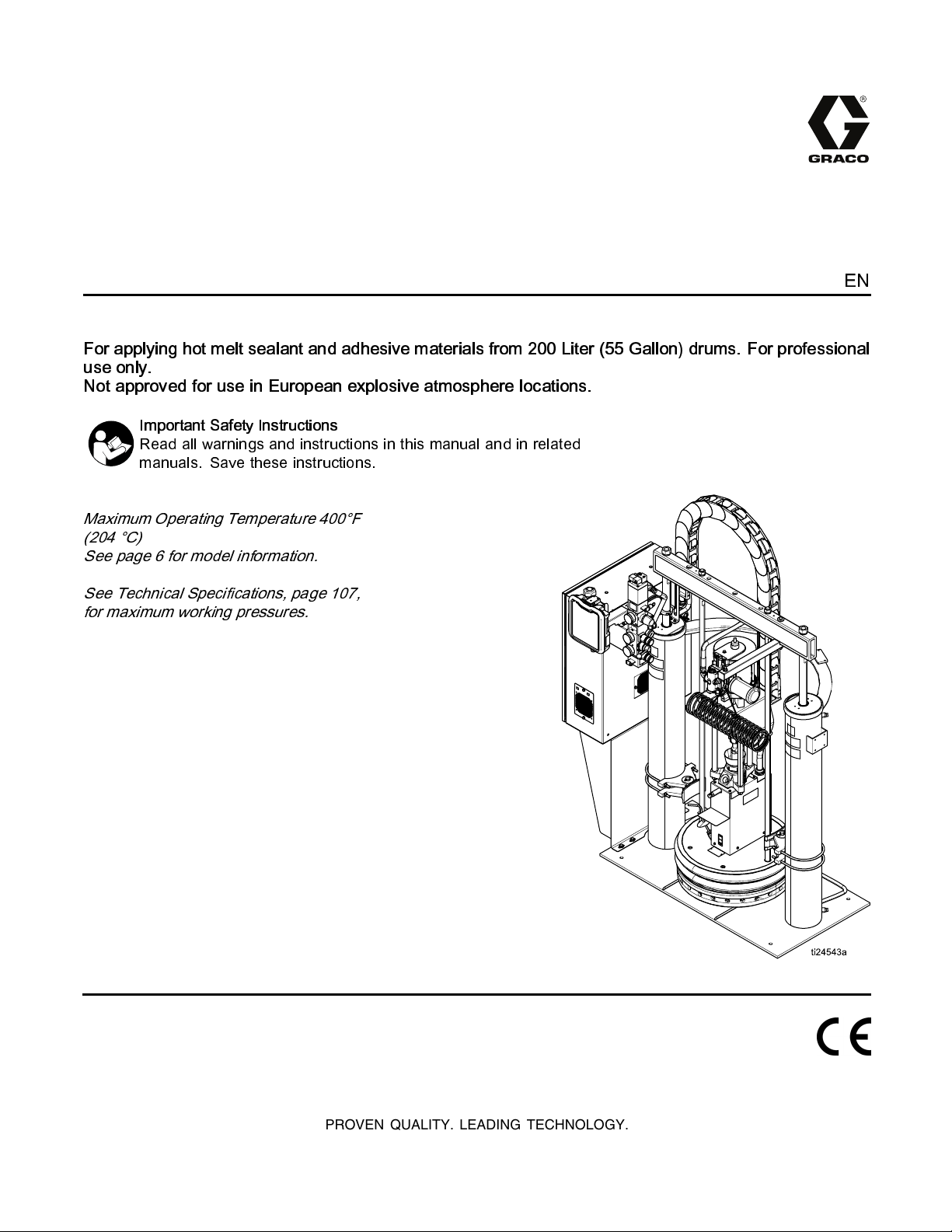
Instructions-Parts
334130B
Therm-O-Flow® 200
For applying hot melt sealant and adhesive materials from 200 Liter (55 Gallon) drums. For professional
use only.
Not approved for use in European explosive atmosphere locations.
Important Safety Instructions
Read all warnings and instructions in this manual and in related
manuals. Save these instructions.
Maximum Operating Temperature 400°F
(204 °C)
See page 6 for model information.
EN
See Technical Specifications, page 107,
for maximum working pressures.
PROVEN QUALITY. LEADING TECHNOLOGY.
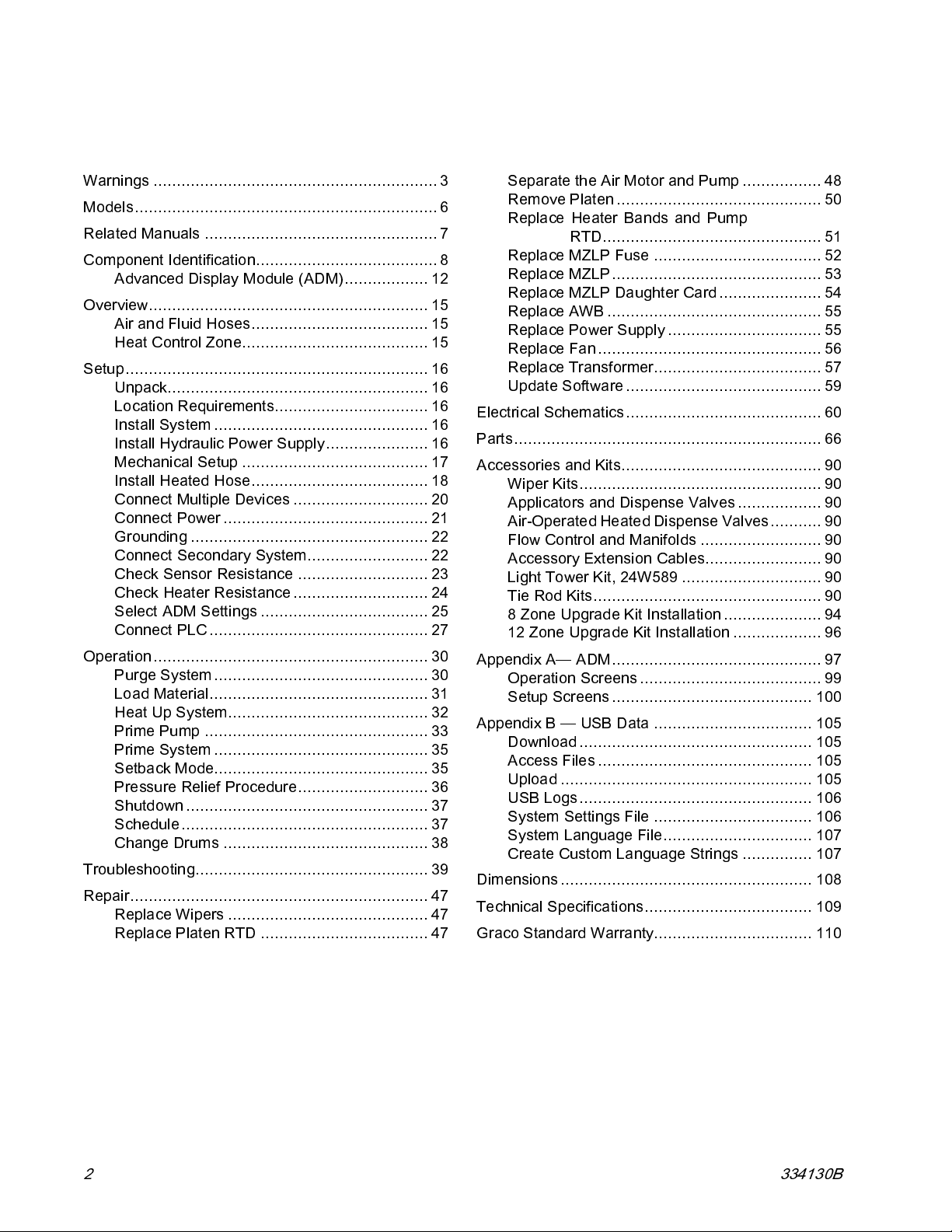
Contents
Warnings .............................................................3
Models................................................................. 6
Related Manuals .................................................. 7
Component Identification.......................................8
Advanced Display Module (ADM).................. 12
Overview............................................................15
Air and Fluid Hoses...................................... 15
Heat Control Zone........................................ 15
Setup ................................................................. 16
Unpack........................................................16
Location Requirements................................. 16
Install System .............................................. 16
Install Hydraulic Power Supply...................... 16
Mechanical Setup ........................................ 17
Install Heated Hose...................................... 18
Connect Multiple Devices ............................. 20
Connect Power ............................................ 21
Grounding ................................................... 22
Connect Secondary System..........................22
Check Sensor Resistance ............................23
Check Heater Resistance............................. 24
Select ADM Settings .................................... 25
Connect PLC............................................... 27
Operation........................................................... 30
Purge System.............................................. 30
Load Material............................................... 31
Heat Up System...........................................32
Prime Pump ................................................33
Prime System.............................................. 35
Setback Mode..............................................35
Pressure Relief Procedure............................ 36
Shutdown .................................................... 37
Schedule..................................................... 37
Change Drums ............................................ 38
Troubleshooting..................................................39
Repair................................................................ 47
Replace Wipers ........................................... 47
Replace Platen RTD ....................................47
Separate the Air Motor and Pump................. 48
Remove Platen ............................................ 50
Replace Heater Bands and Pump
RTD...............................................51
Replace MZLP Fuse .................................... 52
Replace MZLP............................................. 53
Replace MZLP Daughter Card...................... 54
Replace AWB.............................................. 55
Replace Power Supply................................. 55
Replace Fan ................................................ 56
Replace Transformer....................................57
Update Software.......................................... 59
Electrical Schematics.......................................... 60
Parts.................................................................. 66
Accessories and Kits........................................... 90
Wiper Kits.................................................... 90
Applicators and Dispense Valves.................. 90
Air-OperatedHeatedDispense Valves........... 90
Flow Control and Manifolds .......................... 90
Accessory Extension Cables.........................90
Light Tower Kit, 24W589 .............................. 90
Tie Rod Kits................................................. 90
8 Zone Upgrade Kit Installation..................... 94
12 Zone Upgrade Kit Installation ................... 96
Appendix A— ADM............................................. 97
Operation Screens ....................................... 99
Setup Screens........................................... 100
Appendix B — USB Data .................................. 105
Download.................................................. 105
Access Files.............................................. 105
Upload ...................................................... 105
USB Logs.................................................. 106
System Settings File .................................. 106
System Language File................................ 107
Create Custom Language Strings ............... 107
Dimensions...................................................... 108
Technical Specifications.................................... 109
Graco Standard Warranty.................................. 110
2
334130B
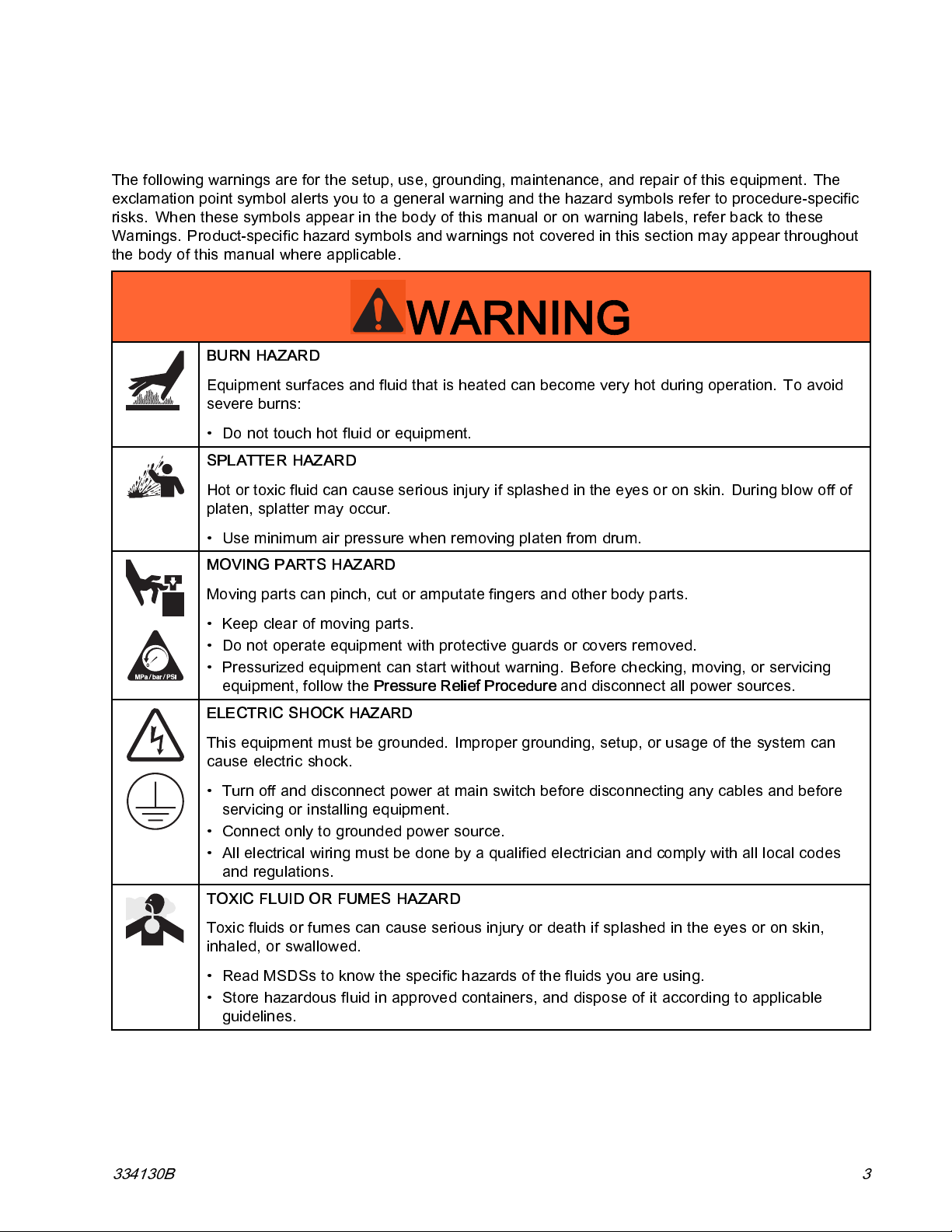
Warnings
Warnings
The following warnings are for the setup, use, grounding, maintenance, and repair of this equipment. The
exclamation point symbol alerts you to a general warning and the hazard symbols refer to procedure-specific
risks. When these symbols appear in the body of this manual or on warning labels, refer back to these
Warnings. Product-specific hazard symbols and warnings not covered in this section may appear throughout
the body of this manual where applicable.
WARNING
BURN HAZARD
Equipment surfaces and fluid that is heated can become very hot during ope ration. To avoid
severe burns:
• Do not touch hot fluid or equipment.
SPLATTER HAZARD
Hot or toxic fluid can cause serious injury if splashed in the eyes or on skin. During blow off of
platen, splatter may occur.
• Use minimum air pressure when removing platen from drum.
MOVING PARTS HAZARD
Moving parts can pinch, cut or amp utate fingers and other body parts.
• Keep clear of moving parts.
• Do not operate equipment with pro tec tiv e guards or covers removed.
• Pressurized equipment can start without warning. Before checking, moving, or servicing
equipment, follow the
ELECTRIC SHOCK HAZARD
This equipment must be grounded. Improper grounding, setup, or usage of the system can
cause electric shock.
• Turn off and disconnect power at main switch before disconnecting any cables and before
servicing or installing equipment.
• Connect only to grounded power source.
• All electrical wiring must be done by a qualified electrician and comply with all local codes
and regulations.
TOXIC FLUID OR FUMES HAZARD
Toxic fluids or fumes can cause serious injury or death if splashed in the eyes or on skin,
inhaled, or swallowed.
• Read MSDSs to know the specific hazards of the fluids you are using.
• Store hazardous fluid in approved containers, and dispose of it according to applicable
guidelines.
Pressure Relief Procedure
and disconnect all power sources.
334130B 3
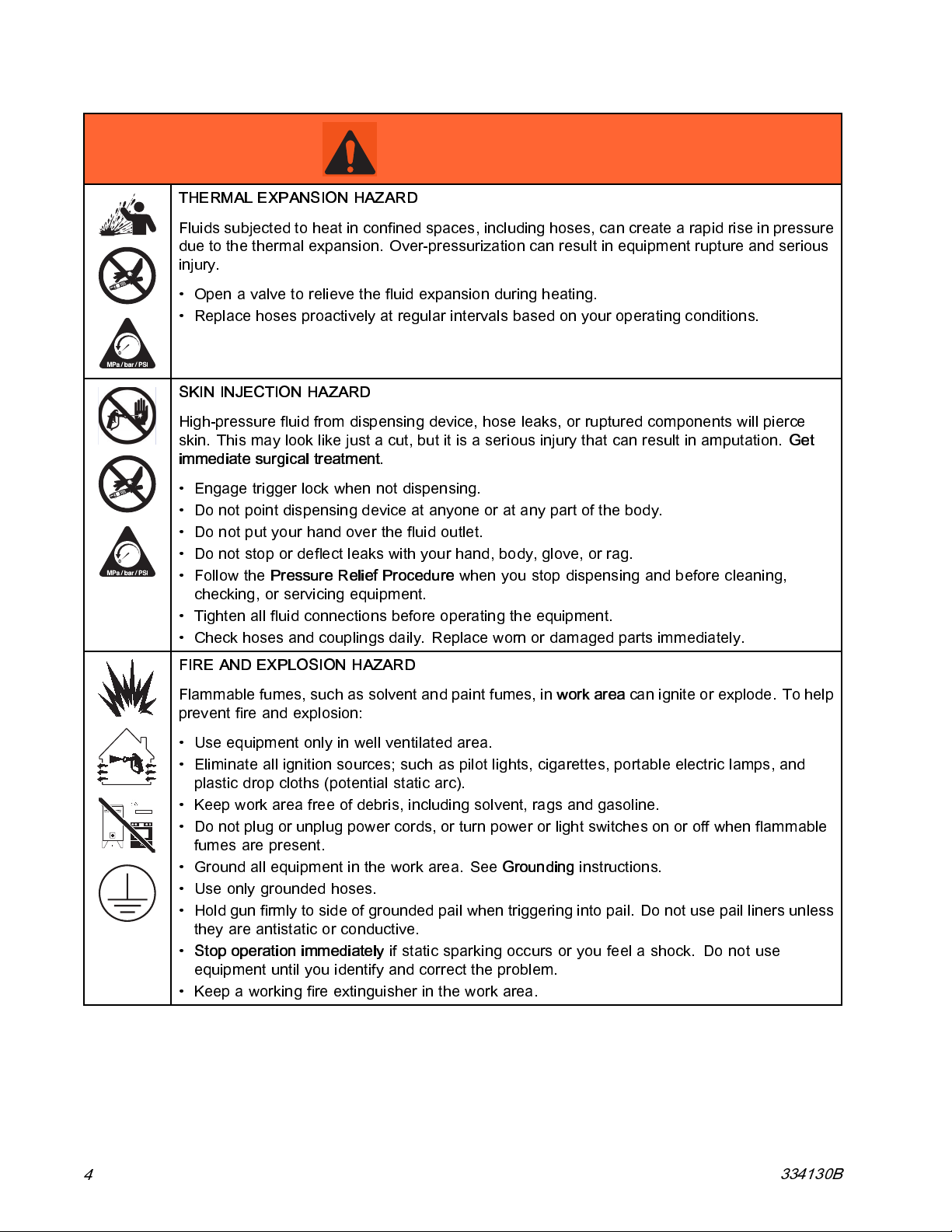
Warnings
WARNING
THERMAL EXPANSION HAZARD
Fluids subjected to heat in confined spaces, including hoses, can create a rapid rise in pressure
due to the thermal expansion. Over-pressurization can result in equipment rupture and serious
injury.
• Open a valve to relieve the fluid expansion during heating.
• Replace hoses proactively at regular intervals based on your operating conditions.
SKIN INJECTION HAZARD
High-pressure fluid from dispensing device, hose leaks, or ruptured components will pierce
skin. This may look like just a cut, but it is a serious injury that can result in amputation.
immediate surgical treatment.
• Engage trigger lock when not dispensing.
• Do not point dispensing device at anyone or at any part of the body.
• Do not put your hand over the fluid outlet.
• Do not stop or defle ct leaks with your hand, body, glove, or rag.
•Followthe
checking, or servicing equipment.
• Tighten all fluid connections before operating the equipment.
• Check hoses and couplings daily. Replace worn or damaged parts immediately.
Pressure Relief Procedure
when you stop dispensing and before cleaning,
Get
FIRE AND EXPLOSION HAZARD
Flammable fumes, such as solvent and paint fumes, in
prevent fire and explosion:
• Use equipment only in well ventilated area.
• Eliminate all ignition sources; such as pilot lights, cigarettes, portable electric lamps, and
plastic drop cloths (potential static arc).
• Keep work area free of debris, including solvent, rags and gasoline.
• Do not plug or unplug power cords, or turn power or light switches on or off when flammable
fumes are present.
• Ground all equipment in the work area. See
• Use only grounded hoses.
• Hold gun firmly to side of grounded pail when triggering into pail. Do not use pail liners unless
they are antistatic or conductive.
•
Stop operation immediately
equipment until you identify and correct the problem.
• Keep a working fire extinguisher in the work area.
if static sparking occurs or you feel a shock.Donotuse
Grounding
work area
instructions.
canigniteorexplode.Tohelp
4
334130B
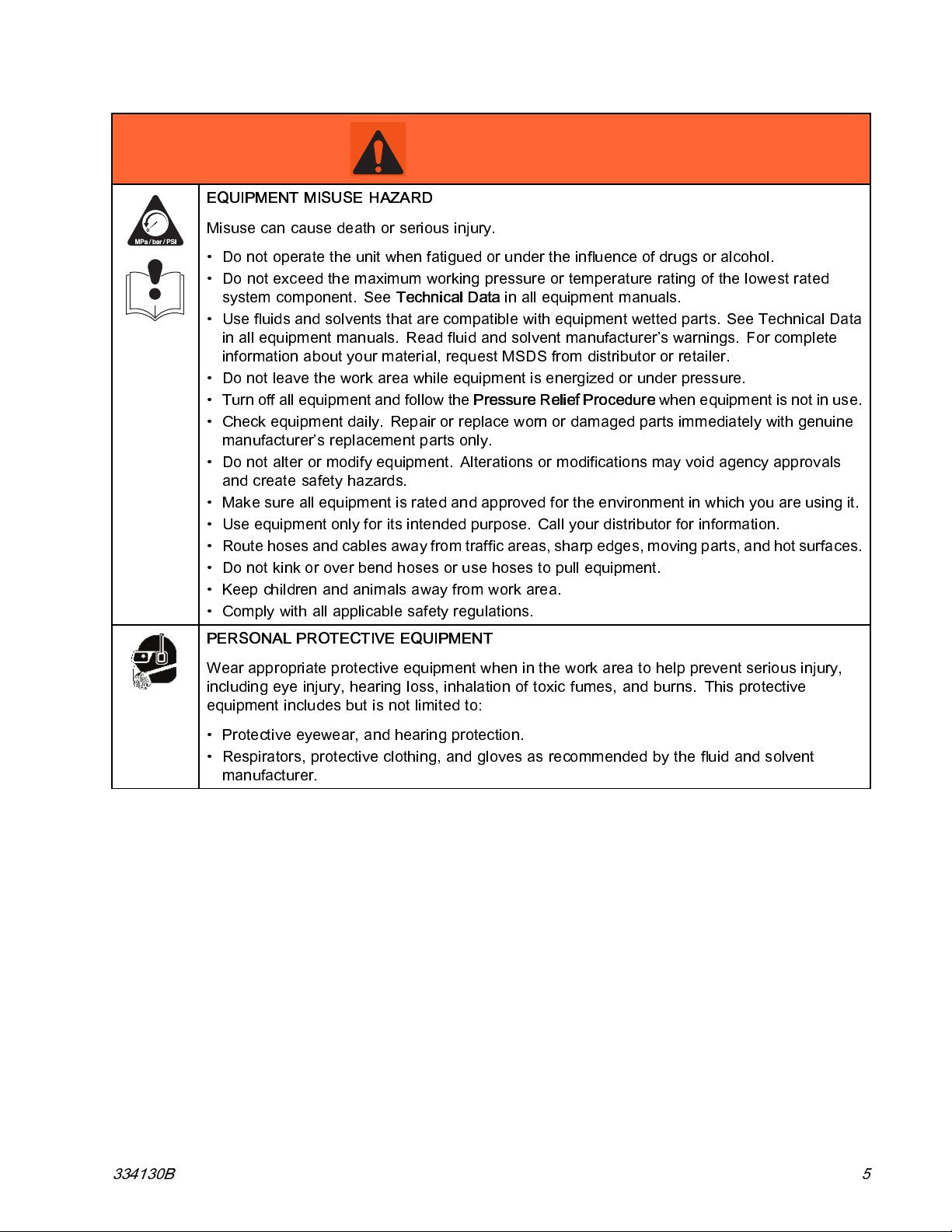
Warnings
WARNING
EQUIPMENT MISUSE HAZARD
Misuse can cause death or serious injury.
• Do not operate the unit when fatigued or under the influence of drugs or alcohol.
• Do not exceed the maximum working pressure or temperature rating of the lowest rated
system component. See
• Use fluids and solvents that are compatible with equipment wetted parts. See Technical Data
in all equipment manuals. Read fluid and solvent manufacturer’s warnings. For complete
information about your material, request MSDS from distributor or retailer.
• Do not leave the work area while equipment is energized or under pressure.
• Turn off all equipment and follow the
• Check equipment daily. Repair or replace worn or damaged parts immediately with genuine
manufacturer’s replacement parts only.
• Do not alter or modif y equipmen t. Al terati on s or modifications may void agency approvals
and create safety hazards.
• Make sure all equipment is rated and approved for the environment in which you are using it.
• Use equipment only for its intended purpose. Call your distributor for information.
• Route hoses and cables away from traffic areas, sharp edges, moving parts, and hot surfaces.
• Do not kink or o ver bend hoses or use hoses to pull equipment.
• Keep children and animals away from work area.
• Comply with all applicable safety regulations.
Technical Data
Pressure Relief Procedure
in all equipment manuals.
when equipment is not in use.
PERSONAL PROTECTIVE EQUIPMENT
Wear appropriate protective equipment when in the work area to help prevent serious injury,
including eye injury, hearing loss, inhalation of toxic fumes, and burns. This protective
equipment includes but is not limited to:
• Protective eyewear, and hearing protection.
• Respirators, protective clothing, and gloves as recommended by the fluid and solvent
manufacturer.
334130B 5
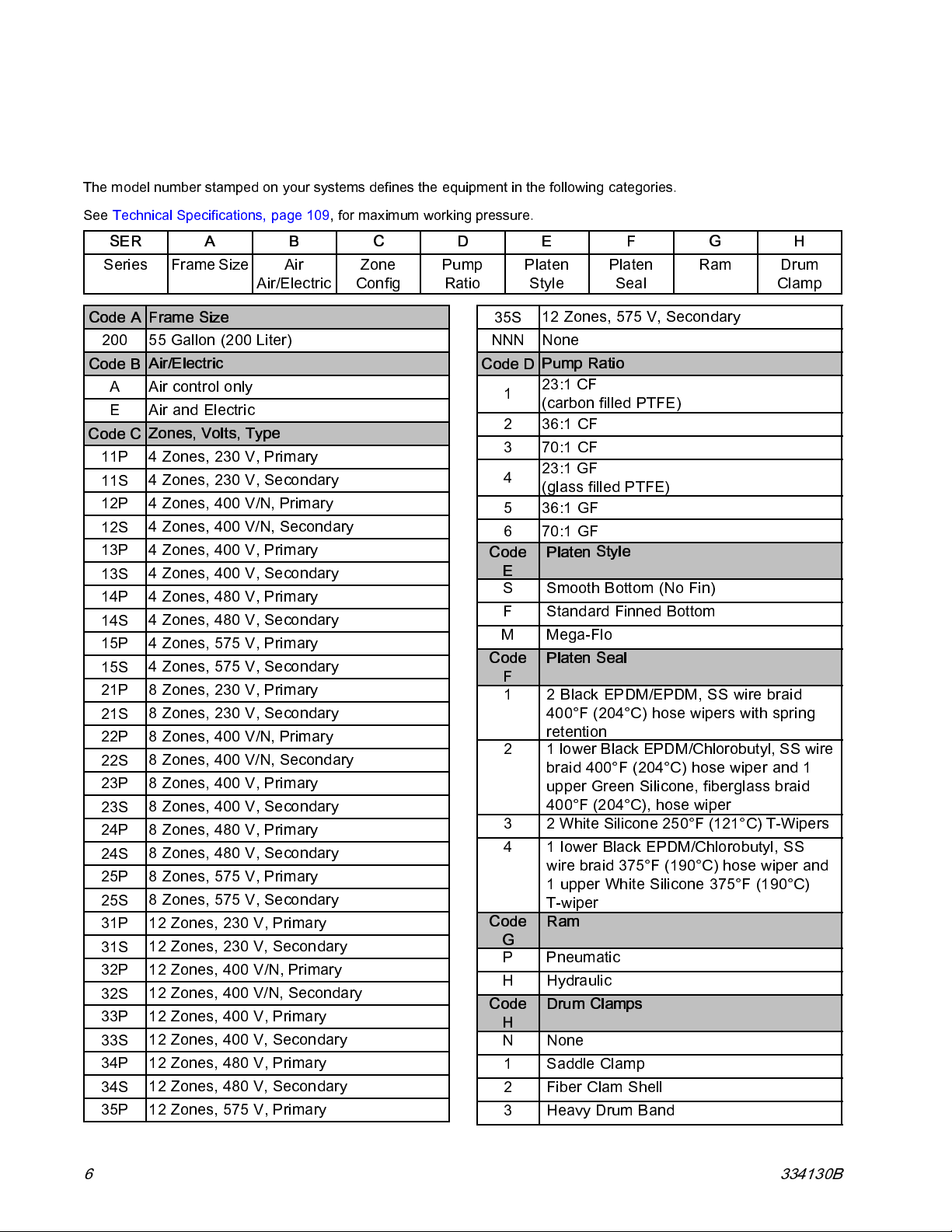
Models
Models
The model number stamped on your systems defines the equipment in the following categories.
See Technical Specifications, page 109, for maximum working pressure.
SER A B C D E F G H
Series FrameSize Air
Air/Electric
Zone
Config
Pump
Ratio
Platen
Style
Platen
Seal
Ram Drum
Clamp
Code A Frame Size
200
Code B
Code C
11P
11S
12P
12S
13P
13S
14P
14S
15P
15S
21P
21S
22P
22S
23P
23S
24P
24S
25P
25S
31P
31S
32P
32S
33P
33S
34P
34S
35P
55 Gallon (200 Liter)
Air/Electric
Air control only
A
E Air and Electric
Zones, Volts, Type
4 Zones, 230 V, Primary
4 Zones, 230 V, Secondary
4 Zones, 400 V/N, Primary
4 Zones, 400 V/N, Secondary
4 Zones, 400 V, Primary
4 Zones, 400 V, Secondary
4 Zones, 480 V, Primary
4 Zones, 480 V, Secondary
4 Zones, 575 V, Primary
4 Zones, 575 V, Secondary
8 Zones, 230 V, Primary
8 Zones, 230 V, Secondary
8 Zones, 400 V/N, Primary
8 Zones, 400 V/N, Secondary
8 Zones, 400 V, Primary
8 Zones, 400 V, Secondary
8 Zones, 480 V, Primary
8 Zones, 480 V, Secondary
8 Zones, 575 V, Primary
8 Zones, 575 V, Secondary
12 Zones, 230 V, Primary
12 Zones, 230 V, Secondary
12 Zones, 400 V/N, Primary
12 Zones, 400 V/N, Secondary
12 Zones, 400 V, Primary
12 Zones, 400 V, Secondary
12 Zones, 480 V, Primary
12 Zones, 480 V, Secondary
12 Zones, 575 V, Primary
35S
NNN None
Code D
CodeEPlaten
CodeFPlaten Seal
Co
CodeHDrum Clamps
12 Zones, 575 V, Secondary
Pump Ratio
23:1 CF
1
(carbon filled PTFE)
2
36:1 CF
3
70:1 CF
23:1 GF
4
(glass filled PTFE)
5
36:1 GF
670:1GF
Style
S Smooth Bottom (No Fin)
F
Standard Finned Bottom
MMega-Flo
1
2 Black EPDM/EPDM, SS wire braid
400°F (204°C) hose wipers with spring
retention
2
1 lower Black EPDM/Chlorobutyl, SS wire
braid 400°F (204°C) hose wiper and 1
upper Green Silicone, fiberglass braid
400°F (204°C), hose wiper
3
2 White Silicone 250°F (121°C) T-Wipers
4
1 lower Blac k EPDM/Chlorobutyl, S S
wire braid 375°F (190°C) hose wiper and
1 upper White Silicone 375°F (190°C)
T-wiper
deGRam
PPneumatic
HHydraulic
NNone
1
Saddle Clamp
2
Fiber Clam Shell
3HeavyDrumBand
6 334130B
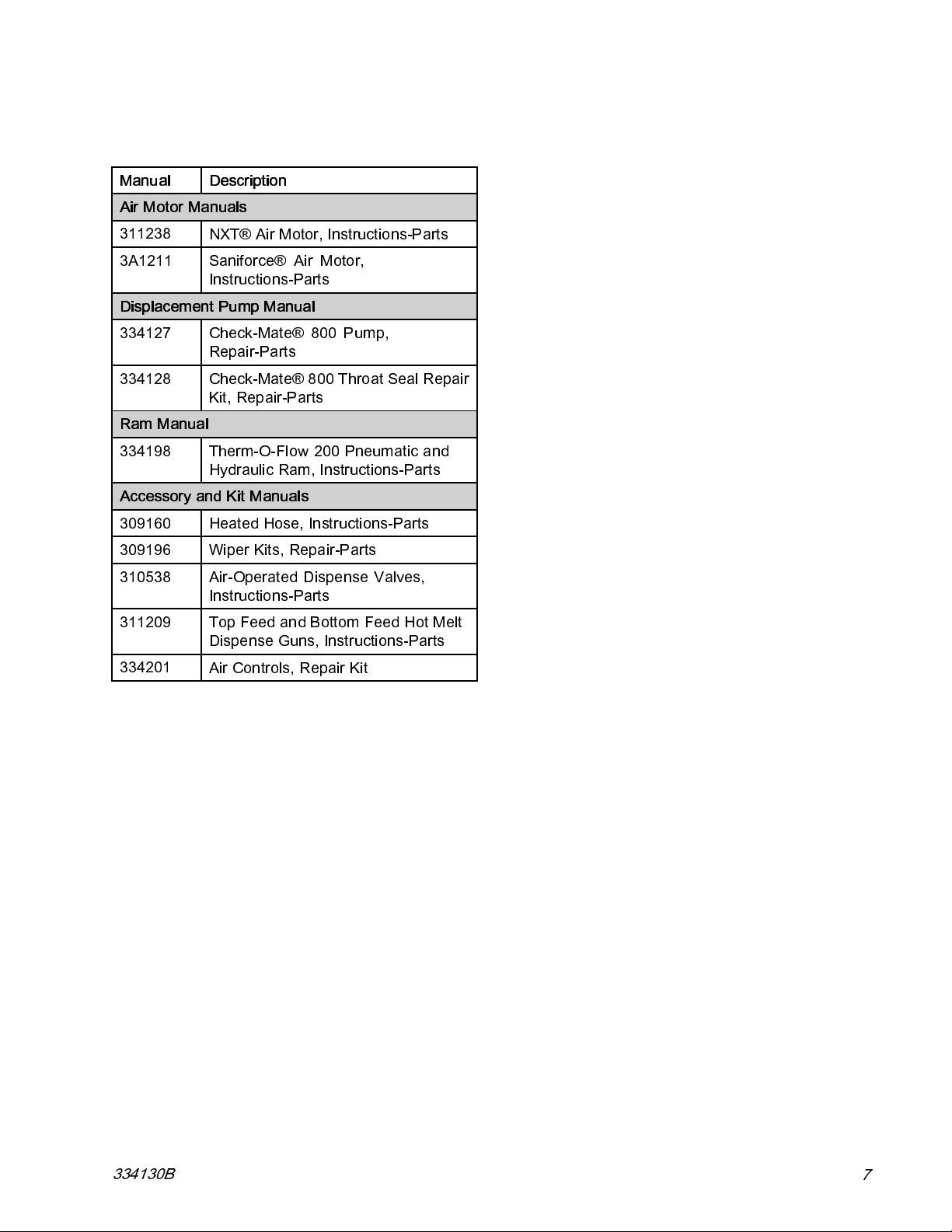
Related Manuals
Manual Description
Air Motor Manuals
Related Manuals
311238
3A1211
Displacement Pump Manual
334127
334128
Ram Manual
334198
Accessory and Kit Manuals
309160 Heated Hose, Instructions-Parts
309196 Wiper Kits, Repair-Parts
310538 Air-Operated Dispense Valves,
311209 Top Feed and Bottom Feed Hot Melt
334201
NXT® Air Motor, Instructions-Parts
Saniforce® Air Motor,
Instructions-Parts
Check-Mate® 800 Pump,
Repair-Parts
Check-Mate® 800 Throat Seal Repair
Kit, Repair-Parts
Therm-O-Flow 200 Pneumatic and
Hydraulic Ram, Instructions-Parts
Instructions-Parts
Dispense Guns, Instructions-Parts
Air Controls, Repair Kit
334130B
7
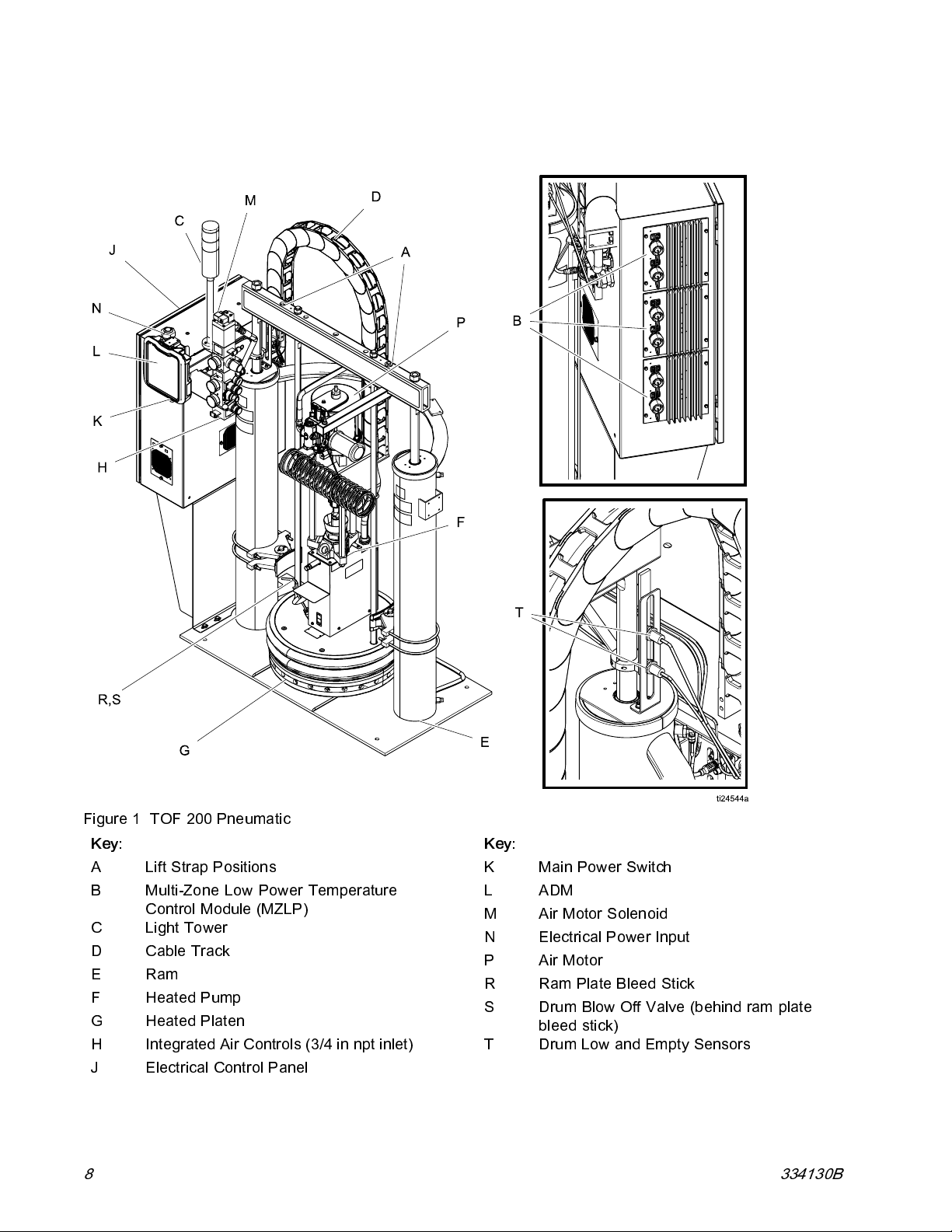
Component Identification
Component Identification
Figure 1 TOF 200 Pneumatic
Key:
A
B Multi-Zone Low Power Temperature
C
D
ERam
F Heated Pump
G
H
J
8 334130B
Lift Strap Positions
Control Module (MZLP)
Light Tower
Cable Track
Heated Platen
Integrated Air Controls (3/4 in npt inlet)
Electrical Control Panel
Key:
K
LADM
M
N Electrical Power Input
PAirMotor
R
S Drum Blow Off Valve (behind ram plate
T
Main Power Switch
Air Motor Solenoid
Ram Plate Bleed Stick
bleed stick)
Drum Low and Empty Sensors
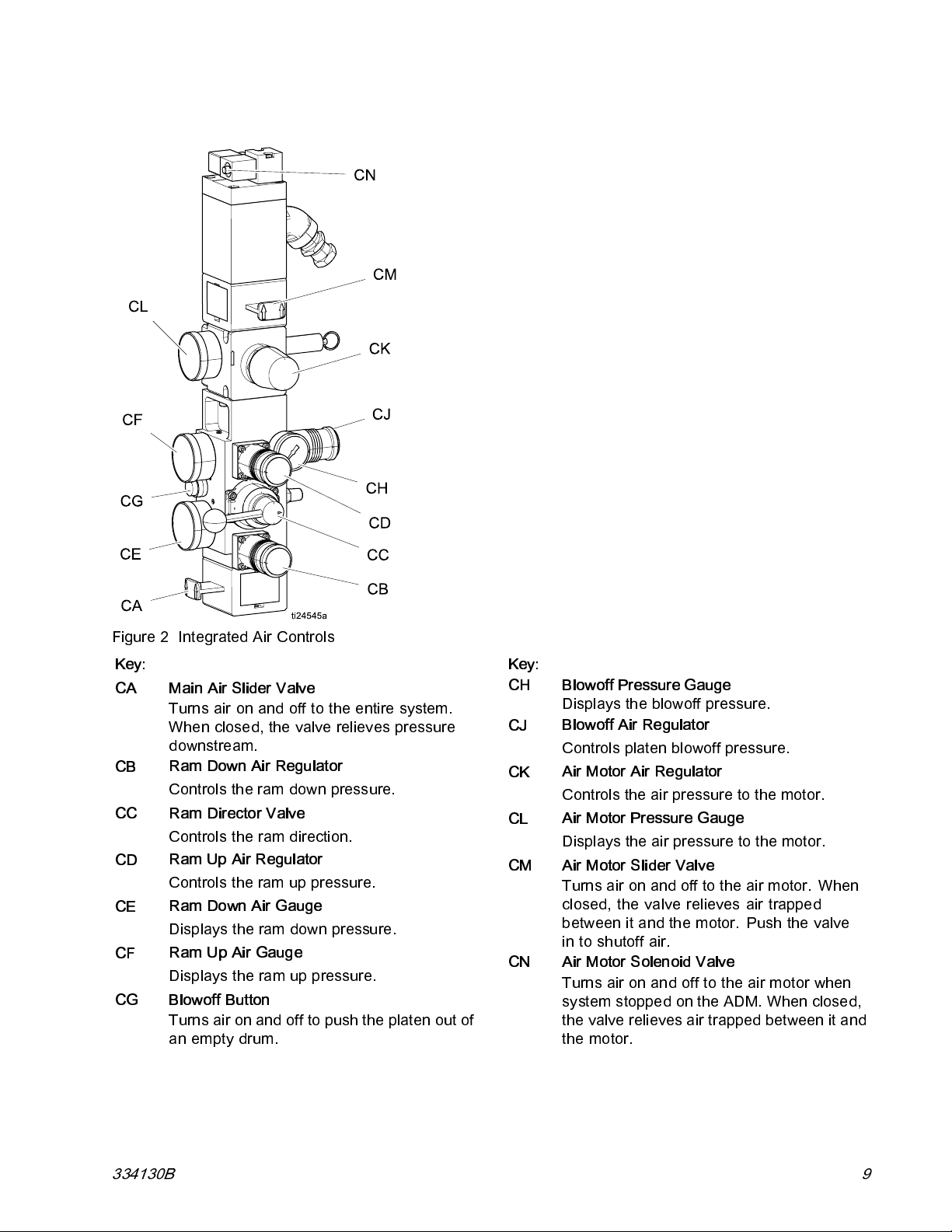
Integrated Air Controls
Component Identificatio n
Figure 2 Integrated Air Controls
Key:
CA Main Air Slider Valve
Turns air on and off to the entire system.
When closed, the valve relieves pressure
downstream.
CB
CC Ram Director Valve
CD
CE
CF
CG Blowoff Button
Ram Down Air Regulator
Controls the ram down pressure.
Controls the ram direction.
Ram Up Air Regulator
Controls the ram up pressure.
Ram Down Air Gauge
Displays the ram down pressure.
Ram Up Air Gauge
Displays the ram up pressure.
Turns air on and off to push the platen out of
an empty drum.
Key:
CH Blowoff Pressure G auge
Displays the blowoff pressure.
CJ
CK
CL
CM Air Motor Slider Valve
CN Air Motor Solenoid Valve
Blowoff Air Regulator
Controls platen blowoff pressure.
Air Motor Air Regulator
Controls the air pres sure to the motor.
Air Motor Pressure Gauge
Displays the air pressure to the motor.
Turns air on and off to the air mo tor. When
closed, the valve relieves air trapped
between it and the motor. Push the valve
in to shutoff air.
Turns air on and off to the air motor when
system stopped on the ADM. When closed,
the valve relieves air trapped between it and
the motor.
334130B 9
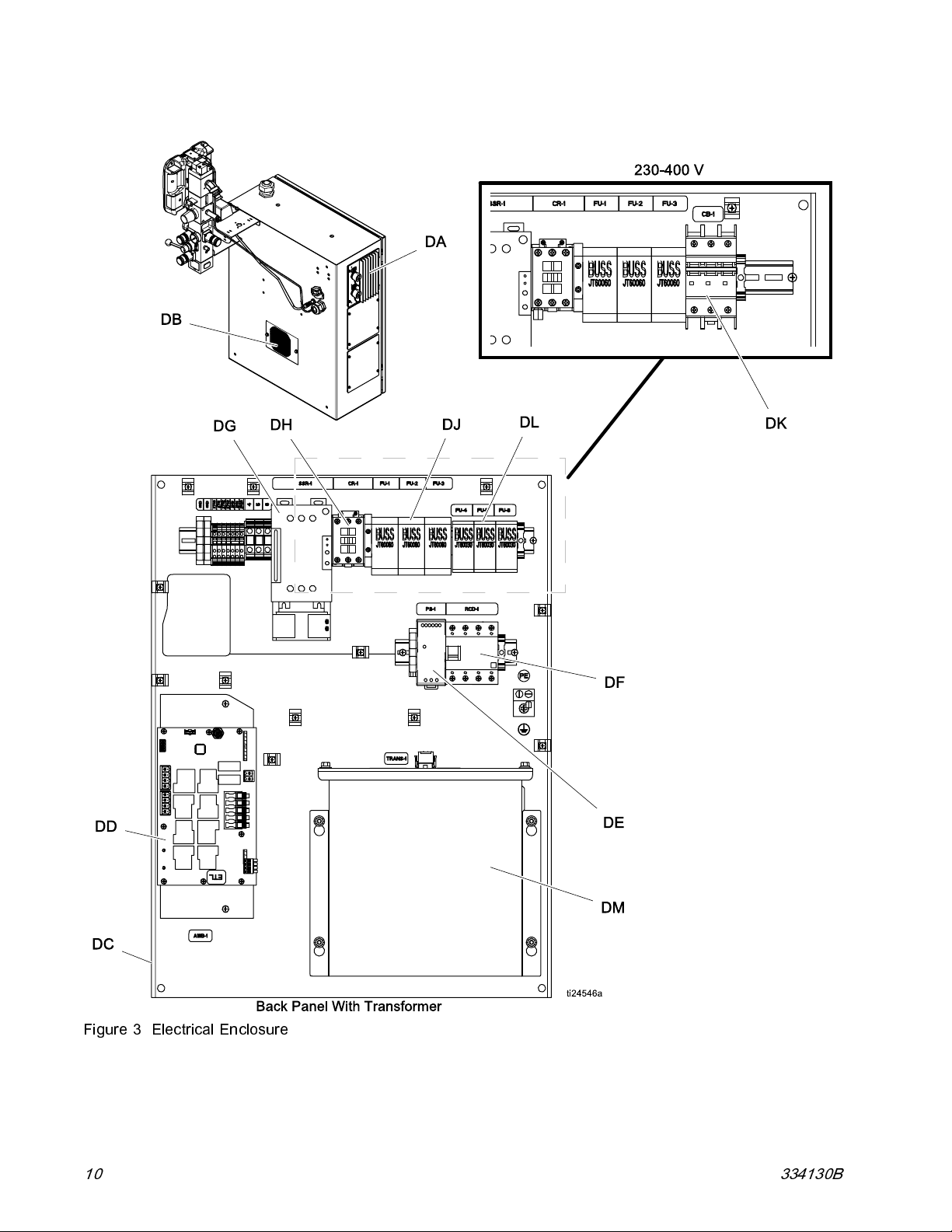
Component Identification
Electrical Control Enclosure
Figure 3 Electrical Enclosure
10 334130B
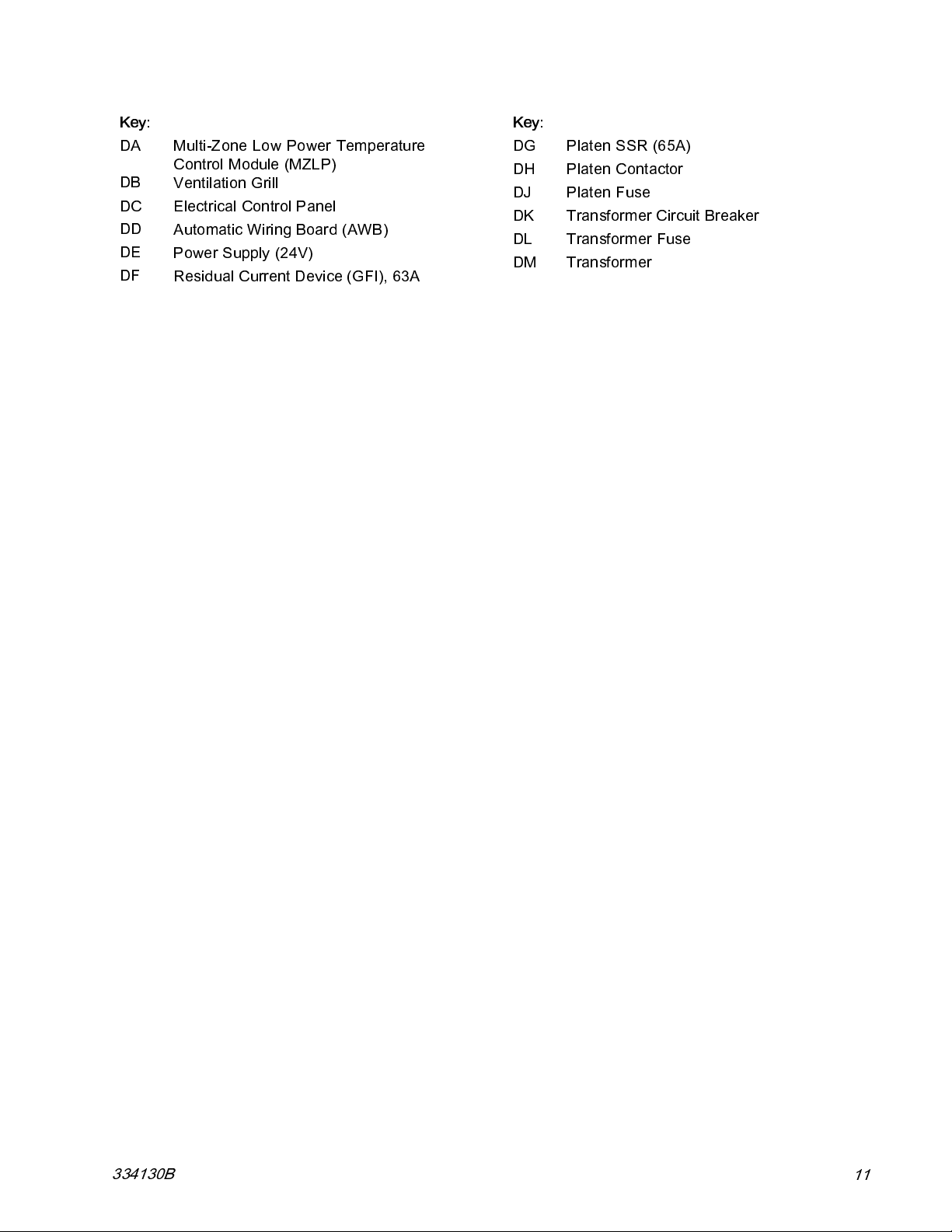
Component Identificatio n
Key:
DA Multi-Zone Low Power Temperature
Control Module (MZLP)
DB
DC Electrical Control Panel
DD
DE
DF
Ventilation Grill
Automatic Wiring Board (AWB)
Power Supply (24V)
Residual Current Device (GFI), 63A
Key:
DGPlatenSSR(65A)
DH
DJPlatenFuse
DK
DL
DM
Platen Contactor
Transformer Circuit Breaker
Transformer Fuse
Transformer
334130B
11
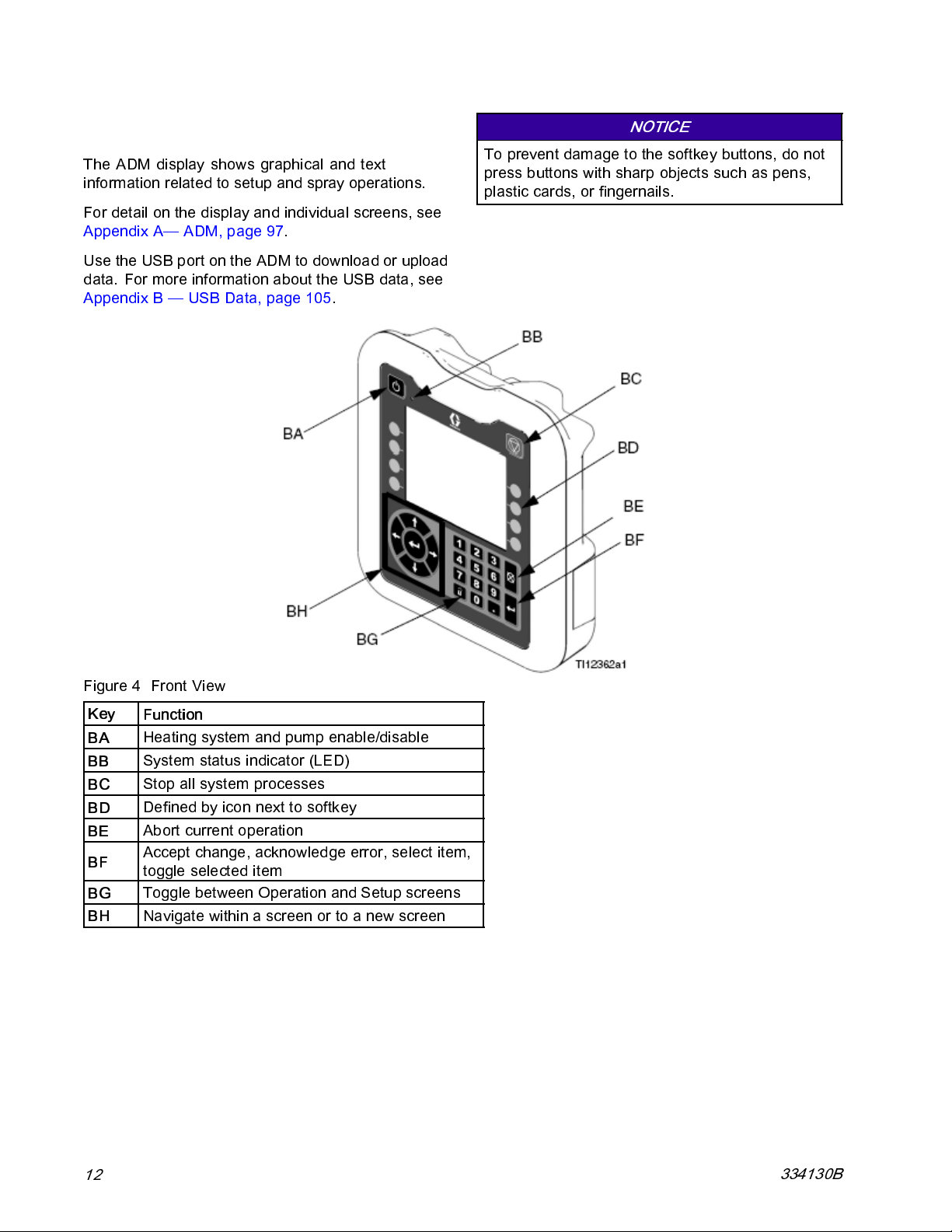
Component Identification
Advanced Display Module (ADM)
The ADM display shows graphical and text
information related to setup and spray operations.
For detail on the display and individual screens, see
Appendix A— ADM, page 97.
Use the USB port on the ADM to download or upload
data. For more information about the USB data, see
Appendix B — USB Data, page 105.
NOTICE
To prevent damage to the softkey buttons, do not
press buttons with sharp objects such as pens,
plastic cards, or fingernails.
Figure 4 Front View
Key
BA
BB
BC
BD
BE
BF
BG
BH
Function
Heating system and pump enable/disable
m status indicator (LED)
Syste
ll system processes
Stop a
dbyiconnexttosoftkey
Define
current operation
Abort
Accept change, acknowledge error, select item,
toggle selected item
Toggle between Operation and Setup screens
Navigatewithinascreenortoanewscreen
12
334130B
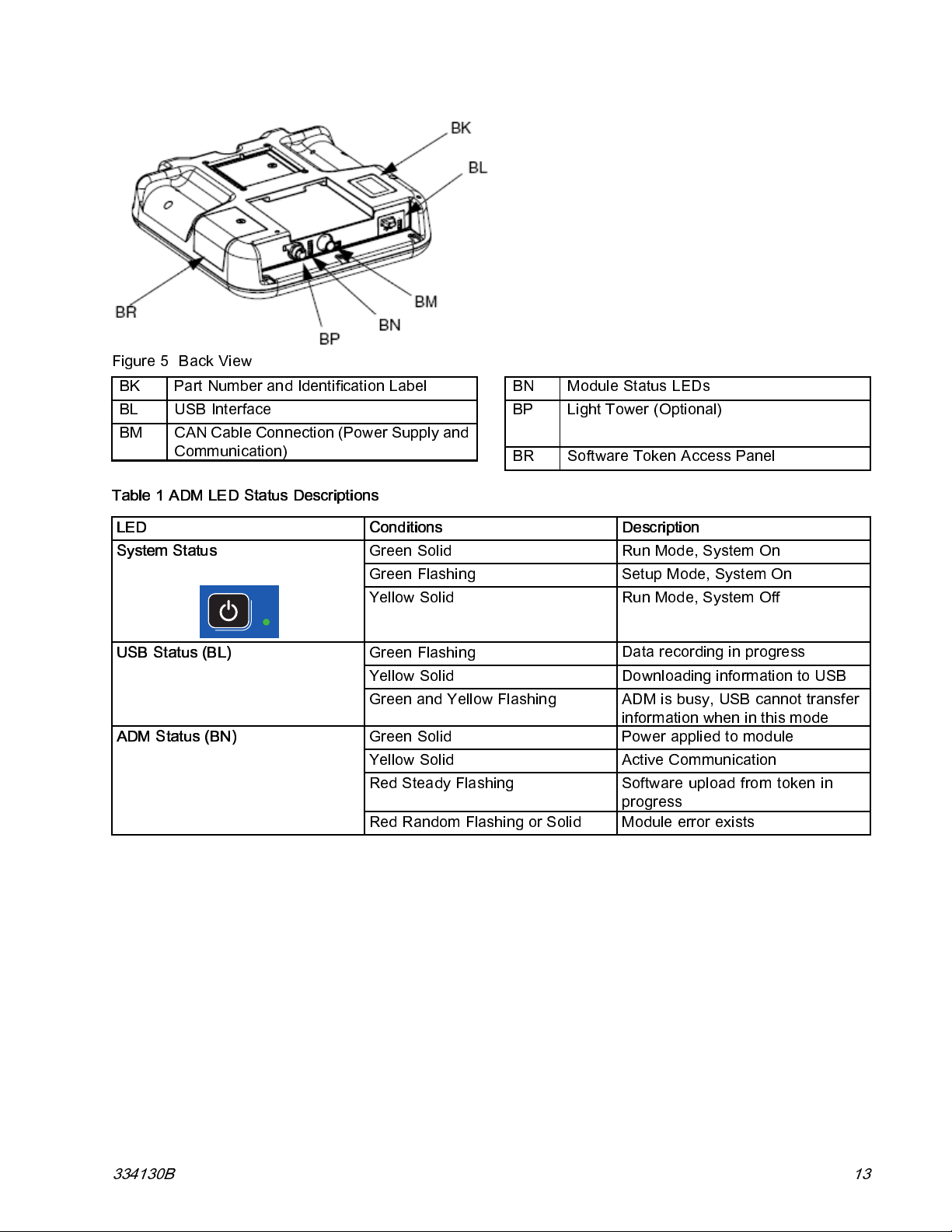
Figure 5 Back View
BK
BL
BM
Table 1 ADM LED Status Descriptions
Part Number and Identi fication Label
USB Interface
CAN Cable Connection (Power Supply and
Communication)
BN
BP
BR
Component Identificatio n
Module Status LEDs
Light Tower (Optional)
Software Token Access Panel
LED
System Status
USB Status (BL)
ADM Status (BN)
Conditions
Green Solid Run Mode, System On
Green Flashing Setup Mode, System On
Yellow Solid Run Mode, System Off
Green Flashing
Yellow Solid Downloading information to U SB
Green and Yellow Flashing ADM is busy, USB cannot transfer
Green Solid
Yellow Solid Active Communication
Red Steady Flashing Software upload from token in
Red Random Flashing or Solid
Description
Data recording in progress
informationwheninthismode
Power applied to module
progress
Module error exists
334130B 13
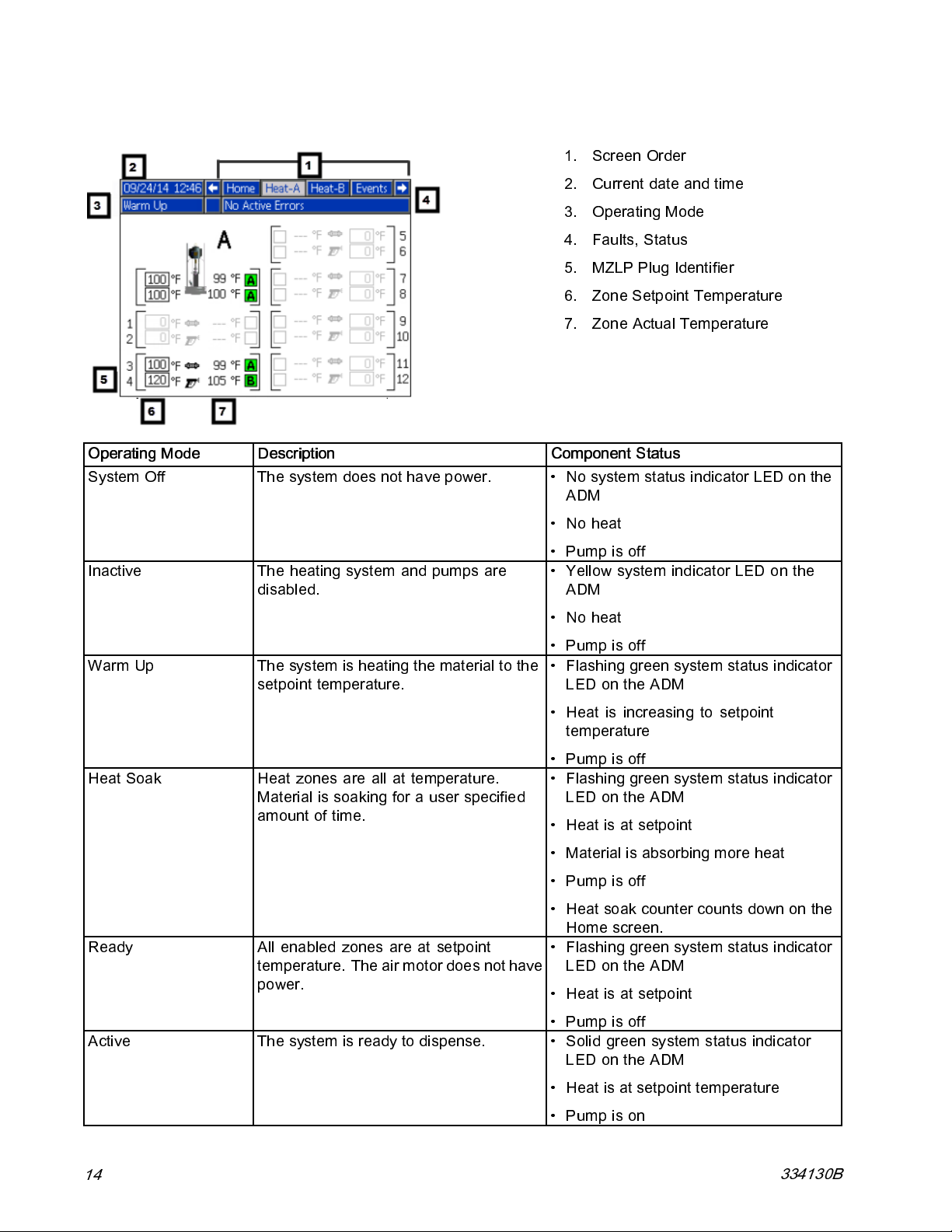
Component Identification
Screen Components
1. Screen Order
2. Current date and time
3. Operating Mode
4. Faults, Status
5. MZLP Plug Identifier
6. Zone Setpoint Temperature
7. Zone Actual Temperature
Operating Mode Description Component Status
System Off The system do
es not have powe r.
• No system sta
ADM
tus indicator LED on the
Inactive The heating system and pumps are
disabled.
Warm Up The system is heating the material to the
setpoint temperature.
Heat Soak
Ready All enabled zones are at setpoint
Heat zones are all at temperature.
Material is soaking for a user specified
amount of time.
temperature. The air motor does not have
power.
•Noheat
•Pumpisoff
• Yellow system indicator LED on the
ADM
•Noheat
•Pumpisoff
• Flashing green system status indicator
LED on the ADM
• Heat is increasing to setpoint
temperature
•Pumpisoff
• Flashing green system status indicator
LED on the ADM
• Heatisatsetpoint
• Material is absorbing more heat
•Pumpisoff
• Heat soak counter counts down on the
Home screen.
• Flashing green system status indicator
LED on the ADM
• Heatisatsetpoint
Act
14
ive
system is ready to dispense.
The
•Pumpisoff
• Solid green system status indicator
LED on the ADM
• Heatisatsetpointtemperature
•Pumpison
334130B
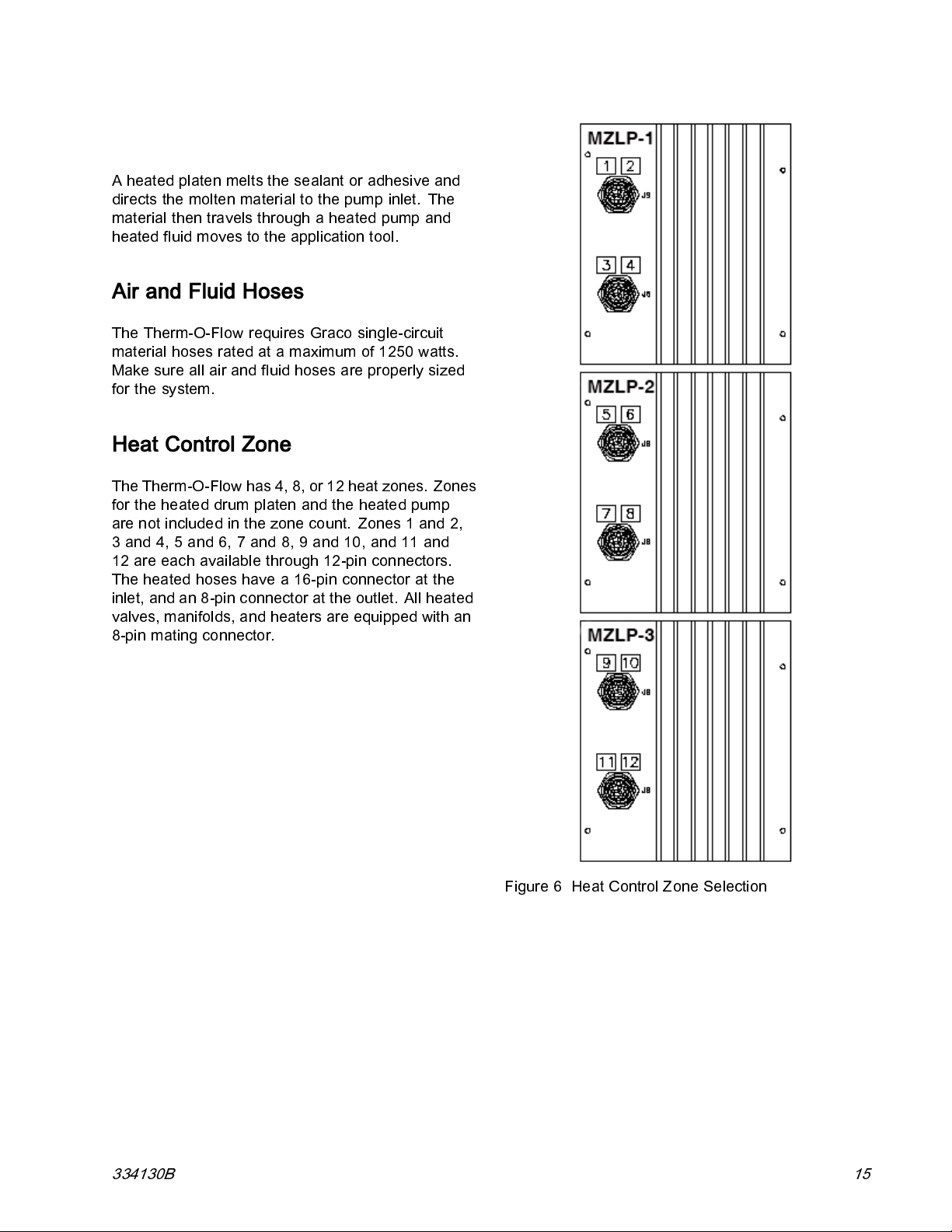
Overview
A heated platen melts the sealant or adhesive and
directs the molten material to the pump inlet. The
material then travels through a heated pump and
heated fluid moves to the application tool.
Air and Fluid Hoses
The Therm-O-Flow requires Graco single-circuit
material hoses rated at a maximum of 1250 watts.
Make sure all air and fluid hoses are properly sized
for the system.
Heat Control Zone
The Therm-O-Flow has 4, 8, or 12 heat zones. Zones
for the heated drum platen and the heated pump
are not included in the zone count. Zones 1 and 2,
3 and 4, 5 and 6, 7 and 8, 9 and 10, and 11 and
12 are each available through 12-pin connectors.
The heated hoses have a 16-pin connector at the
inlet, and an 8-pin connector at the o u tlet. All heated
valves, manifolds, and heaters are equipped with an
8-pin mating connector.
Overview
Figure 6 Heat Control Zone Selection
334130B 15
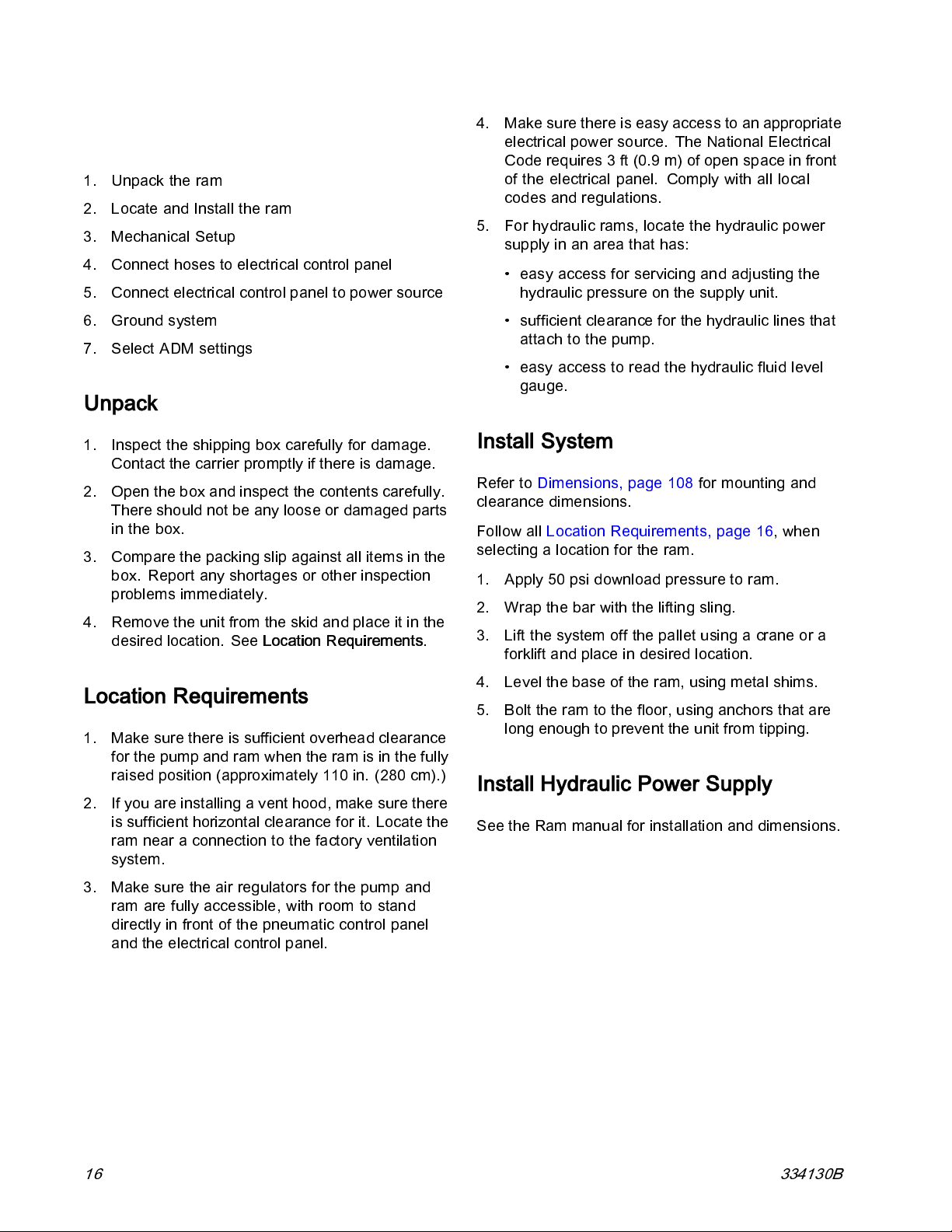
Setup
Setup
1. Unpack the ram
2. Locate and Install the ram
3. Mechanical Setup
4. Connect hoses to electrical control panel
5. Connect electrical control panel t o power source
6. Ground system
7. Select ADM settings
Unpack
1. Inspect the shipping box carefully for damage.
Contact the carrier promptly if there is damage.
2. Open the box and inspect the contents carefully.
There should not be any loose or damaged parts
in the box.
3. Compare the packing slip against all items in the
box. Re port any shortages or other inspection
problems immediately.
4. Remove the unit from the skid and place it in the
desired location. See
Location Requirements
.
4. Make sure there is easy access to an appropriate
electrical power source. The National Electrical
Code requires 3 ft (0.9 m) of open space in front
of the electrical panel. Comply with all local
codes and regulations.
5. For hydraulic rams, locate the hydraulic power
supply in an area that has:
• easy access for servicing and adjusting the
hydraulic pressure on the su pply unit.
• sufficient clearance for the hydraulic lines that
attach to the pump.
• easy access to read the hydraulic fluid level
gauge.
Install System
Refer to Dimensions, page 108 for mounting and
clearance dimensions.
Follow all Location Requirements, page 16,when
selecting a location for the ram.
1. Apply 50 psi download pressure to ram.
2. Wrap the bar with the lifting sling.
3. Lift the system off the pallet using a crane or a
forklift and place in desired location.
Location Requirements
1. Make sure there is sufficient overhead clearance
for the pump and ram w hen the ram is in the fully
raised position (approximately 110 in. (280 cm).)
2. If you are installing a vent hood, make sure there
is sufficient horizontal clearance for it. Locate the
ram near a connection to the factory ventilation
system.
3. Make sure the air regulators for the pump and
ram are fully accessible, with room to stand
directly in front of the pneumatic control panel
and the electrical control panel.
4. Level the base of the ram, using metal shims.
5. Bolt the ram to the floor, using anchors that are
long enough to prevent the unit from tipping.
Install Hydraulic Power Supply
See the Ram manual for installation and dimensions.
16 334130B
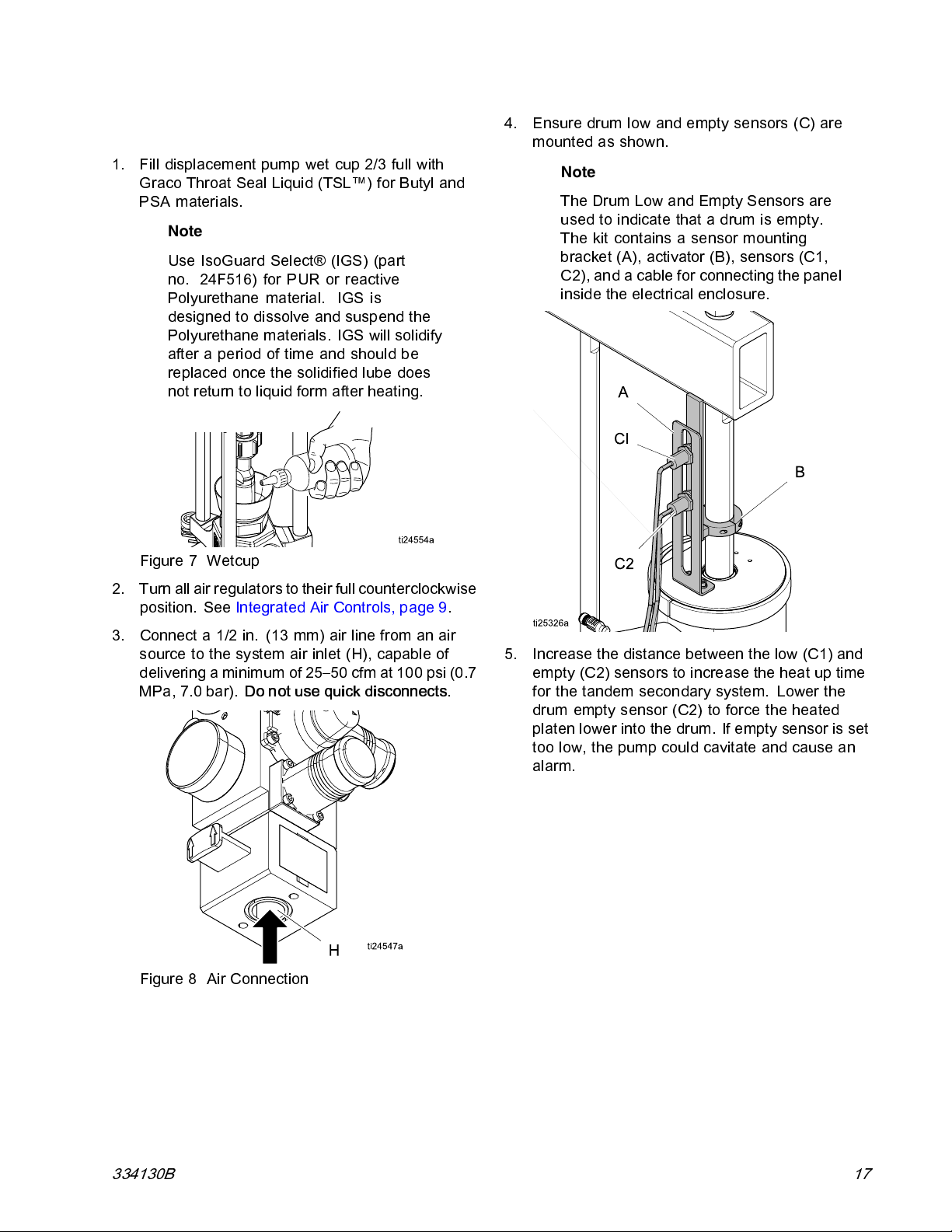
Setup
Mechanical Setup
1. Fill displacement pump wet cup 2/3 full with
Graco Throat Seal Liquid (TSL™) for Butyl and
PSA materials.
Note
Use IsoGuard Select® (IGS) (part
no. 24F516) for PUR or reactive
Polyurethane material. IGS is
designed to dissolve and suspend the
Polyurethane materials. IGS will solidify
after a period of time and should be
replaced once the solidified lube does
not return to liquid form after heating.
Figure 7 Wetcup
4. Ensure drum low and empty sensors (C) are
mounted as shown.
Note
TheDrumLowandEmptySensorsare
used to indicate that a drum is empty.
The kit contains a sensor mounting
bracket (A), activator (B), sensors (C1,
C2), and a cable for connecting the panel
inside the electrical enclosure.
2. Turn all air regulators to their full counterclockwise
position. See Integrated Air Controls, page 9.
3. Connect a 1/2 in. (13 mm) air line from an air
source to the system air inlet (H), capable of
delivering a minimum of 25–50 cfm at 100 psi (0.7
MPa, 7.0 bar).
Figure 8 Air Connection
Do not use quick disconnects
.
5. Increase the distance between the low (C1) and
empty (C2) sensors to increase the heat up time
for the tandem secondary system. Lower the
drum empty sensor (C2) to force the heated
platen lower into the drum. If empty sensor is set
too low, the pump could cavitate and cause an
alarm.
334130B
17
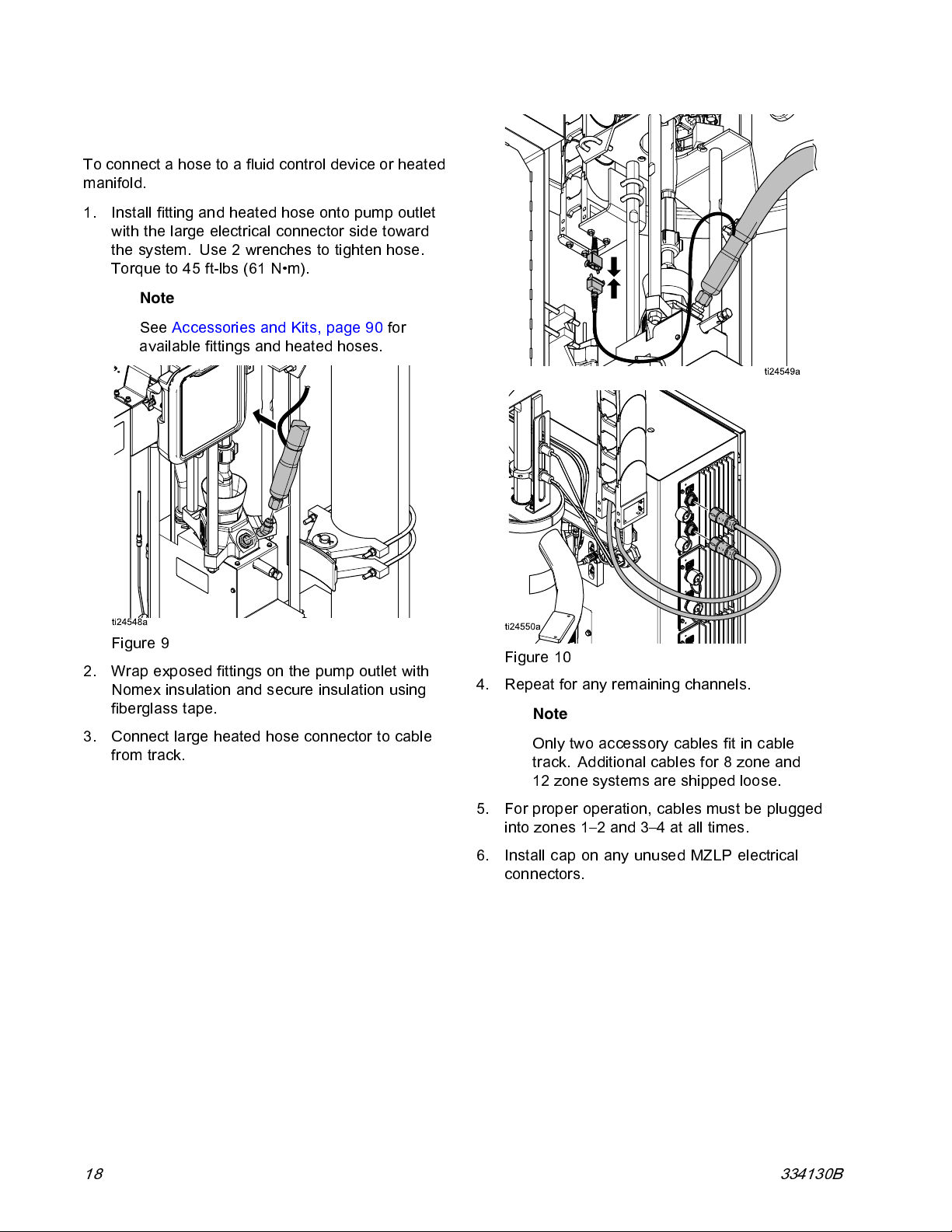
Setup
Install Heated Hose
To connect a hose to a fluid control device or heated
manifold.
1. Install fitting and heated hose onto pump outlet
with the large electrical connector side toward
thesystem.Use2wrenchestotightenhose.
Torque to 45 ft-lbs (61 N•m).
Note
See Accessories and Kits, page 90 for
available fittings and heated hoses.
Figure 9
2. Wrap exposed fittings on the pump outlet with
Nomex insulation and secure insulation using
fiberglass tape.
3. Connect large heated hose connector to cable
from track.
Figure 10
4. Repeat for any remaining channels.
Note
Only two accessory cables fit in cable
track. Addi tional cables for 8 zone and
12 zone systems are shipped loose.
5. For proper operation, cables must be plugged
into zones 1–2 and 3–4 at all times.
6. Install cap on any unused MZLP electrical
connectors.
18 334130B
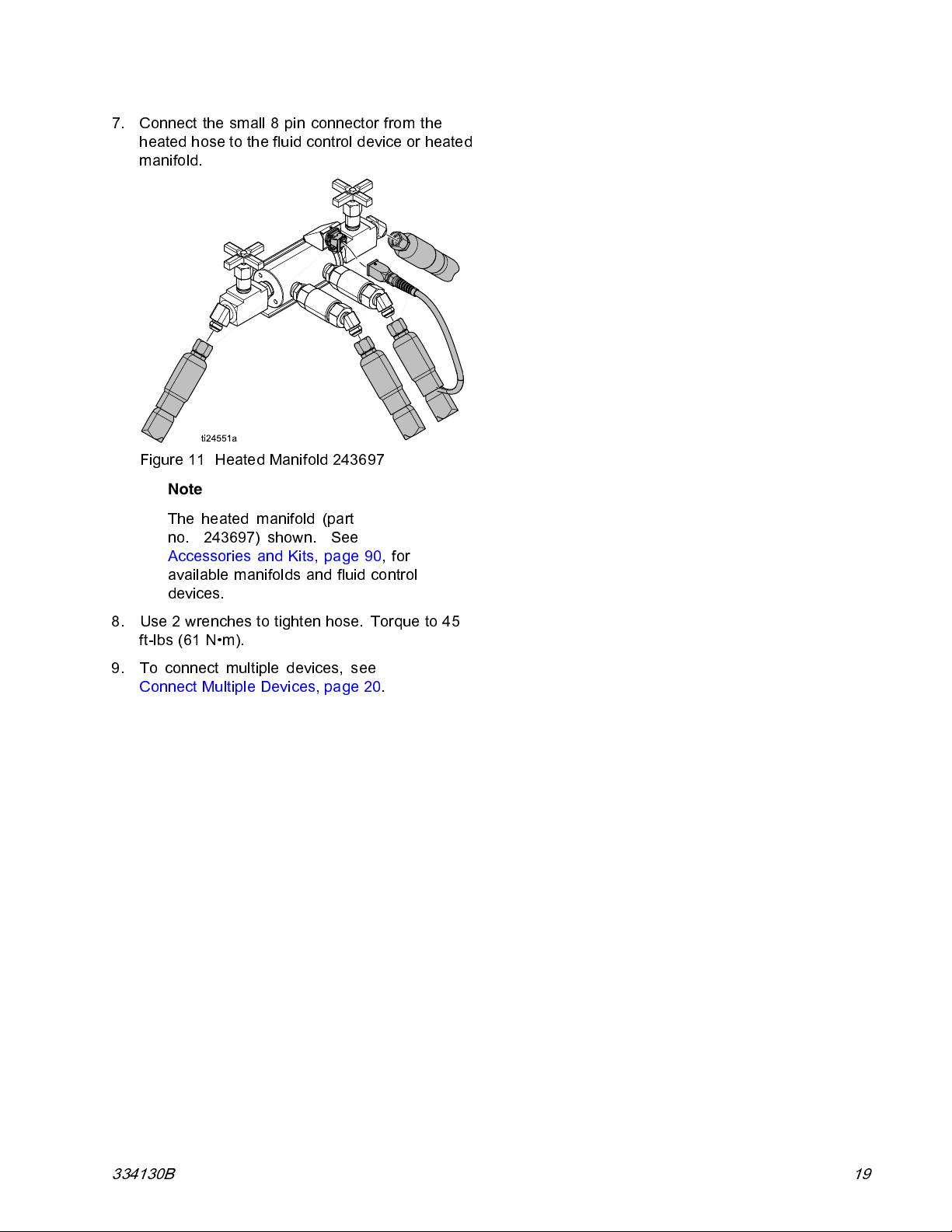
7. Connect the small 8 pin connector from the
heated hose to the fluid control device or heated
manifold.
Figure 11 Heated Manifold 243697
Note
Theheatedmanifold(part
no. 243697) shown. See
Accessories and Kits, page 90,for
available manifolds and fluid control
devices.
Setup
8. Use 2 wrenches to tighten hose. Torque to 45
ft-lbs (61 N•m).
9. To connect multiple devices, see
Connect Multiple Devices, page 20.
334130B 19
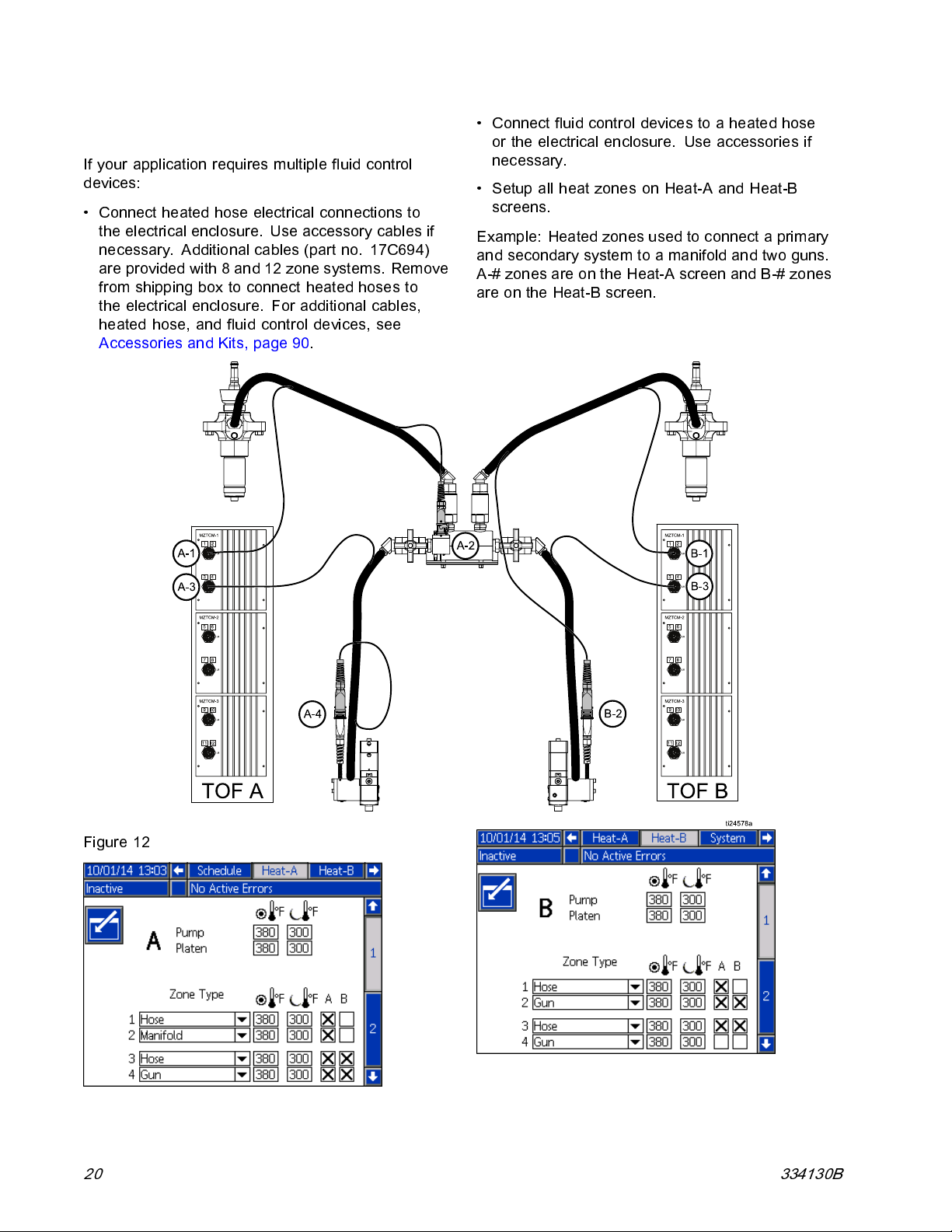
Setup
Connect Multiple Devices
If your application requires multiple fluid control
devices:
• Connect heated hose electrical connections to
the electrical enclosure. Use accessory cables if
necessary. Additional cables (part no. 17C694)
areprovidedwith8and12zonesystems.Remove
from shipping box to connect heated hoses to
the electrical enclosure. For additional cables,
heated hose, and fluid control devices, see
Accessories and Kits, page 90.
• Connect fluid control devices to a heated hose
or the electrical enclosure. Use accessories if
necessary.
• Setup all heat zones on Heat-A and Heat-B
screens.
Example: Heated zones used to connect a primary
andsecondarysystemtoamanifoldandtwoguns.
A-# zones are on the Heat-A screen and B-# zones
are on the Heat-B screen.
Figure 12
20 334130B
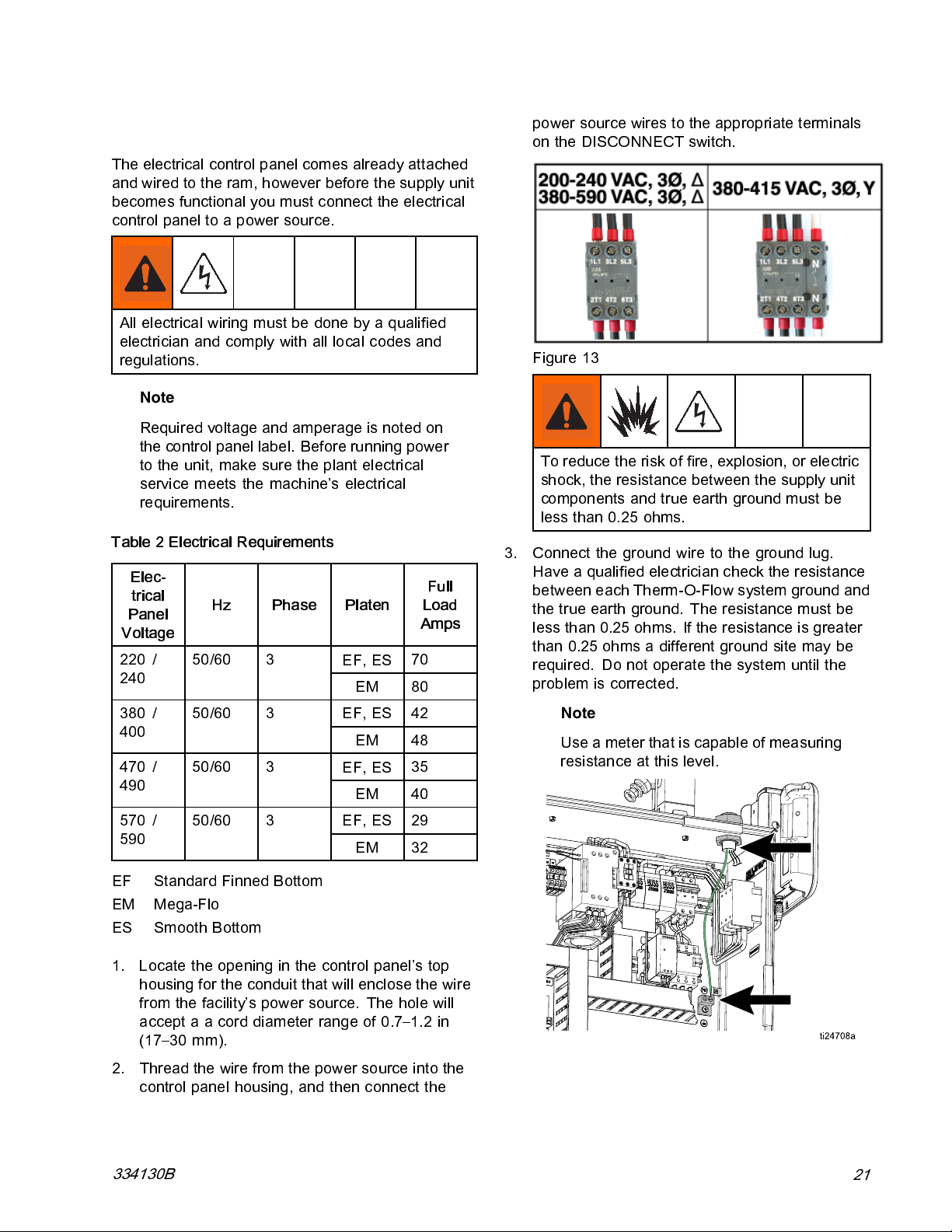
Setup
Connect Power
The electrical control panel comes already attached
and wired to the ram, however before the supply unit
becomes functional you must connect the electrical
control panel to a power source.
All electrical wiring must be done by a qualified
electrician and comply with all local codes and
regulations.
Note
Required voltage and amperage is noted on
the control panel label. Before running power
to the unit, make sure the plant electrical
service meets the machine’s electrical
requirements.
Table 2 Electrical Requirements
Elec-
trical
Panel
Voltage
220 /
240
Hz Phase Platen
50/60 3
EF, ES
EM 80
Full
Load
Amps
70
power source wires to the appropriate terminals
on the DISCONNECT switch.
Figure 13
To reduce the risk of fire, explosion, or electric
shock, the resistance between the supply unit
components and true earth ground must be
less than 0.25 ohms.
3. Connect
Haveaqu
between
the true
less tha
than 0.2
requir
proble
the ground wire to the ground lug.
alified electrician check the resistance
each Therm-O-Flow system ground and
earthground. Theresistancemustbe
n 0.25 ohms. If the resistance is greater
5 ohms a different ground site may be
ed. Do not operate the system until the
m is corrected.
380 /
400
470 /
490
570 /
590
EF
EM Mega-Flo
ES Smooth Bottom
1. Locate the opening in the control panel’s top
housing for the conduit that will enclose the wire
from the facility’s power source. The hole will
accept a a cord diameter range of 0.7–1.2 in
(17–30 mm).
2. Thread the wire from the power source into the
control panel housing, and then connect the
50/60 3
50/60 3
50/60 3
Standard Finned Bottom
EF, ES
EM 48
EF, ES
EM 40
EF, ES
EM 32
42
35
29
Note
Use a meter that is capable of measuring
resistance at this level.
334130B
21
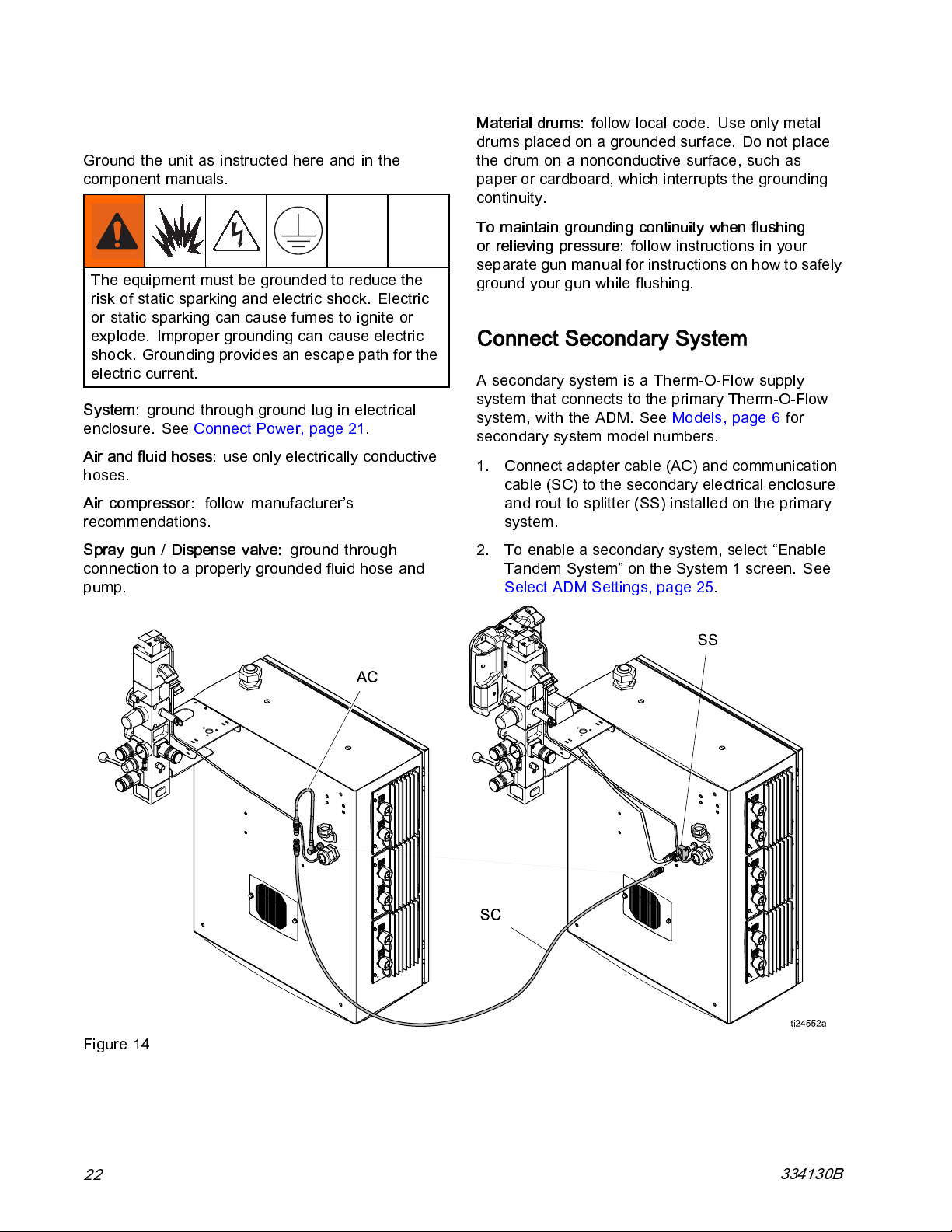
Setup
Grounding
Ground the unit as instructed here and in the
component manuals.
The equipment must be grounded to reduce the
risk of static sparking and electric shock. Electric
or static sparking can cause fumes to ignite or
explode. Improper grounding can cause electric
shock. Grounding provides an escape path for the
electric current.
System:
enclosure. See Connect Power, page 21.
Air and fluid hoses:
hoses.
Air compressor:
recommendations.
Spray gun/Dispense valve:
connection to a properly grounded fluid hose and
pump.
ground through ground lug in electrical
use only electrically conductive
follow manufacturer’s
ground through
Material drums:
drums placed on a grounded surface. Do not place
the drum on a nonconductive surface, such as
paper or cardboard, which interrupts the grounding
continuity.
To maintain grounding continuity when flushing
or relieving pressure:
separate gun manual for instructions on how to safely
ground your gun while flushing.
follow local code. Use only metal
follow instructions in your
Connect Secondary System
A secondary system is a Th erm-O-Flow supply
system that connects to the primary Therm-O-Flow
system, with the ADM. See Models, page 6 for
secondary system model numbers.
1. Connect adapter cable (AC) and communication
cable (SC) to the secondary electrical enclosure
and rout to splitter (SS) installed on the primary
system.
2. To enable a secondary system, select “Enable
Tandem System” on the System 1 screen. See
Select ADM Settings, page 25.
Figure 14
22
334130B
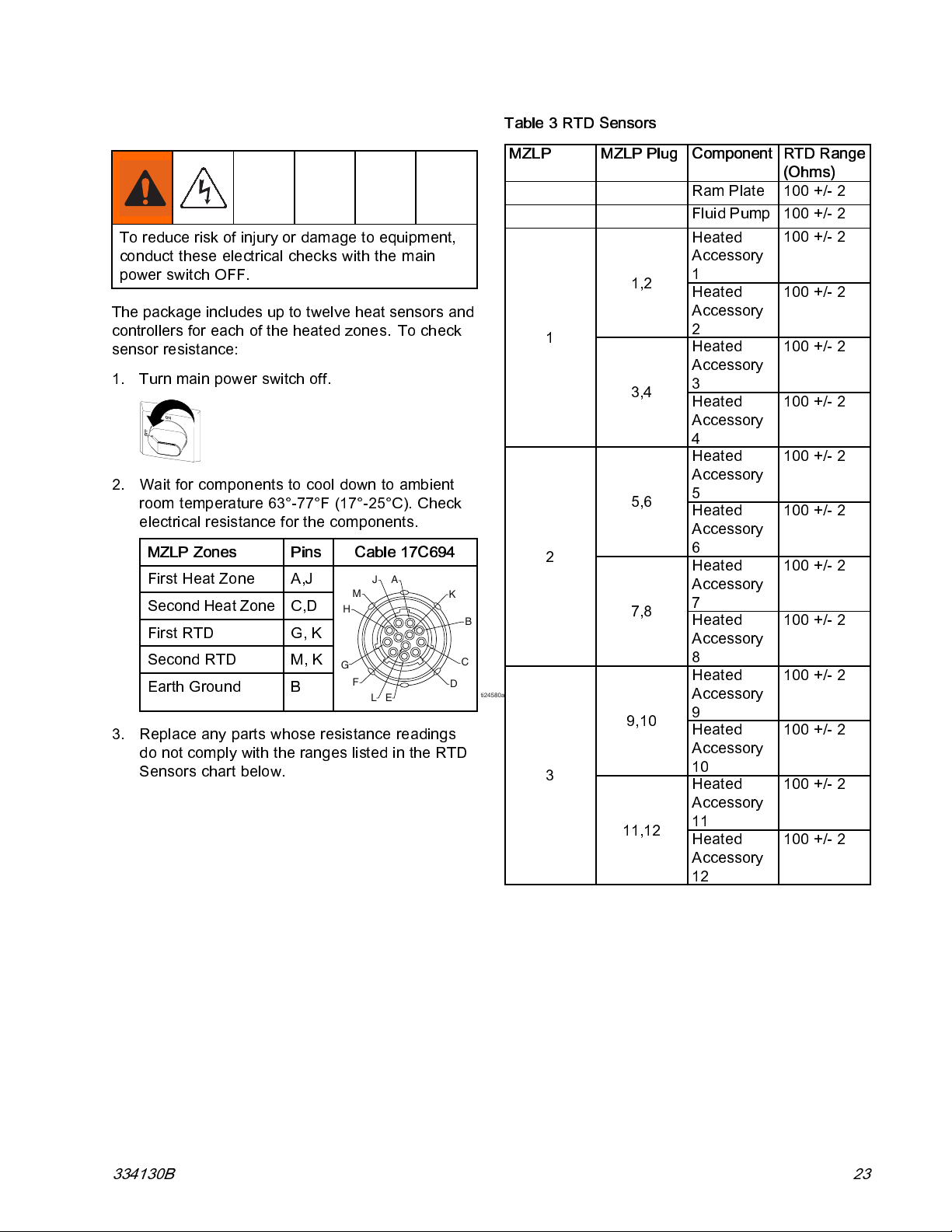
Setup
Check Sensor Resistance
To reduce risk of injury or damage to equipment,
conduct these electrical checks with the main
power switch OFF.
The package includes up to twelve heat sensors and
controllers for each of the heated zones. To check
sensor resistance:
1. Turn main power switch off.
2. Wait for components to cool down to ambient
room temperature 63°-77°F (17°-25°C). Check
electrical resistance for the components.
MZLP Zones Pins
First Heat Zone A,J
Second Heat Zone C,D
First RTD
Second RTD
Earth Ground
G, K
M, K
B
3. Replace any parts whose resistance readings
do not comply with t he ranges listed in the RTD
Sensors chart below.
Cable 17C694
A
J
M
H
G
F
E
L
K
C
D
Table 3 RTD Sensors
MZLP MZLP Plug
1
2
B
ti24580a
3
1,2
3,4
5,6
7,8
9,10
11,12
Component
RTD Range
(Ohms)
Ram Plate 100 +/- 2
Fluid Pump 100 +/- 2
Heated
100 +/- 2
Accessory
1
Heated
100 +/- 2
Accessory
2
Heated
100 +/- 2
Accessory
3
Heated
100 +/- 2
Accessory
4
Heated
100 +/- 2
Accessory
5
Heated
100 +/- 2
Accessory
6
Heated
100 +/- 2
Accessory
7
Heated
100 +/- 2
Accessory
8
Heated
100 +/- 2
Accessory
9
Heated
100 +/- 2
Accessory
10
Heated
100 +/- 2
Accessory
11
Heated
100 +/- 2
Accessory
12
334130B 23
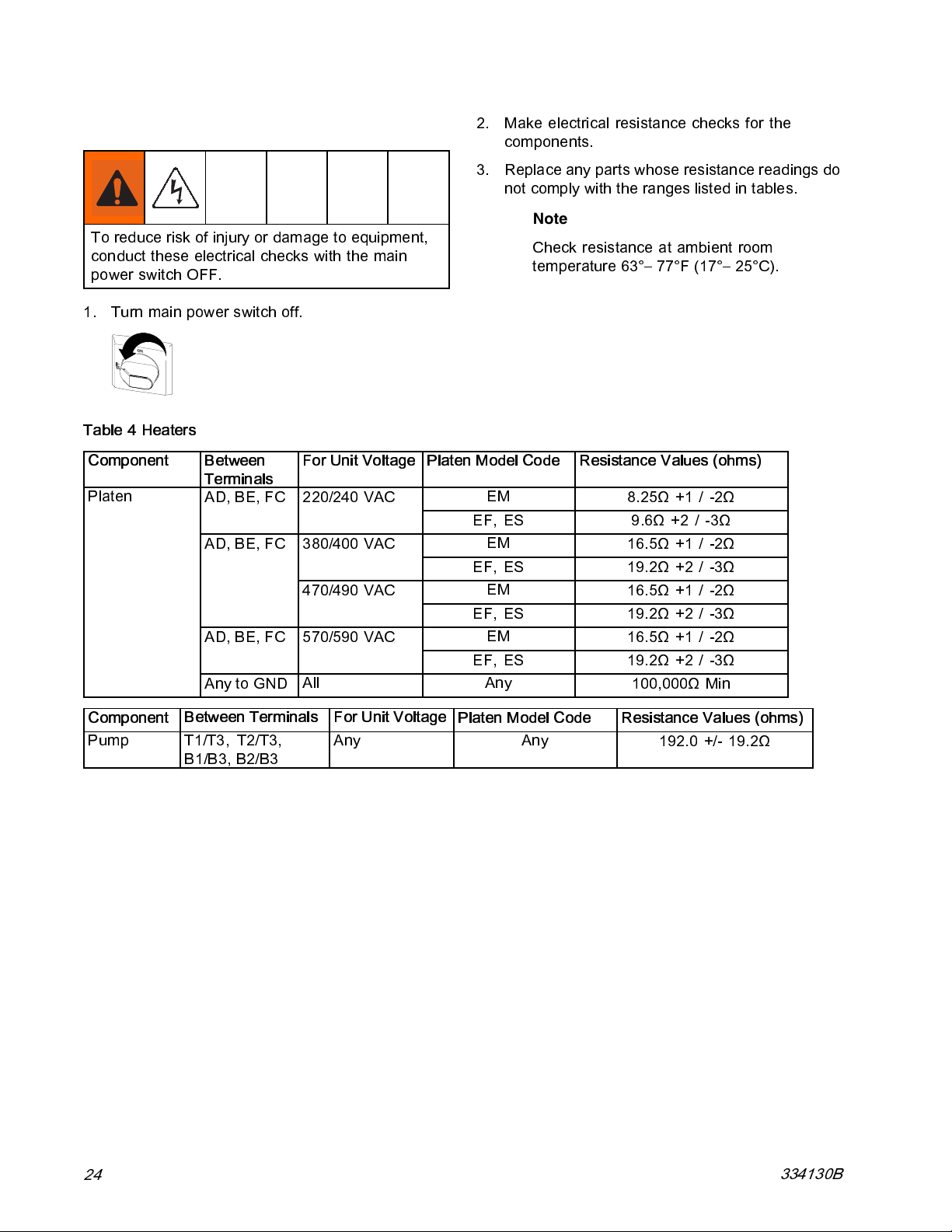
Setup
Check Heater Resistance
To reduce risk of injury or damage to equipment,
conduct these electrical checks with the main
power switch OFF.
1. Turn main power switch off.
Table 4 Heaters
Component
Platen
Between
Terminals
AD, BE, FC 220/240 VAC
AD, BE, FC
AD, BE, FC 570/590 VAC
Any to GND
For Unit Voltage
380/400 VAC
470/490 VAC
All Any
2. Make electrical resistance checks for the
components.
3. Replace any parts whose resistance readings do
not comply with the ranges listed in tables.
Note
Check resistance at ambient room
temperature 63°– 77°F (17°– 25°C).
Platen Model Code Resistance Values (ohms)
EM
EF, ES 9.6Ω +2 / -3Ω
EM
EF, ES 19.2Ω +2 / -3Ω
EM
EF, ES 19.2Ω +2 / -3Ω
EM
EF, ES 19.2Ω +2 / -3Ω
8.25Ω +1 / -2Ω
16.5Ω +1 / -2Ω
16.5Ω +1 / -2Ω
16.5Ω +1 / -2Ω
100,000Ω Min
Component
Pump T1/T3, T2/T3,
Between Terminals For Unit Voltage
B1/B3, B2/B3
Platen Model Code Resistance Values (ohms)
Any Any
192.0 +/- 19.2Ω
24
334130B

