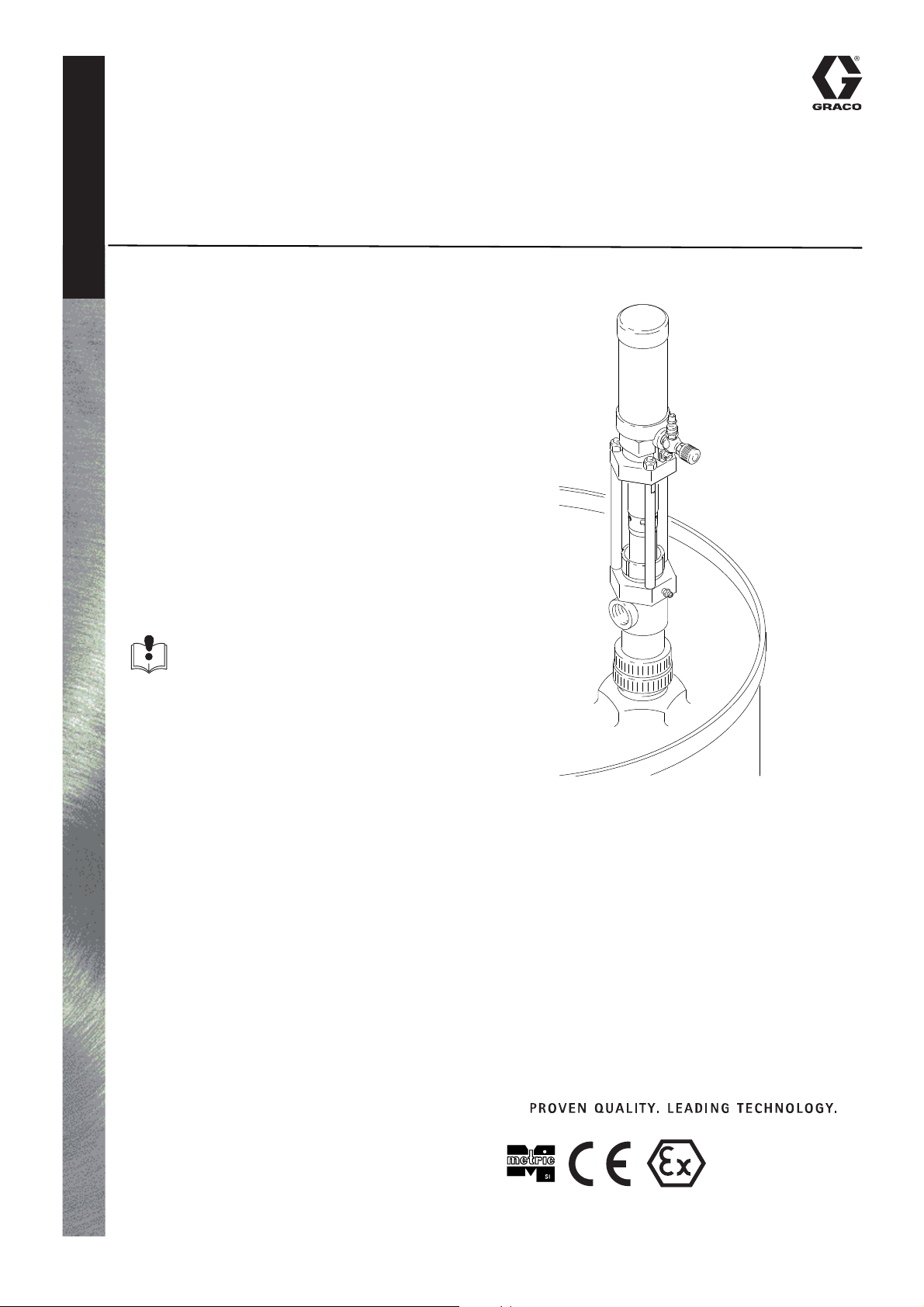
Instructions — Parts List
II 1/2 G T6
ITSO3ATEX11227
1:1 RATIO, 210 LITER (55 GAL.) SIZE
Foam-Cat
For use in drums of polyurethane chemicals.
