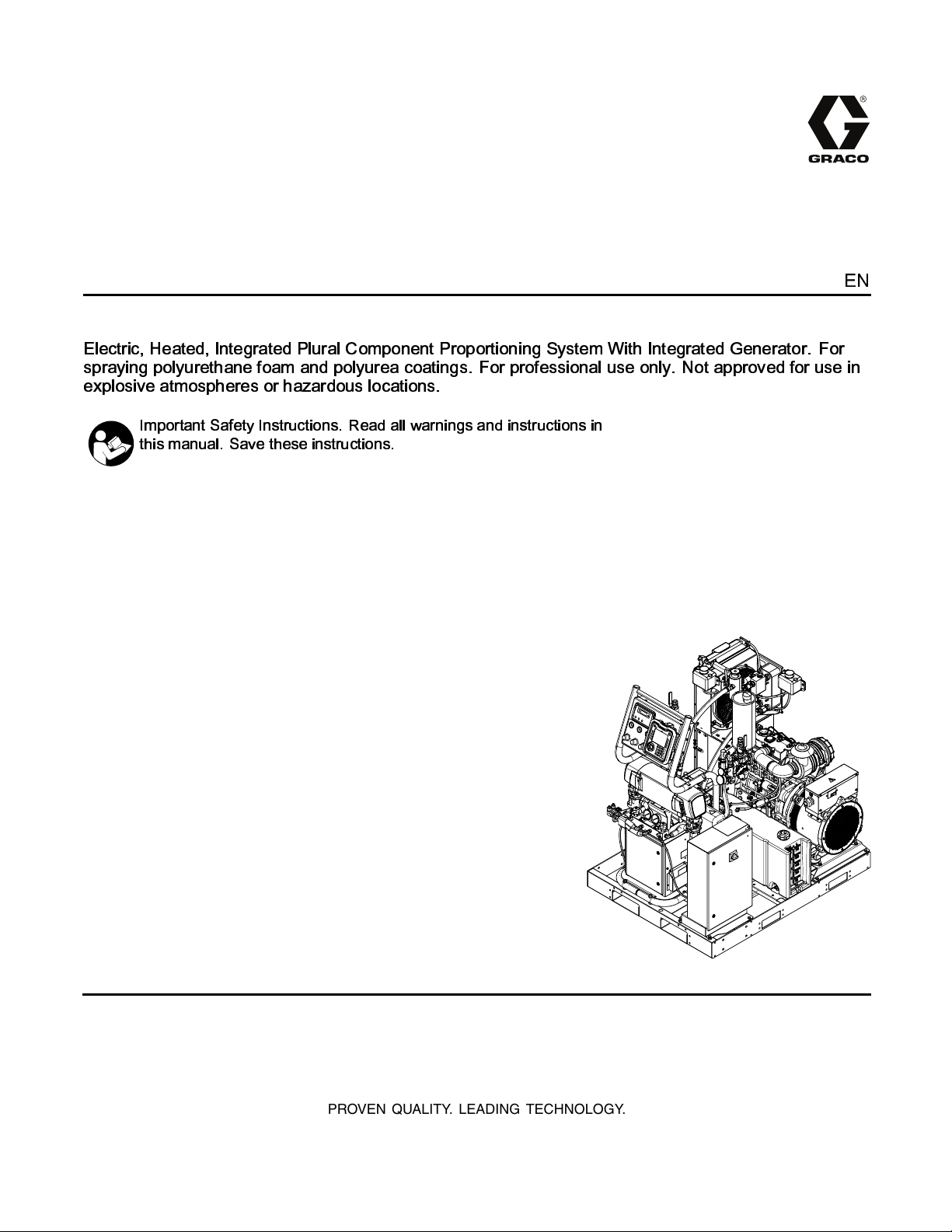
Repair-Parts
Reactor® 2 Elite Integrated
Proportioning System
Electric, Heated, Integrated Plural Component Proportioning System With Integrated Generator. For
spraying polyurethane foam and polyurea coatings. For professional use only. Not approved for use in
explosive atmospheres or hazardous locations.
Important Safety Instructions. Read all warnings and instructions in
this manual. Save these instructions.
332637C
EN
PROVEN QUALITY. LEADING TECHNOLOGY.
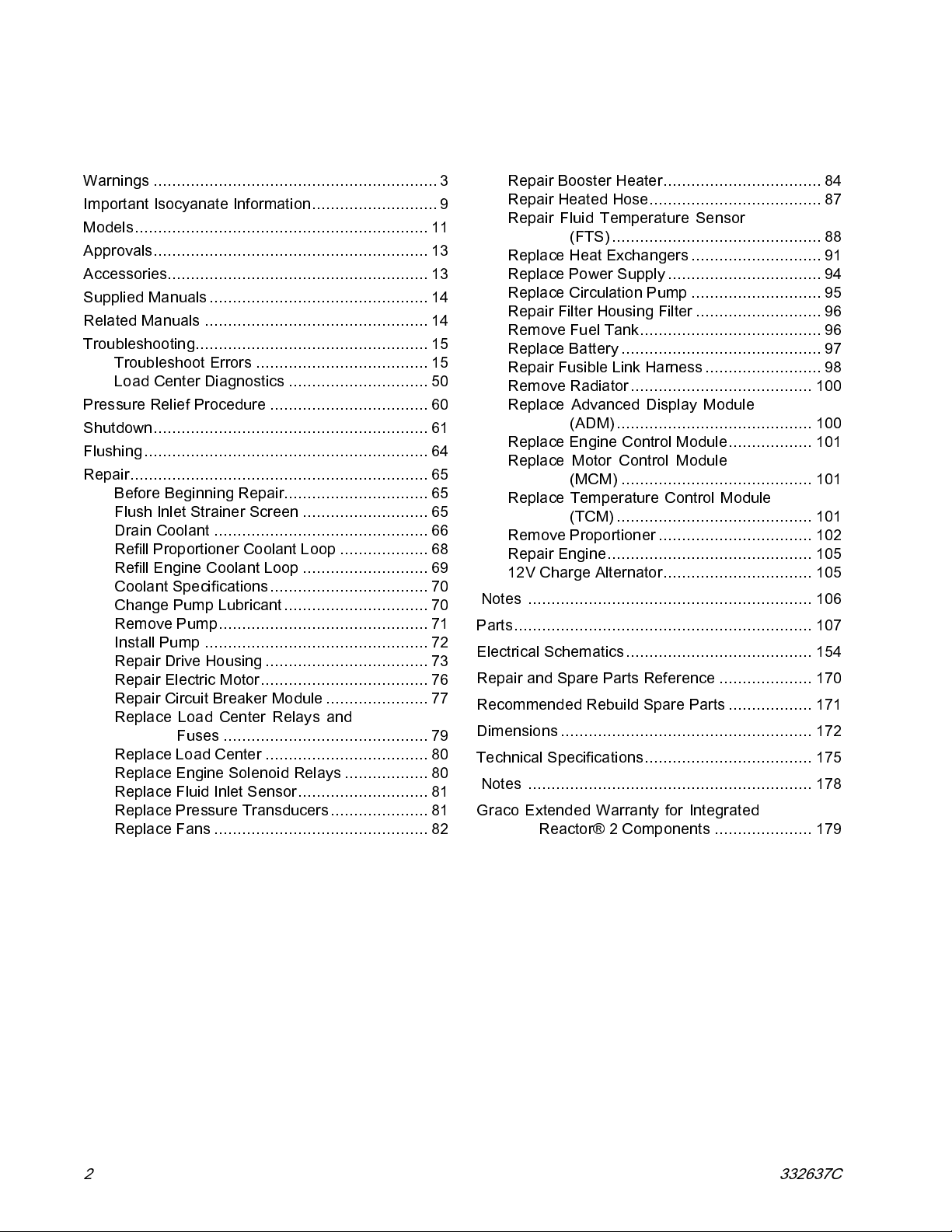
Contents
Warnings .............................................................3
Important Isocyanate Information........................... 9
Models............................................................... 11
Approvals........................................................... 13
Accessories........................................................13
Supplied Manuals............................................... 14
Related Manuals ................................................ 14
Troubleshooting.................................................. 15
Troubleshoot Errors ..................................... 15
Load Center Diagnostics .............................. 50
Pressure Relief Procedure .................................. 60
Shutdown........................................................... 61
Flushing............................................................. 64
Repair................................................................ 65
Before Beginning Repair...............................65
Flush Inlet Strainer Screen ...........................65
Drain Coolant .............................................. 66
Refill Proportioner Coolant Loop ................... 68
Refill Engine Coolant Loop ........................... 69
Coolant Specifications.................................. 70
Change Pump Lubricant............................... 70
Remove Pump............................................. 71
Install Pump ................................................ 72
Repair Drive Housing ................................... 73
Repair Electric Motor.................................... 76
Repair Circuit Breaker Module ...................... 77
Replace Load Center Relays and
Fuses ............................................ 79
Replace Load Center ................................... 80
Replace Engine Solenoid Relays ..................80
Replace Fluid Inlet Sensor............................81
Replace Pressure Transducers ..................... 81
Replace Fans .............................................. 82
Repair Booster Heater.................................. 84
Repair Heated Hose.....................................87
Repair Flui d Temperature Sensor
(FTS).............................................88
Replace Heat Exchangers............................ 91
Replace Power Supply ................................. 94
Replace Circulation Pump ............................ 95
Repair Filter Housing Filter ........................... 96
Remove Fuel Tank....................................... 96
Replace Battery ........................................... 97
Repair Fusible Link Harness.........................98
Remove Radiator....................................... 100
Replace Advanced Display Module
(ADM).......................................... 100
Replace Engine Control Module .................. 101
Replace Motor Control Module
(MCM) ......................................... 101
Replace Temperature Control Module
(TCM) .......................................... 101
Remove Proportioner ................................. 102
Repair Engine ............................................ 105
12V Charge Alternator................................ 105
Notes ............................................................. 106
Parts................................................................ 107
Electrical Schematics........................................ 154
Repair and Spare Parts Reference .................... 170
Recommended Rebuild Spare Parts .................. 171
Dimensions...................................................... 172
Technical Specifications.................................... 175
Notes ............................................................. 178
Graco Extended Warranty for Integrated
Reactor® 2 Components ..................... 179
2
332637C
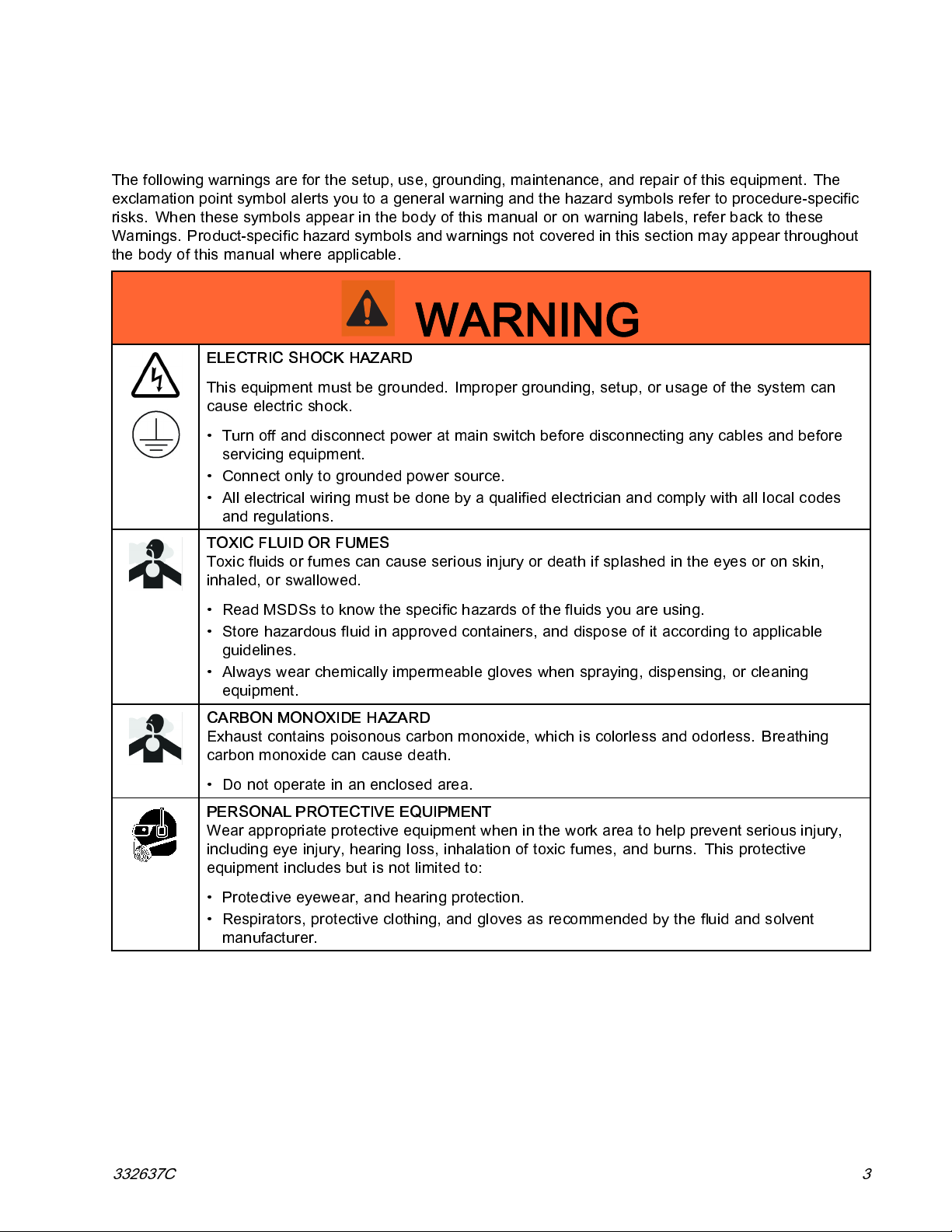
Warnings
Warnings
The following warnings are for the setup, use, grounding, maintenance, and repair of this equipment. The
exclamation p oi nt symbol alerts you t o a general warning and th e hazard symbols refer to procedure-specific
risks. When t hes e symbols appear in th e body of this manual or on w arning labels, refer back t o these
Warnings. Product-specific hazard symbols and warnings not covered in this section may appear throughout
the body of this manual where applicable.
WARNING
ELECTRIC SHOCK HAZARD
This equipment must be grounded. Improper grounding, setup, or usage of the system can
cause electric sh oc k.
• Turn off and disconnect power at main switch before disconnecting any cables and before
servicing equipment.
• Connect only to grounded power source.
• All electrical wiring must be done by a qualified electrician and comply with all local codes
and regulations.
TOXIC FLUID OR FUMES
Toxic fluids or fumes can cause serious injury or death if splashed in the eyes or on skin,
inhaled, or swallo wed.
• Read MSDSs to know the s pec i fic hazards of the fluids you are using.
• Store hazardous fluid in approved containers, and dispose of it accordin g to applicable
guidelines.
• Always wear chemically impermeable gloves when spraying, dispensing, or cleaning
equipment.
CARBON MONOXIDE HAZARD
Exhaust contains poisonou s carbon monoxi de , which is colorless and odorless. Breathing
carbon monoxide can cause death.
• Donotoperateinanenclosedarea.
PERSONAL PROTECTIVE EQUIPMENT
Wear appropriate protective equipmen t when in the work area to help prevent serious inj ury,
including eye injury, hearing loss, inhalation of toxic fumes, and burns. This protective
equipment includes but is not limited to:
• Protective eyewear, and hearing protectio n.
• Respirators, protective clothing, and gloves as recommended by the fluid and solvent
manufacturer.
332637C 3
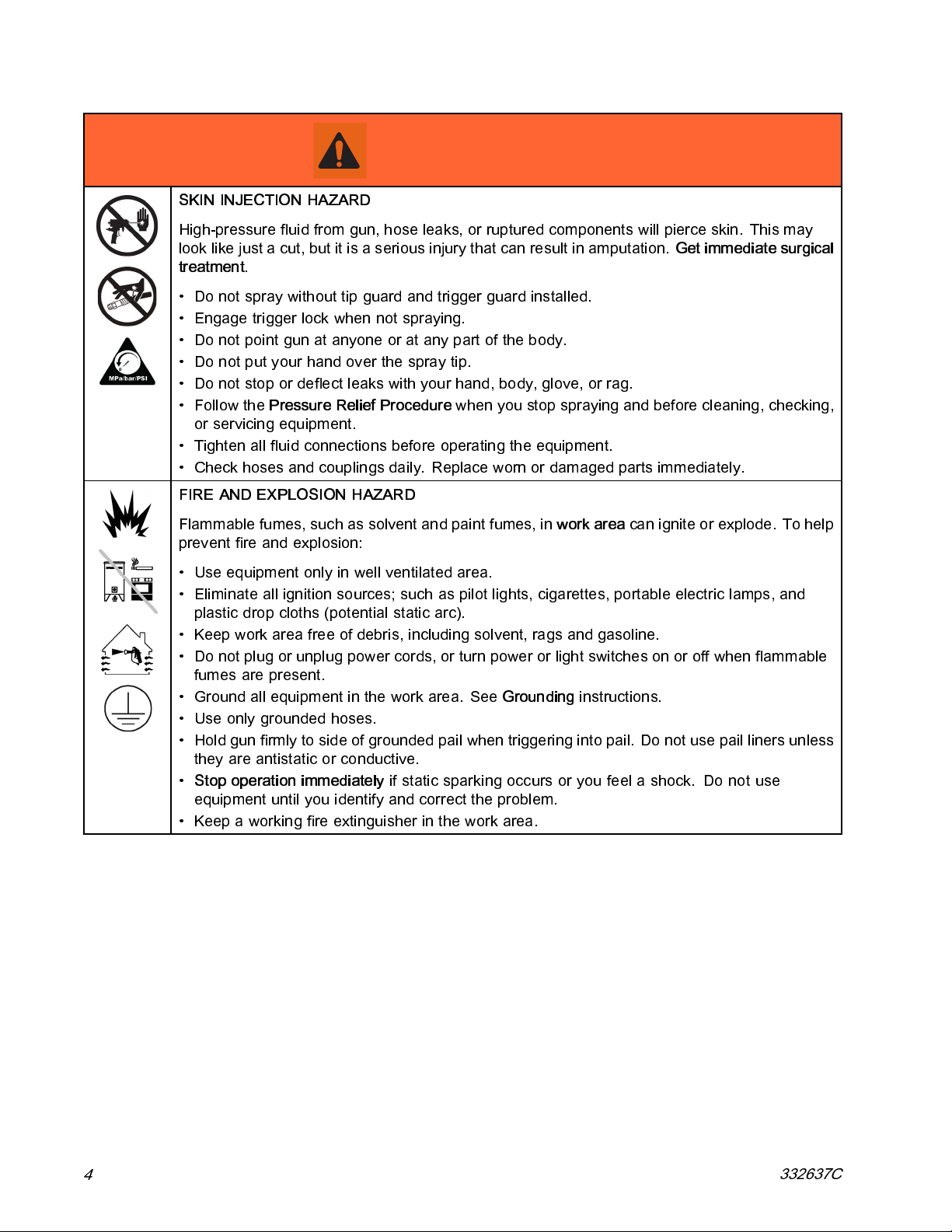
Warnings
WARNING
SKIN INJECTION HAZARD
High-pressure fluid from gun, hose leaks, or ruptured components will pierce skin. This may
look like just a cut, but it is a s erious injury that can result in amputation.
treatment
• Do not s pra y without tip guard and trigger guard installed.
• Engage trigger lock when not spraying.
• Do not point gun at anyone or at any part o f the body.
• Do not put your hand over the spray tip.
• Do not stop or deflect leaks with your hand, body, glove, or rag.
• Follow the
or servicing equipment.
• Tighten all fluid connections before operating the equipment.
• Check hoses and couplings daily. Replace worn or damaged parts immediately.
FIRE AND EXPLOSION HAZARD
.
Pressure Relief Procedure
when you stop spray i ng an d be fore c l ean ing , ch eck ing ,
Get immediate surgical
Flammable fumes, such as solvent and paint fumes, in
prevent fire and explosion:
• Use equipment only in well ventilated area.
• Eliminate all ignition sources; such as pilot lights, cigarettes, portable electric lamps, and
plastic drop cloths (potential static arc).
• Keep work area free of debris, including solvent, rags and gasoline.
• Do not plug or u npl ug power cords, or turn power or light switches on or off when flammable
fumes are present.
• Ground all equipment in the work area. See
• Use only grounded hoses.
• Hold gun firmly to side of grounded pail when triggering into pail. Do not use pail liners unle ss
they are antistatic or conductive.
•
Stop operation immediately
equipment u nti l you identify and correct the problem.
• Keep a working fire extinguisher in the work area.
if static sparking occurs or you feel a shock.Do not use
Grounding
work area
instructions.
canigniteorexplode.Tohelp
4
332637C
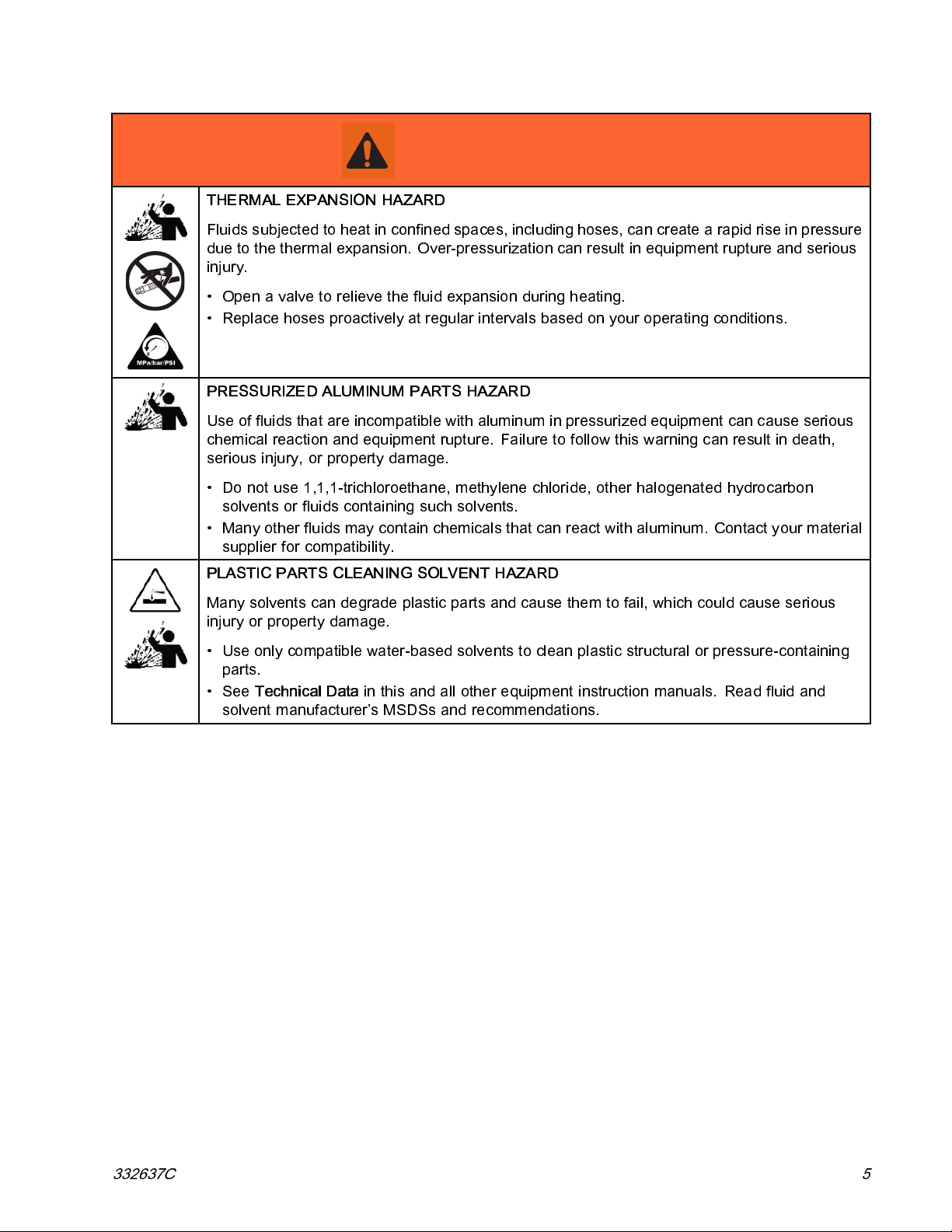
Warnings
WARNING
THERMAL EXPANSION HAZARD
Fluids subjected to heat in confined s paces, includin g hoses, can create a rapid rise in pressure
due to the thermal expansion. Over-pressurization can result in equipment rupture and serious
injury.
• Openavalvetorelievethefluidexpansionduringheating.
• Replace hoses proactively at regular intervals based on your operating conditions.
PRESSURIZED ALUMINUM PARTS HAZARD
Use of fluids that are incompatible with aluminum in pressurized equipment can cause serious
chemical reaction and equipment rupture. Failure to follow this warning can result in death,
serious injury, or property damage.
• Do not use 1,1,1-trichloroethane, methylene chloride, other halogenated hydrocarbon
solvents or fluids containing such solvents.
• Many other fluids may contain chemicals that can react with aluminum . Contac t y ou r mate rial
supplier for compatibility.
PLASTIC
Many solvents can degrade plastic parts and cause them to fail, which could cause serious
injury or property damage.
• Use only compatible water-based solvents to clean plastic structural or press ure-containing
parts.
•See
solvent manufacturer’s MSDSs and recommendations.
PARTS CLEANING SOLVENT HAZARD
Technical Data
in this and all other equipment instruction ma nua ls . Read fluid and
332637C 5
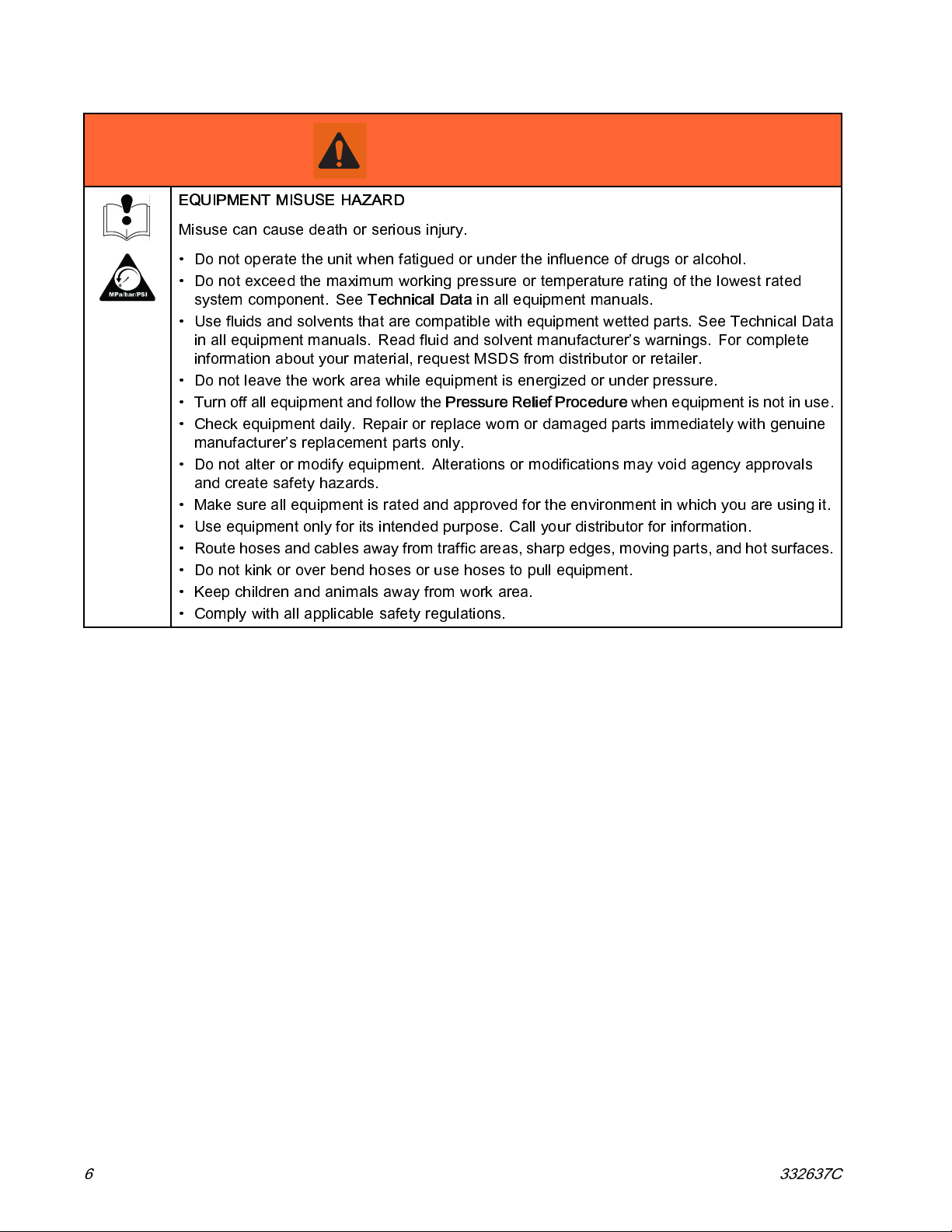
Warnings
WARNING
EQUIPMENT MISUSE HAZARD
Misuse can cause death or serious injury.
• Do not operate the unit when fatigued or under the influence of drugs or alcohol.
• Do not exceed the maximum working pressure or temperature rating of the lowest rated
system component. See
• Use fluids and solvents that are compatible with equipment wetted parts. See Technical Data
in all equipment manuals. Read fluid and solvent manufacturer’s warnings. For complete
information about your material, request MSDS from distributor or retailer.
• Do not leave the work area while equipment is energized or under pressure.
• Turn off all equip ment and follow the
• Check equipment daily. Repair or replace worn or damaged parts immediately with genuine
manufacturer’s replacement parts only.
• Do not alter or modify equipment. Alterations or modifications may void agency approvals
and crea te safety hazards.
• Make sure all equipment is rated and approved for the environment in which you are using it.
• Use equipment only for its intended purpose. Call your distributor for information.
• Route hoses and cab les away from traffic areas, s ha rp edges, moving parts, and hot su rfac es .
• Do not kink or over bend hoses or use hoses to pull equipment.
• Keep children and animals away from work area.
• Comply with all applicable safety regulations.
Technical Data
Pressure Relief Procedure
in all equipment manuals.
when equipment is not in use.
6 332637C
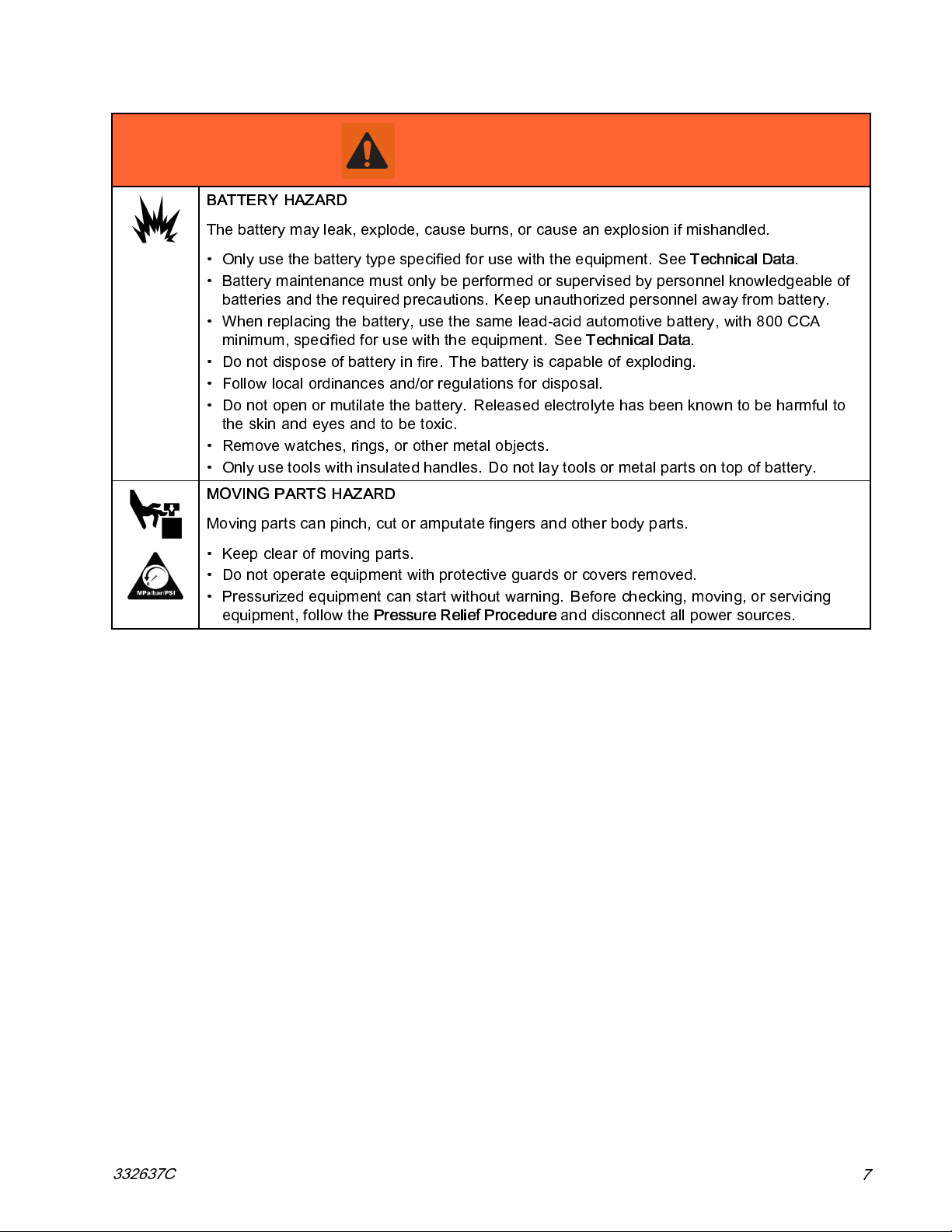
WARNING
BATTERY HAZARD
The battery may leak, explode, cause burns, or cause an explosion if mishandled.
Warnings
• Only use the battery type specified for use with the equipment. See
• Battery maintenance must only be performed or supervised by personnel knowledgeable of
batteries and the required precautions. Keep unauthorized person nel away from battery.
• When replacing the battery, use the same lead-acid automotive battery, with 800 CCA
minimum, specified for use with the equipment. See
• Do not dispose of battery in fire. The battery is capable of exploding.
• Follow local ordinances and/or regulations for disposal.
• Donotopenormutilatethebattery. Releasedelectrolytehasbeenknowntobeharmfulto
theskinandeyesandtobetoxic.
• Remove watches, rings, or other metal objects.
• Only use tools with insulated handles. Do not lay tools or metal parts on top of battery.
MOVING PARTS HAZARD
Moving parts can pinch, cut or amputate fingers and other bo dy parts.
• Keep clear of moving parts.
• Do not operate equipment with protective guards or covers removed.
• Pressurized equipment can start without warning. Be fore checking, m ov ing, or servicing
equipment, fol low the
Pressure Relief Procedure
Technical Data
and disconnect all power sources.
Technical Data
.
.
332637C
7
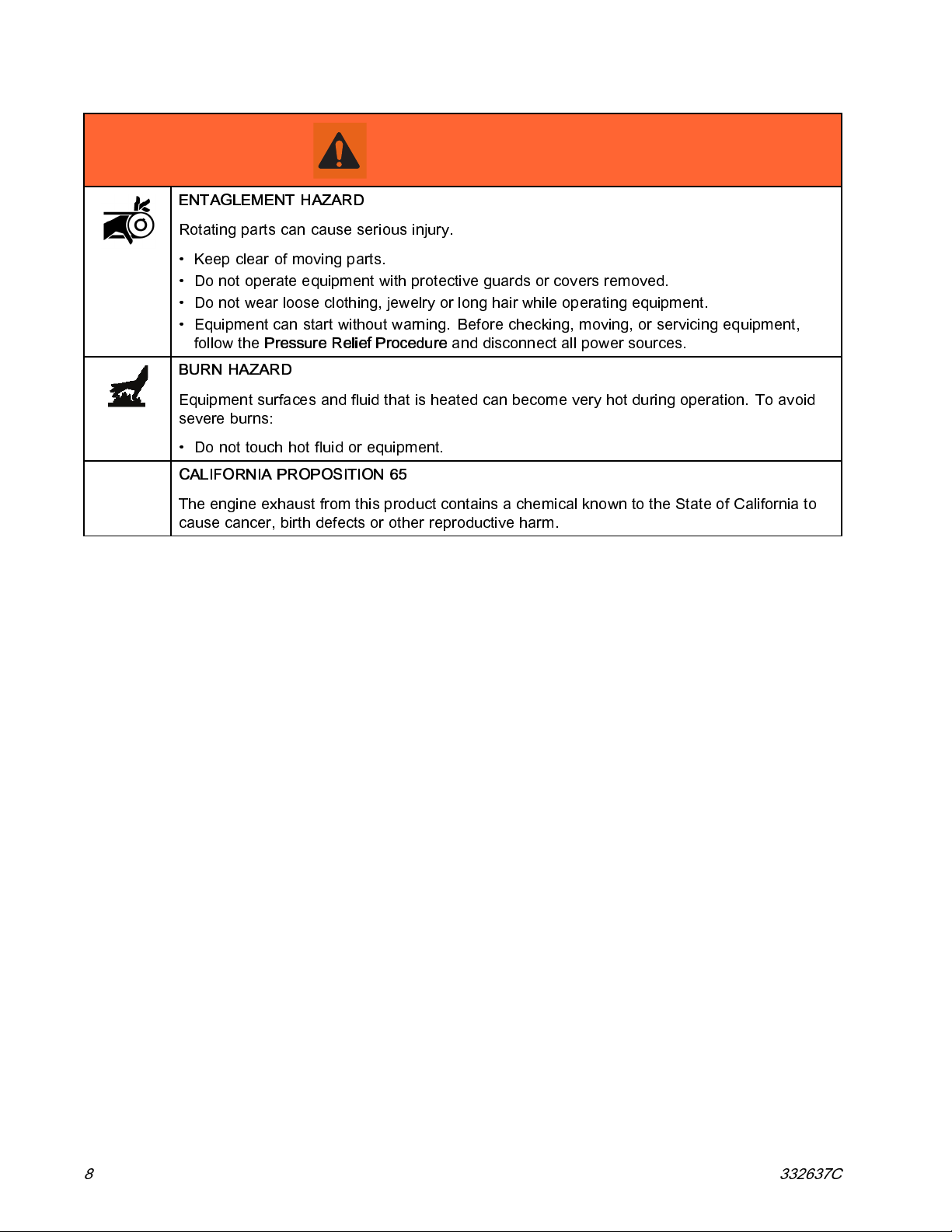
Warnings
WARNING
ENTAGLEMENT HAZARD
Rotating parts can cause serious injury.
• Keep clear of moving parts.
• Do not operate equipment with protective guards or covers removed.
• Do not wear l oo se clothing, jewelry or long hair while operating equipment.
• Equipment can start without warning. Before checking, moving, or servicing equipment,
follow the
BURN HAZARD
Equipment surfaces and fluid that is heated can become very hot during operation. To avoid
severe burns:
• Do not touch hot fluid or equipment.
CALIFORNIA PROPOSITION 65
The engine exhaust from this product contains a chemical known to the State of California to
cause cancer, birth defects or other reproductive harm.
Pressure Relief Procedure
and disconnect all power sources.
8 332637C
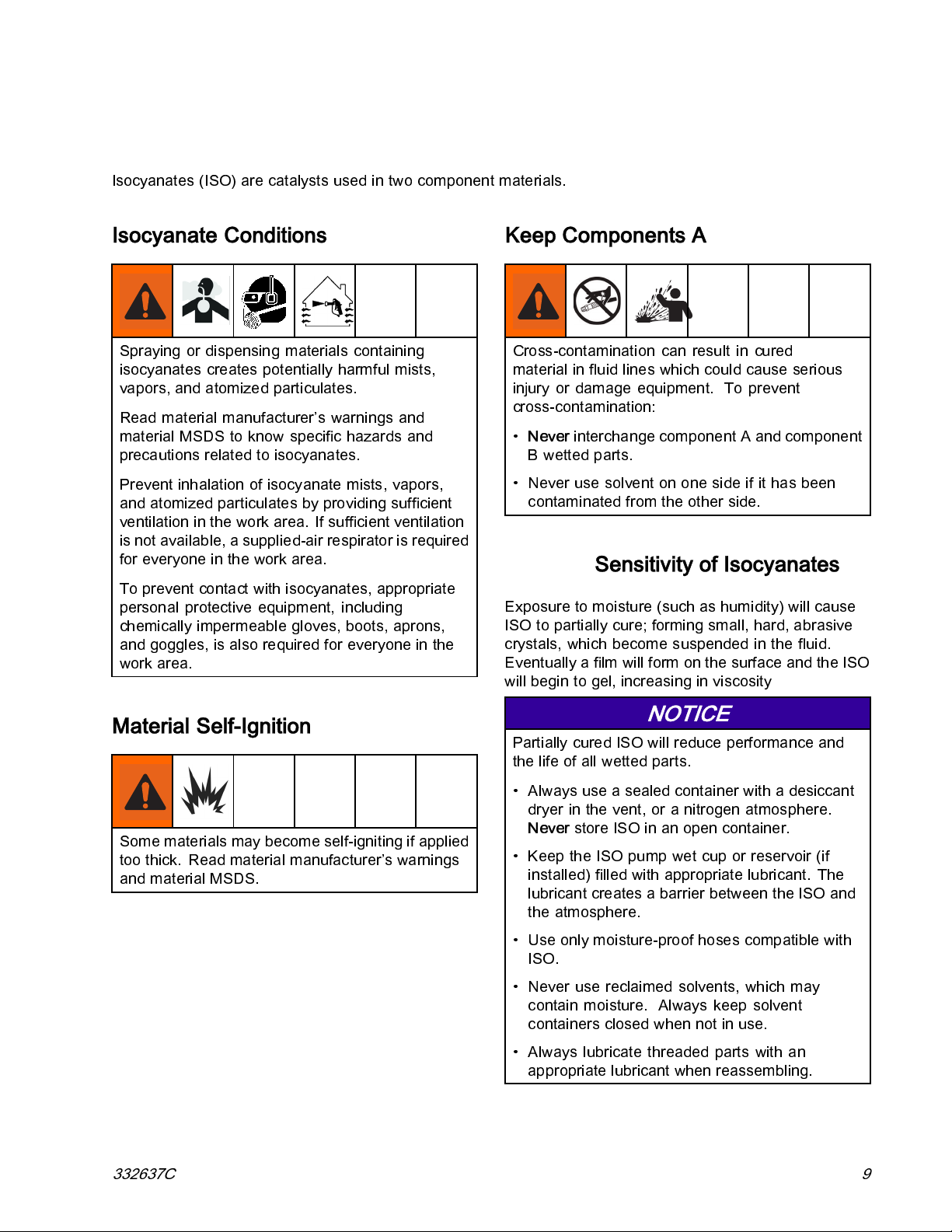
Important Isocyanate Information
Isocyanates (ISO) are catalysts used in two component materials.
Important Isocyanate Information
Isocyanate Conditions
Spraying or dispensing materials containing
isocyanates creates potentially harmful mis ts,
vapors, and atomized particulates.
Read material manufacturer’s warnings and
material MSDS to know specific hazards and
precautions related to isocyanates.
Prevent i nh ala tio n of isocy ana te mists, vapors,
and atomized particulates by providing sufficient
ventilation in the work area. If suffic i ent ventilation
is not available, a supplied-air respirator is required
for everyone in the work area.
To prevent contact with isocyanates, appropriate
personal protective equipment, in cluding
chemically impermeable gloves, boots , aprons,
and goggles, is also required for everyone in the
work area.
Keep Components A and B Separate
Cross-contamination can result in cured
material in fluid lines which could cause serious
injury or damage equipment. To prevent
cross-contamination:
•
Never
interchange component A and component
B wetted parts.
• Never use solvent on one side if it has been
contaminated from the other si de.
Moisture Sensitivity of Isocyanates
Exposure to moisture (such as humidity) will cause
ISO to partially cure; forming small, hard, abrasiv e
crystals, which become suspended in the fluid.
Eventually a film will form on the surface and the ISO
will begin to gel, increasing in viscosity
Material Self-Ignition
Some materials may become self-igniting if applied
too thick. Read material manufacturer’s warnings
and material MSDS.
NOTICE
Partially cured ISO will reduce performance and
the life of all wetted parts .
• Always use a sealed container with a desiccant
dryer i n the vent, or a nitrogen atmosphere.
Never
store ISO in an open container.
• Keep the ISO pump wet cup or reserv oi r (if
installed) filled with appropriate lubricant. The
lubricant creates a barrier between the ISO and
the atmosphere.
• Use only moisture-proof hoses compatible with
ISO.
• Never use reclaimed solvents, which may
contain moisture. Always keep solvent
containers closed when not in use.
• Always lubricate threaded parts with an
appropriate lubrica nt when reassembling.
332637C 9
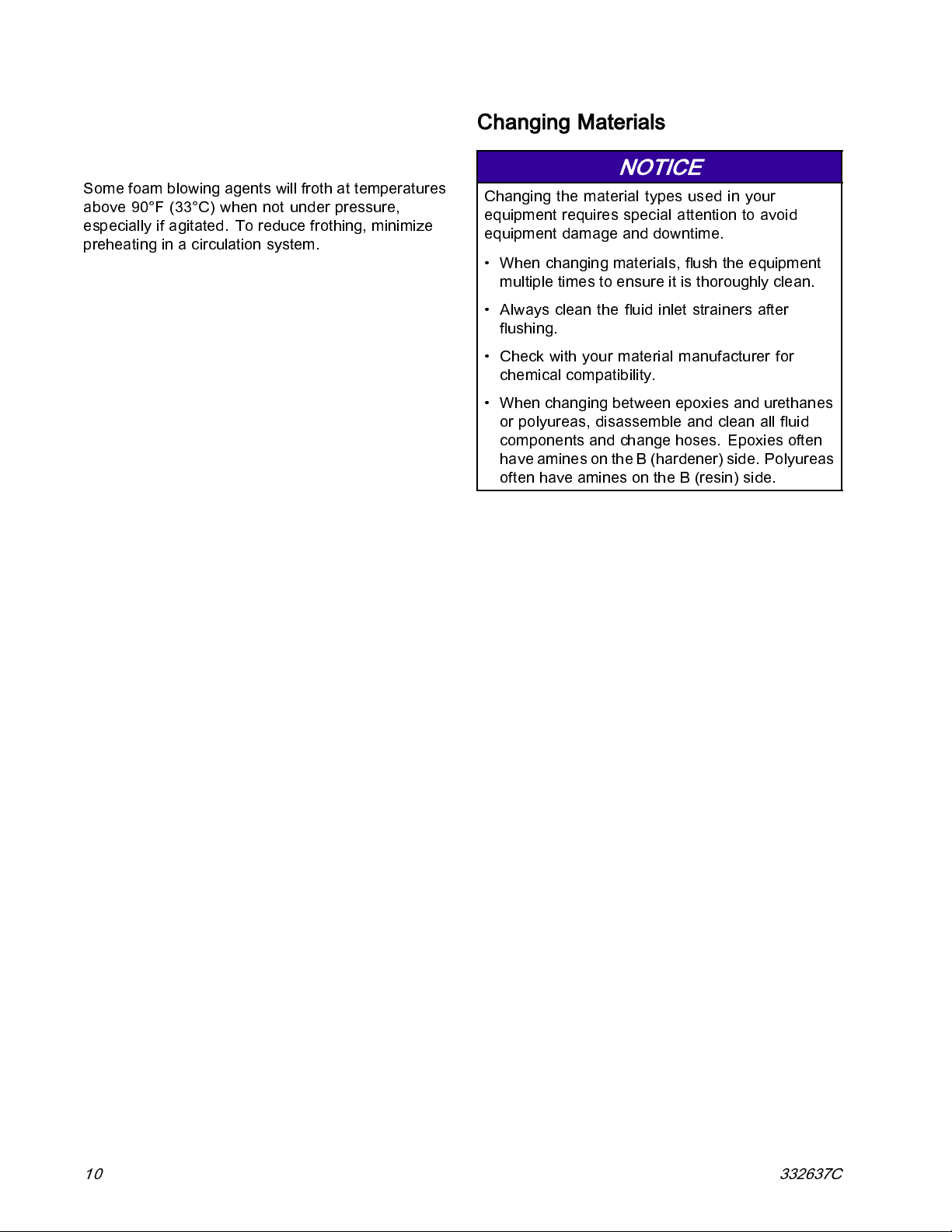
Important Isocyanate Information
Foam Resins with 245 fa Blowing
Agents
Some foam blowing agents will froth at temperatures
above 90°F (33°C) when not und er pressure,
especially if agitated. To reduce frothing, minimize
preheating in a circulation system.
Changing Materials
NOTICE
Changing the material types used in your
equipment requires special attention to avoid
equipment damage and downtime.
• When changing materials, flush the equipment
multiple times to ensure it is thoroughly clean.
• Always clean the fluid inlet strainers after
flushing.
• Check with your materi al manufacturer for
chemical compatibility.
• When changing between epoxies and urethanes
or polyureas, disassemble and clean all fluid
components and change hose s. Epoxies o ften
have amines on the B (hardener) side. Polyureas
often have amines on the B (resin) side.
10 332637C
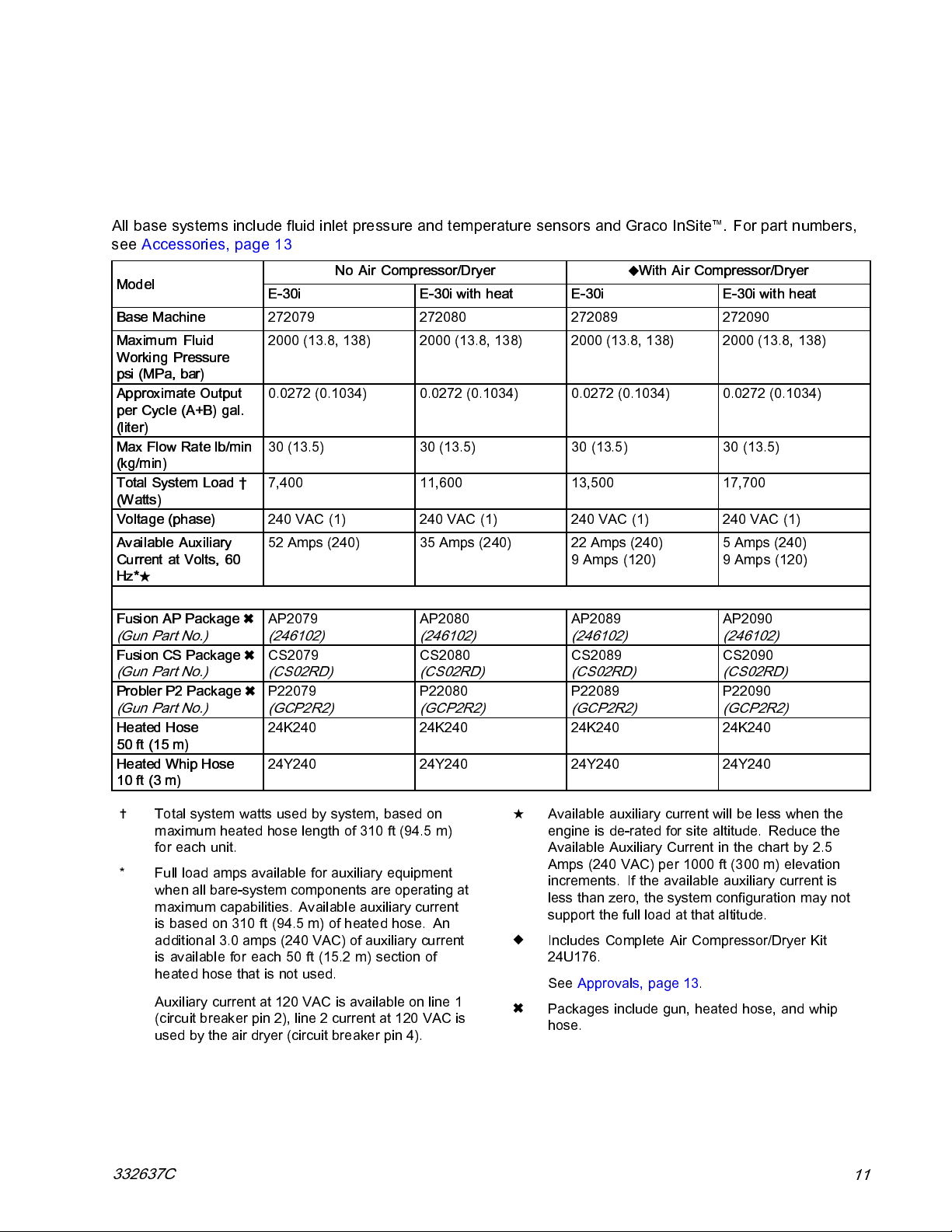
Models
Models
Reactor 2 E-30i Elite
All base systems include fluid inlet pressure and temperature sensors and Graco InSite™. For part numbers,
see Accessories, page 13
Model
Base Machine
Maximum Fluid
Working Pressure
psi (MPa, bar)
Approximate Output
per Cycle (A+B) gal.
(liter)
Max Flow Rate lb/min
(kg/min)
Total System Load †
(Watts)
Voltage (phase)
Available Auxiliary
Current at Volts, 60
Hz*
No Air Compressor/Dryer
E-30i E-30i with heat E-30i E-30i with heat
272079 272080 272089 272090
2000 (13.8, 138) 2000 (13.8, 138) 2000 (13.8, 138) 2000 (13.8, 138)
0.0272 (0.1034) 0.0272 (0.1034) 0.0272 (0.1034) 0.0272 (0.1034)
30 (13.5) 30 (13.5) 30 (13.5) 30 (13.5)
7,400 11,600 13,500 17,700
240 VAC (1) 240 VAC (1) 240 VAC (1) 240 VAC (1)
52 Amps (240) 35 Amps (240) 22 Amps (240)
9 Amps (120)
With Air Compressor/Dryer
5 Amps (240)
9 Amps (120)
Fusion AP Package
(Gun Part No.)
Fusion CS Package
(Gun Part No.)
Probler P2 Package
(Gun Part No.)
Heated Hose
50 ft (15 m)
Heated Whip Hose
10 ft (3 m)
Total system watts used by system, based on
maximum heated hose length of 310 ft (94.5 m)
for each unit.
* Full load amps available for auxiliary equipment
when all bare-system components are operating at
maximum capabilities. Available auxiliary current
is based on 310 ft (94.5 m) of heated hose. An
additional 3.0 amps (240 VAC) of auxiliary current
is available for each 50 ft (15.2 m) section of
heated hose that is not used.
liary current at 120 VAC is available on line 1
Auxi
rcuit breaker pin 2), line 2 current at 120 VAC is
(ci
d by the air dryer (circuit breaker pin 4).
use
AP2079
(246102)
CS2079
(CS02RD)
P22079
(GCP2R2)
24K240 24K240 24K240 24K240
24Y240 24Y240 24Y240 24Y240
AP2080
(246102)
CS2080
(CS02RD)
P22080
(GCP2R2)
AP2089
(246102)
CS2089
(CS02RD)
P22089
(GCP2R2)
Available auxiliary current will be less when the
engine is de-rated for site altitude. Reduce the
Available Auxiliary Current in the chart by 2.5
Amps (240 VAC) per 1000 ft (300 m) elevation
increments. If the available auxiliary current is
less than zero, the system configuration may not
support the full load at that altitude.
Includes Complete Air Compressor/Dryer Kit
24U176.
See Approvals, page 13.
Packages include gun, heated hose, and whip
hose.
AP2090
(246102)
CS2090
(CS02RD)
P22090
(GCP2R2)
332637C
11
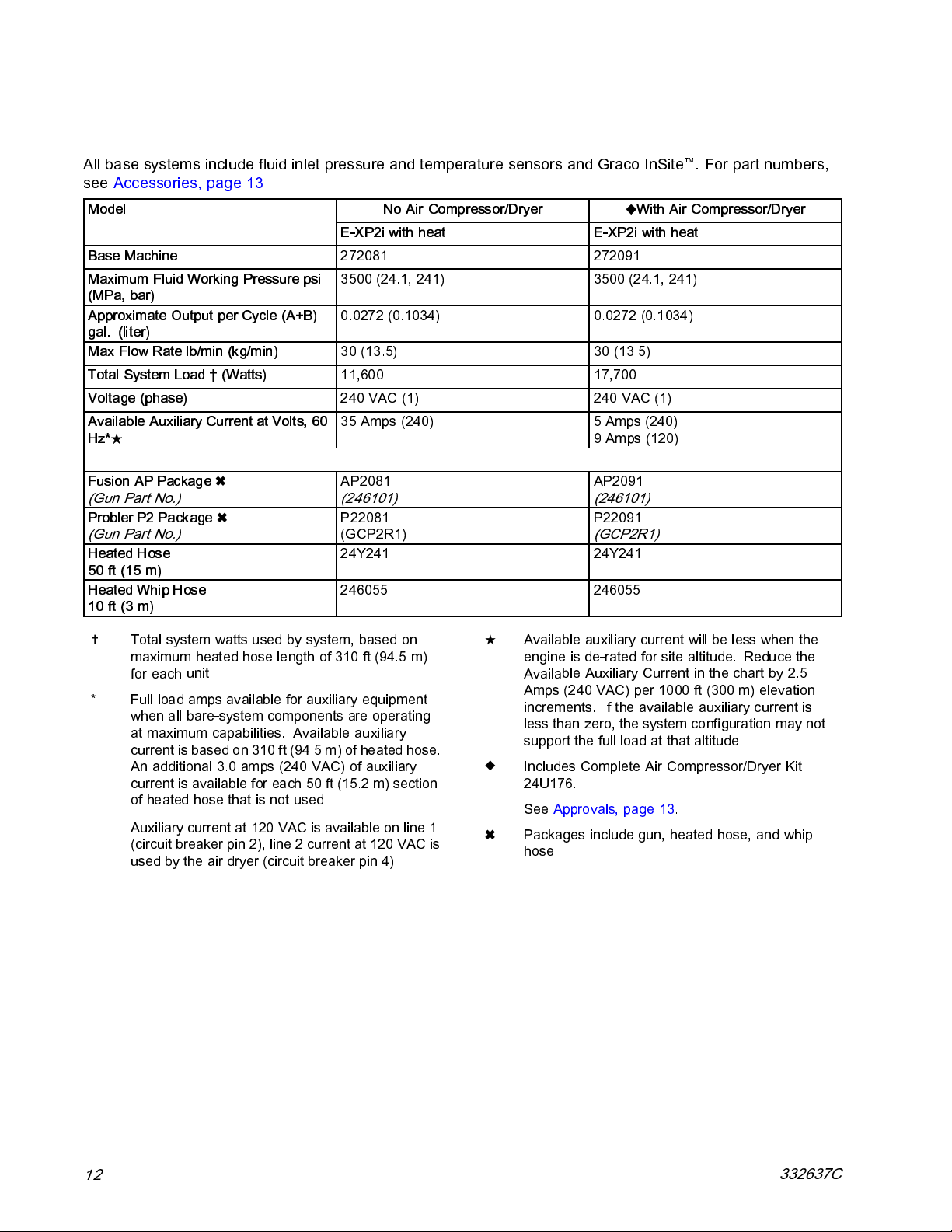
Models
Reactor 2 E-XP2i Elite
All base systems include fluid inlet pressure and temperature sensors and Graco InSite™. For part numbers,
see Accessories, page 13
Model
Base Machine
Maximum Fluid Working Pressure psi
(MPa, bar)
Approximate Output per Cycle (A+B)
gal. (liter)
MaxFlowRatelb/min(kg/min)
Total System Load † (Watts)
Voltage (phase)
Available Auxiliary Current at Volts, 60
Hz*
No Air Compressor/Dryer
E-XP2i with heat E-XP2i with heat
272081 272091
3500 (24.1, 241) 3500 (24.1, 241)
0.0272 (0.1034) 0.0272 (0.1034)
30 (13.5) 30 (13.5)
11,600 17,700
240 VAC (1) 240 VAC (1)
35 Amps (240) 5 Amps (240)
With Air Compressor/Dryer
9 Amps (120)
Fusion AP Package
(Gun Part No.)
Probler
(Gun Par
Heated H
50 ft (15
Heated
10 ft (3
P2 Package
t No.)
ose
m)
Whip Hose
m)
Total sy
maximum
for each
* Full load amps available for auxiliary equipment
when all bare-sys tem components are operating
at maximum capabilities. Available auxiliary
current is based on 310 ft (94.5 m) of heated hose.
An additional 3.0 amps (240 VAC) of auxiliary
current is available for each 50 ft (15.2 m) section
of heated hose that is not used.
Auxiliary current at 120 VAC is available on line 1
(circuit breaker pin 2), line 2 current at 120 VAC is
used by the air dryer (circuit breaker pin 4).
stem watts used by system, based on
heated hose length of 310 ft (94.5 m)
unit.
AP2081
(246101)
P22081
(GCP2R1)
24Y241 24Y241
246055 246055
AP2091
(246101)
P22091
(GCP2R1)
ble auxiliary current will be less when the
Availa
is de-rated for site altitude. Reduce the
engine
ble Auxiliary Current in the chart by 2.5
Availa
Amps (2
increm
less th
suppor
Includes Complete Air Compressor/Dryer Kit
24U176.
See Approvals, page 13.
Packages include gun, heated hose, and whip
hose.
40 VAC) per 1000 ft (300 m) elevation
ents. If the available auxiliary current is
an zero, the system configuration may not
t the full load at that altitude.
12
332637C
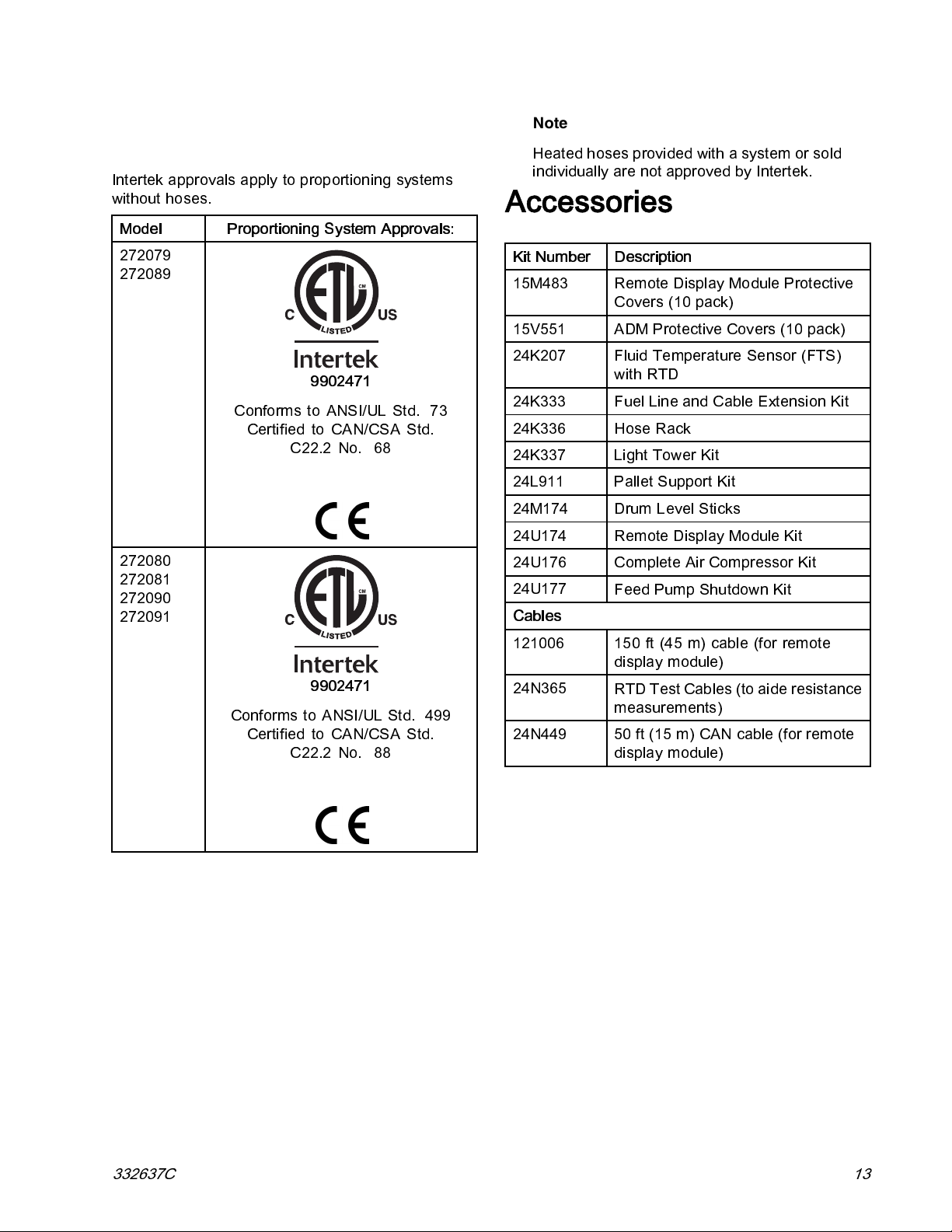
Approvals
Approvals
Intertek approvals apply to proportioning systems
without hoses.
Model
272079
272089
272080
272081
272090
272091
Proportioning System Approvals:
9902471
Conforms to ANSI/UL Std. 73
Certified to CAN/CSA Std.
C22.2 No. 68
Note
Heated hoses provided with a system or sold
individually are not approved by Intertek.
Accessories
Kit Number Description
15M483 Remote Display Module Protective
Covers (10 pack)
15V551
24K207
24K333 Fuel Line and Cable Extension Kit
24K336 Hose Rack
24K337 Light Tower Kit
24L911
24M174 Drum Level Sticks
24U174 Remote Display Module Kit
24U176
24U177
Cables
ADM Protective Covers (10 pack)
Fluid Temperature Sensor (FTS)
with RTD
Pallet Support Kit
Complete Air Compressor Kit
Feed Pump Shutdown Kit
9902471
rms to ANSI/UL Std. 499
Confo
fied to CAN/CSA Std.
Certi
C22.2
No. 88
121006 150 ft (45 m) cable (for remote
display module)
24N365
24N449
RTD Test Cables (to aide resistance
measurements)
50ft(15m)CANcable(forremote
display module)
332637C 13
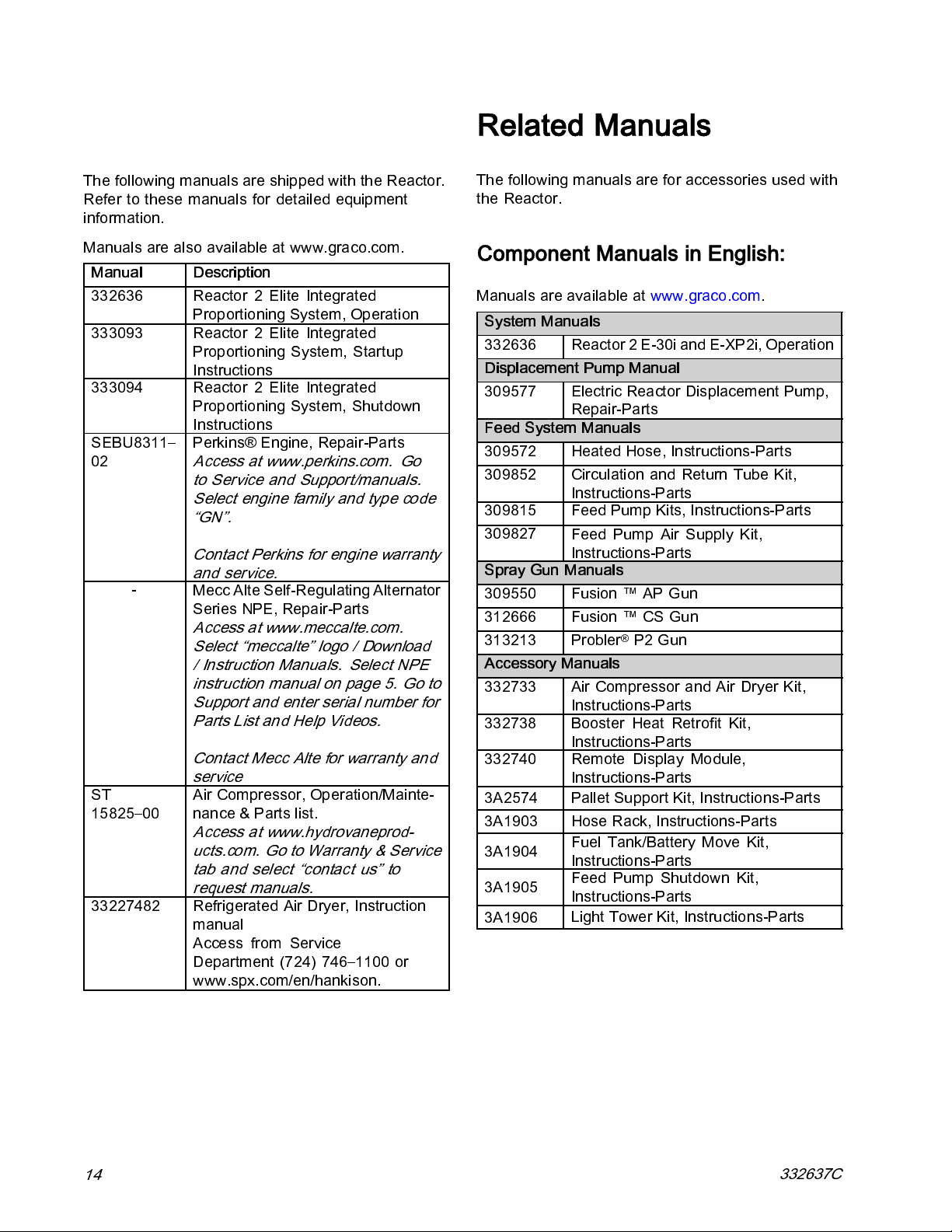
Supplied Manuals
Supplied Manuals
The following m anu al s are shipped with the Reac to r.
Refer to these manuals for detailed equi pm ent
information.
Manuals are also available at www.graco.com.
Manual Description
332636 Reactor 2 Elite Integrated
Proportioning System, Operation
333093 Reactor 2 Elite Integrated
Proportioning System, Startup
Instructions
333094 Reactor 2 Elite Integrated
Proportioning System, Shutdown
Instructions
SEBU8311–02Perkins® Engine, Repair-Parts
Access at www.perkins.com. Go
to Service and Support/manuals.
Select engine family and type code
“GN”.
Contact Perkins for engine warranty
and service.
-
ST
15825–00
33227482
Mecc Alte Self-Regulating Alternator
Series NPE, Repair-Parts
Access at www.meccalte.com.
Select “meccalte” logo / Download
/ Instruction Manuals. Select NPE
instruction manual on page 5. Go to
Support and enter serial number for
Parts List and Help Videos.
Contact Mecc Alte for warranty and
service
Air Compressor, Operation/Mainte-
nance & Parts list.
Access at www.hydrovaneprod-
ucts.com. Go to Warranty & Service
tab and select “contact us” to
request manuals.
Refrigerated Air Dryer, Instruction
manual
Access from S e rvice
Department (724) 746–1100 or
www.spx.com/en/hank i son.
Related Manuals
The following manuals are for accessories used with
the Re ac tor.
Component Manuals in English:
Manuals are available at www.graco.com.
System Manuals
332636
Displacement Pump Manual
309577 Electric Reactor Displacement Pump,
Feed System Manuals
309572 Heated Hose, Instructions-Parts
309852
309815 Feed Pump Kits, Instructions-Parts
309827
Spray Gun Manuals
309550 Fusion ™ AP Gun
312666 Fusion ™ CS Gun
313213 Probler®P2 Gun
Accessory Manuals
332733 Air Compressor and Air Dryer Kit,
332738
332740 Remote Display Module,
3A2574
3A1903 Hose Rack, Instructions-Parts
3A1904
3A1905
3A1906
Reactor 2 E-30i and E-XP2i, Operation
Repair-Parts
Circulation and Return Tube Kit,
Instructions-Parts
Feed Pump Air Supply Kit,
Instructions-Parts
Instructions-Parts
Booster Heat R etrofit Kit,
Instructions-Parts
Instructions-Parts
Pallet Support Kit, Instructions-Parts
Fuel Tank/Battery Move Kit,
Instructions-Parts
Feed Pump Shutdown Kit,
Instructions-Parts
Light Tower Kit, Instructions-Parts
14
332637C
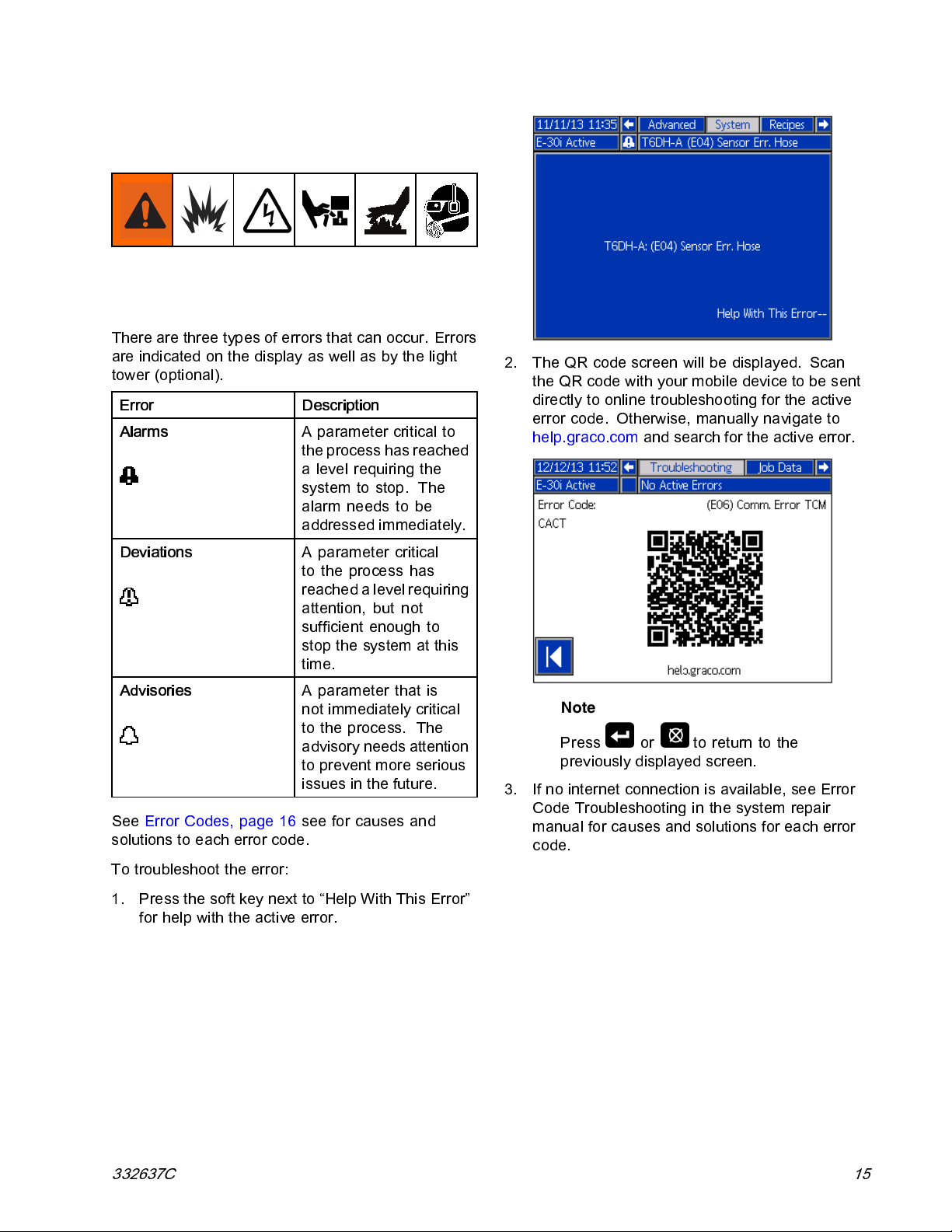
Troubleshooting
Troubleshoot Errors
There are three types of errors that can occur. Errors
are indicated on the display as well as by the light
tower (optional).
Error Description
Alarms
A parameter critical to
the process has reached
a level requiring the
system to stop. The
alarm needs to be
addressed immediately.
Troubleshooting
2. TheQRcodescreenwillbedisplayed. Scan
the QR code with your mobile device to be sent
directly to online troubleshooting for the active
error code. Otherwise, manually navigate to
help.graco.com and search for the active error.
Deviations
Advisories
See Error Codes, page 16 see for causes and
solutions to each error code.
To troublesh oot the error:
1. Press the s oft key next to “Help With This Error”
forhelpwiththeactiveerror.
A parameter critical
to the process has
reacheda level requiring
attention, but not
sufficient enough to
stop the system at this
time.
A parameter that is
not immediately critical
to the process. The
advisory needs attention
to prevent more serious
issues in the future.
3. If no i
Code T
manu
code
Note
Press
previ
nternet connection is available, see Error
roubleshooting in the system repair
al for causes and solutions for each error
.
or to return to the
ously displayed screen.
332637C 15
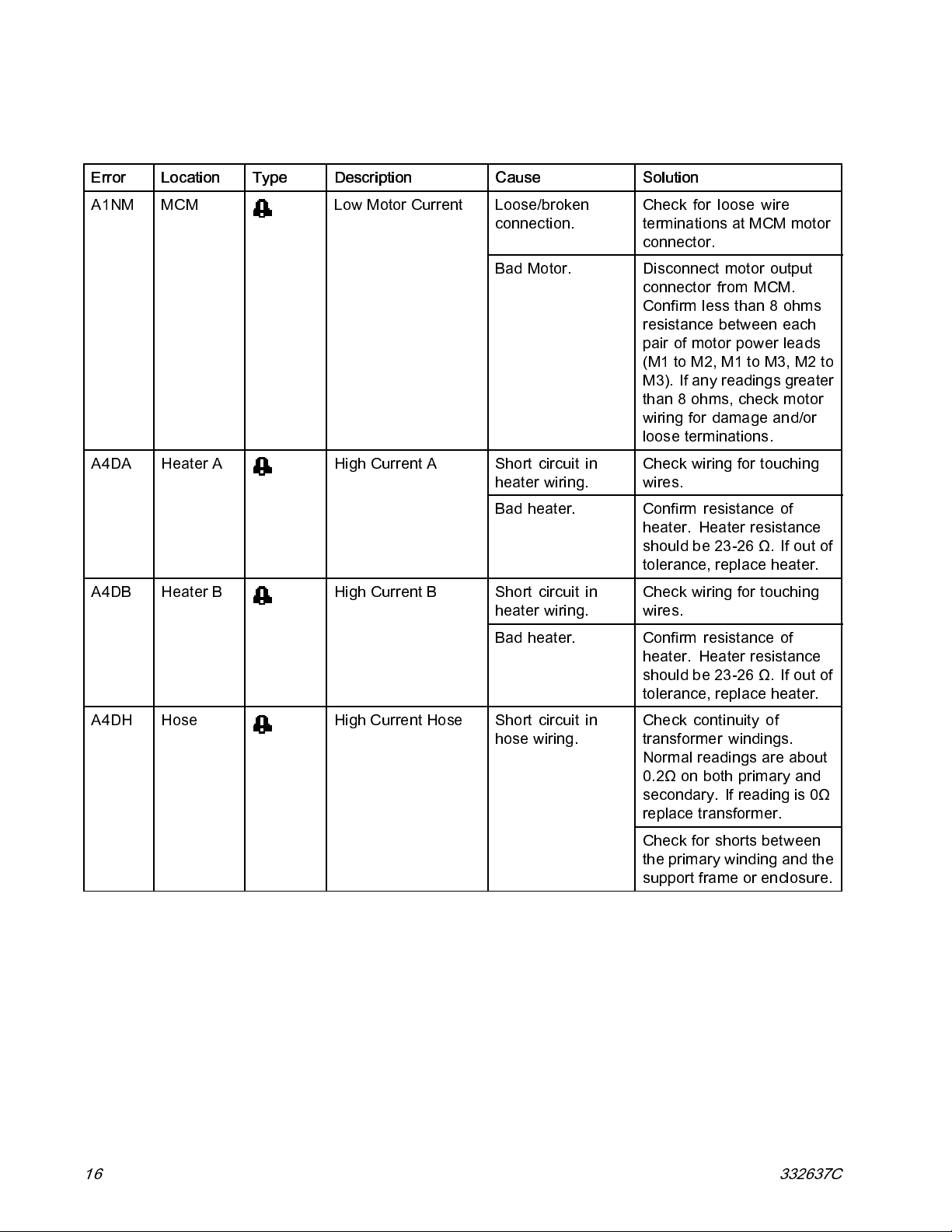
Troubleshooting
Error Codes
Error Location Type Description Cause Solution
A1NM
A4DA Heater A
A4DB Heater B High Current B
MCM
Low Motor Current
High Current A
Loose/broken
connection.
Bad Motor. Disconnect motor output
Short circuit in
heater wiring.
Bad heater.
Short circuit in
heater wiring.
Bad heater.
Check for loose wire
terminations at MCM motor
connector.
connector from MCM.
Confirm less than 8 ohms
resistance between each
pair of motor power leads
(M1toM2,M1toM3,M2to
M3). If any readings greater
than 8 ohms, check motor
wiring for damage and/or
loose terminations.
Check wiring for touching
wires.
Confirm resistance of
heater. Heater re si stanc e
should be 23-26 Ω. If out of
tolerance, replace heater.
Check wiring for touching
wires.
Confirm resistance of
heater. Heater re si stanc e
should be 23-26 Ω. If out of
tolerance, replace heater.
A4DH Hose
High Current Hose Short circuit in
hose wiring.
Check continuity of
transformer windings.
Normal readings are about
0.2Ω on both primary and
secondary. If reading is 0Ω
replace transformer.
Check for shorts between
the p rimary windin g and the
support frame or enclosure.
16 332637C
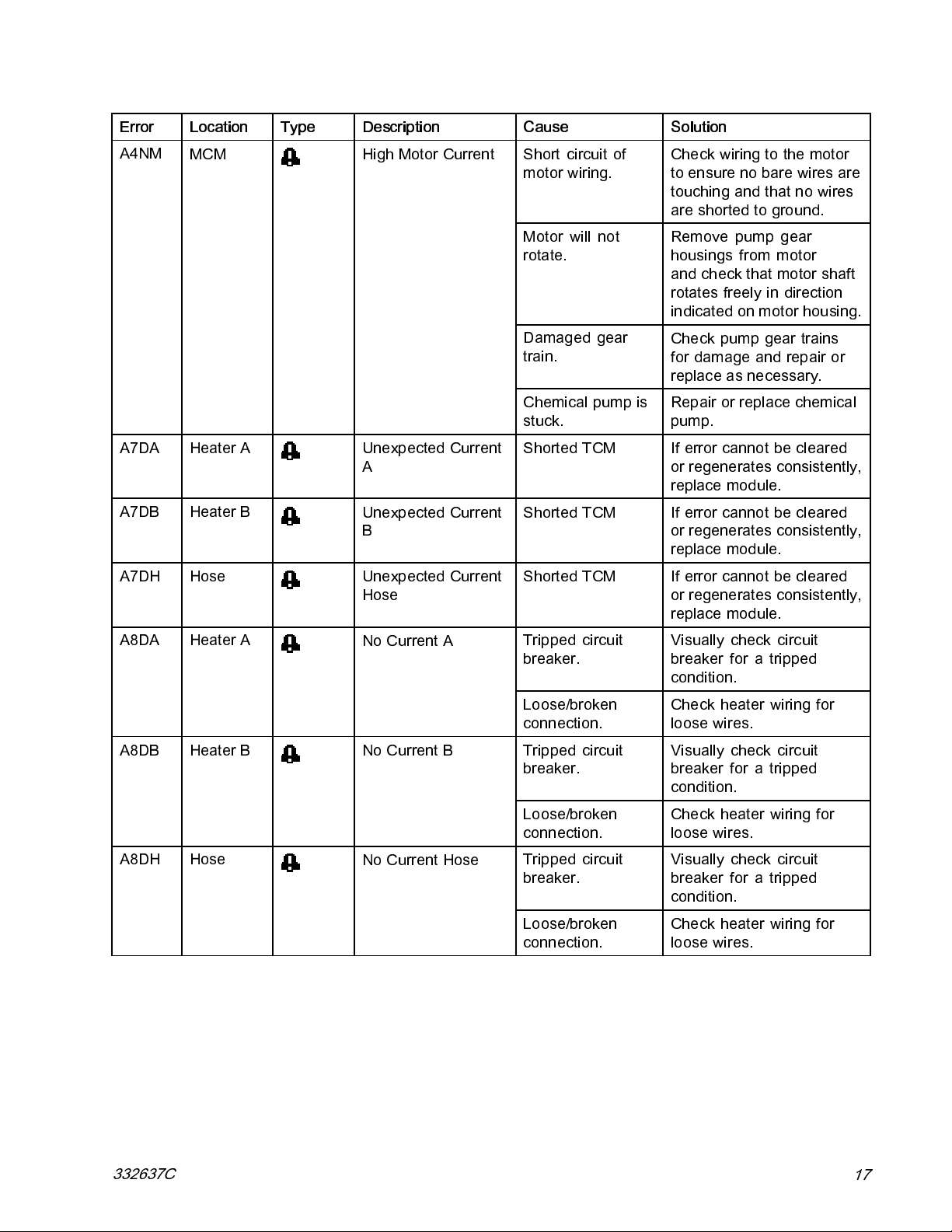
Troubleshooting
Error Location Type Description
A4NM
A7DA Heater A
A7DB Heater B
A7DH Hose
MCM
High Motor Current
Unexpected CurrentAShorted TCM If error cannot be cleared
Unexpected CurrentBShorted TCM If error cannot be cleared
Unexpected Current
Hose
Cause Solution
Short circuit of
motor wiring.
Motor will not
rotate.
Damaged gear
train.
Chemical pump is
stuck.
Shorted TCM If error cannot be cleared
Check wiring to the motor
to ensure no bare wires are
touching and that no wires
are shorted to ground.
Remove pump gear
housings from motor
and check that motor shaft
rotates freely in direction
indicated on motor housing.
Check pump gear trains
for damage and repair or
replace as necessary.
Repair or replace chemical
pump.
or regenerates consistently,
replace module.
or regenerates consistently,
replace module.
or regenerates consistently,
replace module.
A8DA Heater A
A8DB Heater B
A8DH Hose
No Current A
No Current B
No Current Hose
Tripped circuit
breaker.
Loose/broken
connection.
Tripped circuit
breaker.
Loose/broken
connection.
Tripped circuit
breaker.
Loose/broken
connection.
Visually check circuit
breaker for a tripped
condition.
Check heater wiring for
loose wires.
Visually check circuit
breaker for a tripped
condition.
Check heater wiring for
loose wires.
Visually check circuit
breaker for a tripped
condition.
Check heater wiring for
loose wires.
332637C
17
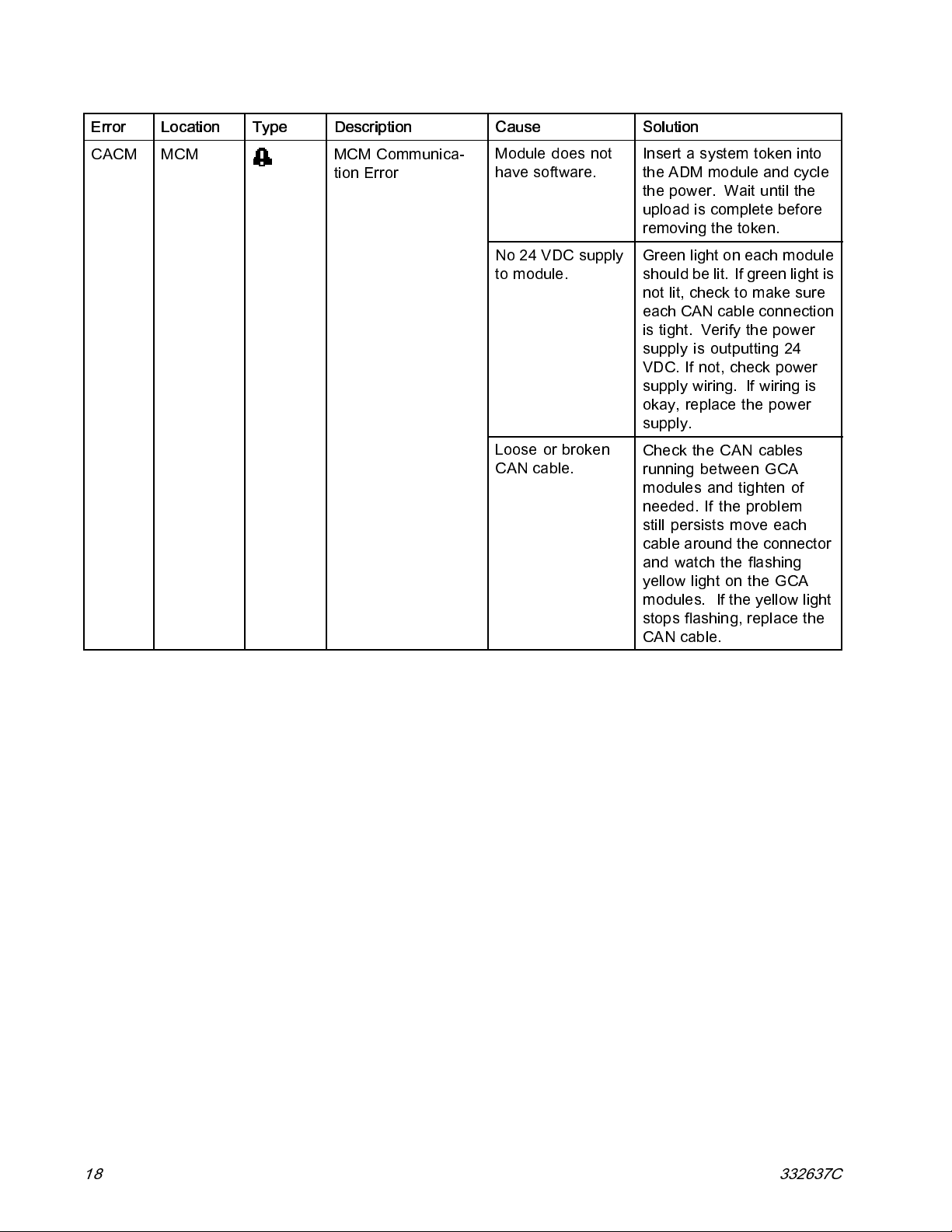
Troubleshooting
Error Location Type Description
CACM MCM MCM Communica-
tion Error
Cause Solution
Module does not
have software.
No 24 VDC supply
to module.
Loose or broken
CAN cable.
Insert a system token i n to
the ADM module and cycle
the power. Wait until the
upload is complete before
removing the token.
Greenlightoneachmodule
should be lit. If green light is
notlit,checktomakesure
each CAN cable connection
is tight. Verify the power
supply is outputting 24
VDC. If not, check power
supply wiring. If wiring is
okay, replace the power
supply.
Check the CAN cables
running between GCA
modules and tighten of
needed. If the problem
still persists move each
cablearoundtheconnector
and watch the flashing
yellow light on the GCA
modules. If the yellow light
stops flashing, replace the
CAN cable.
18 332637C
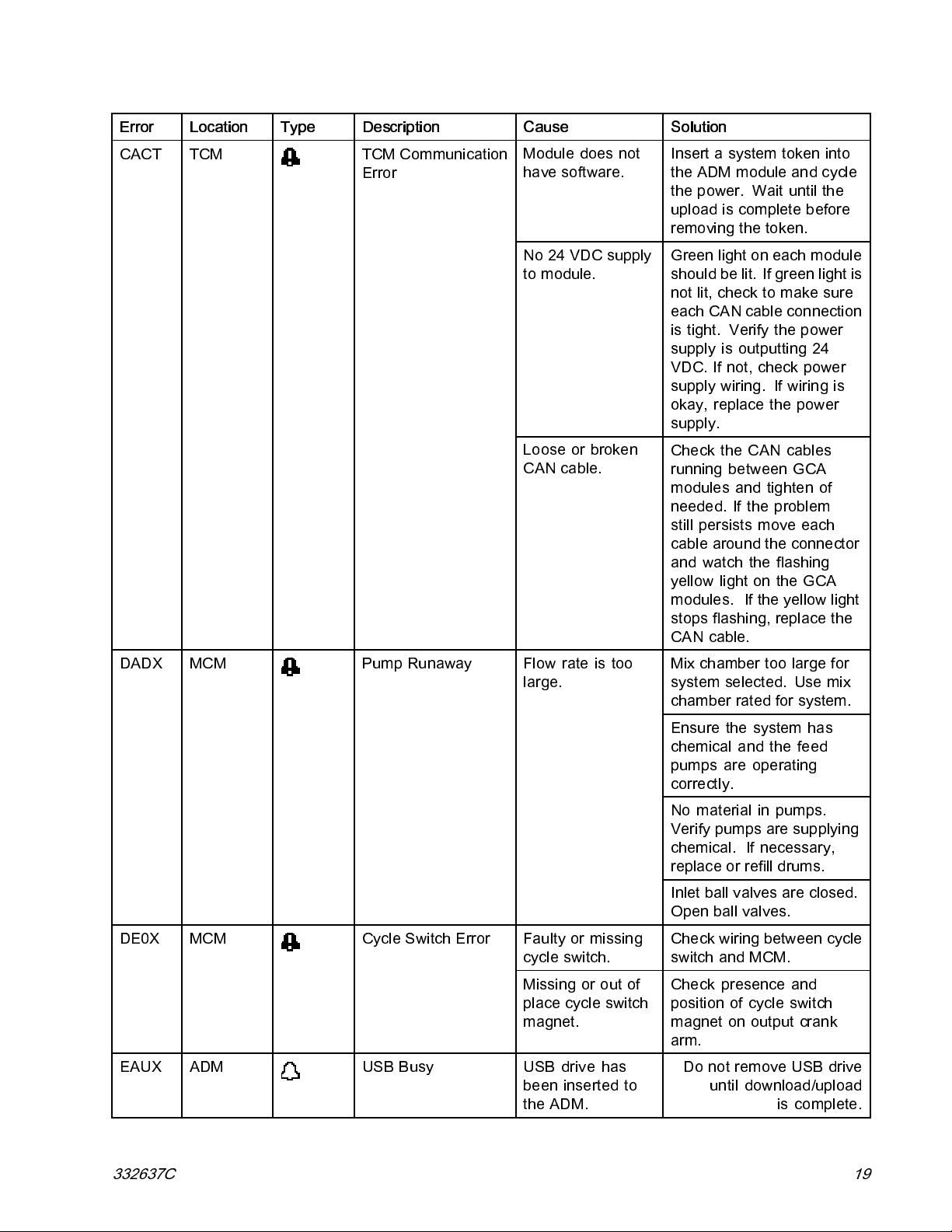
Troubleshooting
Error Location Type Description
CACT TCM TCM Communication
Error
Cause Solution
Module does not
have software.
No 24 VDC supply
to module.
Loose or broken
CAN cable.
Insert a system token into
the ADM module and cycle
the power. Wait until the
upload is complete before
removing the token.
Greenlightoneachmodule
should be lit. If green light is
not lit, check to make sure
each CAN cable connection
is tight. Verify the power
supply is outputting 24
VDC. If not, check powe r
supply wiring. If wiring is
okay, replace the power
supply.
Check the CAN cables
running between GCA
modules and tighten of
needed. If the problem
still persists move each
cablearoundtheconnector
and watch the flashing
yellow light on the GCA
modules. If the yellow light
stops flashing, replace the
CAN cable.
DADX MCM Pump Runaway Flow rate is too
large.
DE0X
EAUX ADM
MCM
Cycle Switch Error
USB Busy USB drive has
Faulty or missing
cycle switch.
Missing or out of
place cycle switch
magnet.
been inserted to
the ADM.
Mix ch am ber too large for
system selected. Use mix
chamber rated for system.
Ensure the system has
chemical and the feed
pumps are operating
correctly.
No material in pumps.
Verify pumps are supplying
chemical. If necessary,
replace or refill drums.
Inlet ball valves are closed.
Open ball valves.
Check wiring between cycle
switch and MCM.
Check presence and
position of cycle switch
magnet on output crank
arm.
Do not remove USB drive
until download/upload
is complete.
332637C 19
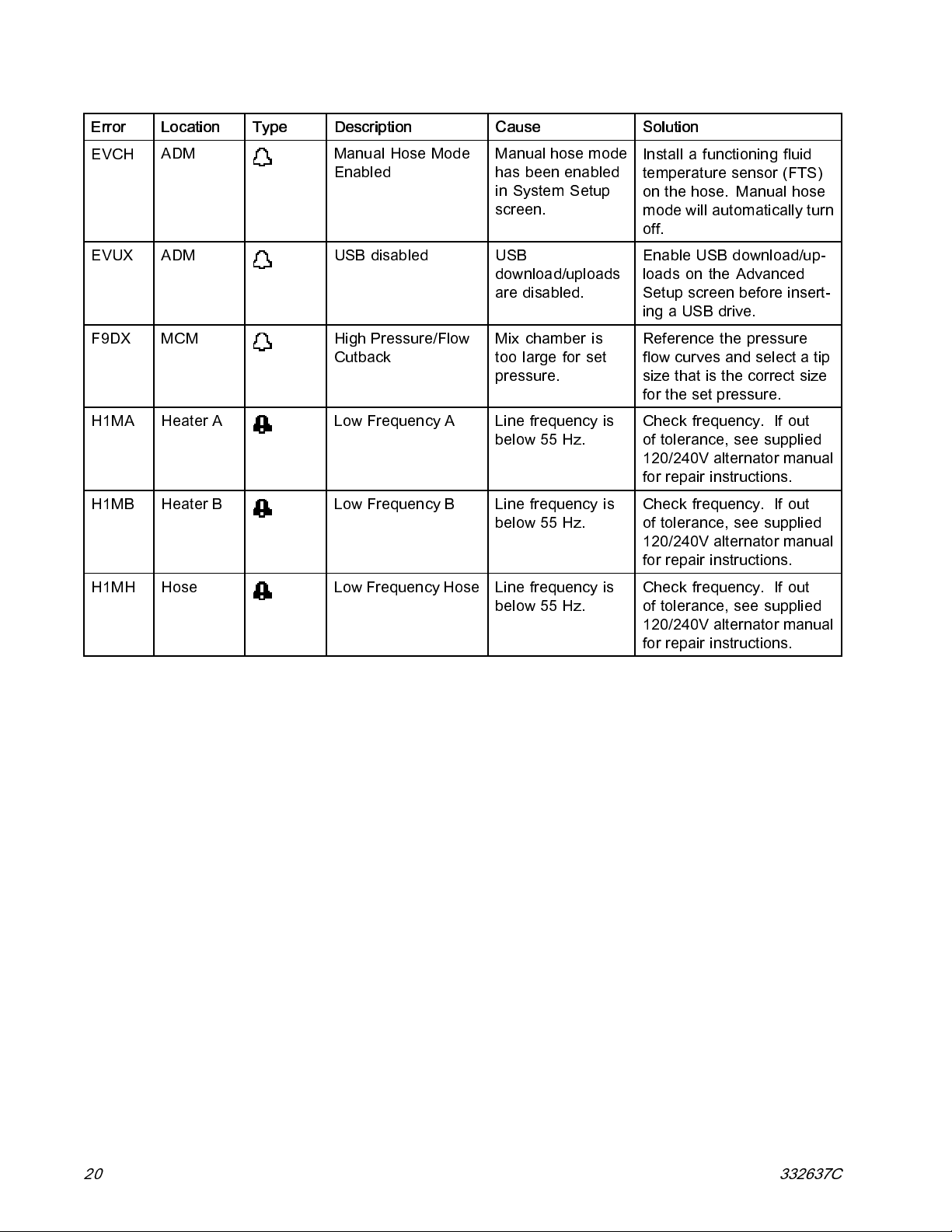
Troubleshooting
Error Location Type Description
EVCH
EVUX ADM
F9DX
H1MA Heater A Low Frequency A
H1MB Heater B Low Frequency B Line frequency is
ADM
MCM
Manual Hose Mode
Enabled
USB disabled USB
High Pressure/Flow
Cutback
Cause Solution
Manual hose mode
has been enabled
in System Setup
screen.
download/uploads
are disabled.
Mix chamber is
too large for set
pressure.
Line frequency is
below 55 Hz.
below 55 Hz.
Install a functioning fluid
temperature sensor (FTS)
on the hose. Manu al hose
mode will automatically turn
off.
Enable USB download/up-
loadsontheAdvanced
Setupscreenbeforeinsert-
ing a USB drive.
Reference the pressure
flow curves and select a tip
size that is the correct size
for the set pressure.
Check frequency. If out
of tolerance, see supplied
120/240V alternator manual
for repair instructions.
Check frequency. If out
of tolerance, see supplied
120/240V alternator manual
for repair instructions.
H1MH Hose Low Frequency Hose
Line frequency is
below 55 Hz.
Check frequency. If out
of tolerance, see supplied
120/240V alternator manual
for repair instructions.
20 332637C
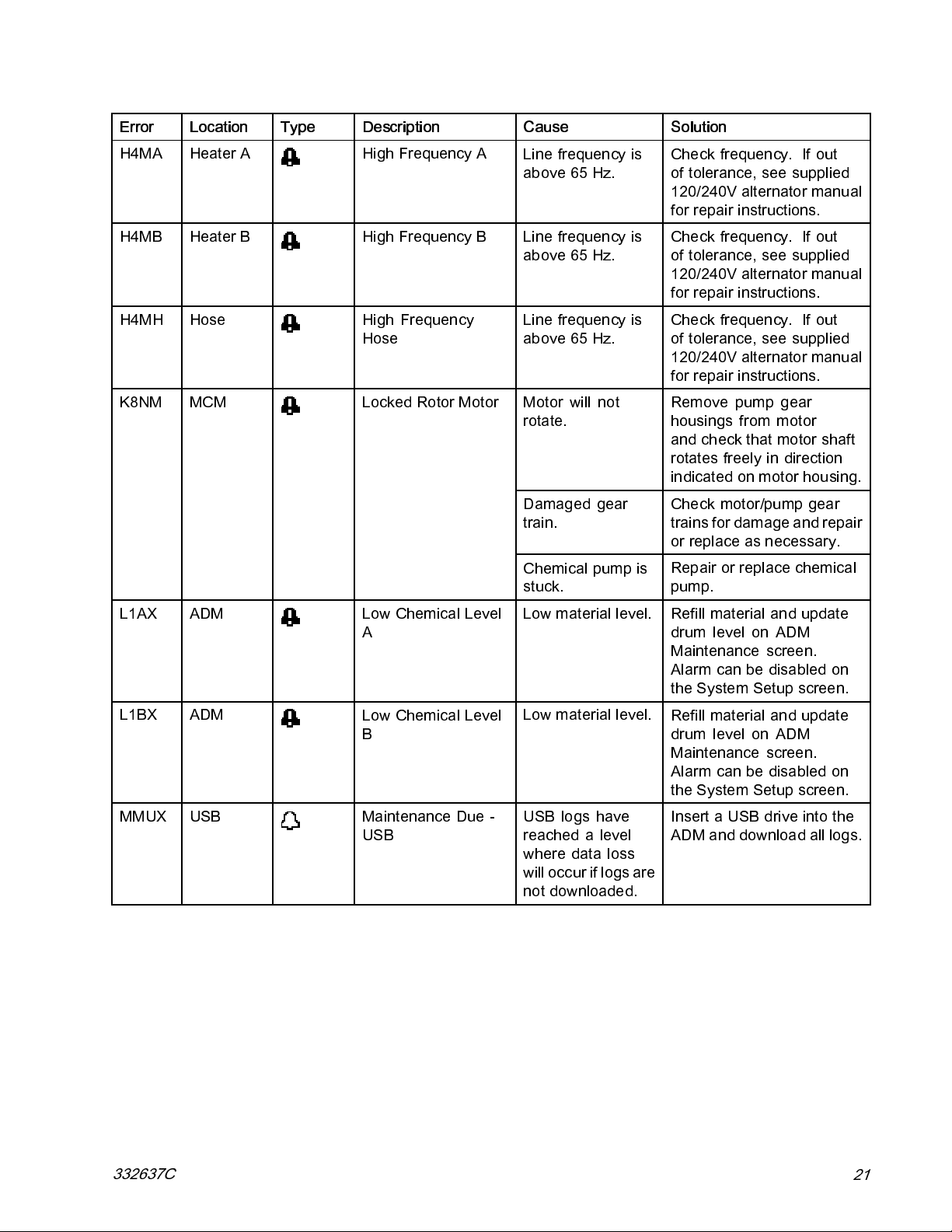
Troubleshooting
Error Location Type Description
H4MA Heater A High Frequency A
H4MB Heater B High Frequency B
H4MH Hose High Frequency
Hose
K8NM
MCM
Locked Rotor Motor
Cause Solution
Line frequency is
above65Hz.
Line frequency is
above65Hz.
Line frequency is
above65Hz.
Motor will not
rotate.
Damaged gear
train.
Chemical pump is
stuck.
Check frequency. If out
of tolerance, see supplied
120/240V alternator manual
for repair instructions.
Check frequency. If out
of tolerance, see supplied
120/240V alternator manual
for repair instructions.
Check frequency. If out
of tolerance, see supplied
120/240V alternator manual
for repair instructions.
Remove pump gear
housings from motor
and check that motor shaft
rotates freely in direction
indicated on motor housing.
Check motor/pump gear
trains for damage and repair
or replace as necessary.
Repair or replace chemical
pump.
L1AX ADM
L1BX ADM
MMUX
USB
Low Chemical Level
A
Low Chemical Level
B
Maintenance Due -
USB
Low material level.
Low material level.
USB logs have
reached a level
where data loss
will occur if logs are
not downloaded.
Refill material and update
drum level on ADM
Maintenance screen.
Alarm can be disabled on
the System Setup screen.
Refill material and update
drum level on ADM
Maintenance screen.
Alarm can be disabled on
the System Setup screen.
InsertaUSBdriveintothe
ADM and download all logs.
332637C
21
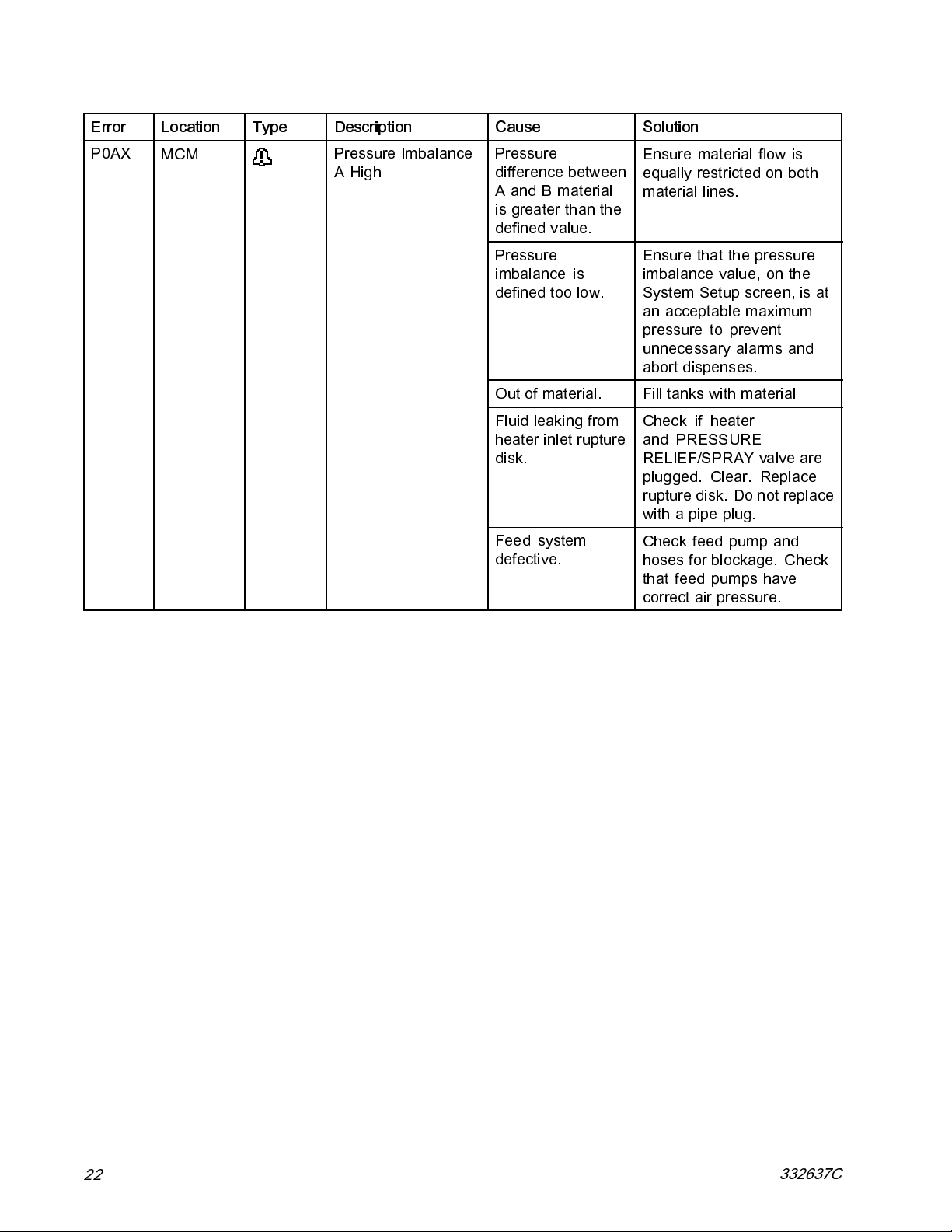
Troubleshooting
Error Location Type Description
P0AX
MCM
Pressure Imbalance
AHigh
Cause Solution
Pressure
difference between
AandBmaterial
is greater than the
defined value.
Pressure
imbalance is
defined too low.
Out of material. Fill tanks with material
Fluid leaking from
heater inlet ruptu re
disk.
Feed system
defective.
Ensure material flow is
equally restricted on both
material lines.
Ensure that the pressure
imbalance value, on the
System Setup screen, is at
an acceptable maximum
pressure to prevent
unnecessary alarms and
abort dispenses.
Check if he ate r
and PRESSURE
RELIEF/SPRAY valve are
plugged. Clear. Replace
rupture disk. Do not replace
withapipeplug.
Check feed pump and
hoses for blockage. Check
that feed pumps hav e
correct air pressure.
22
332637C
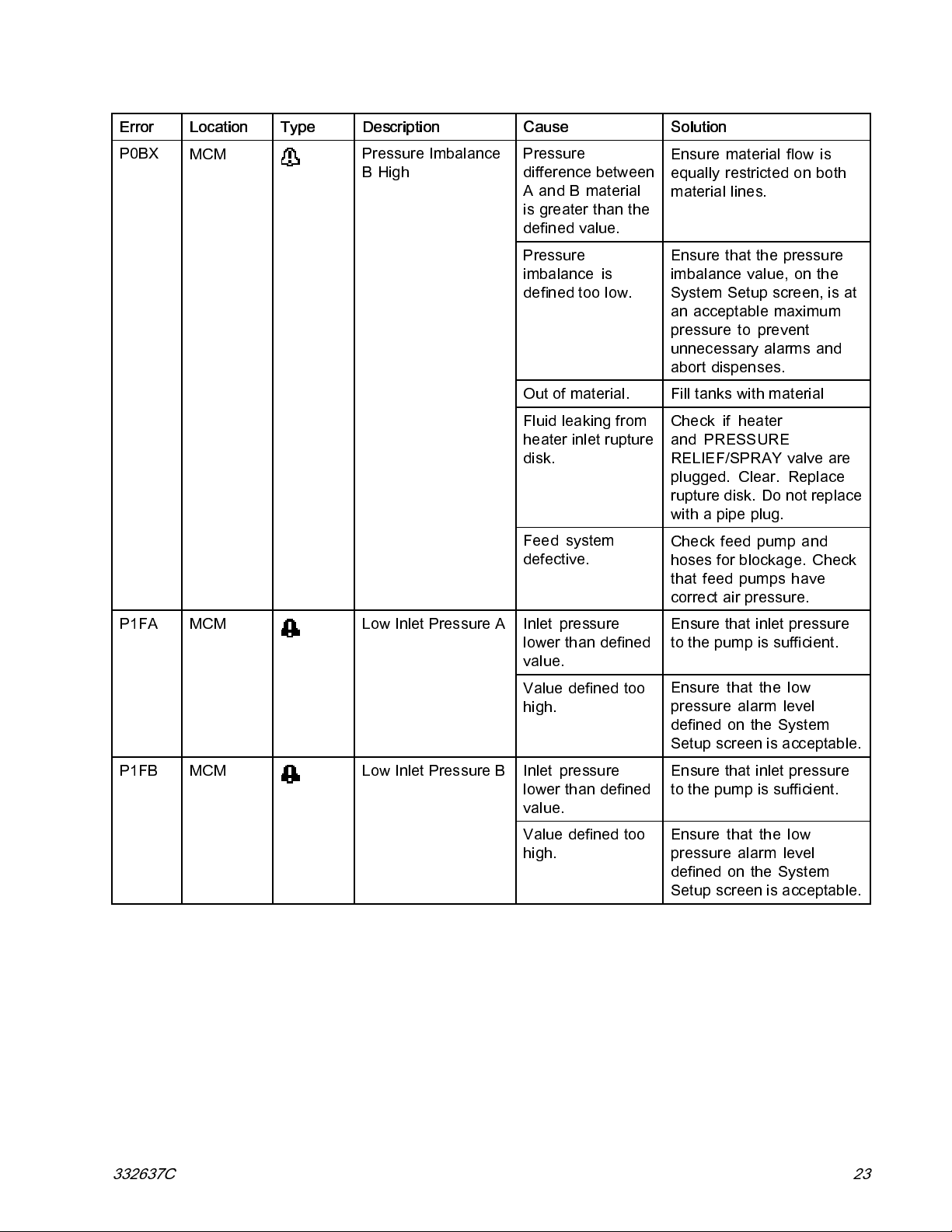
Troubleshooting
Error Location Type Description
P0BX
MCM
Pressure Imbalance
BHigh
Cause Solution
Pressure
difference between
AandBmaterial
is greater than the
defined value.
Pressure
imbalance is
defined too low.
Out of material. Fill tanks with material
Fluid leaking from
heater inlet rupture
disk.
Feed system
defective.
Ensure material flow is
equally restricted on both
material lines.
Ensure that the pressure
imbalance value, on the
System Setup screen, is at
an acceptable maximum
pressure to prevent
unnecessary alarms and
abort dispenses.
Check if heater
and PRESSURE
RELIEF/SPRAY valve are
plugged. Clear. Replace
rupture disk. Do not replace
withapipeplug.
Checkfeedpumpand
hoses for blockage. Check
that feed pumps have
correct air pressure.
P1FA
P1FB
MCM
MCM
Low Inlet Pressure A
Low Inlet Pressure B
Inlet pressure
lower than defined
value.
Value defined too
high.
Inlet pressure
lower than defined
value.
Value defined too
high.
Ensure that inlet pressure
to the pump i s sufficient.
Ensure that the low
pressure alarm level
defined on the System
Setup screen is acceptable.
Ensure that inlet pressure
to the pump i s sufficient.
Ensure that the low
pressure alarm level
defined on the System
Setup screen is acceptable.
332637C 23
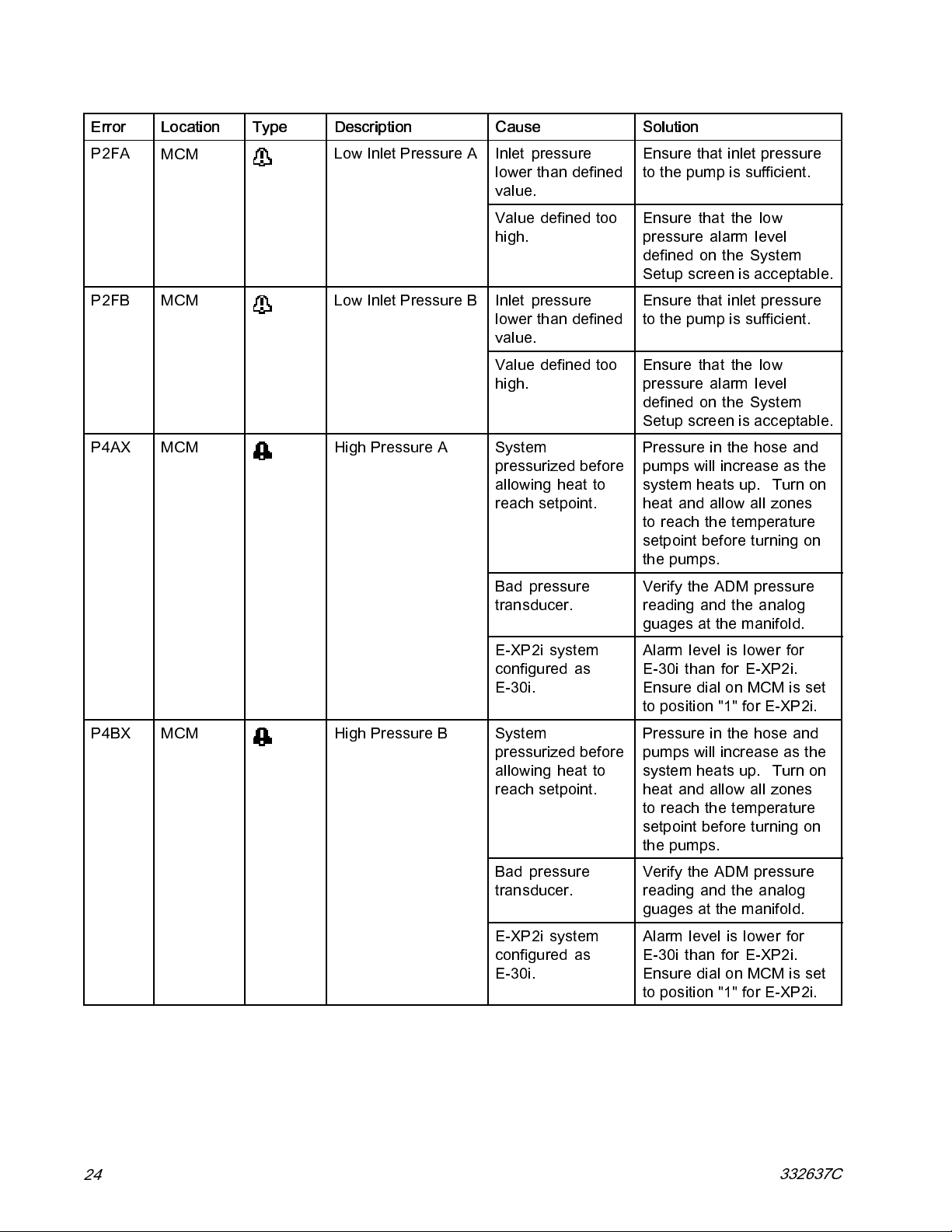
Troubleshooting
Error Location Type Description
P2FA
P2FB MCM Low Inlet Pressure B
P4AX
MCM
MCM
Low Inlet Pressure A
High Pressure A
Cause Solution
Inlet pressure
lower than defined
value.
Value defined too
high.
Inlet pressure
lower than defined
value.
Value defined too
high.
System
pressurized before
allowing heat to
reach setpoint.
Ensure that inlet pressure
to the pump is sufficient.
Ensure that the low
pressure alarm level
defined on the System
Setup screen is acceptable.
Ensure that inlet pressure
to the pump is sufficient.
Ensure that the low
pressure alarm level
defined on the System
Setup screen is acceptable.
Pressureinthehoseand
pumps wil l increase as the
system h eats up. Turn on
heat and allow all zones
to reach the temperature
setpoint before turning on
the pump s.
P4BX
MCM
High Pressure B
Bad pressure
transducer.
E-XP2i system
configured as
E-30i.
System
pressurized before
allowing heat to
reach setpoint.
Bad pressure
transducer.
E-XP2i system
configured as
E-30i.
Verify the ADM pressure
readingandtheanalog
guages at th e manifold.
Alarm level is lower for
E-30i than for E-XP2i.
Ensure dial on MCM is set
to position "1" for E-XP2i.
Pressureinthehoseand
pumps wil l increase as the
system h eats up. Turn on
heat and allow all zones
to reach the temperature
setpoint before turning on
the pump s.
Verify the ADM pressure
readingandtheanalog
guages at th e manifold.
Alarm level is lower for
E-30i than for E-XP2i.
Ensure dial on MCM is set
to position "1" for E-XP2i.
24
332637C
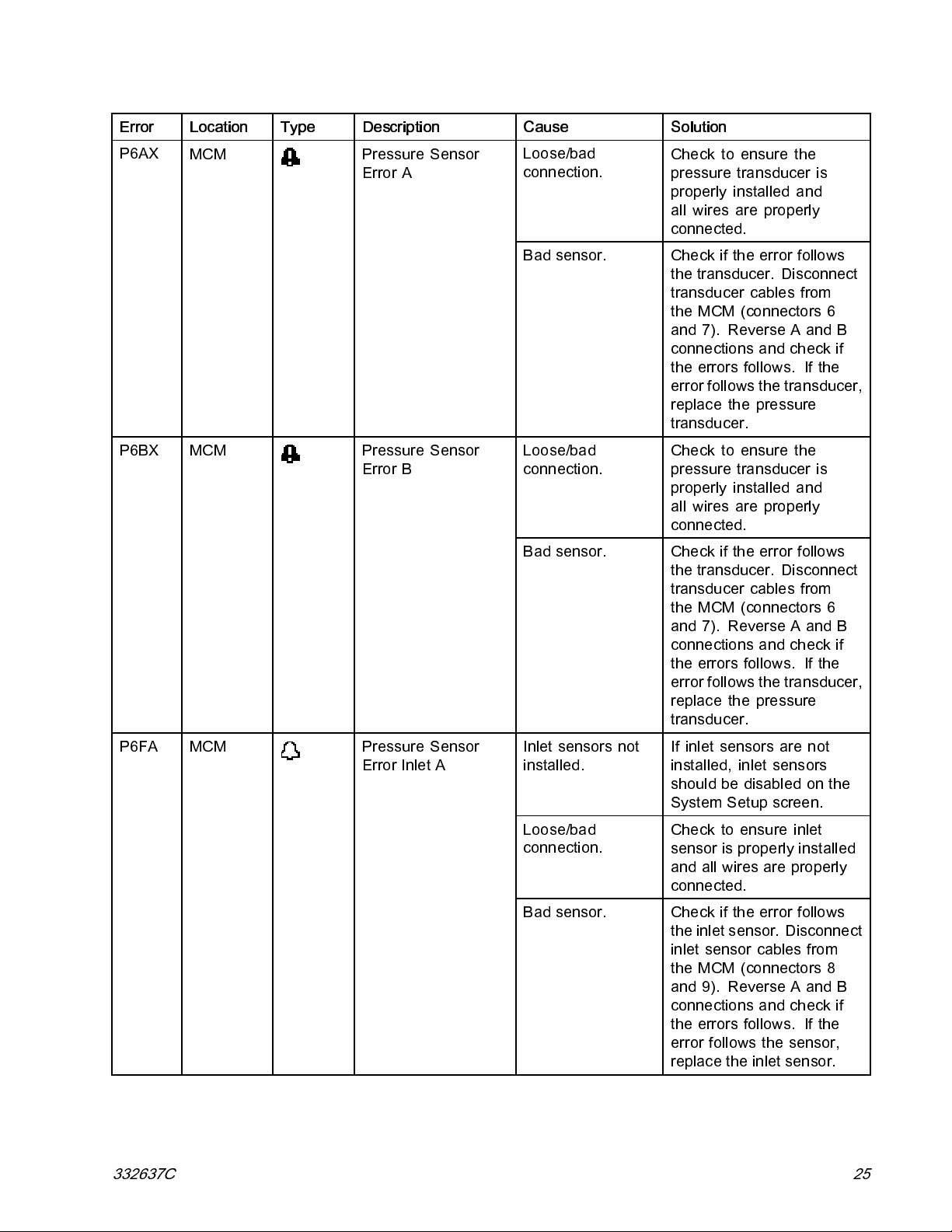
Troubleshooting
Error Location Type Description
P6AX
P6BX
MCM
MCM
Pressure Sensor
Error A
Pressure Sensor
Error B
Cause Solution
Loose/bad
connection.
Bad sensor.
Loose/bad
connection.
Bad sensor.
Check to ensure the
pressure transducer is
properly installed and
all wires are properly
connected.
Check if the error follows
the transducer. Disconnect
transducer cables from
the MCM (connectors 6
and7). ReverseAandB
connections and check if
the errors follows. If the
error follows the trans du ce r,
replace the pressure
transducer.
Check to ensure the
pressure transducer is
properly installed and
all wires are properly
connected.
Check if the error follows
the transducer. Disconnect
transducer cables from
the MCM (connectors 6
and7). ReverseAandB
connections and check if
the errors follows. If the
error follows the trans du ce r,
replace the pressure
transducer.
P6FA MCM Pressure Sensor
Error Inlet A
332637C 25
Inlet sensors not
installed.
Loose/bad
connection.
Bad sensor.
If inlet sensors are not
installed, inlet sensors
should be disabled on the
System Setup screen.
Checktoensureinlet
sensor is properly installed
and all wires are properly
connected.
Check if the error follows
the inlet sensor. Disconnect
inlet sensor cables from
the MCM (connectors 8
and9). ReverseAandB
connections and check if
the errors follows. If the
error follows the sensor,
replace the inlet sensor.
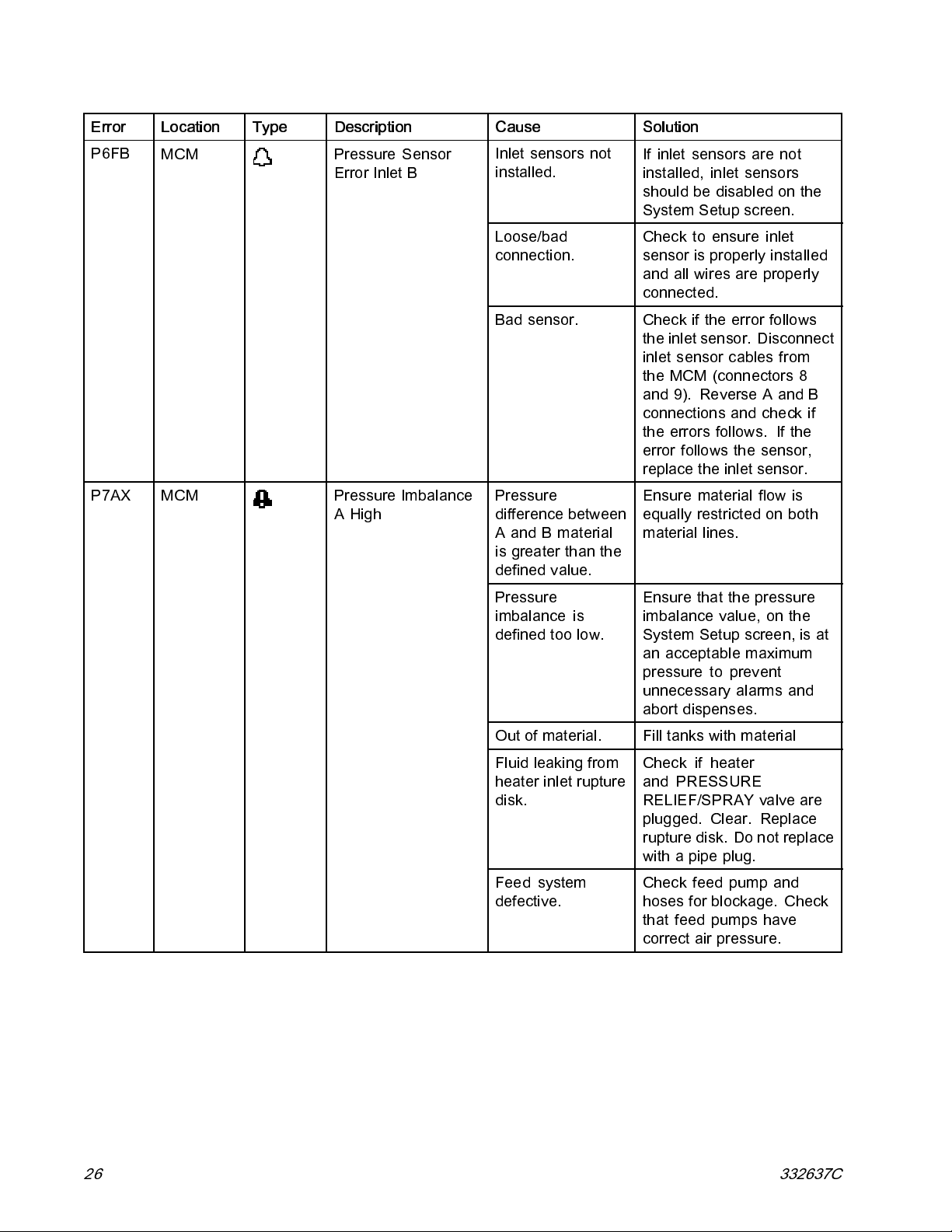
Troubleshooting
Error Location Type Description
P6FB
P7AX
MCM
MCM
Pressure Sensor
Error Inlet B
Pressure Imbalance
AHigh
Cause Solution
Inlet sensors not
installed.
Loose/bad
connection.
Bad sensor.
Pressure
difference between
AandBmaterial
is greater than the
defined value.
If inlet sensors are not
installed, inlet sensors
should be disabled on the
System Setup screen.
Check to ens ure i nl et
sensor is properly installed
and all wires are properly
connected.
Check if the error follows
the inlet sensor. Disconnect
inlet sensor cables from
the MCM (connectors 8
and9). ReverseAandB
connections and check if
the errors follo ws . If the
error follows the sensor,
replace the inlet sensor.
Ensure material flow is
equally restricted on both
material lines.
Pressure
imbalance is
defined too low.
Out of material.
Fluid leaking from
heater inlet ruptu re
disk.
Feed system
defective.
Ensure that the pressure
imbalance value, on the
System Setup screen, is at
an acceptable maximum
pressure to prevent
unnecessary alarms and
abort dispenses.
Fill tanks with material
Check if he ate r
and PRESSURE
RELIEF/SPRAY valve are
plugged. Clear. Replace
rupture disk. Do not replace
withapipeplug.
Check feed pump and
hoses for blockage. Check
that feed pumps hav e
correct air pressure.
26 332637C
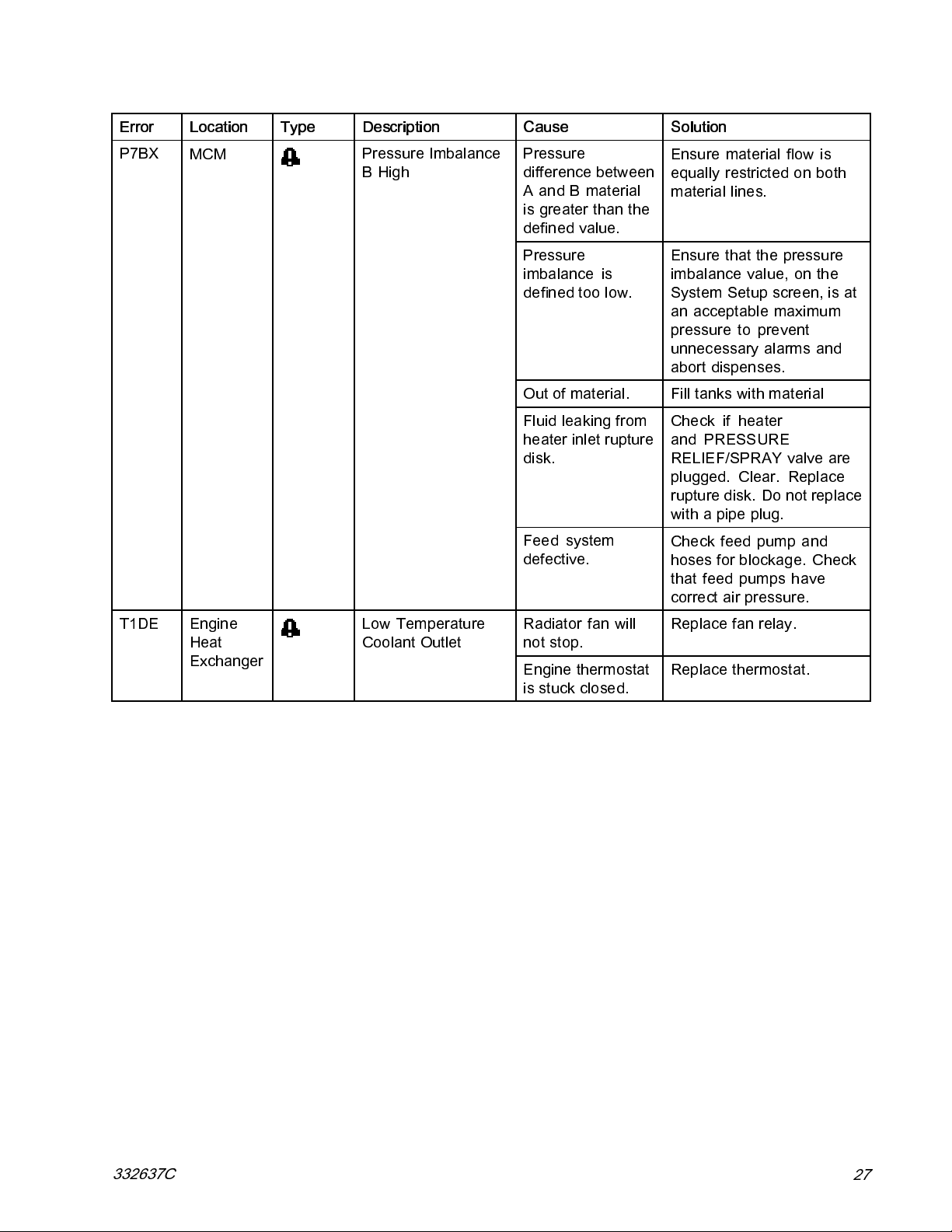
Troubleshooting
Error Location Type Description
P7BX
MCM
Pressure Imbalance
BHigh
Cause Solution
Pressure
difference between
AandBmaterial
is greater than the
defined value.
Pressure
imbalance is
defined too low.
Out of material. Fill tanks with material
Fluid leaking from
heater inlet rupture
disk.
Feed system
defective.
Ensure material flow is
equally restricted on both
material lines.
Ensure that the pressure
imbalance value, on the
System Setup screen, is at
an acceptable maximum
pressure to prevent
unnecessary alarms and
abort dispenses.
Check if heater
and PRESSURE
RELIEF/SPRAY valve are
plugged. Clear. Replace
rupture disk. Do not replace
withapipeplug.
Checkfeedpumpand
hoses for blockage. Check
that feed pumps have
correct air pressure.
T1DE Engine
Heat
Exchanger
Low Temperature
Coolant Outlet
Radiator fan will
not stop.
Engine thermostat
is stuck closed.
Replace fan relay.
Replace thermostat.
332637C
27
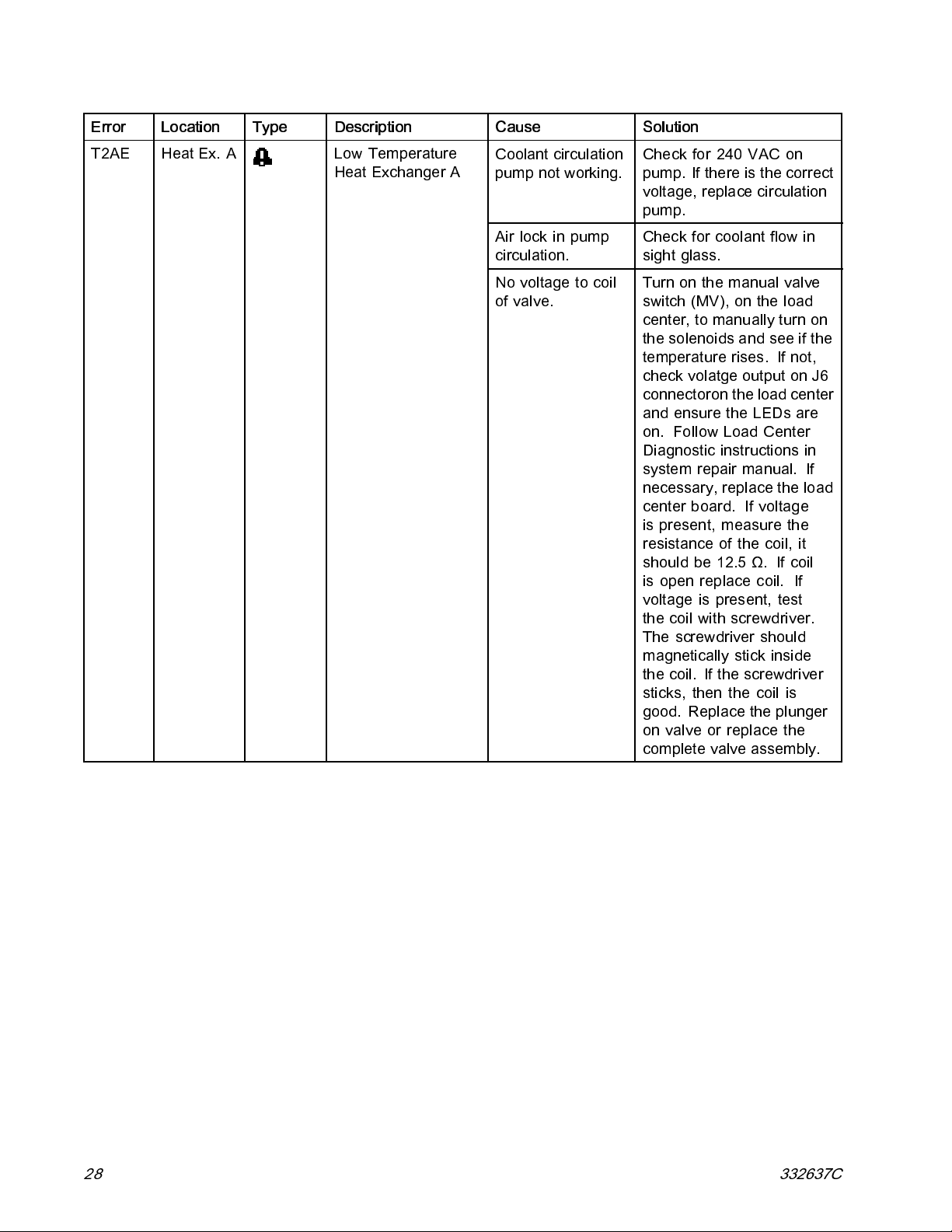
Troubleshooting
Error Location Type Description
T2AE Heat Ex. A Low Temperature
Heat Exchanger A
Cause Solution
Coolant circulation
pump not working.
Air lock in pump
circulation.
Novoltagetocoil
of valve.
Check for 240 VAC on
pump. If there is the correct
voltage, replace circulation
pump.
Check for coolan t flow in
sight glass.
Turn on the manual valve
switch(MV),ontheload
center, to manually turn on
the solenoids and see if the
temperature rises. If not,
check volatge output on J6
connectorontheloadcenter
andensuretheLEDs are
on. Follow Load Center
Diagnostic instructions in
system repair manual. If
necessary, replace the load
center board. If voltage
is present, measure the
resistance of the coil, it
should be 12.5 Ω. If coil
is open replace coil. If
voltage is present, test
the coil with screwdriver.
The screwdriver should
magnetically stick inside
the coil . If the screwdriver
sticks, then the coil is
good. Replace the plunger
on valve or replace the
complete valve assembly.
28 332637C
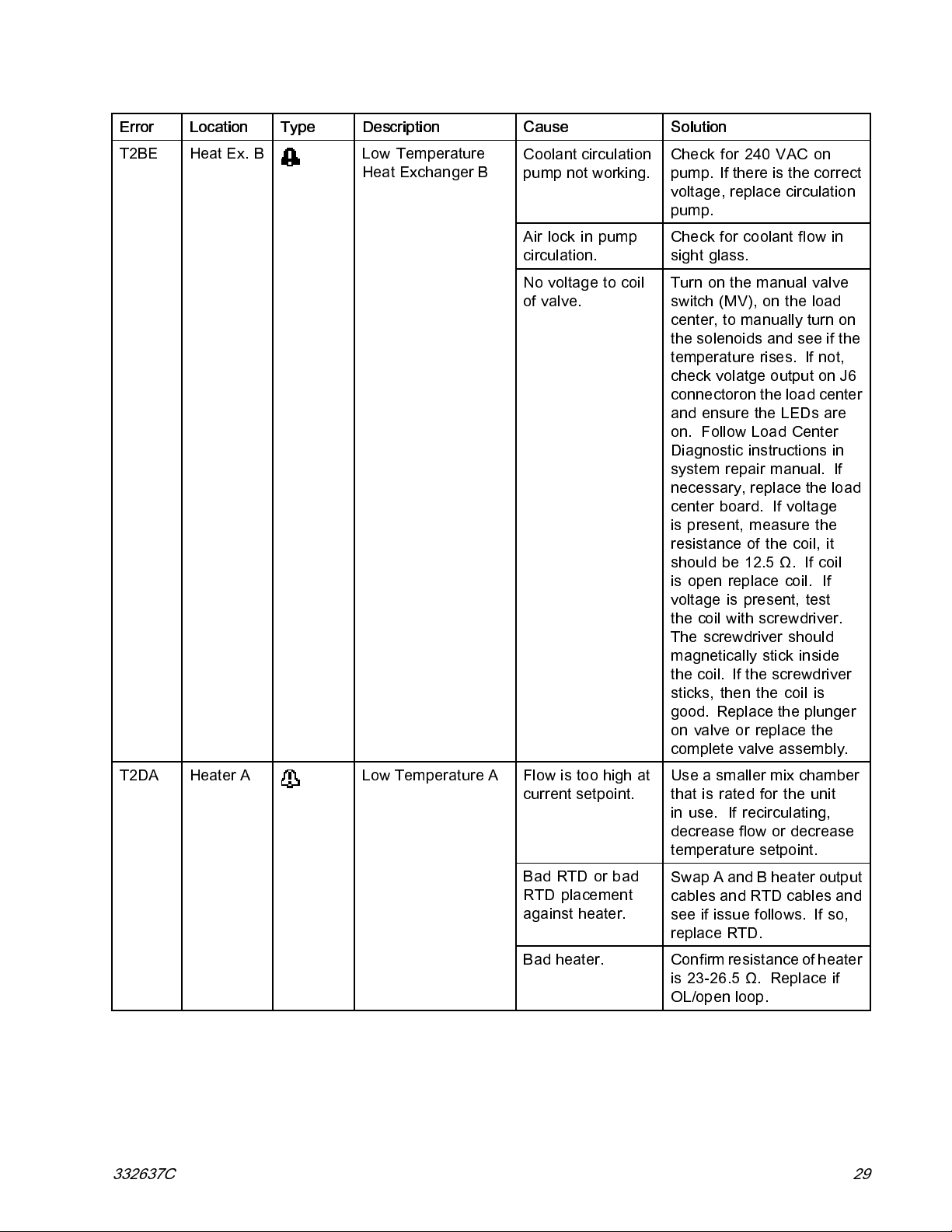
Troubleshooting
Error Location Type Description
T2BE Heat Ex. B Low Temperature
Heat Exchanger B
Cause Solution
Coolant circulation
pump not working.
Air lock in pump
circulation.
Novoltagetocoil
of valve.
Check for 240 VAC on
pump. If there is the correct
voltage, replace circulation
pump.
Check for coolant flow in
sight glass.
Turn on the manual valve
switch (MV), on the load
center, to manually turn on
the solenoids and see if the
temperature rises. If not,
check volatge output on J6
connectorontheloadcenter
and ensure the LEDs are
on. Follow Load Center
Diagnostic instructions in
system repair manual. If
necessary, replace the load
center board. If voltage
is present, measure the
resistance of the coil, it
should be 12.5 Ω. If coil
is open replace coil. If
voltage is present, test
the coil with screwdriver.
The screwdriver should
magnetically stick inside
the coil. If the screwdriver
sticks, then the coil is
good. Rep lac e the plunger
on valve or replace the
complete valve assembly.
T2DA Heater A Low Temperature A
332637C 29
Flow is too high at
current setpoint.
Bad RTD or bad
RTD placement
against heater.
Bad heater.
Use a smaller mix chamber
that is rated for the unit
in use. If recirculating,
decrease flow or decrease
temperature setpoint.
Swap A and B heater output
cables and RTD cables and
see if issue follows. If so,
replace RTD.
Confirmresistance of heater
is 23-26.5 Ω. Repl ace if
OL/open loop.
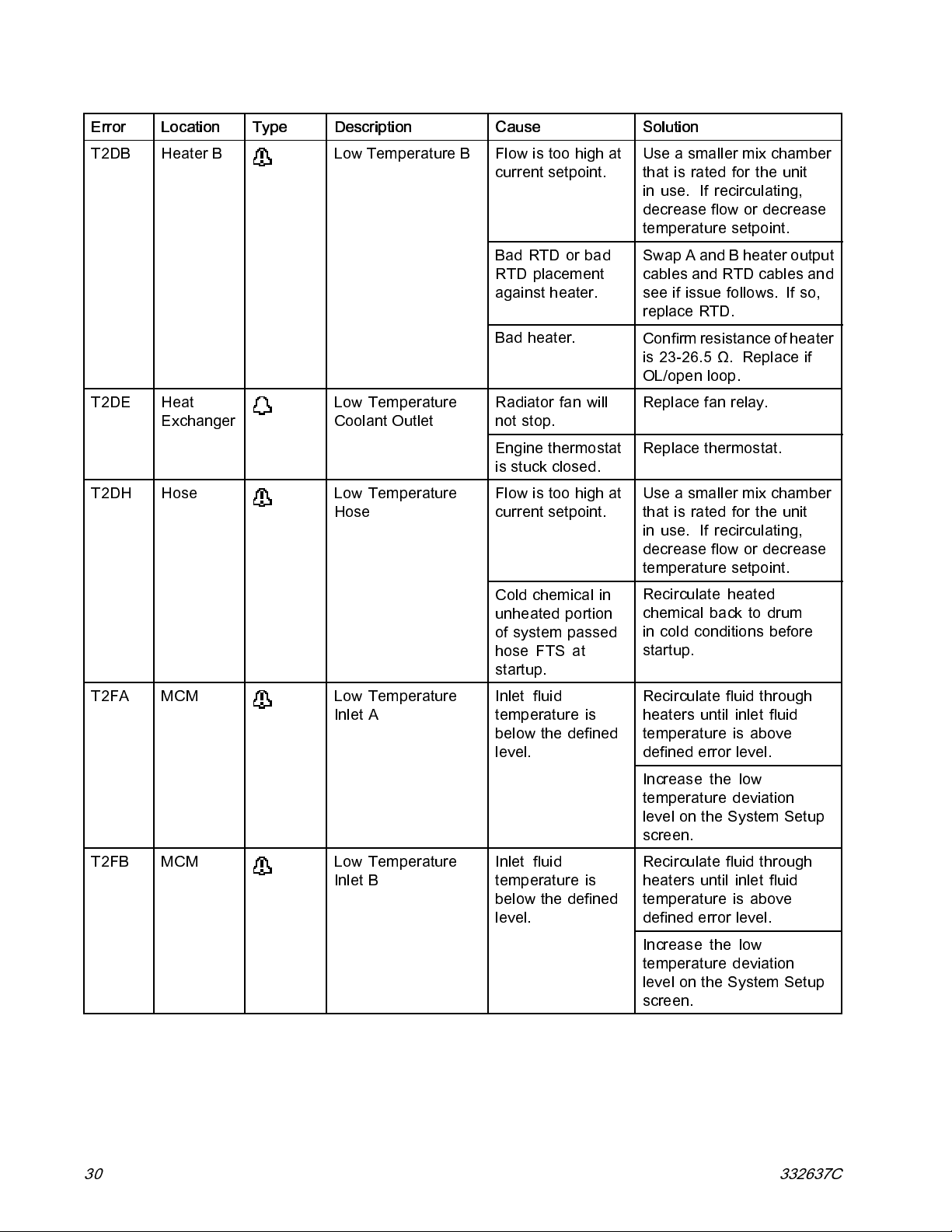
Troubleshooting
Error Location Type Description
T2DB Heater B Low Temperature B
Low Temperature
Exchanger
T2DH Hose Low Temperature
Coolant Outlet
Hose
Cause Solution
Flow is too high at
current setpoint.
Bad RTD or bad
RTD placement
against heat er.
Bad heater.
Radiator fan will
not stop.
Engine thermostat
is stuck closed.
Flow is too high at
current setpoint.
Use a smaller mix chamber
that is rated fo r the unit
in use. If recirculating,
decrease flow or decrease
temperature setpoint.
Swap A an d B heater o utpu t
cables and RTD cables and
see if issue follows. If so,
replace RTD.
Confirmresistance of heater
is 23-26.5 Ω. Replace if
OL/open loop.
Replace fan relay.T2DE Heat
Replace thermostat.
Use a smaller mix chamber
that is rated fo r the unit
in use. If recirculating,
decrease flow or decrease
temperature setpoint.
T2FA MCM Low Temperature
Inlet A
T2FB
MCM
Low Temperature
Inlet B
Cold chemical in
unheated portion
of system passed
hose FTS a t
startup.
Inlet fluid
temperature is
below the defined
level.
Inlet fluid
temperature is
below the defined
level.
Recirculate heated
chemical back to drum
in cold conditions before
startup.
Recirculate fluid through
heaters until inlet fluid
temperature is above
defined error level.
Increase the low
temperature deviation
level on the System Setup
screen.
Recirculate fluid through
heaters until inlet fluid
temperature is above
defined error level.
Increase the low
temperature deviation
level on the System Setup
screen.
30 332637C

