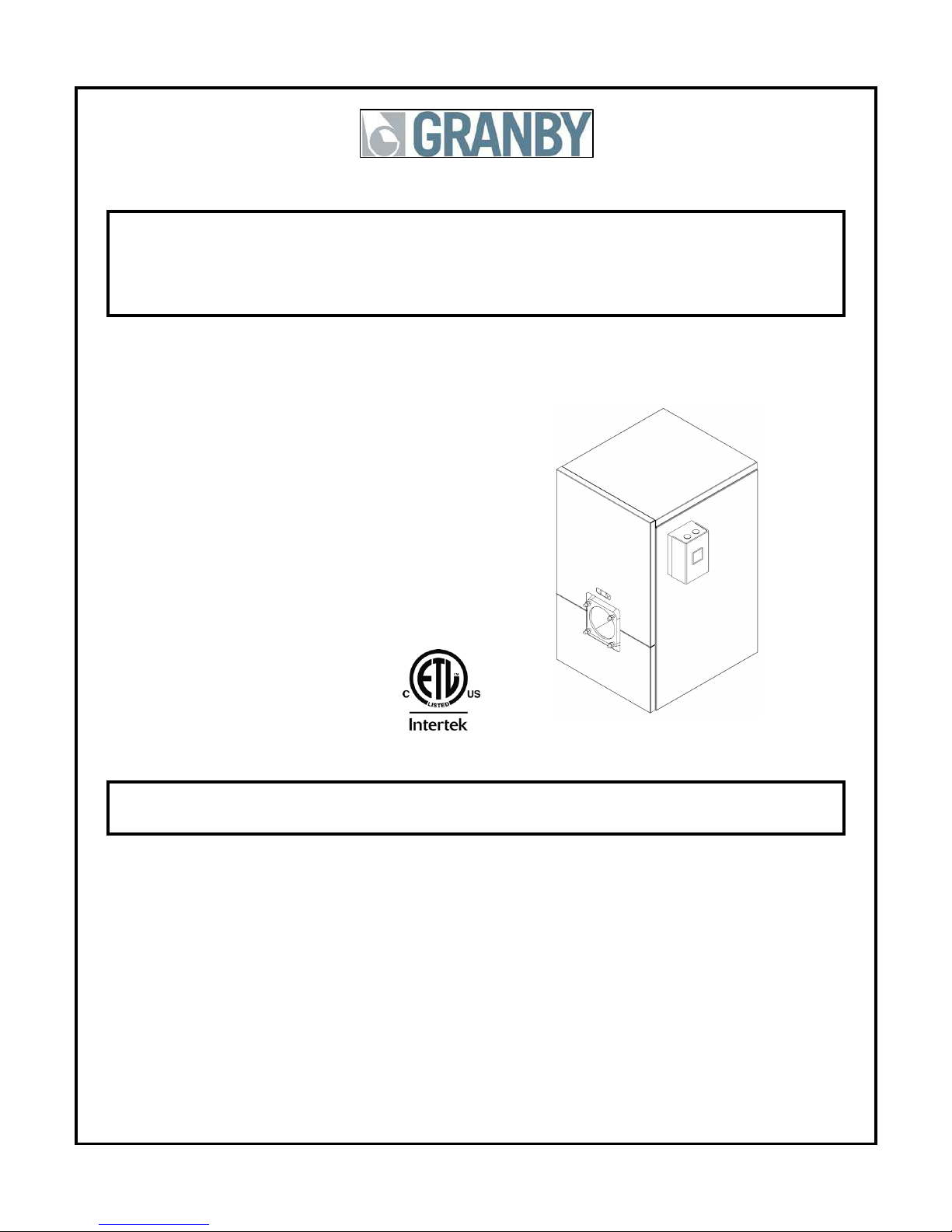
Installation, Operation and
Service Manual
Cast Iron Boiler
SERIES
* *
*Designates Brand Name
B*C, 3 sections illustraded
INSTALLATIONS MUST MEET ALL LOCAL AND FEDERAL
CODES THAT MAY DIFFER FROM THIS MANUAL
Please read the manual in its entirety before beginning installation.
This manual must be kept with the boiler for future reference.
GRANBY FURNACES INC.