180 psi (1.2 MPa, 12.4 bar) Maximum Air Working Pressure
180 psi (1.2 MPa, 12.4 bar) Maximum Material Working Pressure
* Mod
el No. 226946, Series B
Includes airtight bung adapter
Feed Pump Kit 217381
Includes two Model 226946 Feed Pumps, air dryer,
and air and fluid hoses.
Read warnings and instructions. See
page 2 for Table of Contents.
Feed Pump
®
307552K
EN
GRACO INC. P.O. BOX 1441 MINNEAPOLIS, MN 55440-1441
© Graco Inc., 1982. Graco Inc. is registered to I.S. EN ISO 9001
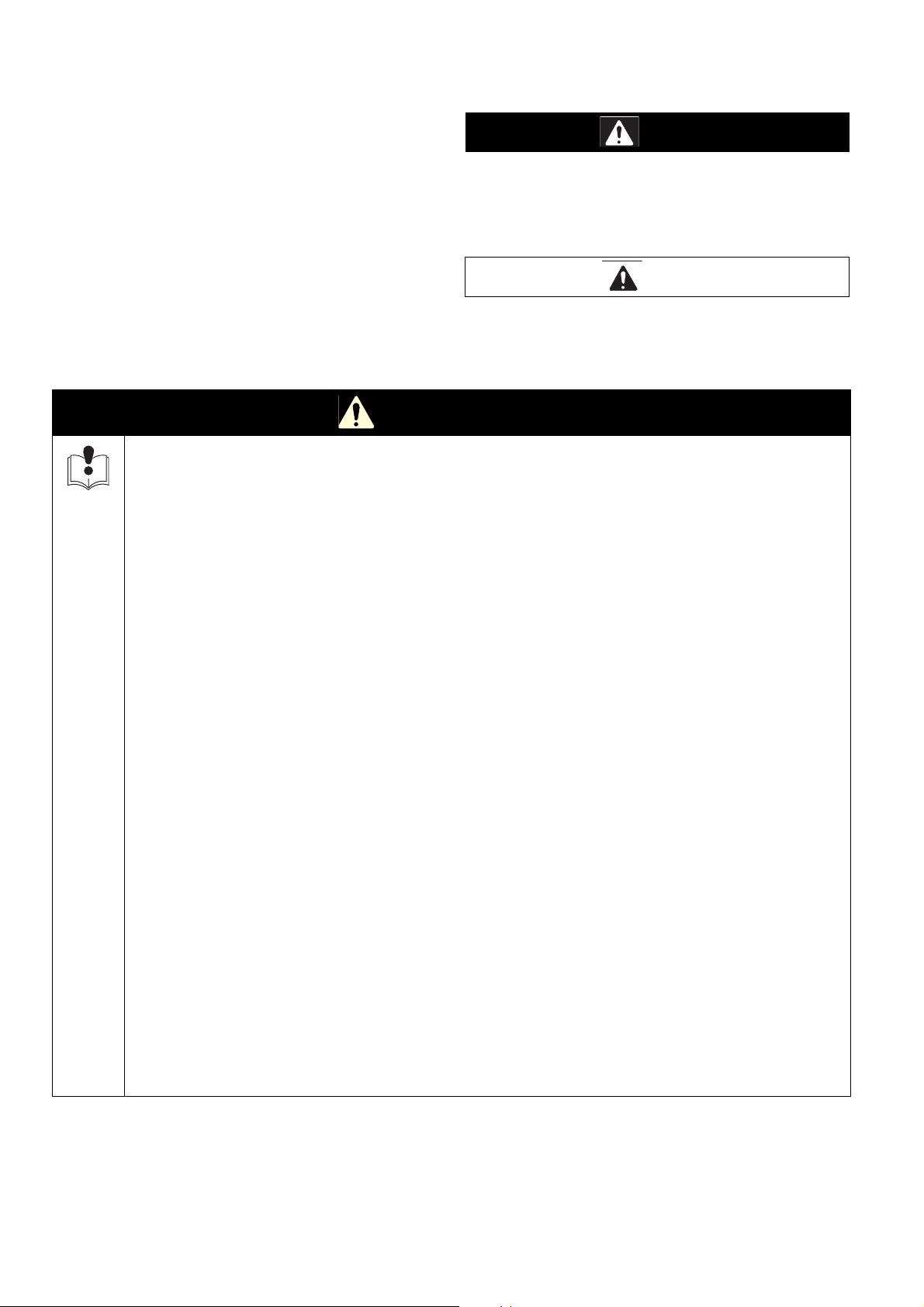
Table of Contents
Symbols . . . . . . . . . . . . . . . . . . . . . . . . . . . . . . . . . . . . 2
Installation . . . . . . . . . . . . . . . . . . . . . . . . . . . . . . . . . . 4
Operation . . . . . . . . . . . . . . . . . . . . . . . . . . . . . . . . . . . 7
Maintenance . . . . . . . . . . . . . . . . . . . . . . . . . . . . . . . . 8
Troubleshooting . . . . . . . . . . . . . . . . . . . . . . . . . . . . . 9
Service . . . . . . . . . . . . . . . . . . . . . . . . . . . . . . . . . . . . 10
Parts Drawing . . . . . . . . . . . . . . . . . . . . . . . . . . . . . . 12
Parts List . . . . . . . . . . . . . . . . . . . . . . . . . . . . . . . . . . 13
Technical Data . . . . . . . . . . . . . . . . . . . . . . . . . . . . . . 15
Graco Standard Warranty . . . . . . . . . . . . . . . . . . . . . . . 16
WARNING
Equipment misuse can cause the equipment to rupture or malfunction and result in serious injury.
This equipment is for professional use only.
•
Symbols
Warning Symbol
WARNING
This symbol alerts you to the possibility of serious
injury or death if you do not follow the instructions.
Caution Symbol
CAUTION
This symbol alerts you to the possibility of damage to
or destruction of equipment if you do not follow the
instructions.
• Read all instruction manuals, tags, and labels before operating the equipment.