Troubleshooting
Error Location Type Description
T3CH
T3CT TCM TCM Cutback
Hose
Hose Cutback
Cause Solution
Hose current has
been reduced
because hose
has been drawing
current for an
extended period.
High ambient
temperature.
Enclosure fan not
operating.
Module fan not
operating.
Hose setpoint higher than A
and B setpoints. Decrease
hose setpoint.
Hose FTS is in a colder
environment than the rest
of the hose. Expose FTS to
the same environment as
therestofthehose.
Ensure ambient
temperature is below
120°F(48°C) before using
the system.
Ensurefaninelectrical
enclosure is spinning. If it
is not, check fan wiring or
replace fan.
If a TCM fan error (WMI0)
has occurred, fan inside
themoduleisnotworking
properly. Check TCM fan
for debris and clear with
forced air if necessary.
T3NM
T4AE Heat Ex. A High Temperature
MCM
MCM Cutback
Heat Exchanger A
Motor is operating
outside of the
pressure flow
curve.
Manual valve
switch (MV) on
load center is in the
ON position.
A or B side control
valve solenoid is
stuck in the open
position.
Short on load
center board.
The system is running at a
lower setpoint to preserve
motor life. Run the system
at a lower duty cycle or with
a smaller mix chamber.
Open cabinet cover and
turn switch to the OFF
position.
Debris in valve diaphragm
or plunger preventing
spring-loaded closed
function. Disconnect
connector from valve
solenoid cable. If
temperature does not
decrease, rebuild solenoid.
IftheblueandredLEDsare
on while heat is off, the load
center board is bad. See
Load Center Diagnostics in
the system repair manual.
332637C 31
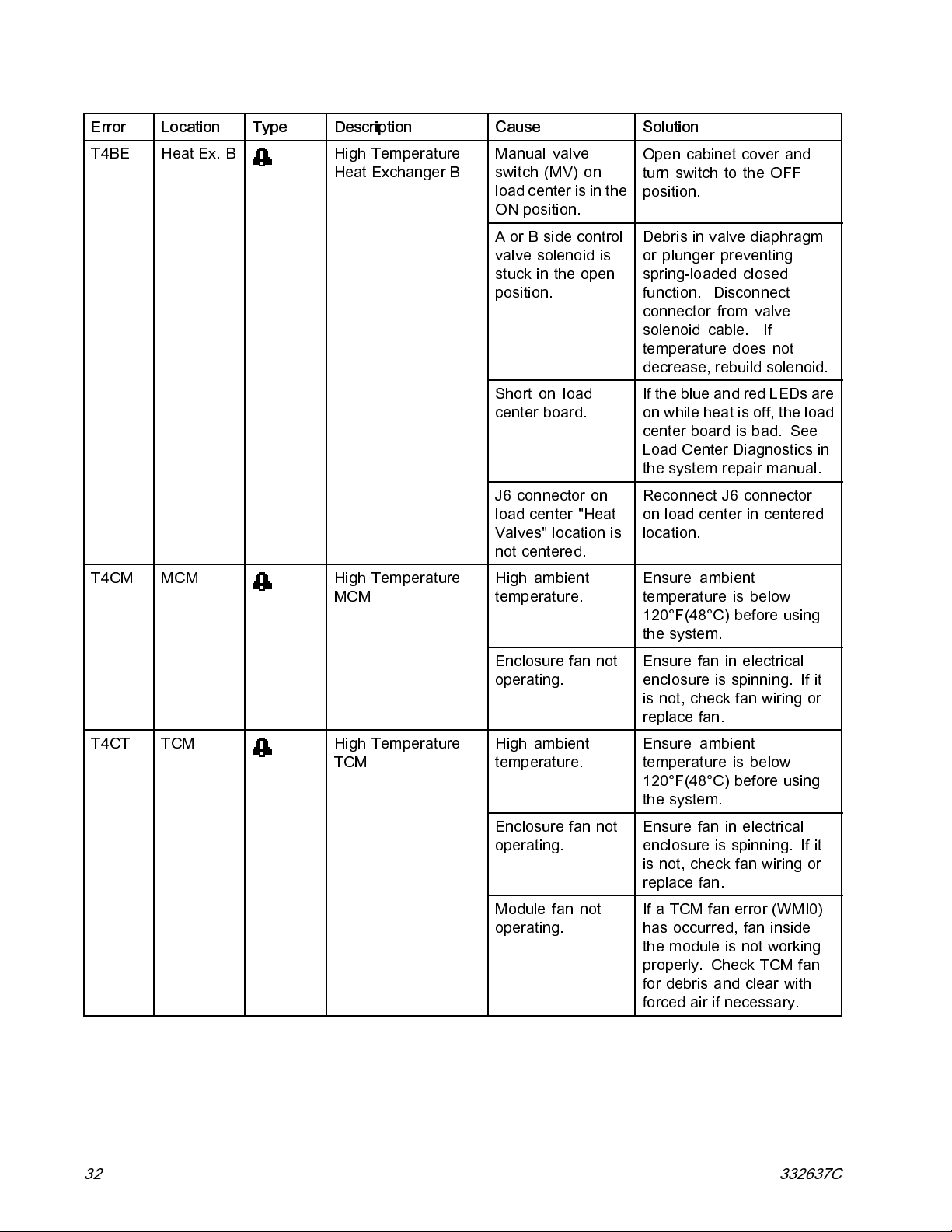
Troubleshooting
Error Location Type Description
T4BE Heat Ex. B High Temperature
Heat Exchanger B
Cause Solution
Manual valve
switch (MV) on
load center is in the
ON position.
A or B side control
valvesolenoidis
stuckintheopen
position.
Short on load
center board.
J6 connector on
load center "Heat
Valves" location is
not centered.
Open cabinet cover and
turn switch to the OFF
position.
Debris in valve diaphragm
or plunger preventing
spring-loaded closed
function. Disconnect
connector from valve
solenoid cable. If
temperature does not
decrease, rebuild solenoid.
If the blue and red LEDs are
on while heat is off, the load
center board is bad. See
Load Center Diagnostics in
the system repa ir manual.
Reconnect J6 connector
on load center in centered
location.
T4CM MCM
T4CT TCM High Temperature
High Temperature
MCM
TCM
High ambient
temperature.
Enclosure fan not
operating.
High ambient
temperature.
Enclosure fan not
operating.
Module fan not
operating.
Ensure ambient
temperature is below
120°F(48°C) before using
the sy ste m.
Ensure fan in electrical
enclosure is spinning. If it
is not, check fan wiring or
replace fan.
Ensure ambient
temperature is below
120°F(48°C) before using
the sy ste m.
Ensure fan in electrical
enclosure is spinning. If it
is not, check fan wiring or
replace fan.
If a TCM fan error (WMI0)
has occurred, fan inside
the mod ule is not working
properly. Check TCM fan
for debris and clear with
forced air if necessary.
32 332637C
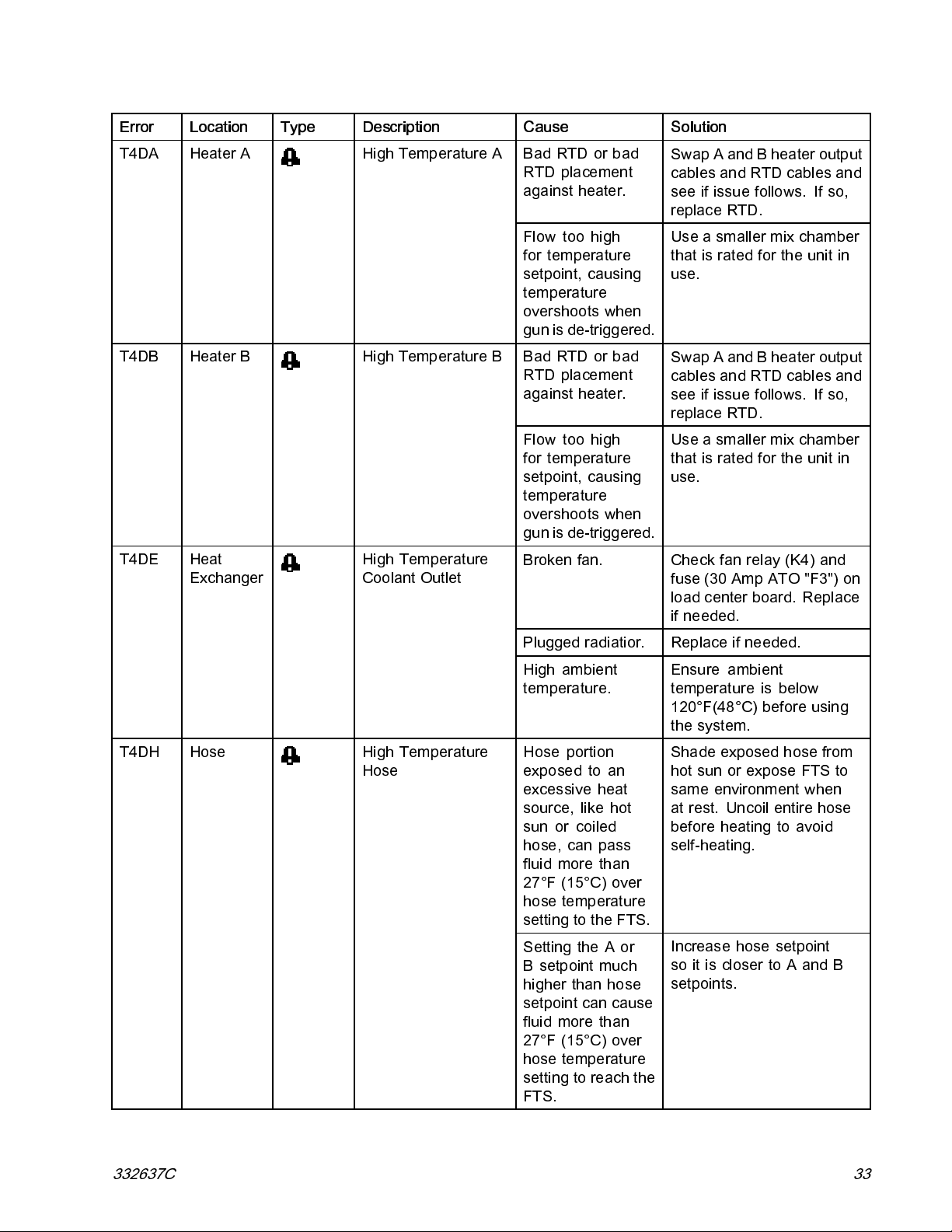
Troubleshooting
Error Location Type Description
T4DA Heater A High Temperature A
T4DB Heater B High Temperature B
T4DE Heat
Exchanger
High Temperature
Coolant Outlet
Cause Solution
Bad RTD or bad
RTD placement
against heater.
Flow too high
for temperature
setpoint, causing
temperature
overshoots when
gun is de-triggered.
Bad RTD or bad
RTD placement
against heater.
Flow too high
for temperature
setpoint, causing
temperature
overshoots when
gun is de-triggered.
Broken fan. Check fan relay (K4) and
Swap A and B heater output
cables and RTD cables and
see if issue follows. If so,
replace RTD.
Use a smaller mix chamber
that is rated for the unit in
use.
Swap A and B heater output
cables and RTD cables and
see if issue follows. If so,
replace RTD.
Use a smaller mix chamber
that is rated for the unit in
use.
fuse (30 Amp ATO "F3") on
load center board. Replace
if needed.
T4DH Hose High Temperature
Hose
Plugged radiatior.
High ambient
temperature.
Hose portion
exposed to an
excessive heat
source, like hot
sun or coiled
hose, can pass
fluid more than
27°F (15°C) over
hose temperature
setting to the FTS.
Setting the A or
B setpoint much
higher than hos e
setpoint can cause
fluid more than
27°F (15°C) over
hose temperature
setting to reach the
FTS.
Replace if needed.
Ensure ambient
temperature is below
120°F(48°C) before using
the system.
Shade expo se d hose from
hot sun or expose FTS to
same environment when
at rest. Uncoil entire hose
before heating to avoid
self-heating.
Increase hose setpoint
so it is closer to A and B
setpoints.
332637C 33