PO Box 637
12118 Hwy 209
Parrsboro Nova Scotia Canada
B0M 1S0
www.granbyindustries.com
30-10-2015 G2012-E5 Rev. D
B*C-4 sections
B*C-5 sections
B*C-6 sections
B*C-7 sections
B*C-8 sections
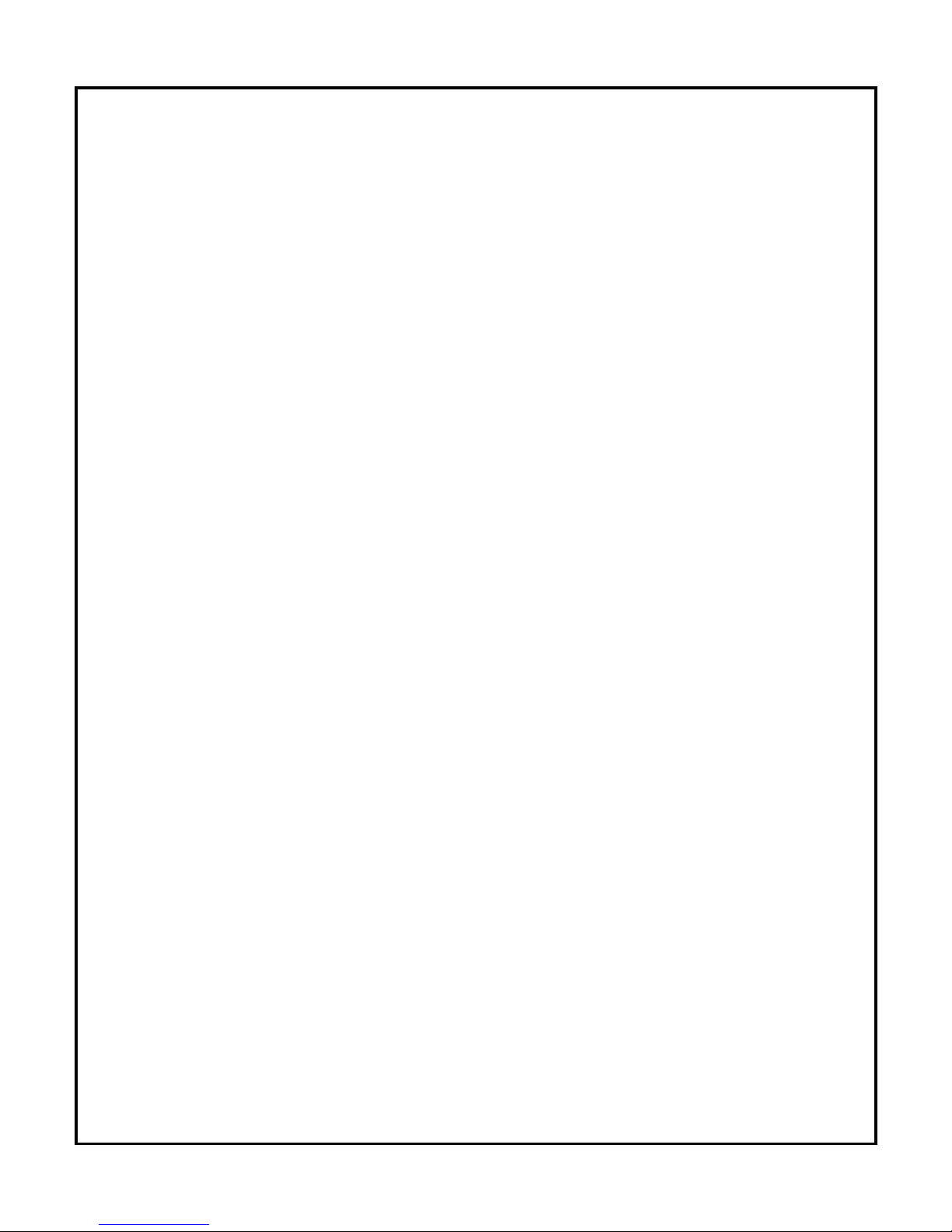
1
TABLE OF CONTENTS
B*C – Oil
1.0 IMPORTANT SAFETY ADVICE 2
2.0 PRODUCT INFORMATION 3
3.0 UNIT INSTALLATION 4
3.1 PLACEMENT & LEVELING OF THE UNIT 4
3.2 JACKET ASSEMBLY & CONTROL INSTALLATION 4
4.0 PIPING 8
5.0 ELECTRIC WIRING 11
6.0 CHIMNEY INFORMATION 13
7.0 FUEL SYSTEM 14
8.0 ACCESSORY INSTALLATION 15
9.0 BURNER INSTALLATION & SETTING 16
10.0 TECHNICAL INFORMATION 20
11.0 BOILER START UP & OPERATION 21
11.1 START-UP PROCEDURE 21
11.2 L7248 HONEYWELL AQUASTAT 22
11.3 FUEL SMART HYDROSTAT 3250 BOILER CONTROL 23
12.0 MAINTENANCE AND SERVICE 26
12.1 CLEANING THE BOILER 27
12.2 BURNER NOTES 27
12.3 PERFORMING COMBUSTION TEST 27
13.0 EXPLODED PARTS VIEW 28
14.0 START UP TEST RESULTS 30
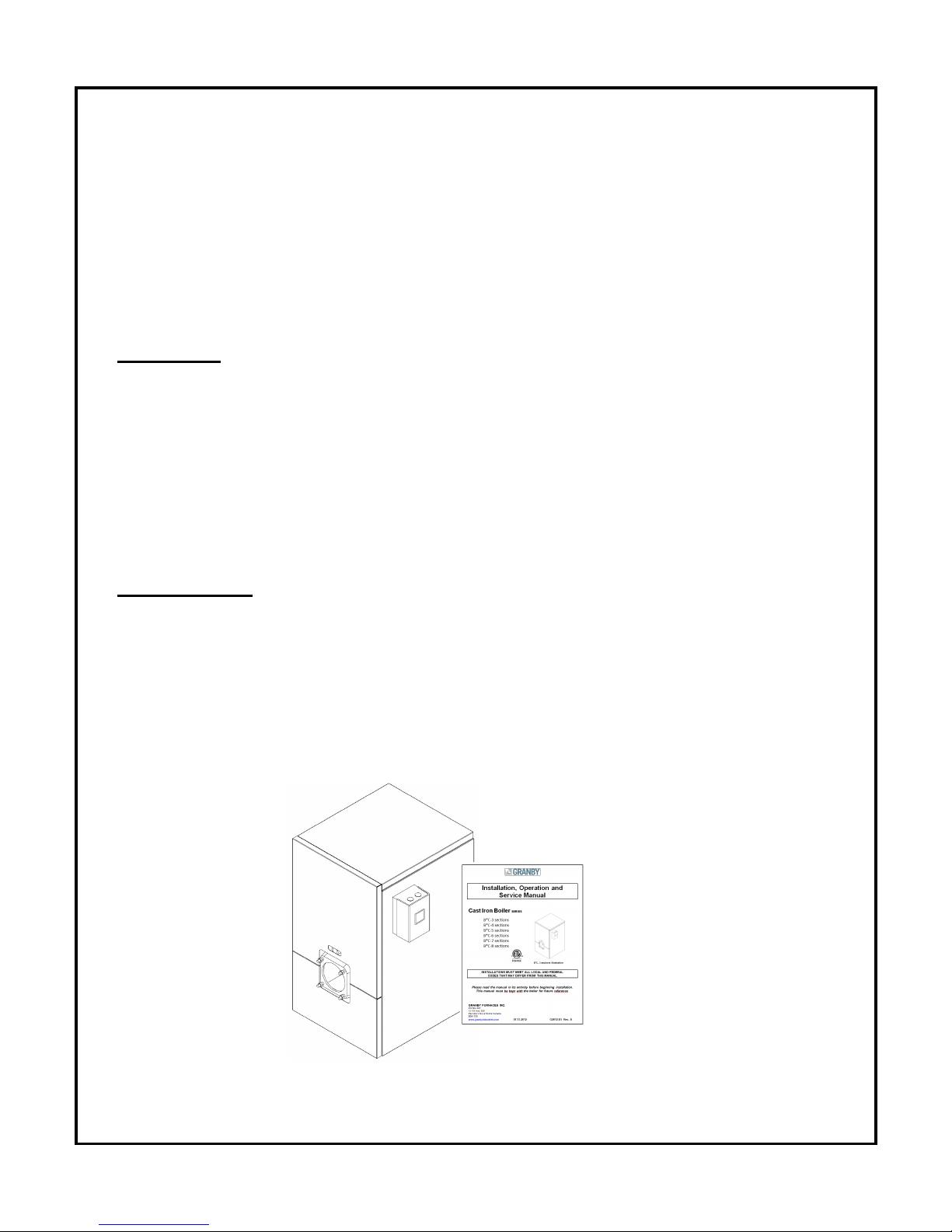
2
1.0 IMPORTANT SAFETY ADVICE
Please read and understand this manual before installing, operating or
