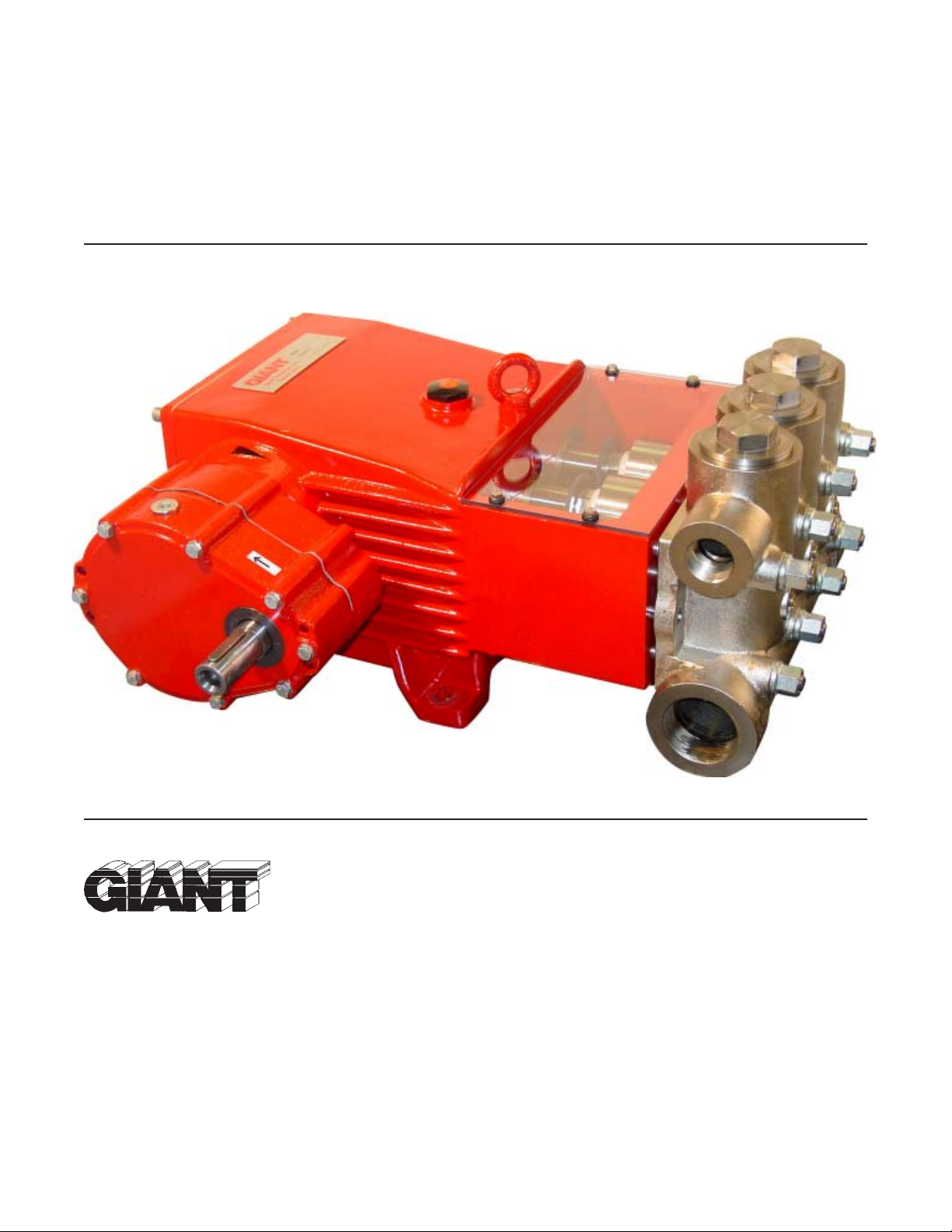
Models
GP7145GB and GP7255AGB
pump with gearbox
Triplex Ceramic
Plunger Pump
Operation Manual
Updated 10/07
Contents:
Installation and Safety Instructions page 2
Pump Specifications (GP7145GB-2.4): page 3
Exploded View: page 4
Parts List: page 5
Pump Specifications (GP7255AGB-2.4): page 6
Kits/Torque Specifications: page 7
Maintenance Information: page 7
Repair Instructions: pages 8-9
Troubleshooting Guide: page 10
Dimensions: page 11
Warranty Information back page
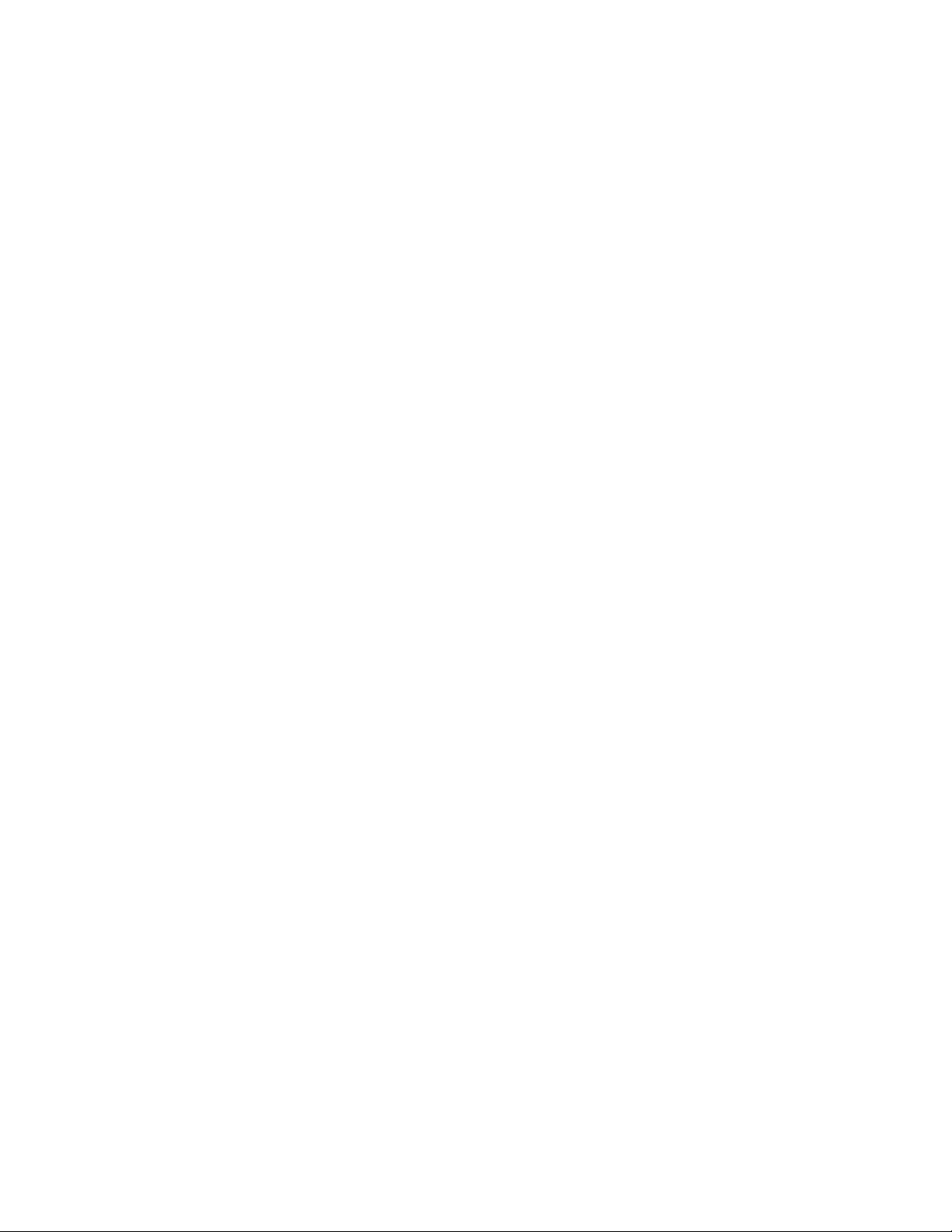
INSTALLATION INSTRUCTIONS
Operation and Maintenance
Check oil level prior to starting and ensure trouble-free
water supply.
Oil: Use only 2 gallons (7.5 liters) if ISO VG-220
synthetic gear oil. Initial change after 50 hours and then
after every 200 operating hours. If used less than this,
change once per year.
IMPORTANT! When operating in humid areas (or areas
with large temperature fluctuations, the oil must be
changed immediately (if condensate or frothy oil occurs in
the gear box).
IMPORTANT! We recommend that both inlet ports be
used in order to ensure cavitation-free operation and
optimal suction conditions. If only one connection is use,
a safety margin of 3 feet (1 meter) has to be added to the
required NPSH.
IMPORTANT! The GP7145GB and GP7255GB pumps
have a black arrow on the reduction gear, which shows the
preferred direction of rotation. The pump can be
delivered either with the gear on the left side or right side
(when facing the front of the pump), which eases planning
assembled units with regard to the desired direction or
rotation. In either case, the larger gear wheel must
rotate towards the front-end of the pump.