Troubleshooting
Error Location Type Description
T4EA Heater A High Temperature
Switch A
T4EB Heater B High Temperature
Switch B
Cause Solution
Overtemperature
switch sensed a
fluid temperature
above 230°F
(110°C).
Broken or loose
overtemperature
switch
cable/connection.
Overtemperature
switch failed in the
open position.
Overtemperature
switch sensed a
fluid temperature
above 230°F
(110°C).
Heater was delivered too
much power, causing the
overtemperature switch to
open. RTD is not reading
properly. After the heater
cools down, replace RTD.
Switch closes and the error
canbeclearedwhenthe
heater temperature falls
below 190°F (87°C).
If heater is not actually
over temperature, check
all wiring and connections
between the TCM and the
overtemperature switches.
Replace overtemperature
switch.
Heater was delivered too
much power, causing the
overtemperature switch to
open. RTD is not reading
properly. After the heater
cools down, replace RTD.
Switch closes and the error
canbeclearedwhenthe
heater temperature falls
below 190°F (87°C).
Broken or loose
overtemperature
switch
cable/connection.
Overtemperature
switch failed in the
open position.
If heater is not actually
over temperature, check
all wiring and connections
between the TCM and the
overtemperature switches.
Replace overtemperature
switch.
34 332637C
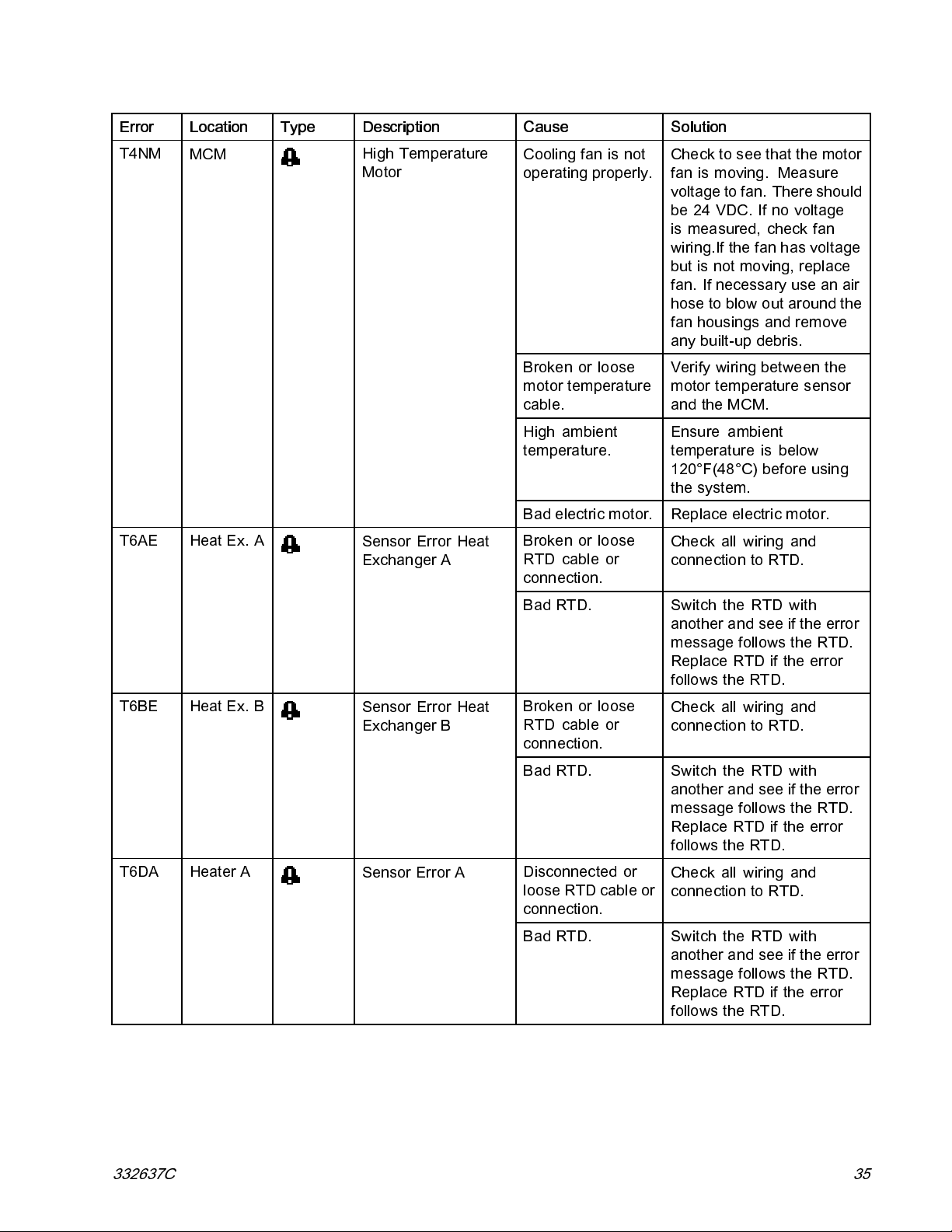
Troubleshooting
Error Location Type Description
T4NM
T6AE Heat Ex. A
MCM
High Temperature
Motor
Sensor Error Heat
Exchanger A
Cause Solution
Cooling fan is not
operating properly.
Broken or loose
motor temperature
cable.
High ambient
temperature.
Bad electric motor. Replace electric motor.
Broken or loose
RTD cable or
connection.
Check to see that the motor
fan is moving. Measure
voltagetofan.Thereshould
be 24 VDC. If no voltage
is measured, check fan
wiring.If the fan has voltage
but is not moving, replace
fan. If necessary use an air
hose to blow out around the
fan hous i ngs and re mov e
any built-up debris.
Verify wiring between the
motor temperature sensor
andtheMCM.
Ensure ambient
temperature is below
120°F(48°C) before using
the system.
Check all wiring and
connection to RTD.
T6BE Heat Ex. B
T6DA Heater A
Sensor Error Heat
Exchanger B
Sensor Error A
Bad RTD.
Broken or loose
RTD cable or
connection.
Bad RTD.
Disconnected or
loose RTD cable or
connection.
Bad RTD.
Switch the RTD with
another and see if the error
messagefollowstheRTD.
Replace RTD if the error
follows the RTD.
Check all wiring and
connection to RTD.
Switch the RTD with
another and see if the error
messagefollowstheRTD.
Replace RTD if the error
follows the RTD.
Check all wiring and
connection to RTD.
Switch the RTD with
another and see if the error
messagefollowstheRTD.
Replace RTD if the error
follows the RTD.
332637C 35
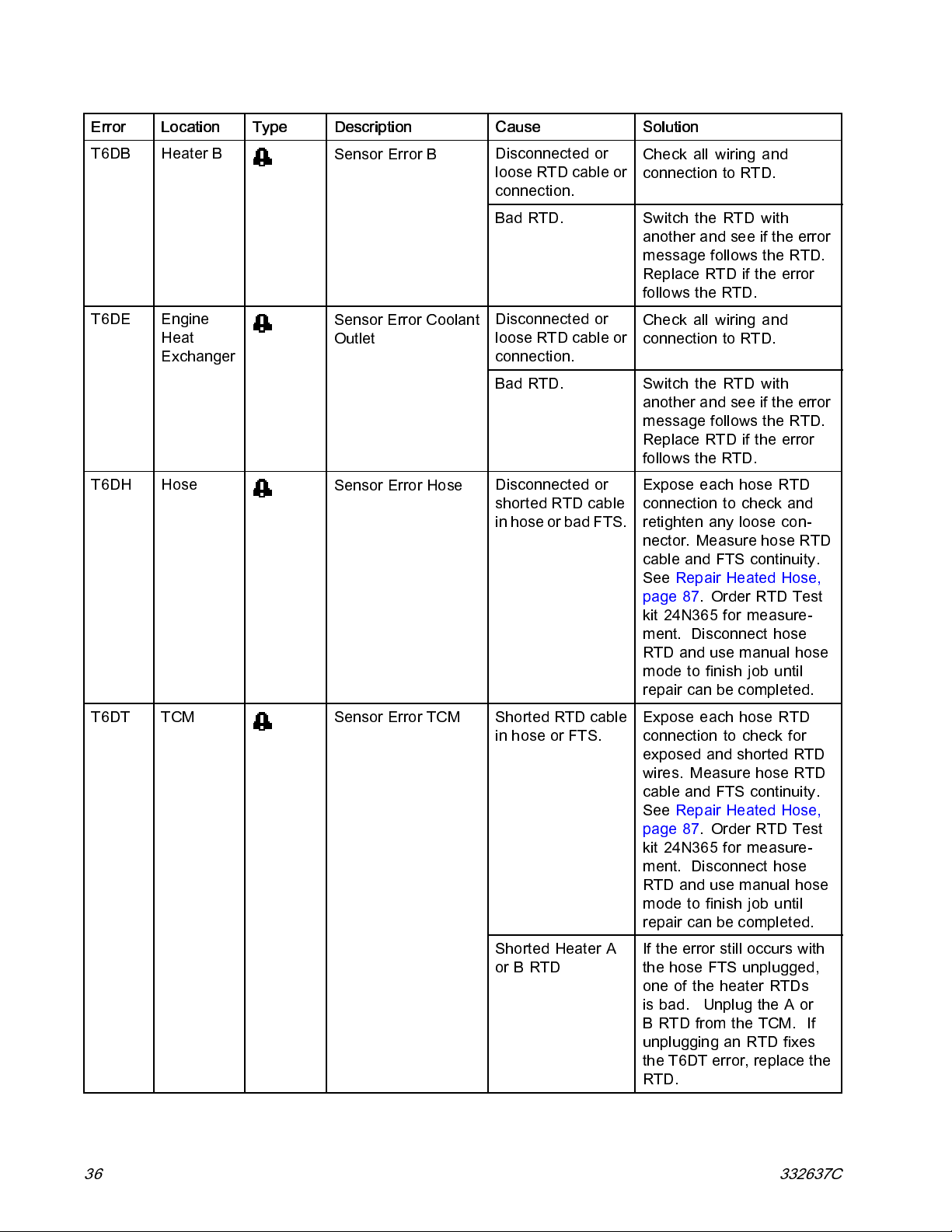
Troubleshooting
Error Location Type Description
T6DB Heater B
T6DE Engine
Heat
Exchanger
T6DH Hose
Sensor Error B
Sensor Error Coolant
Outlet
Sensor Error Hose
Cause Solution
Disconnected or
loose RTD cable or
connection.
Bad RTD.
Disconnected or
loose RTD cable or
connection.
Bad RTD.
Disconnected or
shorted RTD cable
in hose or bad FTS .
Check all wiring and
connection to RTD.
Switch the RTD with
another and see if the error
messagefollowstheRTD.
ReplaceRTDiftheerror
follows th e RTD.
Check all wiring and
connection to RTD.
Switch the RTD with
another and see if the error
messagefollowstheRTD.
ReplaceRTDiftheerror
follows th e RTD.
Expose each hose RTD
connection to check and
retighten any loose c on-
nector. Measure hose RTD
cable and FTS continuity.
See Repair Heated Hose,
page 87.OrderRTDTest
kit 24N365 for measure-
ment. Di sconnect hose
RTD and use manual hose
mode to finish job until
repaircanbecompleted.
T6DT
TCM
Sensor Error TCM
Shorted RTD cable
in hose or FTS.
Shorted Heater A
or B RTD
Expose each hose RTD
connection to check for
exposed and shorted RTD
wires. Measure hose RTD
cable and FTS continuity.
See Repair Heated Hose,
page 87.OrderRTDTest
kit 24N365 for measure-
ment. Di sconnect hose
RTD and use manual hose
mode to finish job until
repaircanbecompleted.
If the error still occurs with
the ho se FTS unpl ug ged ,
one of the heater RTDs
is bad. Unplug th e A or
B RTD from the TCM. If
unplugging an RTD fixes
the T6DT error, replace the
RTD.
36 332637C
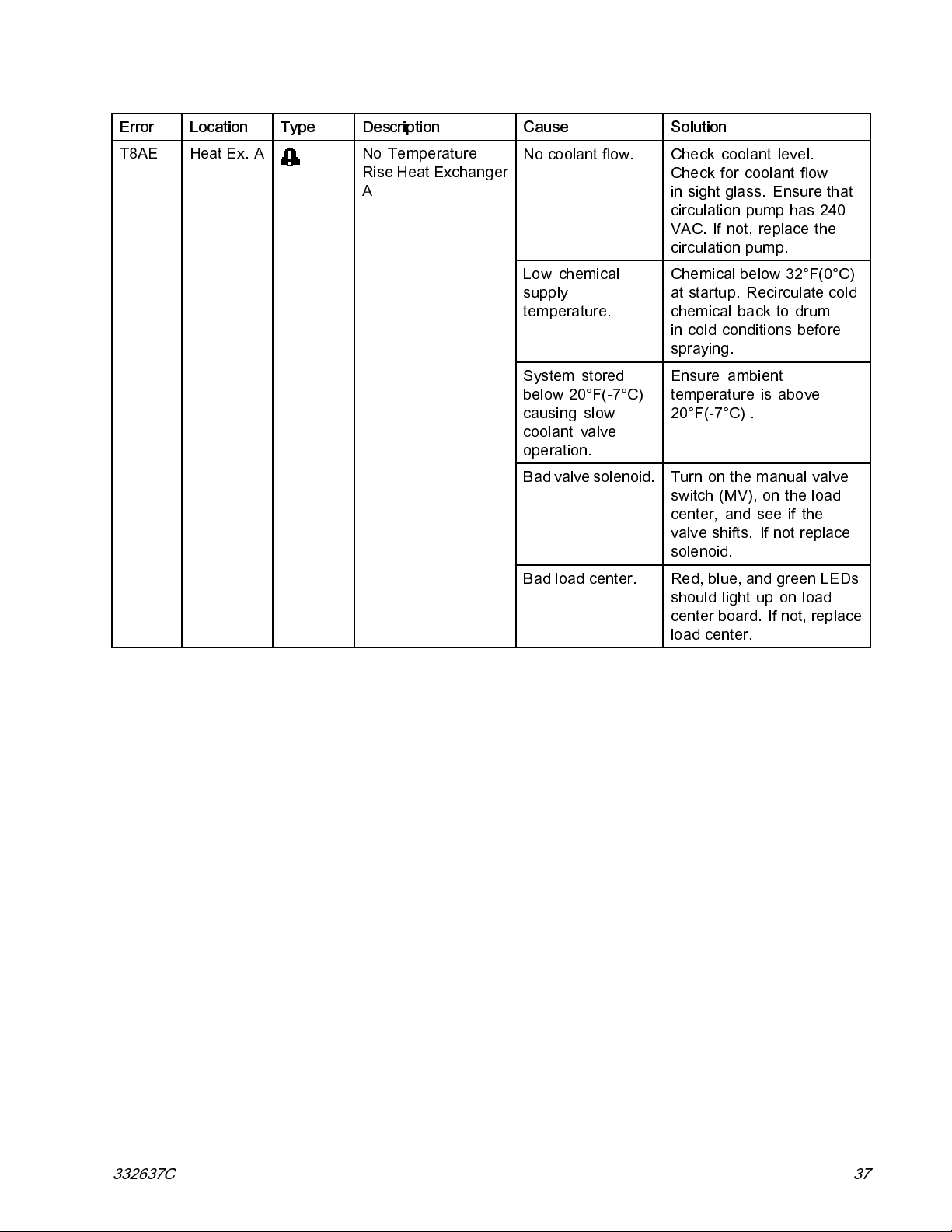
Troubleshooting
Error Location Type Description
T8AE Heat Ex. A No Temperature
Rise Heat Ex ch ang er
A
Cause Solution
No coolant flow. Check coolant lev el.
Check for coolant flow
in sight glass. Ensure that
circulation pump has 240
VAC. If not, re pla ce the
circulation pump.
Low ch emi cal
supply
temperature.
System stored
below 20°F(-7°C)
causing slow
coolant valve
operation.
Bad valve solenoid. Turn on the manual valve
Chemical below 32°F(0°C)
at startup. Recirculate cold
chemical back to drum
in cold conditions before
spraying.
Ensure ambient
temperature is above
20°F(-7°C) .
switch (MV), on the load
center, and see if the
valve shifts. If not replace
solenoid.
Bad load center. Red, blue, and green LEDs
should light up on load
center board. If not, replace
load center.
332637C 37
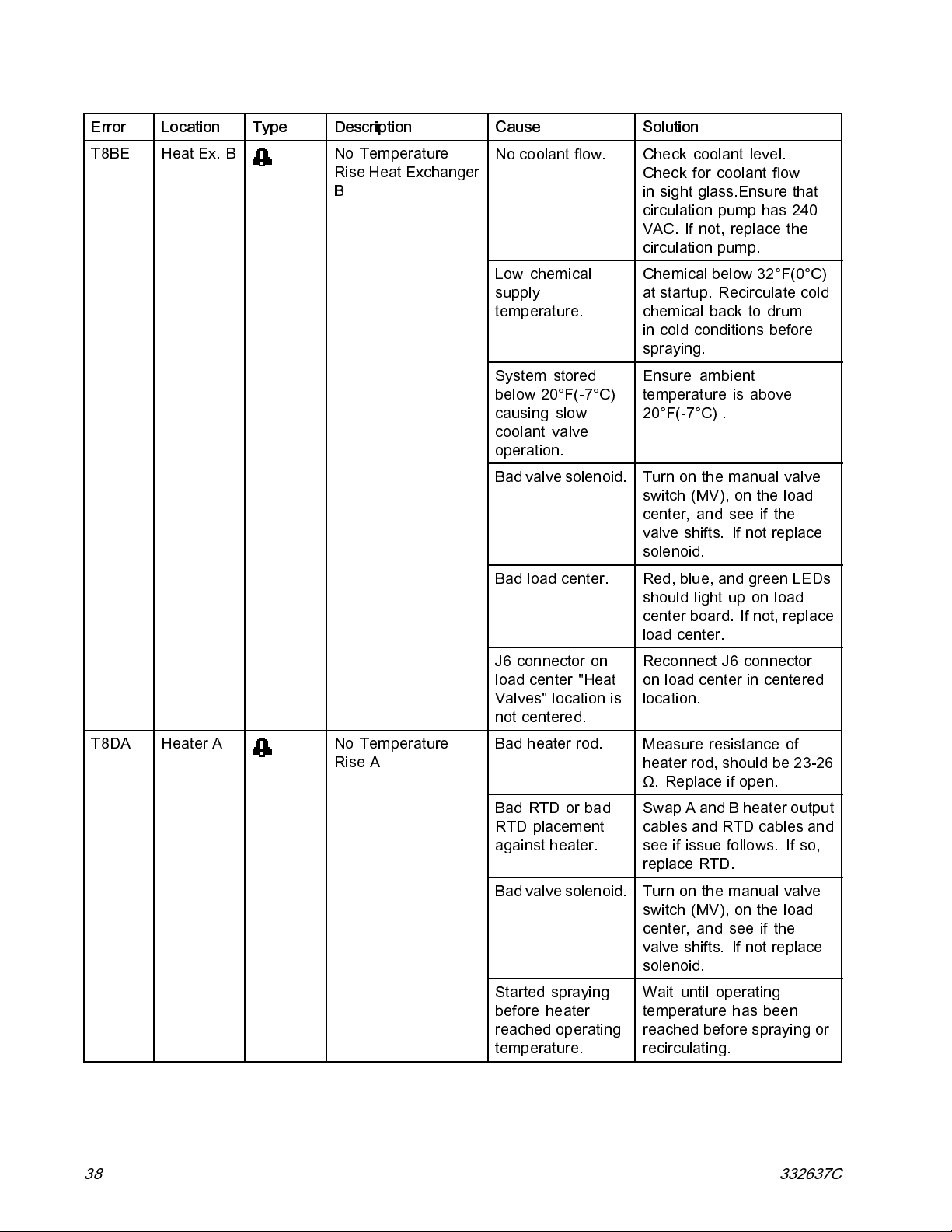
Troubleshooting
Error Location Type Description
T8BE Heat Ex. B No Temperature
Rise Heat Exchanger
B
Cause Solution
No coolant flow. Check coolant level.
Check for coolant flow
in sight glass.Ensure that
circulation pump has 240
VAC. If not, replace the
circulation pump.
Low chemical
supply
temperature.
System stored
below 20°F(-7°C)
causing slow
coolant valve
operation.
Bad valvesolenoid. Turn on the manual valve
Chemical below 32°F(0°C)
at startup. Recirculate cold
chemical back to drum
in cold conditions before
spraying.
Ensure ambient
temperature is above
20°F(-7°C) .
switch(MV),ontheload
center, and see if the
valve shifts. If not replace
solenoid.
T8DA Heater A No Temperature
Rise A
Bad load center. Red, blue, and green LEDs
should light up on load
center board. If not, replace
load center.
J6 connector on
load center "Heat
Valves" location is
not centered.
Bad heater rod.
Bad RTD or bad
RTD placement
against heat er.
Bad valvesolenoid. Turn on the manual valve
Started spraying
before heater
reached operating
temperature.
Reconnect J6 connector
on load center in centered
location.
Measure resistance of
heater rod, should b e 2 3-26
Ω. Replace if open.
Swap A an d B heater o utpu t
cables and RTD cables and
see if issue follows. If so,
replace RTD.
switch(MV),ontheload
center, and see if the
valve shifts. If not replace
solenoid.
Wait until operating
temperature has been
reached before spraying or
recirculating.
38 332637C