Select ADM Settings
Note
See Appendix A— ADM, page 97 for
detailed ADM information, including general
operation.
1. Turn main power switch on.
Setup
2. When the ADM is finished starting up, p res s
to switch from the Operation screens to
the Setup screens. Use the arrows to navigate
between screens.
3. Check system settings on the System 1 screen.
4. Set alarm levels on the System 2 screen.
Note
Setback temperatures must be at least
20°F (10°C) lower than the setpoint
temperatures
Note
To ensure accurate hose temperatures,
be sure all heated hoses have their
“zone type” set to “Hose.” Hoses are only
present on odd zone numbers: 1, 3, 5,
7, 9, or 11.
a. Select the appropriate “Zone Type” for all
installed zones.
b. Check the “A” and “B” boxes according to
which systems needs to use the heated
accessory.
6. If a secondary system is used, set temperatures
on the Heat-B screens.
7. Set the system date and time on the Advanced 1
screen.
5. Set primary system setpoint and setback
temperatures for the pump, platen, and heat
zones on the Heat-A screens.
334130B 25
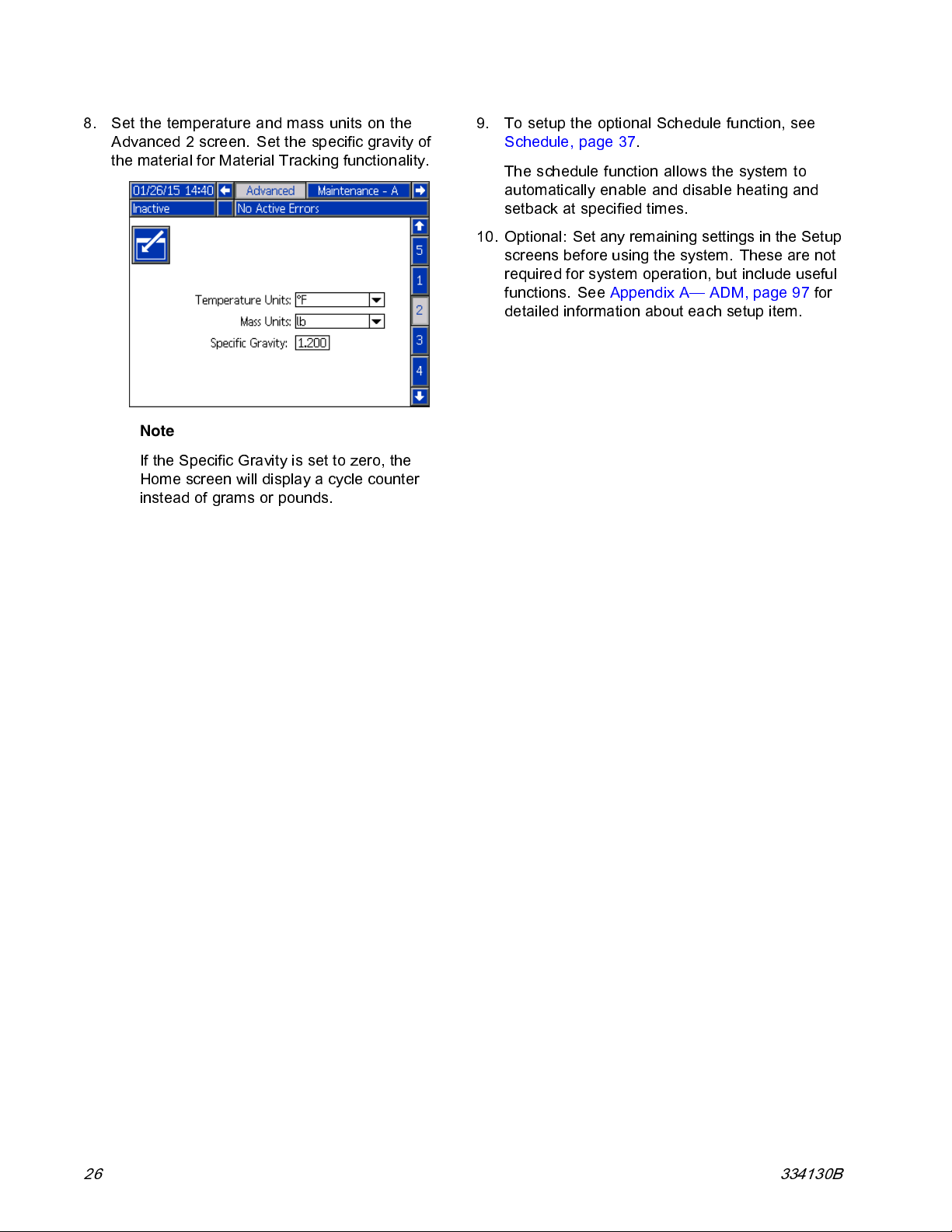
Setup
8. Set the temperature and mass units on the
Advanced 2 screen. Set the specific gravity of
the material for Material Tracking functionality.
Note
If the Specific Gravity is set to zero, the
Home screen will display a cycle counter
instead of grams or pounds.
9. To setup the optional Schedule function, see
Schedule, page 37.
The schedule function allows the system to
automatically enable and disable heating and
setback at specified times.
10. Optional: Set any remaining settings in the Setup
screens before using the system. These are not
required for system operation, but include useful
functions. See Appendix A— ADM, page 97 for
detailed information about each setup item.
26 334130B
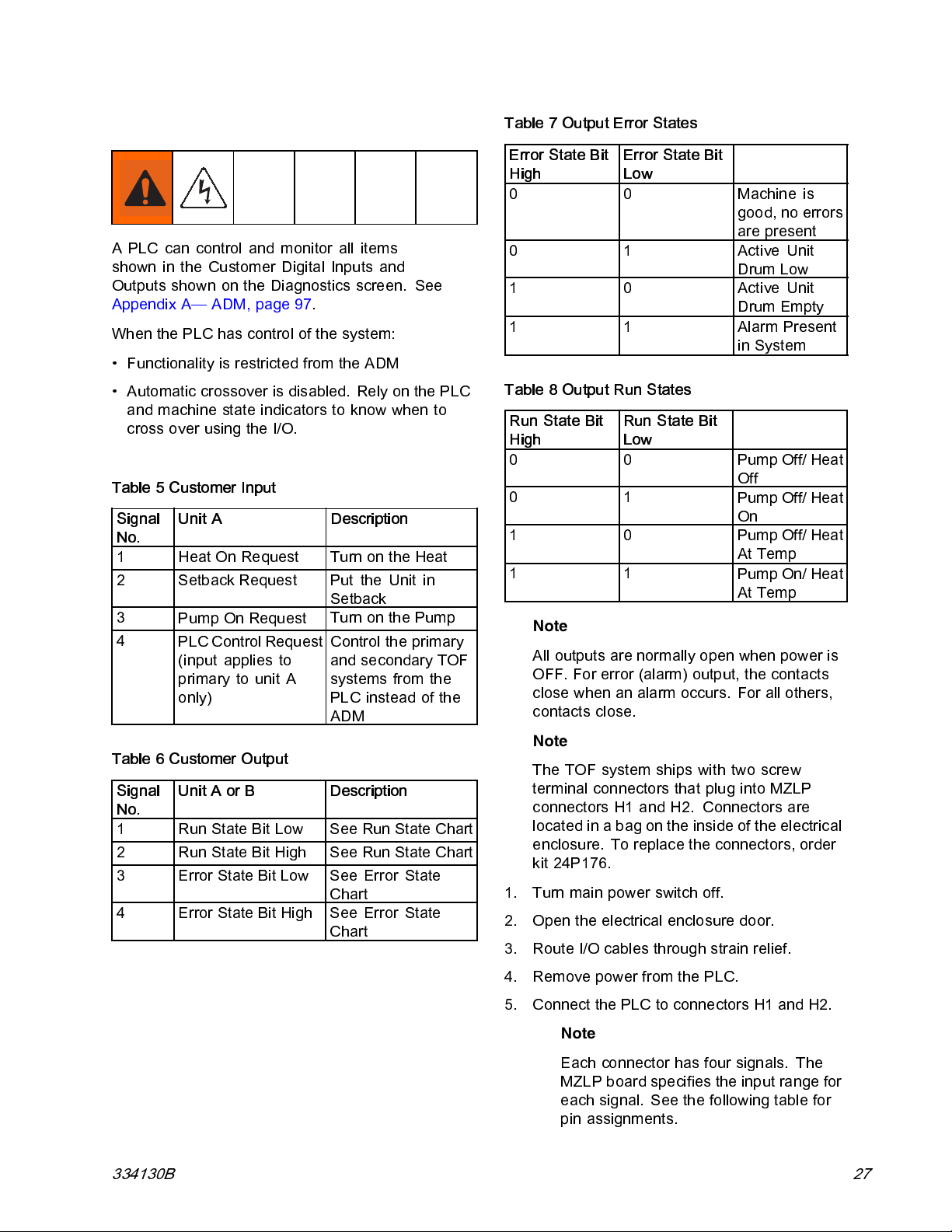
Setup
Connect PLC
A PLC can control and monitor all items
shown in the Customer Digital Inputs and
Outputs shown on the Diagnostics screen. See
Appendix A— ADM, page 97.
When the PLC has control of the system:
• Functionality is restricted from the ADM
• Automatic crossover is disabled. Rely on the PLC
and machine state indicators to know when to
cross over using the I/O.
Table 5 Customer Input
Signal
No.
1
2
3
4
Table 6 Customer Output
Signal
No.
1
2
3
4
Unit A Description
Heat On Request
Setback Request
Pump On Request
PLC Control Request
(input applies to
primary to unit A
only)
Unit A or B Description
Run State Bit Low See Run State Chart
Run State Bit High See Run State Chart
Error State Bit Low See Error State
Error State Bit High See Error State
Turn on the Heat
Put the Unit in
Setback
Turn on the Pump
Control the primary
and secondary TOF
systems from the
PLC instead of the
ADM
Chart
Chart
Table 7 Output Error States
Error State Bit
High
0 0 Machine is
01ActiveUnit
10ActiveUnit
1 1 Alarm Present
Table 8 Output Run States
Run State Bit
High
00
01
10
11
Note
All outputs are normally open when power is
OFF. For error (alarm) output, the contacts
close when an alarm occurs. For all others,
contacts close.
Note
The TOF system ships with two screw
terminal connectors that plug into MZLP
connectors H1 and H2. Connectors are
locatedinabagontheinsideoftheelectrical
enclosure. To replace the connectors, order
kit 24P176.
1. Turn main power switch off.
2. Open the electrical enclosure door.
3. Route I/O cables through strain relief.
Error State Bit
Low
good, no errors
are present
Drum Low
Drum Empty
in System
Run State Bit
Low
Pump Off/ Heat
Off
Pump Off/ Heat
On
Pump Off/ Heat
At Temp
Pump On/ Heat
At Temp
334130B
4. Remove power from the PLC.
5. Connect the PLC to connectors H1 and H2.
Note
Each connector has four signals. The
MZLP board specifies the input range for
each signal. See the following table for
pin assignments.
27
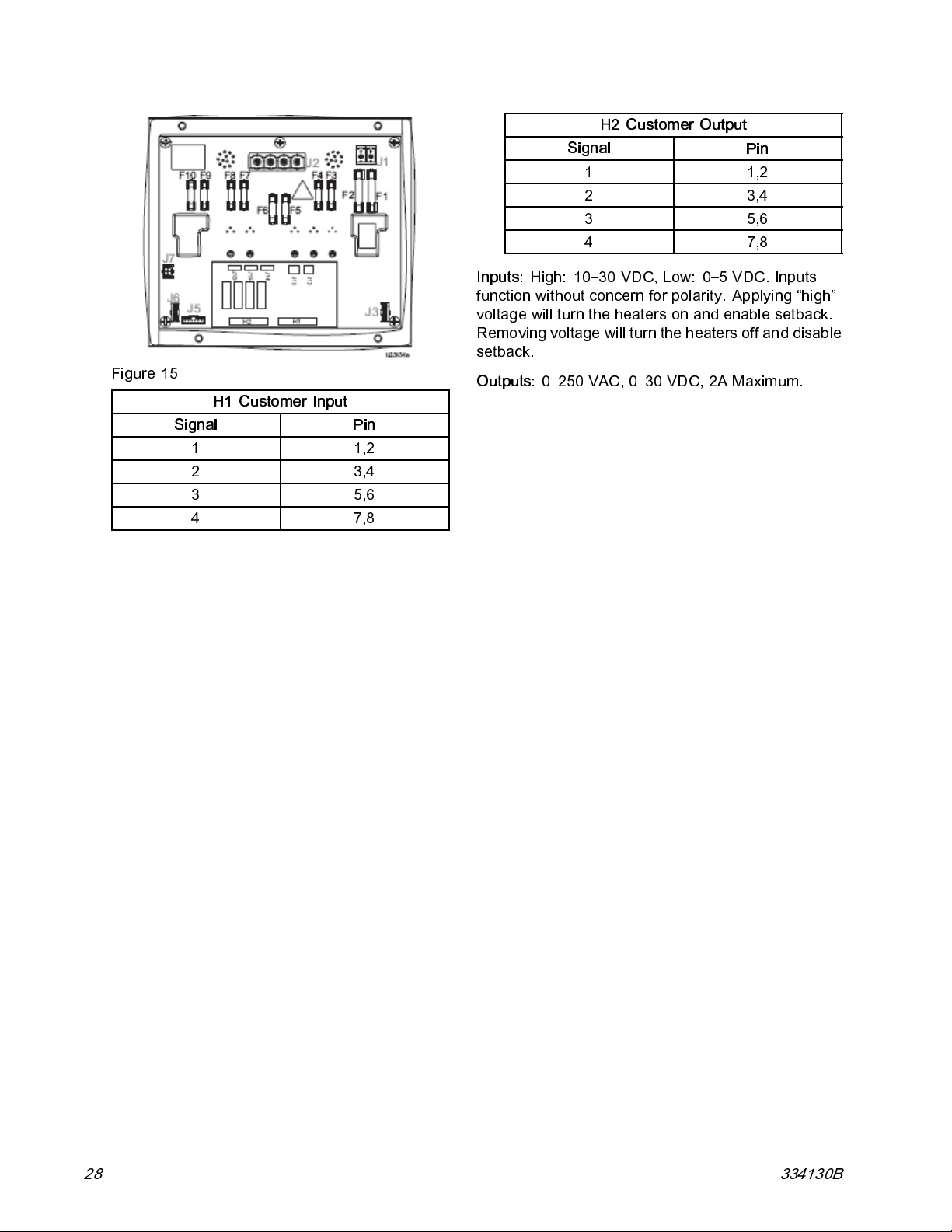
Setup
H2 Customer Output
Signal
11,2
23,4
35,6
47,8
Pin
Figure 15
Inputs:
function without concern for polarity. Applying “high”
voltage will turn the heaters on and enable setback.
Removing voltage will turn the heaters off and disable
setback.
Outputs:
H1 Customer Input
Signal
11,2
23,4
35,6
47,8
Pin
High: 10–30 VDC, Low: 0–5 VDC. Inputs
0–250VAC,0–30VDC,2AMaximum.
28 334130B
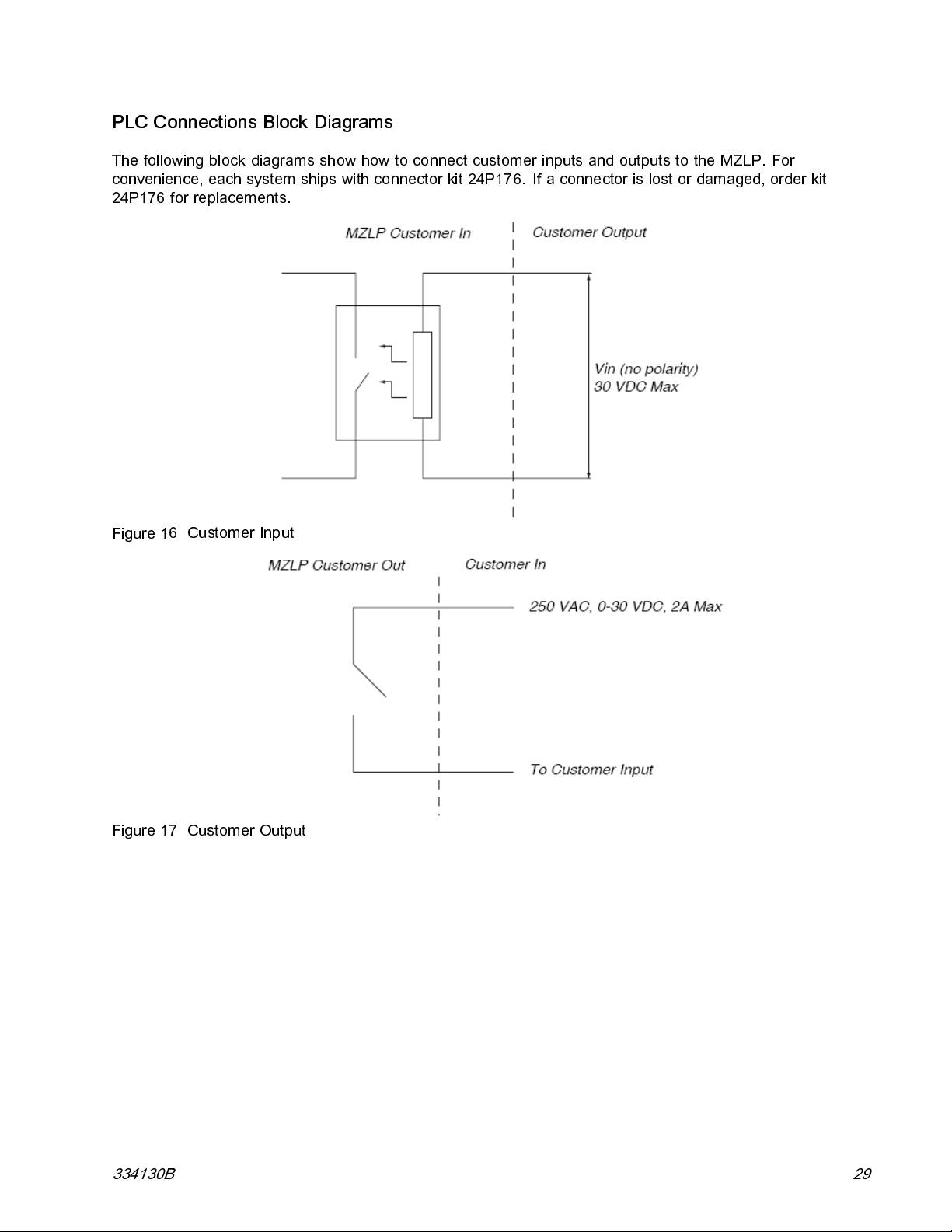
PLC Connections Block Diagrams
The following block diagrams show how to connect customer inputs and outputs to the MZLP. For
convenience, each system ships with connector kit 24P176. If a connector is lost or damaged, order kit
24P176 for replaceme nts.
Setup
Figure 1
Figure 17 Customer Output
6 Customer Input
334130B 29
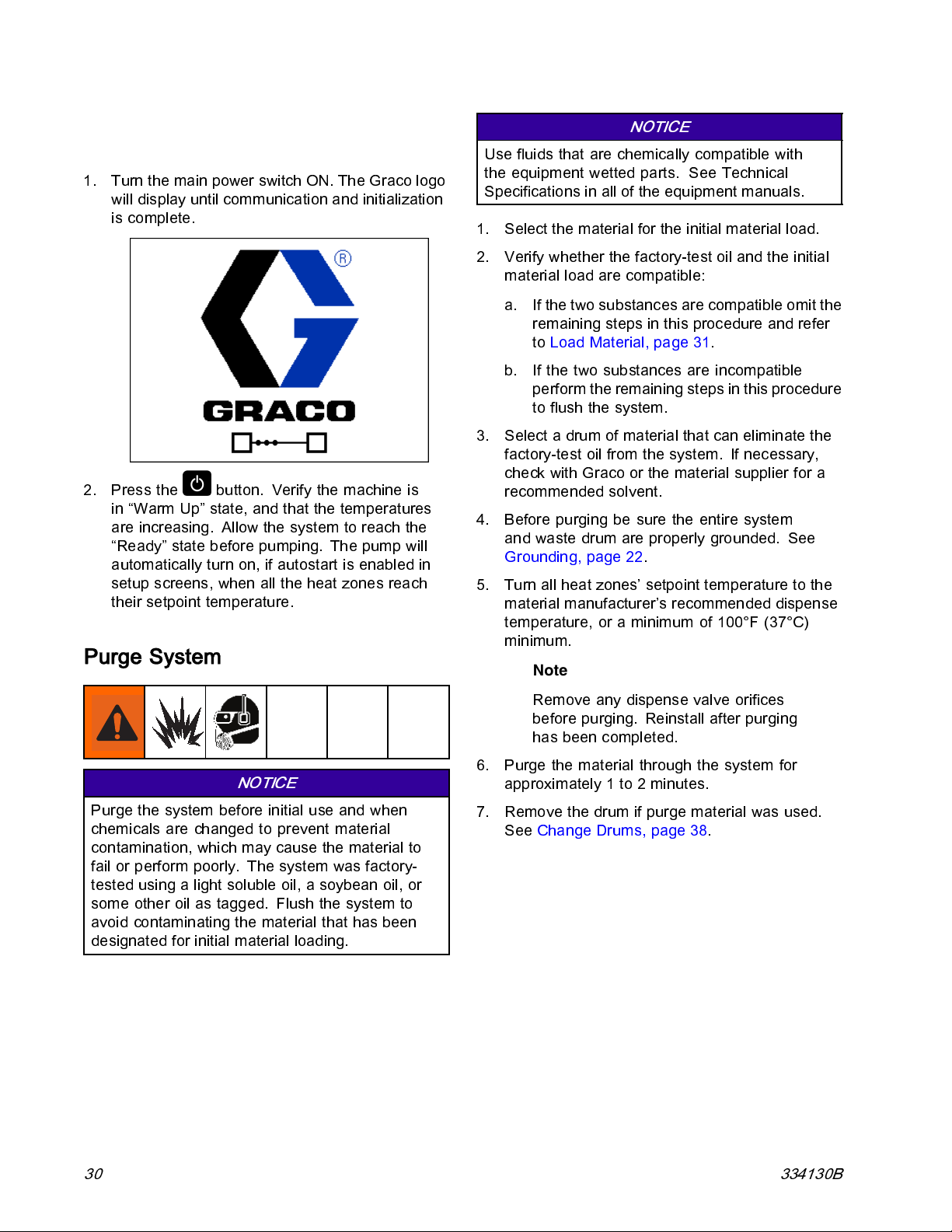
Operation
Operation
1. Turn the main power switch ON. The Graco logo
will display until communication and initialization
is complete.
2. Press the button. Verify the machine is
in “Warm Up” state, and that the temperatures
are increasing. Allow the system to reach the
“Ready” state before pumping. The pump will
automatically turn on, if autostart is enabled in
setup screens, when all the heat zones reach
their setpoint temperature.
Purge System
NOTICE
Use fluids that are chemically compa tible with
the equipment wetted parts. See Technical
Specifications in all of th e equipment manuals.
1. Select the material for the initial material load.
2. Verify whether the factory-test oil and the initial
material load are compatible:
a. If the two substances are compatible omit the
remaining steps in this procedure and refer
to Load Material, page 31.
b. If the two substances are incompatible
perform the remaining steps in this procedure
to flush the system.
3. Select a drum of material that can eliminate the
factory-test oil from the system. If necessary,
check with Graco or the material supplier for a
recommended solvent.
4. Beforepurgingbesuretheentiresystem
and waste drum are properly grounded. See
Grounding, page 22.
5. Turn all heat zones’ setpoint temperature to the
material manufacturer’s recommended dispense
temperature, or a minimum of 100°F (37°C)
minimum.
Note
NOTIC
Purge the system before initial use and when
chemicals are changed to prevent material
contamination, which may cause the material to
fail or perform poorly. The system was factory-
tested using a light soluble oil, a soybean oil, or
some other oil as tagged. Flush the system to
avoid contaminating the material that has been
designated for initial material loading.
E
Remove any dispense valve orifices
before purging. Reinstall after purging
has been completed.
6. Purge the material through the system for
approximately 1 to 2 minutes.
7. Remove the drum if purge material was used.
See Change Drums, page 38.
30 334130B