• Use the equipment only for its intended purpose. If you are not sure, call your Graco distributor.
• Do not alter or modify this equipment.
• Check equipment daily. Repair or replace worn or damaged parts immediately.
• Do not exceed the maximum working pressure of the lowest rated component in your system. This equipment
has a 180 psi (1.2 MPa, 12.4 bar) maximum working pressure at 180 psi (1.2 MPa, 12.4 bar) maximum
incoming air pressure.
• Use fluids and solvents which are compatible with the equipment wetted parts. Refer to the Technical Data
section of all equipment manuals. Read the fluid and solvent manufacturer’s warnings.
• Do not use hoses to pull equipment.
• Route hoses away from traffic areas, sharp edges, moving parts, and hot surfaces. Do not expose Graco hoses
to temperatures above 82°C (180°F) or below –40°C (–40°F).
• Securely mount the pump. Do not attempt to operate it while holding it.
• Do not lift pressurized equipment.
• Comply with all applicable local, state, and national fire, electrical, and safety regulations.
2 307552
• Graco Inc. does not manufacture or supply any of the reactive chemical materials that may be used in this
equipment and is not responsible for their effects. Because of the vast number of chemicals that could be used
and their varying chemical reactions, before using this equipment, the buyer and the user should determine all
facts relating to the materials used, including any of the potential hazards involved. Particular inquiry and
investigation should be made into potential dangers relating to toxic fumes, fires, explosions, reaction times, and
exposure of human beings to the individual components or their resultant mixtures. Graco assumes no
responsibility for loss, damage, expense or claims for bodily injury or property damage, direct or consequential,
arising from the use of such chemical components.