servicing the boiler. To ensure you have a clear understanding of the operating
procedures of the appliance please take the time to read section IMPORTANT
SAFETY ADVICE of this manual.
CAUTION
DO NOT START THE BURNER UNTIL ALL FITTINGS, COVERS AND DOORS
ARE IN PLACE. DO NOT TAMPER WITH THE BOILER OR CONTROLS, CALL
A QUALIFIED BURNER TECHNICIAN. DO NOT STORE OR USE GASOLINE
OR OTHER FLAMMABLE VAPOURS AND LIQUIDS IN THE VICINITY OF THIS
UNIT OR ANY OTHER APPLIANCE.
IMPORTANT
This manual contains instructional and operational information for the B*C OILFIRED Boiler. Read the instructions thoroughly before installing boiler or starting
the burner. Consult local authorities about your local FIRE SAFETY
REGULATIONS. All installations must be in accordance with local state or
provincial codes. Improper installation will result in voiding of warranty.
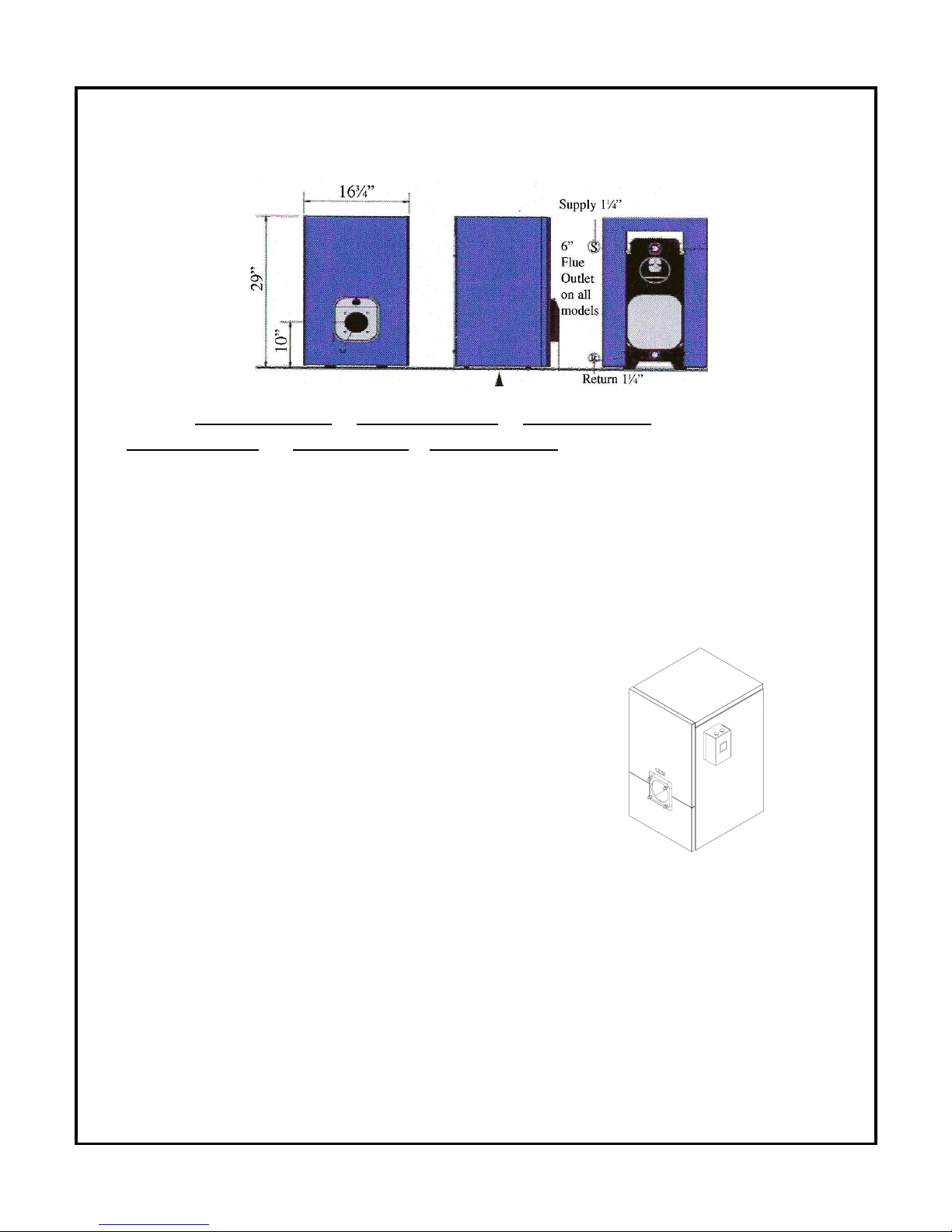
3
2.0 PRODUCT INFORMATION
PHYSICAL DIMENSIONS
Length
: ( 3 sections 18 7/8 ‘’ ) ( 4 sections 22 1/2’’ ) ( 5 sections 26 ¼’’ )
( 6 sections 31 1/8’’ ) ( 7 sections 35 ½’’) ( 8 sections 39 ¼’’)
CLEARANCE