Operation
Load Material
NOTICE
To prevent damage to platen wipers, do not use a
drum of material that has been dented or damaged.
An empty drum clamp can interfere with up and
down operation of the ram.
ram, make sure the drum clamp stays clear of the
platen.
Note
Before loading material, make sure there is a
minimum overhead clearance of 110 in. (280
cm) and all air regulators are backed off to
their full counterclockwise position.
1. Open the main air slider valve (CA).
When raising the
4. Fill displacement pump wet cup 2/3 full with
Graco Throat Seal Liquid (TSL™) for Butyl and
PSA materials.
Note
Use IsoGuard Select® (IGS) (part
no. 24D086) for PUR or reactive
Polyurethane material. IGS is
designed to dissolve and suspend the
Polyurethane materials. IGS will solidify
after a period of time and should be
replaced once the solidified lube does
not return to liquid form after heating.
Figure 19 Wetcup
5. Open drum, remove any packing material, and
inspect material for any contamination.
2. Set ram director valve (CC) to UP and slowly
turn the ram up regulator (CD) clockwise until the
platen (G) begins to rise.
Figure 18 Raise the Platen
3. Apply a thin coating of high temperature grease
lubricant (part no. 115982) to the platen drum
seals.
6. Slide the drum between the drum centering
guides and against the stops at the back of the
ram baseplate.
Figure 20 Drum Placement
334130B 31