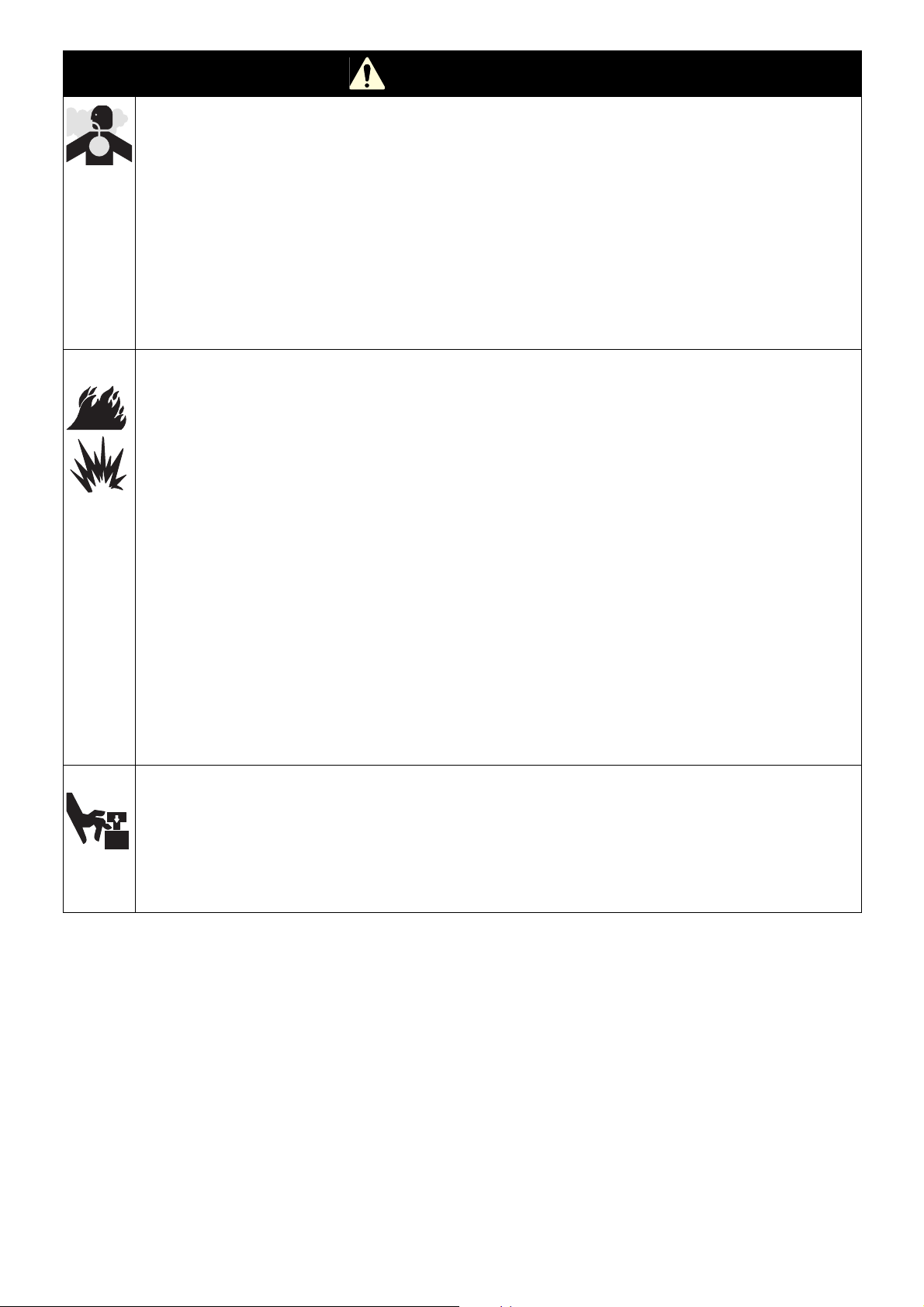
WARNING
TOXIC FLUID HAZARD
Hazardous fluid or toxic fumes can cause serious injury or death if splashed in the eyes or on the skin,
inhaled, or swallowed.
•
Know the specific hazards of the fluid you are using.
• Store hazardous fluid in an approved container. Dispose of hazardous fluid according to all local, state and
national guidelines.
• Any additives to the air supply, such as oil or anti–freeze will be exhausted into the atmosphere.
• Always wear protective eyewear, gloves, clothing and respirator as recommended by the fluid and solvent
manufacturer.
FIRE AND EXPLOSION HAZARD
Improper grounding, poor ventilation, open flames or sparks can cause a hazardous condition and result
in a fire or explosion and serious injury.
•
Ground the equipment. Refer to Grounding on page 5.