Proper clearances must be maintained not only from combustible materials but also to provide
adequate access for servicing. All installations must comply with local codes and CSA B139.
Consult local fire codes for required clearances. Connections to chimney must be made with
the proper gauge thickness and diameter of fluepipe as required by CSA B139.
CLEARANCE (minimum) FOR SERVICING
Front 24” (609 mm)
Rear 24” (609 mm)
Left Side 24” (609 mm)
Right Side 2” (50.8 mm)
Top 10” (254 mm)
CLEARANCE (minimum) TO COMBUSTIBLES
Top 10” (254 mm)
Front 24” (609 mm)
Rear 24” (609 mm)
Left Side 24” (609 mm)
Right Side 2” (50.8 mm)
Chimney Connector 9” (229 mm)
DRAFT PRESSURE
Breech draft pressure 0.03’’ w.c. draft required
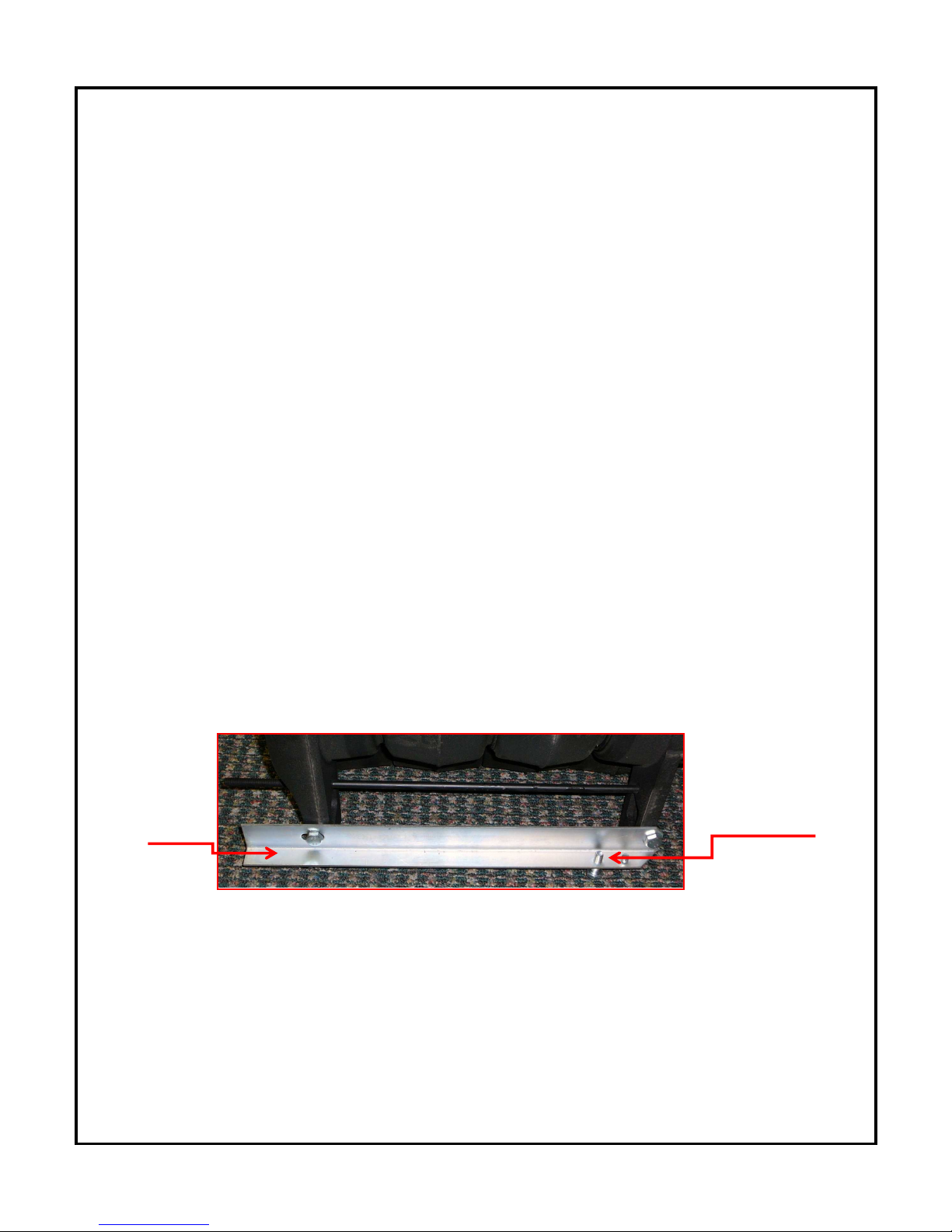
4
FLUE PIPE CONNECTION
CHIMNEY or Direct Vent System DVS Granby kit (3, 4, 5 sections)
CLEANOUTS
Rear removable smoke hood cover & Combustion Front Door Opening
FUEL
Not heavier than No.2 fuel oil
ELECTRICAL
CANADA:120 Volts, 60Hz, 15 amps. fuse or breaker
USA: 13.3A, circuit protection 20A,
AIR SUPPLY
CAUTION: Adequate air supply for both combustion and ventilation must be available.