Operation
7. Remove the platen bleed stick (R).
Figure 21 Platen Bleed Handle
8. Set ram director valve (CC) to down.
Heat Up System
To reduce the risk of bursting a h ose, never
pressurize a hot melt system before turning on the
heat. The air will be locked from the air motor until
all temperature zones are within a preset window
of the temperature setpoints.
Keep the dispense valve open over a waste
container while the system is heating up and also
when cooling down. This will prevent a pressure
build-up caused by fluids or gases expanding from
the heat.
Note
Operate at the lowest temperature and
pressure necessary for your application.
1. Turn the main power switch on the electrical
control panel door to the ON position.
Figure 22 Lower the Platen
9. Slowly turn the ram down air regulator (CB)
clockwise to approximately 5–10 psi (34–69 kpa,
0.3–0.7 bar). The platen will begin to lower into
the drum.
10. After the platen seals enter the material drum,
adjust the ram down air regulator (CB) to 30–50
psi (207–345 kPa, 2.1–3.4 bar).
11. When the ram stops, reinsert the platen bleed
stick (R) and hand tighten.
2. Press the button. The zones begin to
heat (provided they are enabled). Press
if the zones do not begin to heat.
Display status bar reads
temperature reaches setpoint, the display
status bar reads
the status will display in the status bar. See
Advanced Display Module (ADM), page 12,for
operation mode descriptions.
Note
The air will be locked from the air motor
until all temperature zones are within a
preset window of the temperature set
points, allowing the system to heat fully
and complete the material heat soak
period.
Heat Soak
Warm Up
.Whenheatison,
.When
32 334130B