• If there is any static sparking or you feel an electric shock while using this equipment, stop pumping
immediately. Do not use the equipment until you identify and correct the problem.
• Provide fresh air ventilation to avoid the buildup of flammable fumes from solvents or the fluid being sprayed.
• Keep the work area free of debris, including solvent, rags, and gasoline.
• Electrically disconnect all equipment in the work area.
• Extinguish all open flames or pilot lights in the work area.
• Do not smoke in the work area.
• Do not turn on or off any light switch in the work area while operating or if fumes are present.
• Do not operate a gasoline engine in the work area.
MOVING PARTS HAZARD
Moving parts can pinch or amputate your fingers.
•
Keep clear of all moving parts when starting or operating the pump.
• Before servicing the equipment, follow the Pressure Relief Procedure on page 7 to prevent the equipment
from starting accidentally.
307552 3
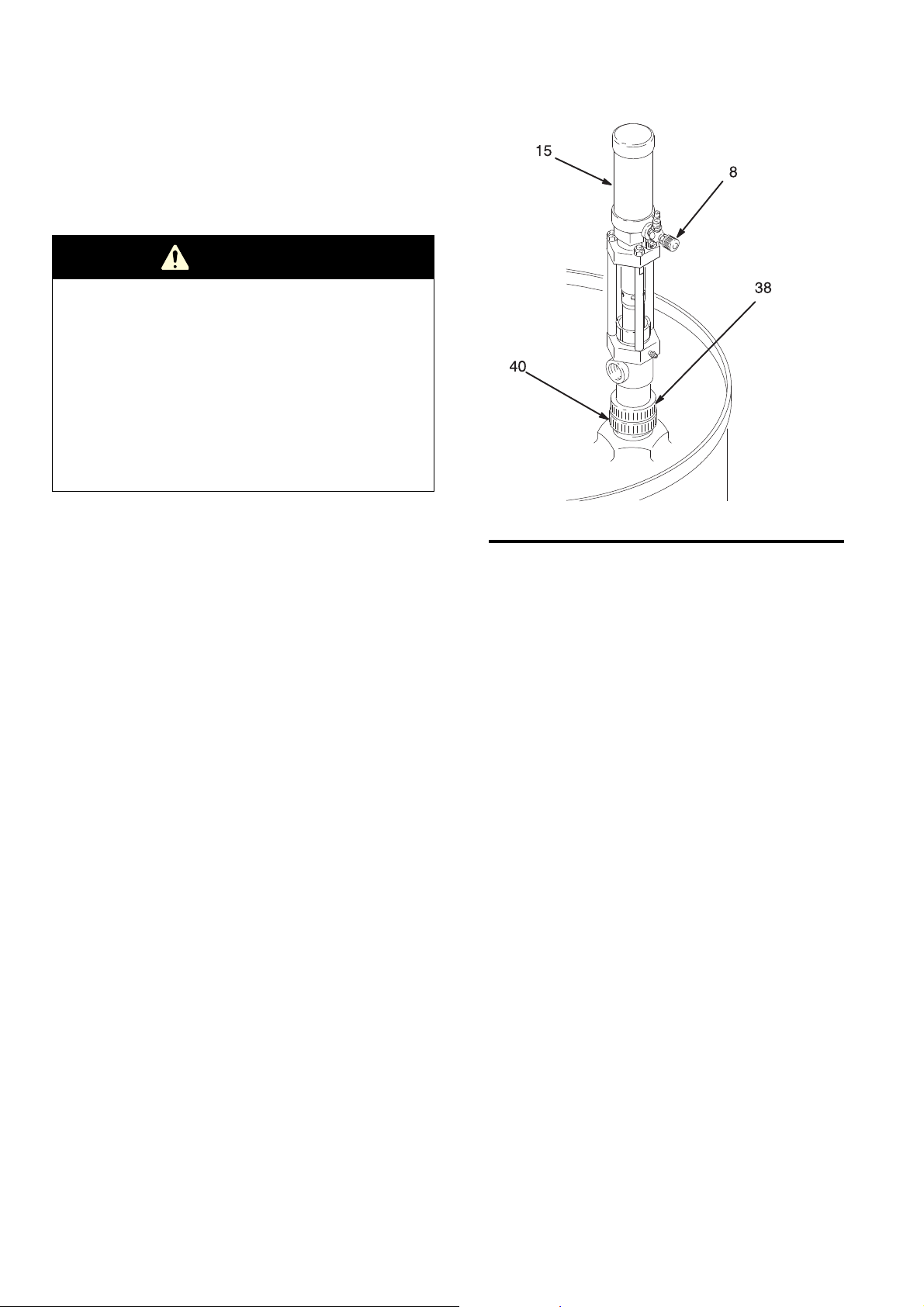
Installation
NOTE: The terms ISO and RES used in the text refer to
the polyurethane foam chemicals, Isocyanate and Resin.