The preferred/optimal direction of rotation ensures that
the oil is correctly splashed on the crosshead guides via
the motion of the connecting rods, which is a particular
advantage where continuous operation is involved.
The pump can also be run against the recommended
direction of the rotation if operated periodically or at
reduced pressure. If this is the case, the pump has to be
run in this direction to smoothen the bearing areas. This is
done by a one-time operation at zero pressure for at least
30 minutes; thereafter, the pressure must be slowly
increased over the next hour to the desired maximum
operating pressure. This should run-in the pump, but you
should also check the oil temperature, which should not
exceed 160 o F (71 oC).
The torque tension on the valve casing nuts (49A) is to be
checked after approximately 200 hours. Please see page 7
for torque values.
IMPORTANT! The service life of the seals is maximized
if a minimal amount of leakage is present. A few drops of
water can drip from each plunger every minute. Leakage
has to be examine every day. If the leakage becomes
excessive (constant dripping), the plunger seals must be
changed.
Safety Rules
The operating instructions must be read and adhered to
before performing any work on the pump or complete
assembled unit. No responsibility will be carried by us
for damage to materials or persons caused by improper
handling of our pumps.
Access to the pump is not allowed by unauthorized personnel. As safety valve is to be installed in accordance with the
guidelines for liquid spraying units, so that the admissible
operating pressure cannot be exceeded by more than 10%.
Pumps operating without a safety valve as well as any excess
in temperature or speed limits automatically voids the
warranty. When the pump is in operating, the exposed shaft
side, the driven shaft side and its coupling must be covered
by a protective guard. The plunger area must also be
covered by the protective plate (30). Do not step onto the
protective plate (30 ) or put weight on it.
Before carrying out any maintenance work to the pump or
pump unit, the pressure in the discharge line and pump must
be at zero. Close off the suction line. Disconnect fuses to
ensure that the driving motor cannot accidently get switched
on. Before starting the pump, make sure that the pump, the
cooling system and all parts on the pressure side of the unit
are vented and refilled with pressure at zero.
In order to prevent air or air/water-mixture being absorbed
and cavitation occurring, the pump NPSHR (Net Positive
Suction Head Required) and water temperature must be
adhered to.
Cavitation and/or compression of gases lead to uncontrollable pressure kicks, which can ruin the pump and
unit parts and also be dangerous to the operator or
anyone standing nearby.
Giant plunger pumps are suitable for pumping clean water
and other non-aggressive or non abrasive media, which have
a specific weight similar to water.
Before pumping other liquids (in particular, flammable,
explosive and toxic media), the pump manufacturer must
be consulted with regard to the resistance of the pump
NOTE: Contact Giant Industries for
Service School Information.
Phone: (419)-531-4600.
2
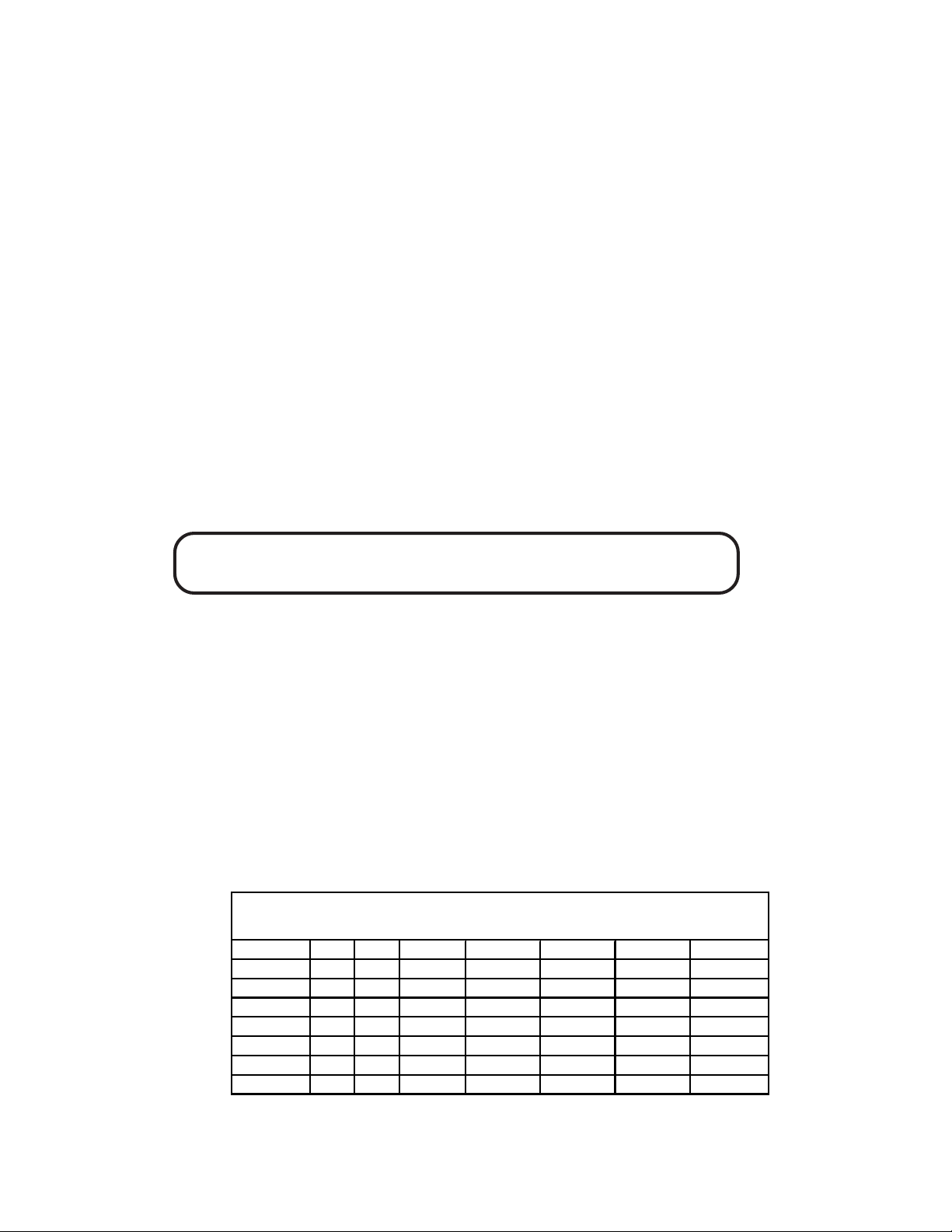
Specifications
Model GP7145GB -2.4
U.S................................(Metric)
Volume (Continuous).............................................................. 47.5 GPM .....................(180 LPM)