Prime Pump
1. Ensure that the system has completed the heat
soak cycle. The display status bar should read
Active
.
2. Adjust the air motor air regulator (CK) to 0 psi.
Operation
5. Adjust the air motor air regulator (CK) to
approximately 20 psi (138 kPa, 1.38 bar).
3. Ensure air motor solenoid valve (CN) is on. The
indicator light on the solenoid connec tor will only
be on if “Ena ble Pump Autostart” is selected on
the System 1 Setup screen.
4. Adjust the air m otor slider valve (CM) to the open
position.
6. Place a waste container under the bleed stem
(Z). Using an adjustable wrench, open the bleed
stem counterclockwise 1/3 -1/2 turn.
334130B 33

Operation
7. If a new drum was installed and the unit is
equipped with proxi mity sensors, press the Pump
Ready button
material tracking.
8. Adjust the air motor air regulator (CK) up by 5 psi
(34 kPa, 0.3 bar). Never adjust the regulator by
more than 5 psi (34 kPa, 0.3 bar) increments.
Make sure the pump begins to cycle and heated
material flows from the bleed stem (Z) after
several cycles of the pump.
. Press pause button on
9. Prime the pump until it moves sm oothly in
both directions with no air popping or erratic
movement and close the main air slider valve
(CA).
10. Close the bleed stem (Z).
11. Press Play button
material tracking.
on home sc reen to enable
34 334130B

Operation
Prime System
1. Close the main air s lider valve (CA).
2. If using a manual gun, lock the dispense valve
trigger open by pulling and securing the trigger
using the trigger retainer (Z).
7. Close the main air slide r valve (CA) and release
trigger lock.
8. Engage trigger lock.
Figure 23 Trigger Lock Engaged
9. Press
10. Turn the air motor regulator to operating
pressure.
Note
The system is now ready to operate.
to engage material tracking.
Setback Mode
3. Place the dispense valve over a waste container.
4. Press the pause material tracking button
on home screen.
5. Slowly open the main air slider valve (CA).
6. Prime the system until a smooth flow of material
dispenses from each dispense valve.
Note
On initial system startup, the pump will
cycle until the hoses are filled. If a new
drum was p laced on the frame, the pump
will cycle until all air has been removed.
Set the ADM to setback mode if the system will only
be inactive for a few hours. This will reduce the time
system needs to return to setpoint temperatures.
1. Press
Note
The amount of time before the pump
is automatically placed in setback is
determined by the Pump Inactivity Timeout,
locatedonSystemSetupScreen1. See
Setup Screens, page 100.
to enter Setback Mode.
334130B 35

Operation
Pressure Relief Procedure
Follow the Pressure Relief Procedure
whenever you see this symbol.
This equipment stays pressurized until pressure
is manually relieved. To help prevent serious
injury from pressurized fluid, such as skin injection,
splashing fluid and moving parts, follow the
Pressure Relief Procedure when you stop spraying
and before cleaning, checking, or servicing
equipment.
Note
If using a different dispense applicator, see
the applicator manual for pressure relief
instructions.
1. Engage the trigger lock.
3. Set the ram director valve (CC) to the neutral
position.
4. Disengage the trigger lock.
Figure 24 Engaged
2. Close the system master air slider valve (CA).
Figure 25 Disengaged
5. Holdametalpartofthegunfirmlytoagrounded
metal pail. Trigger the gun to relieve pressure.
6. Engage the trigger lock.
7. Open all fluid drain valves in the system, having
a waste container ready to catch drainage.
Leave drain valve(s) open until you are ready to
dispense again.
8. If you suspect the tip or hose is clogged or
that pressure has not been fully relieved after
following the steps above, VERY SLOWLY
loosen hose end coupling to relieve pressure
gradually, then loosen completely. Clear hose
or tip obstruction.
36 334130B

Operation
Shutdown
1. Press to disable the heaters and pump.
The screen will say “Inactive”. If using the
Schedule function, the heaters and pump will be
disabled automatically at the set time. Only press
to disable the heating system before the
set time. If the heaters were manually disabled,
the Schedule function will automatically enable
them at the next set time.
Table 9 Schedule Screen Color Identification
Color Description
Green System on
Yellow Setback
Red System off
Gray Disabled
Set Schedule Times
Times are set using a 24–hour clock. Several on and
off times can be set each day.
Note
Do not perform step 2 if using the
Schedule function. Leave the power on.
2. Turn main power switch off.
Schedule
The Schedule function allows the user to specify
times when the system will automatically turn ON and
OFF the heaters and pump.
1. On the Schedule screen (in the Setup screens),
set the ON times for each day of the week.
2. Set the OFF times for each day of the week.
3. Set the setback times for each day of the week.
Enable Schedule Function
The Schedule function is automatically enabled
when values are entered in the Schedule screen. To
disable a scheduled event, navigate to the event and
press
The event will appear gray on the screen when it
is disabled. To re-enable an event, navigate to the
event and press
The event will appear red (system off), yellow (system
setback), or green (system on). If no events are
needed, turn the main powe r switch OFF to prevent
system from automatically enabling and disabling the
heaters.
.
.
Use the Schedule Function
At the end of the work day leave the main power
switch ON. The Schedule function will automatically
enable and disable the heaters and pump at the
specified times.
334130B 37