NOTE: Reference numbers and letters in parentheses in
the text refer to the figure illustrations and the Parts
Drawing.
WARNING
A bleed–type master air valve (E) is required in your
system, to help reduce the risk of serious injury,
including splashing fluid in the eyes or on the skin, and
injury from moving parts if you are adjusting or repairing
the pump.
The bleed–type master air valve (E) relieves air trapped
between this valve and the pump after the pump is shut
off. Trapped air can cause the pump to cycle
unexpectedly and result in serious injury, including
amputation. Locate the valve close to the pump.
Installing the Feed Pumps
1. Screw the bung adapter (40) and pump tightly into the
drum cover. See Fig 1.
2. Tighten the retainer (38) firmly to complete the airtight
seal.
3. Separate the two halves of the identification label (15)
along the perforation. Clean the surface of the air
motor with solvent and apply the appropriate label
(RES or ISO) to identify the type of material being
pumped.
4. Install an air regulator in the feed pump air inlet to
control pump speed. To install, remove the air valve
(8) and use suitable adapters for the regulator and
pin fitting. Use thread sealer on male threads.
4 307552

Installation
5. Connect an air supply hose to the 1/4 npt air line
coupler (13). Air supply hoses (103) are supplied in
Kit 217381. See Fig 3, page 6.
6. Connect a fluid supply hose from the 3/4 npt(f) fluid
outlet of the ISO feed pump to the inlet fitting of the
ISO proportioning pump, using adapters as needed.
Then connect a fluid supply hose between the RES
feed pump and RES proportioning pump.
CAUTION
Be sure all hose connections in your polyurethane
foam spray system are clearly labeled ISO or RES
and make connections only with identically labeled
components to avoid material crossing.
Crossing polyurethane materials will cause the
material to harden in the equipment and may
permanently damage it.
Grounding
Remove the ground screw (Z) and insert through eye of
ring terminal at the end of ground wire (Y). Fasten ground
screw back onto pump and tighten securely. See Fig 2.
Connect the other end of the wire to a true earth ground.
Order Part No. 222011 Ground Wire and Clamp.
Feed Pump Kit Installation
The following instructions assume you are using this kit
with a Graco Foam–Cat Sprayer.
WARNING
Static electricity is created by the high velocity flow of
fluid through the pump and hoses. If every part of the
spray system, and all objects in the spray area are not
properly grounded, the static electricity may cause
sparking. Sparks can ignite fumes from solvents and the
fluid being sprayed, dust particles, and other flammable
substances, causing a fire, explosion and serious bodily
injury and property damage.
To reduce the risk of static sparking, use only conductive
air and fluid hoses and be sure your entire system is
properly grounded. Ground the feed pumps as
explained below.
1. Install the feed pumps as described in Steps 1–4, on
page 4.
2. Mount the Air Dryer (105) in any suitable location.
Refer to manual 307548 for the mounting hole
diagram. See Fig 3.
3. Unscrew the air dryer ring (F) to remove the bowl.
See Fig 3. Remove the filter and fill the bowl with the
desiccant, provided. Reassemble.
CAUTION
One end of each fluid hose and each drum nipple (G)
of the drum fittings (H) is labeled ISO or RES. Make
only ISO to ISO and RES to RES connections to avoid
material crossing.
4. Install the drum fittings (H) in the 3/4 in. vent port of
the proper drum.
307552 5