Volume (Intermittent) ............................................................. 60 GPM* ......................(227 LPM)*
Discharge Pressure ................................................................. 3000 PSI .......................(207 bar)*
Speed (Continuous) ........................................................................................................750 RPM
Speed (Intermittent)........................................................................................................947 RPM
Inlet Pressure (maximum) ...................................................... 145 PSI .........................(10 bar)
Plunger Diameter.................................................................... 1.77” .............................45mm
Plunger Stroke ........................................................................ 2.0” ...............................52mm
Crankshaft Diameter............................................................... 1.9” ...............................48mm
Key Width............................................................................... 0.6” ...............................14mm
Crankshaft Mounting......................................................................................................Either side
Shaft Rotation.................................................................................................................See Instructions on page 2
Temperature of Pumped Fluids .............................................. Up to 140
Inlet Ports........................................................................................................................(2) 2-1/2" NPT
Discharge Ports...............................................................................................................(2) 1-1/4" NPT
Weight..................................................................................... 455 lbs. .........................(206 kg)
Crankcase Oil Capacity .......................................................... 1.6 Gal. .........................(6.0 liter)
Fluid End Material..........................................................................................................Spheroidical Cast Iron
o
F..................(60 oC)
Consult the factory for special requirements that must be met if the pump is to
operate beyond one or more of the limits specified above.
PULLEY INFORMATION
Pulley selection and pump speed are based on a 1725
RPM motor and "B" section belts. When selecting
desired GPM, allow for a ±5% tolerance on pumps
output due to variations in pulleys, belts and motors
among manufacturers.
1. Select GPM required, then select appropriate
motor and pump pulley from the same line.
2. The desired pressure is achieved by selecting the
correct nozzle size that corresponds with the pump
GPM.
GP7145GB-2.4 PULLEY SELECTION & HORSEPOWER
REQUIREMENTS
Input RPM
720 300 19.0 10.9 13.6 20.4 27.1 40.7
960 400 25.3 14.5 18.1 27.1 36.2 54.3
1200 500 31.7 18.1 22.6 33.9 45.2 67.9
1440 600 38.0 21.7 27.1 40.7 54.3 81.4
1800 750 47.5 27.1 33.9 50.9 67.9 101.8
1894 789 50.0 28.6 35.7 53.6 71.4 107.1
2273 947 60.0 34.3 42.9 64.3 85.7 128.6
RPM GPM 800 PSI 1000 PSI 1500 PSI 2000 PSI 3000 PSI*
HORSEPOWER INFORMATION
Horsepower ratings shown are the power requirements for the pump. Gas engine power outputs must
be approximately twice the pump power requirements shown above.