Operation
Change Drums
To prevent serious burns from dripping material,
never reach under the heated platen after the
platen is out of the drum.
Follow the procedure to change the drum on a fully
heated system.
NOTICE
Be sure to reload the empty supply unit with a full
drum of material immediately.
and remove the platen from the empty drum until
you are ready to immediately install a new drum.
Do not raise the ram and remove the platen from
the empty drum unless the supply unit is at full
operating temperature.
performed when the system is heated.
An empty drum clamp can interfere with the up
and down operation of the ram.
lowering the ram, make sure the drum clamp stays
clear of the platen assembly.
Donotraisetheram
Drum changes can only be
When raising or
2. Push in the air motor slider valve (CM) to stop
the pump.
3. Set ram director valve (CC) to UP and raise the
platen (G) and immediately press and hold the
blowoff buttons (CG) until the platen is completely
out of the drum. Use minimum amount of air
pressure necessary to push the platen out of the
drum.
Do not use a drum of material that has been
dented or otherwise damaged;
platen wipers can result.
All systems include Low/Empty Sensors:
• The air will shutoff to prevent the pump from
cavitation. If the light tower kit is installed, a solid
red light indicates that th e pail is empty and ready
to change.
• In a tandem system, a flashing red light means
that both drums are empty and the system has
shutdown.
1. Press
to stop material tracking.
damage to the
Excessive air pressure in the material drum
could cause the drum to rupture, causing
seriousinjury.Theplatenmustbefreetomove
out of the drum. Never use drum blowoff air
with a damaged drum.
4. Release the blowoff air button and allow the ram
to rise to its full height.
5. Remove the empty drum.
6. Inspect platen and if necessary, remove any
remaining material or material build-up.
7. Follow steps in Load Material, page 31, and
Prime Pump, page 33.
38 334130B
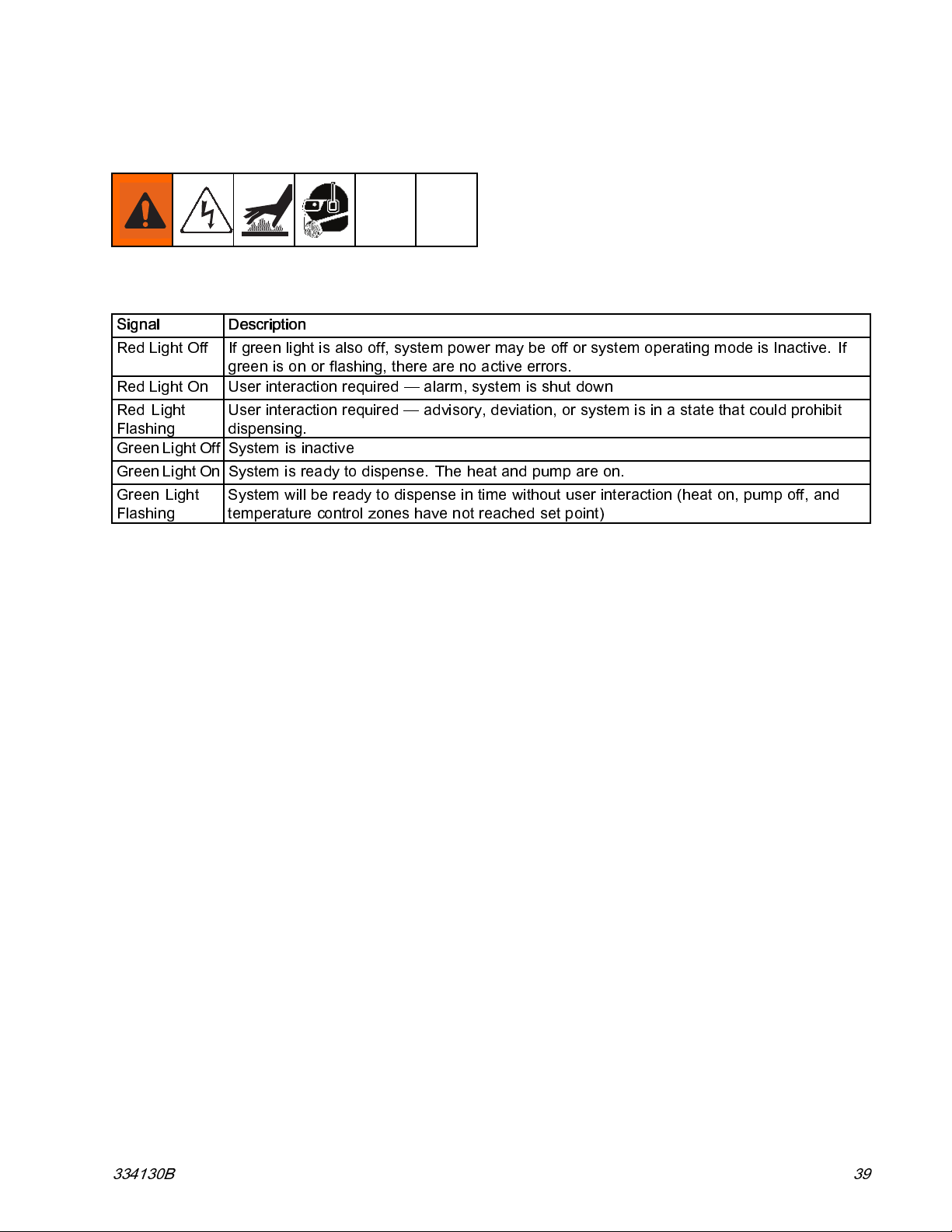
Troubleshooting
Light Tower (Optional)
Troubleshooting
Signal
Red Light Off If green light is also off, system power may be off or system operating mode is Inactive. If
Red Light On User interaction required — alarm, system is shut down
Red Light
Flashing
Green Light Off System is inactive
Green Light On System is ready to dispense. The heat and pump are on.
Green Light
Flashing
Description
green is on or flashing, there are no active errors.
User interaction required — advisory, deviation, or system is in a state that could prohibit
dispensing.
System will be ready to dispense in time without user interaction (heat on, pump off, and
temperature control zones have not reached set point)
334130B 39

Troubleshooting
Error Codes
There are three types of errors that can occur. Errors
are indicated on the display as well as by the optional
light tower.
Alarms are indicated by
a parameter critical to the process has reached a
level requiring the system to stop. The alarm needs
to be addressed immediately.
Deviations are indicated by
indicates a parameter critical to the process has
reached a level requiring attention, but not sufficien t
enough to stop the system at this time.
Advisories are indicated by
indicates a parameter that is not immediately critical
to the process. The advisory needs attention to
prevent more serious issues in the future.
To acknowledge the error, press
The thi
code, i
“
multi
rd digit, or sometimes the last digit of the error
ndicates which unit the error is active on. The
tar) character indicates the code applies to
★
”(s
ple system components.
Third or Last Digit “
AUnitA
BUnitB
★
. This condition indicates
. This condition
. This condition
.
” Codes Relates To:
The last digit of the error code indica tes which
system component the error applies. The “#” (pound)
character indicates the code applies to multiple
system components.
Last Digit “#” Codes Relates To
System Component:
1MZLP1
2MZLP2
3MZLP3
5
6MZLP6
7
VAWBUnitA
WAWBUnitB
X Daughter Board Unit A
Y Daughter Board Unit B
The last digit of the error code indica tes which
heat zone the error applies. The “_” (underscore)
character indicates the code applies to multiple
system components.
Last Digit “_” Codes Relates To Heat
1Zone1
2Zone2
3Zone3
4Zone4
5
6Zone6
7
8Zone8
9Zone9
AZone10
BZone11
CZone12
D Pump
EPlaten
MZLP 5
MZLP 7
Zone:
Zone 5
Zone 7
40 334130B

Troubleshooting
Code
A3MF
A4C# High Current
A8★_
A8C
AM3 # High Current
AM4 # High Current
AM8# No Cu rrent
CAC# Comm Error
CACX
CACY
Description Type
AWB Clean Fan
Filter
Unit _ Zone _
Fan AWB, Unit
_
Unit _ Zone _
No Current Unit
_Zone_
AWB No Fan
★
Current
SSR MZLP _
Contactor
MZLP _
Contactor
MZLP _
MZLP _
DB Not Present
Unit A
DB Not Present
Unit B
Cause Solution
Alarm
Alarm Defective or
Deviation Fan is drawing
Alarm Unexpected
Alarm
Alarm
Alarm Excessive
Alarm
Alarm
Alarm
Alarm Daughter
Alarm Daughter
Cooling inlet
screen is dirty
shorted to
ground on
zone
too much
current
current flow to
zone
No Current
Flow to the
Zone
Cooling fan
not working
current flow
in the SSR
Defective or
shorted to
ground on
MZLP
No Current
Flow to the
Contactor
System not
responding to
ADM.
Board not
responding
Board not
responding
Clean inlet screen.
Verify accessory is rated for 240 VAC.A4★_ High Current
Verify heater resistance and check for shorts to
ground. Replace as necessary.
Verify there is not an air obstruction at the inlet/ou tlet
of enclosure. verify nothing is preventing fan rotation.
Replace fan if necessary.
Replace MZLP.A7★_ Unexp. Curr.
Faulty accessory heater. Measure resistance to
ground between heater leads.
Check for loose or disconnected wires or plugs.
Check for blown fuses on MZLP.
Check heater resistance for open circuit.
Check for shorts between heater and ground.
Verify cable is plugged into zones 3–4. Replace
heater if necessary.
Verify fan is plugged in. Replace if necessary.
Check for shorts in harness to SSR. Check polarity of
wiring to SSR. Replace if necessary.
Check for shorts in the harness to contactor. Check
the polarity to contactor. Replace contactor i f
necessary.
Ensure harness to MZLP is connected. Ensure wiring
to contactor is secure. Replace contactor if necessary.
System is not properly loaded with correct Software.
Dial not set correct on MZLP. Duplicate MZLP dial
positions (i.e. 1 to 1, 2 to 2, ect)
Check all CAN connections between the ADM and
missing MZLP.
Check if hardware exists on the network.
Replace MZLP if necessary.
Dial not set correct on MZLP 5. Set to 5 on board with
daughter board.
Ensure connections between the ADM an d hardware
are secure.
Replace Daughter Board.
Dial not set correct on MZLP . Set to 4 on board with
daughter board.
Ensure connections between the ADM an d hardware
are secure.
Replace Daughter Board.
334130B
41

Troubleshooting
Code
CACV
CACW
DA★X Pump Runaway
DE★X
DC★X
L1★X Material Level
L2★X Material Level
L3★X Material Level
MMUX
MN★XPump_
Description Type
AWB not
present Unit
A
AWB not
present Unit
B
Detected
Reed Switch
Failure
Detected
Pump Diving Alarm
Sensor Error
Empty
Low
USB Log Full
Requires
Maintenance
Cause Solution
Alarm AWB not
responding
Alarm AWB not
responding
Alarm
Alarm Reed switch
Alarm Machine is
Alarm Material drum
Deviation Material level
Advisory
Advisory User defined
Pump is
trying to feed
adhesive, no
adhesive to
feed.
Worn or
damaged
pump seals
failed
Pump is
trying to feed
adhesive, no
adhesive to
feed.
Worn or
damaged
pump seals
detecting an
empty state
without a low
state
is empty
is low
USB logs fulls.
Data loss will
occur if not
downloaded.
pump
maintenance
counter has
run out
Ensure connections between the ADM and hardware
are secure.
If a tandem system, ensure AWB 2 jumper is instal led
at startup.
Replace AWB.
AWB 2 jumper was not in place at start up
Ensure connections between the ADM and hardware
are secure.
Replace AWB.
Adjust the drum empty level sensor to detect an
empty state.
Ensure the ram director valve is in the down position
and sufficient air is forcing the ram down.
Melter at incorrect temperature, too low. Check
setpoint and set to manufactures recommendation.
Inspect pump seals and replace if necessary
Check that sensor cable is plugged into the daughter
board at J16.
Check for loose connection at reed switch. Ensure
reed switch is securely attached to the air motor.
Replace if necessary.
Adjust the drum empty level sensor to detect an
empty state.
Ensure the ram director valve is in the down position
and sufficient air is forcing the ram down.
Melter at incorrect temperature, too low. Check
setpoint and set to manufactures recommendation.
Inspect pump seals and replace if necessary
Make sure the empty level sensor is not covered in
material
Verify the low level sensor is plugged into J15 of the
daughter board. Verify the low level sensor is close
enough to the metal bar; adjust if necessary.
Replace sensors.
Replace material container. If more material is
leftover, lower the empty level sensor.
Replace at appropriate time.
Download USB data o r disable the USB l og errors on
theAdvancedscreen3.
Perform pump maintenance, then reset the counter
on the maintenance setup screen.
42
334130B

Troubleshooting
Code
T1★_ Low Temp. Unit
T2★_ Low Temp. Unit
T3★_HighTemp.
T4C#
T4M#
T4★_HighTemp.
T6★_
T6C#
T8V _ No Temp. Rise
V1I# Low CAN
Description Type
_Zone_
_Zone_
Unit _ Zone _
AWB
Temperature
Runaway
Transformer
AWB High
Transformer
Temp
Unit _ Zone _
Sensor Err. Unit
_Zone_
AWB Invalid
Thermistor
Reading
Unit _ Zone _
Voltage, MZLP
_
Cause Solution
Alarm Zone
temperature
too low
Deviation Zone
temperature
too low
Deviation Temperature
reading has
risen too high
Alarm
Alarm
Alarm Temperature
Alarm Bad RTD
Alarm
Alarm Temperature
Alarm Bad or
Cooling fan
not working
or inlet is
blocked/dirty
Transformer
Temperature
is too High
reading has
risen too high
Reading
Transformer
thermistor
temperature
is incorrect
reading does
not change.
overloaded
power supply
Reduce flow rate.
Increase temperature of accessory upstream.
Faulty accessory heater measure resistance between
heater leads.
Change Low Temp Alarm.
Replace accessory.
Reduce flow rate.
Change Low Temp Alarm.
Add zone (temperature) upstream.
ChangeHighTempAlarm.
Verify setpoint upstream is not hotter than this zone’s
setpoint.
Ensure inlet and outlets are not obstructed.
Verify fan is plugged in.
Ensure inlet and outlets are not obstructed.
Verify fan is plugged in.
ChangeHighTempAlarm.
Verify setpoint upstream is not hotter than this zone’s
setpoint.
Check RTD wiring and harness/connector integrity.
Replace RTD.
Verify thermister is securely connected to J7 of the
AWB. Replace transformer if necessary.
Check fuses on MZLP conne cted to that Zone.
Check wiring to device.
Check heater resistance on device.
Verify power supply voltage is 24 VDC. If voltage is
low, disconnect the power lines and re-check voltage
reading. If voltage is still low, replace power supply. If
voltage is correct after disconnecting the power lines.
Connect items one at a time until the voltage drops
to isolate the bad module.
V1M# Low Voltage
Line AWB, Unit
_
V4I# High CAN
Voltage, MZLP
_
334130B 43
Deviation The voltage
to the AWB
is below
threshold
Alarm Bad or
overloaded
power supply
Verify transformer voltage top matches incoming
voltage. Verify incoming voltage is correct.
Verify power supply voltage is 24 VDC. If voltage is
high, replace power supply unit.

Troubleshooting
Code
V6M#
V8M#
WJ1
WJ2
WSUX Configuration
Description Type
Wiring Error
Line MZLP _
No Line Voltage
MZLP _
AWB High Line
Voltage
★
Pump _
Solenoid is
disconnected
★
Pump _
Solenoid High
Current
Error USB
Cause Solution
Alarm Incoming
power is wired
incorrectly
Alarm Incoming line
voltage is less
than 100 VAC.
Alarm Incoming
voltage is too
high
Alarm Pump is not
turning on
when it should
Alarm
Advisory
Solenoid is
drawing too
much current
USB
configuration
is not loaded
Correct the Wiring.
Verify transformer has the correct tap selected.
Verify CB-1 or FU-4, FU-5, and FU-6 are not
tripped/blown.
Verify RCD-1 is not tripped.
Measure incoming power with system unplugged. If
line voltage is less than 100 VAC, contact qualified
electrician to correct the low voltage.
Verify the MZLP is plugged in at J2 and the AWB is
plugged in at J5 and J6.
Check incoming voltage is correct for configuration.V4M#
Verify the transformer has the correct tap (400, 4 8 0,
600) selected.
Verify harness is plugged into J13 of the daughter
board. Verify it is secured to the solenoid.
Replace Solenoid.
Inspect for short in harness. Inspect for a shorted
solenoid cable/short to the ground. Replace solenoid.
Install software.
44
334130B

Ram Troubleshooting
Troubleshooting
Problem
Ram will not raise or lower.
Ram raises or lowe rs too fast.
Air leaks around cylinder rod. Worn rod seal.
Pump will not prime properly, or
pumps air.
Air pressure will not push platen out
of drum.
Closed main air valve or clogged air
line,
Not enough ram air pressure. Increase ram air pressure.
Worn or damaged ram piston.
Platen not fully up to temperature. Wait for full temperature.
Ram air pressure too high. Decrease ram air pressure.
Dented drum has stopped platen. Fix or replace drum.
Ram "up / down" air pressure too
high.
Ram air pressure too high. Decrease ram air pressure.Fluid squeezes past platen wipers.
Worn or damaged wipers. Replace wipers.
Closed main air valve or clogged air
line.
Not enough air pressure. Increase air pressure.
Worn or damaged ram piston.
Ram directional valve closed or
clogged.
Ram directional valve dirty, worn, or
damaged.
Directional valve not in the down
position.
Dented drum has stopped platen. Fix or replace drum.
Closed main air valve or clogged air
line.
Platen not fully up to temperature. Wait for full temperature.
Not enough blow-off air pressure. Increase blow-off air pressure.
Blow-off valve passage clogged. Clean valve passage.
Dented drum has stopped platen. Fix or replace drum.
Wipers bonded to drum or drum liner. Lubricate wipers with high
Cause Solution
Open air valve; clear air line.
Replace piston. See instruction
manual 310523.
Decrease ram air pressure.
Replace o-rings in guide sleeve. See
instruction manual 310523.
Open air valve; clear air line.
Replace piston. See instruction
manual 310523.
Open valve; clear valve or exhaust.
Clean; repair valve.
Position handle in the down position.
Open air valve; clear air line.
temperature grease at every
drum change.
334130B 45
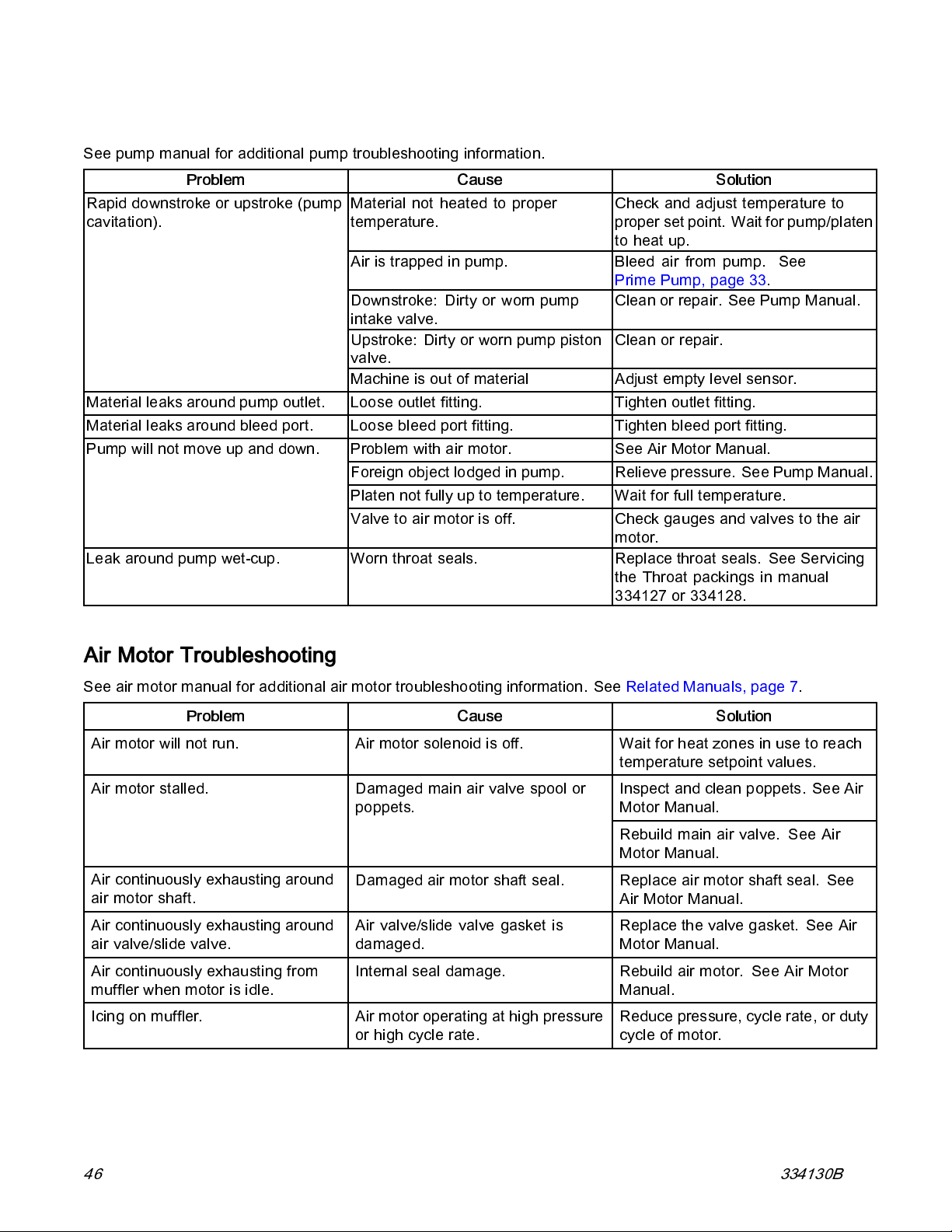
Troubleshooting
Heated Pump Troubleshooting
See pump manual for additional pump troubleshooting information.
Problem
Rapid downstroke or upstroke (pump
cavitation).
Material leaks around pump outlet.
Material leaks around bleed port.
Pump will not move up and down.
Leak around pump wet-cup. Worn throat seals.
Material not heated to proper
temperature.
Air is trapped in pump. Bleed air from pump. See
Downstroke: Dirty or worn pump
intake valve.
Upstroke: Dirty or worn pump piston
valve.
Machine is out of material
Loose outlet fitting. Tighten outlet fitting.
Loose bleed port fitting. Tighten bleed port fitting.
Problem with air motor.
Foreign object lodged in pump.
Platen not fully up to temperature. Wait for full temperature.
Valve to air motor is off. Check gauges and valves to the air
Cause Solution
Check and adjust temperature to
proper set point. Wait for pump/platen
to heat up.
Prime Pump, page 33.
Clean or repair. See Pump Manual.
Clean or repair.
Adjust empty level sensor.
See Air Motor Manual.
Relieve pressure. See Pump Manual.
motor.
Replace throat seals. See Servicing
the Throat packings in manual
334127 or 334128.
Air Motor Troubleshooting
See air motor manual for additional air motor troubleshooting information. See Related Manuals, page 7.
Problem
Air motor will not run.
Air motor stalled. Damaged main air valve spool or
Air continuously exhausting around
air motor shaft.
Air continuously exhausting around
air valve/slide valve.
Air continuously exhausting from
muffler when motor is idle.
Icing on muffler.
Air motor solenoid is off. Wait for heat zones in use to reach
poppets.
Damaged air motor shaft seal. Replace air motor shaft seal. See
Air valve/slide valve gasket is
damaged.
Internal seal damage.
Air motor operati n g at high pressure
or high cycle rate.
Cause Solution
temperature setpoint values.
Inspect and clean poppets. See Air
Motor Manual.
Rebuild main air valve. See Air
Motor Manual.
Air Motor Manual.
Replace the valve gasket. See Air
Motor Manual.
Rebuildairmotor. SeeAirMotor
Manual.
Reduce pressure, cycle rate, or duty
cycle of motor.
46 334130B

Repair
Repair
Replace Wipers
1. To replace a worn or damaged wiper (V) raise
the ram plate up out of the drum. Perform steps
1 through 7 of ChangeDrums,page38.See
wiper kit manual for instru ctions about replacing
the wipers.
2. Makesuretheramplateisdownandtheram
hand valve is in the OFF position.
To reduce the risk of injury or damage to
equipment, make sure the main power switch
is off before continuing with this procedure.
3. Turn the main power switch off.
Figure
26 Replace Wiper
Replace Platen RTD
rence Electrical Schematics, page 60 for wiring
Refe
ections.
conn
1. If the material drum has already been removed
from the supply unit, go to step 2. If you
need to remove the material drum, see
Change Drums, page 38.
4. Remove the pump cover.
Figure 27 Pump Covers and Platen RTD
5. Remove the platen RTD (605) from the platen.
334130B
47

Repair
6. Disconnect the platen RTD wires from pin 3 and
pin 6 from the J5 connector on the AWB.
Figure 28 RTD Wire Connections
2760 Red
2770 White
2790 White
7. Attach the leads from the new sensor to the leads
of the old sensor and pull the new sensor leads
through the cable pump shield, cable track, and
into the electrical enclosure.
8. Install the new sensor (605) into the follower/tire
plate after coating with non-silicone heat sink
compound. Tighten compression nut. Ensure
RTD is fully inserted.
2. Makesuretheramplateisdownandtheram
director valve (CC) is in the neutral position.
3. Follow Pressure Relief Procedure, page 36.
4. Bleed off excess material and pressure in
the system by opening the dispense gun and
catching the material in a waste container.
5. On ADM, turn off the system heat (D).
6. Turn the main power switch off.
9. Connect the red and white wires from the new
sensor to the J5 connector on the AWB.
10. Replace the pump covers.
Separate the Air Motor and Pump
This procedure must be done with the unit still
warm. The material and equipment will be hot!
1. If the material drum has already been removed
from the supply unit, go to step 2. If you need
to remove the material drum, perform steps 1
through 6 of the Change Drums, page 38.Pump
must be in the full down position (air motor shaft
fully extended).
7. Disconnect all material hoses.
8. Remove the pump sheet metal enclosure.
a. Remove the cover screws.
b. Remove the heater bands and disconnect
the ground wire.
9. If vent hood is installed, remove it.
48 334130B

Repair
10. Remove the air motor top cover.
11. Disconnect electrical cable from air motor.
12. Remove air line from air motor and air lines to the
follower blow-off valve.
13. Tightly strap the air motor to the tie bar with a
cable through the air motor lift ring and around
the tie bar. See Fig 29, page 49
14. Loosen u-bolts (X) from platen lift rods.
15. Remove nuts (F) from pump/air motor stand-off
rods at the pump end.
16. Remove nuts (Z) and bolts holding cable tract to
air motor support plate.
17. Slide end of cable track outboard of the mou nting
plate.
18. Remove nuts (N) from follower lift rods.
19. Fully loosen pump rod coupler to the air motor
rod (G).
20. Slowly raise elevator to achieve enough
separation of the pump (air motor) tie rods to
remove the pump.
21. Remove the pump.
22. Reverse this procedure to reinstall the new or
rebuilt air motor.
334130B 49

Repair
Figure 29
Remove Platen
50 334130B
1. Turn the main power switch off.
2. Disconnect the platen power wires and the
ground wire from within the main control panel
and pull out of conduit.
3. Removetheplatenassemblyfromtheram.
4. Reverse this procedure to reinstall the new or
rebuilt platen assembly.