Troubleshooting
Error Location Type Description
T8DB Heater B No Temperature
Rise B
T8DH Hose No Temperature
Rise Hose
V1CM MCM Low Voltage MCM
Cause Solution
Bad heater rod.
Bad RTD or bad
RTD placement
against heater.
Bad valve solenoid. Turn on the manual valve
Started spraying
before heater
reached operating
temperature.
Started spraying
before heater
reached operating
temperature.
Loose/bad
connection or
tripped circuit
breaker.
Measure resistance of
heater rod, should be 23-26
Ω. Replace if open.
Swap A and B heater output
cables and RTD cables and
see if issue follows. If so,
replace RTD.
switch (MV), on the load
center, and see if the
valve shifts. If not replace
solenoid.
Wait until operating
temperature has been
reached before spraying or
recirculating.
Wait until operating
temperature has been
reached before spraying or
recirculating.
Check wiring for loose
connection or tripped circuit
breaker.
Low generator line
voltage.
V1IT TCM Low Voltage CAN Bad 24 VDC power
supply.
V1MA
TCM
Low Voltage A
Loose connection
or tripped circuit
breaker.
Low generator line
voltage.
High auxilary
inrush current.
Measure voltage across
main power switch (CT01).
Voltage should measure
between 195 and 264 VAC.
Check voltage of power
supply. Voltage should
be 23-25 VDC. If out of
tolerance, replace power
supply.
Check wiring for loose
connection or tripped circuit
breaker.
Measure voltage across
main power switch (CT01).
Voltage should measure
between 195 and 264 VAC.
Ensure compressor or
air drier are set up to be
continuous run and sized
accordingtothemanual.
332637C 39
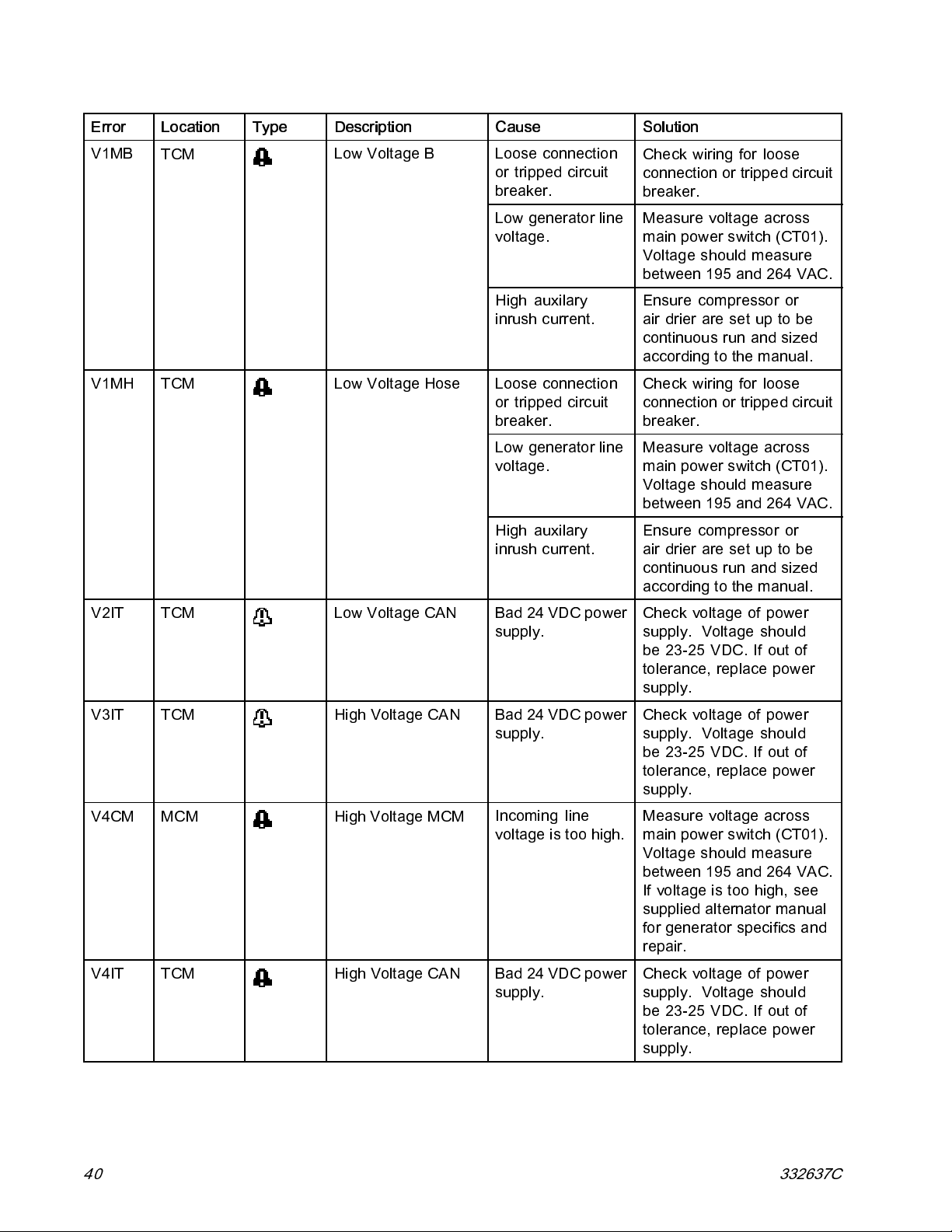
Troubleshooting
Error Location Type Description
V1MB
V1MH
TCM
TCM
Low Voltage B
Low Voltage Hose
Cause Solution
Loose connection
or tripped circuit
breaker.
Low generator line
voltage.
High auxilary
inrush current.
Loose connection
or tripped circuit
breaker.
Low generator line
voltage.
High auxilary
inrush current.
Check wiring for loose
connection or tripped circuit
breaker.
Measure voltage across
main power switch (CT01).
Voltage should measure
between 195 and 264 VAC.
Ensure compressor or
air drier are set up to be
continuous run and sized
accordingtothemanual.
Check wiring for loose
connection or tripped circuit
breaker.
Measure voltage across
main power switch (CT01).
Voltage should measure
between 195 and 264 VAC.
Ensure compressor or
air drier are set up to be
continuous run and sized
accordingtothemanual.
V2IT TCM Low Voltage CAN Bad 24 VDC power
supply.
V3IT
V4CM MCM High Voltage MCM
V4IT
TCM
TCM
High Voltage CAN Bad 24 VDC power
supply.
Incoming line
voltage is too high.
High Voltage CAN Bad 24 VDC power
supply.
Check voltage of power
supply. Voltage should
be 23-25 VDC. If out of
tolerance, replace power
supply.
Check voltage of power
supply. Voltage should
be 23-25 VDC. If out of
tolerance, replace power
supply.
Measure voltage across
main power switch (CT01).
Voltage should measure
between 195 and 264 VAC.
If voltage is too high, see
supplied alternator manual
for generator specifics and
repair.
Check voltage of power
supply. Voltage should
be 23-25 VDC. If out of
tolerance, replace power
supply.
40 332637C
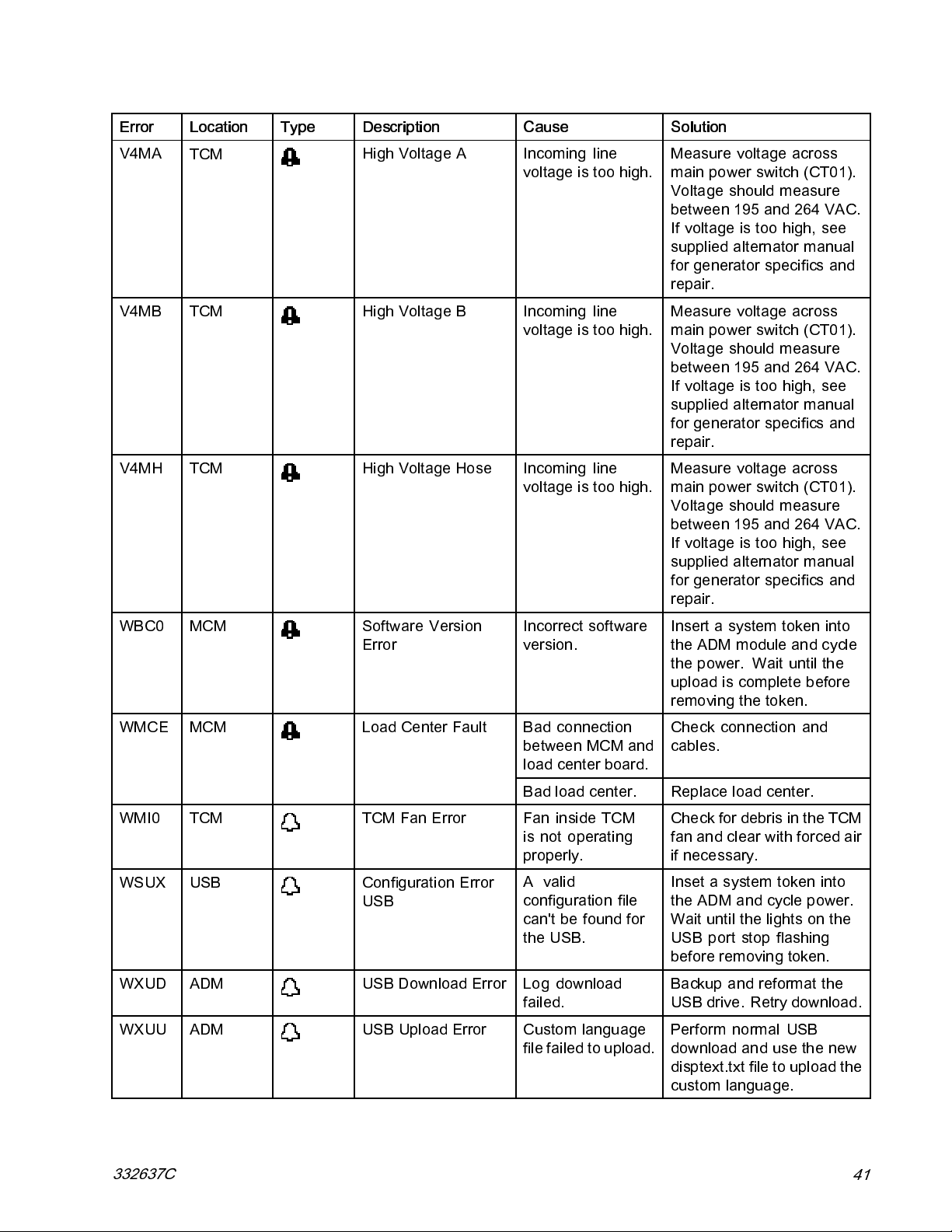
Troubleshooting
Error Location Type Description
V4MA
V4MB
V4MH TCM High Voltage Hose Incoming line
TCM
TCM
High Voltage A Incoming line
High Voltage B Incoming line
Cause Solution
voltage is too high.
voltage is too high.
voltage is too high.
Measure voltage across
main power switch (CT01).
Voltage should measure
between 195 and 264 VAC.
If voltage is too high, see
supplied alternator manual
for generator specifics and
repair.
Measure voltage across
main power switch (CT01).
Voltage should measure
between 195 and 264 VAC.
If voltage is too high, see
supplied alternator manual
for generator specifics and
repair.
Measure voltage across
main power switch (CT01).
Voltage should measure
between 195 and 264 VAC.
If voltage is too high, see
supplied alternator manual
for generator specifics and
repair.
WBC0 MCM Software Version
Error
WMCE MCM Load Center Fault
WMI0
WSUX USB Configuration Error
WXUD ADM
WXUU ADM USB Upload Error Custom language
TCM
TCM Fan Error Fan inside TCM
USB
USB Download Error
Incorrect software
version.
Bad connection
between MCM and
load center board.
Bad load center. Replace load center.
is not operating
properly.
Avalid
configuration file
can't be found for
the USB.
Log download
failed.
filefailedtoupload.
Insert a system token into
the ADM module and cycle
the power. Wait until the
upload is complete before
removing the token.
Check connection and
cables.
Check for debris in the TCM
fan and clear with forced air
if necessary.
Inset a system token into
the ADM and cycle power.
Wait unti l the lights on the
USB port stop flashing
before removing token.
Backup and reformat the
USB drive. Retry download.
Perform normal USB
download and use the new
disptext.txt file to upload the
custom language.
332637C
41