See page 14 for details.
3.0 Unit installation
3.1 PLACEMENT & LEVELING OF THE UNIT
The boiler should be located on firm foundation in an easily accessible area that meets the
previously discussed clearances and air requirements. In situations where the floor may be
uneven the G*C may be level by using the leg levelers provided on the boiler or through the
insertion of shims under the legs.
3.2 JACKET ASSEMBLY AND CONTROL INSTALLATION
The boiler jacket has been designed for ease of assembly and removal. The following step by
step process will ease installation. A screw driver, 17mm socket and ratchet or a 17mm
wrench or adjustable wrench are needed.

5
STEP 1: VERIFY CONTENTS OF JACKET ASSEMBLY PACKAGE.
Your jacket assembly will contain two (2) manifolds with gaskets, a
fastening package which includes all necessary bolts, screws, nuts
and washers for assembly along with burner studs, nuts and
washers, block insulation, rear of block insulation, aluminum faced
tape, leveling frame rails, two (2) side panels, a rear panel top
panel and re-insulated top and bottom front panels.
STEP 2: FRAME RAIL CONNECTION
Attach 10 mm bolts to the underside of the frame rails. These will be used to level the boiler. Screw
the 4 mm jacket affixing screw to the frame rail from the top down. Both the bolt and affixing screw will
be located on the same end of the frame rail. The frame rail will then be bolted to the legs of the boiler
with the frame rail and containing the affixing screw facing in the direction of the front end of the boiler.
STEP 3: MANIFOLD INSTALLATION
Using the gaskets and bolts supplied connect the manifolds directly to the boiler block. The