Repair
Replace Heater Bands and Pump
RTD
Replace Heater Band
1. If the material drum has already been removed
from the supply unit, go to step 2. If you need
to remove the material drum, perform steps 1
through6oftheChange Drums, page 38.Pump
must be in the full down position (air motor shaft
fully extended).
2. Make sure the ram plate is down and the ram
hand valve is in the neutral position.
8. Remove white ceramic caps and disconnect the
electrical wires from heater band (309).
9. Remove the screw that holds the heater band
in place.
10. Remove the heat er band (309a, 309b) from
pump.
11. Coat the inside of the heater with non silicone
heat sink compound before mounting. Maximum
thickness is 0.005 in. Coat only to within 3/4 in.
of vertical ends.
12. Install a new heater band (309a, 30 9b) in the
same location as the old heater band:
a. Locate heater terminals so they line up with
back of pump.
b. Tighten the heater band.
c. Re-connect heater wires and re-attach
ceramic caps that insulate terminal.
3. Follow Pressure Relief Procedure, page 36.
4. Bleed off excess material and pressure in the
system by opening the applicator and catching
the material in a waste container.
5. On ADM, turn off the system heat (D).
6. Turn the main power switch off.
7. Remove the screws and covers.
Figure 30
334130B 51

Repair
Replace Pump RTD
1. Turn the main power switch off.
2. Remove the screws that hold the front shroud in
place and remove front shroud.
3. If sensor wire is connected to electrical enclosure,
disconnect it.
4. Loosen the c lamp (321) holding sensor on pump.
5. Tie the leads of the new sensor (320) to the old
sensor and remove the old sensor. The leads of
the new sensor will b e easily drawn through the
conduit for reconnecting.
6. Replace the sensor (320) in clamp (321):
a. Place sensor approximately 30° counter
clock-wise from pump outlet.
b. Tighten clamp (321).
7. Re-connect sensor wire to electrical enclosure.
Fuse Kit Fuse Part
24V289
To prevent system damage, always use fast
acting fuses. Fast acting fuses are required for
short-circuit protection.
1. Turn the main power switch off.
2. Open electrical enclosure door.
3. Use a proper non-conductive fuse puller tool to
F1, F2
F3-F10 250VAC, 8A, fast acting, clear
Spare fuse kit included with system.
remove the blown fuse.
Using an improper tool, such as screw drivers
or pliers, may break g lass on fuse.
250VAC, 25A, long, white
ceramic
glass
NOTICE
NOTICE
Replace MZLP Fuse
Each MZLP module comes with the following fuses:
J1
F1
J3
J7
J6
F10
J5
F9
F8
F7
F6
F5
J2
F4
F3
F2
Note
F1andF2arewhiteceramicandindicate
25A on the barrel.
Note
F3-F10 are clear glass and indicate 8A
on the barrel.
4. Use a proper non-conductive fuse puller tool to
install the new fuse
NOTICE
Using an improper tool, such as screw drivers
or pliers, may break g lass on fuse.
5. Close electrical enclosure.
Figure 31 Fuse Locations
52 334130B

Repair
Replace MZLP
1. Turn the main power switch off.
2. Disconnect heated hose electrical connectors
from MZLP (111 or 112).
3. Note location of each cable, then unplug all
cables from the MZLP (111 or 112) that will be
replaced.
4. Remove four screws (115) securing MZLP (111
or 112) to electrical enclosure then carefully
remove MZLP from electrical enclosure.
b. To replace MZLP #2 or #33, remove the
jumper(162)fromMZLP#2or#3J5
connector and reinstall it on the new MZLP
J5 connector.
6. To reassemble MZLP, Set MZLP rotary switch
based on location. See
Table
.
7. Use four screws (115) to install MZLP (111 or
112) to electrical enclosure.
8. Reconnect cables to MZLP.
Note
Do not force the electrical connection.
Minimal force is required to seat the
connector. If resistance is felt, stop and
verify the connector orientation.
Note
If unable to determine connector location,
see Electrical Schematics, page 60.
9. Connect heated hose electrical connectors to
new MZLP.
MZLP Rotary Switch
Figure 32 MZLP Identification
5. Replace MZLP.
a. To replace MZLP #1, remove the daughter
card and standoffs, and re-install them on
the new MZLP #1.
Note
MZLP may need updated software. See
Update Software, page 59.
Table10MZLPRotarySwitch
MZLP
#1 with
Daughter Card
#2
#3
System Rotary Switch
Primary 1
Secondary
Primary 3
Secondary
Primary 4
Secondary
5
6
7
334130B 53

Repair
Replace MZLP Daughter Card
1. Turn the main power switch off.
2. Note location of each cable then unplug all cables
from MZLP daughter card on MZLP#1 (112).
3. Remove four mounting screws (112b) from
daughter card (112a) and set aside.
4. Unplug daughter card (112a) from the MZLP
#1 (112).
5. Plug new daughter card (112a) into the
MZLP (112).
6. Use screws (112b) to secure daughter card to
MZLP (112).
7. Connect cables to new daughter card (112a).
Note
Do not force the electrical connection.
Minimal force is required to seat the
connector. If resistance is felt, stop and
verify the connector orientation.
Note
If unable to determine connector location,
see Electrical Schematics, page 60.
Figure 33 MZLP Daughter Card
54 334130B
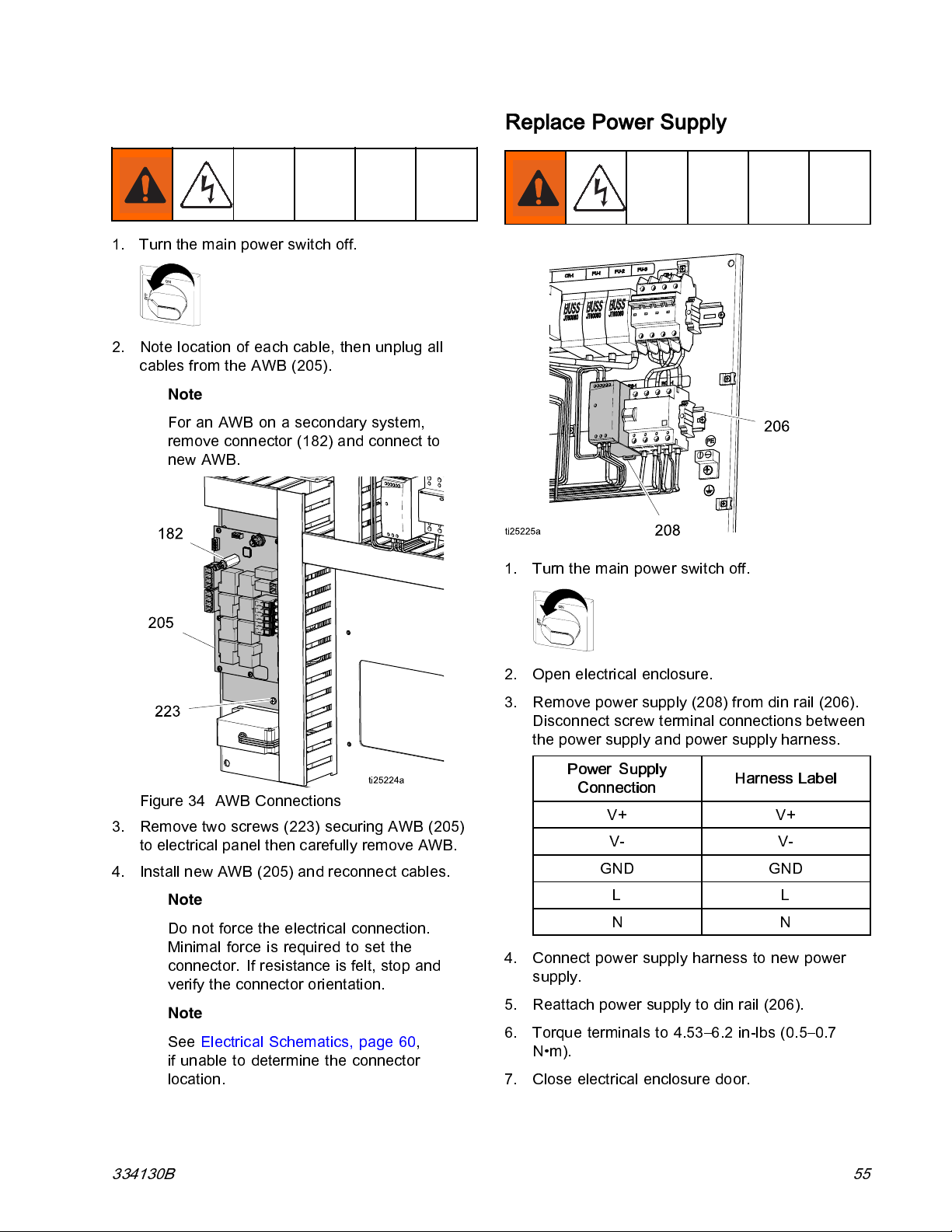
Repair
Replace AWB
1. Turn the main power switch off.
2. Note location of each cable, then unplug all
cables from the AWB (205).
Note
For an AWB on a secondary system,
remove connector (182) and connect to
new AWB.
Replace Power Supply
1. Turn the main power switch off.
Figure 34 AWB Connections
3. Remove two screws (223) securing AWB (205)
to electrical panel t hen carefully remove AWB.
4. Install new AWB (205) and reconnect cables.
Note
Do not force the electrical connection.
Minimal force is required to set the
connector. If resistance is felt, stop and
verify the connector orientation.
Note
See Electrical Schematics, page 60,
if unable to determine the connecto r
location.
2. Open electrical enclosure.
3. Remove power supply (208) from din rail (206).
Disconnect screw terminal connections between
the power supply and power supply harness.
Power Supply
Connection
V+ V+
V- V-
GND GND
LL
NN
4. Connect power supply harness to new power
supply.
5. Reattach power supply to din rail (206).
6. Torque terminals to 4.53–6.2 in-lbs (0.5–0.7
N•m).
7. Close electrical enclosure door.
Harness Label
334130B 55

Repair
Replace Fan
1. Turn the main power switch off.
2. Disconnect plug from power outlet or turn off
circuit breaker for incoming power.
3. Open electrical enclosure door.
4. Remove connector from J7 connector on AWB
board. Remove red (+) and black (-) fan wires
from connector.
6. Remove screws (141), grill (137), four nuts (139),
rear fan grill (138), and fan (136).
7. Mount new fan (136), rear fan grill (138), and
nuts (139) on grill (137) with the arrow pointing
toward the grill (137).
8. Tie down fan wires onto tie down locations on
grill (137) using cable zip ties.
5. Cut any cable ties between the end of the fan
wirestothefan(136).
9. Route fan wires into the electrical enclosure.
Connect red and black fan wires to J7 connector.
Reconnect J7 connector to AWB. Use cable ties
to secure fan wires to other cables in electrical
enclosure.
Note
To prevent fan errors on ADM, remove
excess slack and ensure cabling and zip
ties do not contact fan blades.
10. Reinstall fan grill (137) and close the electrical
enclosure.
56 334130B

Repair
Replace Transformer
See Fig 35, page 57.
1. Turn the main power switch off.
2. Open electrical enclosure door.
3. Disconnect incoming power harness (234) from
top of transformer (235).
4. Disconnect transformer (235) output power
harness wires (RCD-W1, -W2, -W3, -W4) from
RCD-1.
5. Disconnect transformer (235) ground wire from
the back panel ground lug.
6. Disconnect the red (+) and black (-) wire of fan
from pins 4 and 3 of J7 connector on AWB (205).
Disconnect J7 connector from AWB.
13. Connect transformer output power harness (234)
to power terminal connections. Torque to 25–27
in-lbs (2.8–3.1 N•m).
Table 11 Transformer Output Power Harness
Connections
Power Harness Wires
RCD-W1
RCD-W2
RCD-W3 Terminal 3
RCD-W4
14. Install incoming power harness (234) to top of
transformer in voltage port specified on machine
serial number label.
RCD-1 Connections
Terminal N
Terminal 5
Terminal 1
7. Cut wire zip ties securing fan wires.
8. Remove flanged nuts (N) an d transformer (235)
from the back panel (201).
9. Install transformer (235) onto mounting studs on
back panel (201) and secure with flanged nuts
(N).
10. Insert thermal sensor connector from transformer
(235) onto J7 connector on AWB (205).
11.Reconnectred(+)wirefromfanintopin4and
theblack(-)wireintopin3ofJ7connector.
12. Install transformer (235) ground wire onto ground
lug of back panel (201).
15. Verify all electrical connections, including earth
grounds, are compete and tight. All connections
and plugs must be connected prior to applying
power.
16. Close the electrical control panel door.
17. Apply power to the machine. Turn on the main
power switch.
18. Restart the system.
334130B 57

Repair
Figure 35 Inside of Electrical Control Enclosure
58 334130B

Repair
Update Software
When software is updated on the ADM the software
is then automatically updated on all connected
GCA components. A status screen is shown while
software is updating to indicate progress.
1. Turn system main power s witch OFF.
2. RemoveADMfrombracket.
3. Remove token access panel.
4. Insert and press software upgrade token (T)
firmly into slot.
First:
Software is checking
which GCA modules
will take the available
updates.
Second:
Status of the update
with approximate time
until completion.
Third:
Updates are
complete. Icon
indicates update
success/failure. S e e
the following Icon
table.
Icon Description
Update successful.
Note
There is no preferred orientation of token
T
5. Install ADM into bracket.
6. Turn system main power switch ON.
NOTICE
A status is shown while software is updating to
indicate progress. To prevent corrupting the
software load, do not remove token until the
status screen disappears.
Note
When the screen turns on, you will see
the following screens:
Update unsuccessful.
Update complete, no
changes necessary.
Update was
successful/complete
but one or more HCA
modules did not have
a CAN boot-loader
so software was
not updated on that
module.
7. Remove token (T).
8. Replace token access panel.
9. Press
to continue to the operation screens.
334130B 59

Electrical Schematics
Electrical Schematics
230V, 3 Phase/60 Hz
60 334130B

400V, 3 Phase/50 Hz
Electrical Schematics
334130B 61

Electrical Schematics
400–600VV, 3 Phase/60 Hz
62 334130B

AWB and MZLP#1
Electrical Schematics
334130B 63

Electrical Schematics
MZLP #2, MZLP#3, Overtemp, and
Pump Heaters
64 334130B

MZLP Zones
Electrical Schematics
334130B 65

Parts
Parts
Therm-O-Flow 200 Supply Unit
66 334130B

Therm-O-Flow 200 Supply Unit
Parts
Part Description
Ref
1
2 24W870 KIT, air controls; see 1
3
4
5
6
7
8
9 24W812 ADM 1
10 24W589
11 253288 CABLE, track, IGUS 1
12 234966 KIT, hose hanger 1
13 24V745 SENSOR, level, low/empty 1
14 15H543 BRACKET, mounting 1
15 120186 BOLT, mounting, u-bolt 2
---
---
---
---
---
---
---
Frame 1
CONTROL, electrical
MODULE, pump; see
Pump Modules, page 76
PLATEN; see
Heated Platens, page 83
RAM; see ram manual 1
CLAMP, drum; see
Drum Ram Post Saddle
Clamp, page 86
SEALS, see manual
309196
KIT, light tower (optional);
see Accessories and Kits,
page 90
Qty
Ref
16 101864
17 111303 NUT, hex 4
18 100575
1
19 100023
1
20
1
21 100645
22 100016
1
23 110755
24 233559
1
25
1
26
27
28
29
Part Description
SCREW, cap, sch
SCREW, cap, hex hd
WASHER, flat
---
▲
15J076 LABEL, warning,
▲
15J074 LABEL, warning; moving
▲
15H668 LABEL, warning; hot
▲
15J075 LABEL, warning; hot
▲
184090 LABEL, warning 1
BRACKET, mounting,
enclosure
SCREW, cap, sch
WASHER, lock
WASHER, plain
KIT, vent hood (optional);
see Accessories and Kits,
page 90
instructions
objects, pinch
surface, splatter
surface, shock
Qty
8
4
4
1
4
4
4
1
2
4
2
2
▲
Replacement Warning labels, signs, tags, and
cards are available at no cost.
334130B 67

Parts
Air Control Assembly
Integrated Control For
TOF With Electrical Enclosure
Ref
51 24W870
52 121235
53 17A557
54 113445
55
56 120375 ADAPTER, elbow, 3/4–14
Part Description
KIT, CONTROL, air, 3
regulator; see manual
334201
SOLENOID, air motor, ram
HARNESS, solenoid,
MZLP
FITTING, elbow, street
121282
★
Partsonlyusedwith24X026onTOF200
Hydraulic Systems.
▲
Replacement Warning labels, signs, tags, and
cards are available at no cost.
FITTING, swivel, straight
nptf x 1/2–14 npsm
24X026, Integrated Control For
Hydraulic TOF With Electrical
Enclosure
Qty
1
1
1
1
1
1
Ref
57
58
59
60
61
62
TOF Without Electrical Enclosure
Part Description
---
★
★
★
★
★
▲
---
---
---
---
15V954
FITTING, adapter, 1/8 x
1/8 NPT(f)
BLOCK, adapter, regulator
O-RING
SCREW, cap, socket hd;
1.5 in, #8–32
CONTROL, air, 3
regulator, hydraulic
LABEL, valve, shutoff, air
control
Integrated Control For
Qty
1
2
4
8
1
1
68 334130B

Electrical Module
Parts
334130B 69

Parts
70 334130B

Electrical Control Module Parts
Parts
Ref. Part Description Qty
101
103
104
105 125946
106 123967
107
108 100133
109 100307 NUT, hex 8
110 123396
111
112 24V510
112a 24R042 KIT, daugh
113
114 24P175 PLATE, blank
115 125856
116 16T440
117
118
119 100166
120
122 17A543
---
---
---
---
---
---
---
---
17C694 CABLE, tof, lapp to souriau
---
---
ENCLOSURE, electrical 1
BUSHING, strain relief, m40
thread
NUT, strain relief, m40
thread
PLUG, hole, 1/2 in
KNOB, operator disconnect
PANEL, elec, transformer
(transformer assemblies
only)
PANEL, elec, 400v/n
(400V modules only)
PANEL, elec, 230v
(230V modules only)
WASHER, lock, 3/8
NUT, flange, serrated,
3/8-16
MODULE, gca, mzlp w/
daughter board
MODULE, gca
(8 zone asse
Qty 1) (12 zo
only; Qty 2
GASKET, foam
(8 zone assemblies only;
Qty 1) (12 zone assemblies
only; Qty 2)
(4 Zone assemblies only;
Qty2)(8zoneassemblies
only; Qty 1)
SCREW, 8-32, serrated
flange
CAP, souriau, uts14
(4 Zone only; Qty 2) (8 zone
assemblies only; Qty 4) (12
zone assemblies only; Qty
6)
(4 Zone only; Qty 2) (8 zone
assemblies only; Qty 4) (12
zone assemblies only; Qty
6)
WIRE, grounding, door 1
NUT, full hex
GASKET, hphm
HARNESS, power, mzlp1,
awb
,mzlp
mblies only;
ne assemblies
)
ter, board
12
Ref. Part Description Qty
123 17A544 HARNESS, power, mzlp2,
1
1
2
1
1
1
1
4
4
1
1
2
1
1
17A545
125
126
127 17A555
128 17A559
129 127511 CABLE, board, samtec
130 121226
131 121612
132 123969
134
136 24V911 FAN, 24
137 16X884 GRILL, fan
138 115836
139 127278 NUT, keps, hex
140 24V746
141 119865
142
143 24W812 ADM
144 15V551SHIELD, membrane, ADM
45121001
1
---
---
123968
---
17A547
--
awb
(8 zone assemblies only )
HARNESS, power, mzlp2/3,
awb
(12 zone assemblies only)
HARNESS, pump, mzlp1,
tb, tof
HARNESS, output, mzlp1,
ssr, contact
HARNESS, pump, reed
switch, tof
HARNESS, boar
comm
(8 zone assemblies only;
Qty 1) (12 zone assemblies
only; Qty 2)
CABLE, can, male / female,
0.4m
CONNECTOR, thru, m12,
mxf
SWITCH, disconnect, 100a
SWITCH, disconnect, ph
exp 100 A
(400V only)
HARNESS, disc, fuse,
230-600v
HARNESS
tof
(400V on
(400V o
(400V only)
GUARD, finger
(400V only)
(400V only)
GRILL, vent
(230V and 400V assemblies
only; Qty 2) (Transformer
assemblies only; Q ty 1)
SCREW, mach, hex
serrated
-
CONTROL, air, assy; with
solenoid
(Primary assemblies only)
Primary assemblies only)
(
CABLE, can, female /
female 1.0m
(Primary assemblies only)
ly)
vdc,120mx120m
nly)
d, mxm,
, disc, cb, 400v/n,
1
1
1
1
1
1
1
1
1
1
1
1
1
1
1
4
4
1
1
0.1
1
334130B
71

Parts
Part Description
Ref.
146
147 121250
148 102040 NUT, lock, hex
149 110755
150 121253 KNOB, display adj., ram
151
152 101550
153 100016
156 24V745
157
158
159
160 124654
161 121228
162 16W035 CONNECTOR, jumper
163
---
---
---
---
---
---
BRACKET, mounting,
assembly
(Primary assemblies only)
SCREW, shcs, 1/4uncx4.25
(Primary assemblies only)
(Primary assemblies only)
WASHER, plain
(Primary assemblies only)
pkgs
(Primary assemblies only)
BRACKET, pendant pivot,
(Primary assemblies only)
SCREW, cap, sch
(Primary assemblies only)
WASHER, lock
(Primary assemblies only)
SENSOR, level, low/empty
BUSHING, strain relief
NUT, bushing 1
GROMMET, wire
CONNECTOR, splitter,
12(m) x m12(f)
(Secondary modules only)
CABLE, can, fema le/female,
15.0 m
(Secondary modules only)
(8 zone assemblies only;
Qty 1) (12 zone assemblies
only; Qty 2)
CONTACT, socket, 20-24
awg, crimp, tin
Qty
Part Description
Ref.
164
1
165
1
166 127771
1
1
167
1
168
1
169
4
170
▲
5
172
1
181
1
1
182 17C669 CONNECTOR, jumper,
1
1
183 123856
184
3
---
---
---
---
---
196548 LABEL, warning, shock 1
---
---
17C712 TOKEN
TUBE, 1/16 shrink tube 0.13
HARNESS, input, mzlp1,
RTD
BRIDGE, plug-in, 2pos,
ut16
(400V and Transformer
modules only)
FERRULE, wire, 1 0awg
(230V modules only; Qty
2) (400V and transformer
modules only; Qty 8)
FERRULE, wire, 16awg 6
FERRULE, wire, 18 awg,
long
ARTWORK, instructions,
wiring, ul
FERRULE, wire, 10awg,
twin
(Secondary assemblies
only)
male
(Secondary assemblies
only)
HARNESS, CAN, cable
(Secondary assemblies
only)
(Secondary assemblies
only)
Qty
1
1
6
1
3
1
1
1
▲
Replacement Warning labels, signs, tags, and
cards are available at no cost.
72
334130B

Electrical Panel
230V
400V/N
Transformer
Parts
Transformer Panel Shown
Torque terminals to 25–27 in-lbs (2.8–3.1 N•m).
1
Torque terminals to 13.3–16 in-lbs (1.5–1.8
2
N•m).
Torque terminals to 4.53–6.2 in-lbs (0.5–0.7
3
N•m).
334130B 73

Parts
230V Panel 400V/N Panel
Torque terminals to 25–27 in-lbs (2.8–3.1 N•m).
1
Torque terminals to 13.3–16 in-lbs (1.5–1.8
2
N•m).
Torque terminals to 4.53–6.2 in-lbs (0.5–0.7
3
N•m).
74
334130B
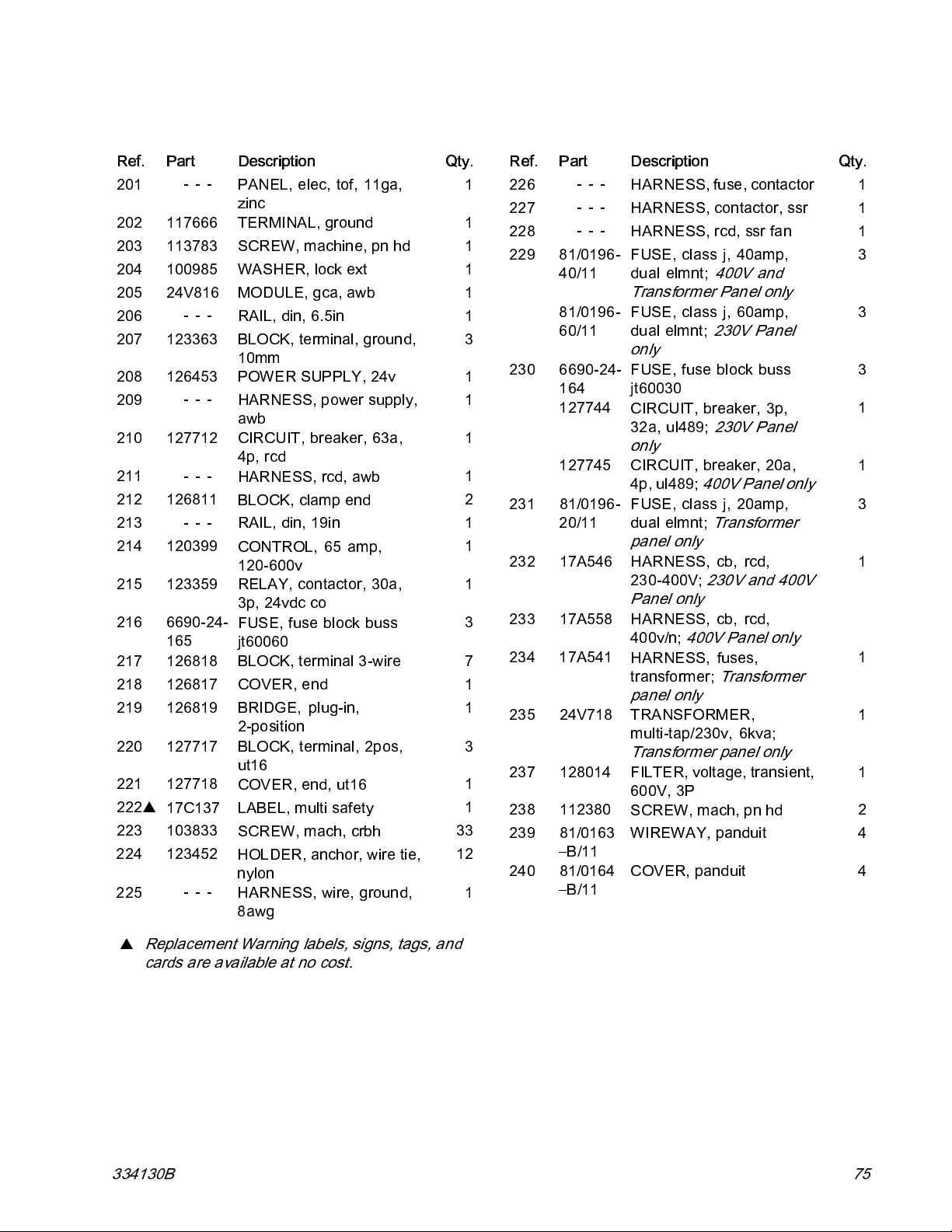
Electrical Panel Parts
Parts
Ref.
201
202 117666 TERMINAL, ground 1
203 113783
204 100985
205 24V816
206
207 123363
208 126453
209
210 127712
211
212 126811
213
214 120399
215 123359 RELAY, contactor, 30a,
216 6690-24-
217 126818
218 126817
219 126819
220 127717
221 127718
222
223 103833
224 123452
225
Part Description
---
---
---
---
---
165
▲
17C137 LABEL, multi safety
---
PANEL, elec, tof, 11ga,
zinc
SCREW, machine, pn hd
WASHER, lock ext
MODULE, gca, awb
RAIL,din,6.5in 1
BLOCK, terminal, ground,
10mm
POWER SUPPLY, 24v
HARNESS, power supply,
awb
CIRCUIT, breaker, 63a,
4p, rcd
HARNESS, rcd, awb
BLOCK, clamp end
RAIL,din,19in 1
CONTROL, 65 amp,
120-600v
3p, 24vdc co
FUSE, fuse block buss
jt60060
BLOCK, terminal 3-wire
COVER, end
BRIDGE, plug-in,
2-position
BLOCK, terminal, 2pos,
ut16
COVER, end, ut16
SCREW, mach, crbh
HOLDER, anchor, wire tie,
nylon
HARNESS, wire, ground,
8awg
Qty.
33
12
Ref.
226
1
227
228
1
1
1
3
230
1
1
1
1
2
231 81/0196-
1
232 17A546
1
233 17A558
3
234 17A541
7
1
1
235 24V718
3
237 128014 FILTER, voltage, transient,
1
1
238 112380
239 81/0163
240 81/0164
1
Part Description
---
---
---
81/0196-
40/11
81/0196-
60/11
6690-24-
164
127744
127745
20/11
–B/11
–B/11
HARNESS,fuse, contactor
HARNESS, contactor, ssr
HARNESS, rcd, ssr fan
FUSE, class j, 40amp,
dual elmnt;
Transformer Panel only
FUSE, class j, 60amp,
dual elmnt;
only
FUSE, fuse block buss
jt60030
CIRCUIT, breaker, 3p,
32a, ul489;
only
CIRCUIT, breaker, 20a,
4p, ul489;
FUSE, class j, 20amp,
dual elmnt;
panel only
HARNESS, cb, rcd,
230-400V;
Panel only
HARNESS, cb, rcd,
400v/n;
HARNESS, fuses,
transformer;
panel only
TRANSFORMER,
multi-tap/230v, 6kva;
Transformer panel only
600V, 3P
SCREW, mach, pn hd
WIREWAY, panduit 4
COVER, panduit
400V Panel only
400V Panel only
230V and 400V
Qty.
1
1
1
3229
400V and
3
230V Panel
3
1
230V Panel
1
3
Transformer
1
1
Transformer
1
1
2
4
▲
Replacement Warning labels, signs, tags, and
cards are available at no cost.
334130B 75

Parts
Merkur 2200, 23:1 Pump Modules
Torque to 50–60 ft-lb (68–81 N•m).
1
Torque to 145–155 ft-lb (196–210 N•m).
2
Coat mounting surface of sensor mounting
3
block(322) w ith non-silicone heat sink compound.
Do not coat sensor.
Prior to tightening band clamp (321), RTD sensor
4
(320)must be fully contained within the sensor
mount (322).
After fastening band clamp (321), secure excess
5
Coat inside of heater (309a, 309b) only to within
6
0.75 in. (19 mm) of vertical ends with non-silicone
heat sink compound before mounting.
Cap screws (311) must be loose while tie rods
7
(307) are being torqued.
Torque to 150 ft-lb (203 N•m).
8
Install swivel fitting (302) prior to screw (303) and
9
reed switch assembly (304).
Apply anaerobic sealant to threads.
10
with fiberglass tape.
76 334130B