Troubleshooting
System
See Supplied Manuals, page 14, for air compressor service or warranty contact information.
Before performing any troubleshooting procedures:
1. Relieve Pressure. See Pressure Relief Procedure, page 60.
2. Turn main power switch OFF.
3. Allow equipment to cool.
Problem Cause Solution
Reactor ADM does not turn on. No power.
Turn main power switch ON.
Turn circuit breakers ON, see
Repair Circuit Breaker Module,
page 77.
Check circuit breaker (CB10). See
Repair Circuit Breaker Module,
page 77.
Electric motor does not operate.
Electric motor runs erratically. Failed motor bearings. Replace motor, see
Loose co nne cti on s. Check MCM connections. See
Electrical Schematics, page 154.
Tripped circuit breaker (CB02). Reset breaker, see Repair Circuit
Breaker Module, page 77.Check
240VAC at output of breaker.
Shorted windings. Replace motor, see
Repair Electric Motor, page 76.
Repair Electric Motor, page 76.
42
332637C

Problem Cause Solution
Electric motor cooling fan not
working.
Pump output low.
Fluidleakinpumppackingnut
area.
No pressure on one side. Fluid leaking from heater inlet
Air compressor does not start.
Air dryer cooling fan not running. Only runs after hot air flow. Normal operation.
Air dryer not draining water.
Tripped circuit breaker (CB03). Reset circuit breaker (CB03).
Check 240VAC at output of
breaker.
Loose wire.
Fan blade obstructed. Remove obstruction.
Defective fan. Replace. See
Obstructed fluid hose or gun; fluid
hose ID too small.
Worn piston valve or intake valve
in displacement pump.
Pressure setpoint too high. Reduce setpoint and output will
Worn throat seals.
rupture disk (372).
Tripped circuit breaker (CB04). Reset circuit breaker (CB04).
Not wired correctly. See
Compressor starter overheated
from rapid multiple start and stop
procedures.
Power not turned on at dryer.
No air usage. Check after air flowing.
Check. See
Electrical Sch em ati cs , page 154.
Replace Motor Fan, page 82.
Open, clear; use hose with larger
ID.
See pump manual.
increase.
Replace. See pump manual.
Check if heater and PRESSURE
RELIEF/SPRAY valve (SA or SB)
are plugged. Clear. Replace
rupture disk (372) with a new one;
do not replace with a pipe plug.
Electrical Sch em ati cs , page 154.
Let starter cool down for 2 minutes
then press reset on the air
compressor electrical enclosure
and start.
TurndryerswitchON(|).
Troubleshooting
332637C 43

Troubleshooting
Coolant System
Problem Cause Solution
Proportioner Coolant Loop
Air bubbles in sight glass .
Heat exchanger coolant flow
stopped. No flow in sight glass.
Material slo wly heats up.
Heat ex ch ang er coolant in sight
glass is a milky color.
A or B material heats up slower
than the other.
A or B material cooling down
slower than the other.
Air trapped in heat exchanger
coolant.
Coolant hoses between the
proportioner coolant loop and
engine coolant loop were modified
and created a high point air pocket.
Proportioner coolant loop
expansion bottle is empty.
Circulation pump stopped running. Check circuit breaker. Check
Bypass control valve does not
open.
Coolant filter plugged. Clean or repla ce filter in filter
A and B control valves are not
opening fully.
System stored below 20°F(-7°C).
Possible material leaking into
coolant.
Control valve opening too slow. Repair or replace valve. See
System stored below 20°F(-7°C). Ensure system ambient
Control valve coil failed. Repair or replace valve coil. See
Control valve coil not allowing
valve to normally close.
Control valve stuck in open
position.
Bad load center. Replac e the load
See Refill Proportioner Coolant
Loop, page 68.
Ensure coolant hoses have a
constant rise in elevation.
See Refill Proportioner Coolant
Loop, page 68.
voltage.
Repair or replace valve. See
Replace Control Valve, page 94.
housing, see Repair Filter Housing
Filter, page 96 and order replace-
ment filter kit 24T028.
Repair or replace valve. See
Replace Control Valve, page 94.
Ensure system ambient
temperature is above 20°F(-7°C).
Drain Proportioner coolant loop.
See Drain Coolant, page 66.
Check for pressurized material
leaks.
Replace Control Valve, page 94.
temperature is above 20°F(-7°C).
Replace Control Valve, page 94.
Repair or replace valve coil. See
Replace Control Valve, page 94.
Repair valve. See
Replace Control Valve, page 94.
center board. See
Replace Load Center, page 80.
44
332637C

Problem Cause Solution
Engine Coolant Loop
Engine coolant does not reach full
temperature.
Engine temperature normal, but
heat exchanger temperature is low
or slowly increases.
Expansion bottle levels are not
rising when coolant is heating.
Coolant level in engine coolant
expansion bottle rises too high
and too fast.
Coolant level in proportioner
coolant expansion bottle does not
rise when hot.
Coolant level in proportioner
coolant expansion bottle rises too
high and too fast.
Coolant level dropping in overflow
bottle but no visible leaks.
Troubleshooting
Radiator fan does not shut off. Check fan relay. Check fan wiring.
Radiator core becoming plugged.
Engine thermostat not opening. Replace engine thermostat.
Coolant level is low in expansion
bottle.
No coolant flow in engine coolant
loop.
Heat exchanger in the engine
coolant loop is plugged.
Radiator or heat exchanger bottle
cap not opening.
Expansion bottle cap and radiator
cap are switched.
Spring loaded gasket inside
radiator cap does not seal.
Expansion bottle cap and radiator
cap are switched.
Expansion bottle cap stuck open. Replace expansion bottle cap.
Cap not fully tightened.
Replace radiator. See
Remove Radiator, page 100.
Refill Engine Coolant Loop, page
69.
Replace heat exchanger. See
Replace Heat Exchangers, page
91.
Replace cap.
Switch radiator caps. Radiator cap
is marked 16 lbs and expansion
bottle is marked 8 lbs.
Replace radiator cap.
Switch radiator caps. Radiator cap
is marked 16 lbs and expansion
bottle is marked 8 lbs.
Push down and tighten cap past
safety latch position.
332637C 45

Troubleshooting
Hose Heat System
Before performing any troubleshooting procedures:
1. Relieve Pressure. See Pressure Relief Procedure, page 60.
2. Turn main power switch OFF.
3. Allow equipment to cool.
Problem Cause Solution
Ambient temperature is too cold. Use auxiliary hose heat system.Hose heats but heats slower
than usual or it do es not reach
temperature.
FTS failed or not installed correctly. Chec k FTS, see Check RTD
Cables and FTS, page 87.
Hose does not maintain
temperature while spraying.
Hose temperature exceeds
setpoint.
A and B setpoints too low. Increase A and B setpoints.
Hose is designed to maintain
temperature, not to increase it.
Ambient temperature is too cold. Increase A and B setpoints to
increase fluid temperature and
keep it steady.
Flow too high. Use smaller mix chamber.
Decrease pressure.
Hose was not fully preheated. Wait for hose to heat to correct
temperature before spraying.
A and/or B heaters are overheating
material.
Faulty FTS connections. Verify that all FTS conn ec tio ns are
Ambient temperature is too high.
Chec k primary heaters for eithe r
a RTD problem or a failed
element attached to RTD, see
Electrical Schematics, page 154.
snug and that pins of connectors
are clean. Unplug and re-plug
RTD wires, cleaning off any debris.
Cover hoses or move to a location
with a lower ambient temperature.
46 332637C

Troubleshooting
Problem
Erratic hose temperature.
Hose does not heat.
Cause Solution
Faulty FTS connections. Verify that all FTS connections are
snug and that pins of connectors
are clean. Unplug and re-plug
FTS wires along length of hose,
cleaning off any debris.
FTS not installed correctly. FTS should be installed close to
end of hose in same environment
as gun. Verify FTS installation,
see Repair Fluid Temperature
Sensor (FTS), page 88.
FTS failed. Check FTS, see Repair Fluid
Temperature Sensor (FTS), page
88.
FTS not installed correctly. FTS should be installed close to
end of hose in same environment
as gun. Verify FTS installation,
see Repair Fluid Temperature
Sensor (FTS), page 88.
Loose hose electrica l co nne cti on s. Check connections. Repair as
necessary.
Circuit breakers tripped. Reset breakers (CB20 and CB02),
see Repair Circuit Breaker Module,
page 77.
Hose zone not turned on. Turn on hose heat zone.
A and B temperature setpoints too
low.
Failed TCM. Remove TCM and install a new
Check. Increase if necessary.
TCM. New module comes with
current software. Update other
modules if necessary. See
software installation instruction
manual.
332637C
47
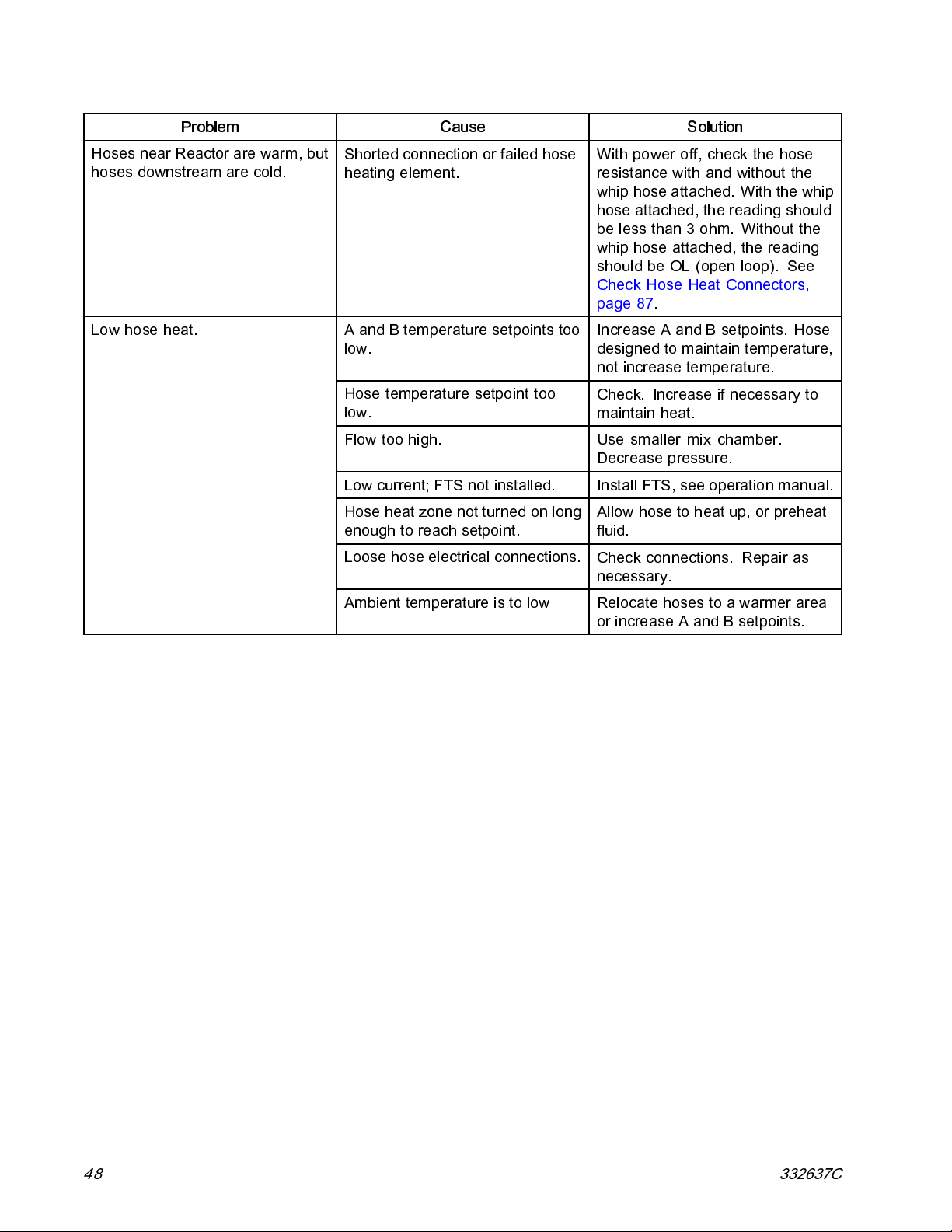
Troubleshooting
Problem
Hoses near Reactor are warm, but
hoses downstream are cold.
Low hose heat.
Cause Solution
Shorted connection or failed hose
heating element.
A and B temperature setpoints too
low.
Hose temperature setpoint too
low.
Flow too high. Use smaller mix chamber.
Low current; FTS not installed. Install FTS, see operation manual.
Hose heat zone not turned on long
enough to reach setpoint.
Loose hose electrical connections.
With power off, check the hose
resistance with and without the
whip hose attached. With the whip
hose attached, the reading should
be less than 3 ohm. Without the
whip hose attached, the reading
should be OL (open loop). See
Check Hose Hea t Connectors,
page 87.
Increase A and B setpoints. Hose
designed to maintain temperature,
not increase temperature.
Check. Increase if necessary to
maintain heat.
Decrease pressure.
Allowhosetoheatup,orpreheat
fluid.
Check connections. Repair as
necessary.
Ambient temperature is to low Relocate hoses to a warmer area
or increase A and B setpoints.
48 332637C
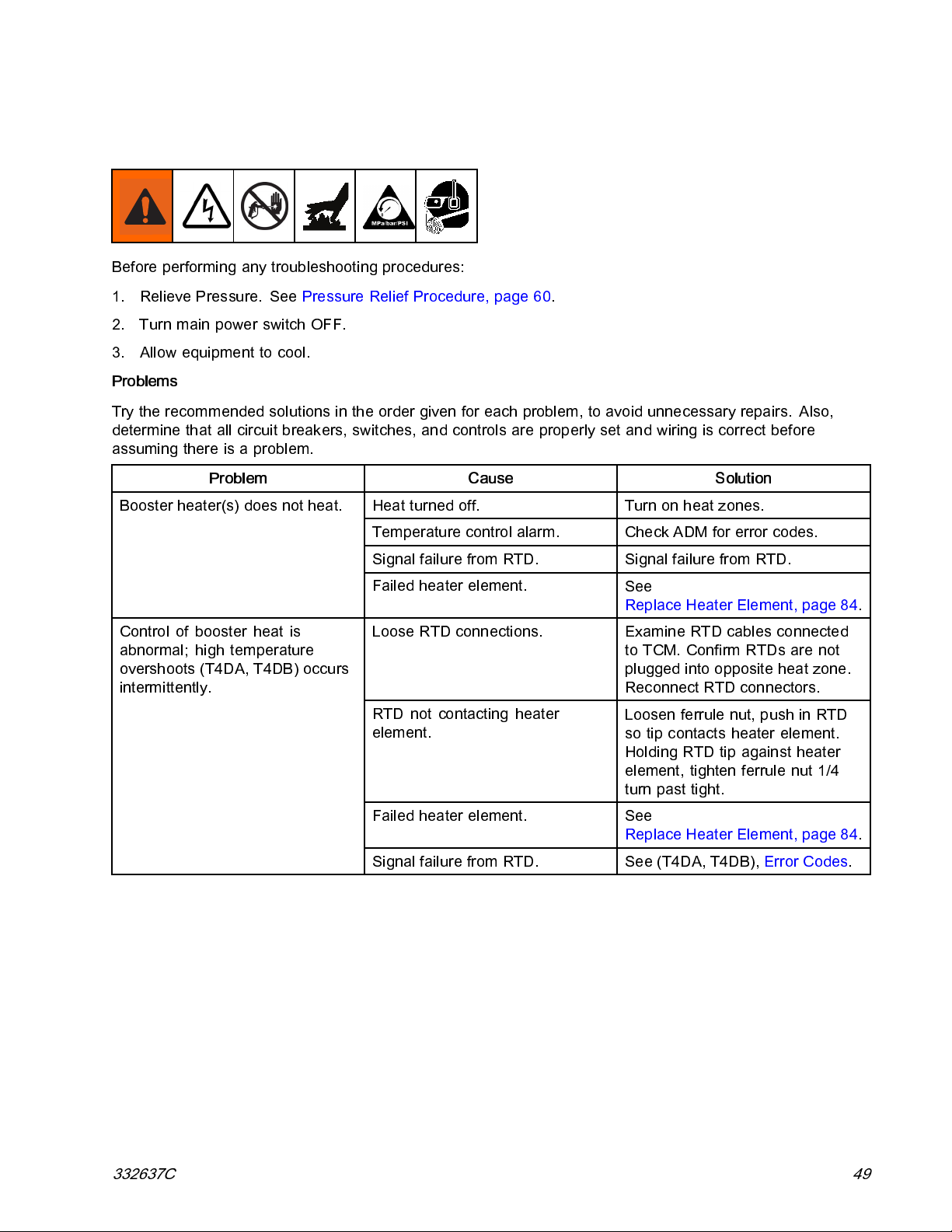
Troubleshooting
Booster Heater
Before performi ng any trouble sh ooti ng procedures:
1. Relieve Pressure. See Pressure Relief Procedure, page 60.
2. Turn main power switch OFF.
3. Allow equipment to cool.
Problems
Try the recommended solutions in the order given for each problem, to avoid unnecessary repairs. Also,
determine that all circuit breakers , switches, and controls are properly set an d wiring is correct before
assuming there is a problem.
Problem
Booster heater(s) does not heat.
Control of booster heat is
abnormal; high temperature
overshoots (T4DA , T4DB) occurs
intermittently.
Cause Solution
Heat turned off.
Temperature control alarm.
Signal failure from RTD. Signal failure from RTD.
Failed heater element.
Loose RTD connections. Examine RTD cables connected
RTD not contacting heater
element.
Failed heater element.
Signal failure from RTD. See (T4DA, T4DB), Error Codes.
Turn on heat zones.
Check ADM for error codes.
See
Replace Heater Element, page 84.
to TCM. Confirm RTDs are not
plugged into opposite heat zone.
Reconnect RTD connectors.
Loosen ferrule nut, push in RTD
so tip contacts heater element.
Holding RTD tip against heater
element, tighten ferrule nut 1/4
turn past tight.
See
Replace Heater Element, page 84.
332637C 49

Troubleshooting
Load Center Diagnostics
Reference Replace Load Center Re lays and Fuses, page 79,andElectric al Schematics, page 154.TheLEDs
on the load center board are helpfu l diagnostic tools wh en troubleshooting problems with the engine. Before
referencing the Engine Troubleshoot ing , page 53, complete the following steps:
1. Identify which LEDs are on and off.
Load Center Component Identification
Figure 1
F3 Radiator Fan Fuse
F4
K1 Fuel Relay
K2
K3
K4 Radiator Fan Relay
MV
LED
D1
D2
D3
D4 Radiator Fan
D10
D12
D14
D23
Load Ce
Starte
Glow Pl
Manua
Related Component
Fuel Shutoff Solenoid Green
Starter
Glow Plugs
A Coolant Valve
B Coolant Valve
Bypass Coolant Valve
Manual Valve Switch
nter Power Fuse
r Relay
ug Relay
lValveSwitch
Manual Valve Switch ON (engine off)
Figure 2
Color
Red
Green
Green Radiator fan is on.
Red
Blue
Green
Red
ON-State Description
Fuel shutoff solenoid on the engine is open.
Starter is cranking.
Glow plugs are heating.
A-side (red) coolant valve is open.
B-side (blue) coolant valve is open.
Bypass coolant valve is open.
al valve switch is in the ON position.
Manu
50 332637C
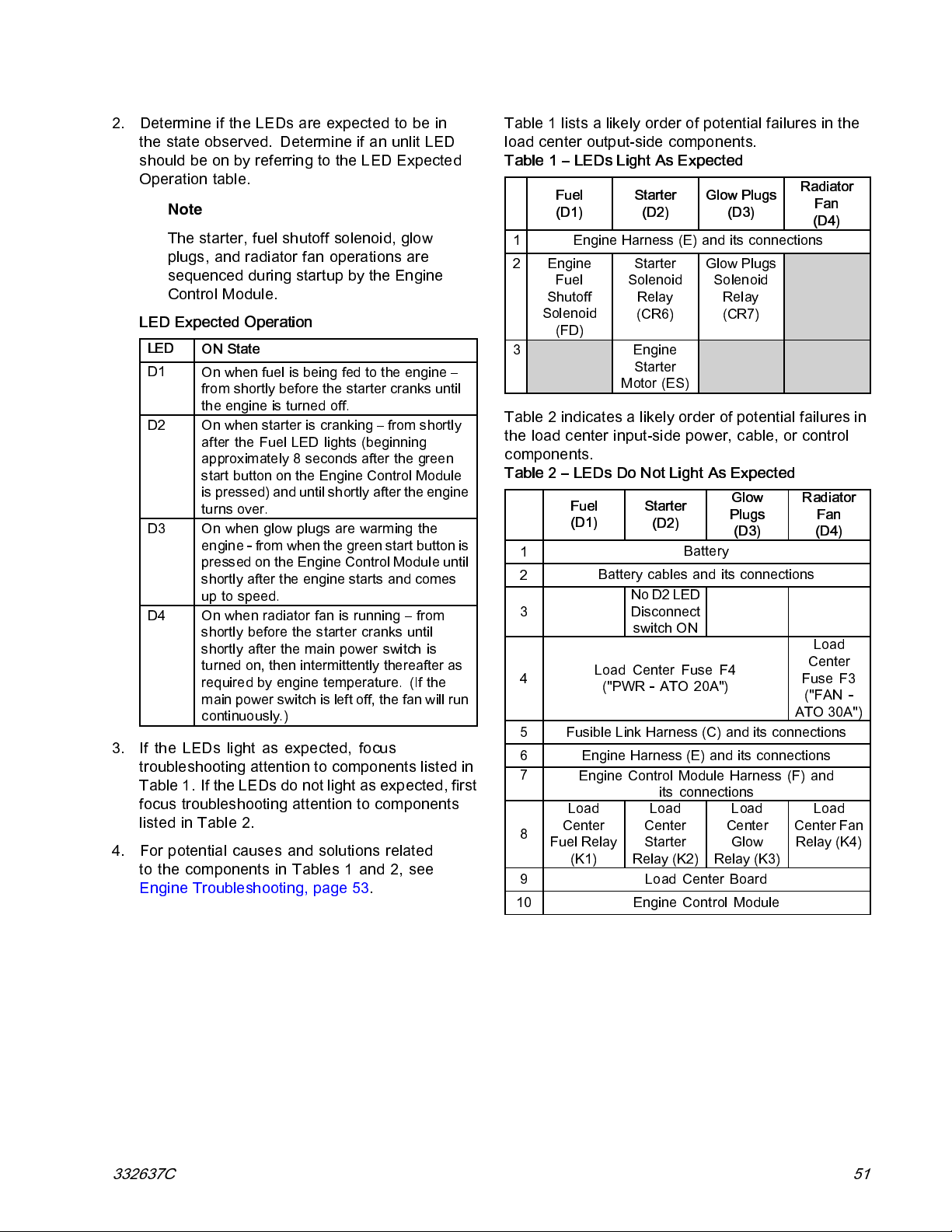
Troubleshooting
2. Determine if the LEDs are expected to be in
the state observed. Determine if an unlit LED
should be on by referring to the LED Expected
Operation table.
Note
The starter, fuel shutoff solenoid, glow
plugs, and radiator fan operations are
sequenced during startup by the Engine
Control Module.
LED Expected Operation
LED
D1
D2
D3
D4 On when radiator fan is running – from
ON State
On when fuel is being fed to the engine –
from shortly before the starter cranks until
the engine is turned off.
On when starter is cranking – from shortly
after the Fuel LED lights (beginning
approximately 8 seconds after the green
start button on the Engine Control Module
is pressed) and until shortly after the engine
turns over.
On when glow plugs are warming the
engine - from when the green start button is
pressed on the Engine Control Module until
shortly after the engine starts and comes
up to speed.
shortly before the starter cranks until
shortly after the main power switch is
turned on, then intermittently thereafter as
required by engine temperature. (If the
main power switch is left off, the fan will run
continuously.)
3. If the LEDs light as expected, focus
troubleshooting a tten tio n to components listed i n
Table 1. If the LEDs do not light as expected, first
focus troubleshooting attention to components
listed in Table 2.
4. For potential causes and solutions related
to the components in Tables 1 and 2, see
Engine Trouble sh ooti ng , page 53.
Table 1 lists a likely order of potential failures in the
load center output-side components.
Table1–LEDsLightAsExpected
Fuel
(D1)
1
2 Engine
3 Engine
Engine Harne
Fuel
Shutoff
Solenoid
(FD)
Starter
(D2)
ss (E) and its connections
Starter
Solenoid
Relay
(CR6)
Starter
Motor (ES)
Glow Plugs
(D3)
Glow Plugs
Solenoid
Relay
(CR7)
Radiator
Fan
(D4)
Table 2 indicates a likely order of potential failures in
the load center input-side power, cable, or control
components.
Table 2 – LEDs Do Not Light As Expected
Fuel
(D1)
1
2
3
4
5
6
7
8
9 Load Center Board
10
Load Center Fuse F4
Fusible Link Harness (C) and its connections
Engine Harness (E) and its connections
Engine Control Module Harness (F) and
Load
Center
Fuel Relay
(K1)
Starter
(D2)
Battery
Battery cables and its connections
No D2 LED
Disconnect
switch ON
("PWR - ATO 20A")
its connections
Load
Center
Starter
Relay (K2)
Engine Control Module
Glow
Plugs
(D3)
Load
Center
Glow
Relay (K3)
Radiator
Fan
(D4)
Load
Center
Fuse F3
("FAN -
ATO 30A")
Load
Center Fan
Relay (K4)
332637C 51
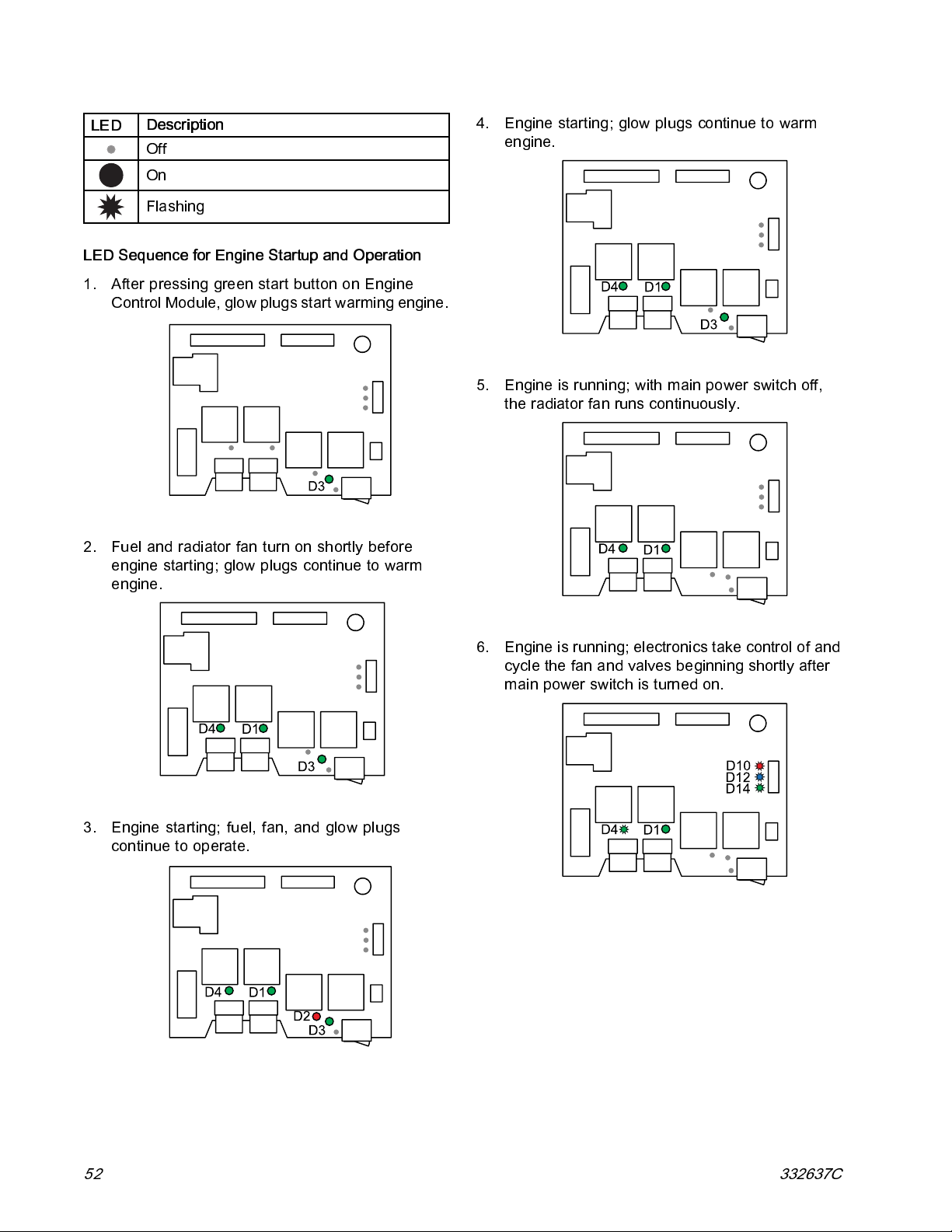
Troubleshooting
LED
LED Sequence for Engine Startup and Operation
1. AfterpressinggreenstartbuttononEngine
2. Fuel and radiator fan turn on shortly before
Description
Off
On
Flashing
Control Module, glow plugs start warming engine.
engine starting; glow plugs continue to warm
engine.
4. Engine starting; glow plugs continue to warm
engine.
5. Engine is running; with main power switch off,
the radiator fan runs continuou sl y .
3. Engine starting; fuel, fan, and glow plugs
continue to operate.
6. Engine is running; electronics take control of and
cycle the fan and valves beginning shortly after
main power switch is turned on.
52 332637C
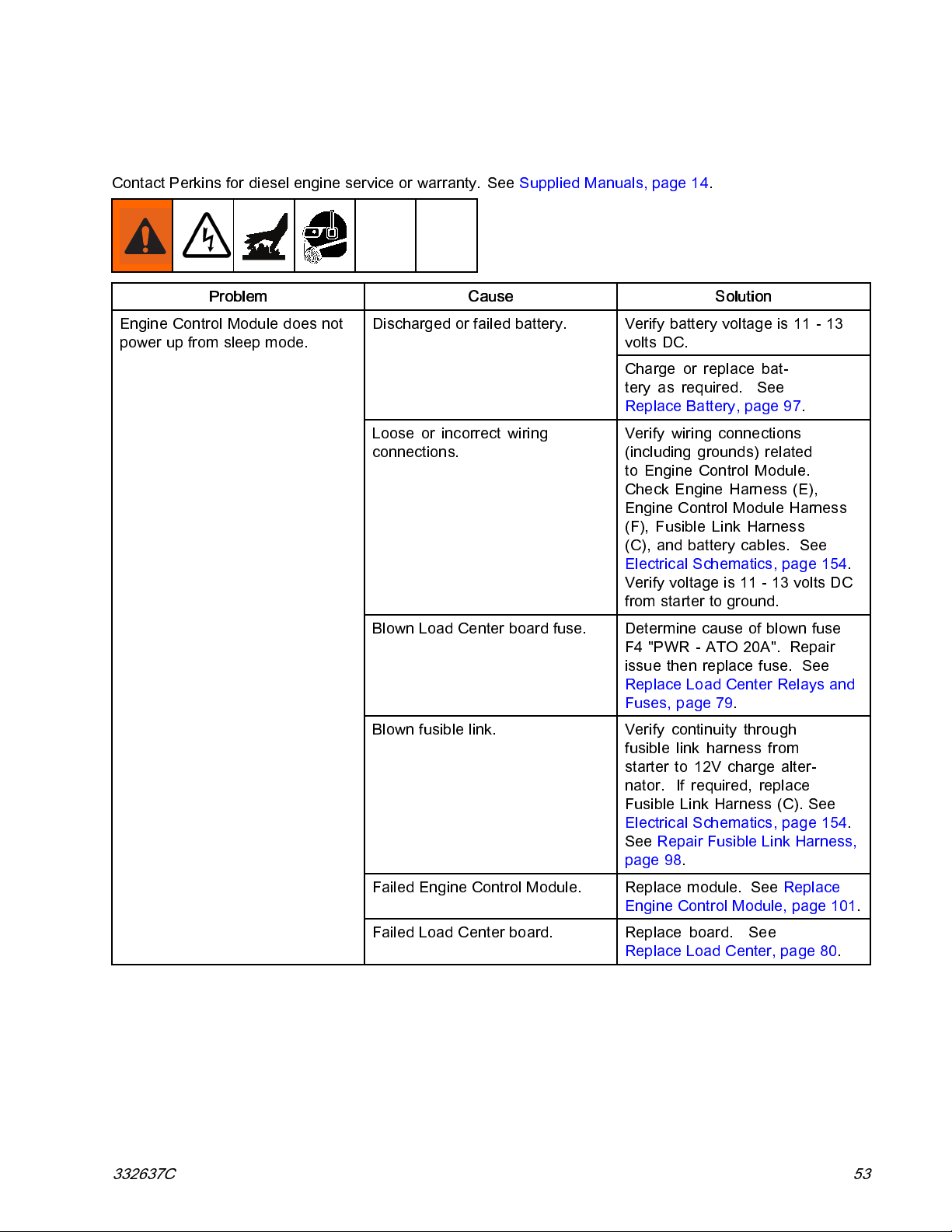
Engine
Contact Perkins for diesel engine service or warranty. See Supplied Manuals, page 14.
Troubleshooting
Problem
Engine Control Module does not
power up from sleep mode.
Cause Solution
Discharged or failed battery.
Loose or incorrect wiring
connections.
Blown Load Center board fuse. Determine cause of blown fuse
Blown fusible link. Verify continuity through
Verify battery voltage is 11 - 13
volts DC.
Charge or replace bat-
tery as required. See
Replace Battery, page 97.
Verify wiring connections
(including grounds) related
to Engine Control Module.
Check Engine Harness (E),
Engine Control Module Harness
(F), Fusible Link Harness
(C), and battery cables. See
Electrical Schematics, pag e 154.
Verifyvoltageis11-13voltsDC
from starter to ground.
F4 "PWR - ATO 20A". Repair
issue then replace fuse. See
Replace Load Center Relays and
Fuses, page 79.
fusible link harness from
starter to 12V charge alter-
nator. If required, replace
Fusible Link Harness (C). See
Electrical Schematics, pag e 154.
See Repair Fusible Link Harness,
page 98.
Failed Engine Control Module. Replace module. See Replace
Engine Control Module, page 101.
Failed Load Center board. Replace board. See
Replace Load Center, page 80.
332637C 53