top supply manifold will have a 3/4” npt tapping for a relief valve and 1/4” npt tapping for a
gauge. The bottom return manifold has 3/4” npt tapping for a drain vlave. Both manifolds have
1-1/4” male npt threads for sytem connection.
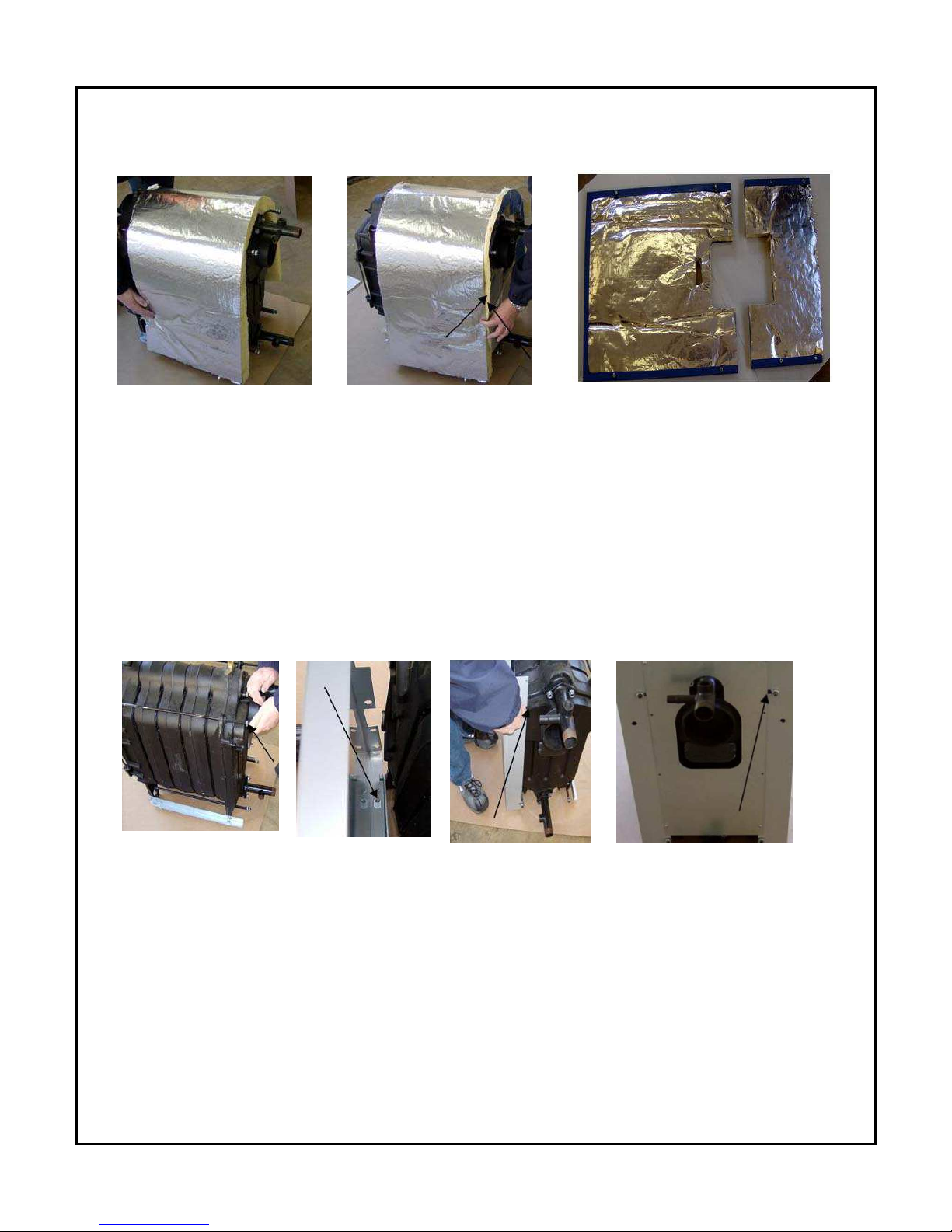
6
STEP 4: INSULATION INSTALLATION
Drape the large piece of block insulation directly over the block taking care to provide adequate
clearance from frame rails. Using the aluminum faced tape attach the preshaped rear
inslulation to the block insulation. The process is simply taping the two pieces together. The
front panels come pre-insulated.
STEP 5: SIDE AND BACK PANEL ATTACHMENT
Affix panel mounting nuts to the rear of the tie rods. Mount the side panels by placing the
panel over the frame rail so that the hole in the bottom lip of the panel fits directly over the
jacket affixing screw on the rail. You can then lock the panel in place by sliding it slightly
forward. The slot on the rear of the panel will now be in position to slide over the tie rod at the
rear of the boiler. Tighten the nuts on the tie rod end to firmly secure the panel. Repeat on the
other side. Screw the back panel to the side panels.
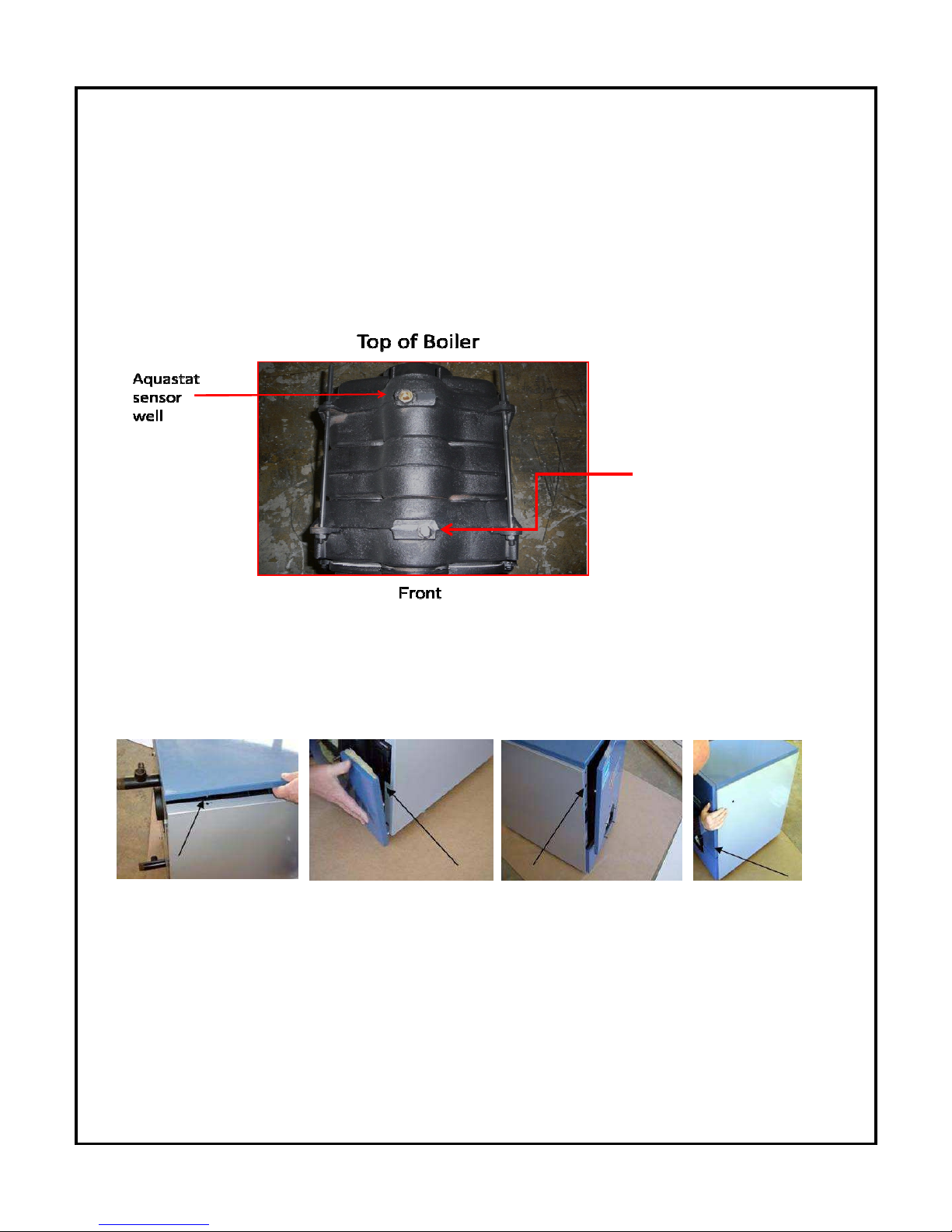
7
STEP 6: CONTROL SENSOR ATTACHMENT
Prior to jacket top and front panel installation the control sensor must be inserted into the brass
well located on the top of the boiler and secured by a clip. Feed the sensor through the hole
on the front of the right side panel from the outside. Penetrate the block insulation to insert the
sensor. The sensor must be fully inserted to the bottom of the well.