Merkur 2200, 23:1 Pump Modules
Parts
Ref. Part
301 24W754
302 155470
303
304 24X441 SWITCH, reed assy 1
305 15H173 BRACKET, motor m ount 1
306 15H397 ADAPTER, rod, pump 1
307 16A223 ROD,tie,vertdriver 3
308 106166 NUT, mach ,hex 3
309 120271 HEATER, pump, 600 watt 2
310 24W150 P UMP, long shaft, cf;
311 109211 SCREW, cap, sch 3
312 17A637 BLOCK, s tandoff, mounting 3
315 102656 MUFFLER 1
316 186925 NUT, coupling 1
317 184129 COLLAR, coupling 2
318 120186 BOLT, mounting, u-bolt 2
---
24W151
Description
MOTOR, air, 6 in, 4.75
stroke, blue
FITTING, swivel, union,
90°
FASTENER, screw, slot
hex, #8-32 tap
24V003 only
PUMP, long s haft, gf;
24V006 only
Qty
1
1
1
1
Ref. Part
320 17F009
321
322
323
324
325
326
329 103347
330
331
333 206994 FLUID, tsl 8 oz bottle 1
334 17B715
335 127671 SWITCH, over temp, fixed,
336 122338
337 214656
338
C31012 CLAMP
C03507 SUPPORT, sensor
C38162 SCREW, machine
C38163 WASHER, lock, ext. tooth
---
---
C33049 TAPE, adhesive, fiberglass
---
16C009 HOOK
Description
SENSOR, RTD
CONDUCTOR, ground
SHIELD, pump, tof200;
see Pump Shield, page 82
VALVE, safety, 100 psi
LUBRICANT, high temp ,
thermal
SUPPORT, block,
overtemp
450°F (232°C)
SCREW, cap, socket bh
HOSE,coupled,10ft(3m)
Qty
1.5
1
1
1
1
1
1
1
1
1
1
2
4
1
1
334130B
77

Parts
Merkur 3400, 36:1 Pump Modules
Torque to 50–60 ft-lb (68–81 N•m).
1
Torque to 145–155 ft-lb (196–210 N•m).
2
Coat mounting surface of sens or mounting
3
block(322) with non-silicone heat sink compound.
Do not coat sensor.
ior to tightening band clamp (321), RTD sensor
Pr
4
0)must be fully contained within the sensor
(2
unt (322).
mo
After fastening band clamp (321), secure excess
5
Coat inside of heater (309) only to within 0.75 in.
6
(19 mm) of vertical ends) with non-s ilicone heat
sink compound before mounting.
Cap screws (311) must be loose while tie rods
7
(307) are being torqued.
Torque to 150 ft-lb (203 N•m).
8
Install swivel fitting (302) prior to screw (303)
9
andreedswitchassembly(304).
Apply anaerobic sealant to threads.
10
with fiberglass tape.
78 334130B
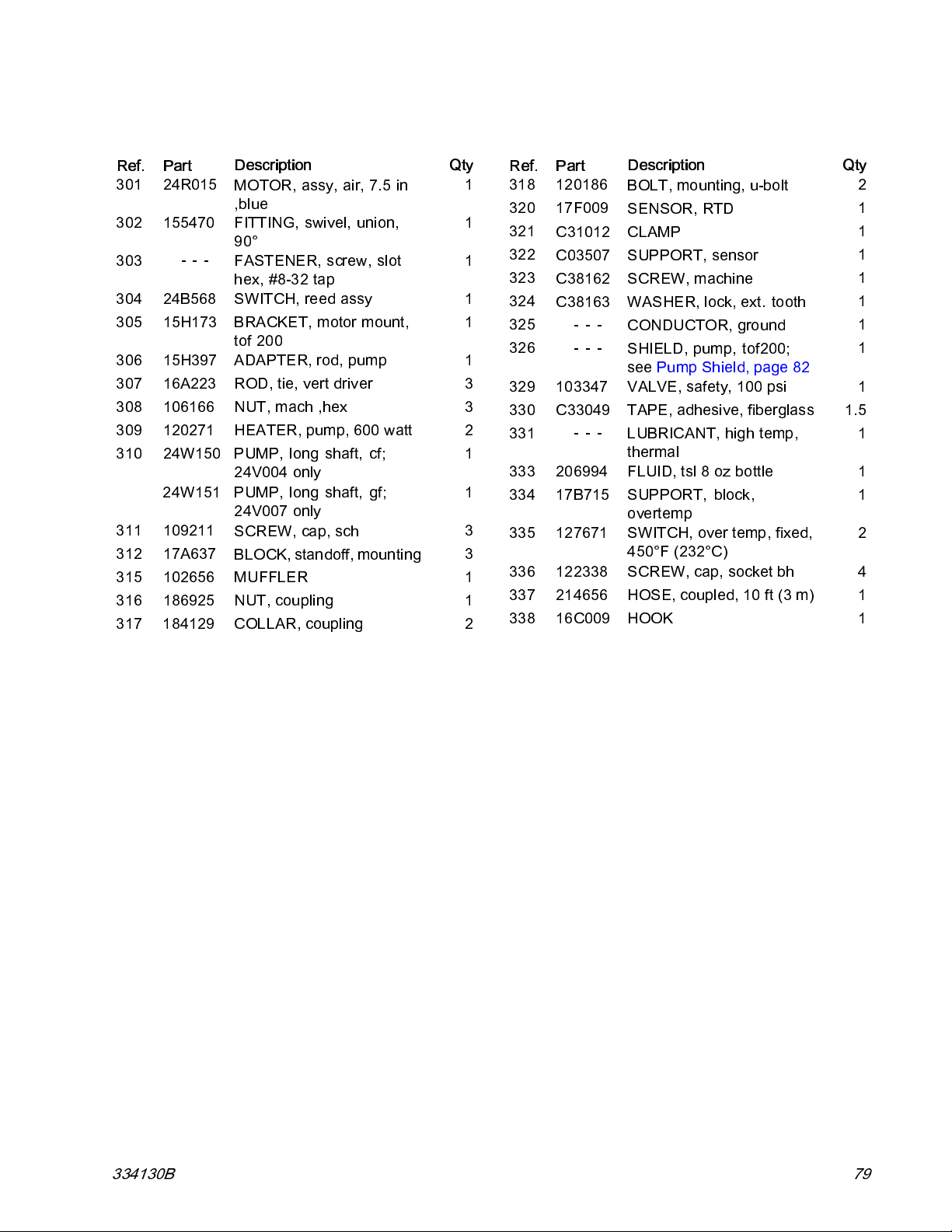
Merkur 3400, 36:1 Pump Modules
Parts
Ref. Part
301 24R015
302 155470
303
304 24B568 SWITCH, reed assy 1
305 15H173 BRACKET, motor mount,
306 15H397 ADAPTER, rod, pump 1
307 16A223
308 106166 NUT, mach ,hex 3
309 120271 HEATER, pump, 600 watt 2
310 24W150
311 109211
312 17A637
315 102656 MUFFLER 1
316 186925 NUT, coupling 1
317 184129
---
24W151 PUMP, long s haft, gf;
Description
MOTOR,assy,air,7.5in
,blue
FITTING, swivel, union,
90°
FASTENER, screw, slot
hex, #8-32 tap
tof 200
ROD,tie,vertdriver
PUMP, long shaft, cf;
24V004 only
24V007 only
SCREW, cap, sch
BLOCK, standoff, mounting
COLLAR, coupling
Qty
Ref. Part
318 120186
1
320 17F009
1
321
322
1
323
324
1
325
326
3
329 103347
330
331
1
333 206994 FLUID, tsl 8 oz bottle 1
1
334 17B715
3
335 127671 SWITCH, over temp, fixed,
3
336 122338
337 214656
338
2
C31012 CLAMP
C03507 SUPPORT, sensor
C38162 SCREW, machine
C38163 WASHER, lock, ext. tooth
---
---
C33049 TAPE, adhesive, fiberglass
---
16C009 HOOK
Description
BOLT, mounting, u-bolt
SENSOR, RTD
CONDUCTOR, ground
SHIELD, pump, tof200;
see Pump Shield, page 82
VALVE, safety, 100 psi
LUBRICANT, high temp ,
thermal
SUPPORT, block,
overtemp
450°F (232°C)
SCREW, cap, socket bh
HOSE,coupled,10ft(3m)
Qty
2
1
1
1
1
1
1
1
1
1.5
1
1
2
4
1
1
334130B 79

Parts
NXT 6500, 70:1 Pump Modules
Torque to 50–60 ft-lb (68–81 N•m).
1
Torque to 145–155 ft-lb (196–210 N•m).
2
Coat mounting surface of sensor mounting block
3
(411) with non-silicone heat sink compound. Do
not coat sensor.
Prior to tightening band clamp (412), RTD sensor
4
(410) must be fully contained within the sensor
After fastening band clamp (412), secure excess
5
with fiberglass tape.
Coat inside of heater (407) only to within 0.75 in.
6
(19 mm) of vertical ends) with non-s ilicone heat
sink compound before mounting.
Torque to 150 ft-lb (203 N•m).
8
Apply anaerobic sealant to threads.
10
mount (411).
80 334130B

NXT 6500, 70:1 Pump Modules
Parts
Ref. Part
401 N65LR0
402 120375 ADAPTER, elbow, 3/4 npti
403 15H542
404 17A406
405 16A223
406 106166 NUT, mach, hex 3
407 120271 HEATER, pump, 600 watt 2
408 24W150
24W151
409
C19837 SCREW, cap, socket hd
410 17F009
411
C03507 SUPPORT, sensor
412
C31012 CLAMP
413 186925 NUT, coupling 1
414 184129
415
C38163 WASHER, lock, ext. tooth
Description
MOTOR, 6500, low-noise,
remote
x 1/2 npte
BRACKET, mounting,
motor, tof200
ADAPTER, rod, pump, tof
ROD,tie,vertdriver
PUMP, long shaft, cf;
24V005 only
PUMP, long s haft, gf;
24V008 only
SENSOR, RTD
COLLAR, coupling
Qty
Ref. Part
416
1
417
1
418 120186
419 100307 NUT, hex 4
2
422
1
423 120588
3
424 120012
425
1
426
428 206994 FLUID, tsl 8 oz bottle 1
1
429 17B715
4
430 127671 SWITCH, over temp, fixed,
1
1
431 122338
1
432
2
433 255792 HOSE, coupled, 13.5 ft (4
1
---
C38162 SCREW, machine
---
---
C33049 TAPE, adhesive, fiberglass
17C255 CABLE, M12, 8p, 5p, m,
Description
CONDUCTOR, ground
BOLT, mounting, u-bolt
SHIELD, pump, tof200;
see Pump Shield, page 82
PLUG, pipe, round
VALVE, safety, 50 psi
LUBRICANT, high temp ,
thermal
SUPPORT, block,
overtemp
450°F (232°C)
SCREW, cap, socket bh
0.2 m
m)
Qty
1
1
2
1
1
1
1
1.5
1
2
4
1
1
334130B 81

Parts
Pump Shield
Ref. Part
501 24W974
502 24W975
503 24W976
504 24W977
505 24W978
506 120792
▲
Replacement Warning labels, signs, tags, and
cards are available at no cost.
82 334130B
Description
COVER, pump, bottom
COVER, pump, right
COVER, pump, left
COVER, pump, top, front
COVER, pump, top, back
FASTENER,
thread-cutting screw
Qty
12
Ref. Part
1
507
▲
184090 LABEL, warning 2
1
508 104088 RIVET, blind 4
1
509
▲
15J075
1
510
511
---
C20731 FITTING, conduit,
Description
LABEL, safety, hot
surface and shock
BUSHING, conduit, 1 in
connector, 1 in.
Qty
2
1
1

Heated Platens
24V633, Heated Drum Platen, Mega-Flo (Code E- option M)
24V634, Heated Drum Platen, Standard Grid(Code E- option F)
24V635, Heated Drum Platen, Smooth Bottom (no fin) (Code E- option S)
Parts
334130B 83

Parts
24V633, Heated Drum Platen, Mega-Flo (Code E- option M)
24V634, Heated Drum Platen, Standard Grid(Code E- option F)
24V635, Heated Drum Platen, Smooth Bottom (no fin) (Code E- option S)
Ref Part Description Qty
601
602 C32204 PACKING, o-ring 1
603 15G967 PLATE, tire 1
604 C19049 SCREW, mach, slotted,
605 17F010
606
607 158491
608 158581
609 617227
610 246501
611 100361
612 100133
613
614 150707 PLATE, designation 1
615 100508
616
---
C32201 GASKET, follower
C19846 SCREW, cap socket, HD
15X470 PLATE, designation;
---
PLATEN — see table below
RND HD
SENSOR, temperature
FITTING, nipple
COUPLING, hex
HANDLE, follower, bleed
VALVE, blow off
PLUG, pipe
WASHER, lock
24V633 only
SCREW, drive
CONDUCTOR, 14.2 ft (4.3
m)
Ref Part Description Qty
617
618
619
1
620 112901 NUT, hex 12
1
621 111640
1
622
1
623 127671
1
624 122338
1
625
1
626
4
627
6
6
628 127690
629 127689
1
630
2
6
---
---
---
---
---
---
---
---
CONDUCTOR, 1.7 ft (0.5
m)
CONDUCTOR, 0.3 ft (0.09
m)
CONDUCTOR, ground
WASHER, lock, internal
PLUG, follower, plate
SWITCH, over temp, fixed,
450°F (232°C)
SCREW, cap, socket bh
TUBE, ptfe, 1/4 X 5/16
TUBE, ptfe, 3/32 X 5/32
SLEEVE, fiberglass,
hi-temp
FITTING, adapter, 5/16 in.
tube x 1/4 in tube
FITTING, adapter, 1/4 in
tube x 5/32 in tube
TUBE, polyeth, 1/4 OD; 26
ft (7.9 m)
2
4
1
12
1
1
2
3
3
3
1
1
1
Platen Model Description
24V633 Mega-Flo 194254 1 16.5 ohms +1/-2
24V634
24V635
ard Grid 617225 1 19.2 ohms +2/-3
Stand
h Bottom
Smoot
Ref. No
C5735
.601
8 1 19.2 ohms +2/-3
Qty.
Element Resistance
84 334130B

Heater Terminal Patterns
24V633 24V634, 24V635
16.5 Ohms across pairs 19.25 Ohms across pairs
Platen Coil Wiring
Parts
3
24V63
334130B 85
24V63
4, 24V635

Parts
Drum Ram Post Saddle Clamp
C32463
Option H-1
Part Description
Ref
701
C32424 BOLT, U, 7 in. (177.8 mm)
702 160111
703 100103 PIN, cotter 2
704 100307 NUT, hex 4
CLAMP, barrel
Qty
2
1
Part Description
Ref
705 100133
706
C38182 WASHER, plain
707
C32461 CLAMP, saddle
708 166265 PIN, pivot 1
WASHER, lock
Qty
4
2
2
86 334130B

Heavy Duty Drum Band Clamp
918395
Option H-3
Parts
Part Description
Ref
702 100101
703 918421
704 918423 KIT, repair 1
705 617395 PIN, quick release 2
756 100133
SCREW, cap, hex hd
CLAMP, b ack half
assembly
WASHER, lock
Qty
8
1
8
Part Description
Ref
707
C19200 WASHER, plain
708 617433
759 617395
710 100131
761
C32424 BOLT, U 7 in. (177.8 mm)
SPACER, drum clamp
CLAMP, saddle
NUT, full hex
Qty
8
8
4
8
4
334130B 87

Parts
Fiber Drum Reinforcement Clam Shell Clamp
918397
OPTION H-2
Part Description
Ref
6
C32424 BOLT, U, 7 in. (177.8 mm)
801
C32271 CLAMSHELL
802
C19126 SCREW, cap, hex hd
803 100133
88 334130B
WASHER, lock
Qty
4
1
8
12
Part Description
Ref
804 100307 NUT, hex 8
805 617340
807 617341
CLAMP, saddle
MOUNT, clam shell
Qty
4
2

Vent Hood Kit, 233559
Parts
Ref
851
852 112166
▲
Part Description
---
Replacement Warning labels, signs, tags, and
cards are available at no cost.
VENT hood 1
SCREW, cap, sch
Qty
Ref
853 100016
4
855
Part Description
WASHER, lock
▲
C14038
LABEL, warning 1
Qty
4
334130B 89

Accessories and Kits
Accessories and Kits
Wiper Kits
See manual 309196 for installation and repair
instructions.
Part No. Description
253243
253244 Hose and T-Wiper Kit
253245 Twin Hose Wiper Kit
253246 T-Wiper Kit
Applicators and Dispense Valves
Part No. Description
249515
249514
249513
249512
Air-Operated Heated Dispense Valves
Part No. Description
243694 Automatic Dispense Valve, 240V,
244951 Automatic Endure Dispe nse Valve,
244909 Automatic Endure Dispe nse Valve,
243701 45 in (114 cm) Distribution Header With
Hose/Spring Wiper Kit
Manual Gun, Top Feed, 240V
Manual Gun, Bottom Feed, 240V
Manual Gun, Top Feed, El ectric Switch,
240V
Manual Gun, Bottom Feed, Electric
Switch, 240V
Air-Operated Heated Dispense Valve
240V, Air-Operated High Flow Heated
Dispense Valve
240V, Air-Operated Snuff-Back Heated
Dispense Valve
Valve, 240V
Flow Control and Manifolds
Part No. Description
243700 Heated Air Operated Mastic Pressure
Regulator, 240V
243656
243657
243697
289208
23:1 Heated Pressure Compensator
Valve, 240V
51:1 Heated Pressure Compensator
Valve, 240V
Heated Distribution Manifold, 240V
Includes (2) 3/4 npt(f) inlet check valves,
(1) npt 4–ported manifold, (2) 1 in npt(f)
outlet gate valves, mounting bracket,
400w 230 VAC heaters, RTD sensor,
and8pinconnectorbox.
Compact Heated Regulator
Accessory Extension Cables
Use to connect fluid control devices and heated
hoses to the electrical control enclosure.
Part No. Description
Connect between controller and heated hose
196313
196314
Connect between controller and heated accessory
196315
196316
Connect between controller and heated devices
196317
196318
15ft,16pinto16pin
25ft,16to16pin
15ft,16pinto8pin
25ft,16pinto8pin
15 ft, 16 pin to (2) 8 pin
25 ft, 16 pin to (2) 8 pin
Light Tower Kit, 24W589
Tie Rod Kits
Use to retrofit Ch eck-Mate 800 Displacement Pump
to an existing Therm-O-Flow system.
Part No. Description
24V750
24V754
90 334130B
Bulldog® and Senator® Tie Rod Kit; see
manual 334131
NXT® Tie Rod Kit; see manual 334132

Heated Hoses and Fittings
Accessories and Kits
Hose Diameter
Hose Length
3ft(1.5m)
6ft(1.8m)
10 ft (3 m)
15 ft (4.6 m)
20 ft (6 m)
25 ft (7.6 m)
30 ft (9 m)
Pump Fittings
TOF 20/200 PUMP 1-11
1/2DUALOUTLETADD
120263
TOF MINI 5 PUMP 1/2
NPT DUAL OUTLET
ADD 120241
Hose to Hose Fittings
-6 Hose (.308 ID)
-8 Hose
-10 Hose (.495 ID )
-12 Hose (.617 ID )
-16 H
-20 Hose (1.125 ID)
(.401 ID )
ose (.687 ID)
-6
(9/16in-18
JIC)
None None None
None 115902 115875 None 115884 None
16J875 115873 115876 115880 115885 117821
None 115874 115877 115881 115886 117822
None None 115878 115882 115887 None
None None 115879 115883 115888 None
None None 121200 None None None
16V432
100380
16V432 C20678 C20679 C38006 6301-85
125778 123684 123683
123684 120241 120242 120244
123683 120242 120243 120246
123683
120265
123683
120265
120267
None
-8
(3/4 in -16
JIC)
253267 253268 120260 120261 120262
120244 120246 120247 120248
120244
120267
6308-82
126521
-10
(7/8 in -14
JIC)
120246
120267
120246
120267
120268
-12
(1-1/16 in
-12 JIC)
15C586
123683
120265
120248 120249
123135
126521
-16
(1-5/16 in
-12 JIC)
None None
123683
120265
120267
120244
120267
120246
120267
120249
120268
-20
(1-5/8 in -12
JIC)
6308-85
120268
None
6308-82
126521
6308-82
126521
123135
126521
120249
120268
120250
334130B 91

Accessories and Kits
Hose Diameter
Fittings
Compensator 51:1,
243657
Compensator 23:1,
243656
Inlet & Outlet: 1-11 1/2
in NPTF
Distribution manifold,
243697
Inlet:3/4inNPTF
Distribution manifold,
243697
Outlet: 1-11 1/2 in NPTF
Compact Heated
Regulator, 289208
Inlet & Outlet: 3/8 in
NPTF
Mastic Regulator,
243700
Inlet & Outlet: 3/4 in
NPTF
Top and bottom feed
guns with and without
switch, 249512, 249513,
249514, 249515
Inlet: 7/8-14 (JIC -10)
male
Standard, High Flow &
Snuff-back Dispense
valves, 243694, 244951,
244909
Inlet: 1/2 NPTF
Distribution header,
243701
Inlet: 1/2 NPTF
Precision Gear Meter
PGM
Inlet: 1-5/16-12 o-ring
face seal
Precision Gear Meter
PGM
Outlet: 3/4 NPTF
PCF Metering System
Inlet & Outlet: 3/4 NTPF
-6
(9/16in-18
JIC)
16V432
100380
16V432
100896
16V432
100380
16V432
100896
16V432
100896
117677 120264 None 120265 None None
16V432 124287
16V432 124287
None None None 124238 124239 124240
16V432
100896
16V432
100896
-8
(3/4 in -16
JIC)
6308-82
124286 15Y934 C20708 125661
6308-82
121311 116765 116766
124286 15Y934 C20708 125661
124286 15Y934 C20708 125661
124286 15Y934
-10
(7/8 in -14
JIC)
123135
120266
123135
120266
C20768
C20768
-12
(1-1/16 in
-12 JIC)
123135 123854 15D936
123135 123854 15D936
94/1027/99 125662
94/1027/99 125662
C20708
-16
(1-5/16 in
-12 JIC)
116766
120267
125661
-20
(1-5/8 in -12
JIC)
125661
120268
116766
120267
120268
125661
120268
125662
120268
125662
120268
125661
120268
125661
120268
92 334130B

8 Channel Upgrade Kit, 24V755
Use this kit to upgrade a 4 Channel system to a 8 channel system.
Accessories and Kits
Part Description
Ref
1
2 125856
3 16T440
4 127511
5 16W035
MODULE, GCA, MZLP
SCREW, 8–32, serrated
flange
CAP, souriau, UTS14
CABLE, board, samtec
CONNECTOR, jumper
Qty
Ref
617A544
1
4
7 112190
8
2
9
1
1
Part Description
HARNESS, power, MZLP2,
AWB
STRAP, wrist, grounding
17C712 TOKEN, software upgrade
17C694 CABLE, TOF, LAPP to
souriau
Qty
1
1
1
2
334130B 93

Accessories and Kits
8 Zone Upgrade Kit Installation
1. Disconnect plug from power outlet or turn off
circuit breaker for incoming power.
2. Place grounding wrist strap (7) over your wrist
andsecureotherendtoagroundedsurface.
3. Set the kit’s MZLP (1) rotary switch to “3” on a
primary system or “6” on a secondary system.
4. Remove screws (B), remove plate (A), and
gasket (C) from system. Use screws (2) to install
MZLP (1) onto system as shown.
Note
The new MZLP (1) will be referred to
as MZLP 2, and the original MZLP that
came with the system will be referred to
as MZLP 1.
5. Open the electrical enclosure door.
Note
Do not force the electrical connection.
Minimal force is required to seat the
connector. If resistance is felt, s top, and
verify the connector orientation.
6. Connect cable (4) to J3 connector on MZLP 1
and J6 connector on MZLP 2.
7. Connect power harness (6) to MZLP 2 connector
J2 and J5 connector on AWB. Install jumper (5)
on the MZLP 2 J5 connector
8. Use fittings and hoses that meet your hose routing
needs. See Accessories and Kits, page 90.
9. To ensure your system has the latest
software, insert token (8) into the ADM. See
Update Software, page 59.
94 334130B

12 Channel Upgrade Kit, 24V756
Use this kit to upgrade a 8 channel system to a 12 channel system.
Accessories and Kits
Part Description
Ref
1
2 125856
3 16T440
4 127511
5 16W035
MODULE, GCA, MZLP
SCREW, 8–32, serrated
flange
CAP, souriau, UTS14
CABLE, board, samtec
CONNECTOR, jumper
Qty
Ref
617A545
1
4
7 112190
8
2
9
1
1
Part Description
HARNESS, powe r,
MZLP2/3, AWB
STRAP, wrist, grounding
17C712 TOKEN, software upgrade
17C694 CABLE, TOF, LAPP to
souriau
Qty
1
1
1
2
334130B 95

Accessories and Kits
12 Zone Upgrade Kit Installation
1. Disconnect plug from power outlet or turn off
circuit breaker for incoming power.
2. Place grounding wrist strap (7) over your wrist
andsecureotherendtoagroundedsurface.
3. Set the kit’s MZLP (1) rotary switch to “4” on a
primary system or “7” on a secondary system.
4. Remove screws (B), remove plate (A), and
gasket (C) from system. Use screws (2) to install
MZLP (1) onto system as shown.
Note
The new MZLP (1) will be referred to as
MZLP 3, and the other two that came
withthesystemwillbereferredtoas
MZLP 1 and MZLP 2.
5. Open the electrical enclosure door.
Note
Do not force the electrical connection.
Minimal force is required to seat the
connector. If resistance is felt, s top, and
verify the connector orientation.
6. Connect cable (4) to J3 connector on MZLP 2
and J6 connector on MZLP (1). Remove existing
power cable from MZLP 2 J2 and AWB J5
connector.
7. Connect power harness (6) to MZLP 2 and MZLP
3 J2 connector and J5 connector on AWB. Install
8. See Install Heated Hose, page 18,toconnecta
heated hose or fluid control device.
9. To ensure your system has the latest
software, insert token (8) into the ADM. See
Update Software, page 59.
96 334130B

Appendix A— ADM
Appendix A— ADM
General Operation
ADM Power
The ADM automatically turns on when the main
power switch is turned on.
Screen Navigation
To switch between the Setup and Operation screens,
press
screens.
. Use the keypad to navigate between
Enable, Disable Heating System
To enable or disable the entire heating system,
press
the heating system is enabled, use the Heat-A and
Heat-B Setup screens.
. To set which channels are active when
334130B 97

Appendix A— ADM
Icons
Screen Icons
These are frequently used icons on the screens.
The following descriptions explain what each icon
represents.
Icon Description
Primary System= A
Secondary System = B
Heating Disabled
Warm Up, Actual temperature
is outside of Target
Temperature
Reached Target Temperature
Hose
Gun
Manifold
PGM
Softkey Icons
The following icons appear in the ADM, directly to
the left or right of the soft key which activates that
operation.
Icon Function
Pause Material Tracking
Continue Material Tracking
Pump Ready
Setback
Reset Cycl
(press an
Add or edit event
Accept sc
Crossov
e Counter
dhold)
hedule
er for Tandem Systems
Flow Me
Pressure Regulator
Other
Advisory. See Error Codes
for more information.
Deviation. See Error Codes
for more information
Alarm. See Error Codes
for more information
ter
Erase or cancel schedule
Cancel
Clear
Schedule Event On/Off
Heat On/Off
98 334130B

Appendix A— ADM
Operation Screens
Home
This screen shows the temperature state of the
system and material usage.
Note
If present, secondary systems will b e shown
on the home page.
Color A and B Zone Status
Yellow
Green/Yellow Flashing
Outside of advisory
range
Warmup
Events
The Events screens store a maximum of 200 events.
The events list can be downloaded in the USB logs.
See Appendix B — USB Data, page 105.
Heat-A
This screen shows the target and actual temperatures
for all zones on the system.
Note
The Heat-B screen shows information for an
optional secondary system.
Color A and B Zone Status
White
Green On and at setpoint
Red Outside of alarm range
Off
temperature
Tracked Events
Custom Language Downloaded
Custom Language Uploaded
Fill Valve Closed
Fill Valve Open
Heat Off
Heat On
Logs Downloaded
Pump Cycles Total Reset
Pump Off
Pump On
Red Stop Button Pressed
Setup Value Changed
System Power Off
System Power On
System Settings Downloaded
System Settings Uploaded
USB Disabled
USB Drive Inserted
USB Drive Removed
User Maintenance Count Reset
334130B 99

Appendix A— ADM
Errors
The Errors screens store a maximum of 200 errors.
See Error Codes. Download the errors list in the USB
logs. See Appendix B — USB Data, page 105.
CAN:
24 VDC power supply voltage reading (18–28
VDC)
DI:
System Digital Inputs
0: Drum Empty
1: Drum Low
2: Pump Cycle S witch Up
3: Pump Cycle Switch Down
DO:
System Digital Outputs
0: Pump Solenoid
1: Not Used
2: Not Used
3: Not Used
ISO DI:
See Connect PLC, page 27.
Customer Digital Inputs
Diagnostic-A
This screen shows details of various items to aid
in troubleshooting the system. This screen can be
hidden by de-selecting “Enable Diagnostics Screen”
on the System 3 screen. The flow rate upda tes every
15–20 seconds with average flow rate over the last
15–20 seconds.
Note
Diagnostic-B shows information for an
optional secondary system.
ISO DO:
See Connect PLC, page 27.
Fan:
Heat Soak:
has reached set temperature.
Life Cycles:
system
MZLP 1:
• 32–160°F(0–71°C)
Pump Sol:
•(0mA-off)
• (150-250 mA - on)
Pump CPM:
USB DL%:
downloading USB data. 5 downloads will occur.
Weight:
system
XFMRTemp:
temperature sensor
Customer Digital Outputs
current to fan
set time for platen to heat after the platen
total number of pump cycles over life of
temperature on MZLP 1
Current draw of pump solenoid
Pump cycles per minute.
Percentage complete, only applies when
Weight of material dispensed over life of
Temperature of tran sformer
The following information is displayed.
Diagnostic Data
ACurrent Draw
B RTD Reading
uty Cycle
CD
100 334130B
Setup Screens
Note
It is important to set all settings in the Sys tem
screens correctly to ensure optimal system
performance.