Troubleshooting
Problem
Reference Load Center Diagnostics, page 50.
Engine does not turn over.
Main power switch on electrical
enclosure is in the ON position.
Discharged or failed battery.
Loose or corroded battery cable
connector.
Loose or incorrect wiring
connections.
Blown Load Center board fuse. Determine cause of blown fuse
Cause Solution
Turn switch to OFF position.
Verify battery voltage is 11 - 13
volts DC.
Charge or replace bat-
tery as required. See
Replace Battery, page 97.
Verify cable connectors. See
Replace Battery, page 97.
Verify wiring connections
(including grounds) related to
starter. Check Engine Harness
(E), Engine Control Module
Harness (F), Fusible Link Harness
(C), Disconnect Check Harness
(H), and battery cables. See
Electrical Schematics, page 154.
Verify voltage is 11 - 13 volts DC
from starter to ground.
F4 "PWR - ATO 20A". Repair
issue then replace fuse. See
Replace Load Center Relays and
Fuses, page 79.
Failed starter relay. Replace relay K2 located
on Load Center board. See
Replace Load Center Relays and
Fuses, page 79.
Failed starter solenoid relay. Replace solenoid relay CR6
locatedonsideofengine. See
Replace Engine Solenoid Relays,
page 80.
Blown fus ib le link. Verify contin uit y through
fusible link harness from
starter to solenoid relay
CR6. If required, replace
Fusible Link Harness (C). See
Electrical Schematics, page 154.
Failed load center board (242). Replace board. See
Replace Load Center, page 80.
Failed engine control module
(428).
Failed engine starter (ES). Contact local Perkins distributor
Replace module. See Replace
Engine Control Module, page 101.
for service.
54 332637C
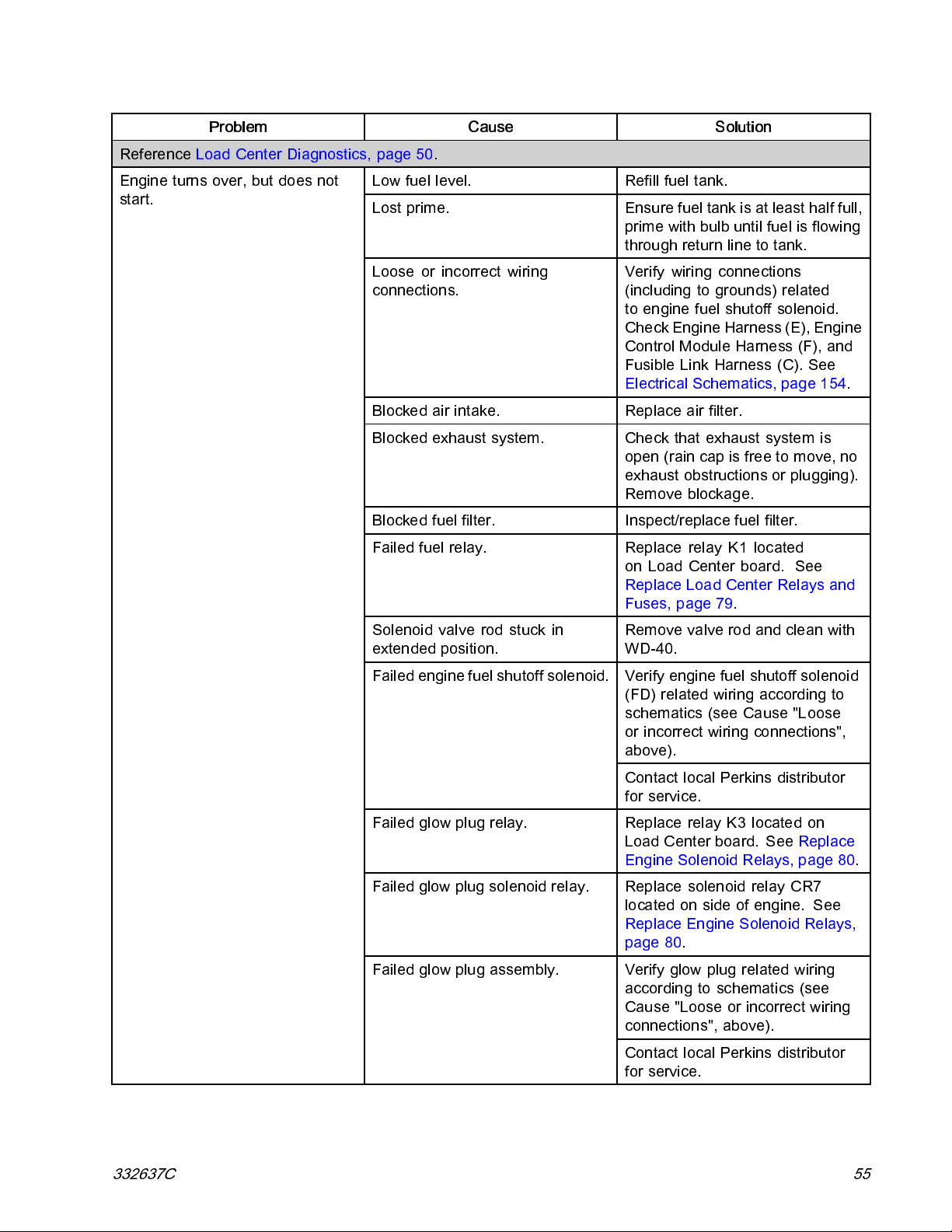
Troubleshooting
Problem
Reference Load Center Diagnostics, page 50.
Engine turns over, but does not
start.
Low fuel level. Refill fuel tank.
Lost prime.
Loose or incorrect wiring
connections.
Blocked air intake. Replace air filter.
Blocked exhaust system.
Blocked fuel filter. Inspect/replace fuel filter.
Failed fuel relay.
Cause Solution
Ensure fuel tank is at least half full,
prime with bulb until fuel is flowing
through return line to tank.
Verify wiring connections
(including to grounds) related
to engine fuel shutoff solenoid.
Check Engine Harness (E), Engine
Control Module Harness (F), and
Fusible Link Harness (C). See
Electrical Sch em ati cs , page 154.
Check that exhaust system is
open (rain cap is free to move, no
exhaust obstructions or plugging).
Remove blockage.
Replace relay K1 located
on Load Center board. See
Replace Load Center Relays and
Fuses, page 79.
Solenoid valve rod stuck in
extended position.
Failed engine fuel shutoff solenoid.
Failed glow plug relay. Replace relay K3 located on
Failed glow plug solenoid relay.
Failed glow plug assembly.
Remove valve rod and clean with
WD-40.
Verify engine fuel shutoff solenoid
(FD) related wiring according to
schematics (see Cause "Loose
or incorrect wiring connections",
above).
Contact local Perkins distributor
for service.
Load Center board. See Replace
Engine Solenoid Relays, page 80.
Replace solenoid relay CR7
locatedonsideofengine. See
Replace Engine Solenoid Relays,
page 80.
Verify glow plug related wiring
accordingtoschematics(see
Cause "Loose or incorrect wiring
connections", above).
Contact local Perkins distributor
for service.
332637C 55

Troubleshooting
Problem
Reference Load Center Diagnostics, page 50.
Engine shuts down, Engine
Control Module sh ows no errors.
Loose or incorrect wiring
connections.
Failed fuel relay.
Failed engine fuel shutoff solenoid.
Cause Solution
Verify wiring connections
(including grounds) related to
engine fuel shutoff solenoid .
Check Engine Harness
(E), and Engine Control
Module Harness (F). See
Electrical Schematics, page 154.
Replace relay K1 located
on Load Center board. See
Replace Load Center Relays and
Fuses, page 79.
Verify engine fuel shutoff solenoid
(FD) related wiring according to
schematics (see Cause "Loose
or incorrect wiring connections",
above).
Contact local Perkins distributor
for service.
56 332637C

Troubleshooting
Problem
Reference Load Center Diagnostics, page 50.
Engine shuts down, Engine
Control Module shows High
Coolant Temperature Shutdown
icon.
Low engine coolant level.
Engine water temperature switch
failed or shorted out.
Loose or incorrect wiring
connections.
Blown radiator fan fuse. Determine cause of blown fuse
Failed radiator fan relay.
Cause Solution
Inspect coolant system for leaks.
Repair as necessary and refill
system.
Check for shorts to
switch wiring. See
Electrical Sch em ati cs , page 154.
Verify wiring connections
(including grounds) related to
radiator fan. Check Engine
Harness (E), and Engine Control
Module Harness (F). See
Electrical Sch em ati cs , page 154.
F3 "FAN - ATO 30A". Repair
issue then replace fuse. See
Replace Load Center Relays and
Fuses, page 79.
Replace relay K4 located
on Load Center board. See
Replace Load Center Relays and
Fuses, page 79.
Obstructed radiator fan. Remove obstructions.
Failed radiator fan. Replace fan. See
Replace Radiator Fan, page 83.
Failed engine coolant temperature
sensor.
Plugged radiator or coolant
system.
Replaceenginecoolant
temperature sensor located
behind radiator connected
to MCM port 3. See
ReplaceEngineRTD,page105.
Clean or replace radiator. See
Remove Radiator, page 100.
Contact local Perkins distributor
for service.
332637C 57

Troubleshooting
Problem
Engine shuts down. Engine
Control Module sh ows Low Oil
Pressure Shutdown icon.
Engine shuts down. Engine
Control Module shows Under
Frequency Sh utd own icon
or Generator Low Voltage
Shutdown icon
.
Cause Solution
Low oil level.
Loose or incorrect wiring
connections.
Failed oil pressure switch.
Low fuel level. Refill fuel tank.
Lost prime.
Blocked air intake.
Blocked exhaust system.
Blocked fuel filter. Replace fuel filter.
Check oil level and refill.
Verify wiring connections
(including grounds) related to
oil pressure switch. Check
Engine Harness (E), and Engine
Control Module Harness (F). See
Electrical Schematics, page 154.
Replace oil pressure switch
Contact local Perkins distributor
for service.
Ensure fuel tank is at least half full,
prime with bulb until fuel is flowing
through return l in e to tank.
Replace air filter.
Check that exhaust system is
open (rain cap is free to move, no
exhaust obstructions or plugging).
Remove blockage.
Generator overloaded. Confirm auxiliary electrical loads
wiredintotheelectricalenclosure
by the customer are within the
system's available auxiliary power
limits.
Loose or incorrect wiring
connections.
Blown voltage sense fuses. Replace fuses F6 and F7 located
Verify wiring connections related
to Engine Control Module, Check
AC Sense Harness (M). See
Electrical Schematics, page 154.
in the junction box above the
120/240 V alternator. Use repair
kit 24M723.
58 332637C

Graco InSite
Troubleshooting
Problem
No module status LEDs are
illuminated.
Has not identified GPS location
(green module s tatus LED
flashing). Unable to identify location. In a
Has not established cellular
connection (orange module status
LED flashing).
Cannot view data for my unit(s) on
website.
Reactor temperature data not
displayed on website.
Hose zone temperature data not
displayed on website.
Reactor pressure data not
displayed on website.
No power to cellular module.
Still identifying location. Wait a few minutes for the unit to
location where GPS lock cannot
occur. Buildings and warehouses
often prevent GPS locks.
Still establishing cellular
connection.
Unable to establish cellular
connection.
Graco InSite unit has not been
activated.
Reactor temperature
measurement is not working.
The RTD is not correctly installed
onthehoseorisbroken.
Reactor pressure measurement is
not working.
Cause Solution
Turn Reactor power ON.
Ensure cable is installed between
cellular module and power supply
and MCM.
identify th e location.
Move system to a location with a
clear view of the sky .
Useextensioncable16X521and
move cellular module to a location
with a clear view of the sky.
Wait a few minutes for the unit to
establish the connection.
Move system to a location with
cellular service to establish cellular
connection.
Useextensioncable16X521and
move cellular module to a location
with a clear view of the sky.
Activate unit. See Registering
andActivatingtheGracoInSite
section.
See System troubleshooti ng
section.
See RTD repair section.
See System troubleshooti ng
section.
332637C 59

Pressure Relief Procedure
Pressure Relief Procedure
Follow the Pressure Relief Procedure
whenever you see this symbol.
This equipment stays pressurized until pressure
is manually relieved. To help prevent serious
injury from pressurized fluid, such as skin injection,
splashing fluid and moving parts, follow the
Pressure Relief Procedure when you stop spraying
and before cleaning, checking, or servicing
equipment.
The Fusion AP gun is shown.
1. Relieve pressure in gun and perform gun
shutdown procedure. See gun manual.
2. Close gun fluid inlet valves A and B.
4. Route fluid to waste containers or supply tanks.
Turn PRESSURE RELIEF/SPRAY valves (SA,
SB) to PRESSURE RELIEF/CIRCULATION
. Ensure gauges drop to 0.
5. Engage gun piston safety lock.
Fusion Probler
6. Disconnect gun air line and remove gun fluid
manifold.
Fusion Probler
3. Shut off feed pumps and agitator, if used.
60 332637C

Shutdown
Shutdown
Shutdown system to avoid electric shock. All
electrical wiring must be done by a qualified
electrician and comply with all local codes and
regulations. To hel p prevent serious injury from
pressurized fluid, such as skin injection, splashing
fluidandmovingparts,followthePressureRelief
Procedure when you stop spraying and before
cleaning, checking, or servicing equipment.
Immediate Shutdown
NOTICE
To avoid system damage, follow daily shutdown
procedure. Use only for immediate shutdown.
For immediate shutdown, press :
2. Turn off all heat zones.
3. Set PRESSURE RELIEF/SPRAY valves (SA,
SB) to PRESSURE RELIEF/CIRCULATION
4. Relieve pressure. See
Pressure Relief Procedure, page 60.
.
Daily Shutdown
NOTICE
Proper system setup, s ta rtup, and shutdown
procedures are critical to electrical equipment
reliability. The following procedures ensure steady
voltage. Failure to follow these proc edu res will
cause voltage fluctuations that can damage
electrical equi pm ent and void the warranty.
1. Press to stop the pumps.
5. Press
park operation is complete when green dot goes
out. Verify the park operation is com pl ete before
moving to next step.
6. Press to deactivate the system.
to park the Component A Pump. The
332637C 61

Shutdown
7. Turn off the air compressor, air dryer, and
breathing air.
8. Closethem
ain air shutoff valve.
9. Turn main power switch OFF. Allow engine
cooling dwell time prior to shutting down the
engine.
To prevent electric shock do not remove any
shrouds or open the electrical enclosure door.
240 V is still present in the system until the
engine h as stopped.
NOTICE
Allow engine cooling dwell time, per
manufacturer recommendations, prior to
shutdown. Dwell time will help engine
properly cool down after running at operating
temperature for any period of time. Stopping
the engine immediately after running it at
full load for an extended period of time can
causetheenginetooverheatduetothelackof
coolant flow. See engine manual.
10. Press to stop the engine.
11. Close all fluid supply valves.
62 332637C

Shutdown
12. Engage gun piston safety lock then close fluid
inlet valves A and B.
Fusion Probler
332637C 63
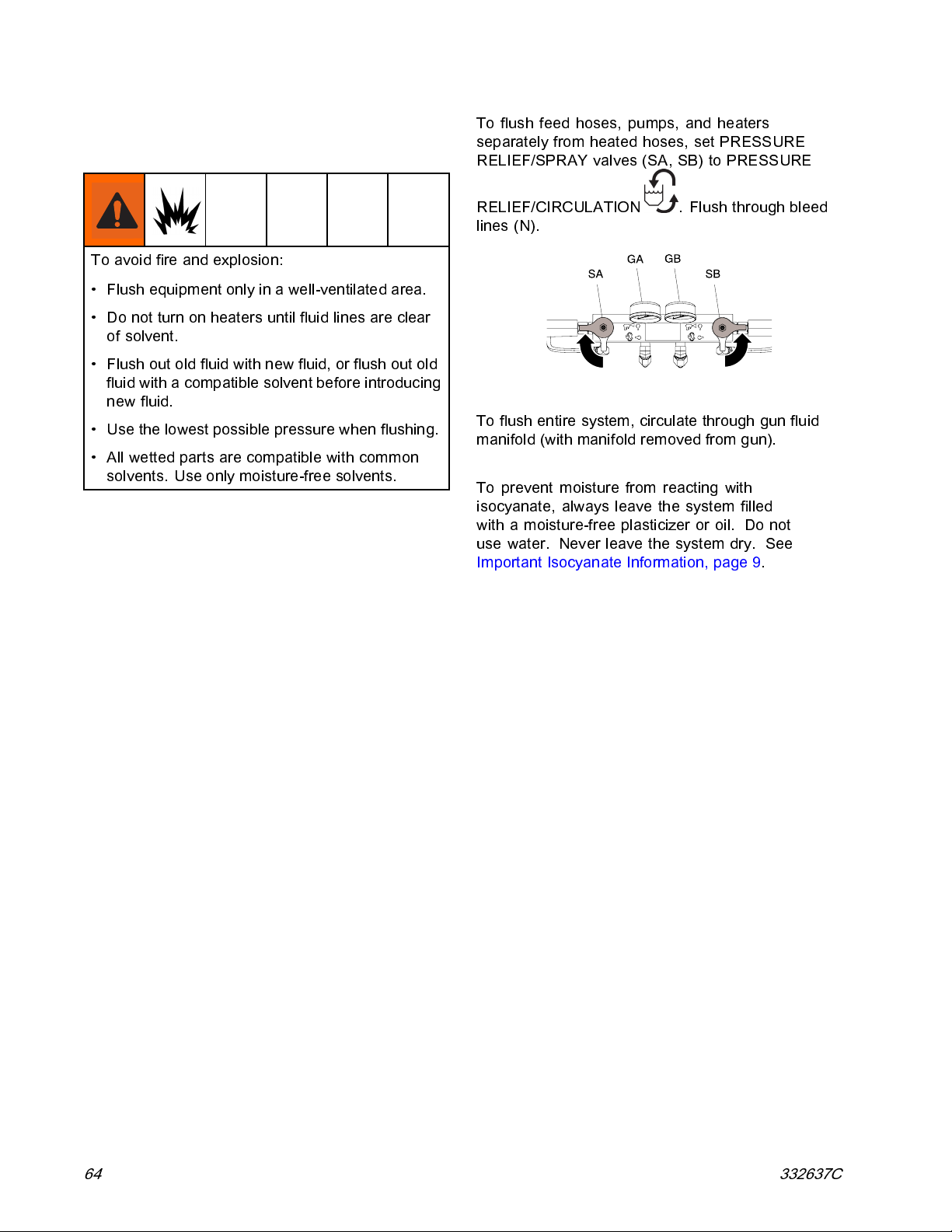
Flushing
Flushing
To avoid fire and explosion:
• Flush equipment only in a well-ventilated area.
• Do not turn on heaters until fluid lines are clear
of solvent.
• Flush out old fluid with new fluid, or flush out old
fluid with a compatible solvent before introducing
new fluid.
• Use the lowest possible pressure when flushing.
• All wetted parts are compatible with common
solvents. Use only moisture-free solvents.
To flush feed hoses, pumps, and heaters
separately from heated hoses, set PRESSURE
RELIEF/SPRAY valves (SA, SB) to PRESSURE
RELIEF/CIRCULATION
lines (N).
To flush entire system, circulate through gun fluid
manifold (with manifold removed from gun).
To prevent moisture from reacting with
isocyanate, always leave the system filled
with a moisture-free plasticizer or oil. Do not
use water. Never leave the system dry. See
Important Isocyanate Information, page 9.
. Flush through bleed
64 332637C