STEP 7: TOP AND FRONT PANEL ATTACHMENT
Affix the top panel by placing the holes located on the underside of the panel over the jacket
affixing pins. Press down on the top panel and it will snap in place. Affix the lower front panel
by placing the openings on the lips of the panel over the jacket affixing screws and pushing
downward on the panel. The panel will lock in place. Repeat the process for the top front
panel.
Manual
Air Vent
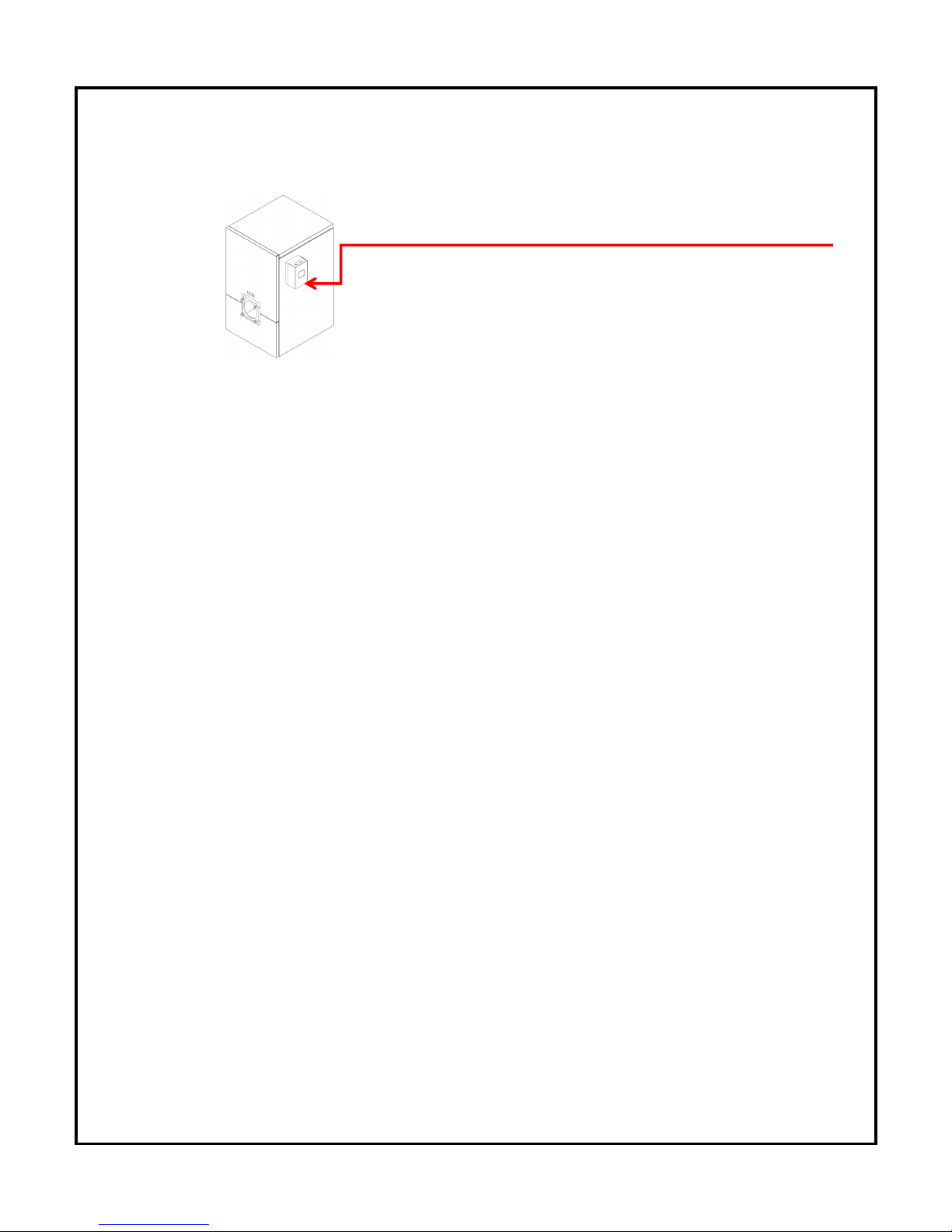
8
Upon completion of the jacket assembly the control unit can be mounted on the side of
the boiler.
Honeywell L7248 Aquastat or Fuel Smart HydroStat 3250 boiler control.
B*C-3 sections boiler illustrated
The boiler is now ready for piping and connection to the fuel system, heating and
domestic hot water, thermostat and 110 Volt 60 cycle AC current.
CAUTION: Safety or relief valve discharge should be piped downward to within
6” of the floor or to a drain. The valve must be mounted in a vertical position.
