro connector. Slide the
pieces of he at shrink tubing
into position and use heat
to shrink the tubing. Note:
Any wire can be connected to any pin.
4. Mount the ESC to your model using double-sided tape or hook
and loop material. Make sure that you choose a place that will allow
all of the wires to reach. Plug the ESC signal lead into your receiver.
5. Connect the male motor
connector to the female ESC
connector. Energize your
radio system. Connect a
2-cell LiPo battery to the
ESC. Using the throttle,
test the direction of motor
rotation. The motor should
rotate counter-clockwise as
viewed from the front of the
motor. If it does not rotate correctly, unplug the micro 3-pole
connector and rotate it 180°. This will reverse the motor rotation.
Note: Do not install the prop for this step.
RIMFIRE MOTOR MAINTENANCE
8
RimFire brushless motors require virtually no maintenance.
There are no brushes to wear out and replace. The precision
bearings have a very long service life and should last a very
long time. The internal parts of the motor should not require
any cleaning. The only thing that needs to be checked is to make
sure all the screws and set screws remain tight.
IMPORTANT PRECAUTIONS
9
Once the battery is connected to the ESC, stay clear of the
motor and prop.
DO NOT apply an input voltage that exceeds the maximum
•
specifi cation of each motor.
DO NOT apply currents to the motor that exceed the maximum
•
specifi cations of each motor.
DO NOT allow the input connectors to accidentally touch
•
each other while power is applied to the motor. Make sure
all input connections are insulated electrically.
DO NOT allow water or moisture to enter the motor, as it can
•
cause permanent damage to the motor and possibly short
out the attached ESC.
DO NOT cut the coated wires from the motor. If you must
•
remove the connector, please unsolder it.
Allow the motor to cool after each fl ight.
•
The shaft of the motor will rotate at very high rpm. DO NOT
•
attempt to touch the shaft while it is rotating. If setting up
the motor/ESC on the workbench, make sure the motor is
securely attached and that nothing is attached to the motor
shaft BEFORE applying power.
NEVER attempt to use a damaged motor (having mechanical
•
or electrical defects).
ElectriFly carries a complete line of Ammo™ (in-runner style)
•
and RimFire (out-runner style) brushless motors, gear drives,
motor mounts, prop adapters and speed controls. For a
complete list of these products, check out our web site at:
www.greatplanes.com, www.electrifl y.com or visit your
nearest hobby shop that carries the full line of Great Planes
and ElectriFly products.
© 2010 Hobbico,® Inc. GPMG4455
If you need to reduce the mounting space, flip over the motor mount and cut out this hole.