Repair
Repair
Repairing this equipment requires access to parts
that may cause electric shock or other serious
injury if work is not performed properly. Be sure to
shut off all powe r to equipment before repairing.
Before Beginning Repair
NOTICE
Proper system setup, s ta rtup, and shutdown
procedures are critical to electrical equipment
reliability. The following procedures ensure steady
voltage. Failure to follow these proc edu res will
cause voltage fluctuations that can damage
electrical equi pm ent and void the warranty.
1. Close the fluid inlet valve at the pump inlet and
shut off the appropriate feed pump. This prevents
material from being pumped while cleaning the
screen.
2. Place a container un der the strainer base to catch
drain off when removing the strainer plug (C).
3. Remove the screen (A) from the strainer
manifold. Thoroughly flush the screen with
compatible solvent and shake it dry. Inspect the
screen. No more than 25% of the mesh should
be restricted . If mo re than 25% of the mesh is
blocked, replace the screen. Inspect the gasket
(B) and replace as required.
4. Ensurethepipeplug(D)isscrewedintothe
strainer plug (C). Install the strainer plug with the
screen (A) and gasket (B) in place and tighten.
Do not overtighten. Let the gasket make the seal.
5. Open the fluid inlet valve, ensure that there are
no leaks, and wipe the equipment clean. Proceed
with operation.
1. Flush if necessary. See Flushing, page 64.
2. See Shutdown, page 61.
Flush Inlet Strainer Screen
The inlet strainers filter out particles that can plug the
pump inlet check valves. Inspect the screens daily as
part of the startup routine, and clean as req ui red.
Isocyanate can crystalli ze from moisture
contamination or from freezing. If the chemicals used
are clean and proper storage, transfer, and operating
procedures are followed, there should be minimal
contamination of the A-side screen.
Note
CleantheA-sidescreenonlyduring
daily startup. This minimizes moisture
contamination by immediately flushing
out any isocyanate residue at the start of
dispensing operations.
A
B
C
D
Figure 3
332637C 65
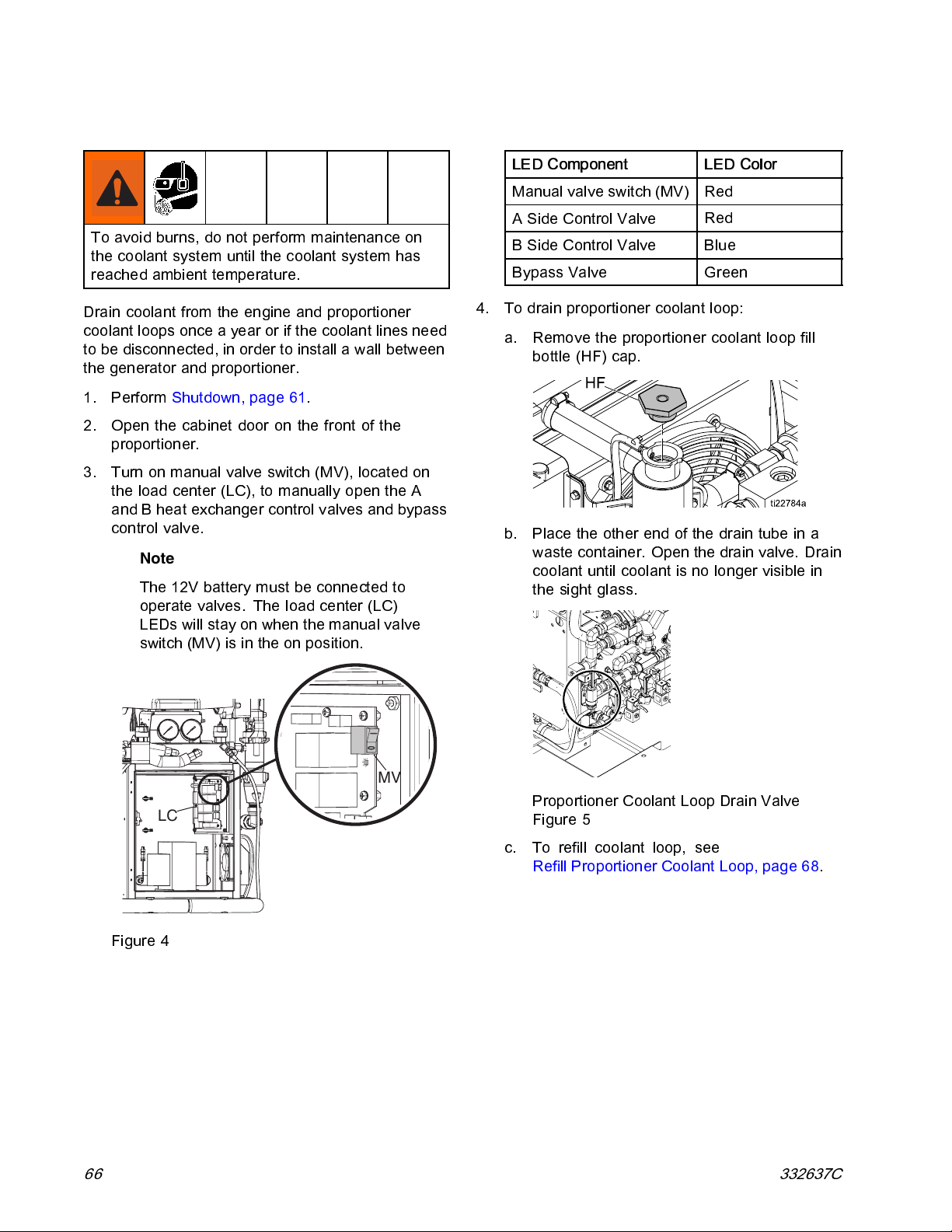
Repair
Drain Coolant
LED Component LED Color
To avoid burns, do not perform maintenance on
the coolant system until the coolant system has
reached ambient temperature.
Drain coolant from the engine and proportioner
coolant loops once a year or if the coolant lines need
to be disconnected, in order to install a wall between
the generator and proportioner.
1. Perform Shutdown, page 61.
2. Open the cabinet door on the front of the
proportioner.
3. Turn on manual valve switch (MV), located on
the load center (LC), to manually open the A
and B heat exchanger control valves and bypass
control valve.
Note
The 12V battery must be connected to
operate valves. The load ce nter (LC)
LEDs will stay on when the manual valve
switch (MV) is in the on position.
Manualvalveswitch(MV)
A Side Control Valve
B Side Control Valve
Bypass Valve
4. To drain proportioner coolant loop:
a. Remove the proportioner coolant loop fill
bottle (HF) cap.
b. Placetheotherendofthedraintubeina
waste container. Open the drain valve. Drain
coolant until coolant is no longer visible in
the sight glass.
Red
Red
Blue
Green
MV
LC
Figure 4
66 332637C
Proportioner Coolant Loop Drain Valve
Figure 5
c. To refill coolant loop, s ee
Refill Proportioner Coolant Loop, page 68.
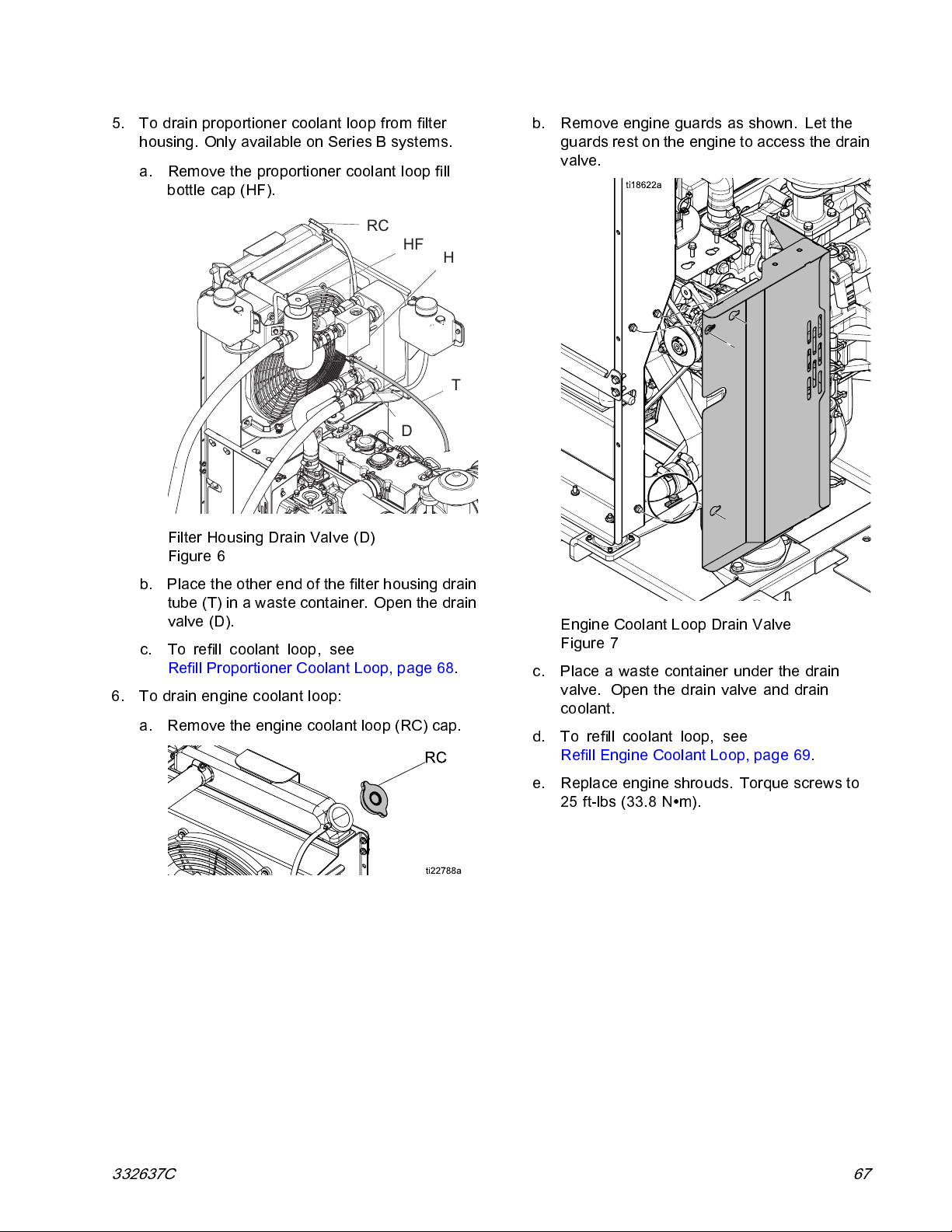
Repair
5. To drain proportioner coolant loop from filter
housing. Only available on Series B systems.
a. Remove the proportioner coolant loop fill
bottle cap (HF).
5&
+)
'
Filter Housing Drain Valve (D)
Figure 6
b. Remove engine guards as shown. Let the
guards rest on the engine to access the drain
valve.
+
7
b. Place the other end of the filter housing drain
tube (T) in a waste container. Open the drain
valve (D).
c. To refill coolant loop, see
Refill Proportioner Coolant Loop, page 68.
6. To drain engine coolant loop:
a. Remove the engine coolant loo p (RC) cap.
Engine Coolant Loop Drain Valve
Figure 7
c. Place a waste container under the drain
valve. O pen the drain valve and drain
coolant.
d. To refill coolant loop, see
Refill Engine Coolant Loop, page 69.
e. Replace engine shrouds. Torque screws to
25 ft-lbs (33.8 N∙m).
332637C 67
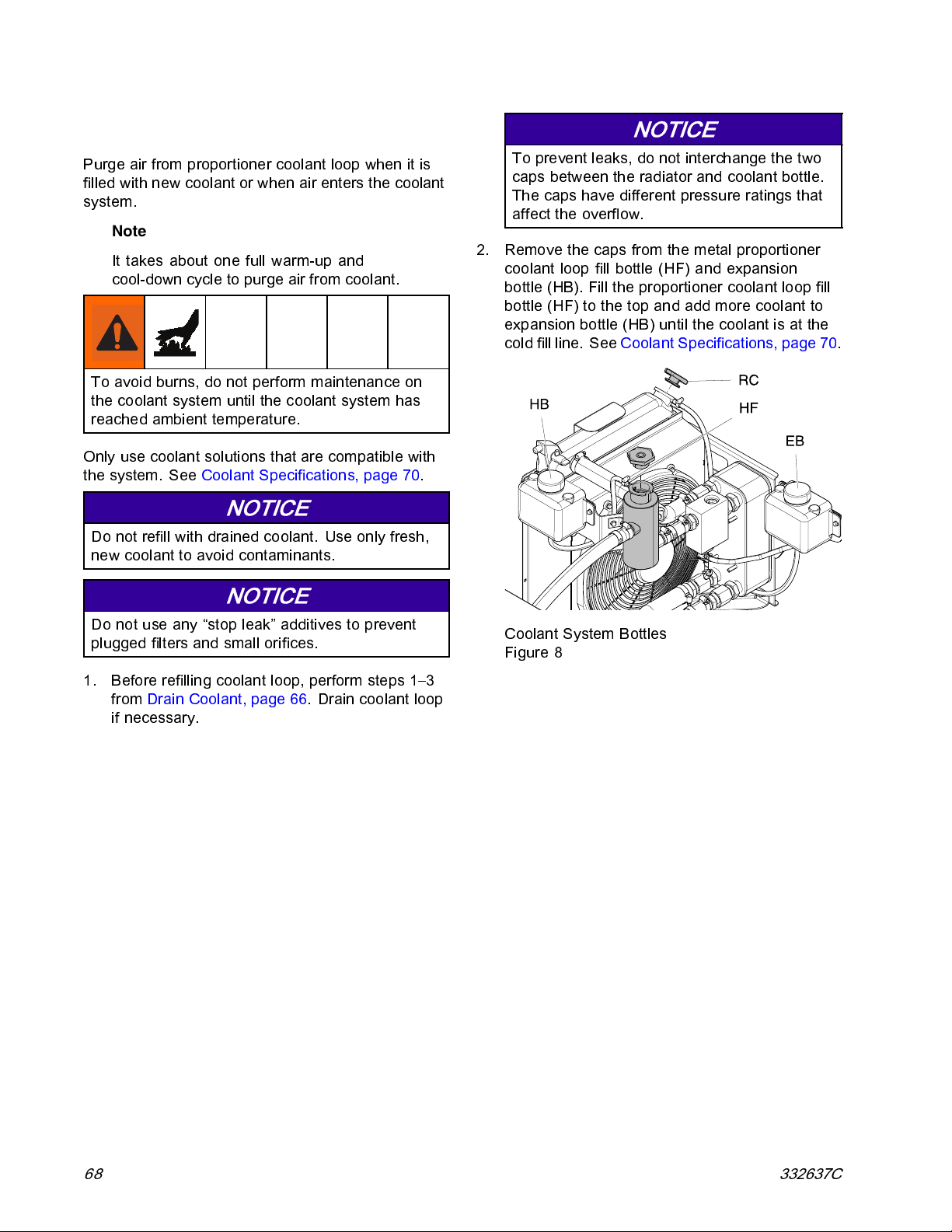
Repair
Refill Proportioner Coolant Loop
Purge air from proportioner coolant loop when it is
filled with new coolant or when air enters the coolant
system.
Note
It takes about one full warm-up and
cool-down cycle to purge air from coolant.
To avoid burns, do not perform maintenance on
the coolant system until the coolant system has
reached ambient temperature.
Only use coolant solutions that are compatible with
the system. See Coolant Specifications, page 70.
NOTICE
Do not refill with drained coolant. Use only fresh,
new coolant to avoid contaminants.
NOTICE
To prevent leaks, do not interchange the two
caps between the radiator and coolant bottle.
The caps have different pressure ratings that
affect the overflow.
2. Remove the caps from the metal proportioner
coolant loop fill bottle (HF) and expansion
bottle (HB). Fill the proportioner coolant loop fi ll
bottle (HF) to the top and add more coolant to
expansion bottle (HB) until the coolant is at the
cold fill line. See Coolant Specifications, page 70.
NOTICE
Do not use any “stop leak” additives to prevent
plugged filters and small orifices.
1. Before refilling coolant loop, perform steps 1–3
from Drain Coolant, page 66. Drain coolant loop
if necessary.
Coolant System Bottles
Figure 8
68 332637C
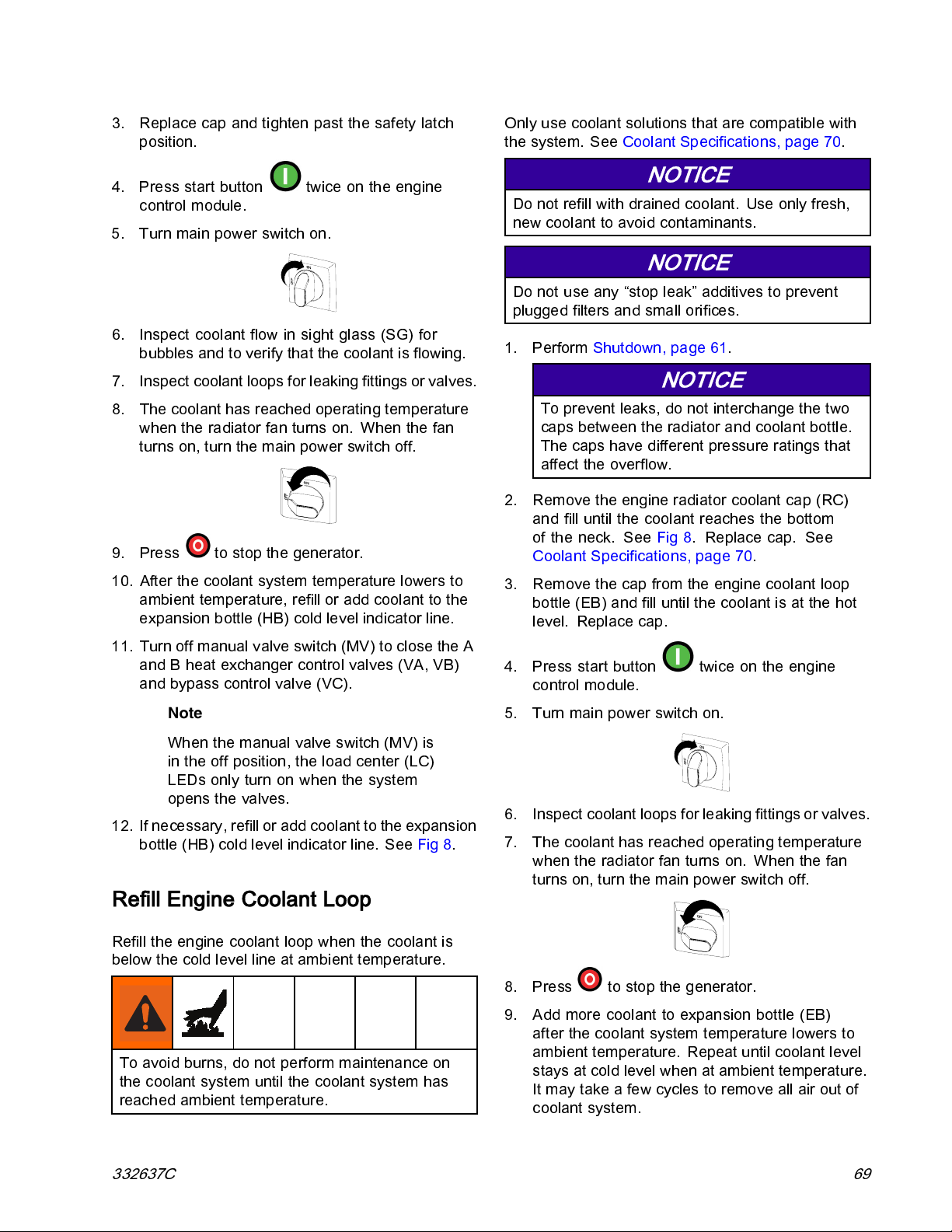
Repair
3. Replace cap and tighten past the safety latch
position.
4. Press start button
control module.
5. Turn main power switch on.
6. Inspect coolant flow i n sight glass (SG) for
bubbles and to verify that the coolant is flowing.
7. Inspect coolant loops for leaking fittings or valves.
8. The coolant has reached operating temperature
when the radiator fan turns on. When the fan
turns on, turn the main power sw itc h off.
9. Press to stop the generato r.
10. After the coolant sy s tem temperature lowers to
ambient temperature, refill or add coolant to the
expansion bottle (HB) cold level indicator line.
11. Turn off manual valve switch (MV) to close the A
and B heat exchanger control valves (VA, VB)
and bypass control valve (VC).
twiceontheengine
Only use coolant solutions that are compatible with
the system. See Coolant Specifications, page 70.
NOTICE
Do not refill with drained coolant. Use only fresh,
new coolant to avoid contaminants.
NOTICE
Do not use any “stop leak” additives to prevent
plugged filters and small orifices.
1. Perform Shutdown, page 61.
NOTICE
To prevent leaks, do not interchange the two
caps between the radiator and coolant bottle.
The caps have different pressure ratings that
affect the overflow.
2. Removetheengineradiatorcoolantcap(RC)
and fill until the coolant reaches the bottom
of the neck. See Fig 8. Replace cap. See
Coolant Specifications, page 70.
3. Remove th e cap from the engine coolant loop
bottle (EB) and fill until the coolant is at the hot
level. Replace cap.
4. Press start button
control module.
twiceontheengine
Note
When the manual valve switch (MV) is
in the off position, the load center (LC)
LEDs only turn on when the system
opens the valves.
12. If necessary, refill or add coolant to the expansion
bottle (HB) cold level indicator line. See Fig 8.
Refill Engine Coolant Loop
Refill the engine coolant loop when the coolant is
below the cold level line at ambien t t emp eratu re.
To avoid burns, do not perform maintenance on
the coolant system until the coolant system has
reached ambient temperature.
5. Turn main power switch on.
6. Inspect coolant loops for leaking fittings or valves.
7. The coolant has reached operating temperature
when the radiator fan turns on. When the fan
turns on, turn the main power switc h off.
8. Press to stop the generator.
9. Add more coolant to expansion bottle (EB)
after the coolant system temperature lowers to
ambient temperature. Repeat until coolant level
stays at cold level when at ambient temperature.
It may take a few cycles to remove all air out of
coolant system.
332637C 69
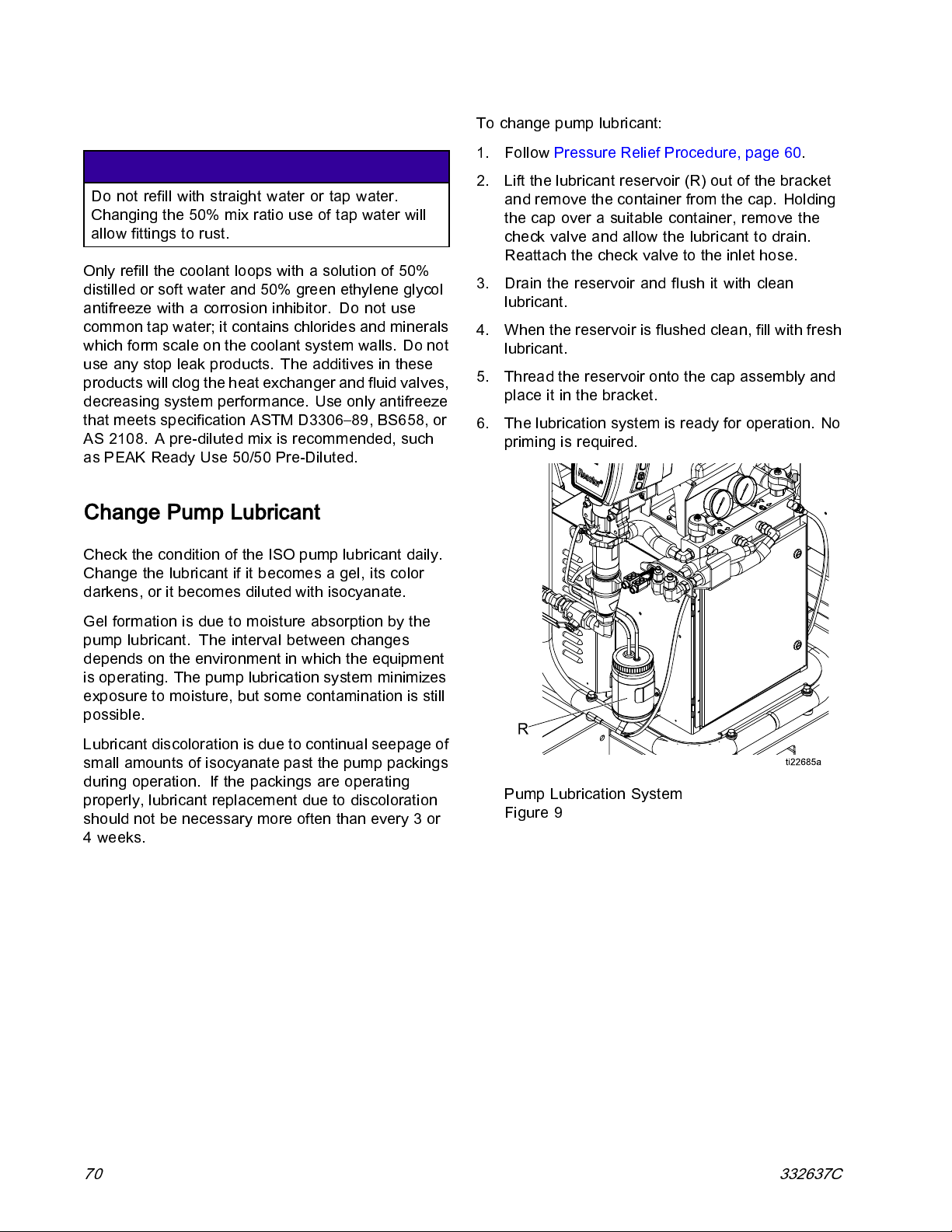
Repair
Coolant Specifications
NOTICE
Do not refill with straight water or tap water.
Changing the 50% mix rat io use of tap water will
allow fittings to rust.
Only refill the coolant loops with a solution of 50%
distilled or soft water and 50% green ethylene g lycol
antifreeze with a corrosion inhibitor. Do not use
common tap water; it contains chlorides and minerals
which form scale on the coolant system walls. Do not
use any stop leak products. The additives in these
products will cl og the heat exc han ger and fluid valv es ,
decreasing system performance. Use only antifreeze
that meets specification ASTM D3306–89, BS658, or
AS 2108. A pre-diluted mix is recommended, such
as PEAK Ready Use 50/50 Pre-Diluted.
Change Pump Lubricant
Check the condition of the ISO pump lubricant daily.
Change the lubricant if it becomes a gel, its color
darkens, or it becomes diluted with isocyanate.
To change pump lubricant:
1. Follow Pressure Relief Procedure, page 60.
2. Lift the lubricant reservoir (R) out of the bracket
and remove th e container from the cap . Holding
the cap over a suitable c ont ain er, remove the
check valve and allow the lubricant to drain.
Reattach the check valve to the inlet hose .
3. Drain the reservoir and flush it with clean
lubricant.
4. When the reservoir is flushed clean, fill with fresh
lubricant.
5. Thread the reserv oir onto the cap asse mbl y and
placeitinthebracket.
6. The lubrication system is ready for operation. No
priming is required.
Gel forma tio n is due to moisture abs orpti on by the
pump lubricant. The interval between changes
depends on th e environment in which th e equipment
is operating. The p ump lubrication system mi ni miz es
exposure to moisture, but some contamination is still
possible.
Lubricant discoloration is due to continual seepage of
small amounts of isocyanate past the pump packings
during operation. If the packings are operating
properly, lubricant replacement due to discoloration
should not be necessary more often than every 3 or
4weeks.
Pump Lubrication System
Figure 9
70 332637C
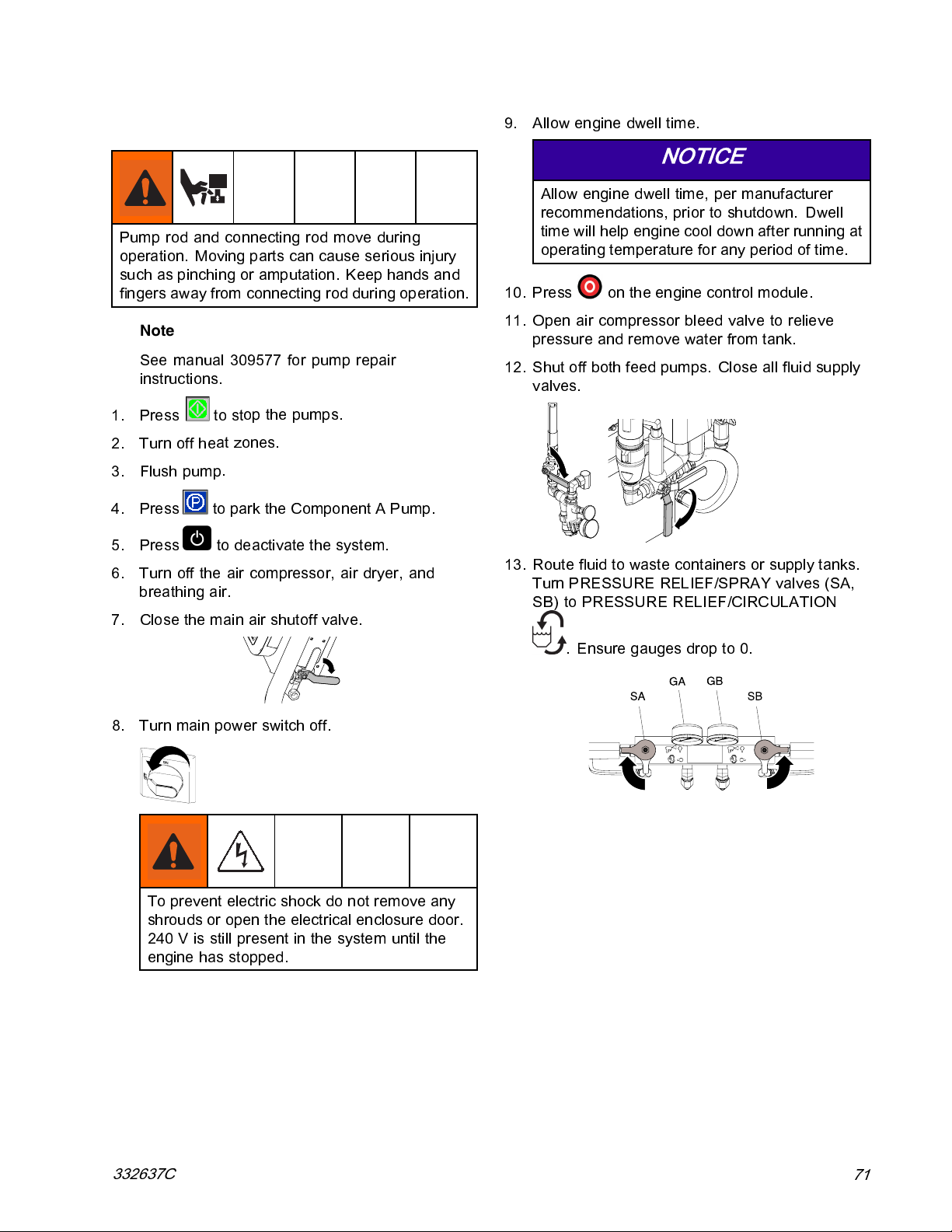
Repair
Remove Pump
Pump rod and connecting rod move during
operation. Moving parts can cause serious injury
such as pinching or amputation. Keep hands and
fingers away from connecting rod during operation.
Note
See manual 309577 for pump repair
instructions.
1. Press
2. Turn off he
3. Flush pump
4. Press
5. Press
6. Turn off the air compressor, air dryer, and
breathing air.
7. Close the main air shutoff valve.
op the pumps.
to st
at zones.
.
to park the Component A Pump.
to deactivate the system.
9. Allow engine dwell time.
NOTICE
Allow engine dwell time, per manufacturer
recommendations, prior to shutdown. Dwell
time will help engine cool down after running at
operating temperature for any period of time.
10. Press on the engine control module.
11. Open air compressor bleed valve to relieve
pressure and remove water from tank.
12. Shut off both feed pump s. Close all flui d supply
valves.
13. Route fluid to waste containers or supply tanks.
Turn PRESSURE RELIEF/SPRAY valves (SA,
SB) to PRESSURE RELIEF/CIRCULATION
8. Turn main power switch off.
To prevent electric shock do not remove any
shrouds or open the electrical encl os ure door.
240 V is still present in the system until the
engine has stopped.
. Ensure gauges drop to 0.
332637C
71
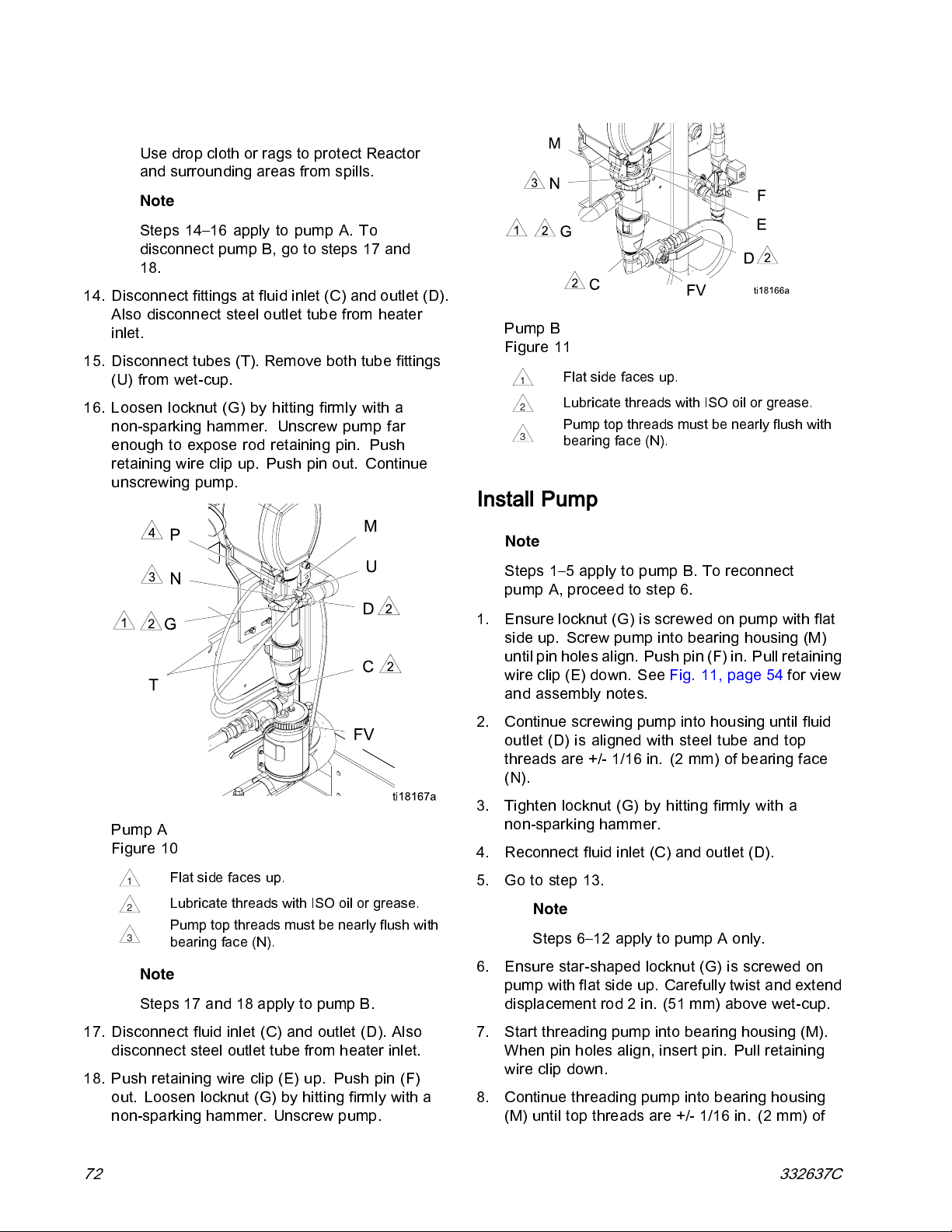
Repair
Note
Use drop cloth or rags to protect Reactor
and surrounding areas from spills.
Note
Steps 14–16 apply to pump A. To
disconnect pump B, go to steps 17 and
18.
14. Disconnect fittings at fluid inlet (C) and outlet (D).
Also disconnect s te el outlet tube from heater
inlet.
15. Disconnect tubes (T). Remove both tube fittings
(U) from wet-cup.
16. Loosen lockn ut (G) by hitting firmly w ith a
non-sparking hammer. Uns crew pump far
enough to expose rod retaining pin. Push
retaining wire clip up. Push pin out. Continue
unscrewing pump.
Pump B
Figure 11
Flat side faces up.
1
Lubricate threads with ISO oil or grease.
2
Pump top threads must be nearly flush with
3
bearing face (N).
Install Pump
Pump A
Figure 10
Flat side faces up.
1
Lubricate threads with ISO oil or grease.
2
Pump top threads must be nearly flush with
3
bearing face (N).
Note
Steps 17 and 18 apply to pump B.
Note
Steps 1–5 apply to pump B. To reconnect
pump A, proceed to step 6.
1. Ensure locknut (G) is screwed on pump with flat
side up. Screw pump into bearing housing (M)
until pin holes align. Push pin (F) in. Pull retaining
wire clip (E) down. See Fig. 11, page 54 for view
and assembly notes.
2. Continue screwing pump into housing until fluid
outlet (D) is aligned with steel tube and top
threads are +/- 1/16 in. (2 mm) of bearing face
(N).
3. Tighten locknut (G) by hitting firmly with a
non-sparking hammer.
4. Reconnect fluid inlet (C) and outlet (D).
5. Go to step 13.
Note
Steps 6–12 apply to pump A only.
6. Ensure s tar-sh ape d locknut (G) is screwed on
pump with flat side up. Carefully twist and extend
displacement rod 2 in. (51 mm) above wet-cup.
17. Disconnect fluid inlet (C) and ou tlet (D). Also
disconnect s tee l outlet tube from heater inl et.
18.Pushretainingwireclip(E)up. Pushpin(F)
out. Loosen locknut (G) by hitting firmly with a
non-sparking h amm er. Unscrew pump.
72
7. Start threading pump into bearing housing (M).
When pin holes align, insert pin. Pull retaining
wire clip down.
8. Continue th readi ng pump into bearing housing
(M) until top threads are +/- 1/16 in. (2 mm) of
332637C
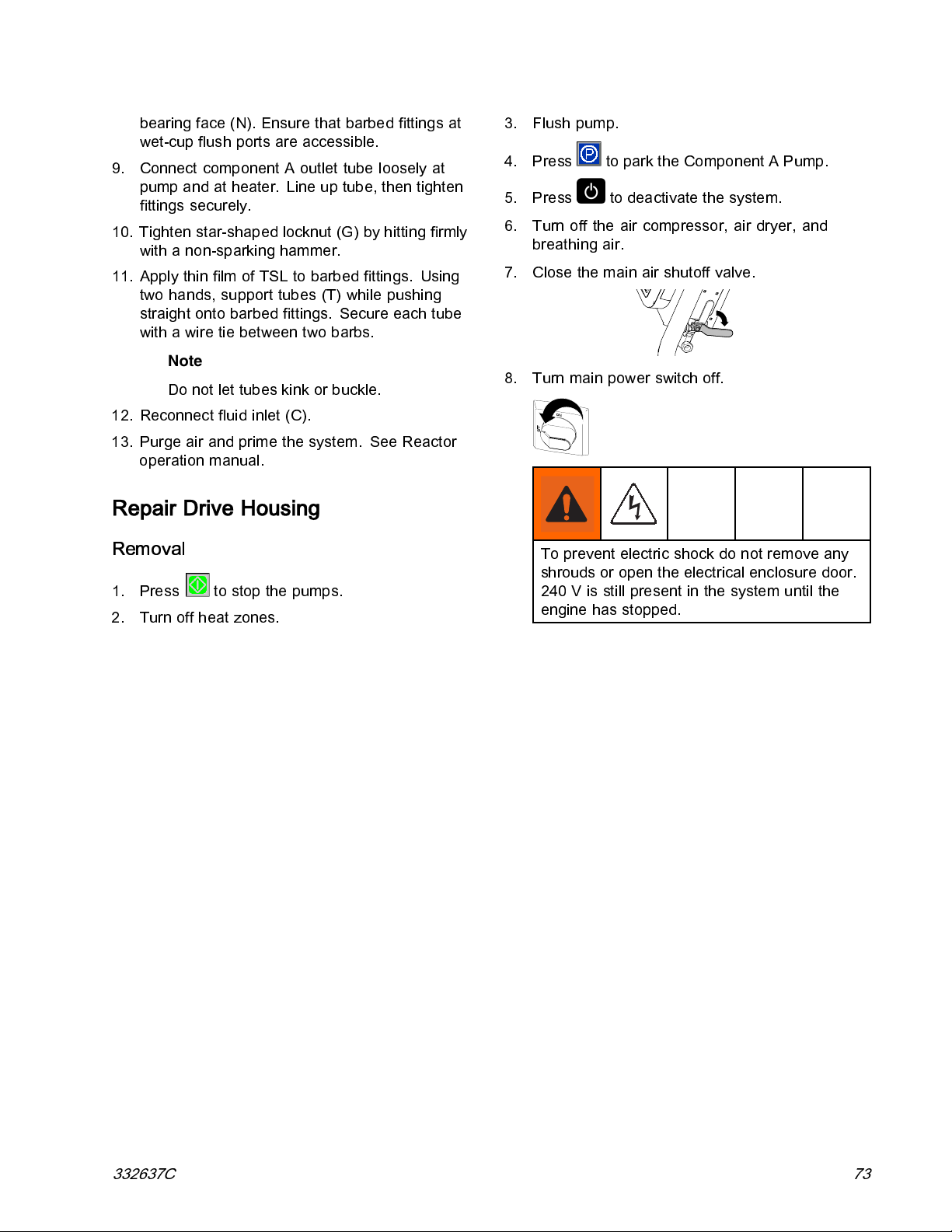
Repair
bearing face (N). Ensure that barbed fittings at
wet-cup flush ports are accessible.
9. Connect component A outlet tube lo osely at
pump and at heater. Line up tube, then tighten
fittings securely.
10. Tighten star-shaped locknut (G) by hitting firmly
with a non-sparking hammer.
11. Apply thin film of TSL to barbed fittings. Using
two hands, s upp ort tubes (T) while pushing
straight onto barbed fittings. Secure each tube
withawiretiebetweentwobarbs.
Note
Do not let tubes kink or buckle.
12. Reconnect fluid inlet (C).
13. Purge air and prime the system. See Reac tor
operation manual.
Repair Drive Housing
Removal
1. Press to stop the pumps.
2. Turn off heat zones.
3. Flush pump.
4. Press
5. Press
6. Turn off the air compressor, air dryer, and
breathing air.
7. Close the main air shutoff valve.
8. Turn main power switch off.
To prevent electric shock do not remove any
shrouds or open the electrical enclosure door.
240 V is still present in the system until th e
engine has stopped.
to park the Component A Pump.
to deactivate the system.
332637C 73

Repair
9. Allow engine dwell time.
NOTICE
Allow engine dwell time, per manufacturer
recommendations, prior to shutdown. Dwell
time will help engine cool down afte r running at
operating temperature for any period of time.
10. Press on the engine control module.
11. Open air compressor bleed valve to relieve
pressure and remove water from tank.
12. Perform Pressure Relief Procedure, page 60.
13. Remove screws (294) and motor shield (293),
see Fig. 12.
Note
Examine bearing housing (303) and
connecting rod (305). If these pa rts nee d
replacing, first remove the pump (315),
see Remove Pump, page 71.
Figure 12
14. Remove cover (74) and screws (75).
15. Remove cycle switch (321) from A side drive
housing. Remov e screws (322) and cycle switch
(321).
16. Disconnect pump inlet and outlet lines. Remove
screws (313), washers (314), and beari ng
housing (303).
NOTICE
Do not drop gear cluster (304) when removing
drive housing (302). Gear cluster may stay
engaged in motor front end bell (R) or drive
housing.
17. Remove screws (312) and pull drive housing
(302)offmotor(301).
Note
The A side drive housing includes
cycle counter switch (321). Switch wire
connects to port #12 on the MCM.
Figure 13
Installation
1. Apply grease liberally to washers (307, 308,
318), all gears, and inside drive housing (302).
2. Install one bronze washer (308) in drive housing,
then install steel washers (307, 318) as shown.
3. Install second bronze washer (308) on gear
cluster (304) and insert gear cluster in drive
housing.
74
Note
Drive housing crankshaft must be in line
with crankshaft at other end of motor.
See Fig. 13, page 56.
332637C

Repair
4. Push drive housing (302) onto motor (301).
Install screws (312).
Note
If bearing housing (303), connecting rod
(305), or pump (315, 306) were removed,
reassemblerodinhousingandinstall
pump, see Install Pump, page 72 .
5. Install cycle counter switch (3210) and screws
(322).
6. Install bearing housing (303), screws (313), and
washers (314). Pumps must be in phase (both at
same position in stroke).
7. Install cover (74) and screws (75).
8. Install motor shield (293) and screws (294).
ure 14
Fig
332637C 75

Repair
Repair Electric Motor
Removal
NOTICE
Be careful not to drop or damage the motor. The
motor is heavy and may require two people to lift.
1. Remove drive housing and pump assemblies.
See Repair Drive Housing, page 73.
2. Disconnect electric motor (301) power cable from
port#15ontheMCM.
3. Remove screws (294) and motor shield (293).
Rest motor shroud assembly behind the motor
without strain ing the fan power ca bl e.
Installation
1. Place motor on unit. Thread motor
cables into conduit as before. See
Electrical Schematics, page 154.
4. Disconnect over temperature cable from port
#2 on MCM. Cut tie wraps around harness to
remove cable.
5. Remove four screws (268) holding motor (301) to
bracket. Lift motor off unit.
2. Fasten motor (301) with screws (268) until
screws are fully threaded in mounting bracket.
Do not tighten screws until drive housing and
pumpsareconnectedtothemotor.
Note
If necessary, loosen screws (268) to
align the motor (301) wi th side brackets.
3. Install driv e housing and pump assemblies, se e
Installation, page 74.
4. Route motor (301) power cable from motor
through top port into Reactor cart, through back
port out of the Reactor, through cord grip (518),
and into the electrical enclosure. Connect to port
#15onMCM.Usetiewrapstosecurepower
cable to other cables on pallet.
5. Install drive housing covers and motor cover.
6. Return to service.
76 332637C

Repair
Repair Circuit Breaker Module
1. See Before Beginning Repair, page 65.
2. Using an ohmmeter, check for continuity across
circuit breaker (left to right). If no continuity, trip
breaker, reset, and retest. If still no continuity,
replace breaker as follows:
a. Refer to Electrical Schematics, page 154,
and tables on next page.
PS1
b. Follow Shutdown instructions. See
Shutdown, page 61.
c. Refer to circuit breaker identification table
and electrical diagrams in Reactor repair
manual.
d. Loosen four screws connecting wires and bus
bar to circuit breaker that will be replaced.
Disconnect wires.
e. Pull locking tab out 1/4 in. (6mm) and pull
circuit breaker away from the din rail. Install
new circuit breaker. Insert wires a nd tighten
down all screws.
1
A
5
A
5
1
A
5
1
A
30
A
0
2
A2
40
A
0
A
5
1
0
B
C
2
0
B
C
03
B
C
4
0
B
C
B11T
T
2
1
B
05
B
C
6
0
B
C
7
0
B
C
08
B
C
Circuit Breakers
Figure 15
Ref. Size Component
CB01
5A
Power Supply, Fan,
Coolant Pump
CB02
CB03
15 A Boost Heat A
15 A Boost Heat B
332637C
Ref. Size Component
CB04
30 A Hose Heat
CB05 20 A Motor Control
CB06*
CB07*
CB08* 1
40 A
20 A
5A
Air Compressor/Open
Open
Air Dryer/Open
77

Repair
Circuit Breakers Inside Cabinet
Figure 16
Ref. Size Component
Circuit Breakers Inside Alternator Assembly
Figure 17
Ref. Size Component
CB10
90 A 120/240V Alternator
CB20
50 A Heated Hose
78 332637C

Replace Load Center Relays and
Fuses
1. Disconnect the negative lug from the negative
post of the battery. See ReplaceBattery, page97.
2. Remove the bad relay or fuse from the load
center (242) and install a new relay or fuse. See
Fig. 18.
3. Connect battery cable. See
Replace Battery, page 97.
Repair
Relay and Fuse Identification Table
See Load Center Wiring Diagram, page 163.
Repair
Kit
24L958
24L959
Ref
K1
K2
K3
K4
F3 FAN-ATO - 30A
F4 PWR-ATO - 20A
Component
Fuel Relay
Starter Relay
Glow Plug Relay
Fan Relay
Fuse for load center
relay K4 and radiator
fan.
Fuse for load center
relays K1, K2, K3
and their related
components; Engine
Control Module
power; and coolant
valve control.
Load Center Relay and Fuse Identification
Figure 18
332637C 79

Repair
Replace Load Center
NOTICE
Before handling board, put on a static conductive
wrist strap to protect against st atic discharge which
can damage board. Follow instructions provided
with wrist strap.
1. Perform Shutdown, page 61.
2. Disconnect the negative lug from the negative
post of the battery. See Replace Battery, page 9 7
3. Disconnect all connectors. See
Load Center Wiring Diagram, page 163.
4. Remove four nuts (248), and load center (240).
5. Install new load center (240) and
reconnect all connectors. See
Load Center Wiring Diagram, page 163.
Replace Engine Solenoid Relays
1. Perform Shutdown, page 61.
2. Disconnect the negative lug from the negative
post of the battery. See Replace Battery, page 97.
3. Remove two bolts (570) and solenoid relay (569).
The starte r solenoid relay (CR6) i s above th e
glow plug solenoid relay (CR7).
4. Disconnect cables from the old relay
andconnecttothenewrelay. See
Load Center Wiring Diagram, page 163.
6. Connect battery cable. See
Replace Battery, page 97.
Starter (top) and Glow Plug (bottom) Solenoid Relays
Figure 19
80 332637C
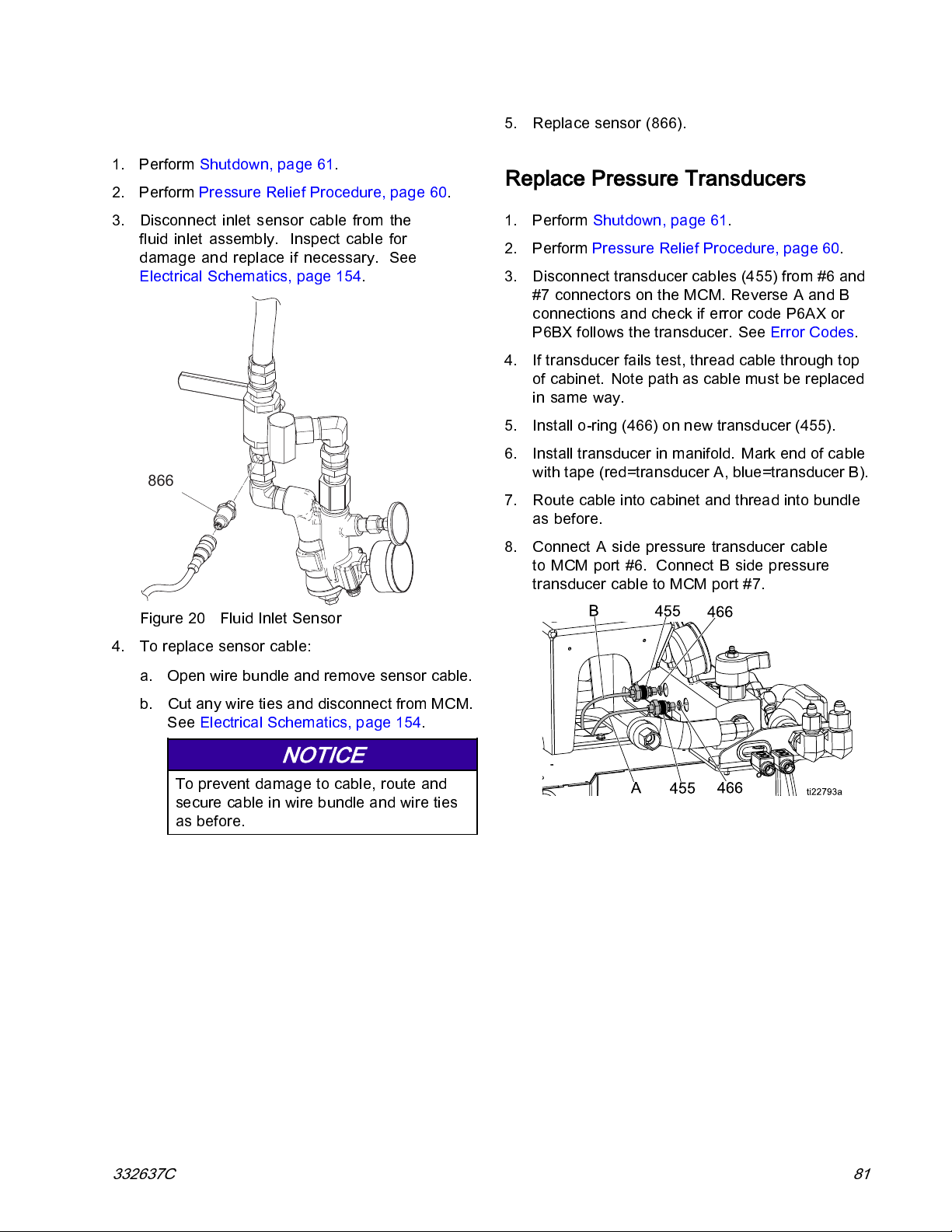
Repair
Replace Fluid Inlet Sensor
1. Perform Shutdo wn, page 61.
2. Perform Pressure Relief Procedure, page 60.
3. Disconnect inl et sensor cable from the
fluid inlet assembly. Inspect cable for
damage and replace if necessary. See
Electrical Schematics, page 154.
5. Replace sensor (866).
Replace Pressure Transducers
1. Perform Shutdown, page 61.
2. Perform Pressure Relief Procedure, page 60.
3. Disconnect transducer cables (455) from #6 and
#7 connectors on the MCM. Reverse A and B
connections and chec k if error code P6A X or
P6BX follows the transducer. See Error Codes.
4. If transducer fails test, thread cable through to p
of cabinet. Note path as cable must be replaced
in same way.
5. Install o-ring (466) on new transducer (455).
6. Install transducer in manifold. Mark end of cable
with tape (red=transducer A, blue=transducer B).
7. Route cable into cabinet and thread into bundle
as before.
8. Connect A side pressure transducer cable
to MCM port #6. Connect B side pressure
transducer cable to MCM port #7.
Figure 20 Fluid Inlet Sensor
4. To replace sensor cable:
a. Open wire bundle and remove sensor cable.
b. Cut any wire ties and disconnect from MCM.
See Electrical Schematics, page 154.
NOTICE
To prevent damage to cable, route and
securecableinwirebundleandwireties
as before.
332637C 81
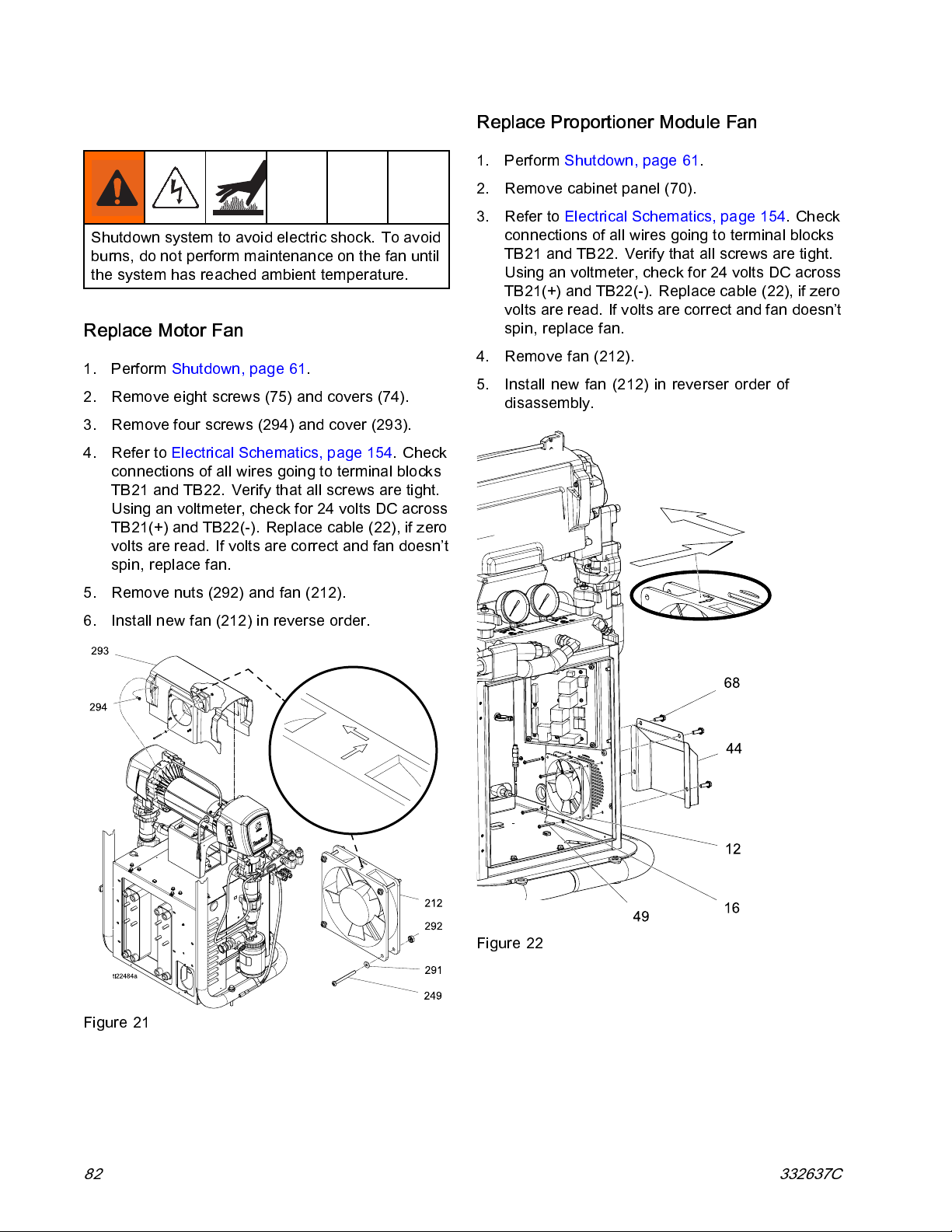
Repair
Replace Fans
Shutdown system to avoid electric shock. To avoid
burns, do not perform maintenance on the fan until
the system has reached ambient temperature.
Replace Motor Fan
1. Perform Shutdown, page 61.
2. Remove eight screws (75) and covers (74).
3. Remove four screws (294) and cover (293).
4. Refer to Electrical Schematics, page 154.Check
connections of all wires going to terminal blocks
TB21 and TB22. Verify that all screws are tight.
Using an voltmeter, check for 24 volts DC across
TB21(+) and TB22(-). Replace cable (22), if zero
volts are read. If volts are correct and fan doe sn’t
spin, replace fan.
Replace Proportioner Module Fan
1. Perform Shutdown, page 61.
2. Remove cabinet panel (70).
3. Refer to Electrical Schematics, page 154.Check
connections of all wires going to terminal blocks
TB21 and TB 22. Verify that al l screws are tight.
Using an voltmeter, check for 24 volts DC across
TB21(+) and TB22(-). Replace cable (22), if zero
volts are read. If volts are correct and fan doesn’t
spin, replace fan.
4. Remove fan (212).
5. Install new fan (212) in reverser order of
disassembly.
5. Remove nuts (292) and fan (212).
6. Install new fan (212) in reverse order.
Figure 21
Figure 22
82 332637C

Repair
Replace Radiator Fan
1. Perform Shutdo wn, page 61.
2. Remove four screws (605) and disconnect power
cable (PC).
3. Install new fan (605) to radiator bracket (601)
with screws (605).
Replace Electrical Enclosure Fan
1. Perform Shutdown, page 61.
2. Open electrical enclosure door (502). Loosen
four nuts (558) and remove fan (561).
3. Refer to Electrical Schematics, page 154.Check
connections of all wires going to terminal blocks
TB13, TB14, and power supply P S1 . Verify that
all screws are tight. Using an voltmeter, chec k
for 24 volts DC across TB13(+) and TB14(-).
Replace power supply PS1 (515), if zero volts
are read. If volts are correct and fan doesn’t spin,
replace fan.
4. Install new fan (561) in reverse order of
disassembly so that the fan blows out o f the
electrical enclosure.
Figure 23
Figure 24
332637C 83
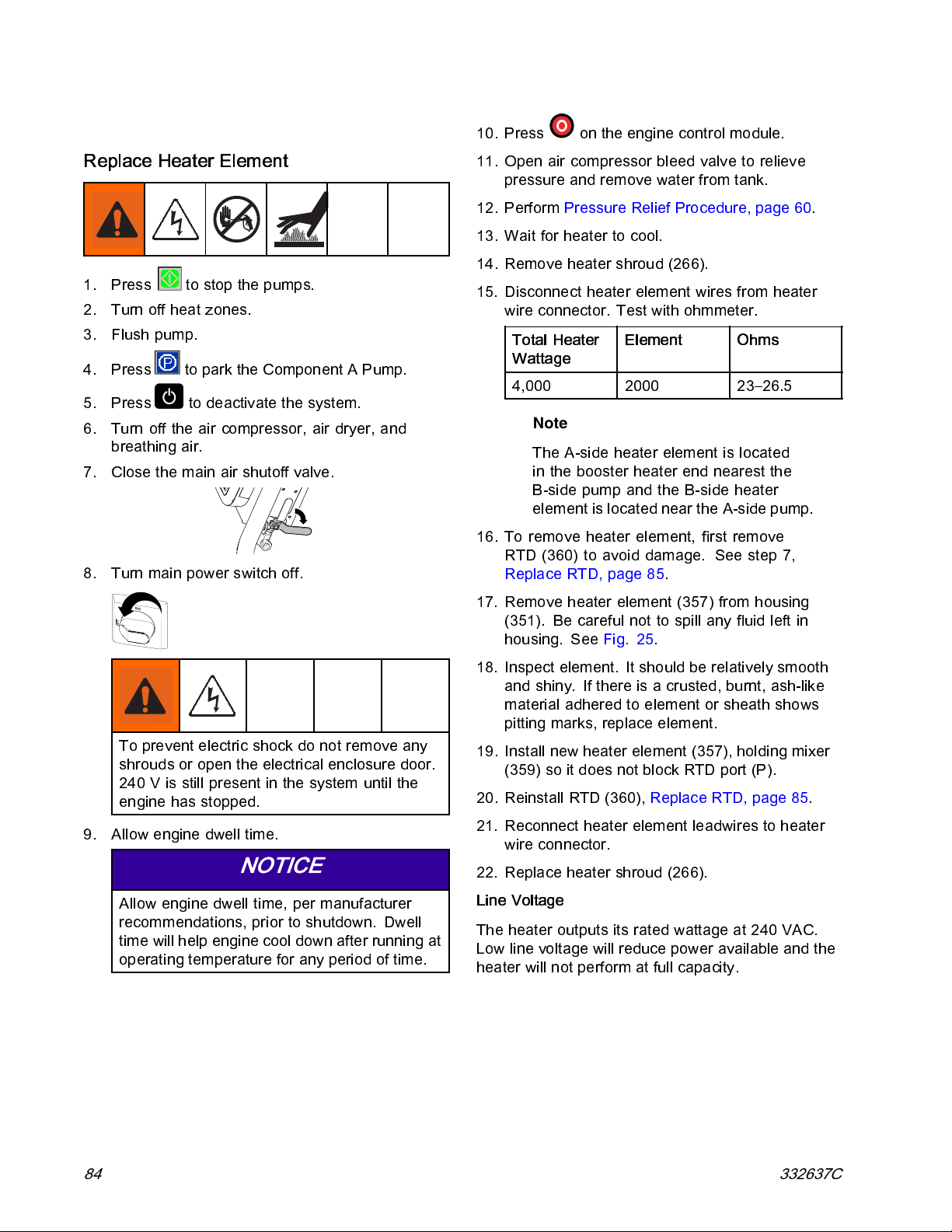
Repair
Repair Booster Heater
Replace Heater Element
1. Press to stop the pumps.
2. Turn off heat zones.
3. Flush pump.
4. Press
5. Press
6. Turn off the air compressor, air dryer, and
breathing air.
7. Close the main air shut off valve.
8. Turn main power switch off.
to park the Component A Pump.
to deactivate the system.
10. Press on the engine control module.
11. Open air compressor bleed valve to relieve
pressure and remove water from tank.
12. Perform Pressure Relief Procedure, page 60.
13. Wait for heater to cool.
14. Remove heater shroud (266).
15. Disconnect heater element wires from heater
wire connector. Test with ohmmeter.
Total Heater
Wattage
4,000 2000 23–26.5
Note
The A-side heater element is located
in the booster heater end nearest the
B-sidepumpandtheB-sideheater
element is located near the A-side pump.
16. To remove heater element, first remove
RTD (360) to avoid damage. See step 7,
ReplaceRTD,page85.
Element Ohms
To prevent electric shock do not remove any
shrouds or open the electrical enclosure door.
240 V is stil l present i n the sys tem until th e
engine h as stopped.
9. Allow engine dwell time.
NOTICE
Allow engine dwell time, per manufacturer
recommendations, prior to shutdown. Dwell
time will help engine cool down afte r running at
operating temperature for any period of time.
17. Remove heater element (357) from housing
(351). Be careful not to spill any fluid left in
housing. See Fig. 25.
18. Inspect element. It should be relatively smooth
and shiny. If there is a crusted, burnt, ash-like
material adhered to element or sheath shows
pitting marks, replace element.
19. Install new heater element (357), holding mixer
(359) so it does not block RTD port (P).
20. Reinstall RTD (360), Replace RTD, page 85.
21. Reconnect heater element leadwires to heater
wire connector.
22. Replace heater shroud (266).
Line Voltage
The heater outputs its rated wattage at 240 VAC.
Low line voltage will reduce power available and the
heater will not perform at ful l capacity.
84 332637C