4.0 PIPING
Prior to connecting the B*C to an existing piping system certain procedures must be followed.
The system should be flushed to insure that scale and sludge will not be introduced to the
boiler. This is a must when replacing a gravity open system.
The B*C is a low mass boiler requiring low water content and steps must be taken to insure
that the boiler is not flooded from an existing high volume standing cast iron system. If the
conversion is from a high volume system a bypass loop must be installed.
Manual shut off valves must be installed on both the supply line and on the boiler bypass
loop. ASME Boiler Code requires that feed or make up water be introduced to the piping
system and not directly to the boiler. Pressure reducing valves should be installed and
adjusted to 12 psi cold water. The pressure relief valve must be piped from the boiler and
downward to within 6” of the floor or to a height to meet existing code. An expansion tank,
circulating pump and automatic air eliminators must be part of the system. The relief valve,
backflow preventer and drain valve should be piped according to code to a drain with piping
that is the same size as the relief valve.
All piping, including heating, domestic hot water and fuel lines must be done in accordance
with all local codes. It is suggested that you refer to the Water Installation Survey and
Hydronic Institute Residential Hydronic Heating Installation/Design Guide. All piping must be
properly sized, free from defect and be made of copper, steel, brass, aluminum or PEX.
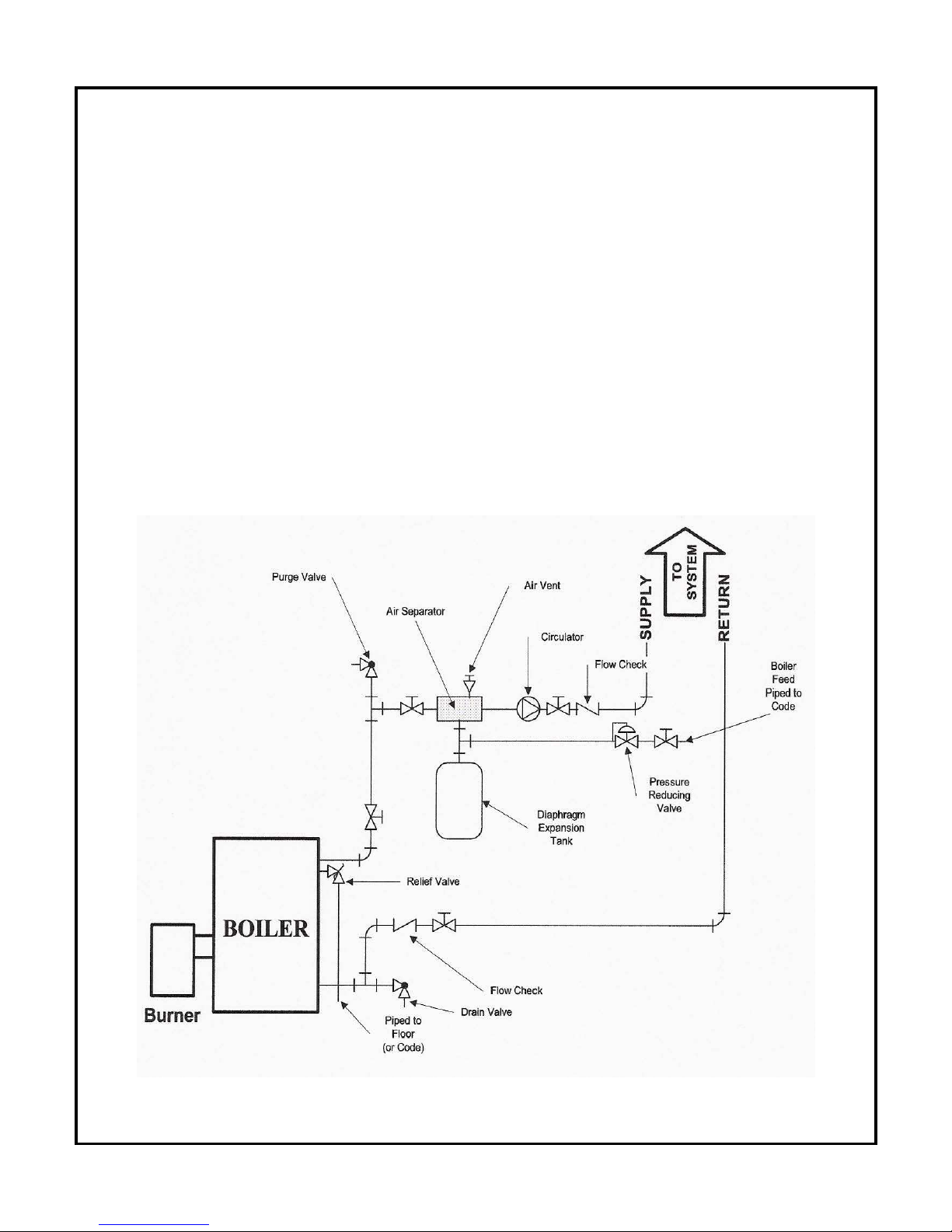
9
Circulation Pump
A calculation for proper pump selection must be performed for all installations. The pump(s)
should not be operated at maximum working pressures above 30 psi or maximum working
temperatures above 200°F and within limits advised by the manufacturer. The pump must not
be operated unless the system has been bled of all air and completely filled with water.
Recommended locations for the circulator, expansion tank, relief valve and other trim
are shown in Figure 1, Figure 2, Figure 3 and Figure 4.
Figure 1
A typical installation with no domestic hot water and no by-pass loop
installed.