We recommend that a 1.1 service factor be specified
when selecting an electric motor as the power source.
To compute specific pump horsepower requirements,
use the following formula:
(GPH X PSI) / 1450 = HP
* Intermittent Duty Only!
3
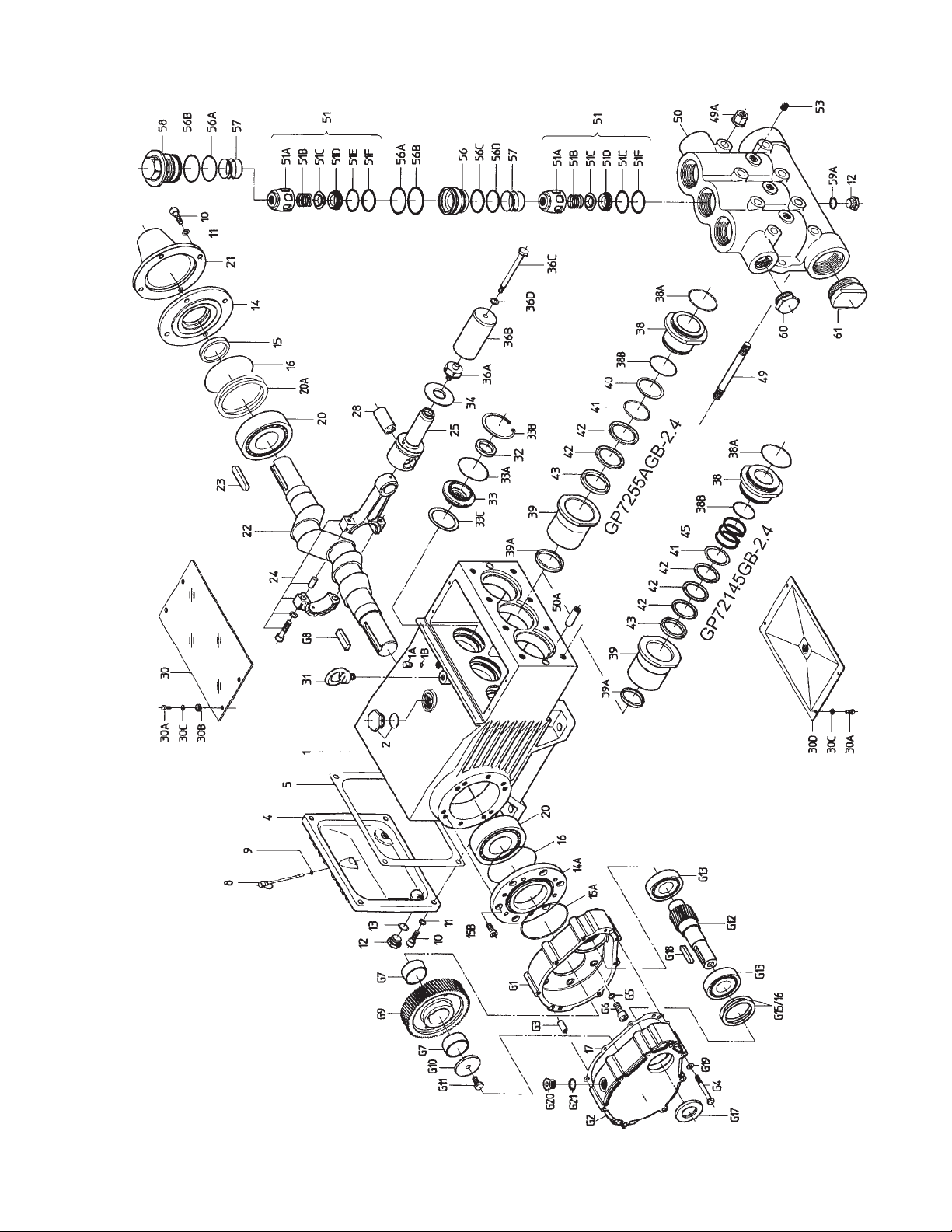
Exploded View - GP7145GB-2.4/GP7255AGB-2.4
4