Repair Overtemperature Switch
1. Perform Shutdo wn, page 61.
2. Wait for booster heater to cool.
3. Remove heater shroud.
4. Verify blue wire and brown/black wires
from cable (54) ”HTR-OT” are connec ted
to overtemperature switch (358). See
Electrical Schematics, page 154.
5. Disconnect overtemperature switch (358) from
cable (54). Test across quick connect terminals
with an ohmmeter.
Repair
a. If the resistance
the overtemperature switch needs to be
replaced. Go to step 6.
b. If the resistanceisapproximately 0 ohms,
test the cable to ensure it is not cut or open.
Reconnect the overtemperature switch
and cable. Disconnect the cable from the
overtemperature port on the TCM. Test
from pin 1 to pin 3 and pin 1 o pin 4 on
cable (54) “HTR-OT”. Resistance should be
approximately 0 ohms.
Note
The cable may have failed if one or b oth
of the readings is above approximately 0
ohms. If the read ings is approximately
0 ohms, then there may have been a
bad connector/connection causing the
problem.
6. If switch fails test, remove screws. Discard failed
switch. Apply a thin layer of thermal compound
110009, install new switch in same location on
housing (351), and secure with screws (361).
Reconnect cables.
is not
approximately 0 ohms,
Replace RTD
1. Perform Shutdown, page 61.
2. Wait for heater to cool.
3. Remove heater shroud (266) and heater guards
(299, 300).
4. B Side RTD:
a. Follow “HT- RTD-B" RTD cable (360) and
open split loom about 18 in. (457.2 mm) away
from the heater attachment. Disconnect “HT-
RTD-B TCM" and “HT-RTD-B” connectors.
See Electrical Schematics, page 154.
b. Visually inspect “HT-RTD-B” connector and
replace extension cable (58) if necessary.
Continue to next step if the extension cable
connector is not damaged.
c. Visually inspect “TCM-A HT-RTD-B”
connection to TCM. Continue to next step to
replace RTD (360).
5. A side RTD:
a. Follow “HT- RTD-A" RTD cable (360) and
open split loom about 18 in. (457.2 mm) away
from the heater attachment. Disconnect “HT-
RTD-A TCM" and “HT-RTD-A” connectors.
See Electrical Schematics, page 154.
b. Visually inspect “HT-RTD-A” connector and
replace extension cable (58) if necessary.
Continue to next step if the extension cable
connector is not damaged.
c. Visually inspect “TCM-A HT-RTD-A”
connection to TCM. Continue to next step to
replace RTD (360).
332637C 85
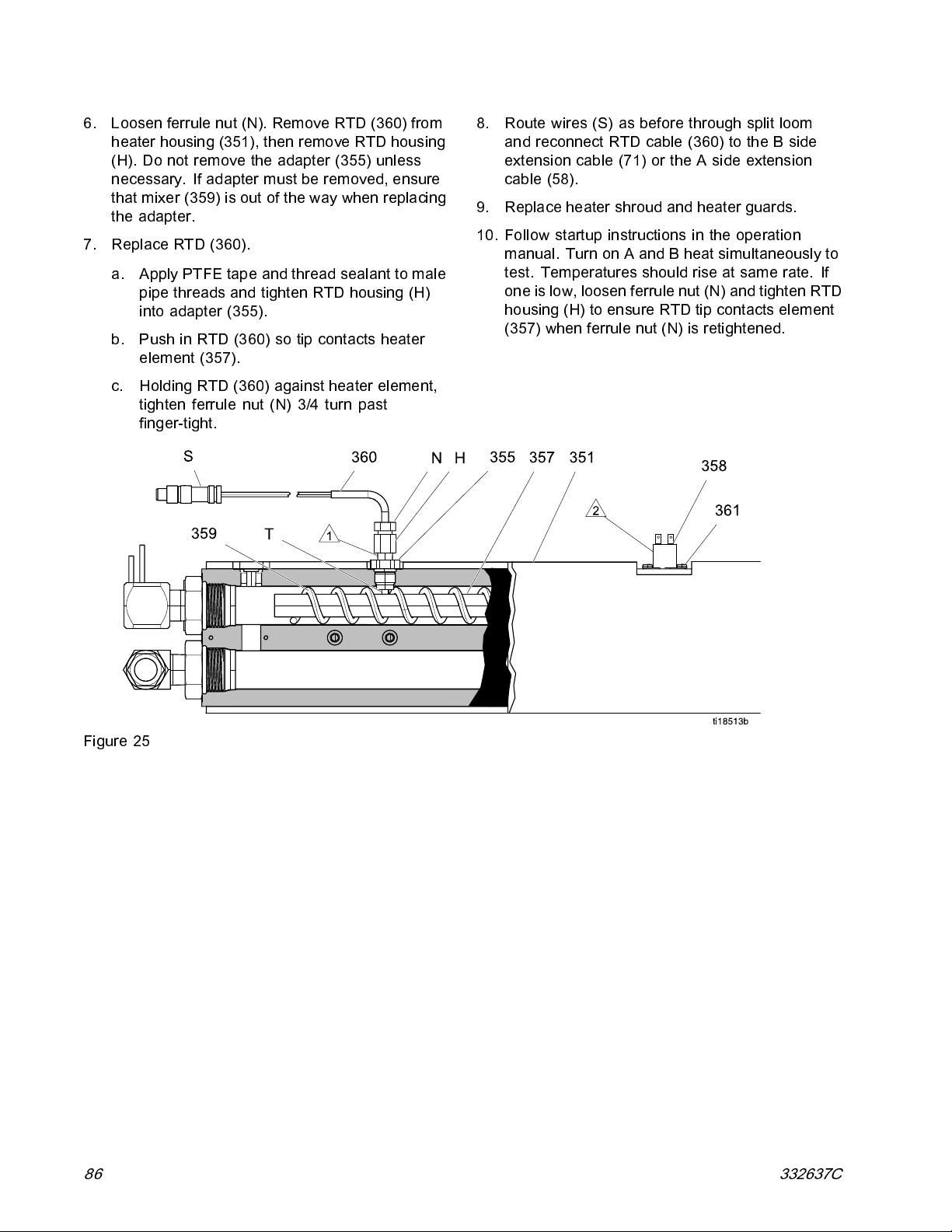
Repair
6. Loosen ferrule nut (N). Remove RTD (360) from
heater housing (351), then remove RTD housin g
(H). Do not remov e the ada pte r (355) unles s
necessary. If adapter must be removed, ensure
that mixer (359) is out of the way when replacing
the adapter.
7. Replace RTD (360).
a. Apply PTFE tap e and thread sealant to mal e
pipe threads and tighten RTD housing (H)
into adapter (355).
b. Push in RTD (360) so tip contacts heater
element (357).
c. Holding RTD (360) against heater element,
tighten ferrule nut (N) 3/4 turn past
finger-tight.
8. Route wires (S) as before through split loom
and reconnect RTD cable (360) to the B side
extension cable (71) or th e A s id e extension
cable (58).
9. Replace heater shroud and heater guards.
10. Follow startup instructions in the operation
manual. Turn on A and B heat simultaneously to
test. Temperatures should rise at same rate. If
one is low, loosen ferrule nut (N) and tighten RTD
housing (H) to ensure RTD tip contacts element
(357) when ferrule nut (N) is retightened.
Figure 25
86 332637C

Repair
Repair Heated Hose
Refer to the heated hose manual 309572 for hose
replacement parts.
Check Hose Heat Connectors
1. Perform Shutdo wn, page 61.
Note
Whip hose must be connected.
2. Disconnect hose connector (V) at Reactor, see
Fig. 26.
3. Using an ohmmeter, check bet ween the
connectors (V). Th ere should be continuity .
4. If hose fails test, retest at each length of hose,
including whip hose, until failure is isolated.
Check RTD Cables and FTS
1. Perform Shutdo wn, page 61.
2. Disconnect RTD cable (C) at Reactor.
3. Test with an ohmmeter between pins of cable
connector C.
Note
5. If the FTS is not reading properly at the end of
the hose, connect FTS directly to RTD cable (C)
at the manifold.
6. If the FTS reads properly at the manifold but
not at the end of the hose, check cable (C)
connections. Verify they are tight.
Heated Hose
Figure 26
Do not touch outer ring with test probe.
Pins Result
3 to 1 approximately 1090
ohms
3 to 4 approximately 1090
ohms
1to4 0.2-0.4ohms
2toany
4. Retest at each length of hose, including whip
hose, until failure is located.
infinity (open)
Note
To assist in taking readings, order RTD
Test Kit 24N365. Kit includes two cables:
one cable with a compatible female M8
connector and an oth er c abl e w ith a male
M8 connector. Both cables have stripped
wire at the other end for easy test probe
access.
Pins / Wire Color
3 to 1 / brown to blue approximately 1090
3 to 4 / blue to black approximately 1090
1 to 4 / brown to bla ck 0.2 - 0.4 ohms
2 to any / N/A infinity (open)
Result
ohms
ohms
332637C 87

Repair
Repair Fluid Temperature Sensor
(FTS)
Installation
The Fluid Temperature Sen so r (FTS) is s up pli ed with
the system. Instal l FTS between main hose and
whip hose. See Heated Hose manual 309572 for
instructions.
Figure 27
Test/Removal
1. Perform Shutdown, page 61.
2. Remove tape and protective covering from FTS.
Disconnect hose cable (F).
3. If FTS is not reading properly at the end of the
hose, see Check RTD Cables and FTS, page 87.
4. If FTS fails, replace FTS.
a. Disconnect air hoses (C,L) and electrical
connectors (D).
b. Disconnect FTS from whip hose (W) and
fluid h os es (A, B).
c. Remove ground wire (K) from ground screw
on underside of FTS.
d. Remove FTS probe (H) from component A
(ISO) side of hose.
88 332637C
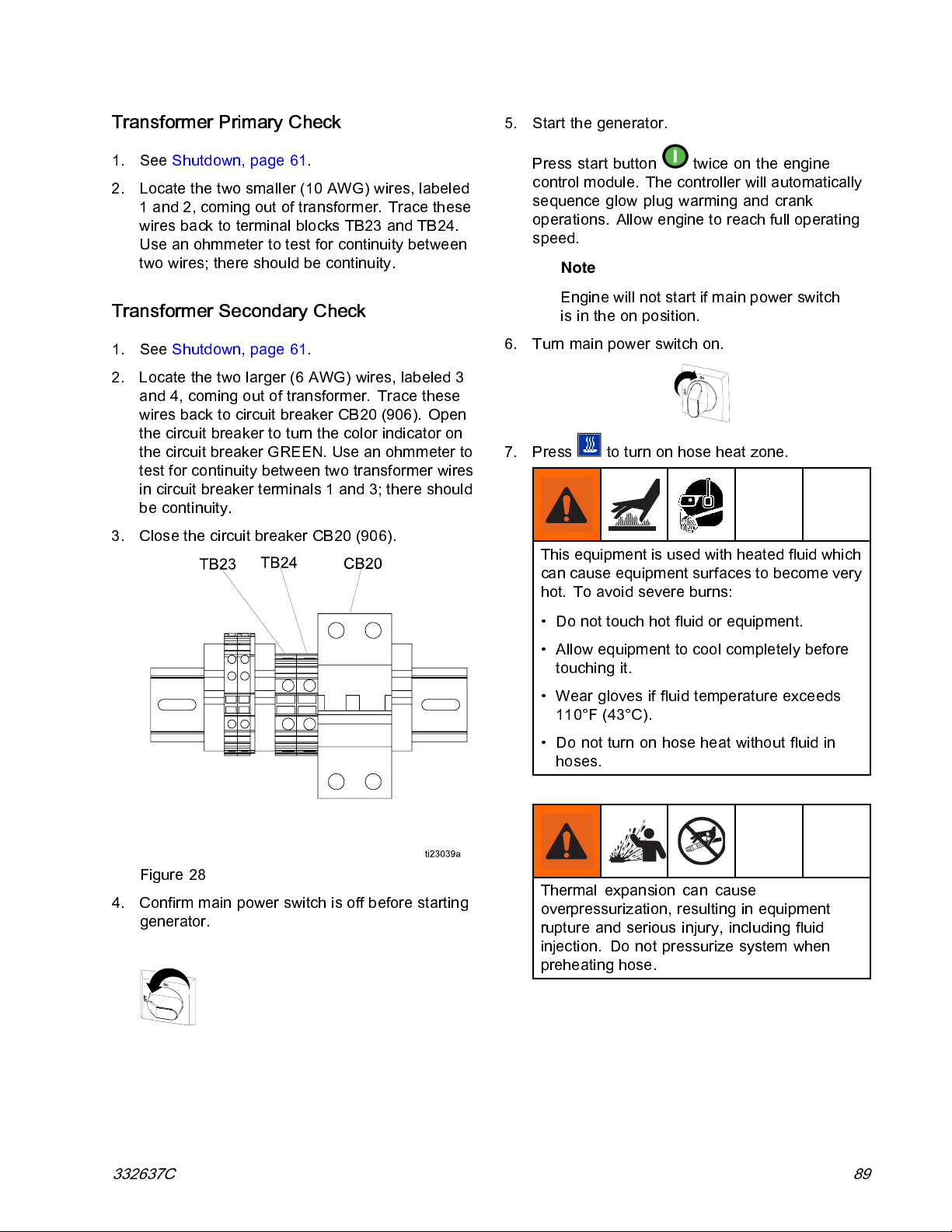
Repair
Transformer Primary Check
1. See Shutdown, page 61.
2. Locate the two smaller (10 AWG) wires, labeled
1 and 2, c omi ng out of transformer. Trace these
wires back to terminal blocks TB23 and TB24.
Use an ohmmeter to test for continuity between
two wires; there should be continuity.
Transformer Secondary Check
1. See Shutdown, page 61.
2. Locate the two larger (6 A WG ) wires, labeled 3
and 4, coming out of transformer. Trace these
wires back to circuit breaker CB20 (906). Open
the circuit breaker to turn the color indicator on
the circuit breaker GREEN. Use an ohmmeter to
test for continuity between two transformer wires
in circuit breaker terminals 1 and 3; there should
be continuity.
3. Close the circuit breaker CB20 (906).
5. Start the generator.
Press start button
control module. The controller will automatically
sequence glow plug warming and crank
operations. Allow engine to reach full operating
speed.
Note
Engine will not start if main power switch
is in the on position.
6. Turn main power switch on.
7. Press to turn on hose heat zone.
Thisequipmentisusedwithheatedfluidwhich
can cause equipment surfaces to become very
hot. To avoid severe burns:
twiceontheengine
Figure 28
4. Confirm main power switch is off before starting
generator.
• Do not touch hot fluid or equipment.
• Allow equipment to cool completely before
touching it.
• Wear gloves if fluid temperature exceeds
110°F (43°C).
• Do not turn on hose heat without fluid in
hoses.
Thermal expansion can cause
overpressurization, resulting in equipment
rupture and serious injury, including fluid
injection. Do not pressurize system when
preheating hose.
332637C 89

Repair
8. To verify voltage on the secondary leads of the
transformer, measure between the terminals 2
and 4 on CB20. This will verify the circuit breaker
is working properly.
Model
310 ft 90 Vac*
210 ft 62 Vac*
* For 240 Vac line voltage.
9. See the Diagnostic Run Screen on the ADM. The
Diagnostic Run Screen displays the incoming
(240 Vac) to the TCM “Hose Voltage” and the
hose current. The diagnostic screen will show
if th e circuit breaker has been trippe d for the
incoming power to the TCM.
Secondary Voltage
Replace Transformer
1. Perform Shutdown, page 61.
2. Open Reactor cabinet.
3. Remove bolts holding transformer (226) to
cabinet floor.
4. Disconnect the transformer wires. See
Reactor Cabinet Wiring Diagram, page 162.
5. Remove transformer (226) from cabinet.
6. Install new transformer (226) in reverse order.
226
90 332637C
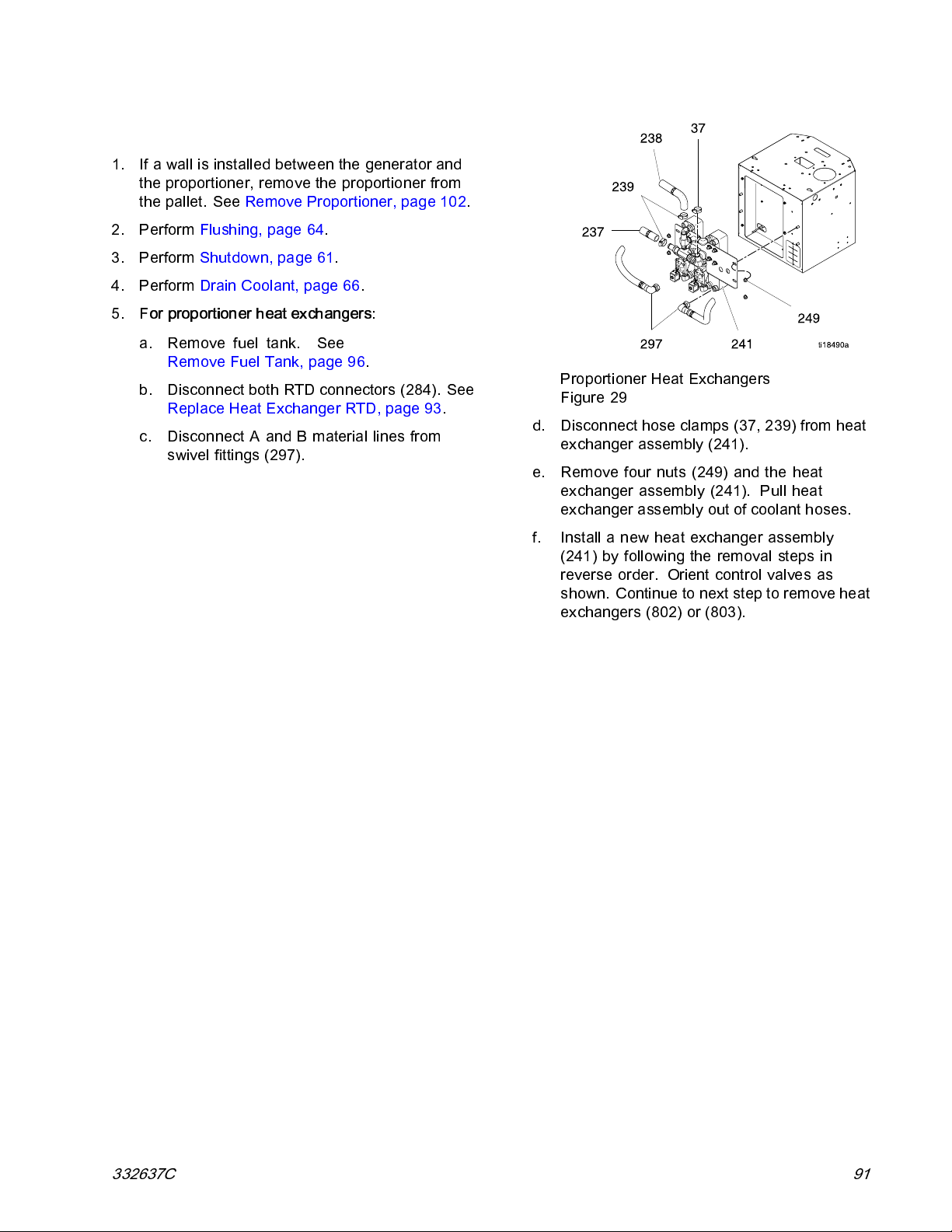
Replace Heat Exchangers
1. If a wall is installed between the generator and
the proportioner, remove the proportioner from
the pallet. See Remove Proportioner, page 102.
2. Perform Flush ing , page 64.
3. Perform Shutdo wn, page 61.
4. Perform Drain Coolant, page 66.
5.
For proportioner heat exchangers:
a. Remove fuel tank. See
Remove Fuel Tank, page 96.
b. Disconnect both RTD connectors (284). See
Replace Heat Exchanger RTD, page 93.
c. Disconnect A and B material lines from
swivel fittings (297).
Repair
Proportioner Heat Exchangers
Figure 29
d. Disconnect hose clamps (37, 239) from heat
exchanger assembly (241).
e. Remove four nuts (249) and the heat
exchanger assembly (241). Pull heat
exchanger assembly out of coolant hoses.
f. Install a new hea t exchanger assembly
(241) by following the removal steps in
reverse order. Orient control valves as
shown. Continue to next step to remove heat
exchangers (802) or (803).
332637C 91

Repair
g. Disconnect two swivel fittings (805) and
swivel fittings on heat exchanger outlet (806)
from the heat exchangers (802, 803).
6.
For the engine heat exchanger:
a. Disconnect swivel fittings (617) and (618)
from heat exchanger (614).
b. Remove nuts (612), washers (613), and heat
exchanger (614). Set expansion bottle and
bracket aside.
c. Install new heat exchanger (614) in reverse
order by following the removal steps in
reverse order.
Proportioner Hea t Exchangers
Figure 30
h. Remove four nuts (810) and washers (811)
for replacing heat exchangers (802) or (803).
Engine Heat Exchanger
Figure 31
92 332637C

Repair
Replace Heat Exchanger RTD
1. Perform Shutdo wn, page 61.
2. Remove Reactor cabinet cover.
3. Disconnect RTD from CAN cable.
NOTICE
ISO and RES will release when either RTD is
removed from the heat exchangers. To prev ent
damage to load center and other electronics,
protect all elec troni cs from chemicals releas ed
from the heat exchanger RTD ports.
4. Remove compression fitting (272) from the b ack
of the heat exchanger with RTD (273) attached.
The RTD probe cannot be removed from the
compression nut.
NOTICE
To ensure accurate temperature readings, only
use RTD Kit 24L972.
5. Tighten compression fitting (272) on RTD sheath
(273).
6. Apply thread sealant to compression fitting pipe
threads (272 and install in heat exchanger.
7. Connect new RTD to extension cable (71).
Figure 32
332637C 93

Repair
Replace Control Valve
Follow thes e instructions to replace a c ont rol valve
solenoid coil or remove the component A control
valve, component B control valve, or the bypass
control valve.
1. Perform Shutdown, page 61.
2. Drain coolant from the proportioner coolant loop.
See Drain Coolant, page 66.
3. To re pai r the control valve, remove the four
nuts (VN) and washers (VW). Remove the front
of the control valve, diaphragm, and gaskets.
Purchase Valve Repair Kit 125774. For complete
installation instructions see the Control Valve
Kits manual 3A1932.
4. To remove the solenoid coil (SC), loo se n
connector screw and disconnect the coolant
valve harness (D). Remove the nut (SN)
and washer (SW) from coil. Purchase Valve
Coil Replacement Kit 125787. For complete
installation instructions see the Control Valve
Kits manual 3A1932.
Replace Power Supply
1. Perform Shutdown, page 61.
2. Disconnect power supply (655) from circuit
breaker CB01 and terminal blocks TB13 through
TB15. See Electrical Schematics, page 154.
3. Insert a flat head screw driver in the mounting
tab on the bottom of the power supply (655) to
remove from the din rail.
Figure 33
4. Install new power supply (655) in reverse order.
94 332637C

Repair
Replace Circulation Pump
To prevent burns, do not perform maintenance on
the coolant system until the coolant system has
reached ambient temperature.
1. Perform Shutdo wn, page 61.
2. Perform Drain Coolant, page 66.
3. If a wall is installed and the ci rcul ati on pump can
not be accessed, remove the proportioner. See
Remove Proportioner, page 102.
4. Disconnect pump fittings (234) from swivel fitting
(275).
5. Remove pump cover (C).
6. Press in tabs to disconnect power wires (W).
7. Remove four outside nuts (254). Hold on to the
pump flanges (234) and remove the circulation
pump (233). Remove four inside nuts (254) to
remove flanges from the pump.
8. Place o-rings, supplied with the new circulation
pump (233), between the pump and the flange
fittings (234). Insert screws (255) through the
pump and flange fittings (234) and tighten four
nuts on screws (255).
9. Place circulation pump (233) on brackets (223)
so that coolant will flow towards the sight glass.
Install four nuts (254) on screws (255).
10. Connect power wires to pump and replace c over.
See Reactor Cabinet Wiring Diagram, page 162.
11. Connect flange fittings (234) to swivel on th e
elbow flange fitting (234) and fitting (275).
Figure 34
332637C 95
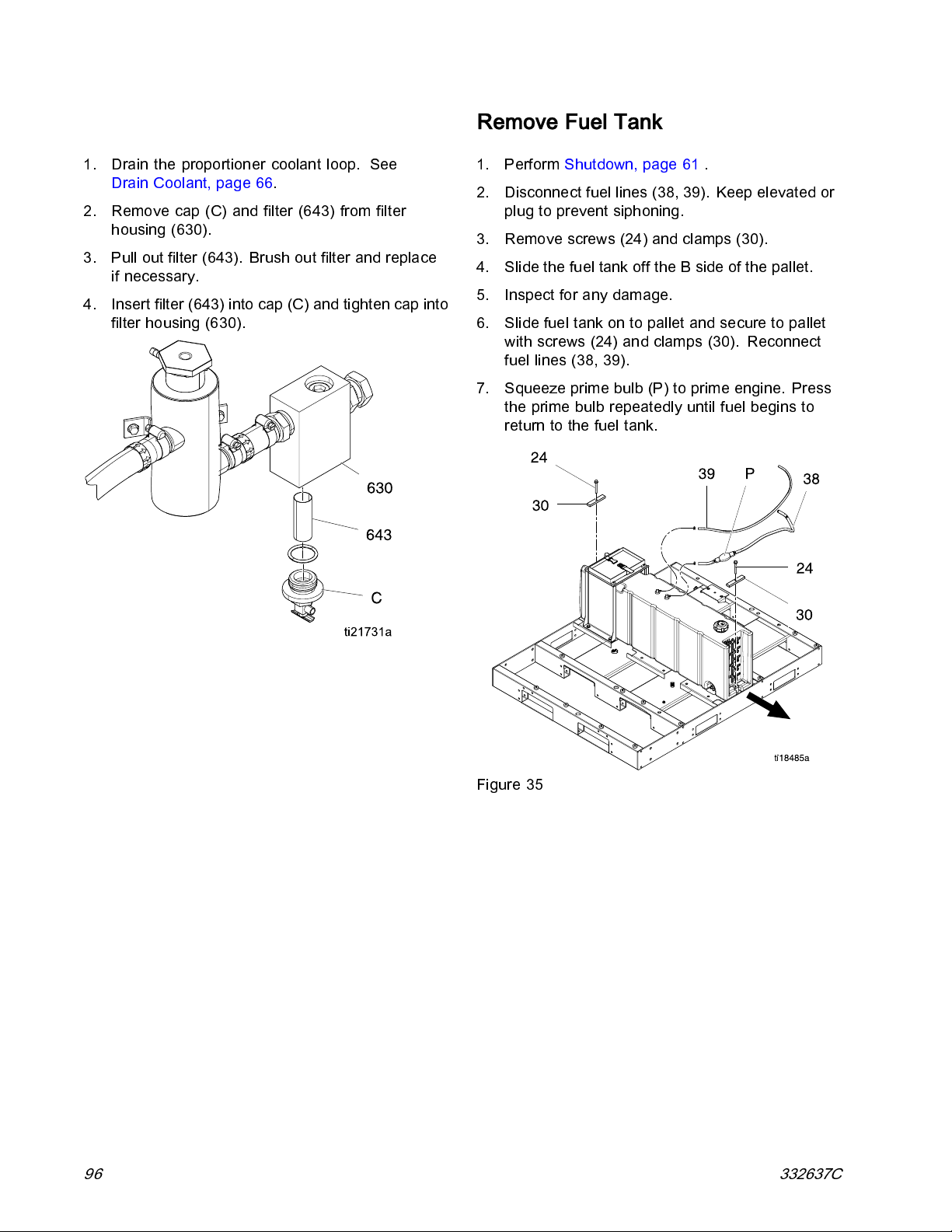
Repair
Repair Filter Housing Filter
1. Drain the proportioner coolant loop. See
Drain Coolant, page 66.
2. Remove cap (C) and filter (643) from filter
housing (630).
3. Pull out filter (643). Brush out filter and replace
if necessary.
4. Insert filter (643) into cap (C) and t igh ten c ap i nto
filter housing (630).
Remove Fuel Tank
1. Perform Shutdown, page 61 .
2. Disconnect fuel lines (38, 39). Keep elevated or
plug to prevent siphoni ng.
3. Remove screws (24) and clamps (30).
4. Slide the fuel tank off the B side of the pallet.
5. Inspect for any damage.
6. Slide fuel tank on to pallet and secure to pallet
with screws (24) and clamps (30). Reconnect
fuel lines (38, 39).
7. Squeeze prime bulb (P) to prime engine. Press
the pri me bulb repeatedly until fuel begins to
return to the fuel tank.
Figure 35
96 332637C

Repair
Replace Battery
Improper battery installation or maintenance
may result in electric shock, chemical burns,
or explosion. Battery maintenance must only
be performed or supervised by personnel
knowledgeable of batteries and the required
precautions. Keep unauthorize d personnel away
from batteries.
See Technical Specifications, page 175 for battery
requirements and recommended battery size.
1. Remove plastic caps (PC) from battery term inals
and disconnect battery cables from battery.
2. Disconnect strap and remove battery.
3. Place new battery on bracket and secure with
strap.
4. Reconnect battery cables and cover battery
terminals with plastic caps (PC). Ensure red
cableisconnectedtothepositive(+)battery
post. Connect black c ab le to the negative (-)
battery post.
Figure 36
NOTICE
Always connect the red battery cable to battery
positive (+) terminal and the black battery cable
to the battery negative (-) terminal. Failure to
properly connect the battery cable to the battery
will damage th e fusible link harness. Do not by pas s
the fusible link when damaged. The fusible link
prevents damage to other system components.
332637C 97
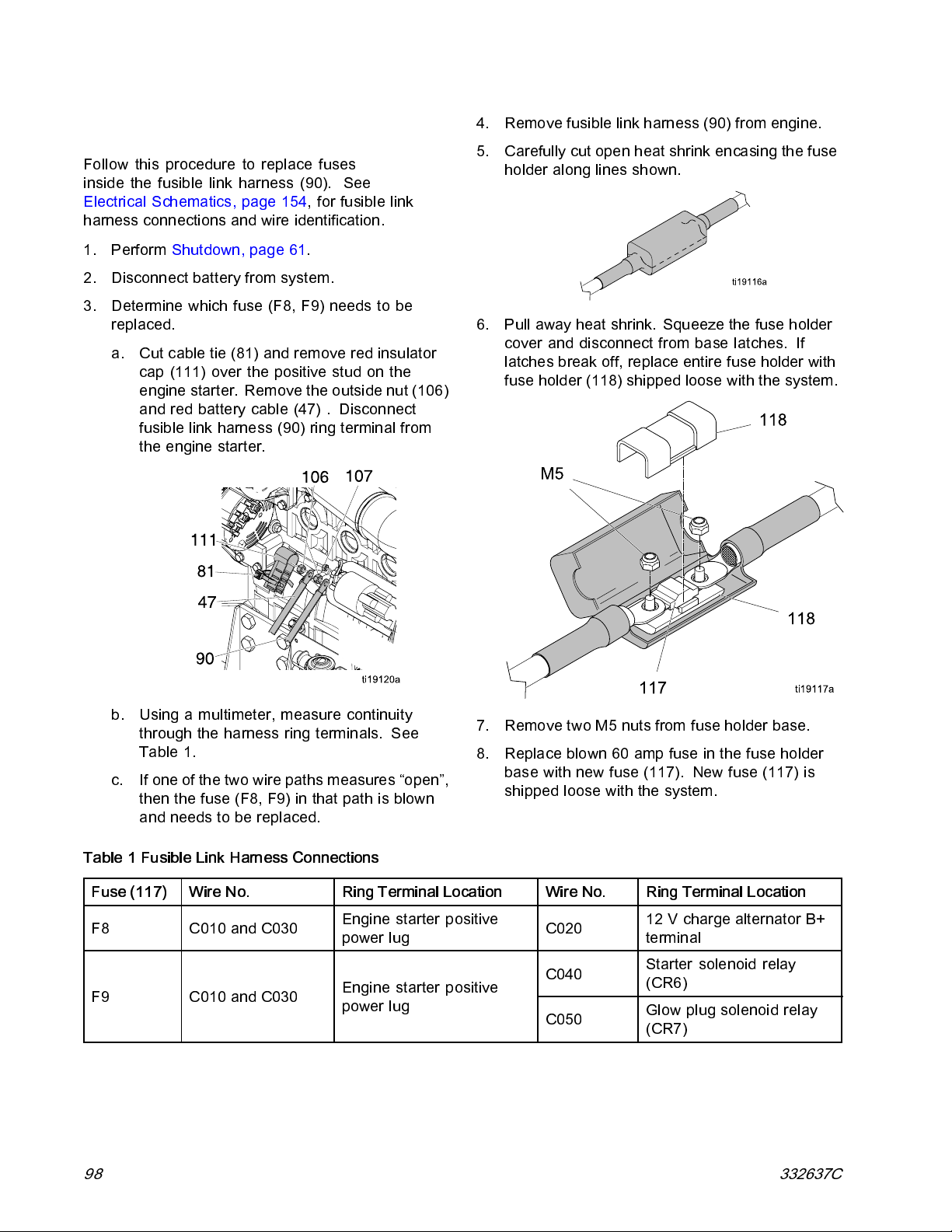
Repair
Repair Fusible Link Harness
Follow th is procedure to replace fuses
inside the fusible link harness (90). See
Electrical Schematics, page 154, for fusible link
harness conn ec tio ns and wire identificat ion .
1. Perform Shutdown, page 61.
2. Disconnect battery from system.
3. Determine which fuse (F8, F9) needs to be
replaced.
a. Cut cable tie (81) and remove red insulator
cap (111) over the positive stud on the
engine starter. Remove the outside nut (106)
and red battery cable (47) . Disconnect
fusible link harness (90) ring terminal from
the engine starter.
4. Remove fusible link harness (90) from engine.
5. Carefully cut open heat shrink encasing the fuse
holder alo ng lines shown .
6. Pull away heat shrink. Squeeze the fuse holder
cover and disconnect from base latches. If
latches break off, replace entire fuse holder with
fuse holder (118) shipped loose with the system.
b. Using a multimeter, measure continuity
through the harness ring terminals. See
Table 1.
c. I f one of the two wire paths measures “open”,
then the fuse (F8, F9) in that path is blown
and needs to be replaced.
Table 1 Fusible Link Harness Connections
Fuse (117) Wire No. Ring Terminal Location Wire No. Ring Terminal Location
F8
F9
C010 and C030
C010 and C030
Engine starter positive
power lug
Engine starter positive
power lug
7. Remove two M5 nuts from fuse holder base.
8. Replaceblown60ampfuseinthefuseholder
base with new fuse (117). New fuse (117) is
shipped loose with the system.
C020
C040
C050
12 V charge alternator B+
terminal
Starter solenoid relay
(CR6)
Glow plug solenoid relay
(CR7)
98 332637C
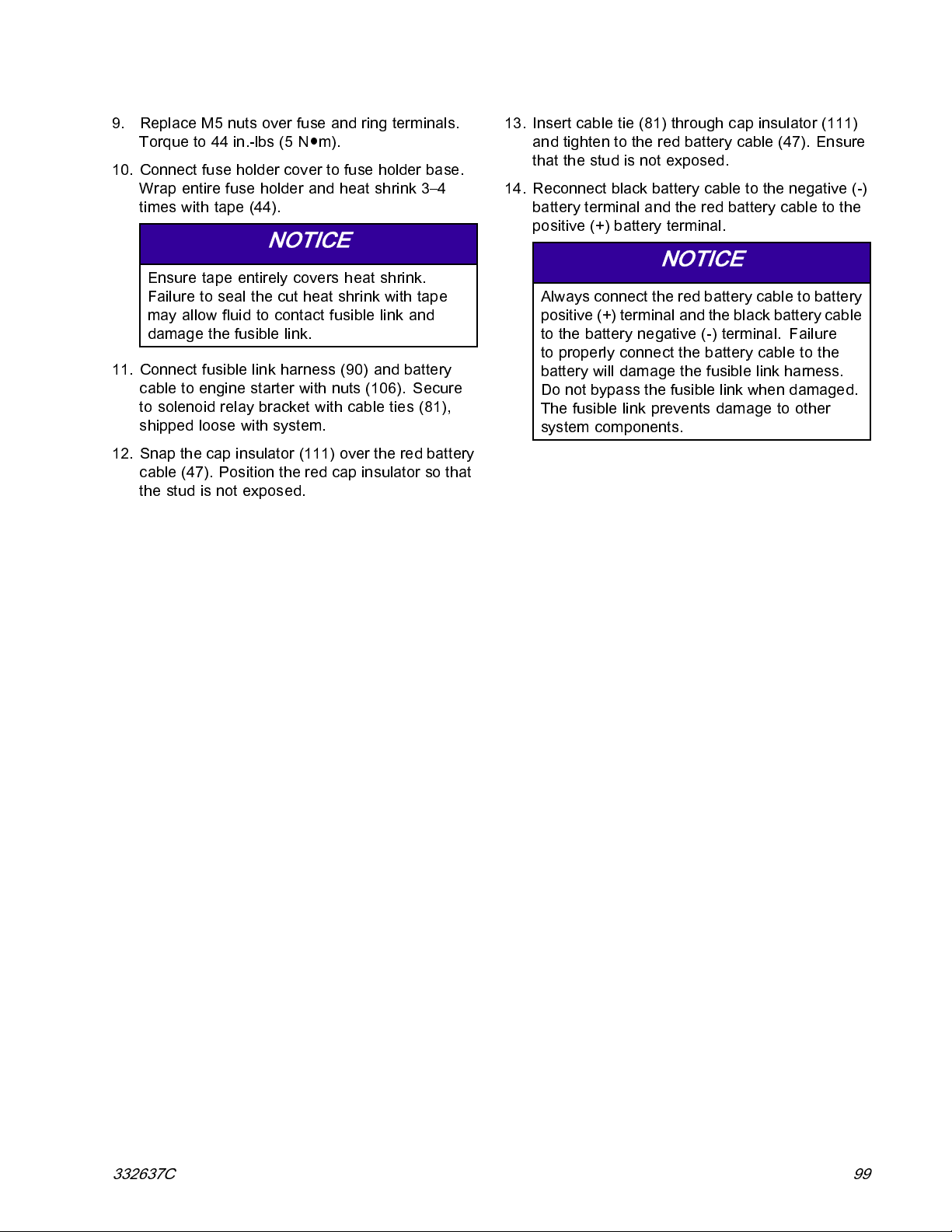
Repair
9. Replace M5 nuts over fuse and ring terminals.
Torque to 44 in.-lbs (5 N●m).
10. Connect fuse holder c over to fuse holder base.
Wrap entire fuse holder and heat shrink 3–4
times with tape (44).
NOTICE
Ensure tape entirely covers heat sh rink.
Failure to seal the cut heat shrink with tape
may allow fluid to contact fusible link and
damage the fusible link.
11. Connect fusible link harness (90) and battery
cable to engine starter with nuts (106). Secure
to solenoid relay bracket with cable ties (81),
shipped loose with system.
12. Snap th e c ap insulator (111) over the red b atte ry
cable (47). Position the red cap insulator so that
the stud is not exposed.
13. Insert cable tie (81) through cap insulator (111)
andtightentotheredbatterycable(47).Ensure
that the stud is not exposed.
14. Reconnect black battery cable to the negative (-)
battery terminal and the red battery cable to the
positive (+) battery terminal.
NOTICE
Always connect the red battery cable to battery
positive (+) termi nal and the black ba ttery cable
to the battery negative (-) terminal. Failure
to properly connect the battery cable to the
battery will damage the fusible link harness.
Do not bypass the fusible link whe n damaged.
The fus i ble link prevents damage to other
system components.
332637C 99
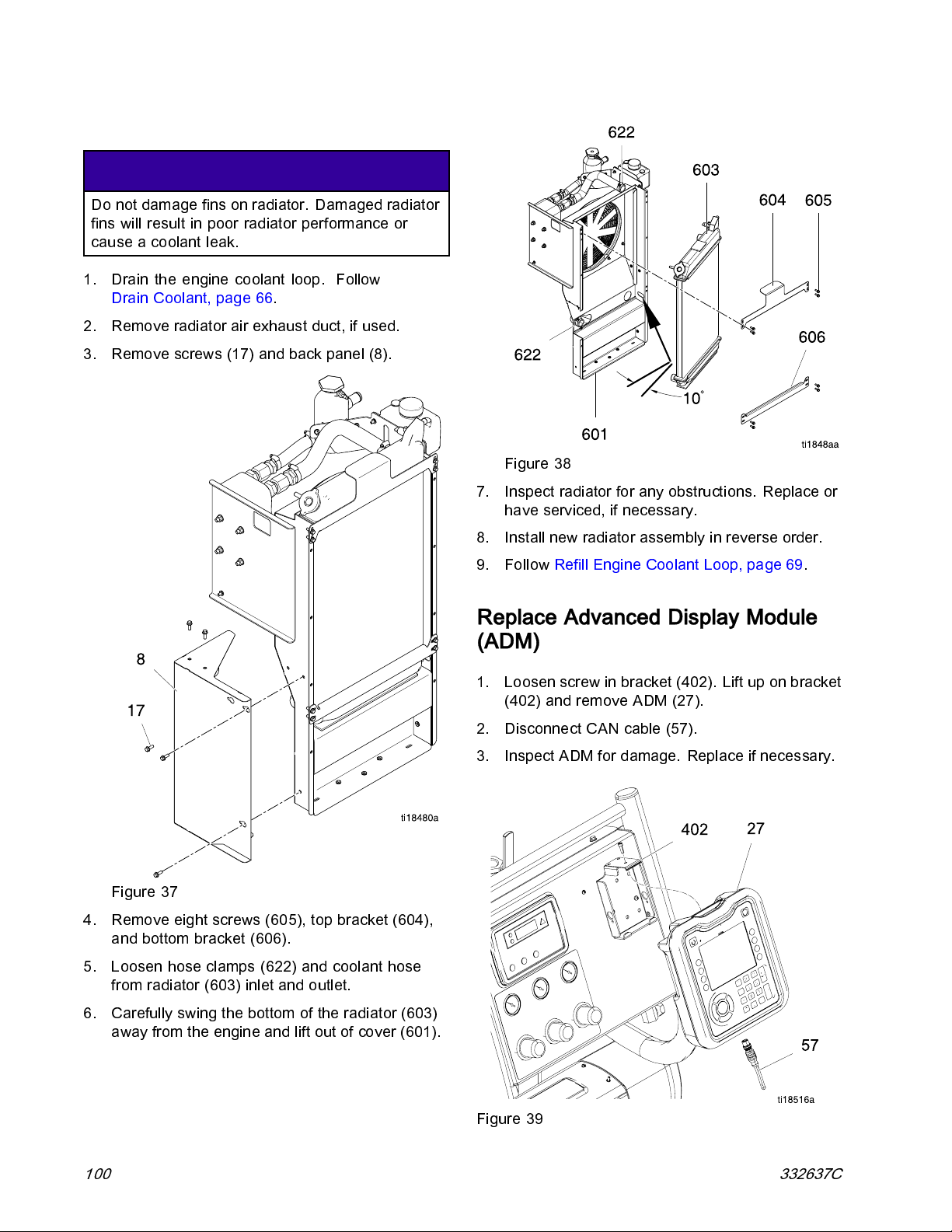
Repair
Remove Radiator
NOTICE
Do not damage fins on radiator. Damaged radiator
fins will result in poor radiator performance or
cause a coolant leak.
1. Drain the engine coolant loop. Follow
Drain Coolant, page 66.
2. Remove radiator air exhaust duct, if used.
3. Remove screws (17) and back panel (8).
Figure 38
7. Inspect radiator for any obstructions. Replace or
have serviced, if necessary.
Figure 37
4. Remove eight screws (605), top bracket (604),
and bottom bracket (606).
5. Loosen hose clamps (622) and coolant hose
from radiator (603) inlet and outlet.
8. Install new radiator assembly in reverse order.
9. Follow Refill Engine Coolant Loop, page 69.
Replace Advanced Display Module
(ADM)
1. Loosen screw in bracket (402). Lift up on bracket
(402) and remove ADM (27).
2. Disconnect CAN cable (57).
3. Inspect ADM for damage. Replace if necessary.
6. Carefully swing the bottom of the radiator (603)
away from the engi ne and lift out of cover (601).
Figure 39
100 332637C